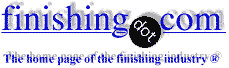
-----
Electropolishing of aluminum and stainless steel
Q. Trying to find the chemical makeup of a solution for electro-polishing of stainless steel, carbon steel, and aluminum.
Merlin Milligan- Somonauk, Illinois, USA
2002
2002
A. Many electropolishing solutions contain phosphoric and sulfuric acids. Various formulas are given in the in the Metal Finishing Guidebook article on Electropolishing
There are many vendors with proprietary solutions; this is a good way to begin as you get the correct solutions and procedures for your particular alloy(s). Also, they will advise as to the most suitable alloys and run sample parts. Click the Chemicals link below, then search for electropolish. At least one of these vendors has a non-environmentally hazardous product.
Ken Vlach [deceased]- Goleta, California

Rest in peace, Ken. Thank you for your hard work which the finishing world, and we at finishing.com, continue to benefit from.
A. I would like to recommend the following formulation to you: Glycolic acid 55%, sulfuric acid 30%, water 15%. The formula is free of phosphate and absolutely environmentally friendly. Of course you can obtain excellent result.
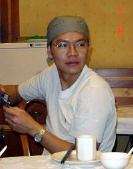
Benlogo G.B. Huang
- Guangzhou, China
2002
and Chemical Polishing
of Metals in
Research and Industry"
by W.J. Tegart
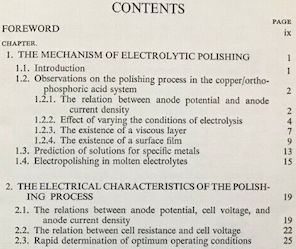
on eBay or Amazon
or AbeBooks
(affil link)
Q. Dear Advisor,
As I could determine from your site, you are interested to support people to find a good and environmental friendly process to electropolish metal parts.
I am a retired Chem. Engineer and am trying to electropolish some machine parts made of stainless steel AISI 304 and AISI 316 to improve surfaces for sanitary use.
I never did electropolishing by myself and want to try it in my garage before to launch any service operation. Could you be of any help giving me some adequate formulation for this task? What also could be a good DC voltage to induce the controlled corrosion of the peaks at metal surface?
Best Regards,
Herbert F. Steffen- São Paulo, SP, Brasil
2003
----
Ed. note: It is kind of Herbert to address the readers as 'advisor', but we don't want people to be misled. This is NOT a consultation service; it's a public forum where everyone is expected to give as good as they get. Every reader knows something, and a great way to learn is to try to teach ... so we're waiting to hear your answers as well as your questions :-)
Q. What could be a good DC voltage be to electropolish stainless steel?
pieter coetzeractive fleet - durdan South Africa
2006
A. Things are, I'm sure, different in Brazil than the U.S., Herbert. But the idea of running a process like electropolishing in a garage is a dangerous one. There is a tendency to think that the selection of the exact electropolishing formulation is the key to success, but it's not. So I'd try Benlogo's suggestion.
Pieter, if you don't find the guidance you seek in the previously mentioned article in the Metal Finishing Guidebook, there is a great chapter on electropolishing in the Electroplating Engineering Handbook ⇦ this on eBay, AbeBooks, or Amazon [affil link] . Voltage has very little to do with anything at all, but maintaining amperage in the 'polishing range' rather than the 'etching range' is a critical element. Good luck.
Merlin, to my knowledge carbon steel cannot be electropolished.
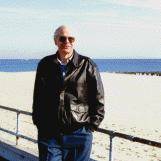
Ted Mooney, P.E.
Striving to live Aloha
(Ted can offer longterm or instant help)
finishing.com - Pine Beach, New Jersey
2006
Multiple threads merged: please forgive chronology errors and repetition 🙂
Electroolishing of surgical instruments
Q. I am a manufacturer of surgical instruments. I am interested in electro polishing my surgical instruments. Can anyone please give me the formula for the chemical composition of the bath as well as machine specifications and requirements? Thanks for your efforts in advance.
