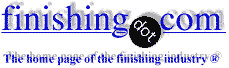
-----
Remove aluminum from etching & anodizing baths
Nadcap Chemical Processing Auditor - PRI, traveling
Process Engineer / Chemist - Denver Metal Finishing, Colorado
Q. Hi guys, my name is Edgar and I newbie on anodizing.
In a few days we will dump the Alkaline etching bath, the last change of the bath was in January, so I think that maybe we can extend the life of the bath through the decantation of the bath?
Is it a good idea? Any comment or ideas to extend the life?
Thanks in Advance.
- Quer´taro, Mexico
May 25, 2022
A. Hi Edgar. As far as I know, decanting the solution (and removing the precipitated aluminum oxides) will not reduce the dissolved aluminum. Excess dissolved aluminum in the etch causes problems, including "Spangle and Shiny Metal" (topic 40098).
Luck & Regards,
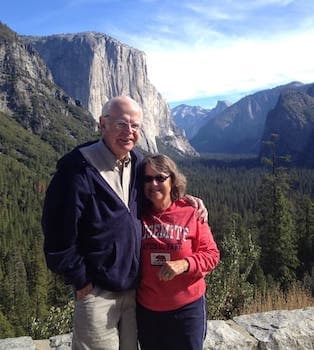
Ted Mooney, P.E. RET
Striving to live Aloha
finishing.com - Pine Beach, New Jersey
Thanks a lot.
Q. I just want to know because the TDS recommends the change when the Al content is greater than 35 g/L. At this moment we have 17.35 g/L but the removal (etch) rate has decreased.
- Quer´taro, Mexico
A. The "dump point" or bleed/feed point has to be determined by you. The dump point varies from shop/shop depending on the desired finish. Keep a log sheet record and determine the level of dissolved aluminum that does not interfere with the particular finish you want, then over time bleed & feed to hold the aluminum constant. Each time pump out, dump the sludge, pump back in, titrate and bring up to desired concentration. If in the middle of the week you see "spangle", drop in a tiny bit of hex chrome and that will hold you until Saturday.
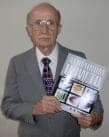
Robert H Probert
Robert H Probert Technical Services

Garner, North Carolina
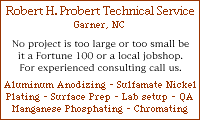
⇩ Related postings, oldest first ⇩
Q. I have clients searching for a good method of removing aluminum from both conventional and hard anodizing solutions. Their present technique is "dumping once a year". The other alternative we have used is to remove 10% of the solution when it gets too high in aluminum content. This solution is replaced with fresh sulfuric acid. There is a "sorption" process available commercially but apparently, first cost is very high.
Bert J. Sherwood- Los Angeles, California, USA
2000
A. An effective method for removing and maintaining the Aluminum concentration at a constant level is by using a Diffusion Dialysis System. My company manufactures this type of system for Acid Recovery and is suited to your application. A majority of the aluminum can be removed and the operation of the bath can be maintained more consistently by removing aluminum as it builds up.
Tony D'Amato[company name deleted by editor] - Chicopee, Massachusetts
A. We do anodizing & hardcoating & have a special ion-exchange system for removing aluminum from a company called [name of ion exchange company deleted by editor] - It works great. We purchased it from [deleted by editor].
David A. Kraft- Long Island City, New York
We appreciate Tony's and David's attempts to be helpful, but please suggest only generic technologies, and use google or another search engine for vendor & sourcing suggestions. There are several compelling reasons why we can't post them ( huh? why?).
Luck & Regards,
Ted Mooney, P.E. RET
Striving to live Aloha
finishing.com - Pine Beach, New Jersey
A. Aluminum can be selectively removed using a so called "ACID RETARDATION PROCESS". It is a relatively simple process and although there is an initial investment it pays back within a year.
Ruud Gerritsen- Simpelveld, Netherlands
Q. Ruud,
Can you explain me what is the 'acid retardation process'?
