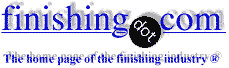
-----
Difference between Electrogalvanized and Hot Dip Galvanized Steel

Q. Hi,
Could you please advise whether nickel-cadmium plated bolts or galvanized bolts are better for outdoor usage.
- Dibrugarh, India
August 11, 2014
A. Hi Marvin. Cadmium is a bio-accumulative toxin with consequences similar to mercury and lead poisoning and should only be used where its unique combination of properties isn't replaceable by another finish; it should never be used solely for corrosion resistance. If galvanizing will do, that's what you should use.
Both galvanizing and plating are available in various thicknesses, but as a general rule galvanizing is significantly thicker and thus more corrosion resistant. The extra thickness can create interferences issues on small threads, so you tend to see galvanizing on large hardware and electroplating on small hardware.
Regards,
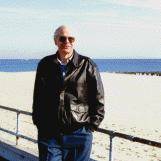
Ted Mooney, P.E.
Striving to live Aloha
(Ted can offer longterm or instant help)
finishing.com - Pine Beach, New Jersey
August 2014
Does zinc plating change the mechanical properties of the steel?
Q. Hello.
Does electroplating of steel with zinc change the mechanical properties of the steel piece?
Student in PNG University of Technology - Papua New Guinea
September 23, 2014
A. Hi Endiken. Ideally, no it doesn't. But high strength steels can suffer hydrogen embrittlement from the plating process which must be relieved by immediate baking. And super high strength steels may be so subject to hydrogen embrittlement that it is not safe to electroplate them.
Regards,
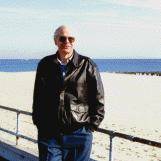
Ted Mooney, P.E.
Striving to live Aloha
(Ted can offer longterm or instant help)
finishing.com - Pine Beach, New Jersey
September 2014
Q. Dear sir,
We use Cold Rolled steel sheet (already annealed, specification SPCC, JIS standard) and carry out electro-galvanizing. After galvanizing, on the surface of steel sheet is occurring a defect which is called 'cross step mark' (Pitch is around 3 cm).
Do defects usually occur on the surface of electro-galvanized steel sheet?
- Ho Chi Minh City, Viet Nam
December 18, 2014
Q. Dear sir,
I want to know the difference between GP sheets and GPSP sheets?
- delhi, India
January 15, 2015
A. Hi cousin Nishant. As I recently posted, these are slang/acronyms, not specifications, and it is risky to rely upon them. Does "GP" mean "galvanized plain"? Probably! Does GPSP mean "galvanized plain / skin pass"? Probably! But please tell us exactly what "GP" means to you, and exactly what "GPSP" means to you, and then we can explain the difference.
I was at the grocer yesterday and the produce manager had scrawled a sign above the grapes which said "GpSP". I only eat seedless grapes, so I want to know whether this sign means "GraPes Seedless Purple" or "GraPes Standard Purple" :-)
Thanks for your understanding that people ought to be extremely hesitant to infer meaning from other people's slang and acronyms. Good luck.
Regards,
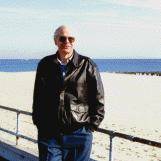
Ted Mooney, P.E.
Striving to live Aloha
(Ted can offer longterm or instant help)
finishing.com - Pine Beach, New Jersey
January 2015
The specification calls for heavy galvanized mild steel, but the offered product is hot dip galvanized steel. My question is which of these has more durability?
Ju lenmottmacdonald - doha, qatar
February 1, 2015
A. Hi, cousin Ju. "Heavy" is a vague and relative term. Unfortunately there is no telling which of the two descriptions implies a heavier and more durable finish. Good luck.
Regards,
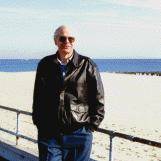
Ted Mooney, P.E.
