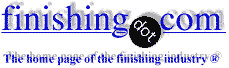
-----
Why must Copper Bus Bar be Tin Plated?
< Prev. page (You're on the last page)
Q. Hi,
I have question about oxygen free copper, specifically about C10100 (Cu-OFE) and C10300 (Cu-PHC) ? Do they need to coated/plated (tin, nickel ...) to prevent oxidation? some sources state they don't.
- Zagreb, Grad Zagreb, Croatia
February 11, 2016
A. Hi Ivan. High purity copper is quite corrosion resistant, and I'm quite familiar with applications where bus bar is not tinned. But it seems that it would depend both on the specific application and any standard codes that apply. Good luck.
Regards,
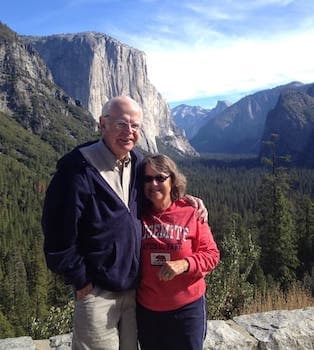
Ted Mooney, P.E. RET
Striving to live Aloha
finishing.com - Pine Beach, New Jersey
February 2016
February 18, 2016
A. This post is in response to the many questions regarding bus bars and which type of plating is best for the application.
I have worked for several large electrical equipment manufacturers over the years and there is no simple answer to which type of plating is best; however, there are only two which are exclusively accepted for electrical distribution: tin and silver.
Electrical equipment is installed indoors and outdoors and subject to moisture, salts, and reactive atmospheres; so, many years have been devoted to failure and cost analysis, and a lot of trial & error. Each has its merits and shortcomings and so knowing the environment in which the equipment is to be installed is of paramount importance.
I would suggest reading Data Bulletin 0100DB0401 "Electrical Equipment and Components in Adverse/Corrosive
Environments" published by Square D.
It is a comprehensive examination regarding choice of plating materials and would likely answer many of your readers questions.
Another document worth mentioning is Data Bulletin 0108DB0602, "Thermal Aging Study of Tin Plating on Aluminum".
Most of your major manufacturers have tomes of white papers and publications regarding electrical equipment design and failure analysis and offer a wealth of information at the click of a button.
Regards,
Large Manufacturer - Austin, Texas
A shop dating back to WWII that I worked at put a sheet of aluminum foil between the copper layers of bolted joints.
It seemed to work quite well and was certainly low cost.
- Navarre, Florida
February 20, 2016
Thanks Scott!
Very interesting, James, but I don't understand what that is supposed to do or how it's supposed to do it :-)
Regards,
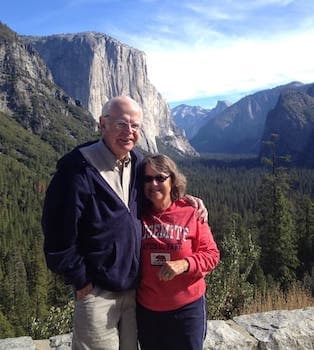
Ted Mooney, P.E. RET
Striving to live Aloha
finishing.com - Pine Beach, New Jersey
February 2016
Q. Please, what does it take to De-oxidise Bus bars and what are the steps to do it?
Charles Emmanuel Ngozi- Lagos Nigeria
July 23, 2016
A. Hi Charles. Although "De-oxidize bus bars" means "remove oxidation from bus bars", it may not be possible for anyone to answer that question except the customer who requested it :-(
It MIGHT mean lightly sand the joint area and apply anti-oxidation compound, but it might not. We'd need to see it in context.
Regards,
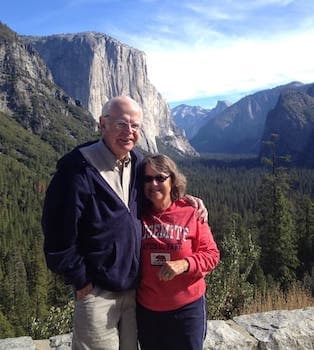
Ted Mooney, P.E. RET
Striving to live Aloha
finishing.com - Pine Beach, New Jersey
July 2016
Black-green deposit on automotive copper terminals
Q. We are facing a problem in car head light switch. There is blackish green deposition on the copper terminals (only the terminals connected to battery ground, the rest are OK). During EDX analysis of copper we observed the deposition of potassium and sulfur. Can there elements come from battery or is this related to environment or something other. Please help.
