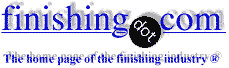
-----
Hot dip galvanizing flux Q&A's, Problems and Solutions

⇦ Tip: Readers want to learn from your situation;
so some readers skip abstract questions.
Q. What should the pH be for a good flux mixture? 4?
When using a hydrometer what should that read? 20+/-?
- Vancouver, BC Canada
June 16, 2023
A. There are several answers to your question.
First pH. Yes about 4 is OK. Too low means acid is being moved across from pickling, likely by poor rinsing, or rinsing in acidic water.
Density. There are at least three systems of measuring density, and I've seen galvanizers using all of them. This is similar to different measures of distance (miles / kilometers), temperature (Fahrenheit, Celsius) etc. These density measures are SG (where water = 1.0) Baume: where water = 0, and Twaddle, used mainly for liquids with SG > 1.0. zero Tw = 1.0 SG.
Yu mentioned 20, so that';s likely Baume, (abbreviated "Be") and a good target for flux is 20-25 Be. In SG the target range is 1.19 to 1.22.
But which type of flux? Double salt, triple? quadra? Each has its place, and its different target density (or concentration).
And remember flux is a mixture, nt a pure substance. Its water, ammonium chloride and zinc chloride. The ratio of these last two is what determines the double, triple etc.
Double salt is two parts ammonium chloride to one zinc chloride.
Contamination and wrong concentration are the two most common issues I've found in galv plants. Usually the flux is too weak, and often too high in iron (Fe). Fe should be less than 1%, and preferably less than 0.5%.
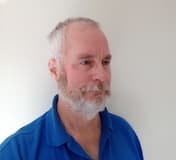
Geoff Crowley, galvanizing consultant
Crithwood Ltd.

Bathgate, Scotland, UK
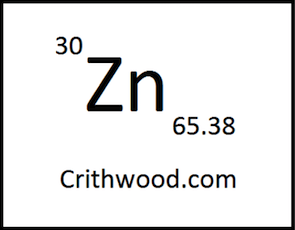
July 13, 2023
⇩ Related postings, oldest first ⇩
Q. Dear Dr. Cook,
I have read the valuable suggestions you give to various galvanisers and here I would like to take this opportunity to get your advice. We galvanize tubes. presently, we are facing problems in getting the right quality of flux. can you please advice us the process and the formulation so that we can prepare our own quality flux based on triple salt.
Regards,
pipe manufacturer - Hyderabad, India
2006
A. Dear Rajiv,
Triple Salt is 54% Ammonium Chloride and 46% Zinc Chloride. This is an "ACN" (Ammonium Chloride Number of 1.17; which is the weight of ammonium chloride divided by the weight of zinc chloride; e.g. ACN of triple salt = 54/46). If you strongly heat the pipes after fluxing then the double salt is more thermally stable with an ACN of 0.8. If you only slightly heat the pipes after fluxing then quadraflux with an ACN of 1.6 is good. Quadraflux has the advantage of producing thinner and smoother zinc coatings on the inside of the pipes. A certain wetting agent produced only in the USA and Germany is the only one that I have found works well in galvanizing fluxes.
Thank you for asking me your question. You could get additional information from my journal articles in Metal Finishing.
Regards,
Galvanizing Consultant - Hot Springs, South Dakota, USA
A. Flux solutions should be kept on 50 degrees to perform well.
Sondergaard- Denmark
A. Dear Sondergaard,
It is true that many automatic pipes galvanizers use 50°C and high baumé(density)flux solution for galvanizing medium and small diameter pipes. If the flux solution is hotter, then the last pipes in the bundle will have corrosion lines on the outside and have "black" (bare) spots. (Higher flux temperature causes faster corrosion.) If however, large diameter pipes are galvanized or the "breaking table" is wide enough and slanted such that a single layer of pipes results (for the fluxed pipes), then low baumé and hot flux gives a better result. Better by having a thinner zinc layer on the inside of the pipes and having much less ash (skimmings) at the kettle.
For general galvanizing it is common practice in North America to use either triple salt flux (ACN=1.17) or quadraflux (ACN=1.60) at about 13 to 14 degrees baumé and 71 °C (160 °F). (ACN = weight of ammonium chloride/weight of zinc chloride.) This often gives a percent gross zinc usage between 4% and 5% (%GZU = zinc consumed/steel galvanized all times 100%) (no zinc credits for ash or dross). The correct pH and the proper wetting agent (surfactant) in the flux also help prevent corrosion of the fluxed steel.