Rajesh ShoneyManufacturer - Pondicherry, India
2004
A. There are many different electropolishing solutions for stainless steel. The most extensive conveniently available list is in The Electroplating Engineering Handbook ⇦ this on eBay, AbeBooks, or Amazon [affil link] . There are also electropolishing chapters in the Metal Finishing Guidebook and ASM Metals Handbook, Vol. 5, Surface Engineering. The AESF (NASF) has an illustrated lecture on electropolishing. Dozens of formulas have worked, but if you focus on finding the best magical chemical formula, you are misunderstanding the subject and are therefore unlikely to achieve success.
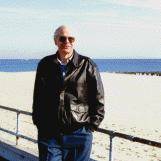
Ted Mooney, P.E.
Striving to live Aloha
(Ted can offer longterm or instant help)
finishing.com - Pine Beach, New Jersey
2004
2004
A. Dear Mr Shoney,
Sorry for not replying after visiting your factory on 6th January.
My concern with suggesting a chemical process for brightening and passivating SS is that your products are used in Surgeries and chromic containing chemistries that are carcinogenic; are not a good idea according to me.
I would suggest that you continue your mechanical buffing, cleaning operations with its difficulties and conclude the process with an Ultrasonic Cleaner. Maybe anyone else here may suggest a safe process.
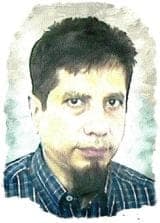
Khozem Vahaanwala
Saify Ind

Bengaluru, Karnataka, India
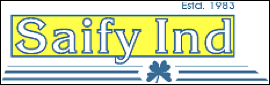
2004
adv.
There is an alternative to chromic-acid-based electropolishing. Non-acid saline based electropolishing will polish to mirror finish 300- and 400-series stainless steel. There will be no need for additional passivation step.
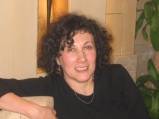
Anna Berkovich
Russamer Lab

Pittsburgh, Pennsylvania
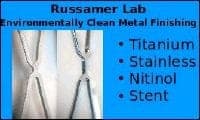
Q. Does anybody know preparation of stainless steel electropolishing mixture? We want to prepare it in our laboratory. Is this possible?
There are alternatives. For example: phosphoric acid, sulfuric acid, chromic acid etc.
We are not sure about the percentages. What might be?
Which one is the best for following issues: performance, economical, environmental, occupational health, easy to applicate & prepare.
Regards
Ayca CAKIRhealthcare products - Turkey
2005
Q. Looking for the chemical composition and metals in electropolishing solution for electropolishing 300 and 400 stainless steel. Also the specific gravity, percent of the acids, water content, metals.
Thank you,
metal finishing - Vicksburg, Michigan, USA
2007
ElectroPolishing of Stainless Steel -- Chemical Formulations
Q. I would like to know what percentages of sulfuric acid and phosphoric acid and any other chemicals required to carry out electropolishing of stainless steel.
Oliver HollardBathroom accessory manufacture - Nelspruit, South Africa
2006
2006
A. 40% sulfuric acid, 60% phosphoric acid
So 11 Volts
The object to electropolishing is anodic-- For cathode use Stainless steel 316L 1:1
Distance between electrodes 2 inches.
For hanger use copper.
Time 7 minutes or by the quality of electropolishing.
Best regards
- Santiago, Chili
2006
This formulation comes from the excellent book Metal Finishing Guidebook and Directory.
Phosphoric acid 40%
Lactic acid 46.5%
sulfuric acid 13.5%
The cold phosphoric and lactic acids are put into the tank first and then stirred to mix. Lastly the sulfuric acid is added and stirred. Heat is generated and the temperature will rise to about 65 °C.
sulfuric acid and lactic acid must not be mixed first because there is a chemical reaction which destroys the lactic acid and generates too much heat. 10% water is acceptable and reduces the tendency for the mixture to char and become black.
60 - 90 °C operating temperature is suitable. About 9 volts is typical.
The reason for using this formulation rather than the sulfuric phosphoric mixture is that I found that the high sulfur content of free machining stainless steels is less liable to be pitted. Metal removal rates are low and the polish is excellent. Maintenance does not require chemical analysis of the composition, just replace drag out with new solution.
