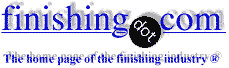
-----
Hot-Dip Galvanizing Kettles: how to build or where to buy
Quickstart:
The central step in hot-dip galvanizing is immersing the work into a kettle of molten zinc. Kettles can be ceramic, but if metal they must be of special grades. These Q&A's also cover clad sheet construction, cast iron, etc.
Q. Very interesting information and experiences in this thread and topic 56390. I have a question regarding the use of clad steel sheet to make the galvanizing kettle. I mean a steel/stainless clad material (35/9 mm each layer). Has anyone dealt with it? What are the drawbacks and advantages of this material against low Si steel? Thanks a lot.
Walter EgliScientist - La Plata / Buenos Aires
September 22, 2023
A. It is indeed an interesting idea. But a kettle is a wearing item, it slowly dissolves in the zinc. Putting a thinner lining on the inside would require that the lining itself does not also dissolve, otherwise after the lining is dissolved, the lower grade steel behind it would rapidly deplete.
So the question really is what rate does some other alloy such as "stainless" dissolve. You mentioned a family of steels with widely variable chemistry. The more common forms of Stainless, 316, 304 etc would not be suitable, their rate of dissolving is slightly slower than low Si carbon steel, but not that much. Someone might know about special grades such as duplex, where the Fe content is low or nil. That might be the area to look at.
Cost is always a consideration too. I could imagine a duplex steel kettle being very expensive.
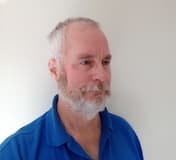
Geoff Crowley, galvanizing consultant
Crithwood Ltd.

Bathgate, Scotland, UK
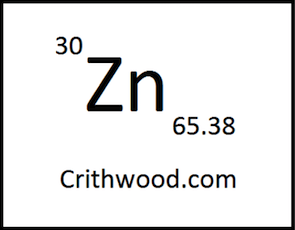
Thank you very much Geoff!!
I think your comments are very reasonable and I agree with you. Probably some other more inert coatings over the low C and Si steel would be better alternatives.
Thanks again for your valuable suggestions.
Sincerely.
- La Plata/Buenos Aires/Argentina
Q. Hi,
Recently, one of my customers requires the maximum carbon content of 0.07% and the maximum silicon content of 0.02% in the zinc kettle steel plate, but this is higher than the domestic standard carbon content of 0.1% and silicon content of 0.03%. How will the content of these two elements affect the performance and life of the zinc pot during use? Thank you!
- SHANGHAI, CHINA
May 19, 2025
Q. Hello,
I am from China, and one of my customers requires the maximum carbon content of 0.07% and the maximum silicon content of 0.02% in the zinc kettle steel plate, but this is higher than the domestic standard carbon content of 0.1% and silicon content of 0.03%. How will the content of these two elements affect the performance and life of the zinc pot during use? Thank you!
- TIANJIN, CHINA
May 19, 2025
Zac,
I wonder if your customer has asked the same question of 2 suppliers and you both posted your question here...
Your customer clearly understands that the correct steel for making kettles is very important. The most important elements are Si and P. Si should be as low as possible, also P. C is less important, but 0.1 might be OK. In China the grade that is commonly used is XG08.
The effect of higher Si% is rapid dissolving of the kettle in the zinc, and so very short life of the kettle. That means more frequent changing of the kettle and all the very high costs associated with that.
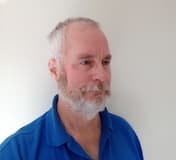
Geoff Crowley, galvanizing consultant
Crithwood Ltd.

Bathgate, Scotland, UK
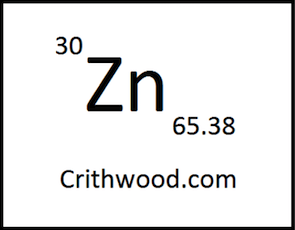
![]() |
Geoff, I went back and checked to better understand the duplication. Both postings are from the same IP address, which is neither in Shanghai nor Tianjin :-(
It was an instant success because, unlike the countless other 'Shop Problems' columns in nearly every technical magazine of the time, we opted for the camaraderie and human interest of people posting with their real names, real locations, and real situations. |
⇩ Related postings, oldest first ⇩
Q. I would like to get access to a design manual (regardless of date) for the construction of a hot-dip galvanizing kettle. I would like to build a very small one (1 cu. ft.). I know it will be expensive. Please help.
