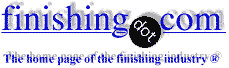
-----
Zincate formulas for plating on aluminum
Q. Hi All,
I wanted to ask the members here I'm trying to copper plate aluminum wires on an industrial scale. I wanted to ask how can I make zincate solution using zinc cyanide and caustic soda ⇦liquid caustic soda in bulk on
Amazon [affil link]
? How many grams of each to mix in water? And before zincating should I use kerosene oil to degrease the wires after heat treating them?
- Gujranwala, Pakistan
January 28, 2023
Treatment &
Finishing of
Aluminium and
Its Alloys"
by Wernick, Pinner
& Sheasby
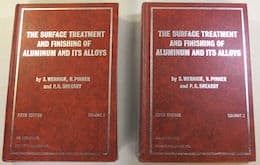
on eBay or Amazon
or AbeBooks
(affil link)
A. Hi Nash Shafique.
2nd question first because it's important; you shouldn't use flammable materials like kerosene to do the cleaning! The generally accepted way to clean aluminum is with a non-etching alkaline cleaner (with ultrasonic agitation added if it helps with the particular parts). If you can't buy a proprietary, and don't want to spend a great deal of time in research about inhibitors, you can see how a mild sodium hydroxide
[affil link] mixture works, but you must limit the immersion time.
Wernick, Pinner & Sheasby suggests that 23 g/l sodium carbonate
⇦ on
eBay or
Amazon]
and 23 g/l of trisodium phosphate
⇦ on
eBay
or
Amazon [affil link]
operated at 60-80 °C might be an adequate cleaner ⇨
Regarding the first question, yes 40-50 g/l zinc oxide
⇦ on
eBay or
Amazon [affil link]
and 400-450 g/l sodium hydroxide
[affil link] can be used. Ramanan Natarajan, in the earliest post in this thread apparently feels it can be improved by adding ferric chloride and Rochelle Salt
⇦ on
eBay
or
Amazon [affil link]
, and it seems that Wernick, Pinner & Sheasby ⇨
feel it's an improvement -- but only one of numerous possible ones ⇨
Ghulam Fareed offers a formulation further down this page.
If a library near you can get you the book I've been quoting, it's over 1200 pages and covers such subjects exhaustively.
We've certainly said this before, but please do your best to test each individual step before committing to it :-)
Luck & Regards,
Ted Mooney, P.E. RET
Striving to live Aloha
(Ted can offer longterm or instant help)
finishing.com - Pine Beach, New Jersey
⇦ Tip: Readers want to learn from your situation;
so some readers skip abstract questions.
Q. What's the best treatment before electroplating for aluminum?
making aluminum handles - Egypt
July 2, 2023
A. Hi Saed,
In brief: non-etch cleaning, etching, desmutting, zincating, a 1st layer of plating compatible with zincate, and final layers of plating.
Luck & Regards,
Ted Mooney, P.E. RET
Striving to live Aloha
(Ted can offer longterm or instant help)
finishing.com - Pine Beach, New Jersey
⇩ Related postings, oldest first ⇩
Q. Hi,
I'm trying to apply a layer of Zinc onto aluminum (3 microns thick; evaporated on Si wafers) using the Standard zincating solution (zinc oxide
⇦ on
eBay or
Amazon [affil link]
, sodium hydroxide
[affil link], ferric chloride
⇦ on
eBay or
Amazon [affil link] , and rochelle salt
⇦ on
eBay
or
Amazon [affil link]
). Before I do the zincating, I treat the aluminum surface in an acidic solution of chromic and phosphoric acid to remove the native oxide. Thus I have to move the Al surface from a highly acidic to a basic solution; this calls for a deionized water
[affil link] rinse in between. What are the chances that this DI water rinse will reoxidise the aluminum? Is there any other rinsing agent that I can use which won't oxidise the aluminum (like isopropyl alcohol
⇦ on
eBay or
Amazon [affil link] ?). Please give me your suggestions/comments.
Also, do you have any suggestions for reagents for native oxide removal in aluminum (commercial solutions, formulations, whatever) and process conditions for the optimization of the zincation (uniform and fine grained structure is my aim).
Thanks a lot,
Rensselaer Polytechnic Institute - Troy, New York
2000
Q. I am interested in wet (immersion) process that will allow deposition of thin (about one micron each) nickel and gold films on aluminum die individually. Zincating is the process that I have heard of, but how mature is this process? Is controlled cleaning/etching of aluminum a problem even if the aluminum is of high purity (sputtered)?
Is this process mature enough that it can be used at flip chip attachment?
