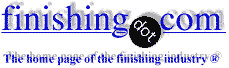
-----
Nickel plating / striking on stainless steel

Nickel plated stainless steel batteries getting pinholes
Q. Nickel plated stainless steel batteries getting pinholes
Hi,
We have button cell batteries with stainless steel substrate and nickel coating on top of them. And we, as end owners of the product, are coating batteries with 25 µm Parylene-C coating and a hydrophobic coating on top of Parylene. Our problem is we start seeing corrosion. Pinhole corrosion on battery surfaces. Batteries are provided by a really big battery manufacturer. And this battery manufacturer gets the battery caps from their sub-supplier.
Our problem is that we test batteries after the final coating. salt mist, temperature & humidity cycling in a cyclic way. We see corrosion suddenly, pinhole corrosion. What is strange is that some of the batteries have many corrosion sites on them and some have no corrosion indication - totally clean. And more interestingly, some corroded batteries have corrosion only on their top (-) cap surfaces but not on larger bottom (+) surfaces. We, in our site performed only coating of the batteries.
Analysis shows corrosion product as Nickel and chlorine. only chlorine is a contaminant. we cannot find any Na, K, Ca, S or any other chemicals -- but lots of chlorine. And this chlorine exists only at the corrosion sites but not on clean surfaces.
By the way, we did the analysis by moving the Parylene coating mechanically.
Our theory is cleaning failures may leave some chlorine -- bonded to nickel as metal salt and during the test, humidity dissolves these salts and creates aggressive electrolyte and local corrosion.
Our problem is that both battery manufacturers and battery caps supplier claim that they did not do anything wrong and they've done this business for many years.
We asked if the battery cups were from the same batch or a different batch which may help to explain why some corrode and some did not, but we have been told that they are from the same batch (but there is no registration).
I want to ask the experts if any have any idea what could be the origin of the chloride we see. Does anyone have a similar experience?
Thanks a lot, in advance
Failure analysis - Berlin
January 18, 2023
A. My initial thoughts are that the nickel plating is not thick enough and the sodium chloride testing "mist" is getting thru to the stainless steel,.
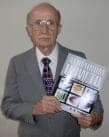
Robert H Probert
Robert H Probert Technical Services

Garner, North Carolina
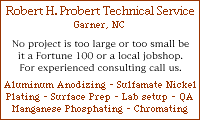
A. Hi Kse
In addition to Robert's comment, I have two additional thoughts.
• Is there any chance that some of these parts are occasionally vapor degreased? A vapor degreaser with old solvent can be a very aggressive chloride based acid.
• Have you considered having the testing done by a backup lab? Salt spray test results sometimes vary very widely from one testing lab to another, perhaps because one of them is doing something wrong.
Luck & Regards,
Ted Mooney, P.E. RET
Striving to live Aloha
(Ted can offer longterm or instant help)
finishing.com - Pine Beach, New Jersey
Q. Hi Robert and Ted
Ni-plating is only 0.9 mu, it is for solderability sake, but not corrosion protection, for battery connections. Stainless steel 316 is difficult to solder battery springs onto.
There is a long chain for the failure arise.
We as a last user, only use plasma cleaning and perform a thick parylene coating.
Salt mist test is a part of our classic test chain.
We are using the same test procedures for years without experiencing similar problem.
Additionally, we have different brands batteries which are also parylene coated and they do not fail in test.
We have a battery provider - assembly house in Europe.
This battery assembly house has battery cap and nickel plating house in east Asia.
My thought was, chlorine introduced into structure during steel surface activation prior to playing or during electrolytic plating where Nickel chloride (probably) is used.
BR
- Berlin
January 21, 2023
A. For plating Nickel on Stainless steel - almost for sure "Woods" Ni strike is used (mix of Ni Chloride with Hydrochloric acid).
Maybe the whole Ni layer is plated from the Chloride bath. However Chlorides should not stay on the part, unless it was no/bad rinsing and no neutralization after the plating.
