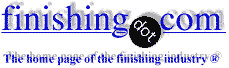
-----
Nickel Plating Adhesion Problems & Adhesion Testing
Q. Actual parts pass, coupons don't :-(
I'm having inconsistencies from my plater. On AL 6061, I'm having nickel plating, followed by gold plating over the nickel.
The parts are thoroughly cleaned before sending to the plater and the plater then cleans.
When I receive the parts back we run bake & bend test on witness coupons to confirm adhesion. Interestingly, the coupon will pass the bake test, while failing the bend test. Nickel is peeling/flaking off the AL. I've sacrificed parts by cutting a coupon out of the part. Those coupons will pass the bake and bend test.
How can I have a part, where the witness coupon fails yet the part actually passes?
As added context, we send other parts to the same plater with AL 4047, and those consistency pass the bake and bend test.
- Minnesota
July 27, 2021
A. Hi Jeremy, although you are nickel plating rather than chromating or anodizing the aluminum, I think step 1 in troubleshooting may remain the same: buy new coupons :-)
Step 2 is probably to insure that the coupons are going through the same zincating process as the parts.
Luck & Regards,
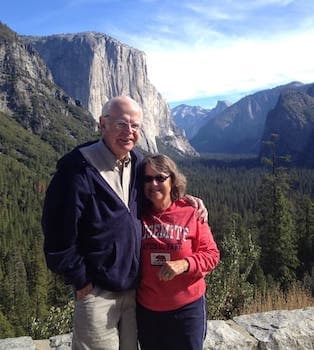
Ted Mooney, P.E. RET
Striving to live Aloha
(Ted can offer longterm or instant help)
finishing.com - Pine Beach, New Jersey
July 2021
⇩ Related postings, oldest first ⇩
Q. Dear Sir,
We have a problem of testing the adhesion of the electroplated Ni layer. We would like to use a non-destructive testing method to test the adhesion strength of the coating.
The available destructive testing method, pull-off testing was suggested for this electroplated layer. But the polymer bonding between the electroplating and the testing assembly is not good compared to the adhesion of the electroplating and the substrate. So it is difficult to test the same using this.
Please suggest some ideas to test the same
Yours Truly,
Kawasaki Heavy Industries Ltd
1998
A. Mr. Rajgopalan, I do not know a non-destructive test for nickel adhesion, but the simple destructive test is soldering a plug or a wire to nickel for pull testing.
Mandar Sunthankar- Fort Collins, Colorado
2000
Multiple threads merged: please forgive chronology errors and repetition 🙂
Nickel plating adhesion problem
Q. The issue is with a metal piece made from B4A2C and finished F70E4A (Ni electroplate, brt. Mild. A weight of 250 lbs slides over the plate through 2 bearings. The piece is experienced flaking problems after a while. Is there a nondestructive test I could perform to verify the Nickel adhesion before the piece get into use? What destructive test I could perform to evaluate my supplier's process?
Regards,
- Monterrey, NL. Mexico
2001
A. Have your supplier produce a test coupon using the same processing as the parts in question and then you can do a bend test.
Russell Richter- Danbury, Connecticut, USA
2001
A. Run a rounded steel tip over the part 10-12 times. If the adhesion is bad it may flake off or may not. The best way would be to try and lift off (exfoliate) the plating by rubbing a file on the edge of the part. nickel should grate off as a powder which is OK and not come off like a banana peel.
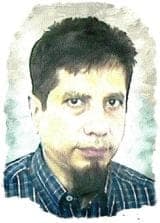
Khozem Vahaanwala
Saify Ind

Bengaluru, Karnataka, India
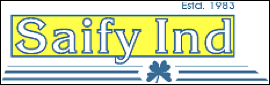
2001
A. Would a transparent self adhesive / scotch tape not do a job? Try it. Stick it well on product and try to lift with another end at one stroke. If plating comes off, you need to improve on pre treatments. A destructive test on coupon can be done. Try bending a coupon.
Payal Mag- Charlotte
2001
A. Pepe:
Disculpa la pregunta pero que es ese material B4A2C y que es ese acabado F70E4A? Es acero, aluminió que? Por otra parte, la prueba del doblez con cinta (bend tape test) se realiza sobre un cupón de acero de 1mm x 25mm x 100mm el cual se recubre y se dobla a 90 degrees, posteriormente se le adhiere la cinta (es especial y la fabrica 3M). Se le da un tirón fuerte en forma perpendicular. No debe observarse ampollas ni desprendimientos. Otra prueba mas severa es rectificar el cupon con piedra abrasiva.
