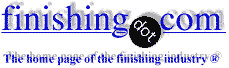
-----
What Part Does Voltage Play in Electroplating?
1 2
What compensatory changes to make if I have very low anode to cathode ratio?
Q. It is usually recommended to have the anode to cathode ratio be 1:1 or >1 : 1. If I am trying to use about a 0.2:1 ratio, what else should I try to change? Lower current density? Higher copper concentration?
Cameron Hill- Provo, Utah, USA
August 5, 2015
A. Hi Cameron. Lower current density should minimize anode polarization, but it's difficult to answer abstract questions which don't mention substrate material, type of copper plating solution, ID vs. OD plating, rack vs. barrel vs. continuous strip, single part for lab work vs. mass production, etc.
I'd predict no solution depletion problem plating a single part in a laboratory, but substantial difficulty in maintaining equilibrium copper concentration and pH in a high production environment. And whether you can get relatively even plate distribution would be an unknown for me since I have no concept of the anode-cathode arrangement. Good luck.
Regards,
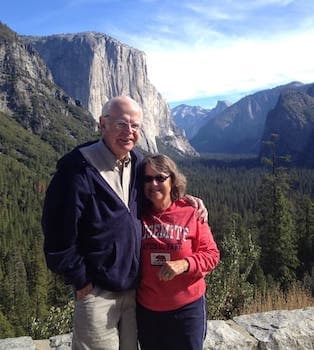
Ted Mooney, P.E. RET
Striving to live Aloha
(Ted is available for instant or longterm help)
finishing.com - Pine Beach, New Jersey
August 2015
Q. How are the different voltage levels used in electroplating? I mean from an inverter point of view, asymmetrical output voltage of inverter can be used for electroplating. How? As we can't measure asymmetrical output voltage of inverter like there is rms term for ac output voltage and average for dc output voltage.
Punit Kumar- New Delhi, India
February 1, 2017
A. Hi Punit. Inverters have no place that I know of in electroplating. It is the direct current that moves ions from the anode to the cathode, and ripple is often very problematical. No abstract questions please; they are usually, as in this case, impossible to answer. Please tell us who you are and your situation which motivates the question. Thanks!
Regards,
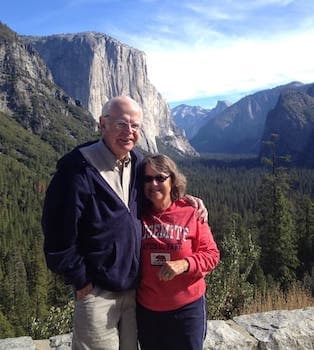
Ted Mooney, P.E. RET
Striving to live Aloha
(Ted is available for instant or longterm help)
finishing.com - Pine Beach, New Jersey
February 2017
Q. I've seen several posts regarding optimal voltages. Note: I do understand Ohm's Law. Additionally, I saw one of your responses related to optimal copper sulphate
⇦ on
eBay or
Amazon [affil link] concentrations, H2SO4 and other materials.
I think some people (and I am) asking:
What would be the maximum voltage before burning occurs?
I'm asking this a little differently. If I have a tank that's being mixed and with the solution with the concentrations that you previously described, what are the typical voltage setting and what amps/inch2 are observed?
What are the "other materials" added to the solution?
Thanks, Joe
- Davenport, Iowa
February 25, 2017
Hi Joe. How fast can a vehicle safely travel?
It's not that 16 years and 40 posts later I am trying to avoid answering your question. It's that people seem to not understand that parts may be pin-head size copper "bumps" or they may be a rack of 50 aluminum alloy wheels. You may be copper plating nickel wire reel-to-reel, or 100 pounds of washers in a polypropylene barrel. And people keep asking what voltage is needed but not responding to my requests that they carefully describe their own situation :-)
So I'll assume you are a hobbyist plating one sheet 6" x 6", with a spacing of 2" between the object and the anodes: the maximum amperage will probably be about 20 amps per square foot, and the voltage probably about 4 volts. The object you are plating can't be steel, raw aluminum, or raw zinc because they can't be successfully plated in copper sulphate. What is the object you are plating?
