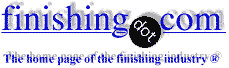
-----
Need details of 'the 7-tank process

⇦ Tip: Readers want to learn from your situation;
so some readers skip abstract questions.
Q. HI SIR,
I'M SEETHA I HAVE DOUBT ABOUT 7 TANK PROCESS.
WHAT ARE THE TANK MATERIALS AND HOW MANY MATERIALS USED FOR POWDER COATING?
employee - Chennai
April 4, 2022
A. Hi Seetha. As you can see on this thread, many people have offered the general (if sometimes slightly varying) sequence of operation and the names of each of the seven steps. The '7-tank process' is a generalization of the zinc phosphatization process (which comprises the pretreatment before powder coating), but it's not a specification.
The easiest way forward is to hook up with a supplier of these pretreatment processes, and they will recommend their overall sequence exactingly, and their proprietary chemicals for each of the steps in the sequence; and they will provide technical data sheets for the operation of each step.
If you wish to proceed without relying on proprietary chemicals from a supplier, or just to learn more, there are also many excellent books about phosphating which could enable you to start trying ... but generally an applicator of the process would buy the proprietary chemicals which are the result of years of R&D rather than trying to formulate the process solutions from raw commodity chemicals.
Please introduce yourself and your situation so that people can help you most effectively. Thanks!
Luck & Regards,
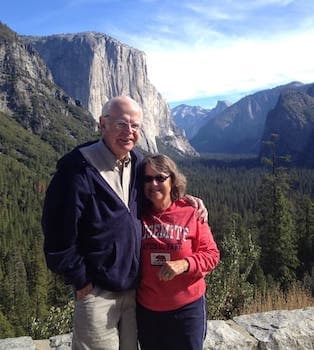
Ted Mooney, P.E. RET
Striving to live Aloha
(Ted is available for instant or longterm help)
finishing.com - Pine Beach, New Jersey
Q. I've a question?
What are the chemicals used for 7 tank process?
Can we use Degreasing with derusting same chemical
employee - Chennai
A. Hi Seetha,
The pre-treatment is commonly called as 7 tank process. It varies with customer's demand. We have two tank process chemicals with proprietary formulation. The customers are expecting ASTM standards at low cost per sq.ft. of treated material. A vague reply won't help you out to implement it practically.
Mr. Ted, as you referred to the knowledgeable Mr. Shankar, he is not with us now. We lost him to Corona infection. He was awarded with honorable medal by then Indian president Ms. Pratibha Patil.
Sundar Bala- Coimbatore, India
January 16, 2023
----
Ed. note: So sorry to hear of his passing, we have now noted this on his responses.
⇩ Related postings, oldest first ⇩
Q. Dear sir,
I am new in powder coating industry. In our company we powder coat HR/CR sheet. So please tell me the details of all 7-tanks.
SHIBY MATHEWpowder coating employee - Pune, Maharastra, India
September 18, 2009
A. Hi, Shiby. A "7-tank process" is simply a process where parts are immersed in seven tanks sequentially. Normally, the zinc phosphating process is done in 7 steps while the simpler iron phosphating pretreatment process is done in 3 steps or sometimes 5 steps. So when you ask about a 7-tank process for pretreatment, you are probably asking about zinc phosphating.
To me the 7 steps traditionally meant soak clean, rinse, acid, rinse, zinc phosphate, rinse, and chrome or chrome-free passivating dip.
These days a DI rinse is sometimes used instead of the passivating dip, and an "activation" step is often inserted before phosphating. But "7 tanks" is slang more than a specification, and the zinc phosphating process could actually involve 6 or 8 steps rather than always exactly seven.
You need to find a supplier for the process, and they will give you the operating parameters for each step. But if you are looking for background info, please see Rausch's "Phosphating of Metals" ⇦[this on Amazon or AbeBooks affil links] or another book on the subject. Good luck.
Regards,
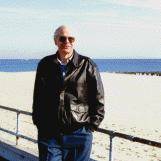
Ted Mooney, P.E.
Striving to live Aloha
(Ted is available for instant or longterm help)
finishing.com - Pine Beach, New Jersey
A. Hi shiby,
The 7 tank system is the following below.
1)Degreasing.
2)Waterwash
3)Acid pickling
4)Water wash
5)Phosphating.
6)Waterwash
7)Drying
This is the common steps, but now it's going up to 11 tank system also.