- Whitstable, Kent, UK
A. For optimum, it is going to depend on the alloy and exactly what you need. Several books have good suggestions.
James Watts- Navarre, Florida
2006
I agree with James completely. I have seen straight sulfuric acid used in a very capable high production shop although a substantial mix of phosphoric acid is more common, and there are dozens of mixes. But a starting point is to really understand what electropolishing is about, and a great article on the subject is in the Electroplating Engineering Handbook .
It is problematic to try to learn the 'right' formula and the 'right' operating conditions, without much knowledge of things practitioners should probably understand about it, like the need for a clean surface, the problems of water accumulation, getting from the 'etch' range to the bright polishing range, why the parts probably won't get as bright as mechanically polished parts, etc.
Regards,
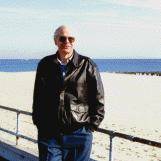
Ted Mooney, P.E.
Striving to live Aloha
(Ted can offer longterm or instant help)
finishing.com - Pine Beach, New Jersey
Q. We want to know the process of electro polishing of SS 316/SS316L. What is the composition of the electrolytic bath, what voltages are to applied and the temperature of the bath and time to keep the component inside the bath for best results?
Girish Anantha Iyer- Coimbatore, Tamilnadu, INDIA
2006
Multiple threads merged: please forgive chronology errors and repetition 🙂
Stainless steel electropolish chemical composition
June 2, 2008Q. I'm developing electropolish for stainless steel in India. So, I'd like to know if someone can help me giving the chemical composition of the liquid used in the bath.
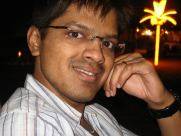
Sudarsan Avinash
partner - Chennai, Tamilnadu, India
A. Read this...
http://www.euro-inox.org/pdf/map/Electropolishing_EN.pdf
This was of immense help when I was finding out the requirements for an electropolishing plant
- Mumbai, Maharashtra, India
March 4, 2015
March 2015
A. Hi folks. There's a lot of good info on this page, but there has also been great progress in the last several years on "no dump" extended life electropolishing chemistry, and processes which use less toxic chemistry. Read the suggested books, articles, and websites, etc. ... but make contact with the proprietary vendors like Russamer Lab [a finishing.com supporting advertiser] to learn about what's new before making final commitments.
Regards,
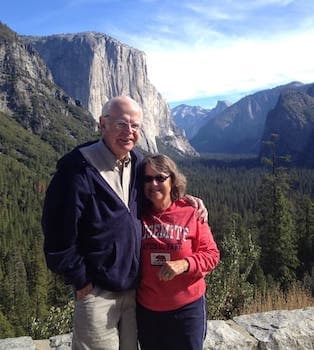
Ted Mooney, P.E. RET
Striving to live Aloha
(Ted can offer longterm or instant help)
finishing.com - Pine Beach, New Jersey
February 4, 2016
Q. Does anyone know the life of electropolishing solution?
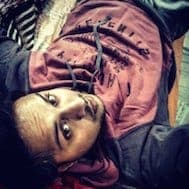
puneet singh
- Ludhiana, Punjab, India
February 2016
? Hi Puneet. What material are you electropolishing and what solution are you using? With that information, a guess might be possible. But these days there are "never dump" solutions, and a number of proprietary approaches as well.
Regards,
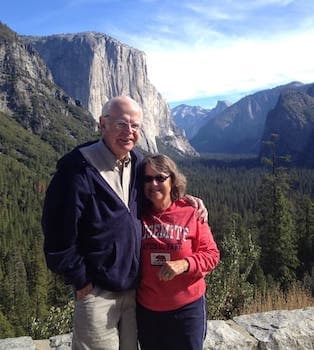
Ted Mooney, P.E. RET
Striving to live Aloha
(Ted can offer longterm or instant help)
finishing.com - Pine Beach, New Jersey
How to do electropolishing in my garage?
April 11, 2016Q. I would like to try to do electropolishing in my garage. Questions:
What stuff do I need?
How long to process?
What chemical do I have to buy?