Which companies can I contact in Europe for this technique? [ed. note: Sorry, Francesco, we cannot post vendor or sourcing suggestions]
Thank you and best regards.
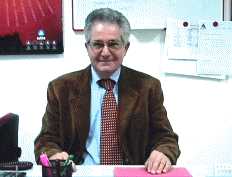
Francesco Cicchetti
- Sulmona, Italy
A. Francesco, Acid retardation is an ion-exchange process where the aluminium contaminated sulfuric acid is passed through a resin. After loading the resin it is eluted with water, resulting in a sulfuric acid stream with low Al and an aluminium sulphate solution with low sulfuric acid. A large number of European companies provide this system.
Ruud Gerritsen- Simpelveld, Netherlands
Multiple threads merged: please forgive chronology errors and repetition 🙂
Recycling of Aluminum Etch Solution
Q. I am an Environmental Engineer trying to reduce the cost/waste from our company's aluminum etching process. We use a caustic cleaner/etch to remove a stearate based lube from aluminum cans, and to etch the surface prior to painting. We overflow the bath to remove foam, and then add caustic to maintain a conductivity of about 12 mS. This is done at 65 °C.
I believe we are wasting a lot of caustic. Is there a way to recycle the bath, or control it better to reduce overflow?
Steve Roosz- Greensburg, Pennsylvania USA
2000
A. I think that electrodialysis is used to recycle aluminum containing solutions but an even better way is to use an acidic etch instead of an alkaline one. The acidic etch for aluminum etches only 10-15% aluminum compared to an alkaline etch.
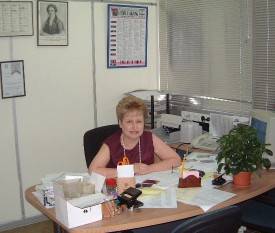

Sara Michaeli
Tel-Aviv-Yafo, Israel
A. Electrodialysis would work, I think. The EPA ETV metal finishing center is in the process of verifying one unit being used to remove Al from a chromic anodizing bath.
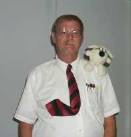
James Totter, CEF
- Tallahassee, Florida
A. Have you considered using alkaline cleaner prior to etching so you don't have to saturate your etch solution with lube? This will mean longer service life and less disposal.
dado macapagal- Toronto, Ontario, Canada
by Matsuo Tomonori (Editor)
on AbeBooks
or Amazon
(affil link)
A. Bravo Dado!
Many times I've seen a single alkaline tank doing double duty as both the aluminum cleaner and the etch but it's corner-cutting that comes back to bite you.
For example, when you get a batch of parts that needs extra cleaning, you'll automatically get extra etching that you didn't want; then your desmut isn't strong enough to remove the alloying ingredients left behind from etching that much aluminum. Then you're wondering why you have smut problems, and you're adding extra pickling steps or moving to more toxic pickles :-)
We should clean the parts in a non-etch cleaner first, THEN etch them (Sara could be right that an acid etch is preferable). Also, this way the organic contaminants are in one tank and most of the dissolved aluminum is in another and you have a much better chance of prolonging the solution life through one recovery mechanism or another.
When I went to work for Lancy Laboratories way back in the mid 1970's the centerpiece display in their building's atrium was a adsorbtion tower device for removing aluminum from caustic etches they'd been developing for years; people have been working on this issue 'forever'. But in my experience, many if not most of the recovery systems you see written up in the journals are decommissioned due to impracticality in actual operation once the grants expire. So if you try to remove both dirt & organic contaminants and dissolved aluminum simultaneously it will only be that much harder, and I'd bet you'll end up in that "most" category
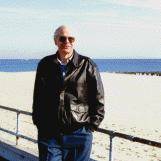
Ted Mooney, P.E.
Striving to live Aloha
finishing.com - Pine Beach, New Jersey
A. For cleaning of oily aluminum work pieces we had the same problem and received 3 pieces of advice as follows:
1- changing lubricant to evaporative or water soluble type.