Thanks,
Al Henderson- Tallapoosa, Georgia
2002
Q. We have a hot dip galvanizing workshop but kettle is from ceramic for high temperature. We are going to establish a metal kettle of about 3,20 m long, 1,50 m deep and .80 m wide. If you received any information from somebody kindly share it with us or we can share our information too.
Mansour Mansouri- Esfahan, Iran
2003
Multiple threads merged: please forgive chronology errors and repetition 🙂
Q. Is there a standard for chemical composition of a galvanizing kettle material? What is a typical chemical composition of steel used for manufacturing galvanizing kettle?
Erhan Ulvan- Mississauga, Ontario, Canada
2005
A. In the United States it called Flange and Firebox quality steel. It basically is a very low carbon, very low silicon steel plate. Rods for welding it should also be low in C and Si.
Guillermo MarrufoMonterrey, NL, Mexico
Can we use a cast iron galvanizing pot?
Q. We manufacture galvanized steel sheet (both plain & corrugated). Presently, our zinc melting pot is fabricated out of steel plates.But we don't get good life of melting pot, besides its cost. Can we use Cast iron melting pot? What would be other problems with CI melting pot?
P.R.DharGalvanized Steel Sheet - Kolkata, WB, India
2006
A. Sir,
Cast iron is NOT a suitable material to make a galvanizing kettle. In the "old days" the common material was fire box steel. Some years ago "Max Ten" was specified which means the alloying agents in the steel would add up to no more than 0.10%. Today modern kettle makers know what can and cannot be used to make a galvanizing kettle. Certainly silicon, aluminum, and phosphorus contents in the steel must be VERY LOW. Also one MUST use the correct welding rod or else the welds will be "eaten up" by the zinc. In addition only the side walls can be heated (NEVER THE BOTTOM). Also a horizontal stripe 6 inches high at the top of the walls and a horizontal stripe 12 inches at the bottom of the kettle are insulated and (NEVER HEATED). The maximum heat throughput through the walls is 10,000 BTU/sq.ft. on the heat zone of the side walls. My article about a year ago in Metal Finishing (the magazine) would help you. A proper kettle with a proper furnace can have a lifetime of 10 years or more even with high production. A kettle depth to width ratio (e.g. d/w) should be 2 or greater.
Regards,
Galvanizing Consultant - Hot Springs, South Dakota, USA
A. Use a special alloy or a ceramic bath.
Wilfred SprangTHE NETHERLANDS
Chemical composition of galvanizing kettle
Q. Dear sir,
Please let me now the chemical composition of steel used in zinc kettle and also let me know if this composition varies for different size of zinc tank.
Since I am working for a galvanizing Company and we are starting a new plant for which I need the following detail.
Plant In Charge - United Arab of Emirates
2007
A. Dear Sir:
About 35 years ago kettle makers used "max ten" which means that the kettle "steel" was nearly pure iron with the combined alloying agents adding up to less than 0.10%. Armco made "steel" (iron) of this type. Today I do not think this type steel is available. Another term that I have heard is "boiler plate steel."
Today there are two kettle makers that likely make most of the galvanizing kettles. One is in the USA and the other is in Germany. These kettles now usually have 2 inch thick walls (years ago they were 1 inch thick). The weld rod and welding methods are quite specialized. I recommend that you purchase rather than make a kettle. With a proper kettle and proper furnace, the kettle can last 10 or more years. A poor kettle and poor furnace can give a kettle life of only a few months.
In the journal Metal Finishing you can get my article on kettle furnace design though interlibrary loan (xerox copy) from most large libraries. This article details the most efficient system which is end-firing with high velocity burners. Galvanizing kettles and galvanizing kettle furnaces are NOT do-it-yourself projects.
Regards,
Galvanizing Consultant - Hot Springs, South Dakota, USA
A. The most critical element in the steel for kettles is Silicon.
This needs to be at or close to zero.
Silicon is used extensively in steelmaking to de-oxidize the steel while molten and in casting processes. (The slabs cast in continuous casting plants are later rolled to plate.)