Dheerendra SinghAutomotive (car) switches manufacturer - Gurgaon , Haryana , India
September 27, 2016
A. That sounds like a reaction with pollutants in the air, likely SO2. "Blackish green" sounds like a mixture of CuS and other Cu compounds.
How's your local air quality? Perhaps you could install some kind of air filter.
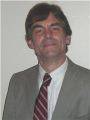
Dave Wichern
Consultant - The Bronx, New York
September 29, 2016
Q. Thank you Mr. Dave
I also think same this is like CuS, but this deposition is only on three terminal rest are OK, we have received almost 50 defective parts all have same pattern only three terminals which are connected to the battery ground have the deposition , if the cause is polluted air it should be on entire all Cu terminals.
Automotive (car) switches manufacturer - Gurgaon , Haryana , India
October 9, 2016
Q. Good Morning all!
Dear sir,
I have a doubt which type of insulation we have to provide in tinned copper busbar cutting edges whether we have to do tin coating again?
Please give a suggestion.
Regards
electrical Industries - Muscat, seeb, oman
December 19, 2016
A. Hi Sriram. It is possible that a given customer spec or industry standard requires re-plating of the ends. If you find no such spec, I guess my feeling would be that if only the contact ends of the bar are tin plated, there would not seem to be any reasonable need for plating the cut ends; but if the whole bar is tin covered end-to-end, and you have now exposed copper by cutting it, aesthetics or the possibility of galvanic corrosion might necessitate plating of the ends depending on the circumstances.
Regards,
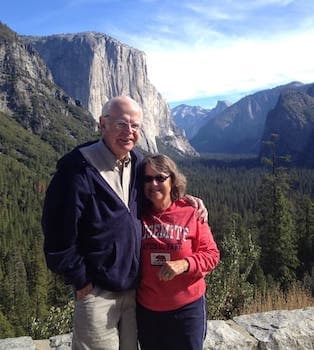
Ted Mooney, P.E. RET
Striving to live Aloha
finishing.com - Pine Beach, New Jersey
December 2016
Q. Dear sir,
Thanks for the reply.
Sometimes it may not be possible to re-Tin busbar edges. I think there is no tin sprays are available in the market. Whether zinc coating is advisable for the edges?
Regards,
electrical Industries - Muscat, seeb, oman
December 20, 2016
A. Hi again. Sorry, but zinc plating of the cut ends sounds to me like a terrible idea.
Regards,
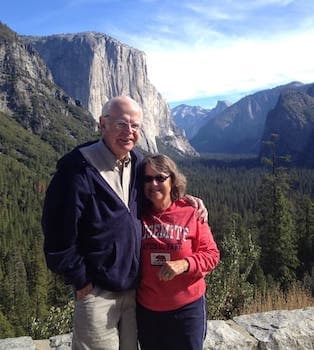
Ted Mooney, P.E. RET
Striving to live Aloha
finishing.com - Pine Beach, New Jersey
December 2016
A. Dheerendra,
An undercharged battery can cause this. I would suggest a protective coating for the Cu.
Sriram,
The thing to do, in my humble opinion, is to cut the bus bars and then tin them. The bus bars should be completely coated.
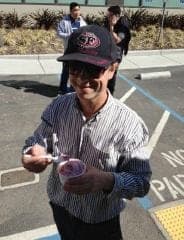
Blake Kneedler
Feather Hollow Eng. - Stockton, California
January 1, 2017
Q. Are there any methods available for tin plating over aluminium bars by spray plating method??
dhanus mohan- Coimbatore, Tamilnadu, India
December 27, 2016
? Why would you need tin plating if there is the use of a suitable oxide-inhibiting compound between the joints to stop oxidation? Yes, the exposed copper will discolor; however, that won't limit its ability to conduct 600 A or greater.
keith GoshN/A - Boulder, Colorado USA
February 20, 2017
Q. If said Tinning will not increasing Ampere rating, some cases using Uniniven cables for higher current applications please clarify
HARSHA KUMARPowertech Industires - Ajman UAE
June 15, 2017
? Hi cousin Harsha. Google comes up empty for "Uniniven" -- perhaps it's a typo.
This thread now contains more than 80 entries; to further 'clarify' the claim that tinning improves the reliability of an electrical joint but does not necessarily increase its ampacity, we would need you to take a couple of paragraphs to carefully detail your situation so we can present a detailed defense of what has been claimed. Otherwise, I don't know how to 'clarify' something which I've already repeatedly tried to make clear, when I don't even understand your posting :-(
Thanks for your understanding.
