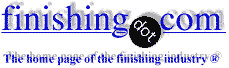

Continue with this -----
Zinc plating blind holes / threaded holes
... or jump to this related thread if your interest is primarily dimensional questions:• Topic 2906 "Plating external threads: dimensional effects"
• Topic 12211 "Thread dimensions after plating"
• Topic 22409 "Zinc Plating Thickness and Tolerance on Fasteners"
• Topic 57493 "Zinc Plating Internal Threads: dimensional changes & coverage issues"
Quickstart:
Plating thickness is essentially proportional to the applied current and time (per Faraday's Law). But electricity wants to take the path of least resistance, so edges, corners, and protrusions get thicker plating, while recesses and inside diameters get lesser, sometimes none.
Some plating solutions (usually the more chelated or complexed ones) exhibit better "covering power" or "throwing power" than others. Cyanide zinc plating solutions and alkaline zinc do better at this than acid zinc.
Addition agents (brighteners) can also help with covering and throwing power by being attracted to the high current density areas and somewhat covering/blocking/insulating them to steer the current away so it flows towards other areas.
Holes, especially blind holes not only have coverage issues, they can also be a problem by causing air locks which prevent the process solutions from getting into the hole, or by dragging solutions cupped in the holes to the next tank.
Q. What depth, if at all, can I expect ASTM B633 type II Fe/Zn5 plating, should withstand the nominal 5 microns of Zn and the salt spray test accordingly, for 3/8" to 1/2" blind threads.
Rudi PeresMech. engineer in the electronic industry - Ramat Gan, Dan area, Israel
2004
A. Hi, Rudi. Most thickness specifications only cover the area that can be touched with a 3/4" dia. ball; some may specify "coverage" of all areas, but not thickness. Alkaline zinc offers better coverage than acid zinc, so you might verify that your plater is using an alkaline process.
You can specify and obtain anything you want, including generous plating thickness inside blind holes, but it requires special procedures like internal anodes, holes up during plating and down during tank-to-tank transfer, etc., so it can be unaffordable for production parts.
Regards,
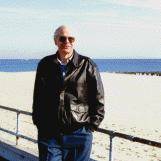
Ted Mooney, P.E.
Striving to live Aloha
(Ted is available for instant or longterm help)
finishing.com - Pine Beach, New Jersey
Q. I have a component which has blind holes (M10) to a depth of 20 mm, and I am unable to get the plating (Alkaline Zinc) to the total depth. Is it possible to get the plating on a production lot?
Nanjund BhatSMS, Sheet Metal - Gurgaon, Haryana, Indiana
2006
A. Hi Nanjund. Anything can be done, including getting full plating in a blind hole whose depth is twice its diameter. But when you say "on a production lot", I think you are implying "without taking special measures" or "without special and exotic jigging". If it's a part that is barrel plated, it's not likely. You can do it in rack plating, with auxiliary anodes, and tilting the rack to eliminate air pockets and carryover of solutions, but probably not without these special measures. The rule of thumb, although mileage may vary, for ordinary plating without those special measures is that you will get coverage to a depth about equal to the diameter of the hole (i.e. 10 mm in your case).
Best of luck.
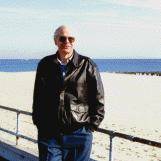
Ted Mooney, P.E.
Striving to live Aloha
(Ted is available for instant or longterm help)
finishing.com - Pine Beach, New Jersey
Q. Hi ! I am designing a special nut which technically termed as "Insert". This material is used for sling support when lifting heavy equipments or parts.
The material is a deformed bar with Diameter 19 mm and an inside thread at M12. The depth of the thread is 30 mm. Customer requirement is to penetrate yellow zinc chromate inside the thread, and I mean all over until the bottom of the thread.
The problem is, during the basic barrel plating, the output does not satisfy the plating requirement. The M12 thread has not been fully covered with zinc chromate. The bottom has no plating at all.
What possible solution must I apply in order to make electroplating penetrate the whole thread depth ?
