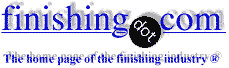
-----
Difference between Electrogalvanized Steel and Hot Dip Galvanized Steel

for Engineers, Shops, Specifiers
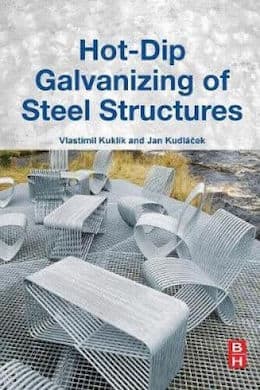
avail from eBay, AbeBooks, or Amazon
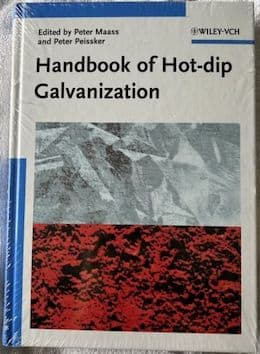
avail from eBay, AbeBooks, or Amazon
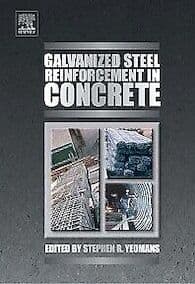
avail from eBay, AbeBooks, or Amazon
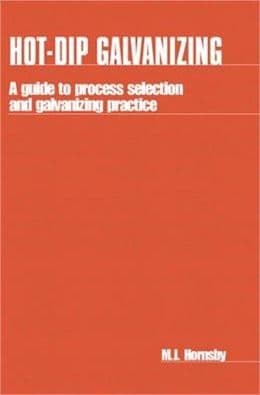
avail from eBay, AbeBooks, or Amazon
avail from Amazon
"User's Guide to Hot Dip Galvanizing for Corrosion Protection in Atmospheric Service" by NACE (1997 only rarely avail.)
avail from AbeBooks, or Amazon
(as an Amazon Associate & eBay Partner, we earn from qualifying purchases)
Q. Hi,
We are working in a Data Center where there are some pipe fittings and fixing brackets etc that are Zinc Coated. Is there a coating we can apply to prevent Zinc Whiskers forming?
Many Thanks in advance for your help!
Kind Regards
- Dublin, Ireland
August 18, 2010
A. Hi, Keith.
Whiskers are believed to be a stress reduction mechanism which I wouldn't expect to be sped up or slowed down by painting. And I would expect the painting itself to dislodge any whiskers which have already formed. But I suppose that paint offers a "binder" effect, so a primer designed for use on galvanized steel should be fine if applied before the materials go into the data center.
I need to add the disclaimer that the subject of "zinc whiskers" is an evolving science without a long and accepted history, so there's a good sized serving of hearsay and guesses in such a reply, but that it's generally believed that hot dip galvanizing is not as subject to zinc whiskers as zinc electroplating (electrogalvanizing).
Regards,
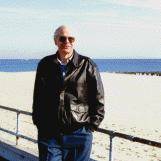
Ted Mooney, P.E.
Striving to live Aloha
(Ted can offer longterm or instant help)
finishing.com - Pine Beach, New Jersey
Q. Good day Sir.
Thanks for an informative forum. My query is related to one above and relates to the process of e.g., and HDG. My understanding is that the dip bath temp is about 450 °C and the anode bath is about 150. However what temps can a component in a bath be exposed to when current is applied and over what period? Especially on any machined edge. An example will be a meter long machined, threaded bolt with an OD of 40 - 50 mm made from as rolled EN8.
What will be likely impact of temp on the base material if any at all?
Construction - Durban, South Africa
August 19, 2010
A. Hi, Shane.
Zinc electroplating is done at a temperature that would rarely exceed 100 °F, although the solutions in the pre-cleaning process are hotter and may approach 100 °C. The component will never reach 100 ° C, let alone 150 °C. There are things that can go wrong, I suppose, but overheating of the threaded bolt seems extremely unlikely. There is a potential defect in electroplating called "burning" which is related to excessive current density and which resembles scorching, but it doesn't actually involve high temperatures, it just looks that way :-)
Regards,
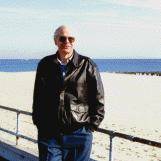
Ted Mooney, P.E.
