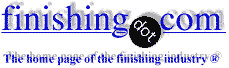
-----
Chromate carburetors/diecastings: is zinc plating required first
Current question and answers:
Q. SO IT IS NOT SAFE TO DO IT OURSELVES , FINISH OUR OWN CARBS. QUESTION IS "WHAT PAINT IS AVAILABLE THAT LOOK'S LIKE SAY HOLLY OR ROCHESTER CARBS. I AM NOT BEING SPECIFIC ANY REASONABLE PAINT WILL DO. COULD BE IN A CAN AND COULD BE DUAL ACTIVATED PAINT IN A CAN, MUST BE IN A SPRAY CAN PLEASE. WHAT ARE THE CHOICES OUT THERE ?
MICHAEL BOSCARINOhobbyist - COCONUTCREEK FLORIDA
September 19, 2021
A. Hi Michael. I don't think anyone on this thread said it wasn't 'safe', although strong & regulated chemicals are surely involved. But they said the likelihood of successfully re-chromating a carburetor without first zinc electroplating it was low.
Yes, there are spray paints intended to look like the gold/yellow chromate coating on O.E.M. carburetors. Eastwood has a 3-step system where it looks like you paint the whole thing with their gold color, then touch up with little streaks of red and green to give the iridescent look. But I can't say how well it works.
Luck & Regards,
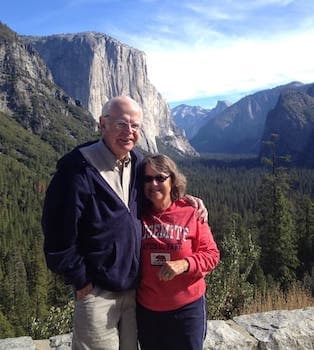
Ted Mooney, P.E. RET
Striving to live Aloha
(Ted can offer longterm or instant help)
finishing.com - Pine Beach, New Jersey
September 2021
September 20, 2021
Ted, years ago I researched the same system you're talking about. One of the carb. re finisher & Tri-power builders gave the information away. So I just asked him recently if I can use this same finish on the Rochester carbs, and he said no. He wants me to buy carb. renew 2 that Eastwood can't get from China at this time. So I figured he lied because I wrote the formula down about "Golden Cad and Red /Green"in my notes. After reviewing the notes I found that he did use this kit 7-8 years ago. Anyway, there goes the trade secret.
So I just got off the phone with Eastwood and we came up with this system:This is what I am going to try on my 1966 Pontiac Tri-power Rochester carbs:
1) Media Glass Bead the parts on the outside only.
2) Since I polished these carbs before and did not clear over them, they dulled too soon; but I believe that 3 different polishes and 3 different wheels could have closed the pores of the metal enough that I won't have to repeat the process again. Triple polish the carbs first, then media Blast.
3) Prep.and Paint using 16160Z Golden Cad 3-step Eastwood red/green. Apply Golden Cad first on Body and air Horn and certain Linkage parts that you choose. After normal prep. is completed then lightly over cast an Antique look with the Red and Green. Use Silver Cad on some of the linkage also #10022Z. I am going to use the silver cad on the lower Throttle Bodies.
I am not spraying any paint on the inside nor am I painting the valves. Plug off any holes with wire or pin so you don't have to rod them out later as much. Next, clear with 2K Matte Clear # 14792Z. This clear is the 2-part can that you activate the hardener.This will protect the entire job according to Eastwood.
I will post the Pictures on this site when I am done and I will post any problems that I run into so people won't make the same mistakes. Linkages won't get the Red or Green over spray like the Air Horn and Body. All Linkages will get cleared. All linkage will be media Blasted to remove any existing paint. I am going to clear coat as I go and try another clear coat when the parts are assembled if I deem it necessary.
MICHAEL BOSCARINO [returning] hobbyist - COCONUTCREEKSeptember 2021
Thanks for the very complete explanation.