Regards,
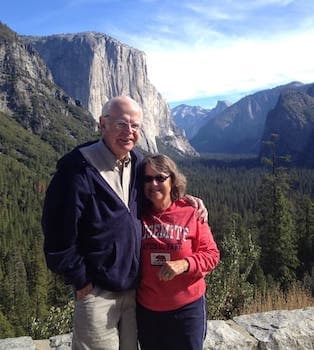
Ted Mooney, P.E. RET
Striving to live Aloha
finishing.com - Pine Beach, New Jersey
June 2017
Q. Dear Sir,
As you said low frequency current will not pass on outer surface of the conductor rather its core. My question is we are making tin coating on the copper conductor, while making the joints(as you explained in drawing) surface of two tin material is touching if this is the case current is flowing on the surface of the conductor. kindly brief me if I am wrong (resistance of tin and copper is different, tin will affect current carrying capacity of copper) .
Regards,
Jack
- Dubai, UAE
November 9, 2017
A. Hello Jack. Please imagine for a moment that you were trying to connect copper bus bars to carry current, but someone had inadvertently painted those bus bars, so they had a layer of paint on them which was interfering with a proper connection. You would need to remove that paint in order to make a good connection.
All metals except precious metals like gold & platinum react with the oxygen in the air to "paint themselves" with non-conductive oxide (tarnish) surfaces. Depending on which metal we're speaking of, this naturally forming oxide can be thick, highly insulative, and a serious problem; aluminum is an example of that, and it can never be used as a contact surface. Sometimes the naturally forming oxide/tarnish is quite thin and doesn't present much of a problem for most circuits; for example, nickel is a fine contact surface almost all the time because it's oxide/tarnish is very thin; but extremely low power & low voltage digital circuits must be gold plated so there is absolutely no oxide (tarnish). One reason that copper is plated with tin is because the oxide/tarnish which forms on tin is not as insulative and problematical as the oxide/tarnish which forms on copper. So it is not the case that the current flows only on the tin surface, but that the tin plating help avoid the formation of a heavy insulating oxide on the copper so the current can more can easily flow into and through the copper core.
Regards,
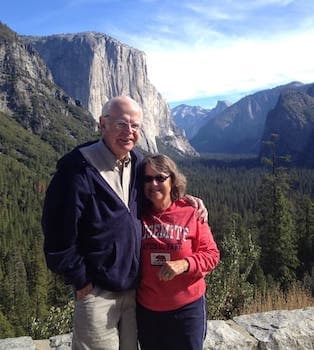
Ted Mooney, P.E. RET
Striving to live Aloha
finishing.com - Pine Beach, New Jersey
November 2017
Q. Dear Sir,
Thank you for your concise explanation. I am an Electrical Engineer working in Dubai UAE.
I have gone through a google search to understand de-rating factors on conductors with respect to temperature (heat vs current). I have a question regarding the current carrying capacity of copper bus bar related to an ambient temperature and temperature rise. How the current carrying capacity of copper has been designed at any ambient temperature. Was there any limitation?
If you brief me with your knowledge and experience, it will be helpful for your student.
Regards, Jack
Jalal Mohamed [returning]- Duabi, UAE
November 26, 2017
A. Hello again cousin Jack. I am not an electrical engineer so my knowledge of this subject is limited. The resistance to electricity flow in metals increases as the temperature rises, and therefore the allowable ampacity of wiring may vary depending on ambient temperature, how many wires are in a conduit, whether bus bars are in the open air vs. enclosed within a bus duct, etc. In the USA we adhere to the NEC (National Electric Code) which has tables for a number of different situations. But I do not have such stuff committed to memory.
Regards,
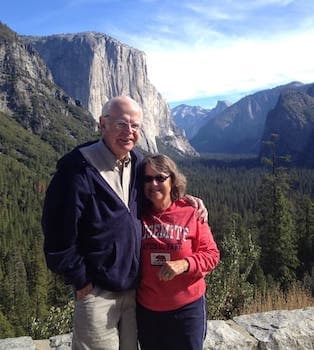
Ted Mooney, P.E. RET
Striving to live Aloha
finishing.com - Pine Beach, New Jersey
November 2017
Q. Can we raise copper current carrying capacity by using tin plating? I found ABB make McCabe spreader link Tin plated and it carries more current than copper bus bar!
Sandip GoswamiElectrical panel - Baroda Gujarat India
February 12, 2019
A. Hi Sandip. Your thought process in claiming that the spreader link carries more current than the bus bar isn't clear to me. But the plating on bus bar is so thin that I would expect its current carrying capacity to be negligible.
