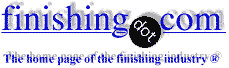
-----
Acid Copper Plating brightener/additives

Q. Hello I am a hobbyist,
I have a copper plating bath that is getting duller after every plate.
The objects I am plating are 3-D printed, then painted with an airbrush with a 1 to 1 ratio of fine 100% graphite and india ink; then put into a dehydrator for 6 hours.
They are then dunked into a bath of distilled water and gently rubbed with a fan style brush to break any surface tension and remove any air bubbles. I see no containments come off when rubbed.
Please see the results image below. from left to right is the first object plated to the third. Each object is plated overnight for about 12 hours:
Current is set at 0.07 amps per square inch
So the last object has a surface area of 5.2
0.007 x 5.2 = 0.0364A or 36.4ma
When set this low my my psu is only showing about 0.1V
I am using Singed Polyester Felt Filter Media Fabric Sheet, 1 Micron as anode bags.
I have 2 anodes 1.25 in x 4 in but i have also tried just using one.
Bath is agitated via magnetic stirrer.
Recipe
100 g / L Copper sulphate
Carrier = 150 ml water / 30 ml Polyethylene Glycol.
270 g / Liter (Sulfuric Acid)
1 Drop / L (Hydrochloric acid)
20 Drops of Rio Grande Brightener
The bath has a pH of about 0.75
Picture of setup:
Things I have tried:
Filter the fluid via coffee filters then again via a cotton ball stuffed into funnel. (cotton ball filter took about 3 hours to filter), no change.
Remake the entire bath and use the old but cleaned anodes. (saved the old fluid in a empty distilled water jug in case it can be saved.)
And again the first plate was perfect second was a bit dull and third was bad.
Remove 1 of the 2 anode bags to increase distance from anode to object, no change.
Add 4 more drops of Rio Grande Brightener, no change
Can someone share some insights of what i can try to bring this bath back and prevent future baths from going the same way?
I do not have a Hull Cell
⇦ huh?
test setup.
I suspect maybe the bath is getting contaminated by my parts but i have talked with others doing the same thing or so they say and are not having the same problem.
Things yet to try out of fear of making things worse:
active carbon filtering, just waiting for it to be delivered and will try that once it arrives.
add more Carrier solution.
Aaron Brown
- Detroit Michigan
September 15, 2022
A. Very good download free article on copper plating =>
You use too much acid and dull plating is typical for high chloride content -- Try simply 250 gms copper sulphate
⇦ on
eBay or
Amazon [affil link] / 75 gms sulfuric acid bath. Hope it helps and good luck!
- Cerovski vrh Croatia
Thanks for you reply with the link -- interesting read.
So I did some more testing including building my own hull cell tester.
It's made from a single milk bottle that was heat fused together at the seams. getting one by mail was going to take about a month and this should help me answer my questions.
I used a soldering iron that had a flat iron like tip and then Kapton tape on the side that the iron was going to be on to keep the hdpe from melting to my iron.
Here is a link the pattern I made.
So seems my plating current was low at 0.07
The solution as I have it seems much better around 0.12-0.15 per inch
Still don't know why all was well in the first few plates but seems to have settled out and is being consistent as of now.
Still need to work on my polish skills but for a first go at copper then Nickel this is amazing and better than any paint has ever gotten me.
I have been able to improve my surface finish a bit with this high acid solution without having to re balance it.
One of my issues seems to have been over agitation causing the conductive paint to lose adhesion partly.
So my solution was to turn off agitation until the entire piece was coated in a thin layer of copper. while also keeping the current low in the beginning.
My second solution is to change to a different paint that should be a bit more resistant to acid and agitation.
Paraloid B72 and acetone
⇦ on
eBay
or
Amazon
[affil link] Warning! Flammable!
mixed with the same pure graphite from before.
This seem to be working but its so thick it cant be done using a airbrush and only allows submerging the part.
Even with extra acetone this still can lead to streaks and runs.
Still not sure why the bath ran fine at the start but with the above changes I have gotten 3 good parts
- Michigan Detroit
Very cool Hull Cell! Thanks!