Thanks
- Columbia, Maryland, USA
2001
Treatment &
Finishing of
Aluminium and
Its Alloys"
by Wernick, Pinner
& Sheasby
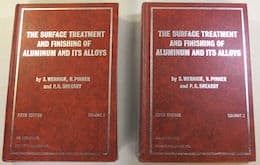
on eBay or Amazon
or AbeBooks
(affil link)
A. Hi Ramanan, hi Adarsh.
I am not experienced in zincating of evaporated thin films, but zincating of aluminum as a preparatory step to electroplating on aluminum is a very popular and mature industrial process, at least for large parts. Thousands of miles of aluminum bus bar has been zincated then copper plated; hundreds of thousands (maybe millions) of aluminum automobile and truck bumpers have been zincated then copper-nickel-chrome plated; tens of millions of aluminum die castings and electronic parts have been zincated then plated.
So a lot of research has been done. Here are some good papers by David Lashmore that focus on what is happening at the molecular level, and which may be helpful to your studies:
- "Immersion Deposit Pretreatments for Electroplating on Aluminium - Literature Review", Plating & Surface Finishing, Apr. 78.
- "Progress in Plating onto Aluminium", Plating & Surface Finishing, Jan 80.
- "Plating on Aluminium - A Review", Plating & Surface Finishing, June 85.
General conclusions seem to include the observations that:
- Proprietary mixed metal zincates (such as Macdermid/Canning/Gumm's Bondal) really do work better, and
-The common procedure of zincating followed by stripping with nitric acid and re-zincating (commonly called double zincating) is essential to a fine grained deposit on some types of aluminum.
As for pretreatment, the same steps used for anodizing and chromate conversion coating (clean, etch, de-smut) are fine. Your evaporated films may, of course, not sustain the robust pretreatment used in industrial electroplating onto aluminum.
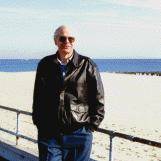
Ted Mooney, P.E.
Striving to live Aloha
(Ted can offer longterm or instant help)
finishing.com - Pine Beach, New Jersey
A. The use of zincate is well established as an adhesion layer for Al. Developed a process for plating Ni and Au on very thin films of Al on power devices using zincate as an activation layer. It was a technology used to fabricate flip chips
RP Daniel- Placentia, California
2001
Multiple threads merged: please forgive chronology errors and repetition 🙂
Uneven, Discolored Zincate Film
Q. I tried to put together a zincate solution prior to plating aluminum pads on an IC. I started from the suggested recipe from Electroless Plating by Mallory and Hadju, pg. 198:.
zinc oxide 50-100 g/L
potassium hydroxide 250-500 g/L (We currently don't have sodium hydroxide in stock)
Temperature 27 °C (80 °F)
Time: 1 minute
Resultant thickness ~ 3K
The die was first cleaned in a 1:1 HNO3:H2O solution and then immersion plated in a basket, the solution in a beaker [beakers on
eBay
or
Amazon [affil link] on a
⇦ on
eBay or
Amazon [affil link]
(the stir set to 200 RPM to keep the ZnO suspended).
The resultant zinc film was uneven and brownish in color. I then stripped it off in a 2:1 (H20:HNO3) etchant and repeated the process several times with similar results.
It has been recommended to purchase a proprietary zincate solution to avoid such roadblocks. Still any information on what may have gone astray would be appreciated.
Santa Barbara, California
2000
A. Yes, that formulation doesn't have much to recommend it, except that it won't violate any patents, and you did not have to ply a formulator with strong drink to get it:-0
Die castings will take an uneven zincate, due to the exposed grain structure, but you might want to try degreasing the part with an alkaline cleaner and aluminium etch for your next experiments. A blotchy zincate could mean that the part was dirty with grease or oil too.
Proprietary formulas will do a much better job.
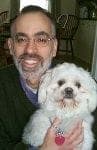

Tom Pullizzi
Falls Township, Pennsylvania
A. As Tom mentioned, your preplating process is not good enough. You need to degrease, etch and desmut before the zincate. Using only Hydroxide with zinc oxide will give you an unstable zincate layer. (By the way, you have to use a double zincate). A proprietary zincate will be far better.
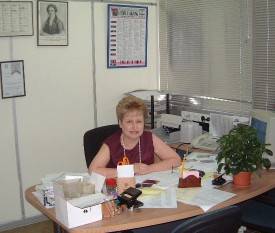

Sara Michaeli
Tel-Aviv-Yafo, Israel
A. Zincate is best double-dipped but not necessary. We have a great zincate that uses a combo of zinc, copper, nickel and iron. The advantage of so many complexes is that they can attach to different sites on the alloy. 5 to 1 ratio is best for your zinc to hydroxide formulation, but try to add 10% sodium cyanide, 5% nickel carbonate, 3% ferric chloride, 6% copper cyanide. That's the best the industry can offer and is very forgiving in its nature.
