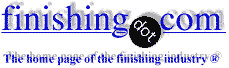
-----
Cleaning oil/fat from steel surface
November 11, 2021
Q. Hi all.
I look after a coconut oil yoghurt plant in Raglan, New Zealand.
We are out in the country and don't have proper sewer facilities to drain our washing up water. This has probably less than 5% yoghurt and part of that is coconut oil. We use caustic to create saponification to clean the systems.
Up the hill is a avocado orchard that has agreed to use our cleaning water for irrigation. Smiles all around!
Until after some time the orchardist noticed the fat leaving residues on his dirt.
So now we have to separate the fat from the saponified water mix.
We looked at filtering with maybe saw dust/chips (because we have access to large volumes of these) but we need to get rid of just over 10,000 litres of this mix per day.
Could I use a mild acid like vinegar
⇦in bulk on
eBay
or
Amazon [affil link] to release the fat?
We can quite easily chill large volumes so we could just remove the sheets of fat from the top of tanks, we just need the oil to float to the top.
Any solution has to be avocado growing friendly. :-)
Any ideas would be greatly appreciated!
Thanks very much in advance!
General engineering in a coconut yoghurt plant - Hamilton, New Zealand
A. Hi Rino
Probably, if you add a perforated pipe with compressed air at the bottom of a chilled tank (air agitation), it may help to bring solidified coconut oil particles to the top for skimming and filtration. However, it is not clear how much foaming will be created...
This is one of the most amazing posts I have seen on finishing.com. Good luck to you!
- Winnipeg, Canada
December 30, 2021
January 2, 2022
Thanks Leon!
After some experimenting we found that a PH 5.3 or lower causes the fat to break loose and float to the top.
So now we use an automated doser with sulfuric acid to get the PH to that after close of business. The tank contents is pumped around to ensure even mixing.
We then allow it to settle (read oil to rise) for some 4 hours.
Then we pump the relatively clean water from the bottom to the orchard.
At 1/4 of the tank the pump stops.
We have 5 swimming pool type skimmers at that level which will now suck the grease of the top. To push the grease to the skimmers we have an air hose with a number of small holes blowing the fat from the other side of the tank towards the skimmers. This only takes about 7 minutes to clear the surface.
Now we pump more clean water out down to 10% and we are ready for the next batch.
The grease is now in a sludge tank which we also allow to settle after which we can remove some more clean water from the bottom. The skimmers pull in some water to operate efficiently.
I did put some samples in the fridge but to my surprise the fat sank to the bottom of the jar!? Once warmed up to room temp the fat rose again. I didn't see that one coming..
General engineering in a coconut yoghurt plant - Hamilton, New Zealand
⇩ Related postings, oldest first ⇩
Q. Some steel sheets imported from Russia has a very thick oil/fat to prevent corrosion. We have difficulty to clean this film from the surface for pretreatment for painting. Is there any recipe that you would advise, other than proprietary chemicals?
Tim Ulu- Istanbul, Turkey
2001
A. One option for the removal of oils and greases is an alkaline cleaner. This is probably the most common method of grease and oil removal. Since you are not looking for proprietary chemistry, a caustic solution of sodium hydroxide and water will saponify the oils and greases on the sheet, dissolving them in the water. The sheets would then require adequate rinsing, but should be clean. I don't know how long you would need to immerse the material however. This works especially well if you have an ability to spray this solution onto the parts to actively help remove the contaminants. We typically use a chemistry supplied by someone, but the theory is the same. For some added help, you can squirt in some liquid dish detergent or similar to the solution to add some surfactants to help clean off the grease.
Jim Hanley- Redmond, Washington
2001
2001
A. Boiling water does an excellent first course on *some* fats and greases. Take a sample piece and boil it in a beaker [beakers on
eBay
or
Amazon [affil link] on a hotplate and see what happens. There is no cheaper, more recyclable, more ecological first step for cleaning than boiling water. There is also nothing as worthless for the wrong kinds of fats and greases! Don't try it on a production line until you see whether it works in the lab -- been there, done that, wasted time & money, kicked myself :-(
Good luck.