Alternative de-oxidants are available for this special grade of plate.
S and P are also important.
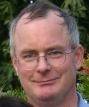
Geoff Crowley
Crithwood Ltd.
Westfield, Scotland, UK
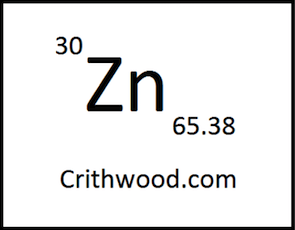
for Engineers, Shops, Specifiers
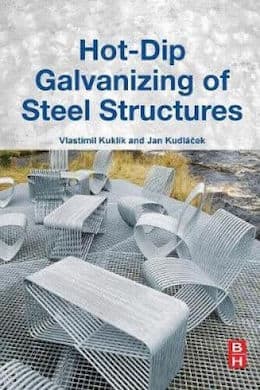
avail from eBay, AbeBooks, or Amazon
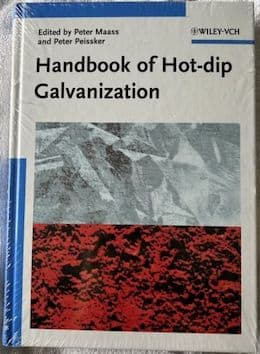
avail from eBay, AbeBooks, or Amazon
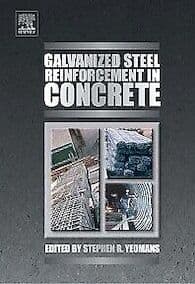
avail from eBay, AbeBooks, or Amazon
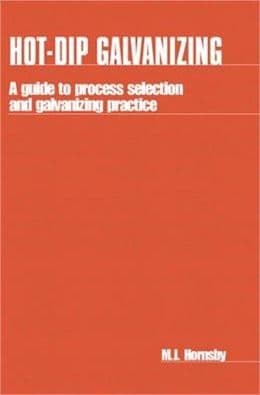
avail from eBay, AbeBooks, or Amazon
avail from Amazon
"User's Guide to Hot Dip Galvanizing for Corrosion Protection in Atmospheric Service" by NACE (1997 only rarely avail.)
avail from AbeBooks, or Amazon
(as an Amazon Associate & eBay Partner, we earn from qualifying purchases)
Q. Looking to install a hot dip galvanizing line, have great potential customers but little know-how on the operation.
Any feedback would be greatly appreciated.
- San Diego, California, USA
March 6, 2012
A. Sir:
Obtain and read the two books: Hot Dip Galvanizing by Heinz Bablik and Handbook of Hot-Dip Galvanization ⇨
by Peter Maas.
Visit galvanizing plants including San Diego Galvanizing and LA Galvanizing.
California is an environmentally tough state to have a galvanizing plant. Check the California Proposition 65 list to better understand the regulations, especially with regard to lead, nickel, and hex chrome.
Regards,
Galvanizing Consultant - Hot Springs, South Dakota, USA
Q. Kindly suggest the specification for melting zinc for hot dip galvanising; we want to make a tank nearly 5.5 meters long and 0.50 meters depth, please suggest the width.
Can we use normal mild steel plates? Also please suggest the thickness of the plates used, welding rod grades.
Can you guide us in the process for fabrication of such tank?
Please reply at your earliest.
Regards
- Indore, (M.P.), India
April 9, 2013
A. Hi Asit. Welcome! We appended your inquiry to a thread which answers some of your questions, but it's a tall order to ask for complete instructions for safely designing and fabricating a galvanizing tank. I don't think it's going to happen for free in a public forum.
Good luck, but if you don't have all the info you need quickly enough, please see the ads for galvanizing consultants at the bottom of the page.
Regards,
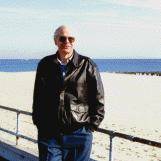
Ted Mooney, P.E.
Striving to live Aloha
(Ted can offer longterm or instant help)
finishing.com - Pine Beach, New Jersey
A. You should not attempt to make a galvanizing tank yourself if you cannot answer these questions.
Your depth of 0.5 m seems far too small. What could you use such a tank for?