The object I want to electro polish is:
1. metal
2. aluminum
Almost the object was part of machine of motorcycle.
This is first time I want to try. And I want to do it safely. Thanks.
hobby - indonesia, Bandung
April 2016
A. Hi Muliana. Electropolishing of aluminum is probably not a good hobby, and electropolishing of "metal" might not even be possible, depending on the kind of metal. You can read about the topic in textbooks and get a general introduction to it, but for motorcycle parts it will probably be cheaper, safer, faster, and much less to learn if you simply mechanically polish them, which is what "everybody" does. Please start with letter 800, "Aluminum motorcycle polishing -- rims, wheels, swingarm, frame". Good luck.
Regards,
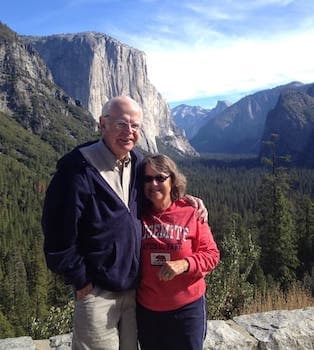
Ted Mooney, P.E. RET
Striving to live Aloha
(Ted can offer longterm or instant help)
finishing.com - Pine Beach, New Jersey
Q. FOR ELECTROPOLISHING OF BALL BEARING STEEL WHAT TYPE OF SOLUTION WE CAN USE? AND WHAT WILL BE THE COMPOSITION?
manisha baby- Bangalore, Karnataka, India
June 14, 2016
August 26, 2016
Q. Hi all
We are anodizers of aluminium in Bangalore. Polishing aluminium has been very difficult.
I used 60% sulfuric and 40% phosphoric acid
Temperature 60 degrees
I got excellent shine but metal removal rate is very high and pit formation in some places, and non-uniform shine in contours of parts.
Can anyone help me as to how to reduce metal removal rates and increase uniformity?
I guess we have to do something about throwing power!
Please suggest to me in this regard.
- Bangalore Karnataka, India
Q. I want to reduce the cost of electropolishing SS202. My workshop manufactures SS baskets. Is there any effective way?
Also how can I analyse the solution?
Currently I use 33 percent sulfuric and 66 percent sulfuric^phosphoric. And simply add sulfuric or phosphoric without calculations.
- Luncknow, India
August 27, 2016
Electropolish 304V Stainless
September 20, 2016Q. Hello everyone,
I am using following formula for electropolish of SS 304V, but can't get shining surface ... any suggestion? Please help.
Formula:
#1 sulfuric acid 41% = 543.25
#2 phosphoric acid 45% = 596.25
water 14% = 185.5
operating temp: 140 °F
Kind regards,
- Karachi, sindh, Pakistan
September 2016
A. Hi Adnan. I'm not familiar with that particular formulation, but dozens of different formulations have been successfully used, and I have no reason to think that your formulation would be unworkable when so many similar ones work. Where did you get the formula?
No part of your item polishes? Does it etch or does nothing happen? What current density are you using? Have you been electropolishing successfully and it suddenly stopped working, or are you just beginning your research and have never successfully electropolished anything before? Are you sure the surface is clean to the point of waterbreak-free?
If you can get access to the previously suggested Electroplating Engineering Handbook, it has an excellent chapter on electropolishing. We'd like to help, but if our response is limited to just suggesting a different formulation, odds are strong that it won't help much.
Regards,
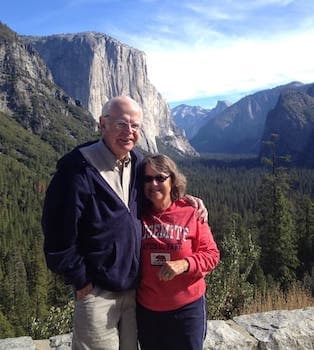
Ted Mooney, P.E. RET
Striving to live Aloha
(Ted can offer longterm or instant help)
finishing.com - Pine Beach, New Jersey
September 20, 2016
Q. Hello Sir,
Thanks for your kind reply. Following are the answers to your questions:
Where did you get the formula? I got this formula from the net I think it's made by ESMA.