Saludos y feliz navidad.
Monterrey, NL, Mexico
2001
----
Ed. note: This is an reply from a long time ago. We thank Guillermo greatly for his efforts to translate to Spanish to help his countrymen, but Finishing.com can no longer print inquiries and replies except in English. Sorry.
Test adhesion of nickel plating on aluminum
Q. How can I test the adhesion of Nickel over Aluminum. Is there any standard for the above test.
Ilan Gabayan- Haifa, Israel
2003
A. Use the slash test. Criss-cross the plated part with hatches cut into the surface with a sharp blade. Firmly adhere adhesive tape to the part, over the hatches and quickly pull it off again. Any poor adhesion will result in metal being attached to the tape. I do not know if there is a prescribed standard for this test, but it is very effective.
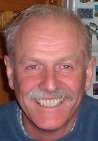
Trevor Crichton
R&D practical scientist
Chesham, Bucks, UK
2003
A. Additionally, I would bake the parts before doing the cross-hatch test. With extremely poor adhesion on aluminum, the plating may bubble just from the bake. Seeing if the adhesion is poor from the bake alone gives you the opportunity to see if your adhesion is "very poor" or "poor" (pass bake, fail cross-hatch).
Keith Rosenblumplating shop - St. Paul, Minnesota
2003
2003
A. A standard method for the test described by Trevor is given in paragraph 13 of ASTM B571 Qualitative Adhesion Testing of Metallic Coatings. Also, the bend test in paragraph 3 is required by US standards MIL-C-26074 [⇦ this spec on DLA] and ASTM B733 for electroless nickel plating. It can also be used for electroplated nickel per FED-QQN-290 (replaced by AMSQQN290) and ASTM B689.
- Goleta, California

Rest in peace, Ken. Thank you for your hard work which the finishing world, and we at finishing.com, continue to benefit from.
Nickel plated items rip after crimping
2006Hello All,
Thank you for such a useful site Mr. Mooney.
I'm an engineer working in the plating shop. We plate all kinds of textile accessories like buttons, rivets, eyelets, washers, etc. in millions of quantities every year.
We plate nickel in a barrel process from a sulphate bath, which is sort of a Watts type. Bath composition is as follows:
Bath volume ==> 400 l
Nickel Sulphate ==> 250 g/l
Nickel Chloride ==> 100 g/l
Boric Acid ==> 50~62.5 g/l
Brightener
Wetter
Because our brightener and wetter are proprietary materials I do not know what they are made up of exactly. We plate in a barrel process generally at around 12 and rarely up to 15 Volts DC for approximately one hour.
I'll try to summarize my problem below:
My item, whose base material is brass, is subject to a crimping operation of app. 270 degrees after being plated. When I crimp it the plating does not peel off. Rather than that the base material rips
(cracks from three or four places) as mentioned in letter 25470. When I crimp the plated item after sand blasting with ST110 grade steel balls, it does not rip. This tells me that the coating has internal tensile stress. One strange thing is that when the edge of my nickel plated item is subjected to an emery machine before the crimping operation, it does not rip again. (I still did not understand why this is happening. Can it be the emery machine terminating the sites where stress accumulation occurs?)
I've been trying to read nearly every question about ductility and brittleness of nickel electroplate on this site for more than one week and learned that if I use a sulphamate bath rather than a sulphate one the internal stress will reduce, or maybe will be 0. As I do not have the opportunity to change my bath I now am searching for a stress reducing agent for my process. Watson says that saccharin makes 70 MN/m2 compressive stress when added into the bath at
240mg/l. "Watson, S. A.; Organic Addition Agents for Nickel Electroplating Solutions; NiDI; 1989". There are many other stress reducing agents, for example 1,5 naphtalyne sulphanic acid, mentioned on this site which I can not remember now.
Could you please tell me a way or a substance for eliminating this problem in my coatings please?
Thank You.
plating shop engineer - Istanbul, Turkiye
A. Thank you for the kind words, Mustafa. I am not experienced in trying to lower the stress in Watt's nickel baths, so I may not be able to help you personally, but I think the first thing you need to do is to try to quantify the stress you are getting. Please look into "Stress Tabs" or consider getting a stress measuring instrument from Industrial Instruments Inc. or Special Testing and Development Co.
