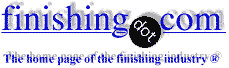
-----
Galvanizing Kettle: Checking for Safe Thickness Loss
Q. Sirs,
I am asking if anyone can tell me the allowable iron loss for a galvanizing kettle before failure (i.e. leak) appears.
Kind regards.
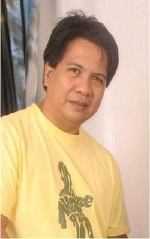
Barlow Campano
galvanizing chemist - Jeddah, KSA
December 23, 2010
First of two simultaneous responses -- December 24, 2010
A. Sir:
You need long and short steel probes to "feel" the side wall erosion on the bottom and top halves of the vertical kettle walls. Be sure to use very thick gloves and a face shield. If the probes get stuck then the cavity is about 3/4 inch or more deep. Next you need a long probe type k thermocouple connected to a fluke digital hand held thermometer. From the opposite kettle side work the probe into any deep cavity and record the temperature. An "active" cavity will be about 25 F hotter than the rest of the kettle. If you find an active cavity then check the burner adjacent to this cavity for dirt, or off center placement. The most likely places for an active cavity is around the thermocouples, just under the air/zinc interface, and at the zinc/dross interface. With proper kettle furnace design and maintenance the life of a kettle can easily be 10 years and my goal now is 20+ years.
In Europe and the USA there is a large machine that "maps" kettle walls (with molten zinc still in it). You can see it operate on youtube.
Regards,
Galvanizing Consultant - Hot Springs, South Dakota, USA
A. 3 to 4 MM per year, provided heating of Zinc Kettle is normal.
Umesh Dalela- Bhuj, Gujrat, India
Second of two simultaneous responses -- December 26, 2010
A. Many kettle start at 50 mm, and many people consider that it's time to change when only 30 mm is left.
But as pointed out above, local "holes" - cavities- could occur.
Its generally over temperature that causes this, and that can be localised for various reasons. Dross buildup can prevent circulation of heat (conduction and thermal convection currents) locally that can overheat the zinc locally, and accelerate the wear.
The most common area for thin spots is near the burners. If radiant heat from the flame is allowed to overheat the kettle wall locally then this too causes wear. Some designs use shields to prevent this radiant heat from the flame.
There are reliable ultra-sonic methods now to test thickness with the zinc still molten in-situ. A complete kettle test can be done in a few hours, saving considerable down time for the alternative (pump out). Of course if a major problem is found then a pumpout might still be required.
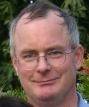
Geoff Crowley
Crithwood Ltd.
Westfield, Scotland, UK
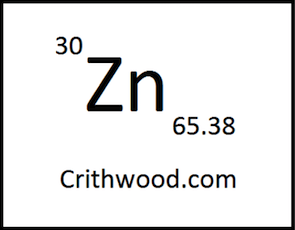
December 29, 2010
A. As a manufacturer of galvanizing kettles and furnaces, it is my view that premature kettle cracks, bulging, etc., occur because of faulty welding process filler selection and de-stressing. But kettle puncture due to rapid erosion depends up on two main factors - a)faulty design of the furnace and its uneven temperature distribution and control, b) Steel plate's chemical composition.
Most important factor for long kettle life is even distribution of heat-flow throughout the kettle wall (it is possible 100% in electrical furnaces) in a well designed oil/gas fired galvanizing furnace almost 90% even-ness is achievable. The working temperature band should be strictly controlled in the range of 452 to 458 °C.
Second part is the plate and its 'silicon content, etc.' because a bad plate or even a good plate will only be highly reactive and make rapid erosion when it will surpass the safe temperature band. We have seen - even so called 'Zero silicon (Armco)' steel plates are also very very unsafe in a bad furnace.
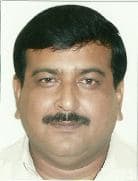
Prosenjit Guha
- Kolkata, West Bengal, India
January 1, 2013
Q. Can you suggest a method to detect badly worn out area in a galvanizing kettle in running condition?
MILIN PATEL- PUNE, India
March 23, 2013
A. Use an on-line ultrasonic thickness test.
There are advertisers on this site who do this.
7m kettle can be checked in about 6 hours.
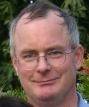
Geoff Crowley
Crithwood Ltd.
Westfield, Scotland, UK
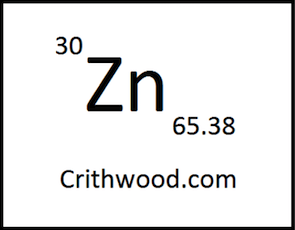
March 25, 2013
A. Sir:
Take a long 5/8 inch diameter steel rod, sharpen like a pencil, bend at right angle at 5 inches from the bottom (sharpened end) and run the sharp point up the kettle walls at 6 inch intervals. If the probe gets stuck while pulling up then the cavity is 3/4 inches deep or deeper. Upon finding a cavity, then measure temperature within the cavity with a type K thermocouple. If the cavity has a temperature 25 degrees F hotter than the rest of the zinc then the cavity is "active" and is likely to burn a hole in the kettle.
Regards,
Galvanizing Consultant - Hot Springs, South Dakota, USA
Zinc Pot/kettle Wall Thickness Measurement
Q. What is the available technique to measure wall thickness for Zinc Pot -kettle- in line.
Mohamed Ali- Cairo, Egypt
September 29, 2015
September 30, 2015
There are two main methods.
1. Pump out the zinc to either moulds to freeze there, or to another hot storage vessel, then cool the kettle and use ultra-sonic testing to check remaining steel thickness.
2. While the kettle is full of molten metal use ultra-sonic probes that are specially designed for high temperature service to probe the wall.
In both cases the dross on the wall must be accounted for.
There are contractors who offer this service, and a typical kettle can be checked hot while on line in about 4-8 hours.
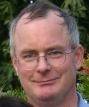
Geoff Crowley
Crithwood Ltd.
Westfield, Scotland, UK
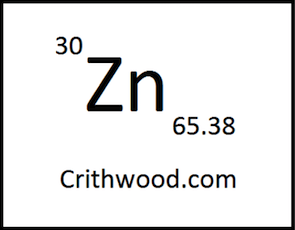

Q, A, or Comment on THIS thread -or- Start a NEW Thread