Striving to live Aloha
(Ted can offer longterm or instant help)
finishing.com - Pine Beach, New Jersey
February 2015
by Jack Dini
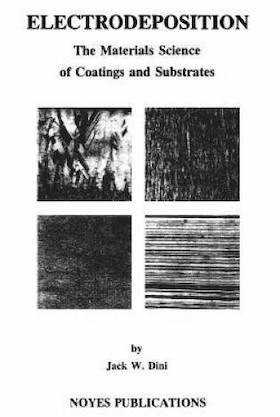
on eBay or Amazon
or AbeBooks
(affil link)
by William Safranek
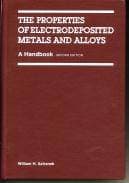
on eBay or Amazon
or AbeBooks
(affil link)
Q. Greetings,
Simply put; is there any significant difference in attachment "force" between the zinc layer and a steel sheet, considering Hot Dip vs. Electroplating?
Reason I'm asking is I'm currently doing my Exam work in an industry, deep drawing (relatively) large sizes of metal sheets pretreated with hot dip, and galling appears in some of the tools in some critical areas.
Best regards,
Christoffer
- Gothenburg, Sweden
February 4, 2015
Hi Christoffer. There probably are theoretical differences, but they are probably not the issue. To expound a little, there are chapters of metal finishing books, like the "Adhesion" chapter of Jack Dini's "Electrodeposition: The Materials Science of Coatings and Substrates" which show fairly substantial variations in adhesion even in a single narrow technology like Wood's Nickel Striking resulting from small variations in operating conditions. Safraneks's "Properties of Electrodeposited Metals and Alloys" studies similar issues.
But the reason I say they are probably not the issue is that poor preparation -- failure to get every bit of dirt, grease, oil, oxide, and corrosion off the substrate -- is generally a far more significant issue in adhesion failures than the limitations of the metal deposition step per se. Good luck.
Regards,
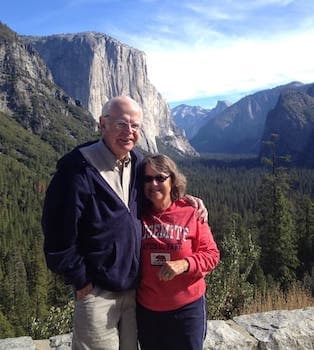
Ted Mooney, P.E. RET
Striving to live Aloha
(Ted can offer longterm or instant help)
finishing.com - Pine Beach, New Jersey
March 2015
Q. Good morning,
My question is just about what is cheaper, electrolytic zinc coated steel or hot-dip zinc coated steel?
Thanks,
- Chihuahua, Mexico
March 24, 2015
A. Hi Brenda. That question was already answered on this page. Zinc electroplating is usually the least expensive way to apply a layer of zinc to components. The thickness tends to be quite a bit less that the thickness of hot dip galvanizing, so the corrosion resistance tends to be quite a bit less.
But abstract questions can rarely be answered well because there are always a dozen "ifs, ands, and buts" which we are forced to not mention instead of dealing with at book length; if you can describe the details of your own situation instead of casting the question in a vague abstract way you will probably get an answer you can rely on. Good luck.
Regards,
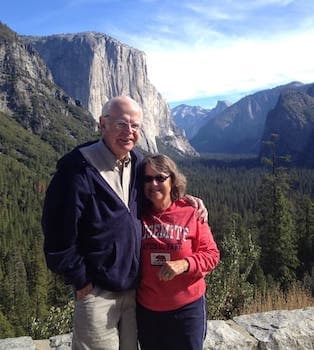
Ted Mooney, P.E. RET
Striving to live Aloha
(Ted can offer longterm or instant help)
finishing.com - Pine Beach, New Jersey
March 2015
Switching from CRS to EG sheet on parts that will be formed, welded, & powder coated?
