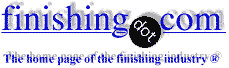
-----
Manganese phosphate coating: issues and answers

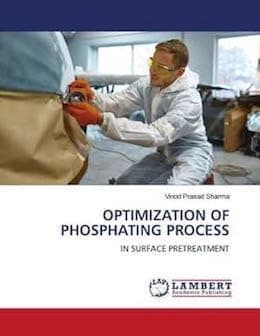
avail from AbeBooks, or Amazon
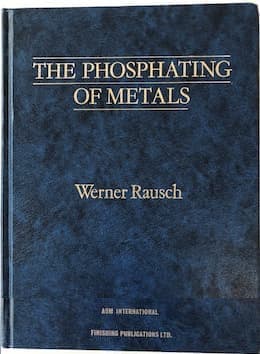
avail from eBay, AbeBooks, or Amazon
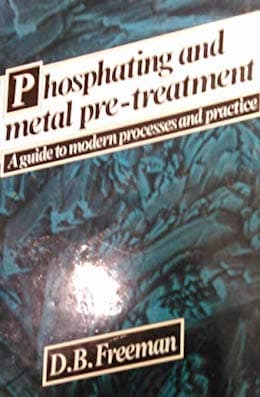
avail from eBay, AbeBooks, or Amazon
(as an Amazon Associate & eBay Partner, we earn from qualifying purchases)
Q. Hi, I work in a manufacturing plant that does manganese phosphating. I see you offered to connect a few dots in this long thread for someone who was having problems with white and grey dots on their phosphate. Wondering if you still had those links jumbled together if you would be willing to share them. Also, not to bother you but if there was some way I could contact you more efficiently if you had the time. I would much appreciate it.
Walker Johnson- South Carolina
July 25, 2023
A. Hi Walker.
Of the general metal finishing texts The Canning Handbook [on
eBay,
Amazon,
AbeBooks affil links] has quite good coverage of manganese phosphatizing, as does ASM Metals Handbook Vol. 5 ⇦ this on
eBay,
Amazon,
AbeBooks [affil link]
.
If you search the site and can't find the specific links you think you saw, or if what you see isn't fully applicable, you are always welcome to post your own questions -- that's the principal thing that this site is about.
It is best to explain what you are doing, what kind of parts are involved, and what the problem issues are. Photos can be e-mailed to mooney@finishing.com for posting with your questions.
Finishing.com doesn't offer private consulting services, but our Consultants Directory does list some people who may be able to help you privately. Best of luck!
Regards,
Ted Mooney, P.E. RET
Striving to live Aloha
(Ted can offer longterm or instant help)
finishing.com - Pine Beach, New Jersey
Q. Good Morning,
We are facing two issues after our manganese phosphate process.
1. Parts have a blotchy appearance. Variation of light and dark grey across the surface. It's inconsistent and not on every part.
2.Parts appear green. It appears to only be at the surface level.
Prior to phosphate, the parts go through a chromic acid rinse
Parts are made from HNV3 and are investment cast. After casting, they are machined and have an internal bore that is chrome plated. The visual inconsistencies only show on the surface.
Any input would be greatly appreciated. I am by no means an expert but would like opinions on what could be the root cause as I continue to investigate.
Quality Engineer - Columbia South Carolina
April 22, 2024
A. Hi Cameron,
It is quite common for phosphated parts to go through a chromic acid rinse post phosphating. Might there be a typo in your process description regarding "prior to"?
Is this a new issue that has arisen in a process that was formerly quite successful, or is there no real history of satisfactory processing to this sequence? ... phosphating of stainless steel is a problem requiring special formulations because the phosphatization reaction occurs in response to a reaction of the metal to the solution and stainless responds differently than steel, so the reaction works differently.
Hopefully a reader with actual experience in manganese phosphatization of chrome plated or chrome rinsed HNV3 parts will respond because it is hard to extrapolate from theory whether the chrome is affecting the phosphate, and it's difficult to demonstrate/prove that it is the problem. But lacking that for now:
Are the chrome plated internal bores masked/capped for phosphatization?
