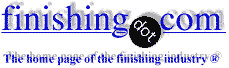
-----
Difference between Electrogalvanized and Hot Dip Galvanized Steel

Q. Hello,
Our spec requires siding fasteners that are either Electroplated (to 30 micron) or hot dipped (30 micron) or Mechanically plated (40 micron). As per AS 3566.2 the Contractor proposes instead to supply fasteners that are electroplated to 15 micron, then Hot Dipped to 20 micron, therefore giving us a "total coating" of 35 micron.
I am concerned about this, having never heard of it before. I can see problems with adhesion between the two coatings, and if they avoid an acid bath then how will HDG perform on a shiny electroplated fastener?
Do you think I am right to have these concerns?
- Perth, WA, Australia
February 13, 2013
for Engineers, Shops, Specifiers
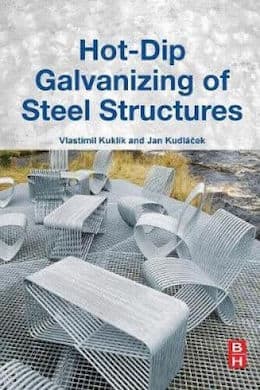
avail from eBay, AbeBooks, or Amazon
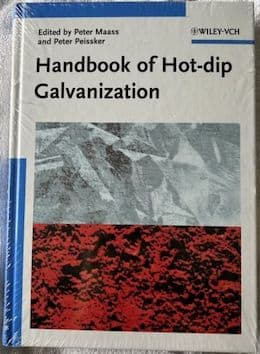
avail from eBay, AbeBooks, or Amazon
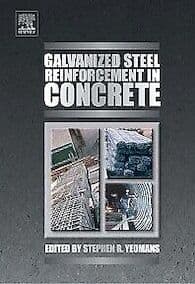
avail from eBay, AbeBooks, or Amazon
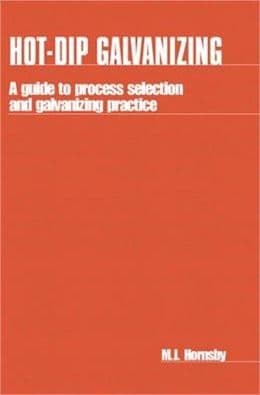
avail from eBay, AbeBooks, or Amazon
avail from Amazon
"User's Guide to Hot Dip Galvanizing for Corrosion Protection in Atmospheric Service" by NACE (1997 only rarely avail.)
avail from AbeBooks, or Amazon
(as an Amazon Associate & eBay Partner, we earn from qualifying purchases)
A. Hi Frank. I don't think I give either side a vote of confidence :-)
A spec calling for zinc electroplating of fasteners to a thickness of 30 microns doesn't sound very practical to me. I've seen fasteners plated to half that thickness and it took 75 minutes plating time and brought on some problems like nicked threads. 25 microns is a lot when it comes to zinc plating of fasteners and is the maximum for "very severe" conditions per ASTM B633. Maybe 12-13 microns of zinc-nickel plating would be a more reasonable spec?
I think hot dip galvanizing or mechanical plating would be more practical, but the ID of nuts is often not galvanized anyway, and mechanical plating of internal threads sounds problematic.
Just because we've never heard personally of something doesn't mean it's impossible, but I've certainly never heard of trying to hot dip galvanize onto a zinc electroplated and chromated surface, and my strong suspicion is that it cannot work. Your contractor may be planning to cold galvanize (spray or dip-spin with zinc-rich paint) on top of the plating. That's probably possible but doesn't sound like a very good idea or robust finish to me.
Regards,
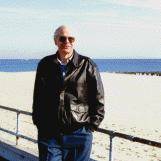
Ted Mooney, P.E.
Striving to live Aloha
(Ted can offer longterm or instant help)
finishing.com - Pine Beach, New Jersey
A. Hot dip galvanizing is not a coating in the usually accepted understanding of the word, rather an alloying reaction between zinc and iron.
If there's no contact between the iron and the zinc then HDG doesn't happen.
When re-galvanizing a piece, the old galv has to be removed in order to reveal the steel (iron), and without that all that happens it heating of the piece due to its immersion in the molten zinc.
I've never tried galvanizing a zinc plated item, but can't see that working. I think it would be a mess.
Further, to claim a control over the process in order to state the thickness of galvanizing like that sounds suspicious (unless it were stated as "about 20µ" or similar). 20µ is very thin for HDG, and an unlikely thickness.
I think you are right to be concerned.
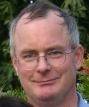
Geoff Crowley
Crithwood Ltd.