Q. Hi, thanks for information. My question is brought by a supplier of mine. He would like to use EG sheet steel rather than CRS or HRS. The sheet metal part will then be powder coated. Is there any concern here given that prior to powder coat, the sheet metal will be formed and welded? As I understand, special precautions are required when welding HG. Is there any out of the ordinary concerns welding EG? Will bending/forming fracture the zinc causing undesirable results when powder coated?
Pete LaBonte- Beverly Massachusetts USA
April 3, 2015
A. Hi Pete. I understand your wish to be cautious and concerned, but it just isn't possible for 3rd parties like our readers to assure your supplier, through you, that his supplier's product will meet his needs. Sorry :-)
In general terms though, the zinc plating is supposed to exhibit good adhesion to the substrate and most bends should be no problem. Further, if the sheet metal supplier is aware that the EG sheet will be powder coated, it should not have a surface that wrecks adhesion of the powder coating, and the powder coater should be able to phosphatize and powder coat it.
Zinc is an essential micronutrient, not a poison, but welding it can generate clouds of zinc oxides which represent a gross overdose and can cause metal fume fever. So ventilation, rather than accumulation of fumes, would be important. But overall, I would tend to be averse to switching from CRS to EG if the parts are going to be subsequently formed, welded, and powder coated. I think it might be better to finish the fabrication, then zinc phosphate, electrocoat, and powder coat -- but again, not knowing the parts in question, the application, the environmental conditions, or the expectations, makes it impossible to usefully suggest what is "better". Good luck.
Regards,
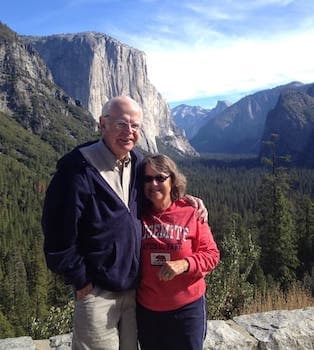
Ted Mooney, P.E. RET
Striving to live Aloha
(Ted can offer longterm or instant help)
finishing.com - Pine Beach, New Jersey
April 2015
April 6, 2015
A. Well, it would be unusual for a supplier to offer more expensive electrogalvanised material, presumably at the same price as Cold Rolled Steel?
This would lead me to suspect a slip in quality!
Maybe the EG steel is a cheap import?
If so, all bets are off as to adhesion under forming duress.
Welding of EG will generate harmful fumes.
Really good fume extraction will be necessary.
Also it is recommended that operators consume milk.
Also a good idea would be to establish the date of manufacture of the EG material.
Most ethical manufacturers give a date for post treatment.
Obviously, pre-treatment prior to powdercoat will require a totally different procedure.
Hope this Helps,
Regards,
Bill
Trainer - Newcastle, NSW Australia
Q. Hi,
What is the official name of Electro-Galvanized? Is it applied for all kind of steels?
- Washington twp, michigan
March 26, 2015
A. Hi Michael. Electrogalvanized doesn't really have an "official name" -- it just means electroplated with zinc. Most people seem to use the word "electrogalvanized" when the plating is applied to a continuous coil of steel, and to use the term "zinc plated" for other instances. There are exceptions though, such as when salespeople try to ride the coat tails of the thicker and more expensive hot dip galvanizing by calling their zinc plated product "electrogalvanized" instead of zinc plated. You'll see this done where it may help them sell their cheaper product through obfuscation, such as on nails and screws :-)
Zinc plating can be applied to any steel except the very hardest, in various thicknesses and with various conversion coatings and topcoats. Please introduce yourself and your own particular situation and then we can probably offer a more useful answer. Thanks!
Regards,
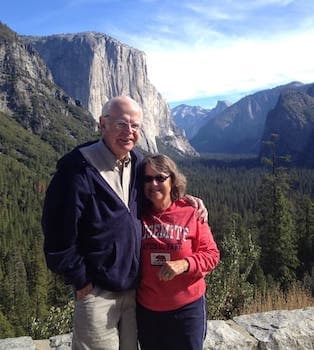
Ted Mooney, P.E. RET
Striving to live Aloha
(Ted can offer longterm or instant help)
finishing.com - Pine Beach, New Jersey
April 2015
Q. Hello,
The company I work for produces steel fencing that is made from 1/8th inch thick material. We currently use hot dip galvanizing and then follow it up with a powder coat over top. I'm wondering if electrogalvanizing would be an option versus hot dip.