Regards,
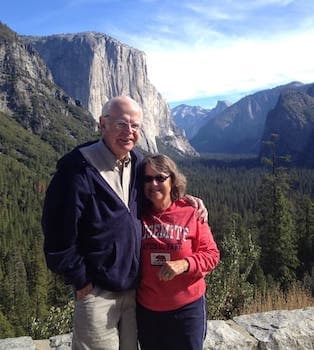
Ted Mooney, P.E. RET
Striving to live Aloha
(Ted is available for instant or longterm help)
finishing.com - Pine Beach, New Jersey
February 2017
Q. Ted,
Thanks for responding. I'm a hobbyist who's just starting out with copper and nickel plating... I'm trying to observe some of the dynamics and understand what's going on.
So far, I'm "testing the water"... making observations using a constant amperage or constant voltage, but I didn't want to be doing this while outside acceptable operating parameters.
My observations so far when I raise the amperage, there's a resistance spike which settles down (maybe after a steady ion flow is established between the nodes). So far, resistance appears that it could be used as an indicator of poor operating conditions.
That's why I'm asked the burning voltage question. Maybe an example of your choice could help me understand what you've been trying to say.
- Davenport, Iowa
February 26, 2017
A. Hello again. Okay, I guess the main point I've been making is that amperage is the key/central parameter in electroplating. Ideally, when your power supply moves 2 electrons from the anode to the cathode, you have raised the oxidation state of one atom of copper (or nickel) on the anode from the metallic state to the ionic state and it will dissolve and migrate to the cathode, where it will regain those two electrons and be reduced back to an atom of copper (or nickel). This is the simple background behind Faraday's Law, which says that 96,485 ampere-seconds of current will cause one gram molecular weight of metal to deposit if things are running at 100% efficiency.
Most everything else about plating -- from pH to temperature to solution concentration to agitation to voltage -- revolves around facilitating this operation. If the voltage is too low, the current won't flow, or the amperage will be too low to produce practical plating thickness in a practical amount of time. And here's what happens if the voltage is too high: too much current flows and you get "burning". What happens in that case is copper ions cannot migrate quickly enough through the bulk of solution and the boundary layer to keep up with all the electrons you are pumping to the cathode. So those excess electrons, which must be satisfied, pull the hydrogen out of the water in the plating solution, turning the water into hydrogen gas which evolves at the cathode, and 0H- ions. If you're only depositing half as much metal as Faraday's Law says you should, you're operating at 50% cathode efficiency. Too much current also forces the metal ions to instantly slap down as a somewhat non-adherent powder instead of permitting a better metal crystal structure.
It's relatively easy to operate in hobbyist mode; it gets harder to operate in production mode because you must maintain an equilibrium condition where the pH and solution concentration are not changing on you and contaminants are not building up, in addition to being sure that you can warranty that the copper plating will not peel or blister or cause problems in the next layer of plating, etc.
One reason the required voltage for plating is so variable is that the biggest resistance is the resistance of the plating solution, so if small parts allow a 1" anode-to-cathode spacing and large parts require 18", you'll see much different voltages required.
Regards,
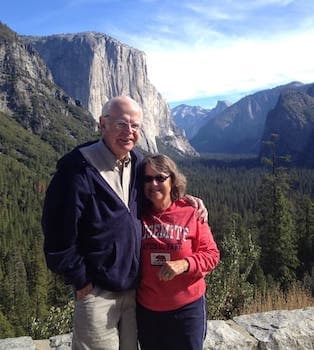
Ted Mooney, P.E. RET
Striving to live Aloha
(Ted is available for instant or longterm help)
finishing.com - Pine Beach, New Jersey
February 2017
Q. Hello, I plan to design the experiment about "the factor that affect the quality of electroplating" and I plan to use the current density as variable. But I'm not sure if this variable is worth to write about 12 pages reports. Can you give me some suggestions about the experiment design and the type of metal I should use? Thank you!
Olivia Xiong- Chengdu, China
July 24, 2017
(affil links)
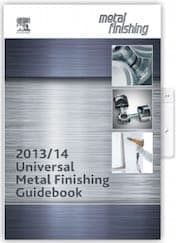
free pdf is currently available from academia.edu
A. Hi. Of course you can write a 12 page report about current density in plating. Just using some of the central terms of this page you can google "Faraday's Law of Electrolysis", "Cathode Efficiency", "Boundary Layer" and go way beyond 12 pages if you wish.
I think you should browse through the Metal Finishing Guidebook to acquire a general feel what electroplating is about, and what interests you, rather than having someone else design your experiment for you. Good luck.
