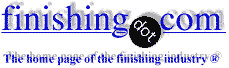
-----
Restoring gold Iridite color to diecast parts
Quickstart:
Aluminum is often 'chromate conversion coated' as a corrosion resistant final finish or as a pretreatment for painting or powder coating. The process actually involves many steps, usually including alkaline cleaning, etching, deox/desmut, the chromate conversion step per se, and water rinses between each step.
MIL-C-5541 / MIL-DTL-5541 / MIL PRF-5541 is the most commonly cited spec. "Alodine" and "Iridite" are proprietary trade names from two suppliers of the process chemistry. "Chem film" is a slang term for the process often used in the USA.
Q. I have an antique motorcycle restoration shop in Texas, Part of my job is to rebuild and restore antique motorcycle carbs from the 1940's-60's (Tillotson in particular here)
Originally the carburetor body and some of the die cast parts were gold chromate to keep the parts from corrosion. It took me a long time to finally get someone to teach me how to renew this finish.
I have been doing this for 20 years now, a big thanks to the guy up in Wisconsin, that didn't mind sharing his knowledge of the process with me. He was cool enough to send me a lab report with all the processes and amounts/temps, etc.
Step 1 was to bead blast the body and the other die cast parts with some real fine glass beads at low pressure to remove all the organic matter. Next was to "soak" the parts in a caustic soda mixture. I learned how to mix the solution, using red devil lye [caustic soda beads in bulk on
Amazon [affil link]
and distilled water. So I made up a batch. What I would like to know is; what exactly does the caustic soda do to the freshly blasted part? He failed to mention how long the "soak" was supposed to be. Next was the hot water rinse. No problem there. Next the part was submerged for 10-45 seconds in a chemical polishing solution, which is basically 5 different types of acid, each with a different percentage and distilled water. This is supposed to polish the metal chemically, so the gold chromate will do it's job on the base metal, Next was to rinse the part in hot water. Next the part went into a gold chromate solution for 3-10 seconds, followed by a cold water rinse and dried in heated air.
I'm just trying to understand what each bath does to the actual part. The process works good, but for some reason the polishing bath tends to get contaminated fairly quickly and I'm not sure why (and the solution ain't cheap), as the parts are really clean before ever touching the polishing solution
vintage motorcycle shop - Wills Point, Texas
February 21, 2021
⇩ Related postings, oldest first ⇩
Q. Can anyone suggest the best way of cleaning corroded aluminium castings? These are automotive, (gearbox tops, bellhousings, etc.) The original finish was satin, ripple finish and bright. The condition now is usually(white and grey) corrosion in parts. I am reluctant to use abrasive methods which will alter the original surface texture. I also want to find a method of cleaning very dark grey oxidation from Mazak zinc diecastings (carburetor bodies).Chromic acid has been suggested - any comments?
ANGUS M [last name deleted for privacy by Editor]- UK
2001
Q. I own a Antique motorcycle restoration Company. I have been searching for 3 years in vain to try and find a solution on how to refinish (gold Iriditing) antique carburetor bodies. The bodies are die cast zinc (pot metal). I have NOS complete carbs that truly show the correct gold Iridited finish. Some of them have more of a green rainbow effect and some have the yellow rainbow effect.
I have been told by a few companies that I could bead blast the castings in question and dip in yellow chromate solution. SO I got a gallon from a aircraft plater in my area (Dallas). He said the same thing. I got a small NOS part that the original gold was fading from and tried it. One minute, two minutes, 5 minutes, etc. every time I would rinse the part in water, the gold color would wash right off ! So I figured I would leave this small part in overnight to see what effect it would bring WRONG ! When I pull the part from the solution and wiped it off with a rag; to my amazement, it FELL APART in chunks. Well that was a waste of time and a waste of a valuable part !.
I called Holley Carbs to see if they could shed some light on the subject and they were NO HELP. They just wanted $100 per body (the body of the carb would nearly fit in a package the size of a cigarette pack). Some companies tell me that I need to cadmium or zinc plate the parts before using the chromate. I sent a body off to try this. It came back gold Iridited but the surface finish of the body looked like the surface of a piece of heavily galvanized steel.? I would so much appreciate if someone would help me out of the predicament I am in. I don't want to give up on restoring these bodies, but I do want to achieve the CORRECT finish on the parts.
ANY AND ALL COMMENTS APPRECIATED.
Charles Hallamvintage motorcycle shop - Wills Point, Texas
2001
A. Dear Charles,
We apply chromate conversion coatings to aluminum alloys rather than zinc. However I have had problems in the past coating previously coated parts via bead blasting alone. The resulting finish, if it has taken at all has been patchy at best. We blast at 30 to 40 psi using a fine glass bead media. Anything more aggressive than this causes more damage than we can accept.