Based on the customer requirement and the part condition it may extend also. For example, if parts are coming with more scale, you need to introduce the Descaling and water wash then it will become the 9 tank system from the 7 tank system.
That is only the example. We will do at X number of tanks also.
- Salem,Tamil nadu, India
A. I differ from KANNAN. The 7 tank process is:
1) DEGREASING
2) Water wash
3) DERUSTING
4) Water wash
5) SURFACE ACTIVATION
6) Zinc PHOSPHATING
7) PASSIVATION.
This is the end of your search. You can go ahead with this and this is universal. It is a foolproof method and is being practised in TAMIL NADU for more than 10 years now.
- Coimbatore, TAMILNADU, INDIA
It is our sad duty to pass along the information that the knowledgeable Mr.Shankar was lost to Covid/Corona.
He was awarded with honorable medal by then Indian president Ms. Pratibha Patil. R.I.P.
3 replies, 3 different answers, which reinforces the point that the term really has no exact meaning -- it's just slang that refers to a zinc phosphatizing process which usually has about that many steps :-)
"Water wash" is sometimes employed between Phosphating and Passivation, which would make 8 steps. Drying is usually required, but I agree with Shankar that it usually isn't counted as one of the 7 steps.
Regards,
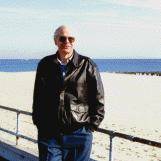
Ted Mooney, P.E.
Striving to live Aloha
(Ted is available for instant or longterm help)
finishing.com - Pine Beach, New Jersey
What is the 9-step Zinc Phosphating process?
Q. Dear Sir,
I want to know about the detail process steps of 9 Tank process of metal sheet. Please also mention the pH of the solution used for processing.
Thanks,
Proprietor - Kandi, WestBengal, India
October 9, 2009
A. Dear,
The 9 tank process is a gimmick; if all of your tanks operate at defined levels, you need not do descaling -- your derusting will take care of it.
Now coming to pH of the solutions,
DEGREASING : take 2 ml solution from the tank, with methyl orange
⇦ on
eBay or
Amazon [affil link]
as Indicator, titrate with N/10 sulfuric Acid, this is your Total Alkali.
Now take another 2 ml, with phenolphthalein
⇦ on
eBay &
Amazon [affil link]
as Indicator, The solution turns pink, now titrate with N/10 sulfuric acid, the END point is Pale Pink colour, the reading is your Free Alkali
Total Alkali
FORMULA ------------ = Should be between 1.4 - 1.8
Free Alkali if >1.4 add Degreaser
If <1.8 discard Tank
I have time for only this today. If you need further details on all tanks I can provide you upon request. Leave your request here, I shall do it then...
- Coimbatore, TAMILNADU, INDIA
It is our sad duty to pass along the information that the knowledgeable Mr.Shankar was lost to Covid/Corona.
He was awarded with honorable medal by then Indian president Ms. Pratibha Patil. R.I.P.
A. By just knowing Total alkali you shall know only the bath strength, only after you find a free alkali and find out its ratio between 1.4-1.8 your degreasing will be proper.
Otherwise though your total alkali may be 33 or more than that and if free alkali is also high (30) degreasing will not occur, even with a longer dipping time.
In another instance, if your total alkali is just 12 and free alkali is just 8.5 or so, then also you shall get a perfect degreasing with a longer dipping time.
I emphasize on the ratio between the total and free alkali you should maintain the ratio to get perfect degreasing.
- Coimbatore, TAMILNADU, INDIA
It is our sad duty to pass along the information that the knowledgeable Mr.Shankar was lost to Covid/Corona.
He was awarded with honorable medal by then Indian president Ms. Pratibha Patil. R.I.P.
Hi Shankar. You are exceptionally knowledgeable about this; thanks.
Regards,
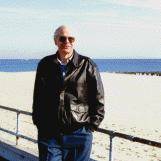
Ted Mooney, P.E.
Striving to live Aloha
(Ted is available for instant or longterm help)
finishing.com - Pine Beach, New Jersey
Q. I need schematic diagram and brief details of Zinc phosphating process.
Naresh Darshini- Hyderabad, Andhrapradesh, India
January 13, 2014
A. Hi Naresh , The schematic flow diagram of zinc phosphating :
Start -> SURFACE PREPARATION : Pre-Cleaning -> Degreasing -> Rinsing -> Rinsing -> Pickling -> Rinsing -> Rinsing -> Activation -> ZINC PHOSPHATING -> Drag Out Rinse -> Rinsing -> POST TREATMENT : Passivation -> Air Drying -> INSPECTION -> Oiling -> Packing.