If you are equipped to do so, it probably would be quite informative to analyze your phosphatizing solution for chrome content -- chrome is often troublesome to other processes. If there is no chrome in the solution, and the components are not super expensive, you could take a few and either not chrome plate them or strip the chromium in hydrochloric acid to test the result.
Luck & Regards,
Ted Mooney, P.E. RET
Striving to live Aloha
(Ted can offer longterm or instant help)
finishing.com - Pine Beach, New Jersey
⇩ Related postings, oldest first ⇩
We use a casting of CH13 (hot worked tool steel investment casting)for our component making. This casting undergoes heat treatment (spherodising, machining, gas carburising, hardening and tempering, Hardness = 60 HRC) followed by sand blasting for surface cleaning.
While performing manganese phosphating, we find white patches. We are looking for a uniform black colour. Can someone help to avoid white patches. Phosphating is followed by tectyl 272 oiling. Corrosion test (as per ASTM B117 on the component with white patches show a good corrosion resistance.
G R PatelManufacturer, Power Equipments - Vadodara, Gujarat, India
2004
Q. I would like to get a recipe for a manganese phosphate coating for steel. If someone perhaps can explain to me the actual chemical actions taking place on the surface too?
I've learned that there are many applications such as:
1 high wear resistance
2 better resistance against corrosion and a nice finish and
3 as a pre-treatment for painting etc.
Is there a big difference in the recipe and chemicals? The one I'm most interested in is protection against corrosion and finish.
Thanks
hobbyist - Kesteren, Netherlands
2005
A. You can use next solution:
25 gm phosphoric acid
1,5 gm manganese dioxide
1 lit water
Boil your objects 2-4 hours.
you must oil, lacquer or wax it!
(according to Angier: Firearm Blueing and Browning [on
eBay ,
Amazon,
AbeBooks affil links]
)
- Cerovski vrh Croatia
A. Jan Van Velde
Manganese phosphating formulations contains basically a manganese salt, phosphoric acid and an accelerator. Deposition of manganese phosphate coating is normally performed at very high temperatures of the order of 95 °C for a period of 30-60 minutes.
It is a conversion coating process and involves the dissolution of the base metal which subsequently forms part of the coating. In manganese phosphate coating the species that deposits on steel is manganese iron phosphate and hence requires a large amount of metal dissolution so that the formation of manganese iron phosphate is possible. This is the reason for the requirement of high operating temperature and higher processing time.
Manganese phosphate coating offers good wear resistance. It can retain oil and lubricants and improves the scuffing resistance. Manganese phosphate coating with higher coating weight offers good corrosion resistance. Impregnation with oil further improves the corrosion resistance.
Zinc phosphate coating is mainly recommended as pretreatment coating for painting.
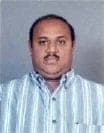
T.S.N. Sankara Narayanan
- Chennai, Tamilnadu, India
(ed.note: The good doctor offers a fascinating blog, "Advancement in Science" )
Heaters get sludged, then damaged
Q. My company conducts manganese phosphate coating on carbon steel pipe. We use heating elements to heat the bath where the pipe coating is carried out. The problem is after the coating maybe for a week the heating element is covered by sludge. The workers usually remove the sludge from the heating element by hammer (mechanical). It doesn't only remove sludge but also cause damage to the heating element (made from stainless steel). So: how to remove the sludge without causing damage to the heating element ?
Dodi Syafardi- Cilegon, Banten, Indonesia
2005
A. Hi Dodi. Two quick notes: heaters should be electropolished stainless steel because this surface has no "tooth" at all and will minimize build-up and make cleaning easier. Oversized (derated) heaters or coils should be used because the smaller the heater, the higher the required surface temperature, which accelerates the sludging.
Topics 114/65 "Sludge buildup on heating coils in phosphating tank" and 51/42
"Materials for zinc phosphating tank" address this issue in some depth. Patient use of our search engine will uncover still more tips on this subject. Good luck.