Product designer - Subic Bay, Olongapo City, The Philippines
February 17, 2009
A. If this is a blind hole, You will never get plating to the bottom of the hole. Typical plating will only go the depth of the hole that is equal to the width of the hole-Aspect ratio, and this does not hold for tiny holes.
If they insist, graciously tell them that it is an absolute impossibility, and pass on the job. You can help your cause if you can find a couple of specifications that have the coverage measurement in the QC section. The mill spec says something like coverage if it can be touched by a 3/4" ball.
for Shops, Specifiers & Engineers
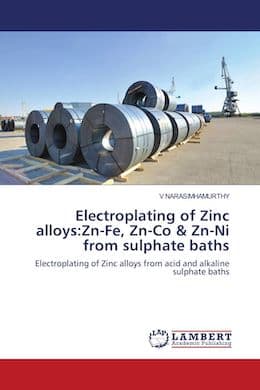
from eBay, AbeBooks, or Amazon
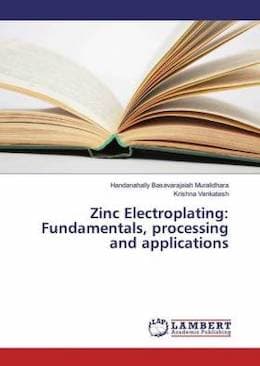
from eBay, AbeBooks, or Amazon
"Alkaline non-cyanide zinc plating with reuse of recovered chemicals" by Jacqueline M. Peden (1994)
from (U.S. EPA)
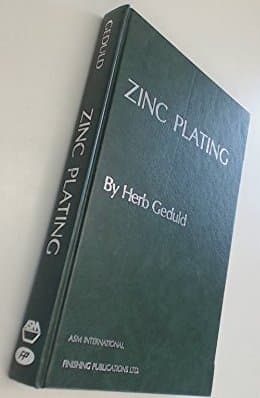
from eBay, AbeBooks, or Amazon
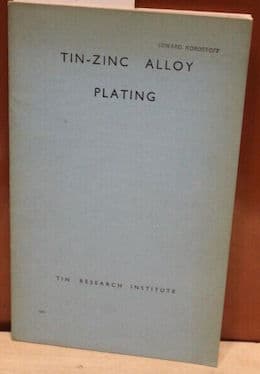
from eBay, or AbeBooks
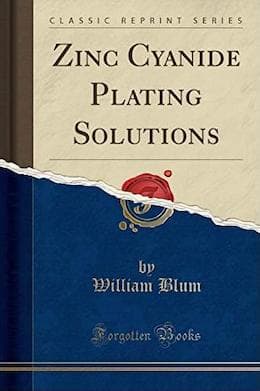
from eBay, AbeBooks, or Amazon
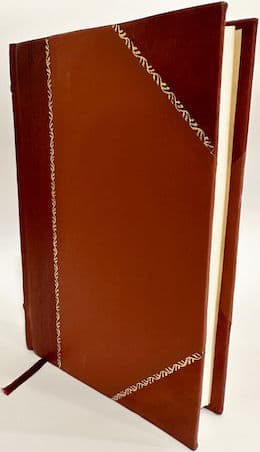
from eBay, AbeBooks, or Amazon
(as an Amazon Associate & eBay Partner, we earn from qualifying purchases)
- Navarre, Florida
A. Sometimes it can be impossible to cover inside holes.
In general... I recommend the following to get maximum coverage...
1) use alkaline zinc process
2) keep the load size of the barrel as small as possible
3) apply the highest current densities that are possible without burning
4) pretreatment and activation can be critical as well to ensure that you have a clean and active surface that readily accepts the initial electroplating deposit.
- Budapest, Hungary
A. Dear Jason,
In order to get Chromate on the zinc layer, you should have certain micron of Zinc layer then you will have chromate layer on it.
In your case your should find a good throw zinc plating (alkaline non cyanide zinc) and in this case I agreed with Thomas.
Just try Thomas recommendation (see above)
Good luck.