Regards,
Process Engineer - Tumkur , Karnataka , INDIA.
May 8, 2014
Q. I AM RUNNING A POWDER COATING PLANT WITH TANK CAPACITY OF 2500 Ltrs. BATH ZINC PHOSPHATING PROCESS, WHAT IS THE VALIDITY OF THE ACIDIC DEGREASER TANK PROVIDED THE OIL CONTENT IS AS PER NORMS.
ASHOK SURVEPRETREATMENT - Mumbai, Maharashtra, India
January 13, 2014
A. Hi Ashok. When doing electroplating on steel, which demands a very clean surface, alkaline cleaning is used without exception. No one would even even attempt just acid degreasing, so there is no doubt that it is a less powerful cleaner and doesn't leave the surface truly clean.
But does acid degreasing leave it good enough for your phosphatizing process? It's hard to say; it probably depends upon what are the norms you speak of? Good luck.
Regards,
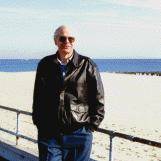
Ted Mooney, P.E.
Striving to live Aloha
(Ted is available for instant or longterm help)
finishing.com - Pine Beach, New Jersey
pH of Every Tank in a Zinc Phosphate Line
⇦ Tip: Readers want to learn from your situation;
so some readers skip abstract questions.
Q. Dear Sir,
Please give me information of pH of chemicals:
1. Degreasing + De rusting.
2. Water rinse
3. Activation
4. Phosphating
5. Water rinse
6. Passivation
Doing business - Ahmedabad, Gujarat, India
July 19, 2014
A. Hi cousin Baiju. The zinc phosphating bath operates at a pH of 3.1 to 3.4 per AES illustrated lecture "Theory and Practice of Phosphatizing", but optimum pH actually depends on phosphate concentration and other factors. The process is actually controlled more by "points" and free acid vs. total acid, rather than by pH. The final rinse should be acidulated. The passivation will probably be at a pH of 4-5.
Please try to tell us what you are up to with your question. It helps the readers because they are rarely interested in dry tabulations of values, presented without direction or context. And it can also help you because our readers can correct a poster's misunderstandings ... but they can't do that for you unless you express your theory, situation, or motivation. Good luck!
Regards,
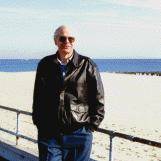
Ted Mooney, P.E.
Striving to live Aloha
(Ted is available for instant or longterm help)
finishing.com - Pine Beach, New Jersey
⇦ Tip: Readers want to learn from your situation;
so some readers skip abstract questions.
Q. What is the effect of post-phosphating rinse with neutral pH water (pH ~ 7) at ambient temperature?
Does the rinsing temperature have any effect?
- Batam, Indonesia
November 7, 2014
A. Hi Donno. This is zinc phosphating you are speaking of? Any dried salts left from the phosphatizing process will cause the paint to blister. Warm water tends to rinse more quickly and effectively than ambient or cold water.
"Please try to tell us what you are up to with your question... "
Regards,
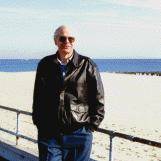
Ted Mooney, P.E.
Striving to live Aloha
(Ted is available for instant or longterm help)
finishing.com - Pine Beach, New Jersey
⇦ Tip: Readers want to learn from your situation;
so some readers skip abstract questions.
Q. Hi all
I wanted to know how to control the pH of conversion coating bath in pretreatment process for powder coating as it is one of the important parameters in maintaining the bath.
Regards
Snehal
- PONDA GOA INDIA
November 20, 2014
⇦ Tip: Readers want to learn from your situation;
so some readers skip abstract questions.
Q. Dear sir we want to know about how to make chemical of seven tank process, and how to check powder and its rinse, and technical process of seven tanks.
Kalyansinh devda- Ahmedabad,Gujarat, India
September 21, 2018
September 2018
(affil links)
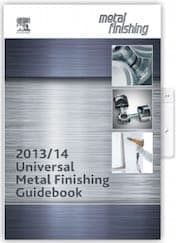
free pdf is currently available from academia.edu
A. Hi Kalyansinh. Any of the books I mentioned earlier will answer a lot of your questions, and there are other other good phosphatization books as well, but the Metal Finishing Guidebook can at least get you started on those questions. Download it TODAY as availability is always shaky.
