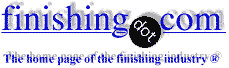
-----
Chrome Plating: sulphate concentration, throwing power, bright range

Q. Good afternoon,
I have a few questions about the throwing power of chrome and the practice of operating at a higher current density for a short period of time, before a lower current density for a longer period of time.
The solution is a hex chrome, 250 g/L chromic acid, 2.5 g/L sulfuric acid bath operating at approx. 42°C. An example jig is of 8.55 dm^2. It would have 30s at 240A (28A/dm^2), and then 2 mins at 30A (3.5A/dm^2).
According to this graph in "Modern Electroplating" [on AbeBooks, eBay, or Amazon affil links] by Frederick A Lowenheim both these current densities should be outside the bright plating range, yet when we do this the items have a good coating.
1- Does this practice have any basis in theory, and if so please could you recommend some further reading?
2- Is it just trial and error until it works?
3- Are the current densities in this graph what we should aim for, given that it appears we are successfully plating outside those rages?
Any help much appreciated,
Will
- Birmingham, UK
February 28, 2022
A. Hi Will
In a conventional bath like you have, current density is interconnected with the bath temperature. Higher temperature will allow much higher current density, but generally the "bright" range is very wide. *By the way, it looks that you operate at little lower temperature than usually mentioned for the conventional bath (120-140 °F)...
In Hard Chrome Training Course from NCMS, they estimate the "bright" range for your temperature approximately 18-43 A/dm2 (so your first number is perfectly within "the range")
If you look at the bottom of this discussion there is an unidentified chart from Humaira Rashid, that starts bright plating for your temperature at approximately 7 A/dm2.
Unfortunately there is no scientific equation (or I'm not aware about it). My feelings - all those diagrams are very approximate. In addition to the temperature, current may be dependent on purity and contamination of the bath. I would recommend to try the Hull Cell
⇦ huh?
. It should give a relatively accurate picture for your specific conditions.
Good luck,
- Winnipeg, Canada
Thank you Leon, that's very helpful
- Birmingham, UK
A. Excellent, thank you Leon!
Will: As a general rule, throwing power does vary with current density so it sounds possible that you might get better throw by operating in two different ranges.
A lot of electroplating is based on scientific kaws like Faraday's Law and Ohm's Law, but a lot is empirical, by which I mean not based on first principles: the exact mechanics of what is going on in the boundary layer is so complicated that we don't calculate it we just chart the results.
Luck & Regards,
Ted Mooney, P.E. RET
Striving to live Aloha
(Ted can offer longterm or instant help)
finishing.com - Pine Beach, New Jersey
![]() |
Q. I want to know this: when I am using something heavy as a cathode (my product to be plated), it's coming out good blue and shiny but when something light is at its place it's all yellow from halfway down. For eg. I am plating on nut and bolts weaving them on copper wire. When I am plating bolts which are heavy it's good but in case of nuts it's like half of nuts on copper wire, upper ones, are good but lower half is not coming out chrome plated. Vashist Pandey- Ludhiana, Punjab, India January 16, 2023 A. Hi Vashist. |
⇩ Related postings, oldest first ⇩
Q. We have been having problems lowering our sulphate concentration in our chrome plating bath. I have analyzed the bath and determined that the concentration is 0.14 oz/gal (I know I hate standard too). We have added a total of 1 3/4 lbs of Barium Carbonate and my analysis still shows no change in sulphate. I KNOW that barium precipitates sulphate rapidly so I don't know what the problem could be. If you have any suggestions please feel free to share them.
Thank you,
- Las Vegas, Nevada
2002
A. Assuming this is a conventional 100:1 bath, why is 0.14 oz/gal too high? It sounds too low.
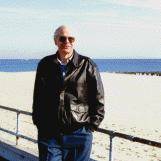
Ted Mooney, P.E.
Striving to live Aloha
(Ted can offer longterm or instant help)
finishing.com - Pine Beach, New Jersey
A. What is the volume of the chrome tank? Are you using the centrifuge method for analysis? Are you having a problem with the deposit, poor throwing power? How many mm of coverage do you have in a 267 ml Hull Cell panel plated at 5 amperes for 3 minutes?


Tom Pullizzi
Falls Township, Pennsylvania
Readers: for an intro to the various catalysts used for chrome plating, please see thread 35184, "FAQ: Chrome Plating Catalysts".