Best regards,
electroplating chemicals supplier- Jakarta, Indonesia
A. YES ALKALINE NON CYANIDE IS BEST ANSWER.
ASK THE CHEMICAL SUPPLIER TO PLATE FEW PIECES FIRST .
THEN THINK OF STARTING THE PROCESS.
REGARDS,
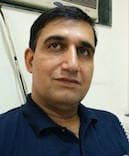
Ajay Raina
Ludhiana, Punjab, India
A. Again, if I read the post correctly, he is trying to plate a blind hole about 1" deep and 1/2" in diameter. Barring using an internal anode, I seriously doubt if any plating process will put enough metal on the bottom to allow the chromate to show color.
James Watts- Navarre, Florida
Q. Hi Guys,
I have a problem with low carbon steel block size 50 x 8 x 16 mm, this block has two blind holes (dia. M3) of depth 8 mm. Block is zinc plated as per ASTM B633, Fe/Zn 8, TYPE III.
This block assembled to a plate made of CRS, with help of hinge. We found rust on threads and mating surface of hole.
Supplier is telling "The blind holes cannot be cleared out effectively after zinc plating. The Zinc plating process leaves residual chemicals that cannot be completely rinsed out. As a result, internal corrosion on the threads occurs and over time leaches to the hinges."
Is that right or any reason for this rust formation?
Now we are making blind holes to through hole is it correct solution to this problem?
Kindly advise me with proper solution.
- Bangalore , Karnataka and India
November 4, 2016
A. Hi santhosekumar. It is true that you cannot expect plating in these holes, but you can expect carryover of plating solutions.
You gave us the size of the block as 50 x 8 x 16 mm, and the depth of the blind holes as 8 mm. This means that if you moved to through-holes they would be dia M3 by 16 mm. That would reduce the carryover of zinc plating solution, but you would still not have plating inside the full length of the holes -- so it would offer an improvement, but not really a full solution.
If this is low volume production, it may be possible to plug those blind holes before plating to retain any rust-proofing solution in them rather than plating them, while also keeping the plating solutions out of them. If it is high production barrel plating where plugging won't prove practical, then through holes are probably you best bet.
Regards,
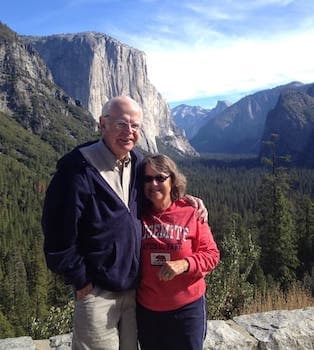
Ted Mooney, P.E. RET
Striving to live Aloha
(Ted is available for instant or longterm help)
finishing.com - Pine Beach, New Jersey
8d Blind Bore Plating
Q. Please could you suggest the best ways to plate down 8d blind bores?
Brad EbreyPlating Shop Employee - Coventry United Kingdom
March 1, 2018
A. Hi Brad. Almost nothing is impossible, but the details of how to achieve this will depend on the material of the substrate, what metal you want to plate it with, and the actual dimensions, not just the 8D ratio.
Auxiliary anodes will surely be required if it's an electrolytic rather than electroless process; rotating the part to prevent air locks and solution carryover will probably be required, and some manner of solution exchange will probably be required to prevent depletion if the bores are tiny but probably not if they are large (because solution volume is proportional to the second power of the diameter).
Regards,
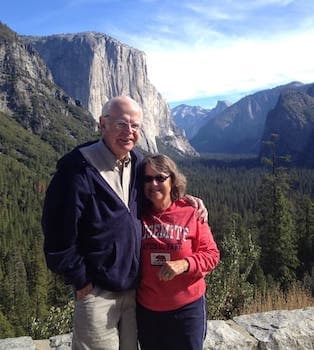
Ted Mooney, P.E. RET
Striving to live Aloha
(Ted is available for instant or longterm help)
finishing.com - Pine Beach, New Jersey
Q. Hi Ted, Thank you for your help with this. The main solutions that we would be plating would be Acid Copper, Nickel, Gold, Tin. Our bore sizes generally tend to be quite small (e.g.: 3 mm+) This is mainly done via both barrel and Jig plating (for larger parts). If you have or anyone else has any further suggestions this would be very much appreciated.