Westfield, Scotland, UK
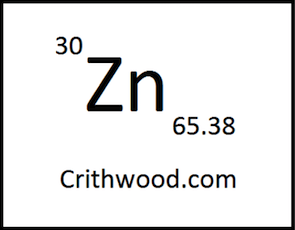
⇦ Tip: Readers want to learn from your situation;
so some readers skip abstract questions.
Q. Is it possible to flux and hot dip galvanize over a zinc electroplated part without stripping it first? i.e., washers or lock washers
Jay Miller- Fort Wayne, Indiana, USA
May 3, 2013
A. Hi Jay. Geoff says no, and I totally believe him. Please explain your situation. Thanks.
Regards,
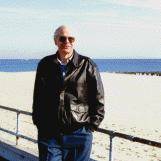
Ted Mooney, P.E.
Striving to live Aloha
(Ted can offer longterm or instant help)
finishing.com - Pine Beach, New Jersey
March 2014
Q. Good morning!
We're stamping car wiper parts using HDG steel. During the stamping process we have a problem of zinc detachment which causes superficial imperfections on the parts. Therefore we want to change to electro galvanization. Seen that the thickness of e.g. is a fraction of HDG's thickness, I believe there will be less zinc detachment with e.g., but for theoretical same thicknesses, which one has the highest adherence, e.g. or HDG?
Metal stamping - Chihuahua, Mexico
February 19, 2013
A. Hi Jeremy. Neither process bonds by any type of "tooth" or mechanical "keying", but rather by metal-to-metal chemical bonds. So I would expect perfect adhesion if processed perfectly. I suspect that the parts are not 100% free of every trace of dirt, oil, rust, mill scale, and oxidation.
I assume that these components are then electrocoated and/or powder coated? -- because bare edges on exterior automotive parts doesn't sound satisfactory.
Regards,
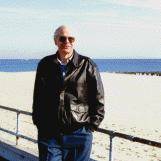
Ted Mooney, P.E.
Striving to live Aloha
(Ted can offer longterm or instant help)
finishing.com - Pine Beach, New Jersey
for Shops, Specifiers & Engineers
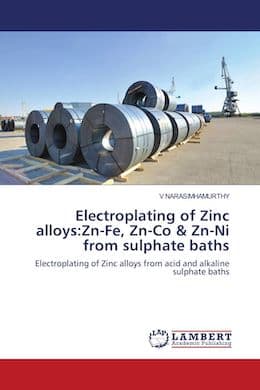
from eBay, AbeBooks, or Amazon
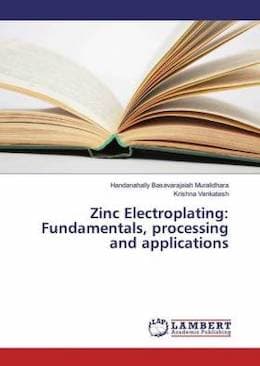
from eBay, AbeBooks, or Amazon
"Alkaline non-cyanide zinc plating with reuse of recovered chemicals" by Jacqueline M. Peden (1994)
from (U.S. EPA)
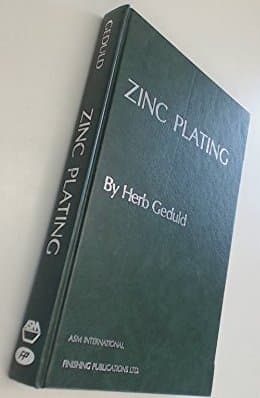
from eBay, AbeBooks, or Amazon
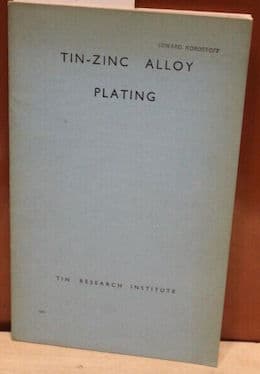
from eBay, or AbeBooks
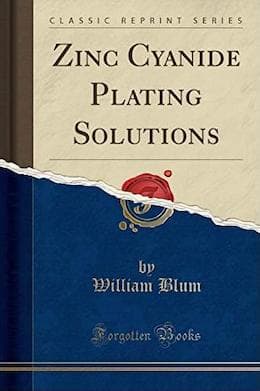
from eBay, AbeBooks, or Amazon
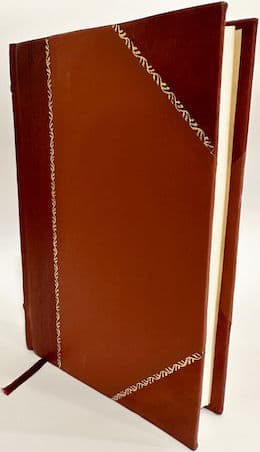
from eBay, AbeBooks, or Amazon
(as an Amazon Associate & eBay Partner, we earn from qualifying purchases)
Q. Hai Mr. Ted
Can you please advise for offshore oil & Gas (under seawater) applications, for Plugs which coating is preferable Hot dip Galvanize or Electro Galvanize?