Striving to live Aloha
(Ted can offer longterm or instant help)
finishing.com - Pine Beach, New Jersey
for Shops, Specifiers & Engineers
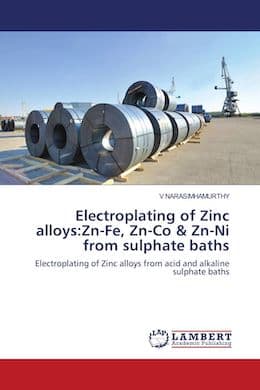
from eBay, AbeBooks, or Amazon
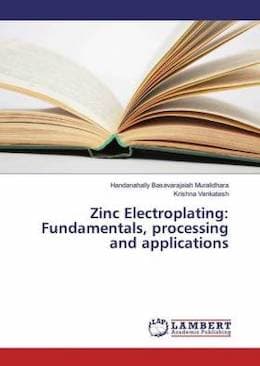
from eBay, AbeBooks, or Amazon
"Alkaline non-cyanide zinc plating with reuse of recovered chemicals" by Jacqueline M. Peden (1994)
from (U.S. EPA)
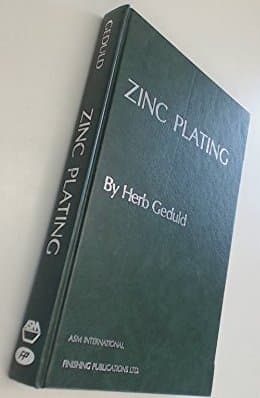
from eBay, AbeBooks, or Amazon
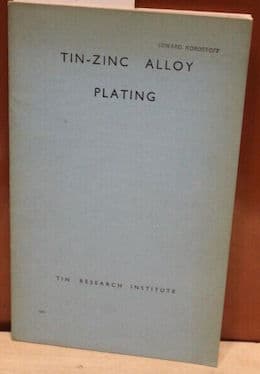
from eBay, or AbeBooks
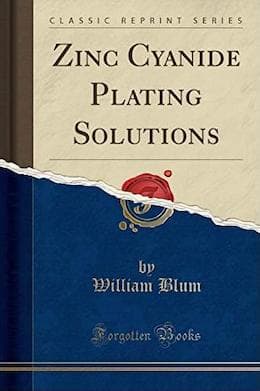
from eBay, AbeBooks, or Amazon
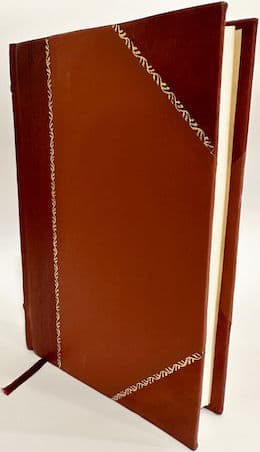
from eBay, AbeBooks, or Amazon
(as an Amazon Associate & eBay Partner, we earn from qualifying purchases)
Q. We have done electro galvanization for pipe supporting "U" bolts for outdoor application.
But as per contract it has to be hot dip galvanized.
In this situation, which of these two options is more suitable.
Doing paint on the already electro galvanized "U" bolt.
OR
Doing hot dip galvanization on the already electro galvanized "U" bolt (if possible)
Is corrosion resistance of these two options is same?
- Bangalore, India
November 9, 2010
A. Hi, Ramarao
Painting sounds simpler, easier, & less expensive, and it may bring the corrosion resistance to an acceptable level -- but it won't comply with the spec, so you would need to get approval. Hot dip galvanization is probably not a problem in your particular case (the usual acid dip that is part of the process will quickly remove the previously electrodeposited coating).
But any time something like this comes up it is important to advise the designer; although I wouldn't expect pipe supports to be hardened steel that could have been damaged by the inadvertent electroplating, high strength components can suffer hydrogen embrittlement during electroplating, so there are some specs that prohibit electroplating for that reason.
Regards,
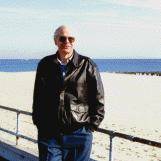
Ted Mooney, P.E.
Striving to live Aloha
(Ted can offer longterm or instant help)
finishing.com - Pine Beach, New Jersey
Q. Please advise if sandblasting materials prior to electrogalvanizing them will incorporate the same rust resistance that just hot dipped galvanizing affords?