Once you have numbers, you can figure out whether the problem is so severe that it must be something obvious like excessive chloride, or whether it is the high end of normal and perhaps able to accept some tweaking like you are thinking of, or already at the low end. It is bad practice to mix a home-brew addition agent into a proprietary bath, so you should be trying your best to get help from the vendor. Good luck.
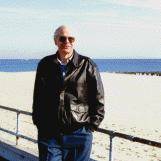
Ted Mooney, P.E.
Striving to live Aloha
(Ted can offer longterm or instant help)
finishing.com - Pine Beach, New Jersey
2006
A. The problem is with the watts nickel. The high chloride results in a tensile stress, just as you say. If you reduce the amount of chloride in the bath, that will reduce the stress. Alternatively you can bromide instead of chloride and this will help a bit. The stress can also be reduced by using sodium saccharin - say about 1 g/l. Alternatively you can change from Watts nickel to nickel sulphamate. Other agents, such as napthalene trisulphonic acid (NTS) will reduce the stress, but it is a very nasty chemical to use in a plating bath because once in, it cannot be removed, except by using it up. Hence you need to be very careful about your additions! Since you are barrel plating, you are limited in the amount you can reduce the current density to reduce the stress.
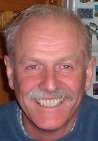
Trevor Crichton
R&D practical scientist
Chesham, Bucks, UK
2006
Multiple threads merged: please forgive chronology errors and repetition 🙂
Poor Adhesion in Plating Nickel over Aluminum
Q. Hi, my name is Francisco Hornelas, I'm from a company that plates on Fe, but we start a new process that is nickel over aluminum. We have a very good appearance and we fulfilled all the specifications except the adhesion. We use the process of double zincate and nickel strike.
Can anyone help me to improve my adhesion please? Or anyone knows which the problem with the adhesion is?
Thanks.
Plating factory general manager - Mexico City, Mexico
February 18, 2009
A. Hi, Francisco. Tell us more about the nickel strike. To my knowledge you are limited to copper cyanide or alkaline electroless nickel after zincate. Dini's "Electrodeposition - The Materials Science of Coatings and Substrates" has a great chapter on
"Adhesion".
Regards,
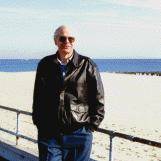
Ted Mooney, P.E.
Striving to live Aloha
(Ted can offer longterm or instant help)
finishing.com - Pine Beach, New Jersey
February 19, 2009
Q. Thanks for the book, I will get it.
I want share something that we tested and to ask other question about the same subject.
After studying in some text book, we found a table that compares the adhesion on aluminum before and after heating the metal in an oven for 1 hr. at 150°C. The table say that the adhesion is better after this process, so we made the test. After a lot of coupons tested we certify that the adhesion increase a lot. Even in coupons that demonstrated loosening or piling before the process, after it the adhesion was great.
Do someone knows what happen physically after applying heat, why the adhesion increases after this process?
Thank you.
- Mexico
February 23, 2009
A. Scientists call it inter-diffusion meaning that both metallic layers tend to penetrate and mix one into the other. Thus, the definite and clear boundary or union plane which is the weak point for adhesion failures disappears.
Guillermo MarrufoMonterrey, NL, Mexico
February 27, 2009
Q. I have a doubt regarding adhesion measurement. I use nickel phosphorous coating on steel. After electroplating I want to test the adhesion strength between Nickel-Phosphorous coating and steel. I want to buy equipment for this test. Can you please suggest me best machine for this test. I want to test only smaller material like 150 mm diameter.
Thanks in advance
- aachen, NRW, germany
February 4, 2014
Q. Hello, I am a student at RWTH. I am doing thesis at Fraunhofer in aachen-germany. What I do is I use nickel phosphorous to electroplate the steel (which is mostly round part). I want to find the adhesive strength of the coating. I tried Positest Pull Off Adhesion Tester. But it did not work. Is there any other way to find the adhesive strength?
Poovarasu vadivel- aachen, nrw, germany
August 11, 2014
-- Second Request
A. Hi Poovarasu. We appended your inquiries to a thread about adhesion testing of nickel plating. The most accurate, but somewhat tedious, approach would probably be the Modified Ollard Test as illustrated in letter 18002, "Hard Chrome Plating Bond Strength and Test Methods: Modified Ollard Test". Best of luck.