Regards and good luck
sandra
electroplating shop - toronto,canada
2003
Q. Would it be possible to put Sandra's Zincate makeup in form of a recipe, please? I did not quite get it.
I understand the initial recipe given in the first post, this is not a really good recipe, I would really like to try Sandra's, but do not understand it. Any help is greatly appreciated.
- Tallinn, Estonia
January 11, 2011
A. Hi, Renar.
We can't say when or if Sandra will return to clarify her response, but the Metal Finishing Guidebook offers this (strong) formulation:
NaOH 67 oz./gal
ZnO 13 oz./gal
FeCl.6H20 0.3 oz./gal.
Sodium Potassium Tartrate
⇦ on
eBay
or
Amazon [affil link]
1.3 oz. gal
So, combining this information with Sandra's, one way of following her suggestions would seem to be approximately:
NaOH 67 oz./gal
ZnO 13 oz./gal
FeCl.6H20 0.3 oz./gal.
NaCN 1.3 oz./gal
NiCO3 .6 oz./gal
CuCN 0.6 oz./gal
Please note that this is a very strong formulation, and it should be possible to very significantly reduce the NaOH and the ZnO as long as they are reduced proportionately, maintaining roughly a 5 to 1 ratio. Also note that this formulation includes cyanide and should not be used unless you are already familiar with cyanide-based processes and their dangers.
Regards,
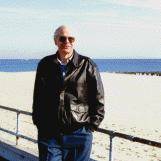
Ted Mooney, P.E.
Striving to live Aloha
(Ted can offer longterm or instant help)
finishing.com - Pine Beach, New Jersey
Multiple threads merged: please forgive chronology errors and repetition 🙂
Q. Hi,
Somebody tell me, what is the zincate formula for plating onto aluminum. I have now a formula like this:
caustic soda ⇦liquid caustic soda in bulk on
Amazon [affil link]
300 grs x liter zinc oxide 50 grs x liter.
That's all, but somebody in this forum wrote the formula is:
525 grs / liter caustic soda
100 grs / liter zinc oxide
1 gr / liter ferric chloride
10 gr / liter rochelle salt. Is this formula correct?
Thanks,
Rafael Arencibia- Caracas, Venezuela
2001
A. There are many different formulations that can be used to make-up a zincate solution. The two you have are good and there are many others depending on what alloy you are using and what you would like your adhesion to be like. You can get the various recipes from literature, books and the internet.
Angie Molnar- Fort Saskatchewan, Alberta, Canada
A. 1 - 245,100 L AGUA [water]
2 - 005,400 KG GLUCONATO DE SODIO [sodium gluconate] (DISSOLVINE NG C)
3 - 004,200 KG CLORETO FERRICO [ferric chloride
⇦ on
eBay or
Amazon [affil link] ]
4 - 138,000 KG SODA CAUSTICA [caustic soda ⇦liquid caustic soda in bulk on
Amazon [affil link]
] 99 / 98 % RAYON GRADE S/ CARB
5 - 020,400 KG OXIDO DE ZINCO [zinc oxide]
6 - 006,900 KG ACIDO SALICILICO [salicilic acid]
- RJ, BRASIL
Multiple threads merged: please forgive chronology errors and repetition 🙂
Cyanide Zincate
Q. Does anyone plate electroless nickel on aluminum who uses a cyanide zincate? Does cyanide zincate help with adhesion of the Nickel to the substrate?
Brandon Hellenbrand- Fairburn, Georgia, USA
2001
A. To call it a cyanide zincate is probably a bit of an overstatement. A zincate or alloy zincate that contains a trace amount of cyanide would be a much fairer answer. When I was actively in plating, I never came across a plater that did not say that it had better adhesion. Harder to control and it does require special haz waste procedures for that tank and rinses. Not all that difficult. Very few platers use it because a normal double zincate will suffice for nearly all work.
James Watts- Navarre, Florida
A. Yes cyanide zincate is used. I think there are non-cyanide zincates that have been developed. I don't know what process you use other than zincate and nitric acid to strip before copper strike/electroless nickel strike.