Luck & Regards,
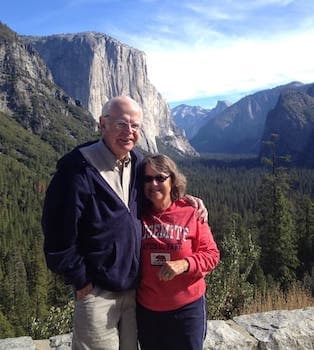
Ted Mooney, P.E. RET
Striving to live Aloha
(Ted can offer longterm or instant help)
finishing.com - Pine Beach, New Jersey
A. Try fine bronze powder instead of graphite paint. Probably best solution is chemical (reductive) silver or copper plating -- somewhat complicated, but really best solution. Hope it helps and good luck!
Goran Budija- Cerovski vrh Croatia
Interesting idea.
I know with the graphite I get about 400 to 700 ohms over 1 inch.
What would be better
Bronze Powder -325 Mesh (25$ a pound)
OR
Nickel Silver -325 Mesh (28$ a pound)
Im thinking the one with silver would be a better conductor but not sure what else to consider.
My end goal is a near a mirror finish or as close as i can get.
- Michigan Detroit
A. Hi Aaron. Actually "nickel silver" has no silver in it, it's nickel, copper, and zinc. The name is apparently derived from the fact that it's used as the substrate metal for silver plated flatware. So the bronze powder is probably better than the nickel silver.
Luck & Regards,
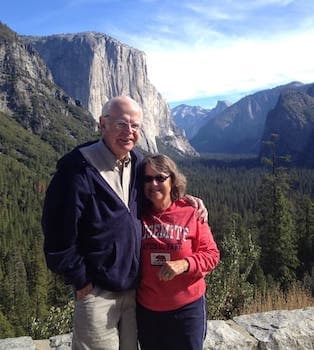
Ted Mooney, P.E. RET
Striving to live Aloha
(Ted can offer longterm or instant help)
finishing.com - Pine Beach, New Jersey
⇩ Related postings, oldest first ⇩
UBAC Bright Acid Copper High Speed
Q. We are currently in need of info on "UBAC" copper plating on stainless steel. Our customer specifies "Udylite Bright Acid Copper" plating on 304 stainless steel that is brazed onto a part made of OFE copper.
Our regular platers in SF Bay area say that all "Bright Acid Copper" is the same, but the customer (government) will not accept it. None use "Udylite".
Customer claims that the "RF, radio frequency" is most desirable with only "Udylite".
Can we prove them wrong? Can we meet the requirement?
We must mask the OFE copper as no buildup is allowed, however, no stainless may remain uncoated either. Will the UBAC process harm or deposit onto the copper if it is exposed? Thickness to be .0008 to .002.
The part is extremely expensive and the customer wants all documentation, certs and written procedures.
Jeff Olson- San Leandro, California
2001
A. Your information is correct that UBAC is a proprietary acid copper process. It is now manufactured by Enthone OMI which purchased Udylite some time back (and has since been purchased itself).
Functionally many other acid copper processes may suffice. They are generally divided into "dye type chemistry" and non dye types. The non dye types are the newer products. Frequently a specific manufacturers product gets written into a specification when it is developed and you need to get a waiver from your client if possible. Otherwise, you might try to contact Enthone (West Haven CT) to find a shop that is using the UBAC process.
Gene Packmanprocess supplier - Great Neck, New York
Multiple threads merged: please forgive chronology errors and repetition 🙂
RFQ: WE ARE ONE OF LEADING ELECTROPLATING CHEMICALS MANUFACTURER COMPANY IN PAKISTAN. WE WANT TO IMPORT ADDITIVES OF ACID COPPER ELECTROPLATING CHEMICALS AND THE FORMULATION AND FUNCTIONING OF GOLD ELECTROPLATING PLANT.
UMER FAROOQ- LAHORE, PAKISTAN
2002
Ed. note: This RFQ is outdated, but technical replies are welcome, and readers are encouraged to post their own RFQs. But no public commercial suggestions please ( huh? why?).
Q. Hi,
I need to know what kind of organic additives (brightener) I should add to a copper electroplating bath, Using CuSO4.5H2O, HCl and sulfuric Acid. Well it should use the Lea Ronal copper Gleam PCM+ though, but since I live in small city where is impossible to get that additive.