Regards,
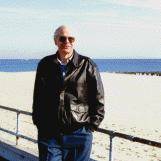
Ted Mooney, P.E.
Striving to live Aloha
(Ted can offer longterm or instant help)
finishing.com - Pine Beach, New Jersey
A. Dodi Syafardi
for exterior coating & if the ends of pipe are open then for interior coating, you may use glass heaters of required wattage and in required number.
- Bhiwadi, Alwar, Rajasthan, India
December 6, 2011
How do I formulate a manganese phosphate bath?
Q. Hello,
I am looking after a Manganese Phosphating line in our company where cast iron components are coated. The phosphating bath concentrate is currently being outsourced and I am not aware of the contents of it.
I am trying to prepare a bath myself using MnO2 [1.5g/L] and H3PO4 [25g/L] and topping the rest with tap water. The problem is I'm not sure what other chemicals to be added (like accelerator, stabilizers etc) and also in what ratio. I also tried measuring the TA & FA values of the above mentioned bath and found them to be 35 & 17.4 respectively. Thus the TA/FA ration is close to 2. But I have read that it should be between 4 ~ 6. Kindly let me know how to improve the ratio.
Alternatively, It would be a great help if anyone can suggest me the method of preparing a Manganese Phosphating Bath and the chemicals required to prepare it in proper ratios.
Plating shop - Shimoga, Karnataka, India
October 1, 2010
Q. Dear sir
We are also facing the white patches after manganese phosphating. Can anyone suggest the same for better control?
- Bangalore, India
April 9, 2012
Q. We have a situation where two pieces of gun steel were Ion Nitrided in an ammonia
⇦ on
eBay or
Amazon [affil link] rich environment. Sample I was Nitrided at a High Temp (still 100 degrees lower than tempering temp) for a short time and Sample II was nitrided at a low temp for a long time. Both samples were subsequently sandblasted with 140 grit alumina then Mn Phosphated (using a conditioner and hex chrome rinse solutions). Sample I has very little Mn Phosphate, very gray in color, and looks terrible in general (in the nitrided and un nitrided sections of the sample) where Sample II looks very typical black coating in nitrided and un-nitrided sections of the sample.
I have been told that this will always happen but not given a good reason as to why (from my experience the only thing that would impact the ability to produce a good coating would be a layer of non-ferrous material/contaminant). Both samples were examined under a 1000X magnification (we hope to view it under SEM technology soon) and can not see any visible layers/differences/heat affected zones/etc. in the base metals. Does anyone out there have a "oh yeah knucklehead it's this" explanation?
Engineer - Watervliet, New York
January 23, 2014
A. The 2nd most frequent problem with Mn Phos is the absence of a "grain refiner" which I guess you covered with what you call a "conditioner". The first most frequent problem is the total/free ratio. You must adjust this ratio, preferably at the tank side, immediately before inserting the parts. If you check the T/F ratio on Monday and phosphate on Tuesday the ratio is too high, add manganous phosphate until you bring it into proper limits, then immediately phosphate.
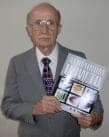
Robert H Probert
Robert H Probert Technical Services

Garner, North Carolina
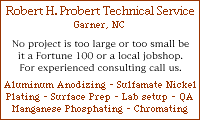
Q. Hello sir, we are doing manganese phosphating on 4130, 4140, 4330 steel parts. It's a new plant we have installed, am not able to standardize the process; I face problems like uneven coating surface, carbon coming out of the surface after phosphating, uncoated areas.
I have failed to do the pre cleaning properly; please suggest a best process for pre-cleaning, and my chemical supplier only supplies the phosphating chemical; please suggest how to overcome these problems? My process is degreasing, water rinse, 5% H2SO4 rinse, water rinse, hot water rinse and phosphating; free acid 6, total acid 31, ferrous ion 1gm/ltr, temp. 90 to 95.,
oil and gas equipment manufacturers - Dubai, UAE
January 27, 2014
A. You must adjust the T/F immediately prior to putting the parts into the solution. For the 4000's series steels you must use a grain refiner. If you supplier dos not have one, then change suppliers.