No part of your item polishes? No sir, when I polish the SS 302 & 303 it was done very well but PH-17 & 304V SS polishes but not like SS slightly gray color try to a lot of times but can't get results.
Does it etch or does nothing happen? Yes it etches but color is slightly gray.
What current density are you using? 7 amps, per square inch, per minute (7 AMSI) at 140 °F.
Have you been electropolishing successfully and it suddenly stopped working? Yes, but you can say a beginner.
Are you sure the surface is clean to the point of water break-free? Yes
If you can get access to the previously suggested Electroplating Engineering Handbook? No, need your suggestion. Different formulation? You know the best one for said SS?
Kind regards,
- Karachi, sindh, Pakistan
(affil links)
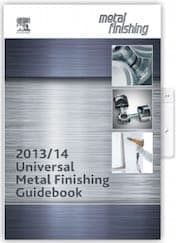
free pdf is currently available from academia.edu
A. Hi again cousin. I run this site and am somewhat familiar with most of the technologies we discuss; but I do not pretend to be heavily versed in all of them. Thus, I think 304V stainless steel is simply 304 which has undergone an extra vacuum purification, so I don't think it should electropolish any differently ... but I don't actually have any experience to make that claim with confidence. PH-17 is a precipitation hardened stainless, and my understanding is that it therefore requires blasting with glass beads or aluminum oxide before electropolishing.
As I've said countless times on this page, numerous solutions have been successfully used, and I don't feel there is a "best", but this letter includes many postings with formulations, and letter 46041 includes another which the people posting them felt were best or at least good. As mentioned, the Electroplating Engineering Handbook and the Metal Finishing Guidebook have additional formulations. Books may be hard to come by in your area, but simply dismissing the need for books is no good at all. You can find still more in patent databases, such as www.google.com/patents/US2334698
Do not consider perchloric acid in any electropolishing formulation; it is tragically explosive.
"Etching" is undesirable in the sense I was using it, and often indicates that the current is too low or the water content too high.
I don't know what you mean by '7 AMSI'. Maybe you mean 1 Amp/ sq. in. for 7 minutes? The current density must be high enough, probably need at least 1 Amp/ sq. in., maybe twice that, or you will get etching.
It is difficult to function without a good library of metal finishing books and without a proprietary solution vendor to assist you, but at least download the Metal Finishing Guidebook. Good luck.
Regards,
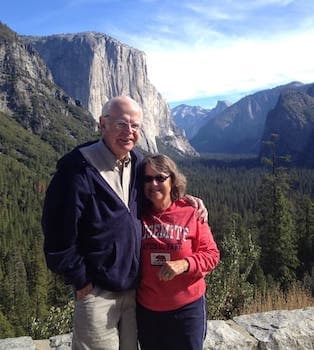
Ted Mooney, P.E. RET
Striving to live Aloha
(Ted can offer longterm or instant help)
finishing.com - Pine Beach, New Jersey
September 2016
A. Adman
I would try lowering the current density. Maybe even as low as 2 amps per square inch.
- Green Mountain Falls, Colorado
September 27, 2016
Q. Hello Willie Alexander,
You mean I will try 2 amps per square inch -- and what time?
- Karachi,sindh, Pakistan
September 28, 2016
A. Adnan
Yes, try electro polishing at 2 amps per square inch (290 asf) or even a little lower. Your 7 amps per square inch could be near the upper limits. Then try in between to find what works best. Time will depend on the starting condition of the surface. Rougher surfaces will take longer than smoother but you will still get a shiny finish first. Smoothing requires longer times for more metal removal.
- Green Mountain Falls, Colorado
September 29, 2016
Q. Can anyone help me how to electropolish stainless steel and aluminum using sulfuric, phosphoric and chromic? What is the concentration for each?
Luvex vilia- Cebu, Philippines
September 28, 2016
Hi Luvex. At least 4 electropolishing formulations are already printed on this one page, with references to authoritative sources for additional information, and suggestions that you consider proprietary formulations, and that you skip chromic acid. Is there a particular reason that you want to use a mix of sulfuric, phosphoric, and chromic acids even though you don't know a suitable ratio?
