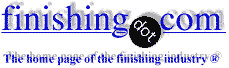
-----
Thick Nickel Erosion Strip not adhering to 6061 Aluminum
Q. I would like to start this post off by mentioning I have read every post on problematic Nickel adhesion to Aluminum bonding. Started here: www.finishing.com/392/30.shtml & read threads 878, 4074, 4487, 12880, 14954, 21801, 22414, 23303, 27627...
We are plating unusually thick nickel for erosion resistance on an aerospace rotating part.
Nickel is per AMSQQN290 & AMS2403 as the baseline followed by the OEM testing criteria which specifies a compressive stress of 2000 psi Minimum & a Vickers hardness value of 600 HV. Using ASTM E190 for converting the hardness value to Rockwell it's Roughly 87.9 (15N).
Nickel Plating is 0.030" thick on a 1" x 6" x 0.040" 6061-T6 strip of Aluminum. I can't find many plating vendors to go above 0.015" thick & the two willing to try are unsuccessful at creating a sample that will pass both the bend test & fracture test. The bend test is per ASTM E290 & ASTM B571 around a 0.5" mandrel with no visible flaking under a 10X magnification. The fracture test involves bending the sample back & forth over a zero radius until it breaks in two. At this point we observe a small de-lamination start between the two substrate approx. 0.010" wide & can stick a box knife in between the nickel & Aluminum to pry the two pieces apart with minimal pressure (Approx. 10 lbs of force). The underside looks very pearl & luminescent. I've attached photos for review.
I understand no plater would ever like this but the specification also calls out for all previous finishes to be applied before nickel & Chromic Anodize (Class 1,Type 1 up to 0.0007" thick) is one of those said finishes. The anodize layer where nickel is to be applied is removed prior to plating. We are aware that Anodize embeds into the Aluminum & account for this by removing 0.002"-0.003" with an abrasive containing no silicone that would affect adhesion at the next stage.
Our plater takes all the normal precautions as follows:
Etch-Less than 1 min.
Zincate dip-2 min.
De-smut Less than 1 min.
Double Rinse with DI water
Hydrofluoric acid etch-Less than 5 seconds
Zincate dip-45 seconds-1 minute
Double Rinse with DI water
EN strike (Alkaline) 8-10 minutes
Double Rinse with DI water
Final Electro plating bath for 19 hours.
SOAK CLEANER (BENCHMARK A-1024)
TIME: 15 MIN.
TEMP: 145 F OPTIMUM (RANGE 130 - 160 F) PH 7.5 - 8.5
MAKE-UP: 7.5% - 8.5% BY VOLUME
*Double Rinse with DI water solution
ALKALINE AL. ETCHANT(ALKLEAN 77)
TIME: 5 SECONDS
TEMP: 100 F OPTIMUM (RANGE 60 - 190 F)
MAKE-UP: 6 oz. / GALLON
*Double Rinse with DI water solution
DESMUT (BENCHMARK A-1734 L)
TIME: 2 MIN.
TEMP: 75 F
MAKE-UP: 7.5% BY VOLUME (RANGE 7 - 8% BY VOLUME)
*Double Rinse with DI water solution
ZINCATE (CONVENTYA, SIRPREP 709ZN)
TIME: 60 SEC.
TEMP: 70 F - 115F PH 10.5 - 11.5
MAKE-UP: 20% BY VOLUME (RANGE 10 - 30% BY VOLUME)
*Double Rinse with DI water solution
NITRIC ACID
TIME: 30 SEC - 1 MIN.
TEMP: 60 - 100 F
MAKE-UP: 50% BY VOLUME
*Double Rinse with DI water solution
REPEAT ZINCATE (CONVENTYA, SIRPREP 709ZN)
TIME: 30 SEC.
TEMP: 70 F - 115F PH 10.5 - 11.5
MAKE-UP: 20% BY VOLUME (RANGE 10 - 30% BY VOLUME)
*Double Rinse with DI water solution
ELECTROLESS NICKEL STRIKE
TIME: 8 MIN.
TEMP: 70 - 110 F(90 F IS OPTIMUM)REF:DATA SHEET PH 8.5 - 11.0
*Double Rinse with DI water solution
NICKEL PLATING
TIME: 28 HOURS TO BUILD UP REQUIRED THICKNESS PH 3.6 - 4.3
TEMP: 117-120F
AMPS: 1.5
We are experimenting with baking to improve adhesion but as I've read it doesn't help adhesion much & with the nickel being so thick the blistering test & the scribe/grid test per B-571 are not successful.
Thanks for all & any comments.
Justin [surname deleted for privacy by Editor]
Aerospace Quality Control/Quality Assurance - Pacific Northwest, USA
November 18, 2010
A. During the 1960s there was a large research project conducted at Wright-Patterson AFB on the subject of nickel coatings against rain erosion. I don't know the particulars, but I do know they were successful. Sorry, I don't have a link, and the participants are long gone, but maybe the DoD can help.