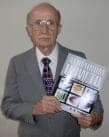
Robert H Probert
Robert H Probert Technical Services

Garner, North Carolina
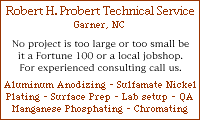
A. Hi Prakash,
After degreasing, whether solvent based or aqueous based I would have an aqueous cleaning step (may sound odd, but the second stage cleaning really does help to get parts really clean). Do a water break check after rinsing to ensure you have an unbroken film of water on the parts, if not then repeat the cleaning process until you get a water break free surface.
Make sure you control the etch, don't over-etch, ensure you chemical analysis is OK and use as short a time as possible to obtain the etch required.
Grain refiners are a good idea to obtain even consistent phosphate crystal formation on your parts. As Robert says, your phosphate solution supplier should have a refiner available.
And I can't emphasise strongly enough that you need to keep the phosphate chemistry under control. Dependent on the level of use I would expect a minimum of twice a day analysis for free acid, total acid and iron, if this doesn't keep the solution under control then increase the frequency. If may be as Robert pointed out that you may need to do the analysis for each bath load, although that would indicate to me you have something else in your phosphate system upsetting the chemistry.
Aerospace - Yeovil, Somerset, UK
Thank you very much sirs, I am getting good results, maintaining the free and total acid in correct ratio, and improved water rinses, and getting good results.
- Dubai , uae
How to computer control Manganese Phosphate process
Q. Hello to all!
We are zinc and manganese phosphate plating company. Demand on Mn Phosphate coatings are rising, therefore also the demand for quality of our service. My question is: how should we make the process more computer controlled to eliminate the human error factor?
Currently we are controlling the temperature automatically with thermocouples, but pH, concentration and acid radio is measured by hand and with analysis.
What are the options for computer control of Mn Phosphate bath?
Second thing, how would you guys hang bush of dimensions 30 mm dia. x20mm for Mn Phosphating, to minimize contact marks? Both sides of bush are smooth finished.
Thanks in advance
- Krsko, Slovenia
March 7, 2014
How to Manganese Phosphate the component without any dimensional reduction
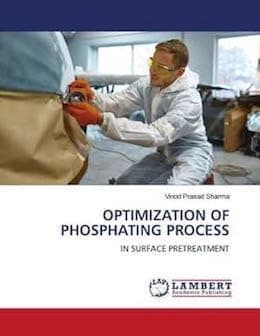
avail from AbeBooks, or Amazon
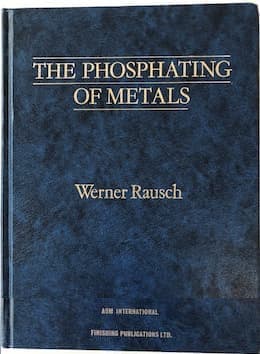
avail from eBay, AbeBooks, or Amazon
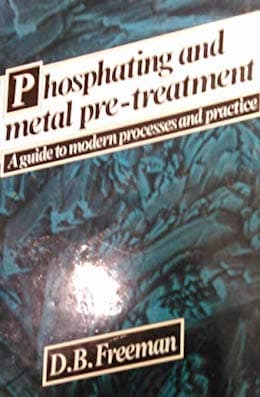
avail from eBay, AbeBooks, or Amazon
(as an Amazon Associate & eBay Partner, we earn from qualifying purchases)
Q. How to Manganese Phosphate the component without any dimensional reduction to the base metal of grinding surface?
Required coating thickness is only 5 to 7 microns.
- Pune, Maharashtra, INDIA
July 20, 2014
A. Hi cousin Ajay. It is not possible to do phosphating without any dimensional reduction because, per John Donofrio in the Metal Finishing Guidebook, "The first reaction that occurs ... is the pickling reaction, which will dissolve some metal from the surface. On steel ... the pickling rate is in the range of 1-3 g/m2 of surface area treated ... This pickling reaction is essential for the coating formation ...". But if you run the numbers, this is very little metal -- well under a micron. Are you implying that your present manganese phosphating process is attacking the base metal? If so, there is surely something wrong.