Many Thanks
- Coventry, United Kingdom
? Who designed that component?! -- rhetorical question :-)
If I'm understanding, you have blind bores about 3 mm in dia. by about 24 mm deep? As previously noted, almost nothing is impossible, but this is the closest thing to it. What is the substrate, steel?
Regards,
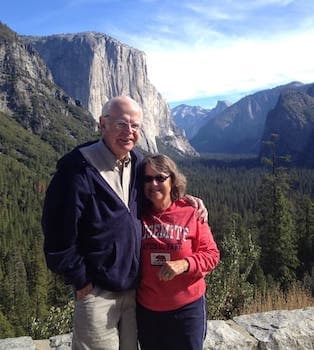
Ted Mooney, P.E. RET
Striving to live Aloha
(Ted is available for instant or longterm help)
finishing.com - Pine Beach, New Jersey
A. Hi Brad
Given one hole 3 mm x 24 deep, I could find a way of plating down it.
It would take time and research and would cost a small fortune!
As a practical production process, it is a non-starter and you must explain this to the designer. Perhaps next time he/she will consult the plater first.
At the very least a small bleed hole at the bottom will help to prevent a trapped air bubble that will negate getting any solution, even the cleaners, getting into the hole. Ultrasonics do not work. They just produce an expensive vibrating bubble! You can force the bubble out and cleaners in with vacuum but from there on getting the cleaners out and rinse/plating solution in relies entirely on diffusion.
Then your problems really start. The processes you list all have different throwing powers and the thickness down the hole will be unpredictable and unmeasurable and the hole will not be 3 mm any more.
I used to visit the drawing office regularly and veto unrealistic plating until the designers learned that it was better to ask first.
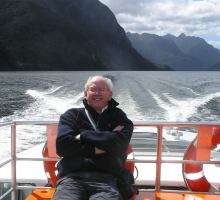
Geoff Smith
Hampshire, England
Q. The substrate is mainly Brass or Copper from what I can remember. The bores are also around 3 mm+ in depth (apologies); these parts are mainly barrel plated.
Thanks.
- Coventry, United Kingdom
A. Hi again. Sorry for apparently misunderstanding what you meant by "8d blind bores", which has resulted in some wasted postings.
You seem to be implying that you are plating the parts anyway, including both rack & barrel plating, even though you don't get coverage in the bores?
Geoff Smith's point remains that it is entirely possible that the bores cannot be plated at affordable cost, but an air hole would help somewhat.
Regards,
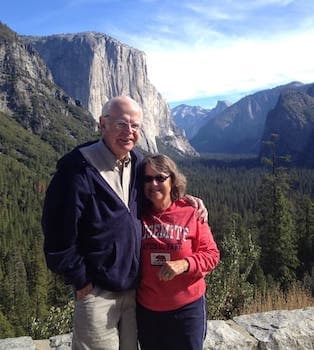
Ted Mooney, P.E. RET
Striving to live Aloha
(Ted is available for instant or longterm help)
finishing.com - Pine Beach, New Jersey
I have a small bet with myself that I know what these components are when we get an accurate description.
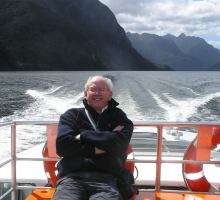
Geoff Smith
Hampshire, England
Alkaline zinc plating doesn't cover axle bolt threads
Q. We are facing Alkaline Zn Plating lack of coverage issue on threaded portion. At machining area there is not any issue. Only we are not getting plating on thread area. Before plating there is heat treatment operation followed by thread rolling then Alkaline Zn Plating.
Plating Sequence as follows-
Degreasing > Anodic Cleaning > 5-10% sulfuric Acid Dip > Descaling > Acid Pickling > Neutralizing dip > Alkaline Zn Plating.
