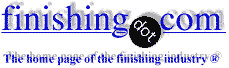
-----
Hard chrome plating catalysts
Quickstart:
This thread discusses the "catalysts" used in hard chrome plating [what is hard chrome plating?]. The curator offers this intro to set the stage so readers aren't quickly lost as the Q&A's bounce from one catalyst issue to another. Please use the dialog to correct or challenge misstatements found here as well as in the dialog.
by Clarence H. Peger
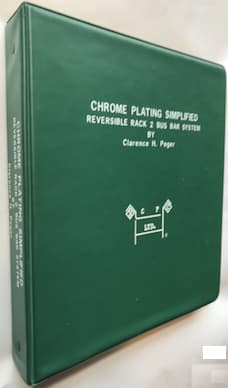
(copies are avail. in select libraries)
Very rarely available from
eBay or Amazon
or AbeBooks
(affil link)
Chrome plating is done in a strong solution [about 28 to 54 oz./gal] of chromic acid H2CrO4 [CrO3-2], but chromium metal will not plate without a small controlled amount of other ions in the solution [the catalyst]. Three general classes of catalysts were developed over the years.
1). Sulfuric acid catalyst -- The first practical chrome plating bath was 100 parts chromic acid to 1 part sulfuric acid, and is sometimes called the "conventional" or "Sergeant" chrome plating bath. It's still widely used, but works poorly if at all if the 100:1 "ratio" is off by even a small amount. The ratio is controlled by periodic additions of sulfuric acid; in the event of too much sulphate, additions of barium carbonate precipitate the excess sulphate. The "efficiency" of this plating bath is poor, maybe 10-12% [only 10-12% of the applied electricity goes towards depositing chrome, the rest is wasted in electrolyzing the water in the bath into hydrogen and oxygen gas].
2). Fluoride (SRHS) catalyst -- A second catalyst system was developed to address these limitations: the fluoride or "mixed catalyst" bath, which adds fluoride salts to the mix. These salts can be made only slightly soluble, so they precipitate and settle to the bottom of the tank. As the catalyst is consumed, these salts (at least in theory) redissolve to maintain the correct catalyst ratio, making the plating bath "self regulating". The bath is also claimed to offer higher efficiency. One vendor (M&T Chemicals, now Atotech) used the tradename SRHS (self-regulating high speed) and promoted the process with the chrome-poem, "Chemical Balance".
But fluoride baths etch the substrate when platers apply reverse current in the chromium bath to activate the surface, which then necessitated that a second fluoride-free chromic acid bath be on hand for the reverse current step.
3). MSA (HEEF-25) catalyst -- A third type of catalyst was developed to address perceived limitations in the earlier catalysts. It was patented and proprietary, and marketed by Atotech as "HEEF-25" (high speed, etch-free, 25% efficiency). This intro names Atotech products only because the editor worked for that company and is more familiar with them; other vendors had similar offerings. It is now well known that the catalyst was or was derived from MSA (methane sulfonic acid). We mention MSA to keep the discussion technical (sulfuric acid vs. fluoride salts vs. MSA), not to suggest that simply adding MSA will give you a workable plating solution.
There is a dissenting school of thought which prefers the conventional sulfuric acid catalysts, with carefully designed anodes for very close anode to cathode spacing and higher operating temperatures, which they feel results in high efficiency and the best overall approach. Clarence Peger (dec.) was the best known proponent of that approach with his "Reversible Rack" system. Clarence conducted training sessions on this approach, and many companies (including finishing.com) have the loose-leaf books from those courses which describe the details of the reversible rack approach.
Q. Does a hard chrome bath need stirring while plating or isn't it allowed? Does the stirring have effects on the plated layer?
Andy Daan- Germany
1999
A. Most hard chrome plating solutions should be agitated during the plating process. Dried compressed air is the best method to introduce agitation. Several benefits are to be had including maintaining electroplating solution temperature. Regards.
