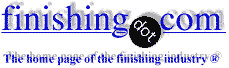
-----
Leakage Problem in PVC Lined Chrome Plating Tank
Q. Dear Sir, We are facing a serious leakage problem in our PVC chrome plating tank which has been used for two months by our customer. Our customer used the machine to do Chrome plating on Aluminum wheels in automobile industry. The Aluminum wheel is firstly plated with Copper, Nickel and then finally with chrome (Cr).
The chrome tank is made of 20 mm PVC. The operating temperature is 46 °C. There are four 6 KW Teflon L-shaped heaters put into the tank for heat generation and TFE cooling coil. There is not any air pipe and filter or circulation pump inside the tank. We have tried to repair the leaking tank and the situation became worse than before. Now, we have to make a new chrome tank for our customer as a replacement. Before doing this, we have to solve the following questions.
1. What material should be used for chrome tank fabrication?
2. What is the thickness of the tank wall with tank size as 36"x110"x65"?
3. Is it possible to add air pipe into the chrome tank with reference to the chemical property aspect?
4. Is it possible to add circulation pump to the chrome tank to prevent localized heat develop inside the tank that may damage the welding of the tank?
We hope you would let me have your professional comment on this issue, which is much helpful to us. Thanks & Best Regards,
- Hong Kong , China
2000
![]() |
A. The problem may be due to cracking of the plastic at welded joints or bends. In my humble opinion polypropylene would be a better bet especially bearing in mind temperature. - Croydon, UK A. You should not be experiencing these types of problems with a new tank. PVC is a correct material for chrome tank construction according to a chart I have. I am assuming that the tank is make of rigid welded PVC Are the leaks near welds? If so this may have more to do with welding technique (on which I do not pretend to be an expert) than on the material the tank is constructed of. process supplier - Great Neck, New York |
A. 1. Chromic acid is a powerful oxidizing agent, so I think I would disagree with the idea of using Polypropylene.
Chromic acid attacks PVC welds such that an attempt to make repairs can indeed make things worse.
I have never seen a chrome plating tank constructed of rigid PVC or rigid polypropylene, so I'm not sure what problems it brings. The traditional method is to use plasticized PVC liners -- either B.F. Goodrich Koroseal or equal, glued in place, or a prefabricated drop-in liner -- in a steel or FRP tank.
The most resistant lining material is Kynar, but this would cost far more than PVC, so it is often impractical.
Sight unseen, the most practical fix may be to glue in a Koroseal liner, which should have a double layer from several inches below the normal solution level to several inches above it, for the reason Gene pointed to.
2. As mentioned, I would build the tank of FRP or steel. Because I would include reinforcement girths (belly bands), the thickness of the wall would be far less than the 20 mm you mention. It would be more like 1/4 to 3/8" (say 8 mm) for steel or FRP.
3. Air agitation, through a perforated PVC pipe, is not a problem.
4. Circulation pumps are not a problem, but they probably ought to be Kynar.
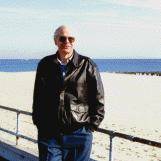
Ted Mooney, P.E.
Striving to live Aloha
(Ted can offer longterm or instant help)
finishing.com - Pine Beach, New Jersey
A. I also disagree with the polypropylene idea. I know for a fact that chromic acid, even in low concentrations will attack and crack the welds. It would leak within a month.
I have seen molded polypropylene tanks hold up for extended periods however.
A common practice for us is to build a 1/2" polypro tank with a 1/4" fabricated PVC liner. This would not be suitable where heavy parts might be dropped.
- chandler, Arizona, usa
A. Temperature and concentration will determine the speed of attack on a molded PP tank. A polyethylene molded tank will last for several years. It will actually last a little longer than most vinyl liners. The chrome will rapidly attack the plasticizers in the PP. Since the weld operation has destroyed some of the plasticisers, welded PP tanks are short lived!
My guess is that your PVC tank failed in the welds. First because of the loss of the plasticizers due to welding, especially if it was a rather hot weld. If it was cold weld, it does not take long for the heating and cooling to cause a problem to go along with the oxidation of the weld.
Re-weld is a nightmare! You must scrape every bit of the chrome affected PVC away or you will BURN the weld and it will fail in days.
Unless your tank had massive reinforcement, on the outside, it stood little or no chance of not failing. 1/2" is way too thin for a tank of this length to not have steel reinforcements. Many people forget that plastics' coefficient of expansion is about 10 times that of steel.
A tank of this length is going to have mega stress put on the corners as it expands and contracts, not to mention the bowing as it heats up and softens. In short, PVC was a poor choice.
- Navarre, Florida
2000
A. Hi everyone. Why everyone? Because a lot of good people are trying to help someone out. I was directly approached on this problem about a week ago and had sent some copious data to Chris.