Thanks & Regards
- Dubai, UAE
March 6, 2013
A. Hi Rajani. Hot dip galvanize might or might not be acceptable, but I can't imagine electrogalvanizing lasting more than a few days under seawater.
Regards,
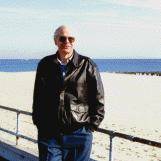
Ted Mooney, P.E.
Striving to live Aloha
(Ted can offer longterm or instant help)
finishing.com - Pine Beach, New Jersey
Q. Hi Ted, have you ever heard of "Hot dipped galvanised electroplated steel" does this mean it would be both hot dipped and electroplated? I want to buy some scaffolding online and that's what it said. Could it be cheap made in China and they don't even know what their product is made from?
thanks
- Perth, WA, Australia
April 14, 2013
A. Hi Simon. The description of an item for sale is designed to entice you to buy, not to technically inform you. There is no such thing as "Hot dipped galvanised electroplated steel".
Regards,
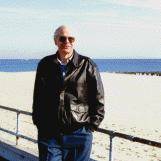
Ted Mooney, P.E.
Striving to live Aloha
(Ted can offer longterm or instant help)
finishing.com - Pine Beach, New Jersey
Q. Sir,
I would like to know the standard to be followed for electrogalvanisation for steel plate. What is the minimum thickness requirement for electrogalvanisation.
- Muscat, Oman
May 20, 2013
A. Hi Kiran. ASTM B633 for zinc plating was already given on this page. If you are applying the plating for no reason except to be able to claim that you complied, then .00015" - .0002" is probably sufficient; but please try your best to clarify your situation because "the minimum thickness requirement" for satisfactory performance clearly depends entirely on the specific application. Thanks. Good luck.
Regards,
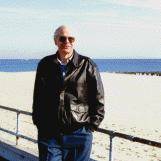
Ted Mooney, P.E.
Striving to live Aloha
(Ted can offer longterm or instant help)
finishing.com - Pine Beach, New Jersey
Galvanised steel supports - can these be used for a environment which demands a non magnetic material.
Mohamed Salman- Bangalore, Karnataka, India
September 16, 2013
A. Surely not, Mohamed. Galvanizing is always applied to steel substrates -- and they are highly paramagnetic.
Regards,
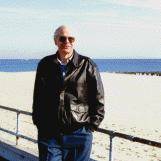
Ted Mooney, P.E.
Striving to live Aloha
(Ted can offer longterm or instant help)
finishing.com - Pine Beach, New Jersey
A. Hi Friends,
Great difference between Zinc Electroplating & Hot Dip Galvanizing.
1. In Zinc Electroplating there is NO ALLOY layers in between Zinc & Steel whereas Hot Dip Galvanizing has an alloy layer in between.
2. Zinc Electroplating is normally thin plating and for cosmetic purpose while as Hot Dip Galvanizing is really thick plating and for metal protection.
- Sana'a, Yemen
Q. Hi -
Thanks for the time and knowledge you share. I'm involved with an existing building in a coastal, salt air environment. The roofing tacks used to attach shingles to roof deck are corroding, even though they are 'electrogalvanized', as are the sheet metal flashings used for the roof. Is there any standards or accepted knowledge documents available for guidance selection of galvanized coatings that I can review? As you have previously stated above, zinc electroplated (sheet) metals are not acceptable for exterior uses where durability is also needed. Being able to refer to an industry standards publication would be very helpful.
Thanks again for your time and help.
November 15, 2013
Q. Hello,
I am new to this whole steel thing. I am looking to buy chain link fence and grassland/horse fence from a supplier in China. My specs on the chain link are as follows:
1. the wire diameter is 3.18 mm
2. aperture is 60 mm * 60 mm
3. height is 1.2 m
4. length is 30 m
5. color is blue
I've been quoted a price for galvanized steel, not hot dipped. He claims it doesn't need to be hot dipped because it will be PVC coated. Is this true? I am trying to get this as close as possible to the spec. of what Home Depot sells. I want a sturdy fence and something that isn't going to fall about in a year or two.