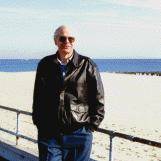
Ted Mooney, P.E.
Striving to live Aloha
(Ted can offer longterm or instant help)
finishing.com - Pine Beach, New Jersey
A. The first reply recommending an alkaline cleaner is close, however using the wrong ratios or and wrong chemistry can damage the surface. Caustic soda (sodium hydroxide) is a highly corrosive substance to both your skin and your steel. I strongly recommend against its use. This process may create the corrosion that the fats were used to prevent. Also, without the addition of coupling agents the fats can redeposit onto the surface leaving a thin film of undesirable oils on the steel. This film will prevent the proper adhesion of any secondary surface coatings. Using a professionally formulated product that has been been proven to be non-corrosive, non-toxic and biodegradable is the best choice to defat/ degrease your steel parts.
Rick Morgando- Skokie, Illinois, USA
July 2, 2010
July 6, 2010
A. Hi, Rick. Yes, proprietary cleaners are usually employed and are better, but Tim very specifically asked for non-proprietary formulations -- presumably because this fat is so thick that it will consume proprietary cleaners too fast to be economically realistic. That's why Jim suggested caustic plus detergent and I suggested trying boiling water as a first step to see how much of the fat (if any) is removed.
But sodium hydroxide does not attack steel. Most soak clean and electroclean tanks (and their anodes and heating coils, etc.) employed in plating lines are mild steel and many have been in production while containing high concentration caustic soda ⇦liquid caustic soda in bulk on Amazon [affil link] cleaners at near boiling for many decades.
Yes, caustic soda is dangerous to people and should be used only in industrial settings, not at the consumer level.
Regards,
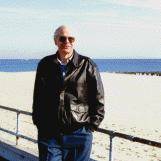
Ted Mooney, P.E.
Striving to live Aloha
(Ted can offer longterm or instant help)
finishing.com - Pine Beach, New Jersey
![]() |
Q. Can I make the case more difficult? - cairo, egypt July 10, 2012 A. Yes, that is much more difficult Ahmed. Caustic definitely attacks aluminum. A proprietary cleaner formulated for aluminum, used in an ultrasonic cleaning tank, is probably your best bet. But next time, clean the aluminum BEFORE heating it to 400 °C! Burned on, carbonized contaminants are very difficult to remove. Regards, |
Q. Dear All
Since I deal metal shaping, I do some general drawing. During this process, of course I use oil to improve the drawn surface. But, it's become a problem during annealing treatment. How can I remove the oil from my metal surface?
So far, I use phosphoric acid, but it's not enough.
Thank you.
steel Production - South Korea
August 13, 2014
August 14, 2014
A. You don't say what metal.
Acids will not help with grease. Try a heated alkaline cleaner. Or, depending on local laws, there's always vapor degreasing. I wouldn't go that way, though.
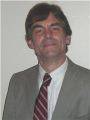
Dave Wichern
Consultant - The Bronx, New York
August 16, 2014
A. Dave is quite right, acids have no degreasing properties.
I suggest that your best option is to consider a water soluble drawing compound which will be much easier to remove.
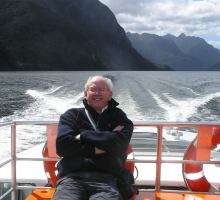
Geoff Smith
Hampshire, England
![]() |
Q. Thank you Dave & Geoff. steel Production - South Korea August 21, 2014 A. Hi Restu, - Penang , Malaysia August 21, 2014 |
Q. I put tons of grease on tool through my caustic vats and there's no trace of it when the solution is changed annually, the solution is pneumatically agitated, where does the grease go?
brendan keenan- peterhead scotland
December 10, 2014
December 2014
A. Hi Brendan. Your greases are apparently based on animal fats: fats + caustic => soap
This is called saponification. Petroleum greases unfortunately do not saponify this way.
Regards,
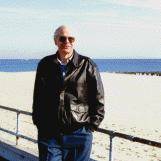
Ted Mooney, P.E.