Stephen C. Ward- Canada
A. Hi Andy. Suppose you like your coffee very very sweet. You might put 3 spoonfuls of sugar into it. If you were to put in still more, say 6 spoonfuls, the coffee can't dissolve it all, the balance will sink to the bottom of your cup as a syrupy sludge. But if you now drink some of your coffee, and top up your cup, your refill will be just as sweet as the original without any further addition of sugar because that syrup at the bottom will go into solution to maintain the sweetness at the maximum sugar concentration that the coffee can sustain.
Traditional chrome-sulfuric plating baths required a 100 to 1 ratio of chromic acid to sulfuric acid, and some people felt that it was laborious to maintain this ratio. So they invented a "self-regulating" fluoride bath where excess catalyst would settle at the bottom of the tank, like the syrup at the bottom of too-sweet coffee.
As the catalyst is consumed, these precipitated salts are supposed to go back into solution to keep the catalyst in balance. Assuming that you are using self-regulating catalysts, periodic stirring is mandatory (Tom Pullizzi reminded me that the solubility of these regulating salts is temperature dependent and, since the bottom of the tank can get cold, periodic stirring is essential to get them back into solution).
Stephen is right about "most hard chrome solutions", but if using partially soluble fluoride catalysts, I think you must let them settle so they don't co-deposit. Regards,
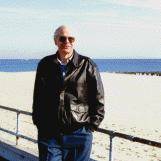
Ted Mooney, P.E.
Striving to live Aloha
(Ted is available for instant or longterm help)
finishing.com - Pine Beach, New Jersey
A. I like Ted's description about coffee. When you use a SRHS bath you must stir the bath for 5 minutes before you start plating. I have seen that when using stirring and I plated hard chromium inside a diameter, the deposit goes faster with using a stirring. It is approximately 23% faster deposit rate. Because the content of trivalent chrome never builds up in the inside diameter you get a change of solution there. But when you plate an outside the chromium deposit goes first to the outstanding portion of the part, because the diffusion layer will be less.
Regards,
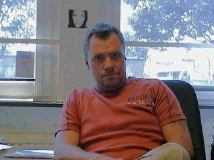
Anders Sundman
4th Generation Surface Engineering
Consultant - Arvika,
Sweden
A. Dear All,
I think it's important to know that stirring during the electroplating may effect the layer in two ways:
1- It can effect the roughness of the layer, allowing Fe, Cu and some metal particles into the layer. Generally, there are some of them such settled in the bottom of bath.
2- It may effect the brightness of layer and lose it.
It happens more on the old solution based on sulfuric acid.
It can be hard to prevent of these problems, dependent on the condition of your solution.
Regards,
- Karaj , Iran
Q. Is it true that vigorous stirring affects the work of the fume suppressant used to reduce the surface tension?
Chris Sigalas- Athens, Greece
October 16, 2008
Q. Hello,
Thank you about your useful information. I'm looking for preparing a catalyst to increase the cathode efficiency for chrome plating up to 29% taking in mind the safety factor for solution composition and anodes. So I need some advice for this purpose.
Thank you again
Best Regards
- Dammam, Saudi Arabia
2005
A. Hello, Mr. Nabeel. If you are a skilled chemical formulator, it is possible that some or all of the patents on MSA-based 25 percent efficiency chrome plating catalysts have expired, so you may wish to study them and consult a patent attorney re. their status. If you are not a skilled chemical formulator, you can buy the chrome plating solution rather than trying to mix it yourself. 25 percent efficiency chrome plating processes are available from most knowledgable suppliers. Best of luck.
But I don't know quite how to respond to "taking into account the safety factor" because the subject of chemical safety fills entire library shelves, so instructing a stranger of unknown skill level on the subject over the internet doesn t sound realistic. Good luck.
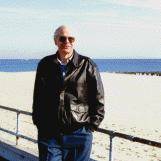
Ted Mooney, P.E.