Ky CassanellProduct & Material Development Manager - Guelph, Ontario, Canada
June 28, 2011
A. Absolutely not, Ky.
Sandblasting can be a good pretreatment for electrogalvanizing, but the zinc coating is sacrificial and its life will be proportional to its thickness. The sandblasting of the substrate does not change that fact.
Regards,
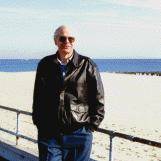
Ted Mooney, P.E.
Striving to live Aloha
(Ted can offer longterm or instant help)
finishing.com - Pine Beach, New Jersey
Q. Dear Sir,
My customer wants pipeline to be electroplated (Electrogalvanized) and ID coating shall be Castrol DW18x for my 65NB and 100NB welded pipes after pickling and passivation.
What process shall I go through to meet my customers requirement.
Regards,
Arhant
- Pune, India
July 2, 2011
Q. Can anybody tell me the cost difference between the two?
GI sheets we consider 1.069 $ per kg. Please advise...
- Bangalore, India
November 24, 2011
Q. Dear sir,
I'm looking for and seeking to know the differences between the cold and hot galvanizing; not in general but specifically in the thickness. I've anchor bolts J-type that I want to galvanize; so I want to know if I use hot dip method, what will be the equivalent thickness if I use the other method (electrical -cold- )
Please give me table or equation to calculate the equivalent...
Thank you
- Cairo, Egypt
April 11, 2012
A. Hi, Hassen. You are apparently calling zinc electroplating "cold galvanizing"; some people call mechanical plating "cold galvanizing"; and still other people call zinc-rich paints "cold galvanizing". So the phrase is slang that has no accepted meaning and may lead to misunderstandings.
The operative phrase is "zinc is zinc", i.e., the corrosion resistance can be expected to be approximately proportional to the zinc thickness.
Although I suppose that it is theoretically possible for zinc electroplating and hot dip galvanizing to be the same thickness, the actual situation is that zinc electroplating is used for thin coatings and hot dipping is used for much thicker coatings, so your question doesn't really come up. I would be surprised to find that electroplated J-bolts are really adequate for general use as anchor bolts.
Regards,
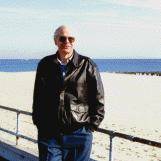
Ted Mooney, P.E.
Striving to live Aloha
(Ted can offer longterm or instant help)
finishing.com - Pine Beach, New Jersey
April 12, 2012
Q. Dear sir,
I am working in pharma plant design engineering,
Which type cable tray is better in pharma Plants.
- Hyderabad,Andhra predesh, India.
May 22, 2012
Q. Dear sir(s), I am curious to know what is the difference between GI, e.g., and GP steel sheets? which one is Superior for corrosion resistance properties? Thanks in advance for help.
Arvind PrasadExporter - Carbon steel sheets/Coils - Kaohsiung, Taiwan
July 30, 2012
A. Hi cousin Arvind. Those acronyms are not specifications -- they are mere slang. Hopefully, "GI", which stands for "galvanized iron", will actually mean hot dip galvanized steel; and "EG" may mean electrogalvanized steel, and "GP" may mean galvanized plain steel. The problem is we can't toss slang around and then ask for quantitative, finely nuanced definitions of its meaning.
As we have said several times in the above discussion, hot dip galvanized coatings are usually significantly thicker than electrogalvanized coatings, and therefore significantly more corrosion resistant. But that's about as far as slang is able take us. Give us an actual specification, and then we can talk about its corrosion resistance. Thanks!
Regards,
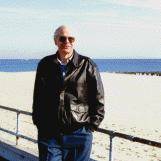
Ted Mooney, P.E.
Striving to live Aloha
(Ted can offer longterm or instant help)
finishing.com - Pine Beach, New Jersey
Q. What metals that zinc do not stick? I am cost accountant. So you can understand the purpose of the question :).
I am new to this industry; Can you guide me on Zinc Calculations and formulas in a simple and easy way?