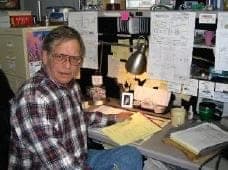
Jeffrey Holmes, CEF
Spartanburg, South Carolina
Jeff,
Thank you for your input, I didn't have any luck searching for a white paper on the rain erosion subject or any testing performed by Wright-Patterson AFB. I do not have any contacts at the DoD but would be interested in reading up on that information if you find any leads. Anymore thoughts on getting the thicker nickel to adhere through both of these tests?
Aerospace Quality Control/Quality Assurance - Pacific Northwest, USA
A. I knew Jim Weaver back when he was doing the rain erosion work at WPAFB. This particular article concerns nickel to protect plastic parts, but I'm certain Jim also worked on nickel/aluminum, helicopter rotors as I remember. That's as much as I know, so I'll let you chase Weaver's work from here.
www.stormingmedia.us/47/4766/0476666.html
One process I've heard of, but have no particulars about consists of anodizing in a copper sulphate/sulfuric acid bath, then electroplating a thin layer of copper (maybe same bath or a separate copper/sulfuric bath) followed by nickel plating. I can see how a copper deposit might thereby become interlocked into the anodize coating, and adhesion of nickel over copper should not be a problem.
At one time there was a proprietary pretreatment which deposited bronze rather than zinc, and which was said to provide better adhesion, but I cannot remember the name or manufacturer. Maybe Ted, Bob Probert or one of the other "time experienced" folks here can recall it
I don't see any obvious flaws in your present process, although there could be some control issues if the process is not strictly monitored.
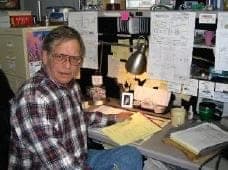
Jeffrey Holmes, CEF
Spartanburg, South Carolina
? Is it sulfamate nickel? What temperature, Metal concentration, pH, halogen level, break down SN to ammonium ion concentration?
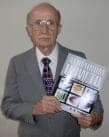
Robert H Probert
Robert H Probert Technical Services

Garner, North Carolina
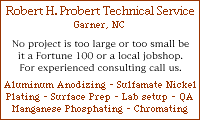
November 24, 2010
Q. My apologies for not being faster at my reply. I hope everyone's holiday went well.
Mr. Holmes,
Thank you for the link to Mr. Weavers book I will order that & have higher hopes of locating him directly if possible. We have tried both the copper & zinc strike methods to no avail but not the bronze coating. Also just to clarify the anodize layer is removed before plating that specific area.
Mr. Probert,
Yes, we run a sulfamate nickel soln. Ni. Conc. 12 oz / gal. 120 F, PH 4.0
The halogen level, break down SN to ammonium ion concentration we don't have any idea or normally measure these parameters. Could you elaborate on where this might be leading to the nickel not bonding to the Aluminum?
We also tried a 115 hr run where the parts were processed at 0.3 amps, 120 F. The idea behind this was to determine if current/voltage parameters were also a factor. The results were the same as above in the photo's.
Again thanks for anyones input.
J.
Aerospace Quality Control/Quality Assurance - Pacific Northwest, USA
A. When the SN breaks down it forms an ammonium ion and this causes the deposit to be brittle, then with the stresses involved with your thickness you may be pulling loose. ammonia ⇦ on eBay or Amazon [affil link] is formed in the sulfamate solution when (1) overheated, (2) years old, (3) too high anode current density (how recently have you cleaned out the bags). 0.003 should be no problem, I have two clients going far over that, one goes as high as 1/2 inch thick. Ammonuim ion analysis is done by distillation in special lab equipment costing over $1200. Back in the days when vendors gave service to small customers, the vendor would do the distillation analysis for the customer, in today's world you probably have to by $100 000 to get that kind of service. In addition to brittleness you may have "stress" and that comes from organics, metals (like the copper in the anodes building up -do you "dummy"?), do you carbon treat with sulfur free activated carbon. Most of that granular low priced carbon causes more contamination than it removes due to the high sulfur content. See if you can get a stress measurement and an ammonium ion analysis. If ammonium, you must dump and start over, if stress, you can dummy and carbon treat and get back to quality. Finally, I assume your EN strike is alkaline, if so it will handle tremendous zinc contamination, but a 4 oz/gal sodium carbonate dip between the zincate and the EN will reduce the zincate solution drag-in to the EN.
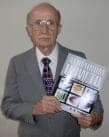
Robert H Probert
Robert H Probert Technical Services

Garner, North Carolina
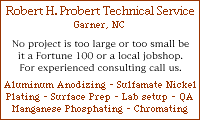
Q. I have contacted Mr. Probert & discussed in great detail with him our situation.
I want to thank both of you for suggestions & I'm very appreciative of the supporting vendors on Finishing.com
I will post again when we find the resolution to our problem.
Then again this thick nickel plating on Aluminum has been such a secret maybe we will keep it to ourselves! :-) (Joking)
Aerospace Quality Control/Quality Assurance - Portland, Oregon, USA
Q, A, or Comment on THIS thread -or- Start a NEW Thread