So my question: Is it possible to replace that additive using other chemical?
Toxadhie Riza- Malang, Jatim, Indonesia
2001
by Jack Dini
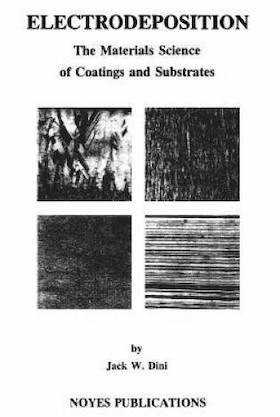
on eBay or Amazon
or AbeBooks
(affil link)
A. Hello, cousin Toxadhie.
According to Jack Dini in "Electrodeposition: The Material Science of Coatings and Substrates", common brighteners for acid copper in the old days included "glue, dextrose, phenolsulfonic acid, molasses and Thiourea ⇦ on eBay or Amazon [affil link] ".
Dini goes on to re-quote Reid from 'An HPLC Study of Acid Copper Brightener Properties' as follows: "Carriers are typically polyalkylene glycol type polymers with a molecular weight around 2000, levelers are typically alkane surfactants containing sulfonic acid and amine or amide functionalities, and brighteners are typically propane sulfonic acids which are derivatized with surface active groups containing pendant sulfur atoms".
But the vendor obviously expended lots of expensive research effort to get from the above-described very general idea to their specific formulation, and if you don't or can't license their process, you're limited to working with the generic materials and having to settle for a less satisfactory result, or expending significant expense yourself in duplicating the R&D efforts of the process supplier. You will presumably not have access to HPLC analysis and expert interpretation of the results, so you'll need to plan on becoming a Hull Cell Master :-)
Best of luck,
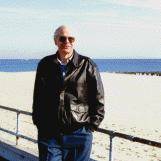
Ted Mooney, P.E.
Striving to live Aloha
(Ted can offer longterm or instant help)
finishing.com - Pine Beach, New Jersey
Q. Dear Ted,
My boss asked me to do some research into this area. Would you please give me a list of reference articles regarding the organic additives used in acid copper plating, their functions and major mechanisms of enhancing plating quality?
Many thanks,
Haifeng Zhang- Allentown, Pennsylvania, USA
2002
A. Hi, Haifeng. You can try scholar.google.com, but I think the best thing is to contact Metal Finishing Information Services in Birmingham^Warrington, England about getting a copy of their MFIS CD-ROM if you can get access to the articles it abstracts, or contract them to do the search and copy the articles. It isn't legal for me to use my copy of the CD-ROM to do a lit search for you, but one promising article looks to be: "Acid copper sulphate plating I. Simple Addition Agent Control" by Mohler J B; Metal Finishing magazine, June 1987, pp 121-122. Good luck!
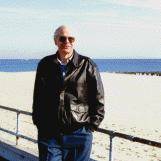
Ted Mooney, P.E.
Striving to live Aloha
(Ted can offer longterm or instant help)
finishing.com - Pine Beach, New Jersey
A. Hi Ted,
MFIS appear to have moved to Warrington (England). Here is a link to their website:
www.finishingpublications.com
Jon
- Saltum Denmark
December 21, 2015
Ed. note: Thanks Jon!
Dye-Free Acid Copper Brightener
For Acid-Copper plating of ABS, I am planning to shift from a 3- component brightener to a singe additive "DYE FREE" brightener.
Do DYE FREE brighteners pose any problems later on in brightness or leveling or any other sorts.
Electroplater - New Delhi, India
2006
A. Why shift? Run the new system in parallel alongside the old one and evaluate for yourself. Each has different situations.
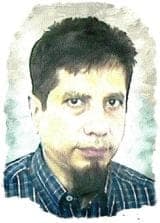
Khozem Vahaanwala
Saify Ind

Bengaluru, Karnataka, India
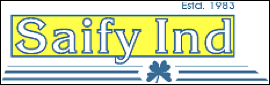
Multiple threads merged: please forgive chronology errors and repetition 🙂
Some one could let me know what dyes used in sulfuric acid solution for Acid Cu bath.