Luck & Regards,
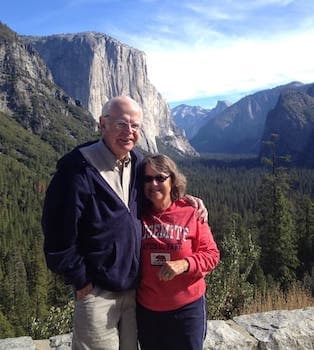
Ted Mooney, P.E. RET
Striving to live Aloha
(Ted can offer longterm or instant help)
finishing.com - Pine Beach, New Jersey
⇩ Related postings, oldest first ⇩
Q. Can someone please give me his input regarding the below concern.
I am employed in an automotive company producing switchgear and are currently in the process of designing a zinc alloy based part that obviously requires some sort of anti tarnish treatment. We will be using a trivalent compound!
However, what we are not certain of is if there is any need to zinc plate the part prior to any passivation.
Regards,
Gregory Joslin- Malta
2001
A. I have seen zinc plating of zinc diecastings, but in my limited experience it seemed to be that it was done to impart a uniform & shiny surface (see thread 35697 "Carburetor re-plating / re-coloring"). But sometimes diecastings are successfully directly chromated without first zinc plating them.
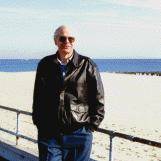
Ted Mooney, P.E.
Striving to live Aloha
(Ted can offer longterm or instant help)
finishing.com - Pine Beach, New Jersey
2001
----
P.S., March 2015: Note that no one on the "Carburetor..." thread I referred to offered any corrosion testing reports. And after seeing the knowledgeable input from Tim, Khozem, Robert, Tom, and others below, I don't think direct chromating of zinc diecastings is a good strategy :-)
A. The older zinc-alloy plating systems consist of a zinc-alloy plating followed by hexavalent chrome passivation. The zinc-alloy protects the base metal from red rust. The passivate protects the zinc-alloy from white corrosion.
In the new system, you have the same zinc-alloy plating followed by a trivalent chrome passivation. Since the trivalent chrome is not as good as the hexavalent, you sometimes need an additional layer of something after the passivation. However, you definitely still need the zinc-alloy.
Passivation with no plating does not make much sense. It is like trying to build a wooden house with paint and no wood.
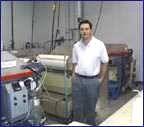
Tim Neveau
Rochester Hills, Michigan
2001
A. Aptly said Tim!
I have Salt Spray tested parts with passivation over Zinc without plate and there is only about 1 hour difference between bare castings and passivated ones to white rust.
However these parts are for two wheeler manufacturers facing extinction from imaginary Chinese competition, hence cost reduction is the issue, not corrosion protection, so choose wisely before changing specs.
By the way we did a good job on the chromating and also tested parts for the presence of the chromate film. As an undercoat to paint or lacquer, chromate alone is okay, but not as a final finish.
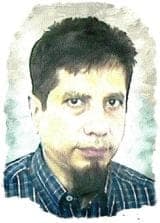
Khozem Vahaanwala
Saify Ind

Bengaluru, Karnataka, India
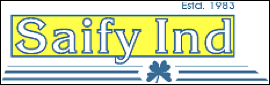
2001
Q. Can we zinc plate a zinc alloy part? How about an aluminium part?
Amaya Munoz- Michigan
2002
A. Zinc dissolves in a cyanide bath, so although I've never tried to do it, I guess the zinc alloy substrate can be attacked before deposition begins and the adhesion could be affected. Obviously zinc alloys are affected by acid zinc baths as well.
Guillermo MarrufoMonterrey, NL, Mexico
2002
A. You can zinc plate over zinc die cast with an alkaline zinc bath. What do you mean by zinc alloy? You can plate zinc over aluminum, but must utilize a zincate process (does incorporate a few process tanks). Suggest you contact a local proprietary vendor for help. Several support this web site nationally.
Bill Hemptech svc. w/ chemical supplier - Grand Rapids, Michigan
2002
A. Hundreds of times I have recommended and implemented the concept of improving the quality of yellow chromate on zinc die cast (the surface of which is about 7% aluminum) by first zinc electroplating a purer top coat of zinc upon which the chromate forms a better gel.
On one occasion I successfully improved the quality of zinc electroplate on rivets by first plating with alkaline zinc to get "throw" under the head and then top coating with acid chloride zinc to get a brighter appearance.