Regards
- Pakistan
August 9, 2012
A. Hi, Abdul. Sorry, I don't quite understand your question. But hot dip galvanizing is only used on steel to my knowledge, whereas zinc is electroplated onto steel, copper, aluminum, zinc diecastings, and probably other materials as well. There are entire books just about zinc electroplating, and many books about galvanizing, so it is very difficult to summarize those subjects in a "simple and easy way" that will be useful to you when we don't know your situation or understand your question. Sorry.
Regards,
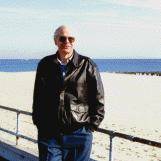
Ted Mooney, P.E.
Striving to live Aloha
(Ted can offer longterm or instant help)
finishing.com - Pine Beach, New Jersey
Q. Hi
I want to know which one is better stuff to produce/manufacture welded pipe of steel, Galvanized Plain Coil or hot dipped galvanized coil. Which one is used in what ratio to make one kg of welded pipe?
Urgent response will be highly appreciated.
Regards
Audit Officer - Lahore, Pakistan
October 24, 2012
Q. If you fabricate/construct something with both normal (uncoated) steel and electroplated steel, will you be able to hot dip galvanise the whole structure without any reaction on the steel that used the electroplated galvanised process?
Mike
- UK
November 5, 2012
A. Hi Mike. The galvanizing pretreatment will strip the previous zinc plating, and you will be hot dip galvanizing the whole item.
Regards,
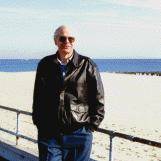
Ted Mooney, P.E.
Striving to live Aloha
(Ted can offer longterm or instant help)
finishing.com - Pine Beach, New Jersey
Q. Hi, I recently started work in a conduit factory where we galvanize through both methods. I work on the e-galv line and not only is the zinc thickness substantially thinner, but the steel used also thinner and much more light weight, so for those asking about the best pipe to use, electrogalvanized steel will not hold up well against high pressure or exposure to the elements. Whereas hot dip conduit is much thicker and can be used for things such as oil rigs and can be put deep in the ground.
I would also like to ask a question, we electroplate our tubes but the inside of the tube does not get galvanized and we have a process where we paint the id of the tube, do you know why and do you know if there is a way in which the inside could be galvanized as well?
Thank you
- Vine Grove, Kentucky, USA
November 23, 2012
A. Hi Brandon. Electrical current is what drives electroplating; 1 gram equivalent weight of metal is deposited for each 96,485 Amp-seconds of electricity. But electricity essentially follows the path of least resistance, and essentially no current flows to the I.D. and no metal will deposit.
It is not impossible to plate I.D.s for critical applications; using internal anodes and high solution flow rates, it can be done (for example on gun barrels)-- but it is prohibitively expensive for commodity items like conduit. Good luck.
Regards,
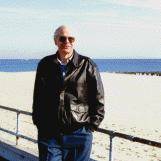
Ted Mooney, P.E.
Striving to live Aloha
(Ted can offer longterm or instant help)
finishing.com - Pine Beach, New Jersey
⇦ Tip: Readers want to learn from your situation;
so some readers skip abstract questions.
Q. Is there any microstructural test to distinguish between hot dip and electrogalvanized coatings?
Nasrul Haque- Dhaka, Bangladesh
November 24, 2012
A. Hi Nasrul. I am not familiar with such a test, although there may be one... but my suggestion is to ask yourself: "Why does it matter?"
Then, when you answer "It matters because ...", this should guide you towards a much more direct and meaningful test :-)
Regards,
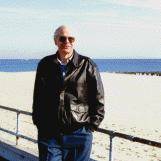
Ted Mooney, P.E.
Striving to live Aloha
(Ted can offer longterm or instant help)
finishing.com - Pine Beach, New Jersey
Q. Hi,
How can I know if the plate is hot dip galvanized or electrogalvanized?
Thanks.
- syria
December 27, 2012
A. Hi Zen. If you have a trained eye, you can usually tell just by looking at it. Electroplating is smooth and bright and uniform in appearance and usually has a chromate conversion coating on it. Galvanizing is mottled, or gritty, or drippy, and usually doesn't have a noticeable conversion coating. Once again we can answer your question best if you tell us why it matters to you? And that way, the readers will learn something from you.