- Winnipeg, CANADA
January 24, 2023
Q. Hi Leon,
Thanks a lot for the answer.
I am also thinking in a similar way for this reason.
Do you have any idea how to verify the hypothesis? Any test methodology or analysis technique?
Thanks in advance
BR
Yks
- Berlin
January 30, 2023
Q. Strike nickel bath installation and ss metal nickel plating process.
Nanaso shivaji kodag- Mumbai, India
July 11, 2023
privately respond to this RFQ
Ed. note: As always, gentle readers: technical replies in public and commercial replies in private please (huh? why?)
A. Hi Nanaso.
Your question is very broad, and I don't think anyone can fully answer it in the few paragraphs appropriate to a public forum ... but the overall thrust of the subject is that stainless steel very quickly grows an oxidized surface, and plating cannot properly be done on top of that oxide, or the adhesion will be very poor.
So it is usual to do a nickel strike, usually a "Wood's Nickel Strike" as the first plating layer. This operation is very similar to regular nickel plating, but it uses a plating solution with a lot of strong acid and a low concentration of nickel at about double the usual amperage of nickel plating, that simultaneously dissolves that oxide on the stainless steel while depositing a very thin layer of nickel plating in its place. Other plating can then be done on this nickel layer.
You can search the site for countless threads on the subject of nickel striking, and Jack Dini's Electrodeposition
[on
Amazon
or
on AbeBooks affil links] has a good chapter titled "Adhesion" which explains this subject a bit further, while Crotty & Probert's "The Sulfamate Nickel How-To Guide" ⇨
offers some practical advice on both the Wood's Nickel Strike (they call it the 'all-chloride' strike, but I knew Donald Wood and will continue to honor his contribution to the subject), and an alternative sulphamate nickel strike.
Luck & Regards,
Ted Mooney, P.E. RET
Striving to live Aloha
(Ted can offer longterm or instant help)
finishing.com - Pine Beach, New Jersey
⇩ Related postings, oldest first ⇩
Q. My supplier in Far East told me that stainless steel is very difficult to be coated with nickel. The stainless steel part we need to plate is SUS304 and is used in battery door as a charge contact. The supplier claimed that the failure rate of plating is about 30%, which is unbelievably high. I am wondering what is the best plating process for nickel plating stainless steel. Is it necessary to insert Nickel strike step?
Thanks in advance for the help.
Consumer products - Kansas City, Missouri
2005
by Jack Dini
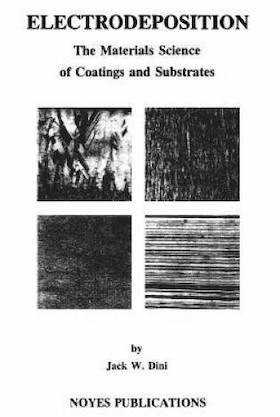
on eBay or Amazon
or AbeBooks
(affil link)
A. Hi E.J. Yes, stainless steel definitely requires a preplate sequence which includes a nickel strike. The very best treatment of that subject is in Jack Dini's book, "Electrodeposition ..." ⇨
Yes, 30% is a ludicrously high reject rate; but it is believable, because when a plating process is done wrong, there is no upper limit on the percentage of rejects.
I don't know how you can afford your parts being a learning experience for a plating shop 12,000 miles away which makes excuses for their incompetence when there are surely shops right in the Kansas City area who can deliver a 99.9%+ pass rate on those parts tomorrow morning :-)
Ted Mooney, P.E.
Striving to live Aloha
(Ted can offer longterm or instant help)
finishing.com - Pine Beach, New Jersey
Q. Can you please tell me what is "Nickel strike"?
V. Ranga Bhuvana Balaji- India
2005
A. You need a high chloride bath Nickel Wood's Nickel
Range Optimal
Contents: Nickel 80- 96 gr/lt, 88 gr/lt
Nickel Chloride 420-467 gr/lt, 434 gr/lt
Chlorhidric Acid 70- 82 gr/lt, 75 gr/lt
3 to 5 volts
I hope this can help you.