If I need to coat a previously coated parts I completely strip the old coating first. This can be done in a number of ways and there are chemical formulations on the market which will do it for you, however I find the following very effective on aluminium, obviously you would have to check its suitability for your zinc castings and modify it accordingly.
1. Degrease (vapour or cold solvent)
2. Boil in water (90 degrees C +) for 15 to 30 mins, this begins to degrade the corrosion resistance of the coating. (chromate conversions on AL don't like temps in excess of 65 degrees)
3. Nitric acid clean for 5 to 10 mins (13 % ish)
4. Deoxidiser / desmutter bath
5. Ultrasonic clean in water. (if not available an old tooth brush will do the job)
As a rule I have found that the longer the components are boiled the shorter the time required in the Nitric tank. If the coating is not completely removed re treat as above but miss out the Nitric so as to avoid over etching.
Once satisfied that the components are clean try the conversion coating, it should take with ease.
Hope this helps a little, let me know.
Rich Mosley- UK
A. This process works fine for aluminum parts but zinc die cast will go up in smoke in nitric acid. An old time recipe is 186 g/L sodium dichromate and 6 ml sulfuric acid/L. Exposure time will have to be determined. Doing zinc castings is tricky because of the many variations in composition of pot metal. Do not rinse vigorously just dip in a rinse tank and let dry. Hope this helps.
Jan Soroka- Dallas, Texas
January 3, 2008
Multiple threads merged: please forgive chronology errors and repetition 🙂
Chromate (CrO4-2) and dichromate (Cr2O7-2) are not the same thing -2 to a chemist, but to a carburetor refinisher they are.
Dichromate and carbs
Q. I am in the process of restoring some old vehicles. One area that could use some expertise is renewing the finish on old carburetors. I understand that the manufactures used a dichromate finish. Could you explain how I might set up at home to renew that finish. What chemicals and where I could get them in small quantities. I have most of the PPE needed to work with chemicals. How would the metal of the carb need to be prepped?
Thank you,
Lew Ladwig- Lafayette, Colorado
2001
A. Have you ever watched the movie "Erin Brockovich [affil link to Amazonaffil links]" starring Julia Roberts? The subject of the movie is hexavalent chrome, and it revolves around dozens of cancer victims suing a polluter of this chemical. This movie is based on a true story. Dichromate IS hexavalent chrome. So, are you trying to make your own personal version of the movie?
A much better idea would be to get this job done by an industrial plating shop. They have the expertise to work with, handle, and dispose of these chemicals properly. You will have to pay a good amount of money for a custom job, but it really is the only way to go.
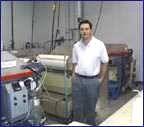
Tim Neveau
Rochester Hills, Michigan
2002
A. While it is possible for a beginner to follow the procedures and get a reasonable finish, carb housings will try most experienced shops. Reason, they are typically a casting that can be a pain when new. These castings will absorb a lot of hydrocarbons (gas/oil) that are very hard to get out and will give you a very poor quality appearance. It can be done, but there will be a lot of trial and error.
Most reputable vendors will not sell to you unless you have a haz waste disposal number from the state.
Handling haz waste can be very expensive unless you are very familiar with the CFRs (Code of Federal Regulations) -- these are books in size and written by lawyers.
James Watts- Navarre, Florida
Multiple threads merged: please forgive chronology errors and repetition 🙂
Yellow iridescent chromating of castings
Q. I am attempting to re-dye carburetor castings in the original yellow iridescent color. The castings are bead blasted, vibratory finished to smooth and brighten the castings, then dipped in a approx. 2% sulfuric solution for about 15 sec. rinsed then dipped in yellow chromate for a approx. 5 sec. The pH of the chromate is around 2-3 at room temp. Color is coming out dark/dull/bronze not the iridescence I am attempting to obtain. Any suggestions? Is my pH too high, and should the temp. be raised or is it in the pretreatment?
Joe Compton- Henrietta, New York
2002
A. A couple of months ago I would have assumed this would work. But then I started reading that sometimes you have to zinc plate these old zinc diecast items if you want to achieve a nice iridescent yellow dichromate finish.
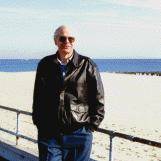
Ted Mooney, P.E.
Striving to live Aloha
(Ted is available for instant or longterm help)
finishing.com - Pine Beach, New Jersey
A. First, I presume you are schooled in the use of hazardous chemicals and have made provisions for the proper environmental disposal of your rinse waters and wastes. That being said, it would appear that two things are out of the ordinary. First, the immersion time in the chromate solution would usually be 15 to 45 seconds depending upon the solution concentration and temperature (should be 70 to 75 deg F.). Second, the pH of the chromate solution should typically be 1.8 to 2.2. You do not mention the formula for the dichromate solution which does make it harder to help. Ted is right that zinc plating the casting first will result in a superior finish (and much more consistent) however the lack of coloration you are referring to is more often due to the chemical formulation of the dichromate solution and other operating conditions. Proprietary products vary considerably in their colors and degrees of iridescence.