We offer a 20 year warranty on our product so that does come into play. The reason I'm asking is due to the extensive amount of time required for cleanup on the parts prior to powder coat. I believe electrogalvanizing would eliminate the cleanup process.
Is there a cost difference between hot dip and electro?
Thank you.
- Joliet, Illinois, USA
May 26, 2015
A. Certainly electroplated zinc can be used, but electroplated zinc is usually much thinner than hot dip.
Even without a topcoat, hot dip zinc can last 20 years; electroplated, probably not unless you specify a considerably greater thickness than normally done.
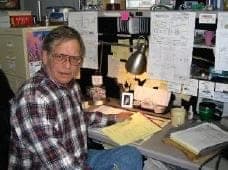
Jeffrey Holmes, CEF
Spartanburg, South Carolina
June 16, 2015
July 16, 2015
Q. Dear sir,
I am a rice miller I am going to purchase a steel silo 2000 mt x 2 nos.
One American company and one European company approached
- the American told me that their process is hot dipped process and they are coating 450 gm/m2; their tensile strength is 483 n/mm2 and yield strength is 380 n/mm2.
- the European company says that their process is Electrostatic galvanization 600 gm/m2 (each side 300 gm/m2); their tensile strength is 420 n/mm2 and the yield strength is 335 n/mm2.
Kindly suggest me which silo I can go for my paddy grain? The cost is immaterial as both are same cost.
Thanks and regards,
- Thanjavur, Tamilnadu, India
Hi cousin Jayakumar. I think the first silo would be better for apples, and the second for oranges :-)
Sorry, but seriously, it is hopeless to try to compare sales pap from one company to sales pap from another. Try to talk to a satisfied customer. Good luck.
Regards,
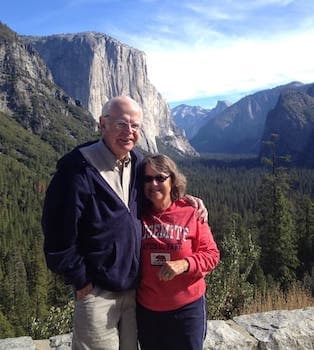
Ted Mooney, P.E. RET
Striving to live Aloha
(Ted can offer longterm or instant help)
finishing.com - Pine Beach, New Jersey
July 31, 2015
Q. To whom it may help us with answers!
We're using metallic wires 0.2 mm in diameter for braiding of flexible metallic conduits (shielding purposes for EMC or RFI and so on).
Now, we're switching to use EG type of wires instead of HD type.
At this switch-over, we got some laboratory results to compare this and that.
But in metallography pictures, we can see the average coating thickness is not highly different!
Now, the raised questions are:
1- Would you please tell us whether we can calculate equivalent coating mass just by multiplying the average thickness by 7.14 (as Zn usual density)?
2- If so, why there's no big difference between those while the first one is for EG type (6.5 micrometer) and the other one is for HD type (7.5 micrometer)?
Warm Regards
Thanks for your so useful forum.
R&D Manager - MHD. IRAN
A. Hi Ario.
1. Yes, you can use the density of zinc multiplied by its volume to calculate the coating weight.
2. Although there might be some particular thickness of zinc which would naturally and intrinsically stick to the steel in a hot dipping operation, some particular shapes of articles being galvanized, like wire, lend themselves to "wiping" the molten coating and reducing that thickness. The hot dipped coating machine probably wipes the coating thickness on the wire down to 7.5 µm while the zinc is still molten.
