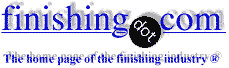
-----
Copper plating steel grounding (earthing) rods

Quickstart:
Grounding or earthing rods are long (often 8 feet) copper plated rods which are hammered into the earth as a reliable grounding connection for electrical distribution systems.
Some common issues include the facts that these rods are a relatively inexpensive 'commodity' product, so the plating is often 'down & dirty' rather than super precision; plus the fact that the rods are often threaded after plating, and when the threads are rolled into the rods, it creates substantial adhesion issues for the plating.
Q. Hi. I was going through the posts for copper plating of earth rods; even I am a manufacturer of earthing rods, we all face the same issues for copper peeling off from the threads and plating not even.
As for the threading we are able to thread on copper without peeling at the ends.
My question is related to uneven deposition of copper in the length of 8 ft.
If we are plating the rods horizontally in the tanks and I am rotating it at a constant speed then the deposition of copper is even in a range 4 to 7 microns -- but when you see it in the length it varies from 50 to 80 microns.
We are supplying current from one end right now. So the end on which the current is applied, the deposition is higher compared to the other end.
I need to reduce the variation to 20 microns.
And when we are rotating the rod, what speed is sufficient in your experience?
Director - Mumbai, Maharashtra
May 26, 2023
Ed. note: Hi Ashwin. This isn't a free consulting service, but a mutual help forum. You've solved the threading issue, which remains a serious problem for many readers, so, while you await a reader to help you, please give the other readers some hints towards solving the threading issue. Thanks!
A. Hello Ashwin,
It would definitely help if you could add another cable/connection to the other side of both anode and cathode bars. Your current density is higher on the ends, so bringing in your anodes from the ends will also benefit you. Lowering your amperage while increasing time will also help with copper thickness distribution. Hope this helps.
- Cazenovia, New York USA
June 4, 2023
Thanks Mark for the reply; will try it and update.
- Mumbai, Maharashtra
June 5, 2023
Q. Facing copper coating tear with (peel off) at the threading process after copper plating. Please help.
Mohmadsalim BadiPlating supervisor - Rajkot, Gujarat, India
July 18, 2025
A. Hi Mohmadsalim.
As mentioned in earlier postings on this thread, threading before plating is the better way to go, because maintaining adhesion during threading is obviously very difficult. But I think you need to first determine whether the adhesion of the plating is excellent because, if not, the plating will certainly peel no matter how good your threading process. Therefore you should have some semi-quantitative measure of the plating adhesion. Do you regularly test the adhesion? If so, how?
Sorry, but I have no hands-on experience in threading of plated rod and cannot offer advice regarding improvements there.
Luck & Regards,
Ted Mooney, P.E. RET
Striving to live Aloha
(Ted can offer longterm or instant help)
finishing.com - Pine Beach, New Jersey
⇩ Related postings, oldest first ⇩
Q. Dear Sir,
We are exploring the possibility of a plant to do copper coating on a mild steel rod. Copper thickness required shall be in range of 20 micron to 125 micron.
Interested to receive electroplating process and how to do equipment sizing.
Regards
electric equipment supplier - Dubai , United Arab Emirates
2003
A. Hi Rajan.
Although you might consider hiring a plating consultant or asking a process supplier to work with you, you start with the size & quantity of rods you want to plate, which will help you decide how to handle them (general purpose racking either vertically or horizontally, vs. rolling them like in a conduit plater, vs. continuously end-to-end, etc).
Then you need to pick a copper plating process; most likely you will need to clean, acid activate, and either cyanide copper plate them or nickel strike them before acid copper plating. And you will end with a tarnish preventer, probably based on sodium benzotriazole.
Good luck!
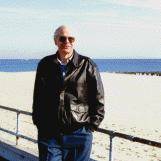
Ted Mooney, P.E.
Striving to live Aloha
(Ted can offer longterm or instant help)
finishing.com - Pine Beach, New Jersey
A. Hello Mr Rajan,
Firstly you should mention the application of the components which your are going to do copper plating for e.g., its printing roller, or earthing rods? Do you need a hard copper? Such details we need to suggest the right process and equipment.
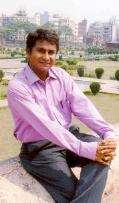
Praveen Kumar
plating process supplier
Mumbai, India
Multiple threads merged: please forgive chronology errors and repetition 🙂
Q. I need to copper coat an earth rod (copper bond ground rod). As you may know, to comply with standards the thickness of the coat should be between 0.2-0.3 mm. Does anyone know the cheap easy way for applying this coating?