Yes. PP is NOT recommended. However, a moulded one piece PP tank, were one available of that size which is not so, would last some years. But then so would a medium density moulded PE tank ... and with Polyethylene tanks (the largest in the USA or Canada being rectangular and having an open top is a paltry 500 gallon Imp.) could easily have the wall thickness increased to 1/2". Ask any reputable rotational moulder of the Engel process. Then the corrosion/chemical attack is vastly reduced. But you must never, ever weld on outlets. They will fail at the weld. Use tank adaptors instead where oxidizers are concerned .... I learned the hard way !
Years and years ago I.C.I. (England) proved that ordinary polyethylene is resistant to chlorine. Ah. Think about it. Of course it will be attacked! Of course it will fail. But what I.C.I. proved was that if the wall thickness were heavy enough, the chemical attack would peter out and a passive layer would be formed. This would apply to thermoplastics but never to fibreglass products as they do not have a homogenous structure.
Then there's the matter of the PVC sheet. Whose? There are some crappy PVC sheets and some damn good ones like SIMONA or, my favourite, TROVIDUR which costs an arm and a leg.
As pointed out to Chris, you MUST have a good thermoplastic welder. A so-called 'union' welder may hit 30% of tensile, a very well trained PVC welder should easily hit 85% of tensile.
Then these leaks probably occurred at welds because of stress distortion. All, YES, ALL the bottom and side corners have to have a decent radius. A radius not, never, a sharp bend!
Because of the size of this tank, the ONLY successful way to make it using type l uPVC is to armour it with fibreglass.......and Y E S that has been done most successfully, I did it for Weiser Lock years and years ago. The bond being the critical factor to prevent deflection.
Because of its size, the most practical $-wise solution is to use a steel tank with a Koroseal type liner with the ubiquitous 1/4" or overlay at the air/liquid interface.
Sure, KYNAR (A trade name for PVDF) would be OK but very expensive. But again only as a liner suitably FRP reinforced. For another 30% more in cost you could go to a proper fluorocarbon such as Halar. PVDF is super for the pump! Consider also a CPVC pump, too, but not a PVC pump as CPVC takes a higher heat and is better in oxidizing areas. Cheers from White Rock,(where it never rains, h'm)
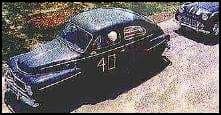
Freeman Newton [dec.]
R.I.P. old friend (It is our sad duty to
advise that Freeman passed away 4/21/12)
Q. Dear Sir,
We are into metal finishing since 3 decades. We are frequently facing leakage problems in our decorative chrome plating tank with an operating temperature of 55 °C.
At present, we are using fibre and steel-reinforced PVC tanks with sheet thickness of 5 mm and tank volume of 10,000 lts. Our present tank life is from 3 to 4 years.
Kindly suggest to us the right kind of material of construction for chrome plating having temperature resistance up to 80 °C and minimum life of 10 to 15 years.
- Bangalore, Karnataka, India
2005
A. Hi Srinivas. PVDF should do it, but at much much higher cost. Is long life critical enough to justify the cost? Most people think not and continue to use PVC.
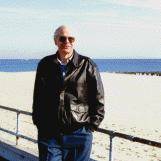
Ted Mooney, P.E.
Striving to live Aloha
(Ted can offer longterm or instant help)
finishing.com - Pine Beach, New Jersey
2005
![]() |
A. Hi ! ![]() Freeman Newton [dec.] R.I.P. old friend (It is our sad duty to advise that Freeman passed away 4/21/12) A. Why in the world do you want 80 degree resistance for a 55 degree process? If you can control your temperature more closely, you will open up options for more tank materials. You should also be aware that additives can be used in fiberglass that make them resistant to chromium oxidation. Not all fiberglass is the same. ![]() Paul Morkovsky - Shiner, Texas, USA |
A. Yes, there is fiberglass that can stand the chemicals in a chrome tank, but they do not like temperature changes IE: they crack and eventually leak.
Freeman is right on on this one.
- Navarre, Florida
A. PVDF is the most optimum material. Having been using it for about ten years on one chrome line, excellent: little to no problems. But you should at least go to CPVC over PVC for higher temperature safety. Then run dual temp controllers to insure temp. does not get away from you. It will warp crack and do all kinds of not so good stuff. Dual controls are important. Just one time you lose control you're toast.
Dwayne Simms- Cozad, Nebraska, USA
February 4, 2009
Readers may be interested in these related threads:
• Topic #42796 "Tank & lining material for chrome plating and chromic acid Q&A"
• Topic #4741 "PVC Tank Linings for 85 °C. use?"
• Topic #61492 "Best way to remove lining from Chrome tank"
• Topic #35118 "Polypropylene Compatibility With Chromic Acid Solutions"
Q, A, or Comment on THIS thread -or- Start a NEW Thread