2- downward streaming to catch 90 percent lube and then cleaning and etching.
3- using double phase cleaner available in the market.
In practice we found No. 2 suitable and cheaper, but for you it depends if your lube being not viscose to be dripped.
About cleaning after lube removal, find a suitable low-attack silicate-free alkaline cleaner.
HADI KHOSRAVI- Tehran, Iran
2002
Multiple threads merged: please forgive chronology errors and repetition 🙂
What to do with the Waste from sulfuric acid anodizing?
Q. Since there are tricks to every trade, I don't have a problem with showing how uneducated I am about anodizing. I have been a machinist for 12 years and seen all types of anodizing. Now that I know a small portion of the process, I must ask, "what do you do with the waste?" I assume that your tank full of sulfuric acid will not be usable forever? What about the hydrogen that is put off while anodizing? I would assume that a hood type ventilation system over your tank would exhaust the hydrogen? Thanks for your help, Allen
Allen James- Calvert City, Kentucky
2000
A. Allen, you pay some people to take away your waste and dispose of it in a proper and responsible manner. That's what I do (I'm a research student working in a lab' on baths where 2 liters would be big) how the chemicals are treated is something I'm interested in, but so far I've not learned much except it's all specific to application. Ian
Ian Brookeuniversity - Glasgow, Scotland
A. Hi Allen. Users attempt to operate their plating and anodizing systems as "equilibrium processes" which are maintained rather than disposed of. Some plating baths have been in use, never dumped, for many decades. But sometimes that can't be done because despite best efforts the baths grow or get contaminated.
Some processes like electroless nickel can't be equilibrium processes because phosphates build up inexorably with use. Some of the support processes like cleaning, etching, desmutting, and dyeing cannot be maintained in equilibrium and do become exhausted. This is generally a matter of neutralization of acid/alkali, with consequent settling out of solids. However, anodizing facilities must be registered and disposal permits obtained. These are generally issued by the POTW serving your area.
Hydrogen evolution is generally not a serious problem, but the tiny droplets of solution that evolve from the tank along with the hydrogen, in ginger ale or champagne style, must be captured with an exhaust system and scrubbed. The exhaust system keeps the hydrogen below the lower explosive limit (although I've never heard of what most people would consider an 'explosion', just the 'popping' we demonstrated to ourselves back in high school chemistry class). Good luck.
Regards,
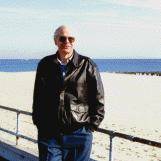
Ted Mooney, P.E.
Striving to live Aloha
finishing.com - Pine Beach, New Jersey
Recycling spent die strip caustic
Q. I have been working on the use of 308A die strip additive to speed up the stripping of dies and the trials were successful. Our consultant further proposed the use of the spent die strip caustic in anodising etch operation, something we are currently pursuing. I would like to know the further additives that we need to use to prevent the adverse effect of the dissolved aluminium carried over from die strip. Currently we are using Almeco plus 2 to hold aluminium ions in solution in our anodising etch, but we are having problems on the accumulation of sludge in the etch tank, which is affecting the heating up of the tank.
Please can you suggest an alternative.
Noah Nyembametal industries - Harare, Zimbabwe
2001
A. Hi Noah. Dissolved aluminum and precipitated aluminum are two different things: you can filter out that precipitated aluminum sludge.
Luck & Regards,
Ted Mooney, P.E.
Striving to live Aloha
finishing.com - Pine Beach, New Jersey
Diffusion Dialysis Membranes
Does anyone know if it is possible to use cation membranes in a diffusion dialysis system to remove free NaOH and retain sodium aluminate (dissolved aluminium in caustic).
Is this process possible? Can the membranes withstand the 25% NaOH solution and the pH 13? Are there companies out there that manufacture such systems?
Any help on the topic is greatly appreciated.