Thanks a lot
employee - Guangdong, China
April 29, 2009
There are several known organic dyes, which can help to improve the leveling:
Janus Green B (Diethyl Safranine Azo Aniline), Safranine T, Janus Black R, Janus Blue B etc. They can be obtained from Sigma-Aldrich. In any case they must be of high quality.
But it's quite hard to formulate good acid Cu additives, you also need MPS, DPS, UPS, a well balanced mixture of special surfactants (incl. block copolymers), etc.
In your case I would contact Raschig company, as they supply many of the needed specialties.
Good luck!
- Berlin, Germany
Q. Hi Everyone,
We have a handful of acid copper plating tanks (copper sulphate, sulfuric acid, chloride ions), and the leveling solution we've been buying for the last 10 years is no longer in production. I always prefer to make my own materials whenever possible, and I'd like to start preparing my own plating additives.
I've been reading a number of studies on Thiourea
⇦ on
eBay
or
Amazon [affil link] and copper deposits in acid copper plating at quantities of about 0.017 g/L, which I will start testing in the coming weeks. An old electroforming friend of mine also suggested polyethylene glycol, which I've been reading up on as well. Does anyone have a ballpark figures on how much PEG to use? Or any other advice or suggestions?
All the best,
Gaelen
- Fairfield, Iowa
December 9, 2020
A. Howdy Gaelen,
PEG is a chain so typically there's a molecular weight of the chemistry you buy. This weight is going to play a role in how much you would use. On top of the molecular weight of the PEG the ratio of your chloride to the volume of PEG is going to be important. I can't give you an exact number as I don't know what type of deposit your shooting for, but some general guidelines is smaller MW compounds need higher g/L large MW compounds typically need less.
Depending on other additives will change how much you will need Patent US4430173A uses 10-100g/L with 9k mw
Studies on Anisotropic Electrodeposition of Copper
with Organic Additives uses 300 g/L with a 3000 mw
Hopefully this gives you a good starting point. There plenty of online studies which use a range of different chemicals for carriers, brighteners, and levelers.
Good luck!
- Sidney, New York USA
Hi William,
Thank you very much for your reply. The 9th was my birthday (the grand ol' 36th) and you made my day with what you wrote back : ) It's a great starting point, and just what I was looking for.
We're electroforming over some highly textured and complicated molds a little 36"-41" across about with 1" variations of depth ... I'll keep reading patents and materials about Thiourea
⇦ on
eBay
or
Amazon [affil link] and PEG - thanks for pointing me in a good direction.
Cheers,
Gaelen
- Fairfield, Iowa
Q. I am working in an Organization where I have to look after Acid Copper Plating process without any additives, maintaining the deposition around 300 microns. My questions are --
1. During the process a huge amount of copper sulphate is generated, which is not taking part in metal deposition.
I have to take out some solution and dilute the bath solution to maintain copper sulphate concentration at 250 gm /ltr.(maximum). This is huge loss. How to stop this generation of copper sulphate, so that the bath efficiency would be increased?
2. If my issue is solved, if the conductivity & pH are measured and corrected, in that case what should be the range of conductivity and pH?
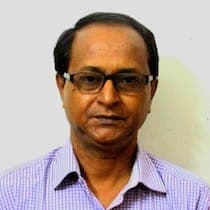
Rathin Mukhopadhyay
- Kolkata, West Bengal, India
May 26, 2022
A. Hi Rathin. Thanks for the question but it remains very difficult to properly answer because there is very little context. This is very thick plating: What are you plating and why? What sort of special properties are expected of this plating? Brightness, small grain size, freedom from porosity are not required? Or are they? Why can't any additives at all be used? Are you familiar with and using phosphorized anodes? Thanks.
The anodic efficiency (dissolving copper) is greater than the cathodic efficiency (plating out copper), and that is why the dissolved copper is increasing. Additives might help, optimized anodes might help, some inert anodes might help, pulse plating might help, but please give us more info on what you are trying to do and why. Thanks!