Please do your best to describe your situation and your own findings from it so we can have an enthusiastic discussion of it here. Abstract questions can rarely garner anything but general guidelines; and there's little real value in our extracting these general guidelines from phosphating texts for you, when the first thing we're certainly going to say is that you should have the texts on hand yourself :-)
Luck and Regards,
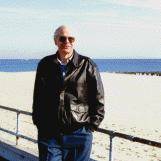
Ted Mooney, P.E.
Striving to live Aloha
(Ted can offer longterm or instant help)
finishing.com - Pine Beach, New Jersey
Manganese phosphate is not adhering to steel -- it rubs off
Q. I was doing manganese phosphate on AISI4145 steel metal. After some pieces it is failing adhesion test (phosphate layer is removed). Can anyone tell why this happens?
The bath preparation is underground tank and heating coil is used to reach temperature required of 90 °C.
- Mussafah, Abudhabi, U A E
July 28, 2014
A. The part cleaning to be rechecked. During the set temperature either oil or other solvent start releasing. Or, check the oil content in your coolant, if there is any leakage of lubrication oil during machining also will effect. So clean the part in a better way.
Rajagopalan ChakiyarkandyProduction Incharge - DUBAI
February 21, 2022
Must we check Ra BEFORE manganese-iron phosphating or AFTER?
Q. WE ARE IN THE LINE OF MANUFACTURING CAST IRON PISTONS. OUR COMPONENTS HAVE MIP COATING OPERATION AFTER FINISH. WE OBSERVE VARIATION IS SURFACE FINISH VALUES (Ra) AFTER MIP COATING GETS CHANGED TO HIGHER SIDE, AND NO CONSISTENCY IN READING. OUR QUESTION IS WHETHER THESE VALUES MUST BE CHECKED BEFORE MIP COATING.
ANIL KHOTEngg. Works - karad, maharastra, India
August 7, 2014
A. Hi Anil. Based on the context, I assume MIP means manganese-iron phosphating, so we assigned a title and appended your inquiry to this related thread. Phosphatization is a soft coating (compared to iron), and manganese phosphate is often used as a "break-in" coating ... so I would assume that the surface finish before phosphatizing is far more important than the finish after it.
Regards,
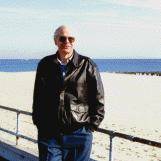
Ted Mooney, P.E.
Striving to live Aloha
(Ted can offer longterm or instant help)
finishing.com - Pine Beach, New Jersey
Q. Dear Sir, I am a custom cutlery manufacturer and have been using Manganese Phosphate impregnated with oil as a corrosion inhibitor on knife blades for some time with good success. I would like to treat kitchen knives the same way, but have concerns about food safety. Is there any reason to suspect that manganese phosphate treatment of carbon steel might be non food safe?
Adam DesRosiers- Juneau Alaska USA
April 28, 2015
A. Hi Adam. First, I don't want to toss around the term "food safe" without agreeing what it means :-(
Many materials that are not "poison" or "toxic materials" are not "food safe" either. For example, zinc is an essential micro-nutrient rather than a poison, but it can dissolve in acids or alkalis, possibly even resulting in an overdose, and it's not food safe by anyone's measure, even if you find no regulation forbidding it. Some of the laws & guidelines set limits on "dissolution" and manganese phosphate is probably not food safe simply by this definition.
Further, if you want to sell such a product there probably are FDA regulations that you can only use GRAS ("generally recognized as safe") materials; there might be NSF or some other applicable guidelines on appropriate materials as well. There are a boatload of regulations in the world today, and they are expanding rapidly; I would not be willing to say that anyone can offer anything for sale without a careful study of the laws regulating that trade.