You didn't introduce yourself so we don't know what you are aware and unaware of, but if you don't know, it is customary to buy proprietary processes rather than to try to formulate such solutions from commodity chemicals; that way the vendor will also give you technical data sheets explaining how to check things. If you want to formulate your own phosphating solution you will need to make some decisions about the type you wish to make. Good luck.
Regards,
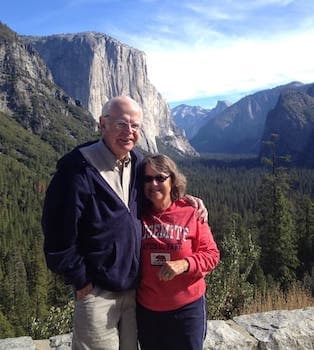
Ted Mooney, P.E. RET
Striving to live Aloha
(Ted is available for instant or longterm help)
finishing.com - Pine Beach, New Jersey
Q. Hello everyone I own a Powder coating company. My problem is I don't have enough space for seven tank process so I have an idea to keep the seven tank in roof top and single tank in working area. My idea is to bring the chemicals one by one to the tank which I keep in the workplace. Will this technique work. I can fit NRV so mixing for chemicals can be very very less.I need to know will the process work?
Arun bhabu- Tamil nadu, India
October 14, 2018
A. Hi Arun. There have been a number of attempts towards that approach in metal finishing, but they mostly have seemed to be a flash in the pan rather than an enduring viable solution. I personally don't think it's the way forward.
If you don't have room for 7-step zinc phosphatizing, maybe top notch 3-step iron phosphatizing with quality proprietaries is a more practical approach?
Regards,
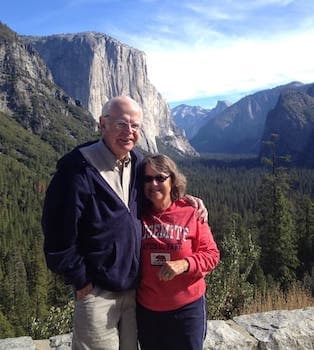
Ted Mooney, P.E. RET
Striving to live Aloha
(Ted is available for instant or longterm help)
finishing.com - Pine Beach, New Jersey
![]() |
Q. Dear sir, NIHON PARKERIZING INDIA PVT LTD - Mohali India April 7, 2019 A. Hi Narendra. I assume you are referring to Cathodic ElectroDeposition Coating? Please search the site for "CED Coating" as we have dozens of threads on the subject and have recommended two books about it. Although phosphatizing usually precedes CED coating as a pretreatment for it, CED coating really has nothing to do with phosphating. It is a special way of painting whereby the work is immersed in a tank which contains polymers, voltage is applied to the work, and the resulting current causes changes in the polymers in the tank, converting them to paint deposited onto the item. It's chief advantages over other painting methods include the fact that the paint is very thin, and that the deposited paint is electrically insulating such that the current is continuously diverted away from areas of the part where the paint has deposited, to lower current density areas of the part, such that very even coverage is possible. Regards, ![]() Ted Mooney, P.E. RET Striving to live Aloha (Ted is available for instant or longterm help) finishing.com - Pine Beach, New Jersey April 2019 |
⇦ Tip: Readers want to learn from your situation;
so some readers skip abstract questions.
Q. Dear sir,
Can I Know what are the tests for pretreated components to find whether they are Good or Bad.
Thanks & Regards
Kalyan
HBL POWER SYSTEMS - VIZIANAGARAM, ANDHRAPRADESH, INDIA
April 15, 2019
![]() |
3-step, 5-step, or 7-step Phosphating for AlmirahsQ. We are manufacturer of almirahs from crc sheet. - Rajkot Gujrat India A. Hi Chirag. If this furniture is used only indoors, and you are a "me too" manufacturer rather than a boutique name brand, 3-steps should be fine. Good luck. Regards, ![]() Ted Mooney, P.E. RET Striving to live Aloha (Ted is available for instant or longterm help) finishing.com - Pine Beach, New Jersey June 11, 2019 |
Iron phosphate vs. zinc phosphate
Q. Estimado Sr. ted Mooney, el proceso de fostatacian en hierro tiene la misma calidad que la fosfatacian en zinc?. Cuales son sus principales diferencias?. Lo usare para pintar chasis de motos.