Is it possible to reach this thickness with electroplating or electroforming? Which one is best suited for this application (quality and financial wise)? Is there any other solution besides these two methods?
earthing system - UAE
2005
A. Actually, Arash, electroforming is the exact same process as electroplating. We just call it electroforming if the substrate is discarded or reused and serves only as a mold for the plating, such that the plating itself constitutes the whole finished object. In your case the steel rod remains in place underneath the copper plating, so it is not an electroforming operation.
Electroplating is how all your competitors make them. Acid copper plating will not adhere well enough to steeI, so you must start with either cyanide copper plating or a nickel strike before acid copper plating. I can't say much more about the exact chemical methods because I was closely involved in the development of a process for one supplier who told me about some non-obvious chemistry. But you might want to consider licensing the patented technology from Galvan Industries [Harrisburg, NC] because it is quite slick and very economical.
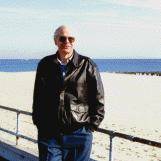
Ted Mooney, P.E.
Striving to live Aloha
(Ted can offer longterm or instant help)
finishing.com - Pine Beach, New Jersey
Q. I hope you do answer our question soon. I specifically write to you because I have seen you have a lot of knowledge about grounding rods. The problem we face is that after plating 250 to 300 microns of copper on the steel core we cannot do the threading on the ends of the rods as required. The copper leaves the rod. The bonding is good enough because we have carried out the bonding test. Maybe the copper is not ductile enough? How can the copper be made ductile easily. How are other manufacturers threading these ground rods after the copper plating?
Ajay Balajimanufacturer - Mumbai, Maharahtra & India
April 13, 2008
A. If my conversion is correct, you are plating about 0.001 inches of copper.
When you thread an end, the copper is not going to stay attached to the core in the threaded area. If it is peeling off beyond the threaded area, then you do have a bond strength problem and your test is not adequate for the use.
One way would be to mask off the end, so you do not have to thread the copper. But why are you threading the rod?
One American chemical company sell proprietary solutions that are made for this purpose and it evidently works. I think that it is an electroless process, so maybe the rod is pre-threaded. Maybe you can overcut the thread by 0.002 per side and truncate the top of the thread more than normal and be able to plate the threads without having to "chase" them after plating.
- Navarre, Florida
A. Hi, Ajay. James is obviously right that doing the threading before the plating is the ideal way to go.
Unless you are doing an undercoat of nickel plating or cyanide copper, you almost surely do not have sufficient adhesion; tell us about your plating process. If you are striking as described, then the copper is probably too hard. You can anneal it to dead soft if you can't deposit it in soft enough form.
The obvious problem for all copper platers of grounding rods is that it is a highly competitive 'commodity' market, and it is hard to afford extra costs like threading before plating, or annealing before threading.
Good luck!
Regards,
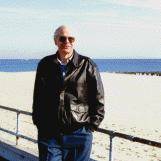
Ted Mooney, P.E.
Striving to live Aloha
(Ted can offer longterm or instant help)
finishing.com - Pine Beach, New Jersey
Q. Dear sir
I want to start a earth rod manufacturing industry I am pretty confused about the copper coating process can you please tell me what kind of machine I require. Is it expensive?
Regards,
- Bangalore, Karnataka, India
May 26, 2009
A. Hi, Gladson.
The rods can be hung from a rack vertically, or they can be hung from a rack horizontally, or they can be plated while rolling in a machine similar to a conduit plater, or they can be plated continuously, end-to-end. To a large extent, the choice of mechanical handling method will probably depend on size & production rate.
If you have not yet visited a couple of ground rod or copper plating facilities and read up on it, I'm not sure that you are yet ready to choose which style of machine you need though. If you have a lot of patience you can probably see sketches of these various approaches in patents. Good luck!
Regards,
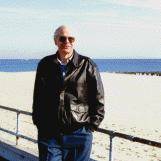
Ted Mooney, P.E.
Striving to live Aloha
(Ted can offer longterm or instant help)
finishing.com - Pine Beach, New Jersey
Q. When I copper plated the rods of size 2500- 4500 mm, the deposition of copper is less at the center of the rods...
Can you suggest some remedies for this.. for 250 microns rods.. and as per UL (Underwriters Laboratories Inc.) standard
engineer - Mumbai, Maharahstra, India
September 15, 2011
A. Hi, Abhiraj
If you are plating these vertically in a conventional tank, the most obvious improvement is to shorten the anodes. This increases the distance from the anodes to the top and bottom of the rods, thereby reducing the buildup on the ends. If you are plating them racked horizontally, you could remove the anodes nearest the ends of the tank for the same reason.