One rather unique way to plate zinc over aluminum that has not yet found a market niche is to clean the aluminum by removing organic soil and then deoxidizing then placing in a alkaline zinc-cobalt or alkaline zinc-nickel or alkaline zinc-iron or any alkaline zinc 30 seconds before turning on the current, then turn on the current and increase very slowly up to about 15 ASF, then plate for thickness. You see, the matrix of the alkaline zinc systems solution is also the matrix of a "zincate" therefore you apply the zincate right in the solution before you start plating.
Just note that zinc die cast is NOT pure zinc. Aluminum die cast is NOT pure aluminum therefore all I have said must be developed around the particular alloy.
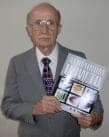
Robert H Probert
Robert H Probert Technical Services

Garner, North Carolina
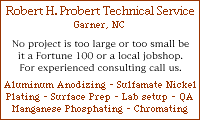
2002
2002
A. Zinc from an alkaline Cyanide-free solution is plated over properly cleaned Zinc diecastings containing less than 5-6 percent aluminium as a regular practice to a thickness of 8 microns.
Then the parts are rinsed, activated in 1 percent Nitric acid, and chromated.
If Aluminium has to be zinc Plated, Zincating is the first step after pre treatment, followed by 8-10 microns in Alkaline Cyanide-free zinc, rinses, activation, chromate, dry.
Alkaline Zinc is plated as bright as required for a particular need and accepts all chromate coatings readily.
Regards,
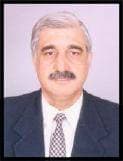
Asif Nurie [deceased]
- New Delhi, India
With deep regret we sadly advise that Asif passed away on Jan 24, 2016
Multiple threads merged: please forgive chronology errors and repetition 🙂
Passivating / Chromating of zinc diecastings -- salt spray life?
Q. Sirs - are we being fair to expect yellow passivation only; as a coating on zinc Diecastings to give salt spray resistance to 96 hours.
Tony CorbettGecom Uk - Birmingham.UK
2005
A. Yellows do typically go up to 96 hours. However you must realise that they are usually applied to a freshly plated item, that is one with a nice even corrosion free & activated surface.
Perhaps you could get 96 hours out of yellow chromating diecast parts, but I bet surface prep would play in important role in this.
- Melbourne, Vic, Australia
2005
Multiple threads merged: please forgive chronology errors and repetition 🙂
Q. We are experiencing tiny blisters on our parts two to three days after they are plated. The parts looked fine immediately after the plating. What is causing the problem?
Jim TouMTI - Clarence, New York
2006
2006
A. Blisters can come from many different things. Typical is...
1) too much brightener or organics in the solution
2) bad pretreatment
It would be helpful to get more information on this problem.
1) What type of zinc solution are you using?
2) Is the zinc layer chromated or passivated?
3) Where on the parts is the blistering occurring?
CRC Specialist - Budapest, Hungary
A. Look for a pattern in the porosity, most likely it is a hot spot in the die casting process or fill related. Try to raise the die temperature and increase the pressure on the injection during solidification. Look at the die condition, you may find that there is a loss of pressure there. Try some of the die coating products... polish the die. Look at process control, often so much is based on visual criteria. Some times it can be plating solution entrapment, but that is only a expedited symptom since casting is full of pores anyway.
What it is.. there are micro pores in the casting from the solidification of the metal, these fill with solution ( even water will do this )often plate over and then bleed out, peeling and or blistering later on.
Pending on the economics you may need to impregnate the part to fill the voids. One other trick is to vibromill the parts, not to remove the surface but to peen over the surface to close the pores ( part on part, or a polish treatment.)
- lake in the Hills, Illinois USA
January 11, 2011
Multiple threads merged: please forgive chronology errors and repetition 🙂
Must Zamak 5 be Zinc Plated?
Q. Is there any need to Zinc plate Zamak 5?
The product I am manufacturing is used in doors and will not be exposed to external weather conditions.
- Beijing, China
December 24, 2012
A. Hi Christopher, I don't think you should either chromate or plate it at all, if you must then CED paint is the acknowledged best coating solution for zinc diecastings than any other coating process.
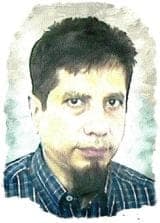
Khozem Vahaanwala
Saify Ind

Bengaluru, Karnataka, India
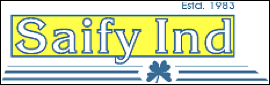
December 28, 2012
A. Hi Christopher.
Interesting question.