Regards,
- Toluca, Mexico
A. Wood's nickel is the most popular. It consists of a highly acidic, low efficiency, all chloride nickel solution prepared with 250 g/L nickel chloride, 250 mL/L conc. HCl, rest DI water. Operated at room temp, 20-100 a/sq-dm, anodes pure nickel.
Guillermo MarrufoMonterrey, NL, Mexico
A. If you have to ask this question, you really need a good reference book on plating.
A nickel strike is a very thin coat of a nickel that will stick to stainless that has been properly cleaned and activated. Typically a Wood's Strike is used. It is a very high chloride bath at a very low pH that plates very slowly and is extremely highly compressive stressed, so you only want enough of a coat to barely give a "color".
- Navarre, Florida
A. Are you rack plating or barrel plating? If you are barrel plating be sure to have good pump agitation as well as a slightly higher HCl concentration. Stainless Steel is not as tricky as some would make it seem. Also try to remember that a Ni strike normally requires a higher current to strike parts. Consider covering surface of your bath with plastic balls, available from plating supply companies, to reduce surface fumes. Good luck!
Regards,
- Methuen, Massachusetts
Q. What happens to the rejects? Can the same steel be "cleaned" and re-plated?
Paulina Natera- Westlake Village, California
2006
A. Hello, Paulina. It's not clear to me if you are following up on E.J.'s question. In general, nickel can be stripped from steel relatively easily, but not as easily from stainless steel because they are somewhat similar. In this case, unless it lacks adhesion, it is more common to try to reactivate the nickel than to strip it.
Good luck.
Ted Mooney, P.E.
Striving to live Aloha
(Ted can offer longterm or instant help)
finishing.com - Pine Beach, New Jersey
Q. I understand Stainless Steel is a tricky material to plate with Nickel followed by Cadmium. Does surface preparation matter? E.g., which is better: sand-blasted surface or vibro-finished surface? And what time lapse permitted after above finishing and before plating ?
B Pramod- Landewadi, India
October 3, 2009
A. Hi, B. In electroplating, the adhesion is molecular, not based on mechanical "keying" as in painting. So either sand blasting or vibro-finishing can be used, depending on what you want the surface to look like.
If sandblasting is practical and convenient for your parts, it's ideal, but you still need the Wood's Nickel Strike before the nickel plating and cadmium plating.
The allowable time lapse depends on your handling and your intentions. For example, if you are going to immediately plate, sandblasting is the only prep you may need before the nickel strike. But if the parts are going to hang around for a couple of days, you will need to alkaline clean them and acid activate them immediately before the nickel strike. The best approach is surely to plate immediately after blasting. Good luck.
Regards,
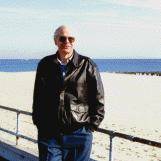
Ted Mooney, P.E.
Striving to live Aloha
(Ted can offer longterm or instant help)
finishing.com - Pine Beach, New Jersey
Q. SIR, PLATING PEELS OFF WHEN WE DO NICKEL ON SS AND THIS LAYER IS FOLLOWED BY 2N FLASH GOLD
MANNU SHARMA- solan h.p. India
July 7, 2011
A. Hi, Mannu. When you say nickel on stainless, it isn't clear that you are applying a Wood's Nickel Strike as explained above. Please give full composition and plating conditions of the nickel strike you are trying to apply. Thanks! Jack Dini's "Electrodeposition" has an excellent chapter labeled 'Adhesion' which gives adhesion values for various approaches to nickel striking stainless steel.
Please check it out. Good luck.
Regards,
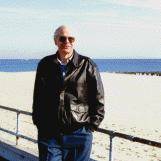
Ted Mooney, P.E.
Striving to live Aloha
(Ted can offer longterm or instant help)
finishing.com - Pine Beach, New Jersey
Q. Sir
We are doing nickel strike on the component and then bright nickel and then 2N flash gold. But after complete process gold plating peels off. Base material is ss.