Regards,
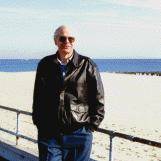
Ted Mooney, P.E.
Striving to live Aloha
(Ted can offer longterm or instant help)
finishing.com - Pine Beach, New Jersey
August 2014
A. Re. adhesion strength of Ni plating. We (at Hoyt Co) experimented with Ni plating cast iron bearings to see if adhesion of Sn base bearing alloy could be improved by a Ni inter layer. We found bond strengths of Ni to cast iron of around 54 N/mm2 by using the Chalmers test which is destructive testing of a machined specimen.
Phil DANDO- Horsham, Sussex, UK
October 3, 2014
Q. What is simple method to check adhesion of nickel plated brass threaded tubes?
Jane dabke- New Brunswick, New Jersey
August 24, 2015
A. Hi Jane. Easiest would probably be to whack the end of the tube with a hammer to make it either flatten or shatter (depending on how soft the tube is). Alternately, if the tube is soft, wrap it around a suitably sized mandrel. If the adhesion is excellent, the nickel plating will adhere despite the stretching or shattering.
Regards,
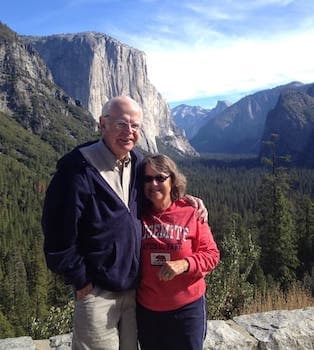
Ted Mooney, P.E. RET
Striving to live Aloha
(Ted can offer longterm or instant help)
finishing.com - Pine Beach, New Jersey
August 2015
August 25, 2015
A. Good day Jane.
Ted has offered some good advice.
I would like to add that the adhesion of nickel on the brass threaded tubes can be compromised, as threaded brass contains lead.
Dependant on your cleaning cycle, I did deal with the lead issue, whether it be be a fluoboric acid dip/ sulfuric + fluorides (sulfuric acid alone will not remove the lead oxide produced from electrolytic alkaline cleaning).
I like to use the bend and break test, or the saw and grind test.
I place the item in a vise, and flatten the tube as Ted has suggested, or grind the tube trying to "pull" off the nickel plating.
A bake test is also useful,(650-700 °F? @ 1 hour) as it is non-destructive, however there will be discolouration of the nickel if the organics (nickel brighteners/wetter) are not removed prior to baking.
Hope this is useful.
Regards,
Lab Tech. - Whitby, on, Canada
Q. I am plating small cans for used in military equipment. After nickel plating, the customer crimps the top of the cans inward 90 degrees. We keep having issues with the plating flaking off during the crimping process. Any thoughts? Thanks!
Jonathan Hale- Cleveland, Tennessee USA
April 4, 2017
A. Hi Jonathan. While poor adhesion is the cause of many such problems, another potential cause is the plating being too stressed and brittle. Even with perfect adhesion, if you severely bend highly stressed and brittle plating it will crack off. You might try plating "stress tabs" and see what kind of tensile stress you are dealing with. What is the substrate ... steel? What kind of plating are you doing ... Watts bright nickel? Have you tried dull nickel or sulfamate nickel?
Regards,
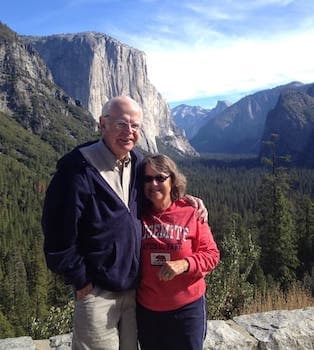
Ted Mooney, P.E. RET
Striving to live Aloha
(Ted can offer longterm or instant help)
finishing.com - Pine Beach, New Jersey
April 2017
XRF Testing for Nickel plating adhesion?
Q. We make CBN electroplated (with Nickel) grinding wheels. Very infrequently we get peeling or delaminating problems. We had a problem recently with a rectifier that was spiking and caused underlying burn which caused peeling. We identified the suspect rectifier and took back a bunch of suspect wheels which we now want to test for underlying burn rather than just strip and re-plate the whole lot. What is the best way to do this? Can we x-ray them? Will heating them up and quenching them work?