Second part of the question is the horse/grassland fence specs are:
100 m roll
1.53 m Top & Bottom wire diameter 2.58mm
Line/Stay wire diameter 2.05mm
square dimension of 6.35cm wide x 10.16cm
My question is and I think you answered this question already, but this fencing needs to be hot dipped, correct?
- Coolidge, Arizona, USA
January 17, 2014
A. Hi Sandy. If the fencing is PVC coated, the underlying layer of zinc is much less critical and zinc electroplating should be sufficient. If it is not PVC coated then I think you will find anything less than hot dip galvanized to be unsatisfactory.
Just an opinion, but the people who can safely buy from China are the big purchasers who can visit the factory, maintain a QA system there, etc. Your approach is often cynically called "throwing it over the wall", and I personally think a consumer is usually going to find that it was a big mistake to try to purchase 100 meter rolls of fencing direct from China.
Regards,
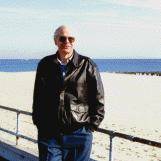
Ted Mooney, P.E.
Striving to live Aloha
(Ted can offer longterm or instant help)
finishing.com - Pine Beach, New Jersey
![]() |
Just wanted to thank Ted Mooney for the excellent education that he is providing. I am relatively new to the EG community and I appreciate his insight into the variations between EG and HDG. Many Many Thanks. Mark WaltzORDA Enterprises - Port Clinton, Ohio, USA February 7, 2014
Regards, ![]() Ted Mooney, P.E. Striving to live Aloha (Ted can offer longterm or instant help) finishing.com - Pine Beach, New Jersey |
Pictures of hot dip galvanized vs. zinc electroplated finish
Q. Hi, regarding is there any difference between the hot dip and the electroplating of the surface:
Do you have any pictures?
- Jakarta, Indonesia
March 5, 2014
A. Hi Reza. I've explained the usual differences in appearance, but sorry, I have no such set of pictures prepared, although there are numerous pictures of both finishes scattered across this site if you search for them. Readers are welcome to submit their picture sets if they wish. And you could start it off by uploading pictures of items on which you'd like to identify the coating.
But I don't think it will be easy! There are several different types of zinc electroplating (acid/alkaline, dull/bright, barrel plated/rack plated), and they nearly always get a subsequent chromate conversion coating (hexavalent / thin film trivalent / thick film trivalent with topcoat / no topcoat), available in a number of colors -- plus the coating looks different depending on the surface it is applied to. In a few cases it's lacquered. Hot dipped coatings may be before fabrication or after, sometimes wiped or spun thinner. Even an expert looking at the actual object rather than a photo would probably only know most of the time rather than all of the time :-(
Let me relate an anecdote. I was asked by one of my country's most famous art museums (a modern one) to consult on a couple of issues involving metal items in their collection. At one point I expressed my hesitation about visual identification; I noted that after reading the labels on their collections of nickel plated and silver plated holloware, I had lost confidence that I could reliably tell the difference between nickel and silver plating by eye anymore. To which the curator responded that if I felt a piece that was marked nickel looked like silver, or vice versa, they could just change the label. What? ... WHAT???!! I assumed there was a written history going back a hundred years or more, plus careful metallurgical examination to confirm ... only to learn that people had in many cases just guessed :-)
Guessing from appearance simply isn't the way!
Regards,
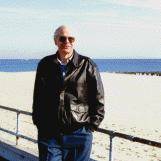
Ted Mooney, P.E.
Striving to live Aloha
(Ted can offer longterm or instant help)
finishing.com - Pine Beach, New Jersey
Q. Dear Sir
After Greetings,
For Cable Tray Installations for RO units, which type of Steel finishing is better?
I understand that the Dip-Galvanized one provides a better corrosion resistance than the Electro-galvanizing one but it is much expensive on the other hand.
So is the Electro-Galvanized one still applicable for the cable trays or not !?
Thank you
water desalination - Cairo, Egypt
March 14, 2014
A. Hi Rafael. Powder Coating is probably better, assuming a water desalination plant has a salty air environment. But it wouldn't hurt to have electrogalvanizing under the powder coating to provide sacrificial protection in the event of scratches or porosity.
Regards,
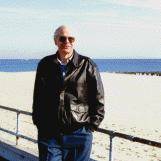
Ted Mooney, P.E.
Striving to live Aloha
(Ted can offer longterm or instant help)
finishing.com - Pine Beach, New Jersey
Q. Hey gents,
Excellent Forum!
I have read almost every post first - I understand the cosmetic and corrosions resistance differences between HDG and electroplate.