Q. Our tank is 830 gal. our ratio is 224:1. I am getting 55 mm of coverage in the hull cell at 5 amps. I had them add 2000 mls of fluoride catalyst and it seems to have fixed the problem but it is too soon to be sure.
P.S. What is this about a 100:1 ratio. I have heard this a couple times, but on all of the spec sheets that I have seen for chrome tanks it says the ratio should be around 170-230:1? Is this wrong?
Thank you,
- Las Vegas, Nevada
A. I thought that you were using a conventional bath when you said you hated standard, I thought this was what you meant, (without other catalysts like fluoride, 100:1 is correct). With fluoride catalyst in a mixed catalyst bath, the 200:1 ratio for sulphate is usually correct.
55 mm coverage is marginal, I like to see 70 mm. Why would you add fluoride, but try to remove sulphate to cure the same problem? They are both catalysts and too much of each would tend to reduce throwing power. What problem were you trying to solve? I don't know why the barium did not work, filter your sample next time.


Tom Pullizzi
Falls Township, Pennsylvania
A. The precipitation of sulphate with barium is not as quick as you think. Because the solution has a lot of chromium and relatively only a little sulphate, the first precipitate will be of barium chromate and only with time (in lab it will take at least an hour) it will create the barium sulphate. So you cannot add the barium carbonate mix and recheck the result right away.
If you use a centrifuge for the analysis, you MUST filter the solution prior to the analysis (even prior to the first analysis prior to the addition of the barium). The reason for it is that the solution contains lead chromate which might precipitate when the centrifuge is used.
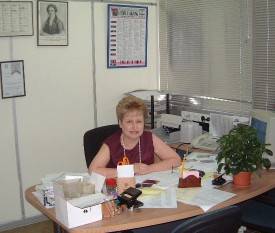

Sara Michaeli
Tel-Aviv-Yafo, Israel
A. Listen to Sara, she has it right. What is your procedure for sulphate analysis? There are a number of things that can go wrong, not filtering your solution is only one. As a rule I give Barium 8 hours to do it's thing, only then will I re-sample.
Steve Delaney- Ontario, Canada
A. Make sure that you stir up the sludge in the bottom of the tank. I use a one foot stainless steel disc, stainless welded to a stainless pipe. Do this every morning of use, and every thousand amp hours, to ensure even solution uniformity, better absorption of sulphate and a true Hull Cell test. Works for me!
Mark Gunn- NSW, Australia
A. Hope,
are you talking about hard chrome or decorative hexavalent chrome? If you have hard chrome, chromic acid-sulphate ratio 100:1; if it is decorative chrome ratio 200:1 ,+/- 5 %. After you add barium, you have to wait at least 12 hrs. because chemical reaction is very slow. If you analyze sulphate very quick you get wrong reading and more confusion.
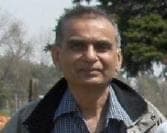
Popatbhai B. Patel
electroplating consultant - Roseville, Michigan
I appreciate and admire Popat's contributions to this site, and I learn a lot from him. But I am not confident that he is right about a 200:1 ratio for a conventional Sergeant bath for decorative chrome plating. I wonder if the bath in question is a mixed-catalyst bath with chromic acid to sulphate at 200:1, but a fluoride catalyst as well?
Luck & Regards,
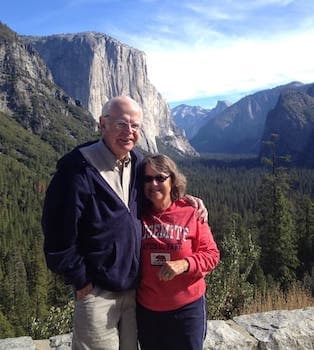
Ted Mooney, P.E. RET
Striving to live Aloha
(Ted can offer longterm or instant help)
finishing.com - Pine Beach, New Jersey
Q. Barium chromate is yellow in colour due to the chromium. Barium chromate precipitates sulphate as a barium sulphate. I want to determine sulphate concentration using barium chromate. But I do not know solubility of barium chromate and how long it will take to precipitate sulphate as a barium sulphate at room temperature?
Patel Rahul PUniversity of Tasmania - Hobart, Tasmania, Australia
2005
A. Hi Rahul. I'm not 100% sure, but I think there is a typo in your question and you mean 'barium carbonate' which is discussed in some detail on this thread. Thread 32838, "Analyze Chrome Plating Bath; Determine sulphates" covers what you want to do in depth (assuming again that you meant barium carbonate).