Thank you,
Jim Pejoski- Canning Vale, Western Australia
2002
A. Probably not.
The difference between diffusion dialysis for acids is that you are trying to recover an anion, which is a large molecular compound in most cases, and also usually divalent, which gives it greater propensity to "attach" itself to water passing thought the membrane. You're trying to recover caustic in the cation application - which competes with hydrogen ions for transport (even in the highly alkaline background). Sodium is a poor transport ion as it is stable and only monovalent.
Have you tried to seed the material and filter it out?
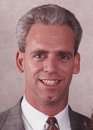
Tom Baker
wastewater treatment specialist - Warminster, Pennsylvania
2002
A. Yes you can recover NaOH using cation membrane if your solution is NaOH and sodium aluminate. The problem is that as you recover the sodium hydroxide the sodium aluminate precipitates, therefore you can only recover as much as 40 % during dialysis. If you crystallize your high aluminum discharge, you can recover the rest of your NaOH. You have to play with the water inflow to reduce the dilution of your NaOH. I had the chance to do this process about 11 years ago at the University of Rhode Island.
Best regards
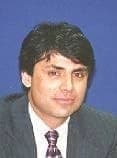
Dr. Belzahet Treviño Arjona
Water Studies Center, ITESM - Monterrey, Nuevo león México
2004
Multiple threads merged: please forgive chronology errors and repetition 🙂
Q. At the moment, a multinational electronic factory engages me as their environmental consultant and my first task with them is to help solve the sludge stock that has been kept in their backyard for the past few years. Those are dewatered (25% dryness) metal hydroxide sludge coming from their waste treatment plant. It contains 8% of nickel and mostly aluminum. The sludge quantity is about 600 metric tonnes. My questions are: a cement factory is keen to reuse them on their product, is there such a case ever happen elsewhere before? If not, what would be more suitable reuse?
Thanks,
Teh Poay HeanWaste Treatment Contractor - Georgetown, Penang, Malaysia
2004
Q. I Am interested in this topic also.
Mr. Chuahmetal Recycling - Penang, Malaysia
March 11, 2009
A. Hi. Unfortunately it can be risky to use your waste in someone else's products. For example, that 8% nickel could be a serious issue in cement. And even if the cement factory plans to use only some much smaller percentage of your waste in their cement to keep the nickel levels down, they may accidentally or deliberately use more and produce cement that is hazardous.
Malaysia is not the USA and your rules are different, but here's what happened here: Companies used to pay other companies to dispose of their waste, but some of those 'other companies' turned out to actually be illegitimate 'midnight dumpers' who contaminated the land, leaving the citizenry with huge cleanup costs :-(
The problem was 'solved' by new rules which said the original generator of the waste was responsible for their waste forever, no matter how much they paid anyone to dispose of it ("cradle to grave"). One unintended result was that the rapidly growing business of "industrial waste exchanges" totally collapsed almost overnight. Who in America would be dumb enough to let their waste be used for concrete in a bridge support if there was any risk of being responsible for removing & replacing that bridge support? One thing I would suggest is that if the concrete company pays you even a token amount, rather than you paying them, you may have reasonable grounds for claiming it was not waste.
Luck & Regards,
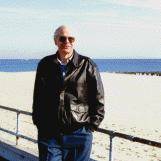
Ted Mooney, P.E.
Striving to live Aloha
finishing.com - Pine Beach, New Jersey
Multiple threads merged: please forgive chronology errors and repetition 🙂
Recycling of sodium hydroxide
Q. I'm wondering about the possibility of recycling NaOH and sodium aluminate from etching rinse solution of Al by reverse osmosis or diffusion dialysis. I need more details about the technology.
Mohamed A BarakatCMRDI Institute - Helwan, Cairo, Egypt
2005
A. Diffusion dialysis is probably the only known commercial mechanism. I am currently working on developing a process for a client, but do not have any results. Diffusion dialysis turns out to be very, very expensive, but has been done. You should be able to find manufacturersthrough the Metal Finishing Guidebook.