Regards,
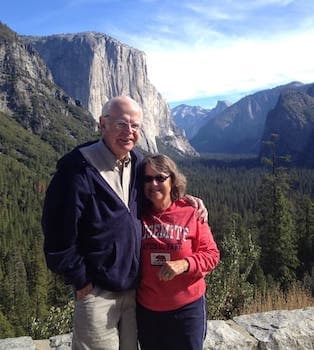
Ted Mooney, P.E. RET
Striving to live Aloha
finishing.com - Pine Beach, New Jersey
February 2019
Q. What is the minimum Requirement of Plating? 10 Micron is enough? Are there any world standards for min. plating requirement for Copper Busbars?
Thanks in advance.
Hitachi Hirel Power Electronics PVT LTD - Sanand, Guarat, India
March 15, 2019
A. Hi Asit,
Usually 8-15 µm tin deposit is good enough for copper busbar to withstand tarnish/corrosion, improve electrical properties at high frequencies and solderability.
Regards,
David
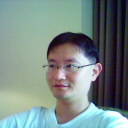
David Shiu
- Singapore
April 11, 2019
Q. I am replacing damaged 2 of 4"x1/2" 2000 A rated copper bus from a 3 phase transformer secondary. Is it absolutely necessary to tin the copper mating surfaces (4"x4")? Can I just clean up the transformer secondary terminals and rough polish the new copper bars mating surface (4"x4" area) and then bolt them together without tin plating?
A muthukumaran- Chennai, Tamilnadu, India
November 24, 2019
A. Hi Amk. I'm not sure if I fully understand your situation, but although tin plating is a good idea, in plating shops the copper bus bar is rarely tin plated -- just wire brushed and bolted together with electrical joint compound like No-Ox-Id.
Regards,
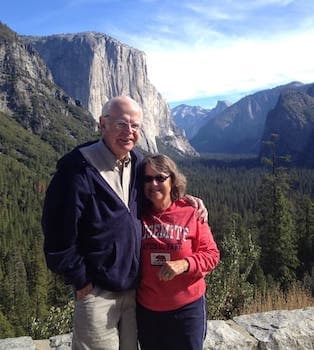
Ted Mooney, P.E. RET
Striving to live Aloha
finishing.com - Pine Beach, New Jersey
December 2019
Q. Thank you, Sir. There seems to be a general misconception in India that all copper to copper mating parts (bus bars, cable terminations etc.) must be tin plated.
I don't agree with plating these joints since copper, after silver, is the best conductor and adding a layer of lead does not aid in low contact resistance. Am I wrong?
Edison Electrical Works - Chennai, India
December 9, 2019
A. Hi again. Tin has lower contact resistance, and doesn't tarnish as badly ... but a clean copper joint, made up with electrical joint compound and then permanently bolted together is, in my experience on DC bussing in plating shops, fine.
Regards,
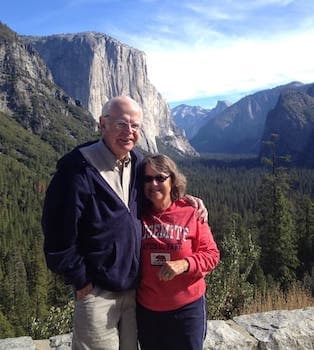
Ted Mooney, P.E. RET
Striving to live Aloha
finishing.com - Pine Beach, New Jersey
December 2019
Thank you, Sir. Much appreciated tip. I will not plate the joints and use the compound you recommended.
Edison Electrical Works - Chennai India
December 10, 2019
Star point in NGR panel is overheating
Q. Hi, we have a bolted joint of aluminium and tinned copper busbar at star point in 11kv 850A alternator NGR [Neutral Ground Resistor] panel and I face joint overheating problem. Please suggest the better solution.
GURBACHAN Singh- BATHINDA Punjab INDIA
January 26, 2020
A. Hi Gurbchan. The aluminum probably requires tin plating. Although I've seen bare aluminum used in some low voltage DC applications as previously mentioned on this site, I'm surprised that un-plated aluminum would be allowed by code for high voltage AC circuits.
As for the main cause of the overheating though, are you sure the problem is restricted to a bad joint and that there is no phase balance issue?