Luck & Regards,
Ted Mooney, P.E. RET
Striving to live Aloha
(Ted can offer longterm or instant help)
finishing.com - Pine Beach, New Jersey
Q. We are trying to find a technical data sheet or procedure on determination of sulphate in chrome tank (HEEF-25).
Any assistance is appreciated.
Quality Manager - Warsaw, Indiana
August 26, 2008
Q. I want to know how can I increase the throwing power of decorative chrome bath, and how can I eliminate the chrome burning at HCD areas and corners?
Nadeem Shahid- Pakistan
June 12, 2012
A. Hi Nadeem.
Chrome plating has notoriously poor throwing power, and as far as I know there is no way to increase it, although the wrong ratio can decrease it. So get your ratios correct, as described by Sara et al, and check the throwing power as described by Tom with a Hull Cell.
You can decrease burning at corners and HCD areas by equipping your racks with "thieves" or "robbers" that absorb the excess current.
Another alternative, if practical, would be to convert to a proprietary trivalent chrome plating bath for better throwing power. Good luck.
Regards,
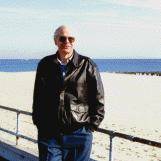
Ted Mooney, P.E.
Striving to live Aloha
(Ted can offer longterm or instant help)
finishing.com - Pine Beach, New Jersey
Q. Please explain what are thieves and robbers that are equipped in the chrome rack to absorb the excess current and purpose is to reduce the burning of chrome at HCD areas.
Nadeem Shahid [returning]Student - Lahore, Punjab, Pakistan
A. Hi Nadeem.
Chrome plating is an electrochemical process whereby current causes chromium to be reduced from hexavalent ions to metal, and the current essentially follows the "path of least resistance". So too much current can flow to corners and exterior edges, causing burning. A thief or robber is a piece of scrap metal that is connected to the cathode (it can be part of the rack) and placed close to those corners and edges to absorb some of the current that is flowing to that area to prevent burning. The thief is later stripped or replaced.
Regards,
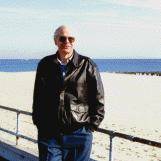
Ted Mooney, P.E.
Striving to live Aloha
(Ted can offer longterm or instant help)
finishing.com - Pine Beach, New Jersey
Q. I want to increase the blueness in chrome plating but I am unable to do so. Please help. Also tell me what ratio should be maintained, I mean what is the ratio of chrome oxide and sulphate ... and how many kinds of sulphate can be used? Please mention their names also.
mohd malik- aligarh,up, India
June 12, 2014
A. Hi cousin Malik. I have never heard of such a thing myself. To my eye, chrome plating from a decorative hexavalent chrome plating bath is always exactly the same color. Maybe a highly experienced chrome plater will disagree with me.
But you haven't told us your own situation, leaving me wondering if, for example, you are trying to plate chrome onto nickel. Because in that case nickel is indeed 'yellowish' and lack of a 'bluish' color means no chrome is being deposited, which might well be the case if the ratio you ask about is wrong.
The formulation of a conventional (Sergeant) hexavalent chromium plating bath is simple: about 28-32 oz./gal of chromic acid, and exactly 1/100th as much sulfate.
Luck and Regards,
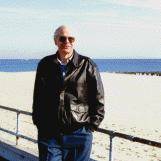
Ted Mooney, P.E.
Striving to live Aloha
(Ted can offer longterm or instant help)
finishing.com - Pine Beach, New Jersey
Q. Hello everyone.
I am facing problem in chrome tank. Recently I prepared the new chrome bath with the ratio of 250 g/ltr chromic acid; the problem is H2SO4 it should be 2.5 g/ltr mistakenly it got 5 g/ltr. To go back to my original value I precipitated the chrome solution with barium carbonate for 12 hrs. Even after 12 hours of waiting the result is a slight change from 5 g/ltr: it's gone down to 4.7 g/ltr
Note tank capacity 915 ltr.
flexible packing industries - HYDERABAD India
August 14, 2018
? Yasseen,
How much barium carbonate did you put into your 915 liters chrome tank to reduce 5 g/l of sulphate to 2.5 g/l?