Zamak 5 is zinc diecasting. The conventional method of plating on Zinc diecasting, as stipulated in ASTM B252 - 'Standard guide for preparation of zinc alloy die casting for electroplating and conversion coating', involves a cyanide copper strike followed by the subsequent required plating. There are no zinc plate involved here.
A lesser known method and to move away from cyanide, which is more harmful to the environment, is to plate a zinc or zinc alloy (preferably an alkaline zinc bath followed by the subsequent required plating. Enthone OMI has a 1996 patent on this method (US Patent 5578187). In this case, the zinc plate is mandatory.
Good Luck.
- Penang, Malaysia
December 28, 2012
A. Hi Christopher. I learned something from Cheah's answer, but I'm not certain if that was actually your question. I think your question may have been whether zinc diecastings are sufficiently corrosion resistant for interior use without further surface treatment.
If you have no specific standard to meet, we are into the realm of personal opinion about what is good enough and what isn't.
Based on a corrosion test project which finishing.com completed for the IZA last year, I agree with Khozem that CED performed quite well in the corrosion tests.
Regards,
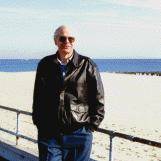
Ted Mooney, P.E.
Striving to live Aloha
(Ted can offer longterm or instant help)
finishing.com - Pine Beach, New Jersey
December 28, 2012
Thank you for your responses, it was my customer's requirement to Zinc plate Zinc die casting components.
They have requested a Zn 5 µm coating with clear passivation, due to possible exposure to external weather.
A 5 µm coating does not provide adequate protection, as per ISO or ASTM requirements, so I was asking does Zinc Die casting really need to be coated to prevent corrosion.
From all your responses the answer is yes.
Thank you
- Beijing, China
January 3, 2013
Direct passivation of diecastings
March 2, 2015Q. Our company intends to do direct passivation on zamak (V). Process sequence for direct passivation on zamak is:
Hot degreasing
Rinse
Activating
Rinse
Passivating
Rinse
Sealing
Drying
I activated zamak in a 5% hydrochloric acid (30 - 60 min), but the result of NSS (natural salt spray test) was only 72 hours. Demand for these pieces is 144 hours of NSS.
Has anyone experience in this surface treatment? How do you activate Zamak?
Any idea will be helpful.
- Slovenia
by Safranek & Brooman
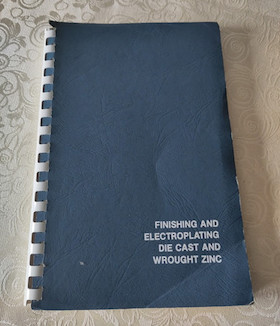
on eBay or Amazon
or AbeBooks
(affil link)
Q. I would like to know if Zamak parts need to be mandatorily Zinc Plated and then Chromate (Trivalent) passivated to get better white rust prevention (72 Hours White Rust). Can this 72-Hours Rust prevention also be met by simply Chromate passivating the Zamak Part directly? Seeking your valuable advise on the matter. Thanks.
Ravneet SinghNew Product Development Professional - Delhi, India
August 21, 2015
A. Hi Teja,
We appended your inquiry to an earlier thread on the same subject. It seems that direct chromate conversion coating is problematical and not really advised. In this age of trivalent chromating, using more finicky, proprietary, processes on substrates for which they were not intended is even more questionable.
Hi Ravneet,
We appended your inquiry to a thread where Teja claims 72 hours was achievable. Still this process doesn't sound robust. And if you want QA traceability you will need to find a statement from the trivalent chromate conversion chemistry supplier that their process is designed for use directly on Zamak castings (and you probably won't). Good luck.