At length 5.5 m, more typical dimensions would be 1.2 m wide and 2-4 m deep. Material will be very low Si steel, a special steel not readily available, and made especially for this purpose of galvanizing tanks. Typically its 50 mm thick. Special welding electrodes are required, and special techniques for welding.
There are 3-4 suppliers worldwide who supply long lasting kettles, but the furnace is equally important for long life.
You might expect 10 years or more from a well made kettle of the right material.
You might expect a few months from a homemade one.
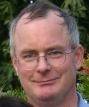
Geoff Crowley
Crithwood Ltd.
Westfield, Scotland, UK
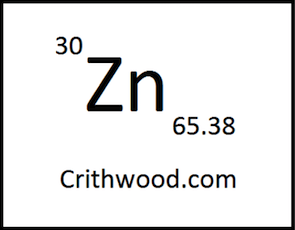
A. Hi, Asit.
Its better to define first size of your materials which are going to be galvanize and required production per day or per shift.
Based on same you have to select the size of your Galvanizing kettle.
Gunatit Builders

Manjalpur, Vadodara, Gujarat
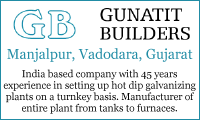
MIG vs. TIG welding for galvanizing kettle? What stick or wire?
Q. Hi Everyone
For welding a Galvanizing pot, fabricated using a DSQ plate. Is it better to use MIG welding or TIG welding. And what is the recommended grade of stick or wire to be used?
Thanks
Kanvar
- New Delhi, India
May 24, 2013
A. Dear Friend
The Welding Electrode must be of same material as Plates. I recommend 45 S, D&H electrodes for DSQ steel.
- Sana'a, Yemen
Q. I need help. I want to make galvanizing kettle. I need help how to make and how it is heated? Thanks.
Ruphert connock- cebu philippines
November 16, 2014
A. Dear Ruphert Connok.
It's better to hire a consultant and supplier who can guide you how to start Galvanizing plant. It will be more advisable then doing it yourself.
Thanks.
Gunatit Builders

Manjalpur, Vadodara, Gujarat
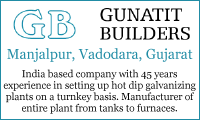
A. Not a good idea to build your own kettle for galvanizing if you have to ask how to do it.
If you want it to last any time, then buy one from a reputable supplier. There are several, even one not so far from you.
Homemade might last 6 months. Bought one 10-14 years.
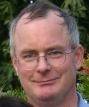
Geoff Crowley
Crithwood Ltd.
Westfield, Scotland, UK
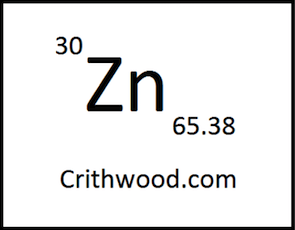
Q. What's the grade and specification for galvanising bath tank.
Regards,
- Hyderabad, telangana, India
August 29, 2015
Hi cousin Rama. That question was already answered in quite deep detail. Please try to request clarification rather than starting over. Thanks!
Regards,
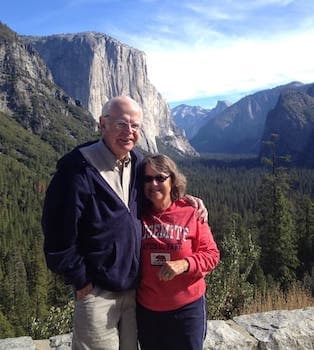
Ted Mooney, P.E. RET
Striving to live Aloha
(Ted can offer longterm or instant help)
finishing.com - Pine Beach, New Jersey
A. Dear MR. Rama Rao Ch.
for Galvanizing Bath , in India, people use DSQ Plate (dead soft Quality).
Gunatit Builders

Manjalpur, Vadodara, Gujarat
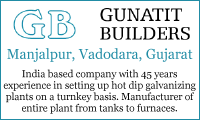
Hot-dip kettle material for Zn-Al-Mg coating
Q. Hi,
We want to design a kettle for coating. Our alloy elements are zinc, aluminum and magnesium. And bath temperature 450 °C-650 °C. We are thinking to use stainless steel (310,316). Is stainless steel suitable for experiment. We will use the bath for one month. Our alloy should contact steel, not brick.