If the coating is 0.0002" thick and you succeed in proving that it is hot dipped despite the low thickness, why does it matter? If the threads of a fastener are jamming and you prove that it was electroplated, despite the heavy coating, why does it matter? If the coating is dull and drippy instead of bright, yet you prove that it was electroplated, so what? If we prove that it was electroplated, but the coating is actually nickel plating or cadmium plating rather than zinc, does that help? If we prove the coating was hot dipped, but it is tin or aluminum rather than zinc, what difference does it make that it was hot dipped? If you have zinc whiskers, why does it matter whether the coating was hot dipped or electroplated?
Regards,
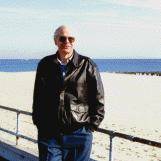
Ted Mooney, P.E.
Striving to live Aloha
(Ted can offer longterm or instant help)
finishing.com - Pine Beach, New Jersey
Q. How do electrogalvanized and hot dipped galvanized look differ by color? Basically we have some parts mixed with both type of finishing and we want to sort by color?
Sanjay Jivani- West Chicago, Illinois
January 24, 2013
A. Hi Sanjay. Please take the time to re-read the page slowly as I have already described the usual differences in appearance three times! If the parts have obvious heavy drips or an obvious mottled crystalline pattern like frost on a window, they are hot dipped. If they are yellow they were zinc plated and chromated. Otherwise it might be hard to know.
But you have to ask yourself how important it is that the parts be correctly identified? It may be better to sell them off at a discount than to have to declare on your certifications that your declaration is based on untrained amateurs guessing based on something they read on the internet:-)
Regards,
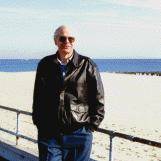
Ted Mooney, P.E.
Striving to live Aloha
(Ted can offer longterm or instant help)
finishing.com - Pine Beach, New Jersey
January 24, 2013
Q. Hello,
Say you have a flat rolled coil which is galvanized. How can you tell the difference if this is electro or hot dip? Zinc coating is supposed to be at 7 microns each side with zero spangle.
Kyprianou Group - Larnaca,Cyprus
February 16, 2018
Q. Hello,
Our company uses galvanized eyebolts, pipe, .125 plate, and hardware quite often. Prior to painting we clean and prime (self etching primer) all parts after welding. Recently, some customers have complained that the paint on the pipe is chipping, but not the hardware or plates. Is there a different method to galvanizing pipe? If so, do all suppliers galvanize pipe in this method?? Should we be roughing the surface more on the pipe? Any help/advice from anyone would be appreciated. Thanks in advance.
- Atlanta, Georgia, U.S.
February 1, 2013
A. Hi Tim. Yes, pipe is often galvanized differently. See letter 43365 or search the site for more on that topic. But I don't think that's the heart of the matter.
Self etching primers can be helpful for field application, consumer projects, touchup, etc. -- but they are not the right pretreatment for galvanized parts . . . zinc phosphatization is. My point is that when a self-etching primer fails to deliver good adhesion, the question is not what is wrong with the galvanizing, but what pretreatment you should be doing instead of simply using self-etching primer :-)
If your other parts are okay, carry on. But if the primer isn't adhering to the pipes, send them out for zinc phosphating. Good luck.
Regards,
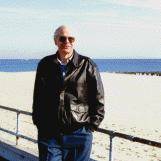
Ted Mooney, P.E.
Striving to live Aloha
(Ted can offer longterm or instant help)
finishing.com - Pine Beach, New Jersey
⇦ Tip: Readers want to learn from your situation;
so some readers skip abstract questions.
Q. What is the life period of electrogalvanization?
SENTHIL KUMAR- Chennai, Tamilnadu, India
January 30, 2013
A. Hi Senthil. This sacrificial coating has been applied across a wide range of thicknesses and in many different service conditions, ranging from essentially non-corrosive air-conditioned offices and computer rooms to severe saline and industrial atmospheres :-)
If you tell us in detail about your application people may be able to offer some predictions about service life. Good luck!
Regards,
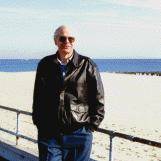
Ted Mooney, P.E.
Striving to live Aloha
(Ted can offer longterm or instant help)
finishing.com - Pine Beach, New Jersey
Q, A, or Comment on THIS thread -or- Start a NEW Thread