- Georgetown , Penang , Malaysia
Chromium Plating Catalyst Ratio
Q. Regarding hexavalent chromium bath: We all know that this type of bath needs a catalyst present in order to form a deposit. In its simplest form it is sulfur alone, at typically 100 : 1 ratio with chromium trioxide (and D.I. water). Also typically, the sulfur is introduced into the bath by way of sulfuric acid.
Since sulfuric acid is not 100% sulfur; 1 molar mass of sulfuric acid is 98.1g, of which only 32.1g is sulfur - the rest being hydrogen and oxygen (please correct me if I'm wrong on this).
So, does the 100:1 ratio refer to the sulfur content alone of the sulfuric acid added to the bath, or does it refer to the total mass of the sulfuric acid added.
In the former case the mass of sulfuric added to the bath would have to be close to 33:1 to achieve a 100:1 chromic to sulfur ratio, whereas in the latter case it would just be by mass 100 parts chromic to 1 part sulfuric acid.
Can anyone verify which out of the two it is please - it is a lot easier to add more acid later than try to remove it with barium carbonate or whatever.
Thanks and Regards,
Vehicle restorer as a hobby. - Birmingham, West Midlands, England
September 11, 2018
A. Hi Nigel; it's actually not exactly either. The 100:1 ratio is Chromic acid to sulphate, H2CrO4 to SO4-2. The ratio is important but it's not written in the stars to six digit precision. According to Guffie, people historically used 54 oz/gal of Chromic acid, which made the desired amount of sulphate 0.54 oz, which worked. The weight of the hydrogen is fquite insignificant in the formula for sulfuric acid -- so you wouldn't be far off if you calculated based on H2SO4 instead of SO4-2 ... but you would be way off if you calculated the ratio based on Sulfur.
Regards,
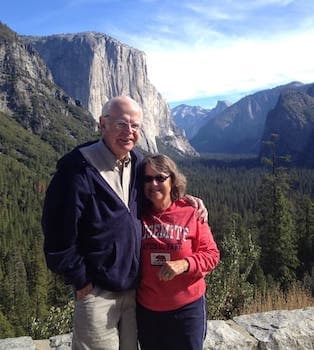
Ted Mooney, P.E. RET
Striving to live Aloha
(Ted can offer longterm or instant help)
finishing.com - Pine Beach, New Jersey
Hello Ted, thanks for verifying the specifics with the catalyst ratio with your reply.
Cheers,
Nigel
- Birmingham, West Midlands, England
September 13, 2018
Q. Hello. Our teacher told us that a dilute bath of CrO3 and H2SO4 will produce hard chromium plating and concentrated bath will produce decorative plating. He said that diluted or concentrated, the acid ratio should be maintained at 100:1 (CrO3: H2SO4). I wanted to know why exactly diluting the bath gives hard coating and concentrated bath gives decorative coating.
I'm sorry if I'm being very vague. And I'm not sure if this has been asked before. I'm having a hard time finding an answer for this.
- Rajshahi, Bangladesh
April 19, 2021
by George Dubpernell"
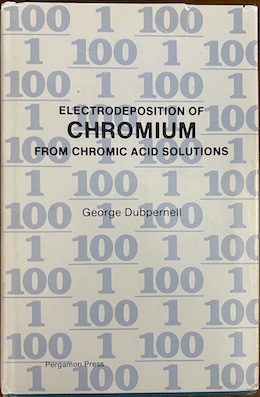
on eBay or Amazon
or AbeBooks
(affil link)
A. Hi Humayra. Your teacher is correct on at least one one claim, but probably either misunderstood or in error on the other...
The conventional "Sergeant" chrome plating bath uses a 100:1 ratio of H2CrO3 to SO4. The precise electrochemical reason is not for most of we mortals to fully understand, although people have won prestigious awards for their efforts to explain it. For us the answer is simply that it doesn't plate if the ratio goes significantly higher or significantly lower.
As an aside though, the Sergeant bath with its H2SO4 catalyst isn't the only type anymore. Some people use fluoride catalysts these days and some use proprietary catalysts reputedly based on methane sulfonic acid. Topic 35184, "Hard chrome plating catalysts" talks in more depth about the various catalysts that can be used in chrome plating baths.
Where I believe your teacher is in error though, if you parphrased him/her correctly, is in the assertion that hard chrome plating uses dilute baths and decorative chrome uses more concentrated ones. To a certain extent the reverse is actually true because some people still advocate highly concentrated baths 48-54 oz/gal of chromic acid for hard chrome plating, although I think most people use 28-32 oz/gal for both. You may be interested in our "Introduction to Chrome Plating".