Bill Hemptech svc. w/ chemical supplier - Grand Rapids, Michigan
Q. Dear sir
I am working in plating area and I do plating on door handles and I need to make a zincate for plating aluminum articles. The formula I have is
to make a liter of zincate bath:
caustic soda ⇦liquid caustic soda in bulk on
Amazon [affil link]
525 g
zinc oxide 100 g
ferric chloride 31 g
rochelle salt 10
But this is not giving me a good result. Each time I do it, some of the door handles look very good and on some the plating comes off. Would you please tell me what I am doing wrong?
thank you for your help,
- Iran
2006
A. Hi Pari. We appended your inquiry to an earlier thread. Please see above, which will refer you to some excellent investigations about zincating. Good luck. Regards,
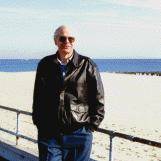
Ted Mooney, P.E.
Striving to live Aloha
(Ted can offer longterm or instant help)
finishing.com - Pine Beach, New Jersey
A. Ted, it's a bit difficult obtaining ca. 1980 issues of Plating & Surface Finishing.
Pari, common problems are 1) inadequate surface pretreatment and 2) too thick zincate (porous, traps liquid). ASTM B253, 'Standard Guide for Preparation of Aluminum Alloys for Electroplating' gives more information. It includes your zincate bath recipe, but with ferric chloride
⇦ on
eBay or
Amazon [affil link] hexahydrate at 1 g/L. It mentions problems associated with rinsing this high-NaOH bath; you may get better results with one of the more dilute formulae or a proprietary zincate.
- Goleta, California

Rest in peace, Ken. Thank you for your hard work which the finishing world, and we at finishing.com, continue to benefit from.
2006
Yes, old issues of P&SF can be hard to find at present, Ken, which greatly limits the value of my answer. But per the exec director's report at Sur/Fin, AESF is planning to put their old issues on line.
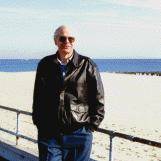
Ted Mooney, P.E.
Striving to live Aloha
(Ted can offer longterm or instant help)
finishing.com - Pine Beach, New Jersey
A. Formulation of zincate:
Sodium Hydroxide 400-500 gm/l
Sodium Cyanide 5-7 gm/l
Zinc Oxide 20 gm/l
Rochelle Salt 50 gm/l
Sodium Nitrate 1 gm/l
ferric chloride 2 gm/l
copper sulphate
⇦ on
eBay or
Amazon [affil link] 10-15 gm/l
- Lahore, Pakistan
February 22, 2011
Q. I have customer that needs aluminium articles tin plated as a bright decorative finish, we do tin plating on ferrous materials but have not done any aluminium materials.
Can anyone help me with a working procedure to do this and a zincate solution formula.
I would really appreciate some technical info.
Business owner - Pretoria, South Africa
2007
A. Proprietary zincate solution are usually considered better, and the technical support may be useful. For do-it-yourself solutions, see ASTM B253, 'Standard Guide for Preparation of Aluminum Alloys for Electroplating.'
Ken Vlach [deceased]- Goleta, California

Rest in peace, Ken. Thank you for your hard work which the finishing world, and we at finishing.com, continue to benefit from.
Q. Dear Sir,
While talking about zincating Cast aluminum, which type of zincating is recommended.
As there are two major types available, one is dual metal containing two metals mostly copper and zinc. While second one is quadra metal that is containing four metallic components with nickel as one of the ingredients.
Can you please provide guidelines for above. Does this have any bearing on final output.
Regards,
- Mumbai, India
January 8, 2014
Aluminum Activation For Electroless Nickel Plating
Q. We currently activate our aluminum for e-nickel(6061, 7075, & 2024) after cleaning by doing a standard double zincate (tri acid nitric zincate nitric zincate) with rinses in between and zincate dragout before entering zincate.
We struggle with consistently getting good e-nickel adhesion on aluminum panels. We get work out the door and I am convinced our operators just plate for 30 min max on panels to get them to pass, but any time I test at anything close to or over a mil they fail or are very inconsistent. You can do the AMS2404 bend test and they look good with minimal cracking but the minute you try to peel with a blade it comes right off.
I mainly suspect it is our zincate, its dump/maintenance schedule or our tri acid formulation.
Our zincate is a proprietary alloy zincate that we run to the TDS parameters but our supplier does not cover it any more. Are there any industry wide alloy zincates that may work better (Bondall I have heard of)? Or is there a heuristic I may be missing for the dump/maintenance schedule? How often, what to track (some sort of standard indication of the performance), only seed it 50% instead of fresh dump so as to mimic a "breaking it in" scenario?
Has anyone known a certain tri acid formulation to work better than others or specific ones for each alloy? Ours is about 90% nitric and the balance DI water with about 120 g/L ammonium bifluoride (no sulfuric which I find odd). We get a nice white look to the panels after it, so I assume it's good but sometimes when we remake it we start having issues.