Then too, what kind of "oil" are you speaking of? A few, like olive oil and mineral oil, are non-poisonous, but petroleum oils are poison.
Interesting question. I hope someone with specific tableware or kitchenware experience will respond.
Regards,
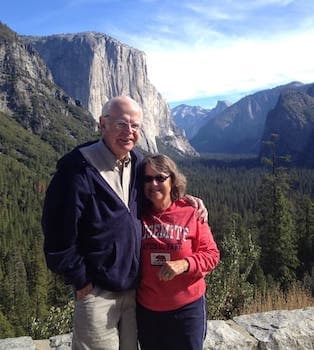
Ted Mooney, P.E. RET
Striving to live Aloha
(Ted can offer longterm or instant help)
finishing.com - Pine Beach, New Jersey
Q. Hi,
Good times.
I am Hamidreza from Iran. Sorry that my English is not good.
I have read your article about manganese phosphate and the questions you had.
I do not know during tests of the mixing materials.
Also, after removing the piece of soluble phosphate, phosphate coating on the surface is easily separated.
My solution is mixed as follows:
Manganese carbonate 15 grams per liter
25 ml phosphoric acid per liter
2 grams per liter of nickel nitrate
3 grams per liter of iron sulphate
Sodium fluoride 0.7 grams per liter
Rochelle Salt
⇦ on
eBay
or
Amazon [affil link]
2 grams per liter
5 ml of nitric acid per liter
pH = 1.5
Temperature 95 °C
Time: 30 minutes
If possible, please help.
Grateful,
- iran, tehran
June 20, 2015
Manganese Phosphating: Lost power for 5 minutes
Q. Hello Sir,
During manganese phosphating process if the power goes for 5 minutes and no DG, what are the quality issues can be raised.
- Bangalore, India
October 30, 2015
A. All depends on your solution temperature. Study the temperature specification given by solution provider follow it. There won't be any reduction of temperature with in 5 or 10 minutes.
Rajagopalan ChakiyarkandyProduction Incharge - DUBAI
February 21, 2022
Different colour tones on finished Manganese phosphating product
Q. Dear Sirs, I am involved on the inspections of the manganese phosphating process. I would like to know if the difference in colour tones of the final coated surface be cause for rejection. Other parameters were within acceptable limits. In the project specs, it is stated that uniformity in appearance as acceptance criteria. Does it include colour tone for uniformity? What is the cause of this defect? And how to rectify?
Ng twuan HuatQuality Inspections - Singapore
November 12, 2015
A. Good day Ng Tuan Huat.
Surely you are working toward a specification.
I work with a minimum/maximum coating weight requirement.
I would think the variations in colour tones is a process control issue.
You state all other parameters are within acceptable limits.
What are your parameters? Do you have a water-break free surface on the substrate before phosphating? Are you using an acid dip before phosphate? I have found dilute HCl to produce denser crystals.
Are you using a dilute chrome solution after phosphate, and if so, what is the concentration?
What is your free/total acid ratio? What is your iron concentration? What is the temperature?
All of these parameters affect the crystal structure of the deposit.
What is the substrate, and does it contain chromium, and if so, how much?" Max 2% will prove difficult.
Do you examine the deposit under a microscope to determine the density of the crystals? If so, can you see the substrate in between the crystals?
Are you conducting salt spray testing, and if so, what is the outcome?
There were only three questions in your posting, and I have posted you a total of eleven.
There are many variables involved to produce a uniform/acceptable deposit.
Hope this helps.
Regards,
Aerotek Mfg. Ltd. - Whitby, Ont., Canada
Q. Dear Mr. Bogner,
Please answer to question: we do Mn phosphating on threads of pipes. On way - alkali cleaning, rinsing, activating (Gardobond 6560 A and 6561 B (Chemetall) - MN phosphating (Gardobond G 4040) - rinsing - rinsing. (We cannot do pickling).
We cannot pass test - 10 screwing unscrewing. Could you inform us what we shall do that Mn phosphating crystal be more strong to wear of thread?