Regards,
Galvanizing Consultant - Hot Springs, South Dakota, USA
What is Quadraflux?
Q. Sir,
I read the name quadraflux during the course of above discussion. I want to know what is quadraflux and what is triple salt flux. Currently I am using flux which is mixture of Ammonium chloride and zinc chloride. Is it called double salt flux. Do triple salt and quadraflux give better result in terms of surface finish and zinc consumption?
Regards
Pipes manufacturing - Anjar, Gujrat, INDIA
2007
A. Dear Atul,
Galvanizing Fluxes Are:
Name Formula ACN Uses
Monosalt ZnCl2.NH4Cl 0.4 Sheet
Double Salt ZnCl2.2NH4Cl 0.8 Preheater Gen. Pipes
Triple Salt ZnCl2.3NH4Cl 1.17 Dryer Gen. Pipes
Quadraflux ZnCl2.4NH4Cl 1.6 Gen. Pipes
Many pipe galvanizers use double salt with starting ACN=0.8. In doing rework zinc is stripped into the flux and the ACN goes down as the pH goes up. Over time these out-of-balance conditions interfere with fluxing action. Flux function can be restored with proper amounts of hydrochloric acid and ammonium chloride. This is true of all fluxes.
Pipe galvanizers often use high baumé double salt and get thick zinc coatings on the pipes, particularly on the inside diameters (as much as 200 to 1000 microns). With quadraflux the i.d. zinc coatings are much thinner (as little as 20 to 40 microns). To use low baumé quadraflux the proper equipment after fluxing which includes a broad, tilted "breaking table," walking beam transport, and suitable zinc immersion device (like progressive screws)are required.
For pipe galvanizing, quadraflux is highly successful in South Africa, Southern India, and the USA. It has not been successful in South America and Central India. Proper equipment is essential.
For general galvanizing, the double salt is widely used in Europe (along with preheaters), whereas in the USA triple salt and quadraflux are widely used (no preheaters) at 71 deg. C.
With proper equipment and flux maintenance, YES, quadraflux does give a higher quality product and much less zinc is consumed. I have published a comprehensive article in the journal Metal Finishing regarding quadraflux and you can get it off the internet.
Regards,
Galvanizing Consultant - Hot Springs, South Dakota, USA
Q. Thank you Dr. Cook for your comprehensive reply.
I think by "breaking table" you mean skid or stand before dryer where bundle is kept after fluxing and feeding in to the dryer. We do not have walking beam type conveyor but chain conveyor and pneumatic cylinder (Plunger Type) dipping flux. Should I adopt quadraflux since I cannot change the equipment?
Regards,
Pipes manufacturing - Anjar, Gujrat, INDIA
A. Dear Atul,
The breaking table is indeed the stand for the fluxed pipes prior to the dryer. The real question here is if the flux is scratched off the pipes prior to entry into the zinc. If the equipment and the pipes do not rub too much then quadraflux at rather low baumé may work for you. Certainly I cannot advise without seeing how the equipment handles the pipes. For small diameter pipes a progressive screw zinc entry is by far the best way to put the pipes into the zinc. A push down device can allow the pipes to bob up causing black (bare) spots. A progressive screw is strictly one way and that is INTO the zinc. Bending of the pipes during entry is also a problem well known to you.
Regards,
Galvanizing Consultant - Hot Springs, South Dakota, USA
Dr.T,
What we really NEED is a Seminar organised by you in India (a 3 Day Workshop?).
Regards,
- Kolkata (Calcutta), West Bengal, India
2007
Q. Doctor Cook
I want to ask is there any chemical which can be used before galvanization with flux or even alone so that
1. It will enhance & intensify surface chemistry
2. It will strengthen the contact bond of interfaces during the process as the iron and zinc combine to form an intermetallic compound at the surface
3. It will heighten the catalytic property of the flux by reducing the surface tension between interfaces.
4. It will let the metal to attain the highest Galvanic protection with zinc by reducing interfacial tension under basic chemical mechanism.
- Hisar Haryana India
August 9, 2008
Q. Kind Attn: Dr. Thomas H. Cook
Dear Sir,
We got the good knowledge of your suggestion regarding Galvanizing Flux; but still we are facing some problem regarding fluxes.