Striving to live Aloha
(Ted can offer longterm or instant help)
finishing.com - Pine Beach, New Jersey
Carbon steel degreasing
Q. My simple question for all the genius scientists here is:
the best way for cleaning the carbon-steel from the fats, oil contamination and organic substances in order to prepare it for the coating of PTFE. I use for its cleaning Trichloroethylene but it is very expensive and has bad effects for the environment.
What should be the best way of cleaning Carbon Steel and also protect it from the atmospheric attack (corrosion)?
Need better solution for degreasing.
- Hyderabad,Sindh Pakistan
July 27, 2016
July 2016
A. Hi Anis. Hot alkaline cleaning is probably the first choice for degreasing carbon steel. Still, if the trichloroethylene is used in a modern vapor degreaser, you should be using little of it, and the effects of the fugitive emissions minimal. Are you wiping with it, dipping into a tank of liquid, or using it in an old fashioned vapor degreaser rather than a modern one?
Cleaning steel does not protect it from corrosion though. After cleaning, the components should probably be phosphatized before the PTFE coating operation. Is it a PTFE powder coating applied in a fluidized bed, or what?
Regards,
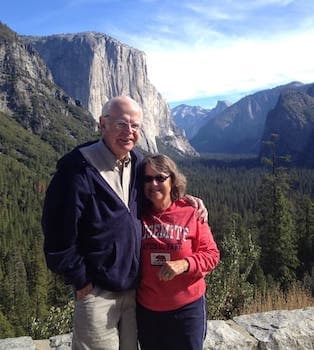
Ted Mooney, P.E. RET
Striving to live Aloha
(Ted can offer longterm or instant help)
finishing.com - Pine Beach, New Jersey
Q. Sir,
it is old kind hot showering of trichloroethylene with pressure of 40psi, and drying with compressed air; but cleaning is not up to the mark.
I have to coat carbon steel with PTFE for it carbon steel must be degreased properly.
Thanks.
- Hyderabad,Sindh Pakistan
July 31, 2016
A. Hello Anis,
Generally, solvents are the best option for reliable degreasing. Use of a air-tight or airless cleaning system will minimize solvent consumption and environmental impact. This type of cleaning system will yield the maximum benefit when operated with chlorinated hydrocarbon, hydrocarbon or modified alcohol and will be the best option for repeatable and reliable degreasing results.
As Mr. Mooney mentioned, corrosion protection has to be considered because the cleaner the parts' surfaces, the more active they are.
- Clawson, Michigan, USA
October 28, 2016
How to degrease zinc coated sheet metal without dissolving the zinc?
Q. Dear sir,
What kind of degreasing material can be used with Zinc coated metal sheets. Alkaline medium seems like dissolving coated zinc layer. Is there any suggestion for zinc coated metal degreasing agent without dissolving coated zinc layer?
- Sri Lanka
August 26, 2016
October 2016
Hi Thanura. It is true that alkaline cleaners designed for steel are too aggressive for zinc. But your chemical supplier should be able to formulate a mildly alkaline cleaner, and you may also be able to do cathodic electrocleaning for better degreasing.
Regards,
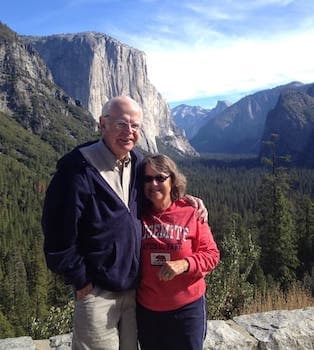
Ted Mooney, P.E. RET
Striving to live Aloha
(Ted can offer longterm or instant help)
finishing.com - Pine Beach, New Jersey
Q. Dear All,
I was wondering that is there any Standard procedure for measuring the efficiency of detergents for cleaning metal oily-surfaces?
If there is any, please let me know!
I appreciate it.
Thanks
Student - Stillwater, Oklahoma, USA
January 9, 2017
January 2017
A. Hi Atashnezhad,
According to the Garden State Branch AESF Electroplating Course Manual, the basic requirements of a good cleaner are:
b. Wet & emulsify
c. Deflocculate
d. Chelate or sequester
e. Buffer
f. Inhibit.