Juzer Jangbarwala- Brea, California, USA
Q. We run an anodising plant in South India. In order to maintain the levels of aluminium below 10 gms per lt we are looking for a solution. Acid purification unit seems one viable option. Can anyone who has used this give me some feedback. Also how effective is regeneration of caustic bath?
Thanks,
Abhinava Aluminium p ltd - India
2005
What to do with solid waste from anodizing process
Is there a way to utilize the solid waste from effluent treatment from an anodizing line?
The average chemical analysis as follows:
As 1.85 ppb
Ba 31.03 ppb
Cd 0.033 ppb
Cr (total) 0.914 ppb
Cu 3.12 ppb
Hg none
Mo 3.26 ppb
Ni 1.15 ppb
Pb 0.19 ppb
Sb 0.64 ppb
Se none
Zn 1452 ppb
Chloride 140 mg/L
Sulphate 427 mg/L
Total dissolved solids 800 mg/L
finishing equipment and service provider - Istanbul, Turkey
2007
A. You seem to be providing analytical data for a liquid waste. So, it's a bit hard to tell.
Aluminium hydroxide based sludge from the treatment of such a wastewater might be suitable for blending with cement. Even with the high price of zinc (the main heavy metal in the water you describe) these days, 0.14% is not enough to interest a recycler.
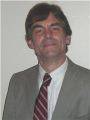
Dave Wichern
Consultant - The Bronx, New York
A. Hi. It may depend to some extent on your country's waste laws. It's ideal to use waste products in gainful fashion, but if they are regulated wastes and you are responsible for them forever like in the USA, that can be very risky. Google "Times Beach, MO".
Luck & Regards,
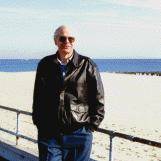
Ted Mooney, P.E.
Striving to live Aloha
finishing.com - Pine Beach, New Jersey
⇦ Tip: Readers want to learn from your situation;
so some readers skip abstract questions.
Q. I am a chemical engineer and want to know the best technique for recovering sodium hydroxide and sodium aluminate from aluminum etching tank to reduce both waste and cost.
Is it more cost effective to do it chemically or by hydrolysis and by some other means.
chemical engineer - Beirut, Lebanon
December 22, 2008
Hi Ghada, people wouldn't continue to use the poorer method if another method was better in any and all circumstances. Please give us actual details of your own situation because lack of detail encourages canned sales pap rather than tailored advice. Thanks!
Regards,
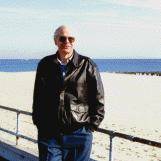
Ted Mooney, P.E.
Striving to live Aloha
finishing.com - Pine Beach, New Jersey
Q. Dear Reader:
I am asking about the ability of recycling caustic soda ⇦liquid caustic soda in bulk on
Amazon [affil link]
[from etching aluminum profiles as a pre-treatment prior to anodizing] by precipitating Al via CaO in the presence of sodium gluconate "scale inhibitor"
Al Plant employee - Cairo, Egypt
January 21, 2009
Extracting / Recovering aluminum from acid waste
Q. I would like to remove about 6 gram/liter of aluminum contamination from a strong sulfuric acid waste so the acid can be used for another purpose. Could electroplating technology work to remove the aluminum? There are other metals in solution, but I don't care if they come out or not.
Claude AndersonWastewater research - Arden Hills, Minnesota, US
October 22, 2010
A. Sorry, Claude, you will not be able to plate the aluminum out of this waste. Aluminum is too active a metal, and you will electrolyze the water into hydrogen and oxygen without the aluminum coming out. Recovery of aluminum is a very difficult proposition that is done by ion exchange, absorption contactors, etc. Please try to contact companies specializing in this and see if there is an affordable solution for your situation. Good luck.
Regards,
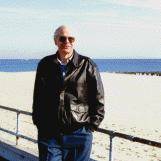
Ted Mooney, P.E.
Striving to live Aloha
finishing.com - Pine Beach, New Jersey
A. Either Diffusion Dialysis or Acid Retardation can remove aluminum from sulfuric acid. Unfortunately, neither will remove all of it.