We are manufacture of Galvanizing flux in India. We have hot dip galvanizer customers in India, they are manufacture of transmission tower & we are supplying galvanizing flux to them, but we are not able to satisfy their quality of flux.
As you suggest in above conversation regarding wetting agent(surfactant) in the flux. We want to try this also, for that we want to know the correct name of the wetting agent (surfactant) and the process. So we can satisfy our valuable customers.
Regards,
- Mumbai, Maharashtra, India
July 30, 2009
Q. Sir,
what is the function of BLANKET FLUX in hot dip galvanizing process?
Trainee quality engg - Kolkata, West Bengal, India
July 22, 2010
A Guide to process Selection & Galvanizing Practice"
by M. J. Hornsby
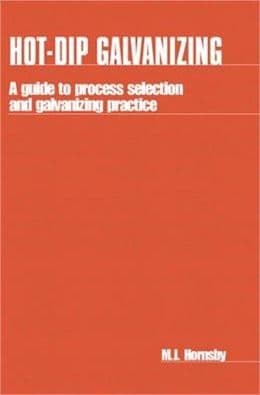
on eBay or Amazon
or AbeBooks
(affil link)
Q. Dr. Cook,
I have read your immensely helpful paper on galvanizing flux. I am currently puzzled by a few things, however. I would very much appreciate if you could give me an answer to these:
1. For quadraflux, the baumé range is quite small and as you have mentioned can go up with use. How do I control the rise of the density?
2. What would be the best indicator to tell me at what pH my bath is?
Much appreciated.
- Canada
March 2, 2012
A. To your first question--- The baumé of the flux likely increases because rework or racking fixtures with zinc on them, or spin baskets (to be stripped) are put into the flux and some zinc dissolves causing the baumé to rise. If needed some flux should be taken out and water added. In this stripping process the baumé rises, the pH rises (counter balanced to some extent by acid carry through of the acid rinse), and the ACN drops. Thus the ability to correct for baumé changes, pH changes, and ACN changes are all three required.
To your second question--- The pH testing and control are consulting matters. This Sunday March 11, 2012 I go consulting to three plants and will install the required testing and control equipment, along with other things.
It would be interesting to know what part of Canada you are residing in.
I presume the article you are referring to is the one with the title like: "Testing and Control of Hot Dip Galvanizing Flux" in Metal Finishing?
Regards.
Galvanizing Consultant - Hot Springs, South Dakota, USA
Dr. Cook,
Thank you for the answers. Indeed that was the paper that I have studied. I am writing to you from Scarborough area in Toronto. Currently I am looking to see how I can make maintenance of the quadraflux bath easier (stretching the baumé range by adding wetting agents?).
- Canada, Toronto
March 12, 2012
Compensating for Fe Concentration When Analyzing Flux
Q. In considering flux, and analysis of it, what correction should be applied to measured density to compensate for Fe concentration.
If measuring flux density to ensure correct strength, in a solution with high [Fe], say 2-4% that some operate at, what correction gives a density that simulates 0% Fe?
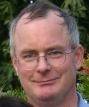
Geoff Crowley
Crithwood Ltd.
Westfield, Scotland, UK
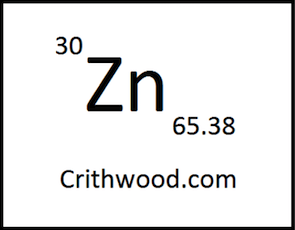
March 15, 2012
A. Geoff:
2% to perhaps 4% iron (Fe+2) in the flux likely increases the baumé by about 2 units. I rarely consider this and have found the best baumé in most cases to be near 13 for quadraflux, and temp. of 71 C. Keep in mind that the original concept of ACN was ammonium chloride as numerator and zinc chloride as denominator. With higher dissolved iron a better concept (ACNV) is to have ammonium chloride as numerator and the zinc chloride plus iron (II) chloride as denominator.
I am now at a site where there are many things I do not like including dirt floors and dirt packed tight against the sides of heated caustic, sulfuric acid, and flux tanks. This causes the heat to go into the ground. This location will be a difficult one. They also use carbon-stick heaters which combust under the solution in the tank, without using suds (causes double the heat bill).
Regards,
Galvanizing Consultant - Hot Springs, South Dakota, USA
! I am on a trip in Eastern USA. The baumé of the flux here is now 14.5. I would rather have it 13.