There is a lot to the topic, and I suggest you do some preliminary research into it before falling into an assumption that an exact ratio of three acids is the key to electropolishing--dozens of different formulations have been used, and I've already mentioned that 100% sulfuric - 0% phosphoric - 0% chromic is one such workable possibility. If you don't have books on hand yet, you can start with the on-line version of the Metal Finishing Guidebook. Best of luck!
Regards,
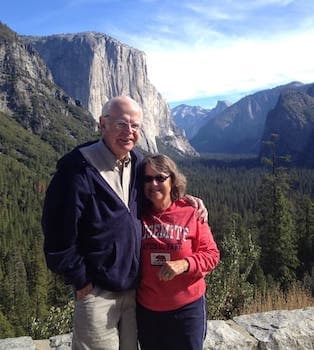
Ted Mooney, P.E. RET
Striving to live Aloha
(Ted can offer longterm or instant help)
finishing.com - Pine Beach, New Jersey
September 2016
October 12, 2016
adv.
I would like you to inform that we have managed to electropolish to mirror finish (no burrs whatsoever) on small pieces of aluminum alloy. So far we do not see any limitations on what aluminum type we cannot electropolish. We are still in the test mode, and are experimenting only on small parts so far.
I think this electropolishing method is suited mostly for high-value parts, for example in electronic industry or airspace, where the level of deburring is extremely important.
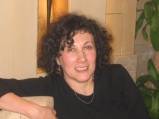
Anna Berkovich
Russamer Lab

Pittsburgh, Pennsylvania
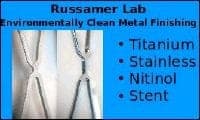
Q. I used to electropolish SS 202 with 50% phosphoric and 50% sulfuric. Is it possible to change the chemical ratio to give SS a mirror shine finish in non polished wire and non polished pipe? And what would be exact time to be in the tank?
Sumit Poddar- Ludhiana India
February 26, 2017
Q. Hello, I run my own SS electropolishing plant and use ready-mixed chemicals for the work. I would like to produce my own chemicals: can anyone please help me out in composition? I tried a mix of 75% phosphoric acid (of 85% strength)(85%) and 25% sulfuric acid (of 98% strength).
I would just like to know the concentration of sulfuric acid as 98% is more concentrated.
We electropolish SS202 wire baskets. Kindly suggest the composition with concentration percentage and weight percentage.
Thank you.
- Kolhapur, Maharashtra, India
January 7, 2018
A. Hello Mahesh. There are modern proprietary formulations of "never dump" chemistry and other higher tech solutions. But if you want to stick with simple mixes of mineral acids: there are few that absolutely won't work. There are a dozen listed in the Electroplating Engineering Handbook, and I have even seen pure sulfuric acid used in a high production electropolishing shop. Your proposed mix is widely used and accepted, but it is important that you use concentrated sulfuric acid because even fairly small amounts of water in the solution can cause etching.
Regards,
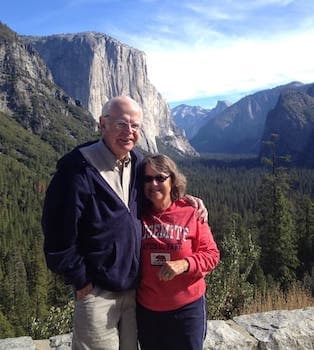
Ted Mooney, P.E. RET
Striving to live Aloha
(Ted can offer longterm or instant help)
finishing.com - Pine Beach, New Jersey
January 2018
Q. Thanks a lot sir; I tried 85% conc. HP3O4 & GLYCERINE, BUT FOAM OCCURS DURING PROCESS.
Is there any anti-foam agent I can add to solution & its %?
Please suggest sir.
- Kolhapur, Maharashtra, India
January 8, 2018
January 2018
A. Hi again, Mahesh. Sorry, but I don't know the answer to that, nor even whether that is an accepted mix. But a good starting point is the books mentioned on this page. The EEH offers lots of patent numbers you can search. If you have no city or university library with metal finishing books accessible to you, and you can't find enough info in the on-line version of Metal Finishing Guidebook which we previously suggested, then please use a free patent search like
https://www.google.com/patents/
to search for "stainless steel electropolishing solution" or other terms which suit your needs. Best of luck.