Lyle Kirman
consultant - Cleveland Heights, Ohio
A. You may want to look into acid filtration units, I don't want to mention specific company or product names here - it is against the forum guidelines - but you should be able to find information relatively easily via google.
It won't remove all of your aluminum, but if you are just trying to get it back down to an acceptable level, it should work quite well.
Good Luck!
Compton, California, USA
A. This is a job for an APU (Acid Purification Unit). If you're looking to reclaim the aluminum, that will be more difficult. Metal Hydroxide precipitation could be used but then you'll have a cake about 75% water and 25% Aluminum Hydroxide.
Dale Burford- Weston, Wisconsin, United States
A. On the initial aluminum and sulfuric acid, if there are no other contaminants of concern you may want to look at it for potential product sale. You have just made Alum which is used for wastewater treatment. There are potential outlets that may buy the material as a product instead of having to perform hazardous waste disposal.
Q. Have just started generating an alum sludge for the removal of phosphate under new pretreatment regulations in the Southeast. Has anyone run into a place to recycle the sludges instead of just ending up burying them. Material has 11.9% AL, 27% Fe, and 3000 ppm Cr by dry weight. Interest in any experience you have for that.
Brian Hart
- Cornelia, Georgia
January 19, 2011
A. Hi Brian,
I think you will find few, perhaps zero, "waste chemical exchanges" in operation anymore because of the EPA's solution to the problem of "midnight dumpers". There was a time when waste generators would pay someone to take their waste (probably at cut-rate prices) but the small hauling companies that took it would keep the money, dump the waste somewhere, and disappear ... leaving the public to bear the cost of cleanups.
To fix this problem, the EPA came up with their 'cradle to grave' rule where the waste generator is responsible for their waste products forever regardless of who they pay or how much they pay to dispose of it. Today it unfortunately feels safer to get your wastes into a secure landfill than to risk them, for example, being made into toxic bricks in a skyscraper which you are then responsible for rectifying :-(
Google 'Times Beach, MO' to fully appreciate the point.
Even when a waste contains no hazardous ingredients it might still be regulated as a 'categorical' waste (a waste generated by a particular industry like plating shops) ... so I strongly suggest that an environmental lawyer be consulted before having your wastes incorporated into someone else's products.
Regards,
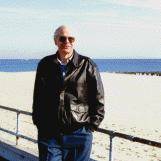
Ted Mooney, P.E.
Striving to live Aloha
finishing.com - Pine Beach, New Jersey
Q. Have you any knowledge about regeneration and recycling systems for caustic etch and anodizing baths rinses? Or used these systems? We have a some ideas for the systems ... maybe we'll try as a project.
Alaattin Tuna- Sakarya, Turkey
May 4, 2013
Q. What is the advantage of sulfuric acid recovery system? I have recently asked for quotation of the same, but it seems it's too costly. My anodizing tank size is 21' x 3' x 3' (L x B x H). H2SO4 concentration is 165-175 gm / liter. Please help me to know the size of recovery system required? The cost of such system? And the most important thing is the ROI (return on investment) on such system. Is it feasible to buy such a system? What is the maintenance required for such system? How regularly do we have to use this system for removing the aluminum dissolved in the anodizing tank? Please explain mathematically the advantage of using such system to get the advantage in the form of reduced electricity bill.
Please guide.
- Nashik, Maharashtra, India
February 18, 2014
A. I used to run our acid recovery unit 3 days a week, about 6 hours at a time.
The advantage is that you can control Al without doing periodic batch dumps of electrolyte. That requires neutralization, with the generation of massive amounts of Al(OH)3 sludge which must be dewatered, and disposed of. The costs and labor associated with this, not the cost of the acid, is why the unit is worth the money.
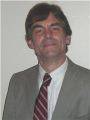
Dave Wichern
Consultant - The Bronx, New York
⇦ Tip: Readers want to learn from your situation;
so some readers skip abstract questions.