Three days ago the ACN was 1.0, then 1.2 and today 1.4 (just now being tested here in the plant). I may raise it to 1.6 tonight. Going from 1.2 to 1.4 ACN gave much better zinc drainage at the kettle and the icicles are now thin like a foil gum wrapper, whereas yesterday they were still like a pencil point.
The flux required 10 gallons of conc. HCl to attain the proper pH of 4.2 the first day. Yesterday it required 4 gallons of HCl. The test today shows the pH is correct. Thus the flux side is good.
I am doing some other things with excellent results, giving absolutely NO BLACK SPOTS whatsoever and the product is very bright indeed.
Regards,
Galvanizing Consultant - Hot Springs, South Dakota, USA
Q. Dr. Cook,
We do 2000 tons of angle galvanizing every month. We use pre-flux bath followed by dryer followed by galvanizing. We are not using any ash boxes. Our ash generation is 0.68% and dross generation is 0.39% of total production. Gross zinc consumption is 4.5%.
Please advise on quality of pre flux bath that should be maintained and method of zinc recovery from ash skimmings.
- Bhiwadi, Rajasthan, India
May 3, 2012
A. Sir,
If these are heavy angles (thick) then your results are average to good. If they are light (thin) angles then your results are very good to excellent.
I believe I have already responded on this website to your other questions.
Regards,
Galvanizing Consultant - Hot Springs, South Dakota, USA
Q. HOW TO PREPARE THE HOT DIP GALVANIZING FLUX SOLUTION
REGARDS
NAG
CHEMIST
- HYDERABAD, INDIA
May 9, 2012
A. Hi, Nag.
Sorry, but in this context I can't quite understand the question. Please take a paragraph to try to phrase your question in terms of the answers that are on the page if possible. Thanks!
Regards,
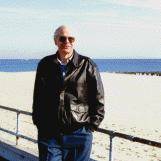
Ted Mooney, P.E.
Striving to live Aloha
(Ted can offer longterm or instant help)
finishing.com - Pine Beach, New Jersey
Ash gets stuck inside tubes
Q. We are galvanizers of tubular towers in which tubes are heated and pressed with a gap of 19 mm. While galvanizing these tubes, ash gets stuck to the walls of the tubes inside and these tubes are rejected.
Can you please guide as to how exactly to overcome this problem?
For your info, all the tubes are almost taken out of zinc bath @ 45 deg angle.
We are using triple salt of zinc amm. chloride with 18 to 22 Be and temp of flux is around 40° C and dried at 50° C
Shall wait for your suggestion.
Thanks & regards
Srinivasan.R
- Chennai, Tamilnadu, India
May 8, 2012
A. S.R.
Perhaps you could e-mail a photo of a "passing" and a "rejected" "TUBE" with some scale indicator (ruler or tape measure or a human hand in the photo). I have had very good success in reducing ash on product over the years via flux composition. In the last 1.6 years I have had outstanding success, via other means of eliminating flux and ash sticking to the product. The work goes on.
Regards,
Galvanizing Consultant - Hot Springs, South Dakota, USA
by Kuklik & Kudlacek
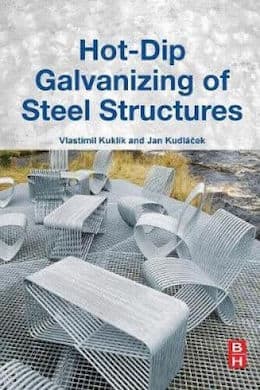
on eBay or Amazon
or AbeBooks
(affil link)
Q. Hello Sir,
Recently I sent my flux sample for a detailed chemical analysis and what I got the results is following. As we are new in hot dip galvanizing and have not reached the profit path, will someone kindly suggest prime actions to control the process fairly as our ash/dross limit is high and I heard that it's because of a bad flux. Test Result Says,
Zinc, Total = 108 g/l (gram per liter)
Ammonium Ion = 59.5 g/l
Zinc Chloride = 225 g/l
Ammonium Chloride = 172 g/l
pH at 25 °C = 3.92
Density at 25 °C = 1.2057 g/l
Total iron = 1.19 g/l
baumé at 25 °C = 25
While we are maintaining our Flux Bath temperature at a value above than 65 degree C.