Please start by telling us what you are currently doing because there are so many ways to do it that discussing it in the abstract will only get you a hundred ifs-ands-&-buts and very little progress 🙂
Thanks and Regards,
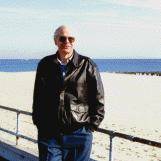
Ted Mooney, P.E.
Striving to live Aloha
(Ted can offer longterm or instant help)
finishing.com - Pine Beach, New Jersey
Q. Hi Sir,
Our tanks are horizontally placed and the rods are placed in the tank parallel to the ground level.
When I copper plated the rods of size 2500- 4500 mm, the deposition of copper is less at the center of the rods.
Can you suggest some remedies for this or 250 microns rods and as per UL (Underwriters Laboratories Inc.) standard.
The time limit is 215 minutes.
And still we don't find the perfect finish nor the deposition of copper is very satisfactory.
Please suggest some remedies in this.
Thanking You.
Engineer - Mumbai, Maharahstra, India
A. Hi, Abhiraj
The plating is thinner near the center and heavier at the ends because there is more electricity flowing to the ends because of the way the electricity bunches up on the ends unless the span of anodes on the anode bar is shorter than the grounding rods.
The easiest fix is to remove the anodes near the end, making sure their span is significantly shorter than the length of the grounding rod. If this isn't enough, you can install "shields" -- vertical PVC or polypropylene sheets that block the shortest current path to the ends of the grounding rods. If the path is longer the resistance will be higher and the excess plating thickness eliminated.
But if you are having multiple problems like "very unsatisfactory deposition", you might wish to retain a finishing consultant; trying to learn satisfactory plating from trial-and-error and books can be a big challenge. Good luck.
Regards,
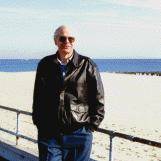
Ted Mooney, P.E.
Striving to live Aloha
(Ted can offer longterm or instant help)
finishing.com - Pine Beach, New Jersey
Q. The answer you gave me was not satisfactory.
Please suggest some other remedies for this as we copper plate rods of various lengths from 4 feet to 10 feet.
Engineer - Mumbai, Maharahstra, India
October 5, 2011
by N. Kanani
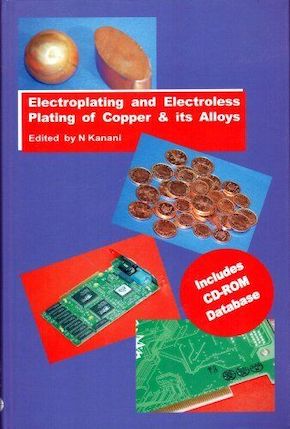
on eBay or Amazon
or AbeBooks
(affil link)
A. Hello again. Hopefully you are not trying to plate rods of different lengths at the same time. Faraday's Law tells us that the thickness of metal deposited will be proportional to the current flowing to it. That is, the plating thickness will follow the current distribution. I suppose that alternatively you could bend the anode rods into a dog-bone shape so that the anodes are closer to the earthing rods at the center than at the ends; or you could hang plastic shields at the ends of the rods to make the electrical path longer. But if you do not repair the "primary current distribution" through either the arrangement of the anodes or the installation of plastic shields to divert the current, Faraday tells us that you will not ever be able to solve this problem of uneven thickness.
As for the other plating problems you are having, if you describe what you are doing in terms of process: sequence, concentrations, temperatures, etc., and in exactly what way the plating is unsatisfactory, people may be able to help you ... or you could study a book on copper plating. But plating is not drop-dead easy, you can easily do a hundred things wrong, so unless you tell us exactly what you are doing and the results, it's unlikely that anyone can tell you what you might be doing wrong.
Best of luck.
Regards,
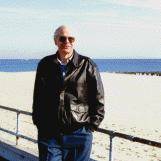
Ted Mooney, P.E.
Striving to live Aloha
(Ted can offer longterm or instant help)
finishing.com - Pine Beach, New Jersey
Multiple threads merged: please forgive chronology errors and repetition 🙂
Q. We are in search of an electroplating plant where we can produce 100 to 300 micron copper coated MS rod 12-20 mm OD, 10-12 ft.long. We want to rotate the MS Rod at the time of electroplating to get uniform copper coating 100-300 micron. Is it possible?