Hot dipping is reportedly less likely to produce "zinc whiskers" than electroplating. You should examine the application and assure yourself that zinc whiskers are unlikely to be a problem for you. Good luck.
Regards,
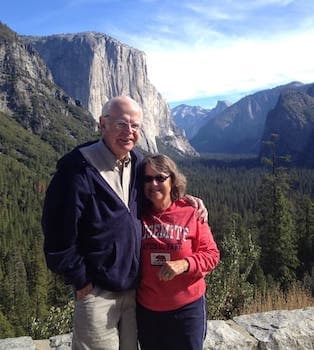
Ted Mooney, P.E. RET
Striving to live Aloha
(Ted can offer longterm or instant help)
finishing.com - Pine Beach, New Jersey
July 2015
July 31, 2015
Q. Dear Mr. Ted Mooney
Hi just the same!
This is Ario from Iran.
Before anything, I appreciate you for your prompt answer/s to my questions.
They motivated me to think about some things by another viewpoints. Thanks!
I read this forum carefully as I found that is an applicable reference to us!
Related to my last question, and following up your guidance, for which I thank you again, as you told at August 3, 2009 by the following sentence :
"Hi, Bui. 10 µm = 0.0004", and that would be a reasonable and believable, and fairly heavy, specification for zinc electroplating -- anything from 0.0002" to 0.0006" would be relatively common. ..."
We concluded that usual thickness of EG type is 0.0004" ~ 10 µm. Right ?
Now, would you please to tell me :
1- 6.5 micrometer (* 7.14 ~ 47 gsm ) of the EG sample, is a good choice, normally ?
2- For these current conditions and regarding to Zn thickness as a high effective factor against corrosion,
Is the EG type better than the current HD type?
- emphatically, for our current cases not for usual .
3- Can you tell us a method to estimate corrosion resistance time (year) of an EG type against Zn-coating mass (gsm)?
It will be so useful to us for our braided metallic conduits
Although we think this prediction may has some deviations since corrosion is a complicated phenomena!
However, if we have an approximate curve or table then it may be useful to use; else please introduce an applicable & reliable well known reference for this prediction, if you can.
Best Regards
R&D Manager - MHD. IRAN
August 2015
A. Hi again Ario. I've personally never seen projections of service life of zinc plating, but what I have seen which should serve well is "suggested standards" of different zinc plating thicknesses for different applications. ASTM B633 offers the following, and other quality guides follow it:
25 µm -- very severe service, bold atmospheric conditions, frequent exposure to moisture & cleaners, likely damage from dents and scratches
13 µm -- severe service (washing machine parts, military hardware, electronics for tropical service)
8 µm -- moderate service, mostly indoors, occasional condensation or wear (TV & radio, screws, bolts, instruments)
5 µm -- mild service, indoors, minimum wear and abrasion (electronic and electrical parts)
[Note: The above descriptions are abbreviated and paraphrased; please see the standard for more complete wording. Many automotive specs call for 8 or 13 µm coating thickness for different applications].
Galvanizers claim that their finish is more corrosion resistant, thickness-for-thickness, due to the zinc-iron alloys; electroplaters claim that their finish is more corrosion resistant, thickness-for-thickness, due to the purity and freedom from tramp ingredients. But I personally go with the "zinc is zinc" philosophy that the corrosion resistance is approximately proportional to the thickness of the zinc coating.
Regards,
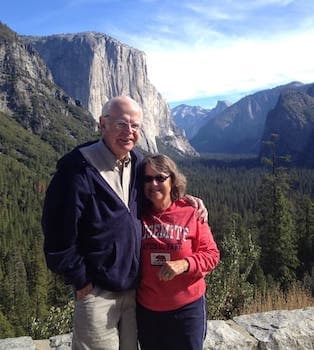
Ted Mooney, P.E. RET
Striving to live Aloha
(Ted can offer longterm or instant help)
finishing.com - Pine Beach, New Jersey
Q, A, or Comment on THIS thread -or- Start a NEW Thread