Zinc bath has,
Zn= 98.8
Iron=0.02
Lead=1.09
Copper=less than 0.01
Aluminium = less than 0.01
Mn= less than 0.01
What's your expert advise?
Thanks!
- Dammam, KSA
May 17, 2012
![]() |
A. In your zinc analysis you said "less than 0.01%", did you mean less than 0.001% ? ![]() Geoff Crowley Crithwood Ltd. Westfield, Scotland, UK ![]() A. Sir: Galvanizing Consultant - Hot Springs, South Dakota, USA |
Q. Sir Geoff Crowley,
Yes it's %. Sorry I forgot to mention that.
And Dr. Cook,
Was that flux description for me? And I really want to obtain your manual for flux preparation.
- Dammam KSA
May 19, 2012
Q. We are performing the process of hot dip galvanizing
for coating on the brass wire with the diameter of 3mm.
In this we are facing a problem of improper bonding lets say like after few months the coating will peel-off from unspecific area. We are not able to find the proper flaw in our process can you give us your valuable suggestion so that we can go for production stage trial?
Best Regards
- Dubai, UAE
May 20, 2012
Q. Dear Dr.Cook,
Refer to my question dated May 8th & your reply on May 12, thank you very much for replying. Sorry being late as I was on my holiday.
I attach 5 photos which indicate ash sticking to the walls of the tube inside.
(Click thumbnail graphic for higher resolution photo)
I would be very thankful to you if you can help us out on this issue.
It is considered rejection by the client.
Hoping to hear from you.
Thanks & regards
- puducherry, India
June 11, 2012
A. SR:
I am not able to determine your problems from your photos.
Crux Dee:
First I do not necessarily believe the flux test results. Secondly you are using mixed (both USA and European methods). You have high temperature 65 °C. (USA) but high baumé and low ACN (Europe) flux. My experience is that such mixing of methods does not work properly. I do not have a "manual for flux preparation."
M.Patel:
What is the chemical composition of the brass wire and why would you want to galvanize brass wire?
Regards,
Galvanizing Consultant - Hot Springs, South Dakota, USA
Q. At what Fe+2 concentration does one have to consider ACNV as opposed to just ACN?
Kevin Carroll- Long Beach, California
June 21, 2012
A. Kevin:
Good question. A few years ago I gave a corporate workshop and I tested the 10 fluxes first. In one case, the ACNV was about 0.4 whereas the ACN was 1.2 (near triple salt). The reason for such deviation was obviously the high iron content, which by my limited memory was around 5%. The easy way to answer this question is to calculate both ACN and ACNV but ALWAYS use ACNV as your standard. It has taken many years just to get galvanizers knowledgeable to ACN. Now the task is to get them to understand and use ACNV.
As a side note, a few months ago I found an ACNV of 1.0 for a 10,000 gallon flux tank and advised that about 4,500 pounds of ammonium chloride was required to attain quadraflux with ACNV of 1.6. The galvanizer added about 3,000 pounds of ammonium chloride and then sent it to a flux company for testing. The result was 0.69 for ACN which was clearly NOT correct. This flux had a sulphate of 1.2% and iron (Fe+2) of 0.8%. I have never really decided where to include sulphate but I expect it should be included in the denominator. This has not been an issue for me because the way I test gives ACNV directly and I have used this ACNV very successfully for many years. 15 years ago I made up in lab a flux with ACN = 1.00 and sent it to 13 labs. ALL the labs got VERY WRONG RESULTS. The results are published in METAL FINISHING under a title like TESTING AND CONTROL OF HOT DIP GALVANIZING FLUX.
Galvanizing Consultant - Hot Springs, South Dakota, USA
Q. Dear Dr. Cook.
The composition of the Brass wire is 60% copper and 39-39.5% zinc; balance is impurities.
The need for galvanizing the brass wire is for a marine application.
Please suggest what kind of flux can be used for the same, and
whether we can use Zinc Ammonium Chloride or if anything else is required for the base metal brass?
Best Regards
- Dubai
June 25, 2012
A. Sir,
I expect triple flux will allow you to galvanize brass wire. Over time, copper will enter the kettle zinc and likely cause the iron zinc kettle to have a short lifetime.
I have no experience in galvanizing brass.
Regards,
Galvanizing Consultant - Hot Springs, South Dakota, USA
(you are on the 1st page of the thread) Next page >
Q, A, or Comment on THIS thread -or- Start a NEW Thread