Luck & Regards,
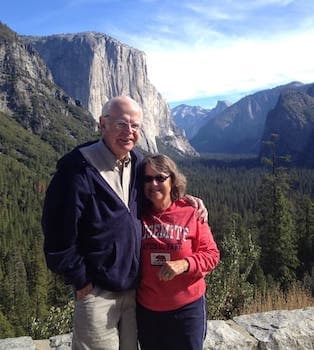
Ted Mooney, P.E. RET
Striving to live Aloha
(Ted can offer longterm or instant help)
finishing.com - Pine Beach, New Jersey
Q. Dear Ted,
Thanks for your early response. Now, I am going to elaborate a few points as per your query :
1. I electroplate Earth Rod / Ground Rods. This is a process of electro copper deposition on steel Rods (MS) of different dimensions like - 1/2 inch X 8 ft, 5/8 inch X 10 ft etc.
2. I don't need extra brightness. Porosity is not my issue but of course grain size is a big issue. I am continuously trying to reduce grain size as much as possible.
3. Yes, I am very much familiar with phosphorised copper anode - I am maintaining it at about 0.04%.
4. Since my system is non-bright, I don't think additives are necessary. These organics make more issues.
5. Bath solution consists of Copper Sulphate, sulfuric Acid and Chloride (60 to 100 ppm). Adequate air agitation and filtration are provided. Operating Current Density -240 amps/sq.ft (maximum).
What I am trying to do is very clear - to stop / minimize generation of copper sulphate in the bath solution during electroplating process.
And why - to increase bath efficiency.
Now, I need your valuable opinion that is the issue is solved by knowing and adjusting the conductivity and pH of the bath solution?
Thanks & regards,
Rathin
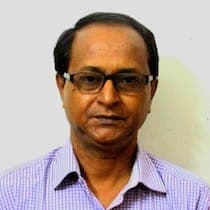
Rathin Mukhopadhyay [returning]
- Kolkata,West Bengal, India
May 27, 2022
A. Hi again Rathin. I have not operated a copper sulphate bath, so all I can offer is book learning, but they all seem to note that the anode efficiency is greater than 100%, so the problem cannot be completely stopped, so the best defense is to keep cathode efficiency as near to 100% as possible by maintaining copper and acid concentrations near the middle of the operating range 20-32 oz./gal and 6-12 oz./gal respectively; keep temperature slightly warm, about 90 °F, and make sure you have very good agitation so there is never any copper starvation at the cathode. Since chloride aids in anode corrosion, you might try to reduce it. I assume you are plating onto an underlayer of nickel plating?
Readers: We have several threads about copper plating of steel earth rods / ground rods here, for those readers with an interest in that subject, including "Copper vs. Galvanized Steel Ground Rods /Earth Rods" and "Copper plating steel grounding (earthing) rods"
Luck & Regards,
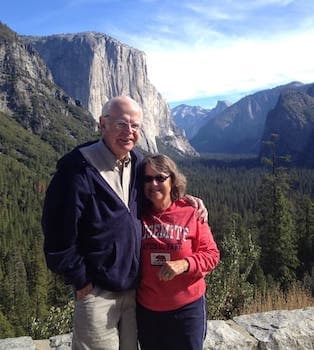
Ted Mooney, P.E. RET
Striving to live Aloha
(Ted can offer longterm or instant help)
finishing.com - Pine Beach, New Jersey
![]() |
Q. Dear Ted, ![]() RATHIN MUKHOPADHYAY [returning] - KOLKATA, WEST BENGAL, INDIA A. Hi Rathin, - Manchester, UK |
A. Hi again, Rathin. The only additives that I know of shield the cathode, thereby possibly even slightly decreasing cathode efficiency, accentuating the problem.
I believe that Dave Kay has the best idea, experiment with platinized titanium anodes, even though expensive. To my knowledge a plain titanium anode will not conduct current in this situation and would instead just increase the current density on the remaining copper anodes, not helping with the problem.
Luck & Regards,
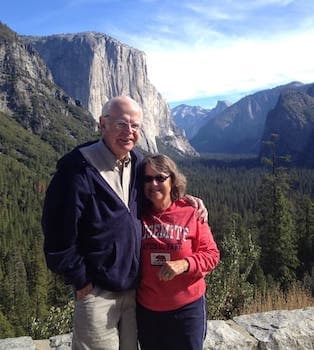
Ted Mooney, P.E. RET
Striving to live Aloha
(Ted can offer longterm or instant help)
finishing.com - Pine Beach, New Jersey
Readers --
Q, A, or Comment on THIS thread -or- Start a NEW Thread