I must choose kettle material. Which material is suitable? Also, the material that we choose should not react with zinc, aluminum and magnesium.
Could you help me, please ?
- Turkey
September 22, 2015
? Hi Teslime. We appended your inquiry to one of several threads here on galvanizing tank construction. I'm reading between the lines that you are talking about a tiny kettle for a short-term experiment, but if you can give us a feel for its size it might be helpful.
Regards,
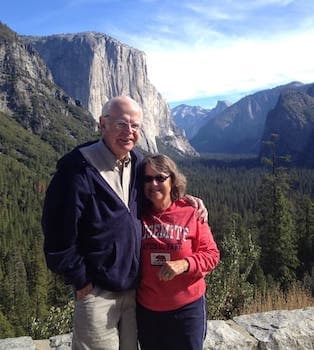
Ted Mooney, P.E. RET
Striving to live Aloha
(Ted can offer longterm or instant help)
finishing.com - Pine Beach, New Jersey
Q. I am building a small kettle and I understand the pitfalls of not having it on full time. I was wondering if I could coat the walls of the kettle with a ceramic coating would that neutralize the erosion of the walls every-time I heated up and cooled down the kettle. The kettle's walls are 1.500" thick. Thanks Matt
Matthew s Willis- Mesa, Arizona, United States
November 4, 2015
Q. I request help to answer the below,
1) What is the best-used Steel Grade for a Galvanizing Kettle? BS 5258, SAE 1006 or some other? Saying only very low Carbon or Silicon contents is an open sentence?
2)What is Grade of Welding Electrodes for best welding of Kettle?
3) Is there any brief procedure having important control points to weld Kettle?
4) What minimum Qualification /experience required for a Kettle Welder?
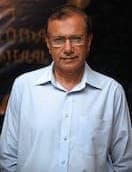
Mukhtar Ahmad
pvd process engineer
- Lahore, Pakistan
December 16, 2015
A. Several steel manufacturers make a special steel for this application. It's a low carbon mild steel, but with ultra low Si - almost zero. I'm not sure if there's a grade name.
To make a kettle out of plain grades of steel would be to ensure a very short life for the kettle.
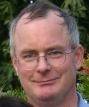
Geoff Crowley
Crithwood Ltd.
Westfield, Scotland, UK
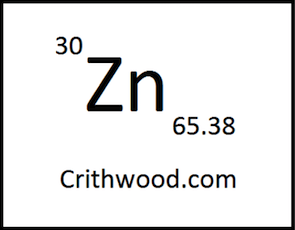
A. Dear Sir.
It's better to purchase Kettle from Reputed manufacturer as they have experience in manufacturing kettles.
Steel generally used to manufacture Kettle should be low carbon, low silicon, with same property for welding electrodes.
Gunatit Builders

Manjalpur, Vadodara, Gujarat
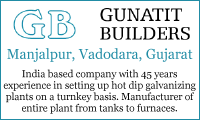
Q. What about the A514B -- is that good for a zinc kettle?
The main problem that I have is the way to manufacture this kettle.
Recently, we had problems with last kettle ... it was made of steel A36 :(
Now I have a question for Dr. Thomas H. Cook:
Why must the kettle have a horizontal stripe 6 inches high at the top of the walls and a horizontal stripe 12 inches at the bottom of the kettle are insulated and (NEVER HEATED)?
Please help!!
- Torreon, Coahuila. mexico
January 29, 2016
A. Dear Juan De Lira
As per specification of A 36 grade steel, Silicon content is much more higher then allowable to fabricate Galvanizing Kettle.
Galvanizers prefer to have silicon content Trace or maximum 0.03 % for better life of kettle.
Gunatit Builders

Manjalpur, Vadodara, Gujarat
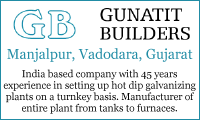
Q. Hello
I want to make hot dip galvanization investment but I'm in a dilemma whether do it in metallic or ceramic material?
Please help me with some of your experienced opinion?
- Durres Albania
February 24, 2016
A. Dear Aleksandro Bardhi,
Selection of Metallic or Ceramic bath mostly based on what kind of materials you would like to Galvanize.