Regards,
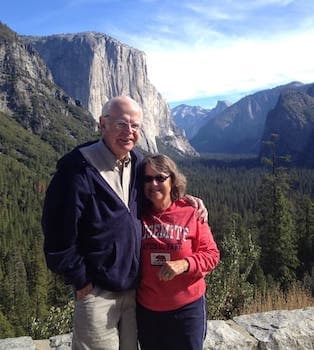
Ted Mooney, P.E. RET
Striving to live Aloha
(Ted is available for instant or longterm help)
finishing.com - Pine Beach, New Jersey
August 2017
What voltage is required for tabletop electroplating console
December 26, 2017Q. I want to build a small laboratory (table) electroplating machine.
For nickel plating, chrome plating, iron plating, gilding and silvering.
Cathode area to 2dm2 (31 sq in), min cathode area 1/100 max.
My question is, what source should I get?
If I run out of max current density 15A/dm2 have current 30A. Because I do not know at what voltage I reach 30A current I do not even know how much power I need.
I need
a). 0 - 5V 30A (150W)
b). 0 - 10V 30A (300W)
c). 0 - 15V 30A (450W)
- Dressden, Germany
A. Hi Hans. I don't think 5V will be enough, and don't feel that 15V will be necessary. My choice is "b)."
I hope you know what you're getting into with chrome plating. Good luck.
Regards,
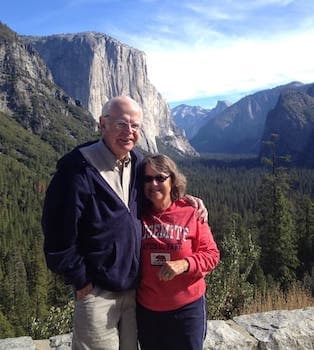
Ted Mooney, P.E. RET
Striving to live Aloha
(Ted is available for instant or longterm help)
finishing.com - Pine Beach, New Jersey
December 2017
Q. Hello, I have a question and it would be very helpful if someone could explain me this:
If I am performing an electroplating experiment, should I conduct it with constant voltage or constant current density?
I usually conduct it with constant current density but need to understand the relationship between constant current density, overpotential, and constant potential.
Thank you.
University of Massachusetts Lowell - Lowell, Massachusetts, USA
February 18, 2018
A. Hi cousin Abbas. I think you may be making things hard on yourself when the question is posed in abstract fashion. If you tell us what the substrate is, what metal you are electrodepositing onto it, the general nature of the experiment, and why you are doing it, things will be easier.
But keeping it general, are you familiar with Faraday's Law of Electrodeposition yet? If you are, great; if you're not, that is the first thing we have to talk about.
In production electroplating, constant voltage is usually used rather than constant current density because the area of the load might vary, and it's constant current density we are aiming for. Some rectifiers (power supplies) may have an adjustment or bias to account for overpotential and other static potentials ... such that beyond that offset or tare point the current density is proportional to the voltage and you can set the rectifier to plate by calculated current density (it's actually controlling the voltage).
Although we clearly understand some scientific rules like Faraday's Law, some other relationships are too complex to fully understand based on theoretical ideas and first principles. For example, we know that nickel plating can come out fully bright at about 40 Amps/sq.ft., and that very substantially below that point it may not be bright, whereas at 50% above that point it will probably "burn" ... but we don't have useful theoretical formulas to arrive at this number, we only have empirical knowledge.
Regards,
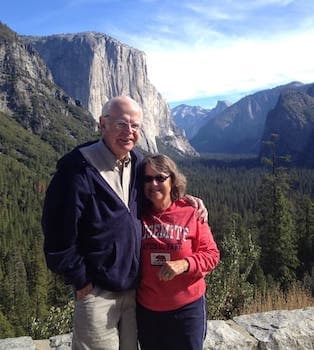
Ted Mooney, P.E. RET
Striving to live Aloha
(Ted is available for instant or longterm help)
finishing.com - Pine Beach, New Jersey
February 2018
Q. Hello Mr. Mooney,
Thank you for your prompt reply. I am electroplating a copper substrate with soft gold solution. The gold solution is acid based cyanide solution.
I appreciate your response but still a little confused. It would be great if you could tell me more about the above mentioned substrate and precursor.
As per your response, you suggest constant potential over constant current density?
Thank you.
University of Massachusetts Lowell - Lowell, Massachusetts, USA
February 19, 2018
A. Hello again Abbas. Sorry for the confusion, I suggest constant current density but I would be surprised if the current density and potential don't remain very closely proportional.
If you can get access to a Hull Cell ⇦ huh? you can probably make quicker progress than with more random experimenting because the Hull Cell is designed to let you see the results of plating across a broad range of current densities from a single experiment. Good luck.