Director - Wolbrom Poland
December 24, 2024
Tip: This forum was created to help build camaraderie through sharing tips, opinions, pics & personalities.
The operator & those readers who want that might not engage with anonymous posters.
A. Hi Vadim
We will try to advise Mr. Bogner of your question, but his posting is from more than 9 years ago.
Phosphates should react with bare metal in order to deposit properly -- not oxidized surfaces with varying and uncontrolled amounts of oxidation. Since you can't pickle these pipes can you sandblast the thread areas, or at least phosphatize them immediately after cutting the threads?
Luck & Regards,
Ted Mooney, P.E. RET
Striving to live Aloha
(Ted can offer longterm or instant help)
finishing.com - Pine Beach, New Jersey
Q. Dear Mr. Mooney,
Thank you for the answer. We do Mn phosphating for antiwear of thread of pipes.
Is it enough to do alkali cleaning before activating?
director - wolbrom Poland
December 28, 2024
A. Hi again Vadim.
Acid dipping to remove oxidation is a conventional part of metal finishing operations. You have told us that you do not and cannot employ such pickling, and that your process is not working. I replied with my theory of why it is not working and suggested some things that can be tried to see if that will make it work. I'm not sure that I can offer any further advice.
But a general principal is that processing should be robust. If you operate a process which offers no provision for dealing with oxides and mill scale which will sometimes be present, it is not robust and although it may work sometimes if things are coincidentally highly favorable -- like the threads freshly cut perhaps -- it will not work reliably. Your process either needs to offer a way to remove heavy oxiding on the pipes or you must constantly operate in a fashion which guarantees minimal oxidation.
Please do a trial of blasting the thread area, or of processing immediately after cutting the threads, or try an alkaline deruster before putting the pipe through your process line, but it seems apparent that a grain refiner before phosphatizing is not a sufficient substitute for acid pickling.
Luck & Regards,
Ted Mooney, P.E. RET
Striving to live Aloha
(Ted can offer longterm or instant help)
finishing.com - Pine Beach, New Jersey
Q. I am facing a problem in distinguishing two washers having almost the same dimension and both are Manganese Phosphate coated. How can I ask the two source to make some visual difference? Please answer, it's urgent.
ARIJIT DAS- JAMSHEDPUR, JHARKHAND, INDIA
November 30, 2015
Manganese Phosphate color variation within the same lot of parts
Q. I would like to know if anyone has experience with some steel parts that are manganese phosphate all together as part of a big lot show some brown/pinkish appearance
Rodrigo Ramos- Salisbury, Maryland, USA
March 22, 2016
A. Good day Rodrigo.
Good Info @ thread 266/94. This web site has a plethora of info!
Regards,
Eric Bogner, Lab. Tech
Aerotek Mfg. Ltd. - Whitby, Ontario, Canada
Oh yes, we have a plethora, guapo ⇨
Regards,
Ted Mooney, P.E. RET
Striving to live Aloha
(Ted can offer longterm or instant help)
finishing.com - Pine Beach, New Jersey
A. I had experienced it with different grade of materials. If you have facility to provide bead blasting surface it can be controlled to a certain extent.
Rajagopalan ChakiyarkandyProduction Incharge - DUBAI
Q. Respected Sir,
We have a new coating plant and are going to perform Manganese Phosphate coating. Customer specifications are written as: Zn Manganese / Nickel Manganese / Manganese Coating for different parts. What is the difference in all above three or are all above same?
Are there different types of Manganese Phosphating?
- Pune, India
March 9, 2017
A. Hi Nitin. Unfortunately you can't ask a third party to put a fine point on someone else's slang and casual phrasing. There is no way for me to know whether "Zn Manganese" is intended to mean "Zinc Phosphating with additional dicationic ions of manganese" vs. "Manganese Phosphating", or what exactly "Nickel Manganese" was intended to mean, or whether "Manganese Coating" was intended to mean "Manganese Phosphating". Guessing is not the way to proceed; you must get clarification and hopefully mutually agree to a more carefully worded specification.