Generally for Fasteners, threaded items peoples are going with Ceramic bath with higher temperature otherwise for structure and bigger job, better to go with Metallic bath.
Gunatit Builders

Manjalpur, Vadodara, Gujarat
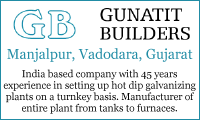
Q. I have a large location and permission to set up a hot dip galvanising plant. The primary use would be for galvanising lampposts (7 meters to 9 meters) and arms (1 meter to 3 meters). I don't expect to galvanise more than 300 per month. I want the most cost effective and fastest method. Are you able to advise me? Any information would be greatly appreciated. Any details for consultants or distributors.
Abaz Lika- Monterrey, Mexico
April 22, 2016
Ed. note: This RFQ is outdated, but technical replies are welcome, and readers are encouraged to post their own RFQs. But no public commercial suggestions please ( huh? why?).
Ed. note: Hi Abaz. The banner near the top of the page lists such advertisers; we can't suggest brands/sourcing within the forum ( huh? why?) -- it leads to boundless spam, hostility, and other problems.
Q. What are the basic reasons of deterioration in galvanizing pot or formation cavity at both side of kettle?
sai misser- Simra, Nepal
April 25, 2016
A. Dear Sai.
Basic reason of deterioration in Galvanizing pot are
1 ) uneven heating
2 ) furnace design.
3 ) Deposition of Hard zinc (Dross) inside zinc kettle.
4 ) Quality of Pot materials.
Gunatit Builders

Manjalpur, Vadodara, Gujarat
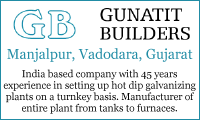
A. The best material for kettles is "CLASS A DSQ (Dead Soft Quality)" and "GP2"
Warm Regards,
- Mumbai, India
Q. Dears,
Our zinc kettle got a puncture within 2 years of service life; now we are in process to find the puncture area. Is there any chance to repair the kettle?
June 18, 2016
- Dubai, United Arab Emirates
Q. Hi,
what would you recommend to prevent a zinc bath from leaking? The client has experienced leaks through bad welds (problem corrected) and now a slow leak from erosion/corrosion.
Thanks for your help,
Philippe
- Montreal, Quebec, Canada
August 29, 2016
Q. Dear sir,
Our Zn-Al-Mg kettle size:
length:150 cm width:25 cm depth: 40 cm.
We will not use ceramics in the construction of the kettle material (because size is small). We want to use metal material. But which metal material we should use (316L, Zirconium, titanium, super alloy)?
The alloy(Zn-Al-Mg) will directly contact the kettle material(316L, Zr, Ti...). Over time, metal material may dissolve .
Thank you.
Regards,
- Tarsus, Mersin, Turkey
February 6, 2017
Q. Are there other credible Galvanizing Kettle Manufacturers besides [name deleted by editor ( huh? why?)]?
Bob Hendricks- Fort Worth, Texas, USA
June 30, 2017
Hi Bob. Apologies but we've learned from 25+ years of this forum that suggesting brands & sourcing questions on a no-registration-required website is a huge mistake (why?)
We hope you'll start by contacting Western Technologies [a finishing.com supporting advertiser] and Gunatit Builders [a finishing.com supporting advertiser] who are making this forum possible for you, before using google for other possibilities.
Regards,
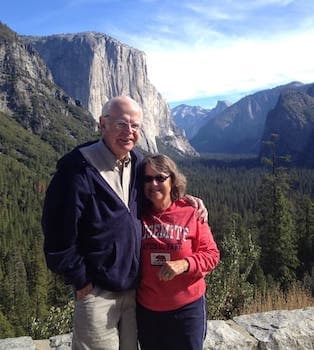
Ted Mooney, P.E. RET
Striving to live Aloha
(Ted can offer longterm or instant help)
finishing.com - Pine Beach, New Jersey
Q. Great thread, and I would like to post a meta discussion here. I am biased for open source, collaborative development -- and I find the information presented quite good and I have a better feel for hot dip kettles now. At the same time -- it is clear that learning the due diligence on the topic is a longer process. Could you perhaps do a summary article on the topic of kettles -- for the small scale and professional alike? We are still trying to get to the bottom of the question: what is the cost, lifetime, and best practice for = a small scale, non-continuous operation kettle? Small scale means 55 gallon drum size kettle. With open source automation, we'd like to make such an enterprise feasible on a scale smaller than imaginable to date.