Alejandro Sanchez Conchafabricacion de chasis de motos - Lima, Lima, Peru
August 19, 2019
by Biestek & Weber
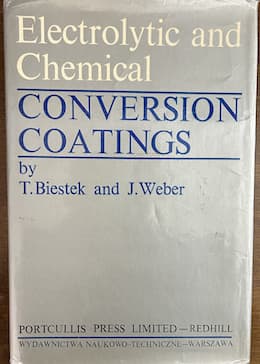
on AbeBooks
or Amazon
(affil link)
A. Hola Alejandro. Perdon: No hablo espanol...
Iron phosphatization is a much thinner coating, and is not the equal of zinc phosphatization, but it usually considered sufficient or equal -- except for exterior use in the weather; even then it is often used, and it is cheaper and easier. If the component will be severely bent after powder coating, iron phosphating is actually often preferred for better adhesion.
Regards,
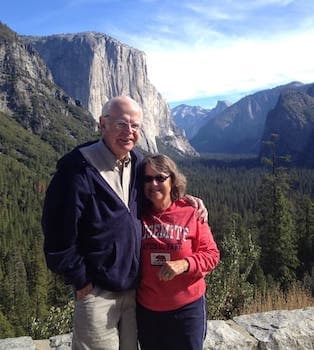
Ted Mooney, P.E. RET
Striving to live Aloha
(Ted is available for instant or longterm help)
finishing.com - Pine Beach, New Jersey
August 2019
Components used in degreasing & derusting
⇦ Tip: Readers want to learn from your situation;
so some readers skip abstract questions.
Q. Hi this is prit
I wanted to know the various components used in the degreasing & derusting process in the 7-tank process.
- Mumbai, India
December 6, 2019
A. Hi Prit.
Thread 11573 is a good start on a discussion of the components in degreasing processes; and hydrochloric acid is the most common building block for derusting (but inhibitors or acid extenders are usually added), so thread 32106 is probably a good start for derusting.
But if you're working in a finishing shop it does little good to engage in theoretical discussions about saponification, wetting & emulsifying, de-flocculating, chelating/sequestering, buffering, and inhibiting because people have spent decades optimizing & testing these processes, and you need to purchase a proven proprietary solution, not waste time fooling around trying to mix commodity chemicals.
But if you are a student studying the chemistry, it doesn't help you to be told that finishing shops purchase proprietary cleaning formulations from specialist suppliers rather than attempting to home-brew them; you'll want us to name books and reference materials...
And if you are a chemist working for a supplier trying to improve a formulation, you'll need to start by building a handy library of patents as well as the books.
So please start with who you are and why you want to know, and then we can probably help you much more efficiently. Meanwhile, best of luck!
Regards,
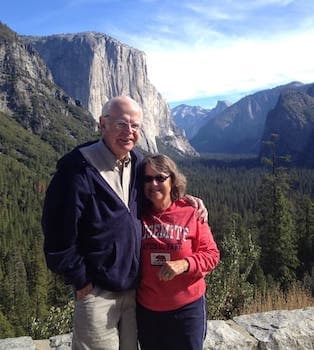
Ted Mooney, P.E. RET
Striving to live Aloha
(Ted is available for instant or longterm help)
finishing.com - Pine Beach, New Jersey
Q. Hey,
I am Navin. My client issue is post 7-tank and cleaning they used to find metal pipes still non-alkaline and even after dipping into Rust preventive oil not preventing surface from rust. Need your guidance.
Business development - Ludhiana, Punjab, India
December 22, 2021
A. Hi Navin
You can probably give the pipes a quick dip in your alkaline cleaner after phosphatizing if pH concerns you. But remember that phosphatizing is a pretreatment and is not intended to be a final finish.
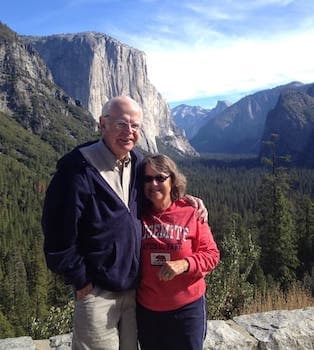
Ted Mooney, P.E. RET
Striving to live Aloha
(Ted is available for instant or longterm help)
finishing.com - Pine Beach, New Jersey
Q, A, or Comment on THIS thread -or- Start a NEW Thread