Regards,
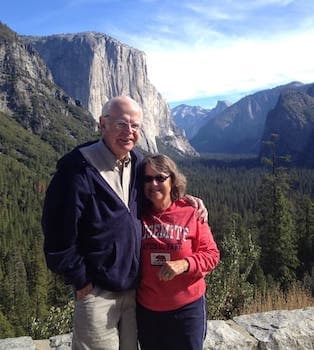
Ted Mooney, P.E. RET
Striving to live Aloha
finishing.com - Pine Beach, New Jersey
January 2020
A. Star point in NGR panel is overheating:
Current through NGR is zero during healthy condition, no reason for high temperature overheating of NGR. The only time NGR carry high current causing high temperature overheating is when there is a Phase to Ground fault causing single phase to ground fault current through the NGR. If this first phase to ground fault is not repaired, prolong fault current may cause another second phase to ground fault occurrence to trip on phase to phase to ground fault condition.
Also check the NGR high voltage insulators for any deterioration in insulation quality.
SWTS Pte Ltd - Singapore
April 25, 2020
October 7, 2020
Comment.
Interesting discussion going on here. Ted, you might be interested to know that most of the world's power grid is aluminium. The Al conductor carries large AC current and very high voltages and is strung out there in all weather, using compression joints for cable to cable connections. I don't work in the transmission industry, but I do know a bit about what they do. No plating used here on the Al.
I have often specified aluminium multicore cable for low voltage (e.g. 400 V) AC power-level connections as it so much cheaper than copper. We commonly use bimetal lugs which have an aluminium body and a bonded copper face, so the surfaces being bolted together in a switchboard is Cu to Cu. This avoids corrosion issues from a Cu-Al interface which can be a big problem, but really this would occur only if there was significant moisture present in the switchboard. Outdoors, Cu-Al contact is a no-no.
- New Zealand
A. Thanks G. I never thought much about long distance transmission lines, but I did know that the 220V service entrance wires on homes in the USA are usually aluminum.
QUICKSTART: Aluminum conducts electricity very well. The issue we need to picture is that aluminum, and to an lesser extent copper, and even tin, silver, and nickel oxidize -- forming an insulating skin on themselves which you could picture as a layer of paint on them. Very high voltages and currents are needed to penetrate the thick skin on aluminum, normal house current are enough to penetrate the thinner skin on copper, and typical battery or rectifier voltages and currents can penetrate the oxides on tin, silver, and nickel. When it comes to the low voltage and very low current digital connectors on a cell phone, they must be gold because even the very minor oxidation on bright nickel is problematical at those levels.
But the contact situation (whether the mechanical contact can cut through that insulating layer) matters too. Service entrance wires can be aluminum because they go into large lugs with pointed screws that really bite through it, assuring a good connection; but the house wiring from that point on must be copper because the joints are not as reliably made.
Luck & Regards,
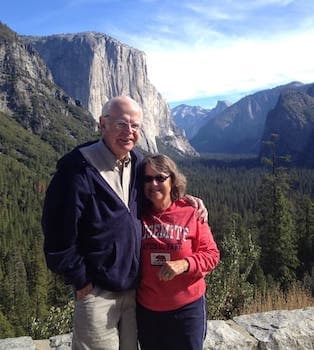
Ted Mooney, P.E. RET
Striving to live Aloha
finishing.com - Pine Beach, New Jersey
October 2020
December 16, 2020
Dear Sir,
We are a manufacturer of Electrical Switchboards and LV Sandwich busways. Could you kindly advise us the recommended tin plating thickness on copper bus bars as well as aluminium busbars.
Thanks and regards,
- Bangalore, Karnataka, India
A. Hi Virendra. RC Murthy has mentioned on this thread that he plates 8-10 µm of tin on copper bus bars and Khozem Vahaanwala says on thread 28003 that he has plated 5 to 12 µm. But in addition should must do a 'code check' for your industry and your area, since these are only opinions not rules.
For aluminum bus bar it probably depends on whether you are doing copper plating first -- in which case the same numbers would probably apply -- or whether you are doing an all-tin process where you'd probably want a higher thickness of tin since it's the only plating protecting the aluminum.
Luck & Regards,
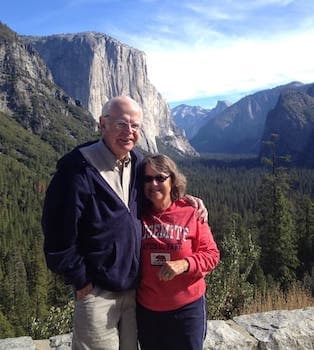
Ted Mooney, P.E. RET
Striving to live Aloha
finishing.com - Pine Beach, New Jersey
December 2020
Q, A, or Comment on THIS thread -or- Start a NEW Thread