Amit Sarkar- Kolkata, West Bengal, India
January 3, 2013
A. Hi Amit.
Try reaching out to Laurens Willard of Galvan Industries, Harrisburg, No. Carolina to see if they are interested in licensing their process and machine design. They copper plate grounding rods. Although there are many companies who can build a plant for you, knowing from experience what works and what doesn't is always a great start, and Galvan invented, developed, and patented a really impressive total process and equipment solution :-)
I did some consulting work for them years ago, but I learned from them far more than I taught them, so I cannot reveal the things they taught me ... and I'm not sure I can be of much help while hiding what I learned :-)
Luck and Regards,
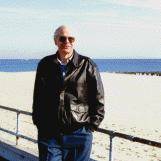
Ted Mooney, P.E.
Striving to live Aloha
(Ted can offer longterm or instant help)
finishing.com - Pine Beach, New Jersey
[editor appended this entry to this thread which already addresses it in lieu of spawning a duplicative thread]
Q. My name is anandh kumar from Chennai
I am doing acid copper plating; I am doing earth rods. For plating these rods we want 250 micron but I need even microns in the rod .
- Chennai Tamil Nadu, India.
July 17, 2017
A. Hi Anandh. We attached your inquiry to a discussion on that subject. If it does not answer your questions, please tell us what you have been doing and what is happening. Thanks!
Regards,
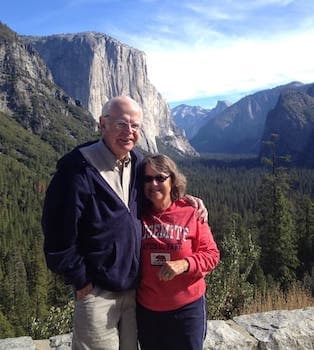
Ted Mooney, P.E. RET
Striving to live Aloha
(Ted can offer longterm or instant help)
finishing.com - Pine Beach, New Jersey
Copper Plating on Mild steel rod
Q. Dear Sir,
When threading is done on copper plated steel rod. Copper tends to peel off on threaded part . Coating thickness is more than 250 micron. Can you suggest any suitable measures to solve this issue??
I have tried various pre treatment process like acid and electro cleaning, but none of them worked yet.
Also tried copper strike using cyanide ...
as well as nickel bath prior acid copper plating...
Still there is no improvement.
Kindly suggest.
Thanks.
Regards,
- Mumbai, Maharashtra, India
October 27, 2017
A. Hi Rahul. It's obviously better to thread the rod before plating. But if you are threading after plating, roll forming the threads offers the only possibility at all. (For the benefit of other readers, if you cut threads into the rod after the copper plating, there certainly would be no copper plating left on the underlying steel, no matter what technology was used in applying it). You can't just "try" nickel striking and then abandon it, you must do it -- there is zero chance of acid copper plating adhering sufficiently directly to steel to allow threading.
Your continuing questions are, of course, always welcome in this forum ... but your e-mail address has been used by your predecessor or a co-worker over a period of more than 6 years now, posting dozens of questions on virtually every aspect of ground rod plating technology -- from poor appearance, to bad adhesion, to uneven thickness, to the plating turning green, to questions about lacquering grounding rods, to threads being blocked by plating after threading -- during which time we've suggested that your company might want to try to license the technology, or to retain someone to guide them in the technology. I'm concerned that without hands-on help you don't seem to be making much progress in this forum even over the course of many years :-(
But just to assure crystal clearness, have you have personally verified that these threads are being rolled after plating? And the plating didn't adhere at all regardless of whether you use a copper cyanide or a nickel strike, correct?
I don't know the normal approach in rolling the threads on plated grounding rods, but the general case for rolled threads is that the ends of the rod must be reduced to the mean diameter of the threads before rolling because otherwise there would be nowhere for the metal to flow. Are your ends reduced before plating? From these photos, it doesn't look like it, so I wonder if the case is that the dies thus allow no room for the plating so they must tear it off instead. What is the thread specification and what is the diameter of the rod ends before rolling the threads? Does the rod end diameter after plating match the mean diameter of the thread? Thanks!
Regards,
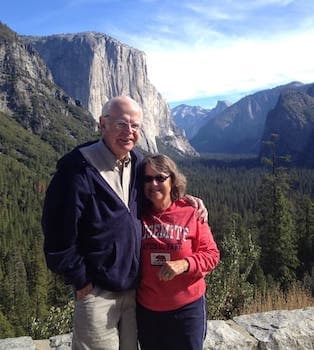
Ted Mooney, P.E. RET
Striving to live Aloha
(Ted can offer longterm or instant help)
finishing.com - Pine Beach, New Jersey
Q. Hello Ted,
I have got a similar problem as Rahul.