Regards,
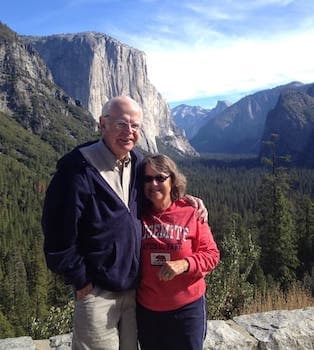
Ted Mooney, P.E. RET
Striving to live Aloha
(Ted can offer longterm or instant help)
finishing.com - Pine Beach, New Jersey
Q. We electropolish SS 316 and 304 wire ropes and get corrosion problems after long storage. We have one tap water and two hot water rinse after electropolish. Please suggest how Post cleaning can be made more effective.
Rajiv jain- gurgaon , Haryana and India
May 13, 2018
May 2018
A. Hi Rajiv. If you're not using DI water for your final rinse, you probably should. It's also possible to add corrosion inhibitors .
But if this wire rope is being stored under the same roof where chemical processing is done, it can be a very corrosive environment. Good luck.
Regards,
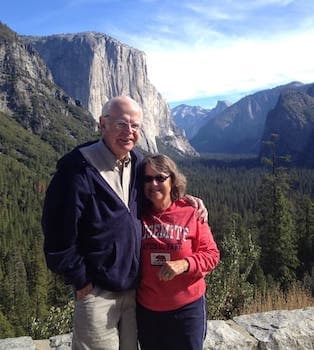
Ted Mooney, P.E. RET
Striving to live Aloha
(Ted can offer longterm or instant help)
finishing.com - Pine Beach, New Jersey
Q. Hi Ted,
Is there a particular edition of the Electroplating Engineering Handbook that has the chapter on Electropolishing? I see a university near me has the 1971 edition on the stacks, but the one you have linked to on the finishing.com site lists the most current as a 1984 edition. I'd rather just order that one if it has more relevant info. Thanks!
- Massachusetts USA
September 26, 2018
A. Hi Dana. The 1st Edition was 1955, the 4th (and current) Edition was 1984. I don't recall ever seeing a 2nd or 3rd Edition, although one of them apparently was 1971 :-)
Sorry but it has been so long since I've seen the 1st Edition that I don't remember whether it has the Electropolishing chapter. The 4th Edition definitely does -- I just checked mine.
Regards,
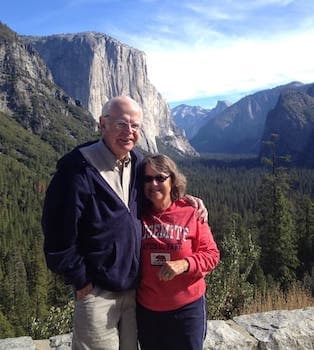
Ted Mooney, P.E. RET
Striving to live Aloha
(Ted can offer longterm or instant help)
finishing.com - Pine Beach, New Jersey
September 2018
Q. I have a solution containing 53% Phosphoric Acid (75%), 45% sulfuric Acid (96%) and 2% Triethanolamine (99%) one of main users is commenting on lack of final shine would you consider there is too much water present or do I need an additive (preferably not chromium)?
Many Thanks
John
Performance Chemicals Ltd - London, UK
September 16, 2019
A. 75% phosphoric/25% sulfuric is the usual formulation It may work better for you
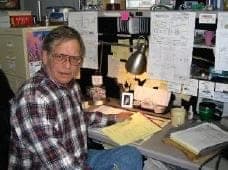
Jeffrey Holmes, CEF
Spartanburg, South Carolina
September 17, 2019
September 18, 2019
Jeffrey, many thanks for your guidance will update you in due course.
Best Regards
John
Performance Chemicals Ltd - London, UK

Q, A, or Comment on THIS thread -or- Start a NEW Thread