Marcin Jakubowskiwww.opensourceecology.org - Kansas City Missouri
February 12, 2021
Ed. note: Don't miss Marcin's TED Talk!
A. Dear Marcin.
According to your subject, it looks like you would like to start small Hot dip Galvanizing plant.
first of all we need to know what kind of materials that you are going to be Galvanize, what would be size of materials and what amount of quantity you would like to produce per day in 8 hrs. shift.
Based on all above , we would suggest you more on size of Kettle and its feasibilities.
Gunatit Builders

Manjalpur, Vadodara, Gujarat
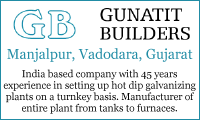
Q. Our size of interest is a vertical pipe 12" in diameter, about 6' tall, for galvanizing columnar-shaped pieces, such as helical pier foundation piles and in-ground steel stakes. We are thinking of putting powdered ceramic insulator material at the bottom, so that the bottom weld is not exposed to molten zinc and therefore the 'kettle' can be made of common, off-the-shelf steel. This would be surrounded by a ceramic heater element of about 20kW, and well insulated. This would be for on-demand galvanizing applications, with automated dipping in all the prep baths so that production galvanizing can be done on a small scale.
marcin jakubowski [returning]www.opensourceecology.org - Kansas City Missouri
? Dear Sir.
You mean to say , you would like to galvanize 12" dia pipe and length of pipe would be 6'-0" long and you would like to dip it vertically.
At a time how many pipes you would like to dip or per day how many pipes you would like to Galvanize.
Based on your answer we will revert back with suitable size for your product.
adv.
You may contact us directly on sales@gunatit.com
Gunatit Builders

Manjalpur, Vadodara, Gujarat
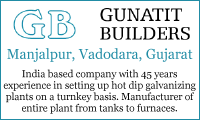
A. Hi Ilesh. No, I think Marcin is proposing that his galvanizing kettle will be a 12" diameter pipe standing about 6' tall, with a bottom plate welded onto it, and the weld protected from the zinc by powdered ceramic insulator material.
I think, however, that 12" diameter pipe is seam-welded rather than cast or extruded. So if the zinc preferentially attacks weld lines, this would still be an issue.
If you get a chance, look at Marcin's fascinating "TED Talk". His interest is in deploying small, simple, inexpensive machines around the world as the building blocks of civilization.
Luck & Regards,
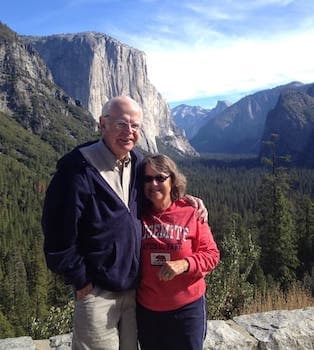
Ted Mooney, P.E. RET
Striving to live Aloha
(Ted can offer longterm or instant help)
finishing.com - Pine Beach, New Jersey
Hi Ilesh,
What Ted Mooney is saying is correct - the vessel itself is the 12" tube. And thanks, Ted, for posting my TED - it's a good overview of our work in 4 minutes.
Marcin
- Kansas City area, Missouri
A. Ted,
At a substantial cost increase you can get tube that has no welds. They are extruded with a mandrel piercing through the billet/ingot.
Q. I would be interested to know if the zinc attacks the welds due to the slightly different chemistry or if the microstructure changes due to the heat of fusion.
Most pipe/tube is made by induction welding which is a forge welding process so there should be minimal if any change to the chemistry of the weld.
If it is due to the different microstructure then normalizing the tube should mitigate the issue at the weld (and if I understand Marcin's intent, it is a relatively easy operation, at least for someone who in going to galvanize things).