1. Unable to achieve threading after coating and
2. Uneven coating on the rods.
Our earth rods are horizontally placed in the tanks and are rolled physically by human by wearing gloves and putting his hands in the tank. So mostly the rolling of rods is not continuous and the rotations differ for each rod. I believe this is the reason for uneven coating. Because we have tried all other measures like shortening the distance between anodes.
Coming to the 1. Issue. The diameter of rods after coating is 17.2 mm and before coating is 16.7 mm. Mostly threading of 3/4" has to be done on it.
We are currently using roll press machine for threading.
If these two things can be solved. We will be able to satisfy our customers like you with the earthing products even better.
Can you help me with this sir?
- Vadodara India
February 1, 2018
A. Hi Tirath. We've moved from copper plating, which I know at least something about, to standard blank dimensions for thread rolling, which I know little about :-)
But even still, how can you be putting a 3/4" thread on a rod of .677" (17.2 mm) diameter? My very limited understanding of thread rolling from a few minutes of Googling, says that the blank diameter for rolling a 3/4-10 thread must be 0.689" ± .001". But again, I have no experience with this and I do see other suppliers claiming that their rod diameter is 17.2 mm as well. Please download some general info about thread rolling, get with your machining department, and try to resolve a chart with all the proper chamfering, blank grinding, and thread rolling dimensions. You probably need to talk with the supplier of the thread rolling machine for a deeper understanding -- perhaps special blank diameters are required for composite materials like copper plated steel; or perhaps different material of construction is required for the rolling dies when rolling soft materials like copper; or different speeds & pressures.
Sorry, you are out of my field with this, but some suppliers (www.amiableimpex.com/ground-rod-catalog/threaded-copper-clad-rod/Threaded-copper-clad-earth-rod.pdf ⇩) say they do the more advisable threading before plating :-(
Best of luck.
Regards,
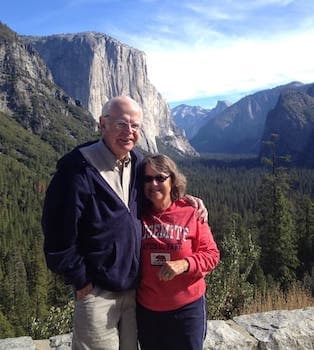
Ted Mooney, P.E. RET
Striving to live Aloha
(Ted can offer longterm or instant help)
finishing.com - Pine Beach, New Jersey
Ed. update: The above link is broken. Thankfully, the Internet Archive preserved a copy here
Please consider a donation to The Internet Archive.
Q. Hey Ted,
Thanks for investing your time in researching about the Roll threads and trying to help me with my question.
Mr. Ted, I have seen you posting several times about asking people to licensing the technology from Galvan Industries.
I would like to ask you if you know that Galvan Industries uses the same technique of threading on their plated products or not?
Also, I'm interested in hiring a consultant from the US to help me with this issue in my factory. Do you have anyone in mind who is willing to come to India and give consultancy in exchange of money?
Awaiting for your prompt response.
Thank you
- Vadodara, Gujarat, India
February 3, 2018
Ed. note: This RFQ is outdated, but technical replies are welcome, and readers are encouraged to post their own RFQs. But no public commercial suggestions please ( huh? why?).
A. Hi again Tirath. Yes, I have suggested that people from other continents see whether Galvan is interested in licensing their technology there because when I saw it many years ago I was very impressed by the economy of their very innovative approach to plating grounding rods.
Sorry, I have no idea how they thread them; my visit was years ago and threading wasn't of interest to me, but I wouldn't be able to comment on the subject if I had seen what they do. I do see in their published data though that their 3/4-10 threads are on .673"-.683" diameter rods, so I guess 17.2 mm rod diameter sounds right after all :-)
I don't travel anymore, but hopefully someone else will respond.
Regards,
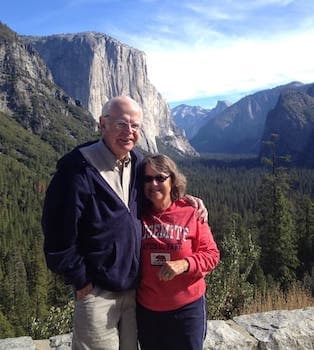
Ted Mooney, P.E. RET
Striving to live Aloha
(Ted can offer longterm or instant help)
finishing.com - Pine Beach, New Jersey
Q, A, or Comment on THIS thread -or- Start a NEW Thread