Q. Can anybody please tell me what is adsorption process, diffusion dialysis, and acid retardation process. Which one is more effective and involves less investment (less costly).
Rahul Mogal [returning]- Nashik, Maharashtra, India
February 20, 2014
Removing aluminum from anodizing bath, separating aluminum salts from sulfuric acid
Q. We are looking into a solution to remove excess aluminum salts from sulfuric acid in the anodizing baths. I have heard some good opinions about specific ion-exchange resins membrane methods offered, e.g., by [deleted by editor]. I have also encountered some diffusion dialysis methods. Are there any other methods, do you have any experience with the methods I mentioned?
Maciej Wieruszyński- Zgierz. lodzkie, Poland
June 8, 2020
A. Diffusion Dialysis is my recommendation for smaller applications, and acid retardation by ion exchange resins for larger applications. If your dump frequency averages less than 50 gallons per day I would definitely recommend Diffusion dialysis, and if it is greater than 100 gallons per day I'd recommend acid retardation. In either case, you should try to maintain an aluminum concentration of 7-8 g/L, since this results in consistent performance.
Lyle Kirmanconsultant - Cleveland Heights, Ohio
Q. I have been working over a project since one month. I wonder if anyone implements this system for etching bath (Also it can be implemented for low caustic etch bath and die cleaning by caustic soda ⇦liquid caustic soda in bulk on
Amazon [affil link]
). Summary of system: Etching bath solution is transferred by a pump to a crystallization tank where aluminium hydroxide precipitates here by cooling, and caustic soda becomes liberated and it turns back to etching bath. Dissolved aluminium hydroxide is filtered by special filter press and gain "salable product".
So, does this recovery project sound implementable?
Sincerely
- Sakarya Turkey
May 3, 2021
Q. We have a lot of solid waste (1700 tons per year) from our anodizing plant (mostly aluminum hydroxide). Any ideas how to re-purpose that material? Right now 80% of our waste is water, we need to figure a way to dry it to powder form or find someone that wants to use it as is. Any ideas would be greatly appreciated.
JH Harg- Olney, Texas
November 19, 2021
A. Hi JH. I'd be very cautious about "find someone that wants to use it" due to EPA regulations, per this aside:
"Midnight dumping" was a very serious environmental problem for several decades. Companies would pay someone (frequently the lowest bidder) to dispose of their waste, and those disposal companies would take the money, illictly dump the waste, and then disappear, leaving the government and the taxpayers to foot the cleanup bill. The EPA solved this problem with "cradle to grave" regulations: if you generate the waste, you are responsible for it forever, no matter how much you pay anyone to dispose of it. So if you can get someone to BUY it, you perhaps have a case that it's not a waste; but if you pay someone a little to take it and "reuse" it I think you're on dangerous ground. Please consult an environmental lawyer about this in any case.
Dealing with aluminum hydroxide wastes from etching & anodizing has been a thorny problem absolutely forever. When I joined Lancy Laboratories almost 50 years ago, Dr. Lancy (the world's first designer of waste treatment systems for metal finishing wastes) already had an sorbtion tower which he had been working on for decades for that purpose as the centerpiece in the atrium. It's possible but it is not easy, cheap, or 100% efficient to recover aluminum or caustic.
We've appended your question to a very long thread discussing all of the alternatives, which hopefully will offer you a direction while we await someone responding directly to your situation.
Luck & Regards,
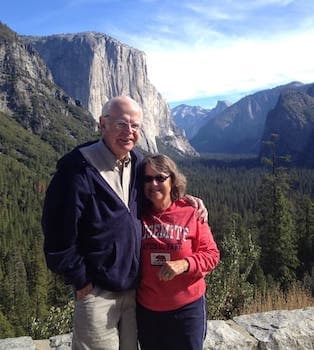
Ted Mooney, P.E. RET
Striving to live Aloha
finishing.com - Pine Beach, New Jersey
Q, A, or Comment on THIS thread -or- Start a NEW Thread