- Ballarat, Australia
December 1, 2023
Q. Hi everyone,
I'm delighted I've found this amazing site and I'm sure most of you will be able to help me with my query! The company I work for is considering building a HDG plant. The plans are all drawn up and the kettle has been ordered from Germany etc. However there was one small detail that has been bothering me and that is: What bolts should be used in the construction of the warehouse? Since the beams and pillars can be painted etc. I assume that the same alloy bolt should be used and then painted over in situ? If anyone that has built a galvanising warehouse could answer my query/fear I'd really appreciate it!
James
July 2, 2021
- Penco, Chile
A. Hi James. Although I don't have galvanizing plant design experience, I have 50 years of electroplating plant design experience, and the shop environment and the acids used, and their effects on the structure, are very similar. Although zinc coatings like electroplating and galvanizing are excellent at corrosion prevention in many outdoor environments, they work only because their corrosion products are stable, tight, and relatively non-porous in most atmospheres.
You may remember from science class that zinc is a very active metal, with lab demos like zinc ribbon dissolving almost instantly in hydrochloric acid. Zinc electroplating and even zinc galvanizing are therefore very very poor finishes in acid-laden environments. I suspect that zinc-rich dip-spin or aluminized coatings would be just about as bad. I think that painted steel, or alloy bolts (and stainless steel for any very small fasteners) is the way to go.
Luck & Regards,
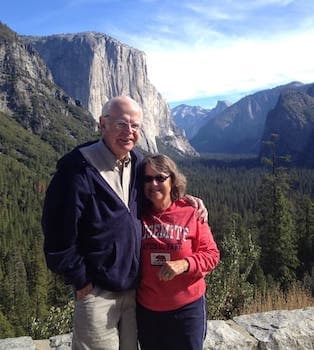
Ted Mooney, P.E. RET
Striving to live Aloha
(Ted can offer longterm or instant help)
finishing.com - Pine Beach, New Jersey
Hi Ted,
thank you so much for replying! I really appreciate it. I'll see what else I can come up with but your confirmation has put my mind at ease. Thanks again and great job being so efficient and knowledgeable.
- Penco, Chile
Q. Is there any risk (for zinc kettle) to galvanizing (sometimes) in low zinc level in the zinc kettle, and what is the best level of galvanizing?
Basel AlnashawatiMechanical Engineer - Dammam , Saudi Arabia
September 26, 2021
A. Hi Basel. Yes there is a risk. Please see Dr. Thomas Cook's comment on this subject on thread 57908
Luck & Regards,
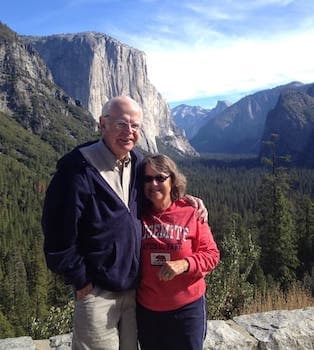
Ted Mooney, P.E. RET
Striving to live Aloha
(Ted can offer longterm or instant help)
finishing.com - Pine Beach, New Jersey
A. Yes there's some risk.
A kettle should not be overheated locally, but requires the temperature of the steel to be as even as possible. If it reaches about 500 °C, then serious erosion of the kettle wall occurs. This is the kettle dissolving in the zinc. Its fastest rate is somewhere around 530 °C, but anything over about 480 °C is too fast. This thinning of the kettle wall keeps going wherever zinc is touching the wall on the inside.
If the zinc level is low, then the top layer of zinc is touching, however low that might be. A furnace is designed to have an unheated area at the top, perhaps about 20 cm from the lip downwards, and it's for this reason. Heat is then only applied to the area that is internally submerged in zinc, so the heat flows into the zinc and doesn't cause the steel to overheat. If you let the level fall too low, below the insulated unheated area, then the steel of the kettle will overheat.
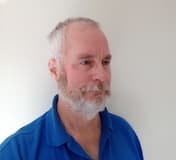
Geoff Crowley, galvanizing consultant
Crithwood Ltd.

Bathgate, Scotland, UK
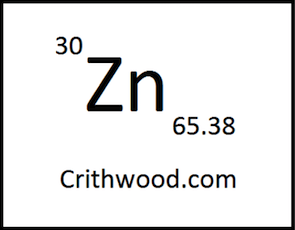
Q, A, or Comment on THIS thread -or- Start a NEW Thread