Normally there will be additional criteria like salt spray hours for testing, coating weight, compliance with a specific standard number from a generally recognized organization like ASTM or ISO, etc. Good luck.
Regards,
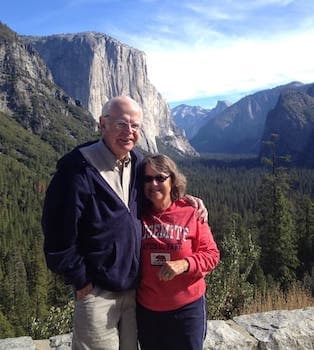
Ted Mooney, P.E. RET
Striving to live Aloha
(Ted can offer longterm or instant help)
finishing.com - Pine Beach, New Jersey
A. Ji, it all has its own different structures as well as application. Chemistry itself has differences. It is better to take advice of your solution provider for the right process.
Rajagopalan ChakiyarkandyProduction Incharge - DUBAI
February 21, 2022
Q. Dear readers,
I have set up zinc phosphate and manganese phosphate coating plant in our company.
I wanted to know if we can distinguish parts which are zinc phosphate coated from those coated with manganese phosphate.
- Pune, Maharashtra, INDIA
June 26, 2017
A. Hi Kathik. Tracking the parts seems a lot more practical than mixing them and then chemically testing every individual piece to re-separate them.
Although I personally have very low confidence in visual identification of finishes, I think only you can answer whether your people can reliably visually sort your specific zinc phosphate from your specific manganese phosphate. Sorry to be of no help :-(
Regards,
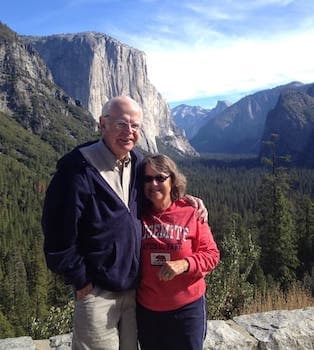
Ted Mooney, P.E. RET
Striving to live Aloha
(Ted can offer longterm or instant help)
finishing.com - Pine Beach, New Jersey
A. Regarding visual identification of phosphate coatings:
Zinc phosphate coatings will typically exhibit a dark gray color. Manganese phosphate coatings will typically exhibit a dark black color.
Imagineering Finishing Technologies - South Bend Indiana
Glittery Manganese Phosphating
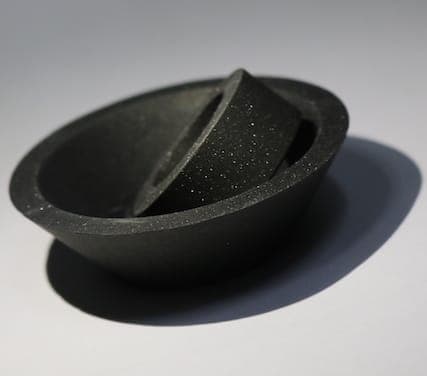
Q. Hi,
I am Jerin. I am from U.A.E. I happen to do manganese phosphating on a small component but ends up with glittery look. Can anyone help to know the reason why?
Thanks,
- United Arab Emirates
August 20, 2017
![]() |
? Hello Jerin, are you using a surface conditioner before the phosphate? Yohands ReyKAT - Chihuahua, Chih., Mexico A. Hi Jerin! TEL - N FERRARIS - Cañuelas, Buenos Aires, Argentina |
Hi Yohands, Thanks for your reply. In order to remove oil- film/grease from surface, we cleaned the surface with normal detergent, then had a rinse.
Hi Daniel, Thanks for your reply. Perhaps that would be the problem. I would try as you suggest :)
- United Arab Emirates
A. Dear Jerin,
Glittery appearance is mostly related to Iron concentration. Check solution parameters. Modify solution to the optimum. Give chance for acidic formation on the surfaces.
Production Incharge - DUBAI
February 21, 2022
(you are on the 1st page) Next page >
Q, A, or Comment on THIS thread -or- Start a NEW Thread