In this process, due to inactivity of threaded area plating is not possible.
Please give solution.
- Pune, Maharashtra , India
September 4, 2018
A. Hi Anoop. Although uneven plating in the threads can have a number of causes, getting no plating would seem to indicate that the steel is not clean and active in the thread area. Are you sure that no silicone lubricants are used in the thread rolling; silicone is for practical purposes impossible to remove sufficiently for plating.
Regards,
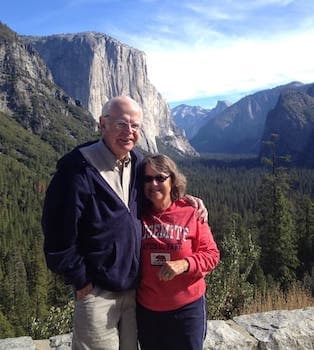
Ted Mooney, P.E. RET
Striving to live Aloha
(Ted is available for instant or longterm help)
finishing.com - Pine Beach, New Jersey
A Anoop,
No plating at threaded area looks to me like you make rack contact in this area; or threaded area not clean in your plating process.
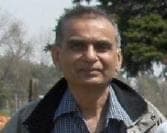
Popatbhai B. Patel
electroplating consultant - Roseville, Michigan
How to clean blind holes for acid zinc plating
Q. Is there a guideline of cleaning times of very small ID blind holes (0.044 inch) to ensure good plating of acid zinc? We have customers complaining that the holes are not plated.
Dan WatsonChicago Rivet and Machine Co. - Tyrone, Pennsylvania, USA
January 22, 2020
A. Hi Dan. How deep are these blind holes, so we don't go down the rabbit hole as in previous entries on this thread? But why do you suspect poor cleaning as the reason the blind holes don't get plated -- I don't think I'd expect them to get plated regardless of how clean they are unless they're very shallow.
Regards,
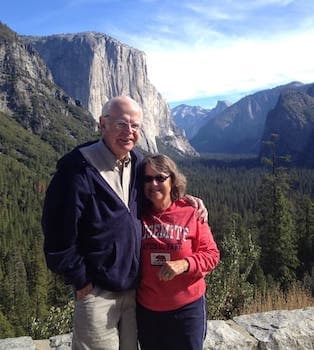
Ted Mooney, P.E. RET
Striving to live Aloha
(Ted is available for instant or longterm help)
finishing.com - Pine Beach, New Jersey
A. Hello Dan,
The company I used to work for plated similar types of holes. They were laser drilled .004" X .006" deep. The work bars in the pre- clean process had side to side agitation against the solution to ensure good cleaning and activation in the holes. We also had solution agitation through a filter pump in each process.
When we went into the plating bath we dropped the current density significantly as compared to a normal plating amperage for the bath. If memory serves me correctly the CD was as low as 3 ASF. We then stepped up the amperage after 60 minutes to 5.5 asf for 60 min then 7 for The same time. The reason for the lower current density is you want the low current density areas of the part to plate, not the surface only. The plating bath was a high throw formulation. We had vigorous solution agitation, cathode bar vibration as well as side to side cathode bar agitation against the solution. Keep in mind, this was copper plating I'm referring to but the principles are applicable. Hope this info helps you.
Retired - Winston Salem, North Carolina USA
Thank you Mark for this information. This is something we can try.
Chicago Rivet and Machine Co. - Tyrone, Pennsylvania
A. There cannot be a single method for cleaning all the various different soils. Get a sample of the drilling soil and put it on a flat panel, then determine whether your cleaning compound will remove that soil. If the cleaning compound will remove the soil from a flat panel, then run the parts up/down/completely in/completely out three times in the cleaner, to fill and drain the holes three times, then do the same in all rinses, then come back and let us know.
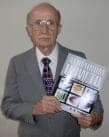
Robert H Probert
Robert H Probert Technical Services

Garner, North Carolina
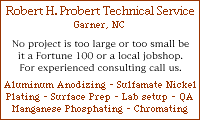
Q, A, or Comment on THIS thread -or- Start a NEW Thread