Regards,
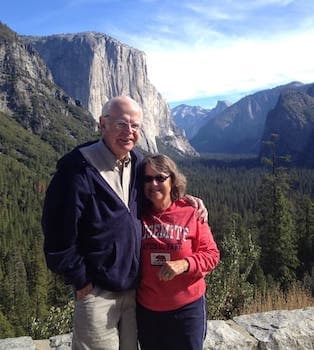
Ted Mooney, P.E. RET
Striving to live Aloha
(Ted is available for instant or longterm help)
finishing.com - Pine Beach, New Jersey
P.S.: Please call me 'Ted', readers. In many cases I don't know a poster's sex, age, or situation, so English forces me to use their first name, and it seems disrespectful for me to call some people by their first name and others by their last. If you sign as "Mr.", "Ms." or "Dr." I'm happy to address you that way.
Thank you so much Ted.
I shall get back to you in case of any more doubt. Once again, thank you much.
University of Massachusetts Lowell - Lowell, Massachusetts, USA
February 20, 2018
Q. My Details:
In a Moebus setup ...
2 anodes 3 cathodes of 316 stainless steel.
area of electrode= 110 sq.cm; distance between electrodes = 5.6cm ; r=0.051 ; conductance=0.051 ohm ; specific conductance=1 ohm ; molar conductance= 0.47 ohm sq.cm mol = eq.conductance
How much ampere can be passed through electrolyte of 1 mole/ltr of Ag, i.e., maximum current to get 100 gms Ag ?
I want to speed up the production.
gemstone business, trying to establish refining business - Lucknow, Uttar Pradesh, INDIA
March 4, 2018
Hi Somesh. Sorry, I don't know what you mean by "Moebus setup".
You might be better off with 2 cathodes and 3 anodes. You can use Faraday's Law of Hydrolysis to calculate how many ampere-hours are required to get 100 gms of Ag (402.4 A-hrs.) Higher silver concentration, higher temperatures, and greater agitation will increase the allowable plating rate, enabling higher amperages and shorter times ... but I believe that calculating allowable current density based on first principles is beyond our present abilities, such that it has to be determined empirically. Good luck.
Regards,
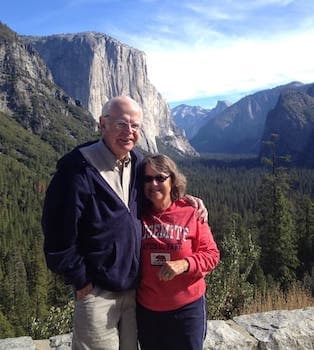
Ted Mooney, P.E. RET
Striving to live Aloha
(Ted is available for instant or longterm help)
finishing.com - Pine Beach, New Jersey
March 2018
March 9, 2018
A. Somesh,
You gave a lot of details but, unfortunately, most of the details you gave provide no help at all to the solution of your problem. To give you a meaningful answer, I would need all of the following information:
1- What is the anode composition?
2- Is the 110 sq cm electrode area 1 side or both sides?
3- How many liters of solution are in your cell?
4- How much amperage and voltage are you presently using?
5- How often do you want to produce 100g of silver?
Most likely, my answer will be a practical one rather than a theoretical one.
- Benton, Arkansas, USA
Q. How does voltage affect the quality of electroplating? Specifically, copper plating onto an iron nail.
All your help would be greatly appreciated!
- Cairns, QLD, Australia
April 21, 2018
A. Hi Ashleigh. In response to many requests from teachers that we "Please just tell the students to do their own homework", I don't answer such questions anymore. But I am happy to refer you to our article on Faraday's Law of Electrolysis which will explain the relationship between voltage and electroplating. Also, if you read this page carefully, you will see the word "burn" / "burning" mentioned 13 times previously ... from which you will be able to infer that excess voltage leads to low quality. Good luck/
Regards,
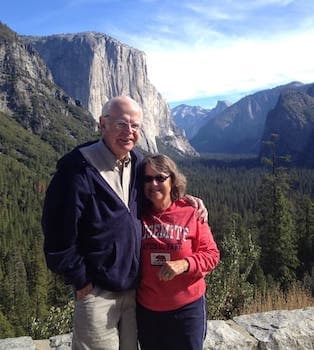
Ted Mooney, P.E. RET
Striving to live Aloha
(Ted is available for instant or longterm help)
finishing.com - Pine Beach, New Jersey
April 2018
Q, A, or Comment on THIS thread -or- Start a NEW Thread