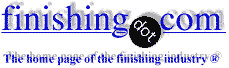
-----
Electroless Nickel delamination
2000
I have an EN plated aluminum part exposed to running DI water and have noticed a delamination of the nickel from the aluminum. Is this a typical result of exposing EN plated aluminum to DI water, or is it possibly just a bad plating job? If so, what could be the cause?
Is EN plated aluminum even an appropriate material for use with DI water? Is there a better treatment/coating for the aluminum, or should a different material entirely be used?
Any help would be greatly appreciated.
Brendan Bagwell- Tucson, Arizona, USA
Although aluminum is highly cathodic to EN, meaning that a breached coating would cause rapid corrosion of the substrate, the spec sounds okay to me. But the EN was not properly applied; plating is not supposed to peel.
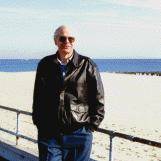
Ted Mooney, P.E.
Striving to live Aloha
(Ted can offer longterm or instant help)
finishing.com - Pine Beach, New Jersey
2000
Normally, EN is about as good as you will get for DI water if it is in the range of 2 meg ohm. Really pure water 15 - 18 meg ohm will attack nearly everything except teflon and similar products. It will even attack glass slightly.
If the EN had a poor zincate treatment, once the EN is breached, it will gradually flake off.
A thin EN coating, under 0.0015" has pores and the DI will gradually attack thru it.
For a critical component, I would spec that a EN strike(alkaline) be used before the EN and that there was a minimum time from zincate to strike to plate. No coffee breaks of potty breaks after the zincate until it is in the final EN tank.
I would also spec out an adhesion test to be run on scrap parts. The high temp bake would be appropriate, but will destroy the aluminum strength, so any of those parts would become scrap. No stripping and replating of test parts subjected to a high temp. False results. I would do the test in my own facility if at all possible. The clean cycle of a small electric oven is about the right temp, but is too long. You would have to prostitute the safety and oven life would suffer. A small muffle furnace might be adequate.
James Watts- Navarre, Florida
2000
Q, A, or Comment on THIS thread -or- Start a NEW Thread