Luck & Regards,
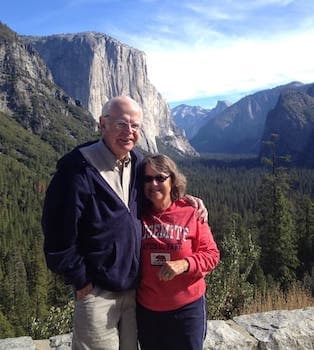
Ted Mooney, P.E. RET
Striving to live Aloha
(Ted can offer longterm or instant help)
finishing.com - Pine Beach, New Jersey
Q. Hello Sir,
Thank you so much for replying. I just finished reading the other post and "Introduction to Chrome Plating". I get that CrO3 and H2SO4 ratio is maintained strictly at 100:1. Fluoride and other baths can be used too as catalysts.
But if we use the 100:1 ratio for both hard and decorative chromium, then why we are getting two different types of coatings? I'm sorry if I'm missing something obvious. As I understand it, decorative plating is done on a nickel electroplated surface and the chrome plating is very thin. And even though the hard chrome plating is called hard, it just thicker than other chrome plating. So is it because we give it more time to develop a thicker coating? I'm coming back with more questions than I started with. But let me clear up how our teacher explained it to us. Being in the pandemic, we couldn't do this experiment in our university. So for now, he only explained this to us on zoom. And he said he did this experiment before the pandemic. He said that for hard chrome plating he used 225g/l CrO3 and 2.25 g/l H2SO4. For decorative coating he used 450 g/l CrO3 and 4.50 g/l H2SO4. He said both the experiment were done for 20 minutes. And he mentioned specifically that the dilute and concentrated baths were the reasons for two types of coatings. Since that's not true, then what really contributes to two different types of coatings? I'm assuming there's little or no effect of time. Is it the effect of temperature and current density then?
Another question I have is that, does the dilute and concentrated baths have different cathode current efficiency? Our teacher showed us a graph. And in the graph the diluted bath had significantly more cathode current efficiency. Sorry for the long read. I feel like I'm missing something really obvious. It'd be really helpful if you cleared it up. Thank you.
Humayra Rashid [returning]- Rajshahi, Bangladesh
A. Hi Humayra. Although people sometimes want the chrome to be as hard as possible, and do things like using different catalysts to accomplish tit, it's actually called "hard chrome" only out of tradition and because it's thick enough to easily measure its hardness.
The difference between decorative chrome and hard chrome is that decorative chrome is always done on top of nickel plating and is always very thin, measured in millionths of an inch, but hard chrome is applied much, much, thicker for wear resistance, usually on hardened steel, although not necessarily.
But the plating times are vastly different! While your teacher may have done an experiment where he plated both for 20 minutes and called one 'decorative chrome' because it was on top of nickel, and called the other 'hard chrome', the plating time is actually a very fundamental difference between the two finishes :-)
Decorative chrome takes as little as 20 seconds and rarely more than 2 minutes. Hard chrome can take hours, sometimes days. Another "Intro" here which you might like to read is "Faraday's Law of Electrolysis for Plating", which explains the dependence of thickness upon plating current and time.
Although things can get interdependent & complicated, there is a chart in Weiner & Walmsley supporting your teacher's chart, that efficiency peaks at a concentration of 250 g/l (33.5 oz./gal) and decreases with increasing concentration.
Luck & Regards,
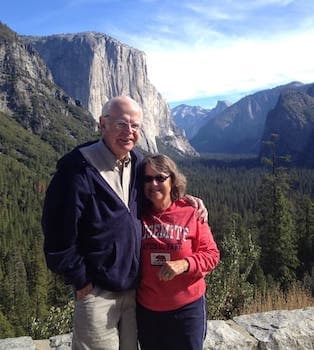
Ted Mooney, P.E. RET
Striving to live Aloha
(Ted can offer longterm or instant help)
finishing.com - Pine Beach, New Jersey
Thank you, sir. I'll spend more time studying the topic.
- Rajshahi, Bangladesh
Nadcap Chemical Processing Auditor - PRI, traveling
Process Engineer / Chemist - Denver Metal Finishing, Colorado
Q, A, or Comment on THIS thread -or- Start a NEW Thread