We have a large steel electroplate tray which is folded (folded state looks like a drawer); however, we have noticed a lot of tooling marks and scratches on the surface.
We tried the same on HDG and the tooling marks largely disappeared due to the slight difference in colour.
However our parent company wishes to proceed using the electroplate -- but we have reservations. So my questions are a little broad / open but here goes:
1. Is cosmetic scratching common on electroplate galv?
2. Is there a way to prevent this scratching if it is common?
3. The HDG sample we made looked great, possibly better than the electroplate and had zero drip or other imperfections. Would there be any other reasons to choose electro over HDG? (other than corrosion resistance and cosmetics I mean, normal manufacturing method for these trays is pressings but we have a much lower production volume and so wish to use folding techniques.)
4. Just a general question from something someone told me - that I don't believe: Is it true the zinc electro and HDG have a self healing capability is only lightly scratch - by this is meant if the scratch does not pass completely through the coating / over time the scratch reduces?
consumer goods - oxford, oxfordshire, united kingdom
June 3, 2014
A. Hi Pete. Good questions.
1 & 2. The plating shop will probably not scratch the components, but less care will be exercised before they are finished, so they may get to the plating shop with scratches -- and electroplating will not hide them. If they are highly decorative you can perhaps use those blue plastic films that are used on appliances for the brakeing application.
3. If you can get good appearance with reasonable economy from HDG, that's the way I'd go. When hot dip galvanizing is done on coils, as opposed to after fabrication, it is common to "wipe" it to a thinner smoother look. Zinc electroplating is usually less expensive.
4. Regarding the "self-healing", there may be two different aspects conflated together here:
a. Zinc coatings from any deposition method are cathodic and sacrificial to steel ... with the implication that even if there is a scratch, pinhole, or porosity, the zinc will protect the steel from rusting. Other coatings like paints are neutral in this regard, not protecting the scratched area. Still other coatings like nickel plating are anodic to steel and the steel will vigorously rust from a scratch in an attempt to protect the nickel plating.
Regards,
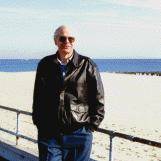
Ted Mooney, P.E.
Striving to live Aloha
(Ted can offer longterm or instant help)
finishing.com - Pine Beach, New Jersey
What solutions are used for zinc electroplating?
Q. Hi Ted,
Thanks for the great information! I had more of a question regarding the Electrogalvanization process.
When electroplating Zinc onto steel, do you know what Zinc solutions are typically used? I've seen a couple different ones mentioned, I'm not sure if there a favored solution or if there are 2-5 main ones.
Any insight you might have would be greatly appreciated.
Thanks!
Sincerely,
Arya
- NYC, New York, USA
July 3, 2014
A. Hi Arya. People in the general zinc electroplating business don't actually call the process "electrogalvanization", they call it "zinc plating" or "zinc electroplating". The "electrogalvanization" term is pretty much used only by continuous coil/strip platers.
In the old days of say 40 years ago, virtually all zinc electroplating was done from a cyanide-based formulation, and the variations were mostly restricted to high cyanide, low cyanide and mid cyanide :-)
Then in the 1970's "acid zinc" was developed and marketed, which had the advantage of less toxicity and greater brightness (acid zinc was occasionally substituted for nickel-chrome plating), but the disadvantages of requiring much better precleaning, not offering as good uniformity of coverage, and being quite corrosive to the building and equipment. Again there were variations like ammonium chloride vs. sodium chloride based. I believe ammonia -based formulations have largely fallen out of favor because their tendency to complex metals makes waste treatment difficult.
The most recently developed and marketed process was the alkaline non-cyanide process. This offers the more uniform coverage of the cyanide process, without the toxicity. These usually have the one extra complication of requiring "generation tanks" -- a side tank with zinc anodes in it (because if the anodes are left in the main tank they dissolve in excess, but a high concentration in the side tank is not a problem, because you can just feed as much or as little of this into the main tank as needed.
Both acid zinc and alkaline non-cyanide are widely used today, with cyanide zinc plating being used in ever less amounts. Acid zinc tends to be used more for barrel plating, and alkaline non-cyanide for rack plating. I don't get out in the field as much as I used to, so I always appreciate updates if anyone disagrees.
Regards,
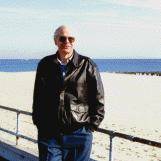
Ted Mooney, P.E.
Striving to live Aloha
(Ted can offer longterm or instant help)
finishing.com - Pine Beach, New Jersey
Q, A, or Comment on THIS thread -or- Start a NEW Thread