Any help would be appreciated!
Quality - West Hartford, Connecticut USA
February 12, 2020
A. Hi Jim. To my obviously limited knowledge I think you're in totally uncharted territory trying to use a non-destructive test of that sort. While I suppose you could get the strongest adhesive tape you can find, and decide that adhesion is good enough if the part passes, you'd need to test every one -- which seems as hard or harder than stripping and replating.
There are baking tests for nickel adhesion which should be more practical if your grinding wheels can otherwise accept the heat, and if the baking is not enough to disturb the hardness of the nickel. Hopefully someone can advise how hot and for how long, but I think it's quite iffy.
Regards,
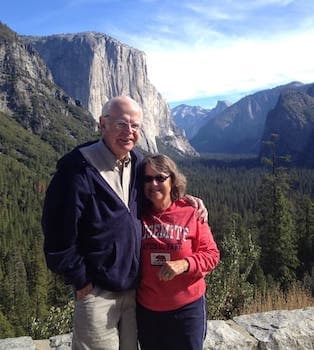
Ted Mooney, P.E. RET
Striving to live Aloha
(Ted can offer longterm or instant help)
finishing.com - Pine Beach, New Jersey
February 2020
Improving Crimpability of Sulfamate Nickel + Bright Tin Plating
Q. My company is currently barrel plating some tubular 12L14 parts with a nickel "flash", followed by bright acid tin.
Our cleaning and prep consists of an ultrasonic clean in alkaline soak cleaner for 15 minutes, 3 minute anodic electroclean in alkaline solution, 30 seconds in sodium hydrosulfite
⇦ on
eBay or
Amazon zincaffil links] solution.
Our nickel flash is a 5 minute plate in a sulfamate nickel bath at 3.25 A/ft2.
Our tin plate consists of ~55 minutes @ 3.6 A/ft2 in a bright acid tin bath.
After plating, these parts go through a solder flow oven at ~800°F for 10 minutes. Finally the end is crimped to hold a gasket snug on the ID of the part.
We have been struggling with the plating flaking off after crimping. Every adhesion test we've run shows solid adhesion between the nickel and steel and between the tin and nickel. Are there any process parameters for the tin or nickel baths that would help increase the ductility of our plated deposit.
- Grand Junction
July 9, 2020
A. Hi David. I happen to have seen a similar problem which was very easily solved, except in my case it was nickel + gold plating, and for that reason the barrel loads were very small; so I'm not sure if the cause of that problem was the same as yours ...
But what happened in my case was the barrel loads were small, the crimpable parts were quite light, and the barrel rotation relatively fast, so the parts got carried to the top of the barrel, and were taking a long time to flutter back down back into contact. Whether the actual problem was the consequent extensive make & break during nickel plating, or whether it was high tensile stress in the plating because of current density much higher than we thought because of so few parts in actual contact, I don't actually know ... because the problem was instantly and completely solved by greatly reducing the rotation speed of the barrels.
So start by considering whether the parts are properly tumbling over each other near the bottom of the barrel, or whether they're fluttering around. If that's not it, I'd suggest trying to plate at a significantly higher current density and then a significantly lower current density to see if there is an improvement. When parts are crimped it's not solely an issue of adhesion, it's also an issue of stress because if there is already very high stress, the plating can flake off no matter how well it adheres. Berl Stein's article on stress might be interesting reading for your situation.
Luck & Regards,
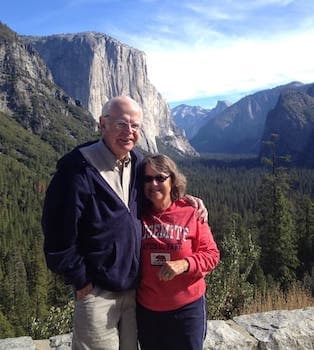
Ted Mooney, P.E. RET
Striving to live Aloha
(Ted can offer longterm or instant help)
finishing.com - Pine Beach, New Jersey
July 2020
![]() |
Go back and consider the lead content of the 12L alloy, dip in 30% fluoboric acid prior to the sulfamate to clear the exposed lead of oxides, then the SN will stick. ![]() Robert H Probert Robert H Probert Technical Services ![]() Garner, North Carolina ![]() July 10, 2020 A. Hey David, - Sidney, New York USA July 11, 2020 |
Q, A, or Comment on THIS thread -or- Start a NEW Thread