So it's obviously difficult to quantify the efficiency of detergents for cleaning from the first principles of these 6 requirements. So the measure most widely used in the electroplating industry is the very simple "water-break test". After cleaning, rinse water should sheet and wet the surface completely with no breaks at all -- almost the exact opposite of what you would see if a teflon coated pan is rinsed. This freedom from water break should be sustained after dipping in mild acid (to remove any surfactants) and rinsing again. Good luck with your studies.
Regards,
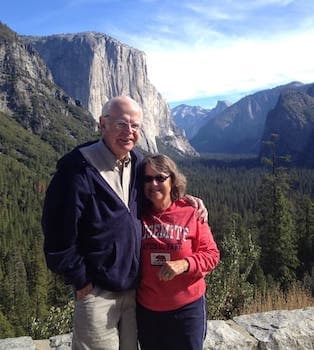
Ted Mooney, P.E. RET
Striving to live Aloha
(Ted can offer longterm or instant help)
finishing.com - Pine Beach, New Jersey
Q. Dear Sir,
Thank you for your information provided above. My question is what's the proper timing & concentration of soaking pipes carbon steel to be cleaned from grease using sodium hydroxide and what is the proper purging & permanent coating for the pipes
Petromaint - Alexandria Egypt
January 15, 2017
Oil /grease removal
Q. Hello Professionals,
What is the best methods to removing oil & grease from the components? As it required before any plating or coating operations?
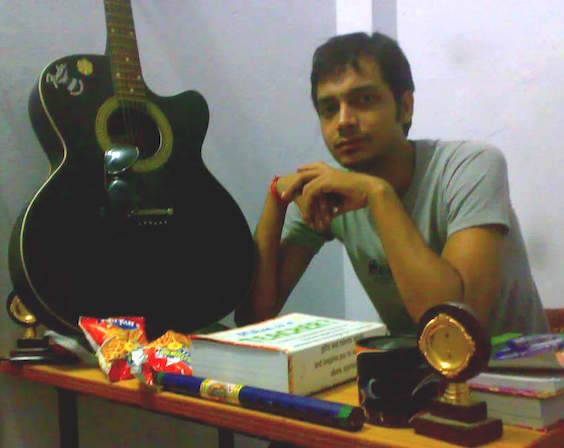
Neeraj Rao NKR
Learning - New Delhi, India
October 7, 2018
A. Hi Neeraj. We appended your inquiry to a thread on the subject. The first question is what is the substrate? For pre-cleaning of steel for subsequent plating the most accepted cleaning method is alkaline electrocleaning at nearly boiling temperature. Painting and powder coating do not need quite so spotlessly clean a surface, so a 3-in-1 iron phosphate (combination cleaner and phosphating) is probably the most common pretreatment; but a 5 to 7 step zinc phosphatization sequence with the first step being hot alkaline cleaning is very common. In the developed world, proprietary formulations rather than home brews are usually employed because the requirements usually include saponification, wetting & emulsifying, de-flocculating, chelating/sequestering, buffering, and inhibiting.
The subject is quite broad, however, and most plating and coating textbooks devote at least a couple of chapters to it. Good luck.
Regards,
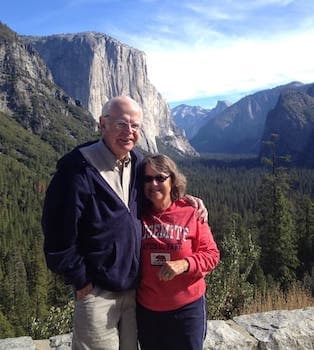
Ted Mooney, P.E. RET
Striving to live Aloha
(Ted can offer longterm or instant help)
finishing.com - Pine Beach, New Jersey
October 2018
October 9, 2021
Clean my truck frame often, always good to know a better way to remove road salt, grease, dirt. I often use oven cleaner ⇦ on eBay or Amazon [affil link] .
Just liked "Striving to live Aloha"
-- a cup of coffee on beach for me.
Truck Driver - Elsa, Texas
Q, A, or Comment on THIS thread -or- Start a NEW Thread