- solan h.p. India
A. Hi again.
If it's the gold plating peeling off of the nickel plating, rather than all of the plating peeling off, then probably you are either waiting too long to begin the gold plating (you should quickly rinse the nickel, then immediately go into the gold plating bath) or there is an excess of brighteners in the bright nickel plating. Good luck.
Regards,
Ted Mooney, P.E.
Striving to live Aloha
(Ted can offer longterm or instant help)
finishing.com - Pine Beach, New Jersey
Q. Hello, I have a fundamental questions: why put nickel on stainless steel? (Only for appearance?). Is there somewhere a chart with values of nickel adhesion on stainless steel obtained in a test on flat surface with a specific device like nano-indenter? What value should it be?
I would like to ask if you could recommend me some basic/fundamental source (article, book) where I could find something solid about nickel plating adhesion on stainless steel (values). I read a chapter Jack Dini's "Electrodeposition" but it does not explain the basics like why put nickel on stainless steel. Could you recommend something?
- Lodz, Poland
January 26, 2013
by Jack Dini
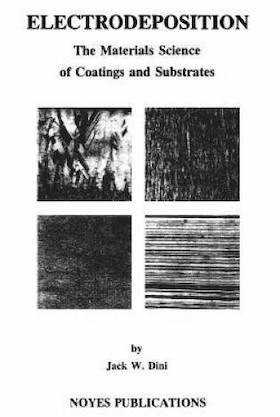
on eBay or Amazon
or AbeBooks
(affil link)
A. Hi Jurek. We appended your inquiry to a thread which implies the answer: Electroplating must be done on bare metal (not tarnish or oxides) for proper adhesion, but stainless steel instantly forms a passive oxide on its surface which prevents that proper adhesion. The most popular way of addressing that problem is to start with a Wood's nickel strike or other nickel strike. Being highly acidic, it dissolves the oxide, while simultaneously applying a thin layer of nickel plating to the bare stainless steel. The book by Jack Dini that you referenced.
is excellent once you understand that the chapter in question is titled "Adhesion", and it's all about the best procedures for getting good adhesion onto stainless steel with a nickel strike.
Regards,
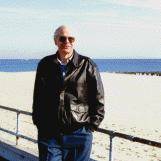
Ted Mooney, P.E.
Striving to live Aloha
(Ted can offer longterm or instant help)
finishing.com - Pine Beach, New Jersey
Q. Hello,
Why put nickel coating on stainless steel? Better corrosion resistance? Better adhesion of solder to nickel than to steel? So why do it? Not how, this I already know.
Best regards,
- Lodz, Poland
April 4, 2013
A. Hi Jurek. The short answer is, of course, that stainless steel is nickel plated when the surface properties of nickel are better suited for the application in question. If you search this site for "nickel plating stainless", you will see a number of applications discussed. For example, nickel will have much better surface conductivity and will be a much better electrical contact than stainless steel; also, as you suggest, it will be more readily solderable; it may be more corrosion resistant in certain environments. Also, the nickel plating may be necessary before other types of plating like gold plating can be done on the stainless steel. But it's not possible to list or predict every possible application where the surface properties of nickel would be more desirable than those of stainless steel. Good luck.
Regards,
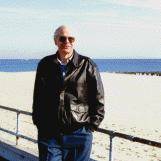
Ted Mooney, P.E.
Striving to live Aloha
(Ted can offer longterm or instant help)
finishing.com - Pine Beach, New Jersey
Q. Hello, we are having problems with adhesion on stainless steel. We run a Zinc Nickel bath with no brighteners and nickel strike all stainless steel parts before plating. What are the components of a good nickel strike bath for a barrel process? Please include volts, amps, and processing time. Thank you.
Asa Sanders- North Richland Hills, Texas USA
March 14, 2013
A. Hi Asa,
You can find formulations for nickel strike in any decent text book on plating, such as the Electroplating Engineering Handbook ⇦ this on
eBay,
AbeBooks, or
Amazon [affil link]
, the Canning Handbook [on
eBay,
Amazon,
AbeBooks affil links] and the Metal Finishing Guidebook. These include formulations, temperatures, voltages, etc.