Gene Packmanprocess supplier - Great Neck, New York
A. I read the article on recoloring carburetors and it interested me for the reason that I would like to restore my own carburetors, I am currently restoring two '63 impala ss and a '64 impala ss,. I did some research and I found out that the chromic acid, which is hard to find, can be made by using sulfuric and nitric acid to dissolve chromium trioxide which is easier to get so I read, then you would anodize the part you want to recolor you can add dyes to this acid base to enhance the tones. One must be very careful as these chemicals are very dangerous to handle especially since the positive and negative anodes are electrically charged and can cause an explosion if the fumes are ignited. I would recommend anyone getting involved with chemicals, electroplating, etc., to research extensively before attempting hands-on practice with hazardous and volatile chemicals. I am going to buy a electroplating kit as soon as I can afford it and try my hand on the anodizing and plating skills; hope this helps answer you question.
Joe Delao- Anthony, New Mexico
January 9, 2008
A. I agree with the need for further research, Joe. But I need to note (perhaps not for you, but for readers who may not know what you do) why chromic acid is hard to get. It isn't because it's rare or expensive. Rather, it's available by the pallet load and relatively inexpensive from many sources eager to sell it.
The reason it's hard to get is "product stewardship". Suppliers will not, in general, ship this toxic & carcinogenic chemical which made Erin Brockovich famous to businesses & people who haven't demonstrated responsible stewardship by obtaining mandated hazwoper training, and having required OSHA, EPA, and DOD certification. Carcinogenic toxins like this don't belong in residential basements and garages :-(
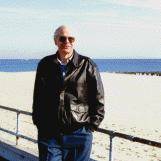
Ted Mooney, P.E.
Striving to live Aloha
(Ted is available for instant or longterm help)
finishing.com - Pine Beach, New Jersey
Q. I'm looking for the best way to refinish Holley carburetors.
They are made of pot metal, mostly zinc. They have an aluminum baseplate as well. The zinc pot metal body was originally finished in a zinc dichromate according to Holley.
I need to find a way to strip the original finish off completely, along with any carbon and fuel deposits, and then brighten the stripped finish up chemically. Then, to apply a fresh zinc dichromate via immersion.
I believe that the original finish on these carbs was probably done using a hexavalent chromium, without zinc plating, and just relying on the zinc in the carb body to be rich enough in zinc to react with the hexavalent chromium.
I have tried using a phosphoric acid product, Alumiprep 33
⇦ on
eBay or
Amazon [affil link] , to clean and activate the zinc diecast body, but it does not seem to strip what's left of the original finish, nor does it leave a bright finish. It does do a nice job of cleaning the aluminum baseplate, but it also darkens the cast aluminum. I was thinking to try muriatic acid 20:1 next.
The original finish I am looking for would be basically yellow zinc, and specifically a yellow or even tan color that likely has some oily-like residues... hues of mostly green and maybe a little red.
So in short, I need to strip, brighten, and activate cast zinc pot metal. I need to strip and brighten cast aluminum. And I need to yellow dichromate the activated zinc pot metal.
Any advice would be greatly appreciated. Google has not really been beneficial thus far!
Hobbyist - Ocala, Florida, USA
June 13, 2013
A. Hi Steve. We have a good number of threads here about restoring carburetors if you widen your search term to perhaps just "carburetor". But some knowledgable people say the only really practical approach is to have them zinc plated before re-chromating because the pot metal is just too far and variably gone to restore to a consistent look.
You are right in describing the greens and red colors as "oily-like", but oil actually hasn't much to do with it. Those are diffraction colors similar to the rainbow colors of a puddle with a drop of oil on it. There is nothing red or green in the process, it's just a prism-like effect from the varying thicknesses of the deposit. Good luck.
Regards,
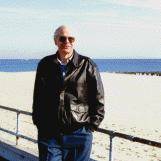
Ted Mooney, P.E.
Striving to live Aloha
(Ted is available for instant or longterm help)
finishing.com - Pine Beach, New Jersey
Carburetor cleaning and refinishing has been a perennial subject. Please see also --
• Topic 0338 "Zinc plating & chromating of Carburetors"
• Topic 16200 "Zinc plate carburetors & diecastings vs. chromating"
• Topic 33779 "Clean and brighten carburetor bodies"
• Topic 35697 "Carburetor re-plating / re-coloring"
• Topic 37255 "Restoring the yellow dichromate finish on automobile carburetors"

Q, A, or Comment on THIS thread -or- Start a NEW Thread