Regards,
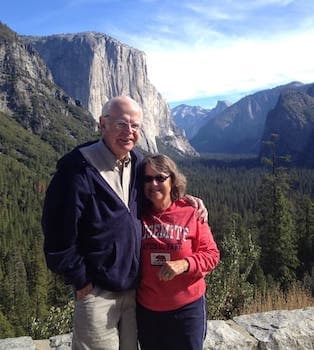
Ted Mooney, P.E. RET
Striving to live Aloha
(Ted can offer longterm or instant help)
finishing.com - Pine Beach, New Jersey
A. The reason that Zamak presents a problem for conversion coatings is that there are a number of Zamak alloys (2, 3, 5, and 7 being the most common) and within each numbered alloy there is variation in metal content. So it would be uneconomical for a metal finishing supplier to develop a large number of passivates that would be specifically targeted to a single alloy, of which there are probably dozens. And not only would it take time to develop them, and they would have to stock small quantities. That's why the most common commercial practice is to plate with zinc and passivate the zinc, as many formulations and suppliers are available. So the optimal coating for Zamak would be one that does not react with the substrate. So the best bet would be a topcoat of a paint like Doerken, Magni, Zintek, Geomet or the like. A single coat should give 200+ hours, but check with your supplier. No-rinse or dry-in-place trivalent passivates are available in the USA but not generally worldwide.
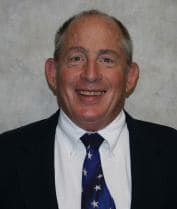
Tom Rochester
CTO - Jackson, Michigan, USA
Plating Systems & Technologies, Inc.

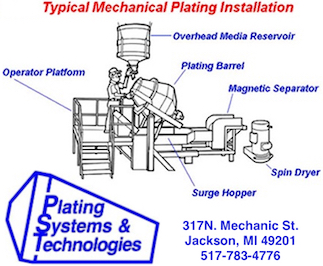
September 11, 2015
Q. I have a customer with zinc casting components who requires a zinc plate topcoat. My last plater was using a cyanide copper strike, then zinc/chromate. They "lost" the process and no longer are willing to try.
Is there a different process? I am having difficulty finding platers in the SF Bay Area who have cyanide copper.
buyer - San Jose, California USA
December 18, 2015
October 8, 2020
Q. The following problem happened at our barrel zinc plating line, on zamak pieces. Some of the pieces came out with a lot of small blisters (see attached pictures).
These 'blisters' tend to peel off if scratched.(also shown on one of the pictures) They don't seem like the usual blisters that are sometimes found even on raw zamak pieces.
The process is as following:
electro-degreasing (alkaline bath, anode-cathode prepolarization)
activating
zinc (alkaline, non-cyanide)
activating
brightening
passivating
sealing
Not all of the pieces plated at the same time had those blisters, and when checked later we couldn't find any of these blisters on raw material (although not 100% checked)
Is it possible that the cause is an old rectifier not working properly? Maybe raw material after all? Or could it be something else completely?
Any idea will be appreciated.
- Ljubljana, Slovenia
A. Hi Robert. The rectifier wouldn't be my first guess. But what is not clear to me yet is whether this is an established process which started acting up, or whether you have not yet obtained reliable robust plating on these components.
My experience with zinc plating of diecastings is limited, but it looks to me like the castings in the top photo have received no mechanical pretreatment. And while we appreciate you not naming proprietary treatment chemistry, if any, your description of your process is general enough that I'm not really learning much from it.
One thing I have seen on barrel lines is one barrel not quite meshing with the rotation drive on an important tank like your electrodegreasing tank, and leaving the parts dirty such that they blister like this. Make sure you "walk the line" to find out what really goes on, not just what the paperwork says :-)
Hopefully between the entries already on this page, and the anticipated responses, you will get some useful input.
Luck & Regards,
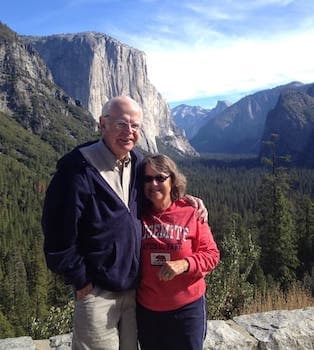
Ted Mooney, P.E. RET
Striving to live Aloha
(Ted can offer longterm or instant help)
finishing.com - Pine Beach, New Jersey
November 2020
Carburetor cleaning and refinishing has been a perennial subject. Please see also --
• Topic 0338 "Zinc plating & chromating of Carburetors"
• Topic 11847 "Restoring gold Iridite color to diecast parts"
• Topic 33779 "Clean and brighten carburetor bodies"
• Topic 35697 "Carburetor re-plating / re-coloring"
• Topic 37255 "Restoring the yellow dichromate finish on automobile carburetors"
Q, A, or Comment on THIS thread -or- Start a NEW Thread