It sounds like you have to go back a bit further than the nickel strike to start your investigation.
Firstly look at your degreasing and cleaning process, are you getting a water-break free surface? Yes - good, No - time to investigate your cleaning process.
Secondly look at your etching process prior to nickel strike. Are you using one? For stainless steels I would highly recommend it as the steel will have a naturally passive layer on it that needs removing before plating.
Next it is important that you do not delay from nickel strike to the plating tank. From nickel strike you need to rinse and be in the Zn/Ni tank within 2 minutes. Any longer and you'll end up with a passive nickel strike.
That should get you started down the right road to a robust process.
Aerospace - Yeovil, Somerset, UK
Q. We are activating the parts before nickel strike in HCl for 2-5 minutes. We have already looked at our degreasing process and are good. We also get the parts into the strike within 2 minutes. We are only getting .8 to 3.2 microinches of nickel on the parts in 8 - 10 minutes. Is this enough for our barrel process?
Thank you.
- North Richland Hills, Texas, USA
A. Hi Asa,
A couple more questions:
Do you know if the plating is failing between the base materials and the nickel strike, or is it failing between the nickel strike and the Zn/Ni plating?
If you find that it is failing between the base material and the nickel strike it indicates either a problem with the nickel strike or the pre-cleaning.
If it is failing between the nickel strike and the plating then it may be the nickel layer going passive or you may have a problem with the Zn/Ni plating process.
The nickel strike is designed to give a very thin, adhesion promoting coating on the surface of the base material. I must admit I have never checked the thickness of the nickel strike, but it would certainly be less than a micron, so I would guess the thickness is probably in the right ballpark.
If the nickel strike is acting unpredictably it could be due to a build up of tramp metals in the tank (usually copper and/or iron). You can do one of two things about that, either dummy out the metals (large surface area cathode, low current density) or dump and re-make the tank.
Aerospace - Yeovil, Somerset, UK
We actually found the problem when we dumped the tank, there was a clamp at the bottom and had corroded away depositing iron to the metal. I thank you for all your help, it was much needed.
- North Richland Hills, Texas, USA
Q. We have been trying to do nickel strike on stainless steel boxes . . .
We have done strike nickel on other materials and we have been successful but we have failed to do strike nickel on these boxes. We are using degreasers properly, the rectifier is set at 8 volts and the boxes are put into the chloride tank for at least 4 minutes but the minute we remove it the box is a little black and the nickel is not catching the box. I hope you could help me with this.
Best Regards,
- Dubai, UAE
July 25, 2013
? You left out a lot of importance. What is your strike chemistry. Have you checked for tramp metals in solution. What are your anodes. Are the bags clean. What is the parent metal, not just SS. What is your agitation. What is your anode to cathode ratio? Tank temp. Exact pre-plate cycle (all of it)
James Watts- Navarre, Florida
Coating inside a channel
Q. Hello,
I have a metal part with a channel inside (2 mm diameter of the channel). I wonder if the Ni coating would be or could be thinner inside this channel?
Another question is if the coating could be too thick? Does the higher thickness influence adversely the adhesion of a coating?
Best regards,
Jurek
- Lodz, Poland
September 29, 2013
A. Hi Jurek. The nickel plating deposits in proportion to the current flowing to the particular area (see Faraday's Law of Electrolysis). And the current flows in accordance with Ohm's Law (the greater the resistance, the lower the current flow). And the resistance between the anodes and points inside that 2 mm channel is very high compared to the resistance to points on the exterior. So little if any current will flow and little if any nickel will deposit.
Within reasonable limits of thickness the adhesion will not be determined by the thickness. Good luck.
Regards,
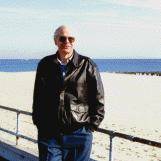
Ted Mooney, P.E.
Striving to live Aloha
(Ted can offer longterm or instant help)
finishing.com - Pine Beach, New Jersey
(you are on the 1st page) Next page >
Q, A, or Comment on THIS thread -or- Start a NEW Thread