Any and all advice is very much appreciated. And, I understand alkaline e-nickel strikes are recommended before going into a regular 4.9 pH high phos bath but I do not currently have that option.
- United States
September 16, 2019
A.
1. You do not need "tri-acid" for the wrought alloys you listed, just use plain nitric acid without the ABF.
2. Select a "dilute" zincate from any reputable supplier.
3. My experience has found no reason for double zincate.
4. Strike first in an alkaline electroless nickel, then rinse, dip in ammonia
⇦ on
eBay or
Amazon [affil link] rinse and go on into the acid electroless nickel. The expensive acid EN will last longer by not "seeing" the zinc, and the alkaline EN has far more tolerance for the zinc.
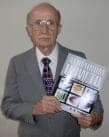
Robert H Probert
Robert H Probert Technical Services

Garner, North Carolina
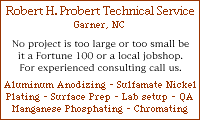
Q. Hi everyone. I just happen to have Hydrochloric Acid and Zinc Oxide powder. Can I make Zincate for Zinc plating from these?
dale sturdedvant- Chapala,Jal. Mexico
January 20, 2021
A. Hi Dale. We appended your inquiry to a thread which addresses most of your inquiry, except that the previous posters seemed more interested in zincate as an immersion pretreatment for aluminum rather than as a plating solution. Are you trying to make acid, cyanide, or alkaline non-cyanide plating solution? Are you a hobbyist or are you an experienced zinc plater and this is for production use?
Luck & Regards,
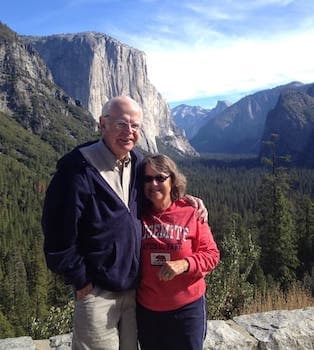
Ted Mooney, P.E. RET
Striving to live Aloha
(Ted can offer longterm or instant help)
finishing.com - Pine Beach, New Jersey
Q. Hi Ted. Absolute hobbyist. for now. I have done some research with google patents, looks like a sodium oxide, hydrogen peroxide and Ferric Acid with a little nickel thrown in is the current rage. Not sure about dip or electro. Want to Ni plate or coat, whatever is the best, Al roll flashing. I know "IMPOSSIBLE." Hasn't stopped me yet.
Need to apply a colorful decal, anodizing will change the colors plus Ni should be an eye catcher. Will try alkaline degreaser then caustic soda ⇦liquid caustic soda in bulk on Amazon [affil link] dip then phosphoric + Nitric de-smut and/or Oxalic acid de-smut. Read Oxalic does not remove Al, if any left, but does remove the Si alloy, the biggest problem, and I hope Cu et al. Will do the double zincate. I guess that makes me an immersion person. Or does it :]
Sure buying cyanide is a no go. Hope you can give me some expertise with my experiment. Thank you.
dale sturdedvant [returning]- chapala, Jal. Mexico
Q. Hey all, I just have a question.
what formula or products of the zincate that used to aluminum alloy? Especially alloy with zinc?
Thank you
- East java
January 27, 2021
A. Hi Muhtar. Numerous formulas are on this page we appended your question to, along with suggestions that proprietary zincates will probably outperform them. Good luck.
Regards,
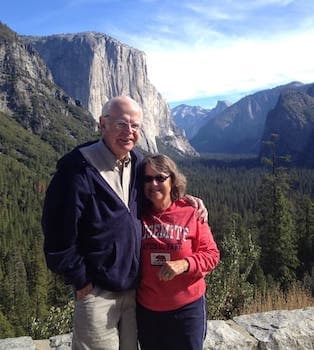
Ted Mooney, P.E. RET
Striving to live Aloha
(Ted can offer longterm or instant help)
finishing.com - Pine Beach, New Jersey
A. Old zincate formula according to Hewitson patent (1926.) -
1,000 water,
50 parts of zinc chloride,
150 parts of sodium hydroxide, and
40 parts of sodium silicate solution.
Hope it helps and good luck!
- Zagreb, Croatia
----
Ed. note: We have other threads about this general topic, including
0878, "Zincating of aluminum for plating & electroless nickel";
4074, "Zincating of aluminum- single or double & why?";
8041, "Q&As on Nickel Plating of Aluminum"; and
39909, "Plating Electroless Nickel on Aluminum Substrate".
Or search the site for many more.
Q, A, or Comment on THIS thread -or- Start a NEW Thread