Striving to live Aloha
(Ted is available for instant or longterm help)
finishing.com - Pine Beach, New Jersey
RFQ: Dear Sir,
We need hard chrome proprietary additives or catalyst which does not cause etching of anode and which makes the hard chrome bath run on 35% efficiency thus saving energy cost.We are looking for such a product but have not found any product which does not cause etching of anode and have high efficiency. Due to etching of anode the contamination level in the bath increases making the bath unstable.
plating shop - Delhi, Delhi, India
2006
Ed. note: This RFQ is outdated, but technical replies are welcome, and readers are encouraged to post their own RFQs. But no public commercial suggestions please ( huh? why?).
Q. Dear Sir,
I have the following questions and I will highly appreciate if you give answer to all of them.
I wanted to know if the patent of Atotech for HEEF-25 (High Efficiency Etch-Free) has expired or the patent is still continuing (i.e., still in the duration of patent)?
Now if the patent is still in continuation than how are other companies selling high speed or high efficiency products?
Which are the other companies that have patented product for hard chrome plating for any hard chrome system or additive or catalyst. What is the name of that product?
What is the maximum efficiency that can be achieved by any hard chrome process or additive or catalyst?
Regards,
- Rajkot ,Gujarat, India
2006
A. If I'm informed correctly, the Patent is still on. However this patent is divided between 3 suppliers. Depending on your global position you can find the following suppliers and products:
Atotech, HEEF-25
Enthone, ANKOR 1127
Canning, MACH?
Other additives to give higher efficiency are mostly fluoride based.
Maximum efficiency is, of course, depending on your maximum current density. Under optimal conditions you may reach 24,5% at 50 Adm2 but that can go up to 27,5% at 90 Adm2.
- Maasbommel, Netherlands
Q. Hi there,
Switching from a mixed-catalyst hard chrome bath to a HEEF bath: yea or nay?
Have any of you switched from a mixed-catalyst (i.e. sulphate + fluoride) hard chrome plating bath to a high-efficiency, etch-free (HEEF) formulation? If so, have you found the HEEF bath more cost-effective -- and how much so? I've tried getting costing info from Atotech (main distributor around here), but I'm running into the catch-22 position where they don't want to give a quote (or even ballpark estimate) until the company I work for decides to adopt the system, and understandably, my company isn't prepared to make the switch until they have a good idea of the costs involved. While I understand that info is available re: HEEF increases current density by x% and reduces plating time by y%, etc., I'm more interested in hearing how these savings on paper have translated into reality.
Thanks for any input!
environmental engineer - Guelph, Ontario, Canada
2007
A. It is not quite that easy as it depends how each one is used: temperatures, current density, anode /cathode spacing, drag out, etc.
I have used the HEEF-25 bath but not the mixed catalyst as I could not risk the etching problem.
I think that the greatest savings is made by switching to a mesh conforming anode with a close spacing. This allows you to use a higher amperage; so it plates faster. It increases the efficiency of the bath because less is lost to heat. You still have a huge loss to hydrogen gas forming. I used it at a higher temperature which gave a wide CD range for bright plate. The neat part of the conforming anode is you can get the plate to go where you want it to go by tweaking the anode.
This means less grinding cost if you are doing heavy plate.
The anodes will go dead after X hours of use, unless you do heavy scraping. We just recycled the lead/tin/silver anode into a new one. We also added a small amount of tire weights to get a harder anode. I forget the metal that was in the tire weight alloy, but it does not take much. You have about a day after pouring the mat to make the anode, or it is too hard to bend easily. Welding (lead burning) mesh mat together is a learned capability that some never master.
- Navarre, Florida
Q. Using Barium Carbonate to Lower sulphate in Hard Chrome Solutions. I work with a rather stubborn individual who refuses to use barium carbonate to lower sulphate concentrations in our hard chrome plating baths. I use to use it quite often in a previous life, only in a decorative chrome solution. I never had any problems with roughness, nodules, specular finish, etc. He claims that hard chrome is not the same has decorative chrome (lol), so when the occasional high sulphate is noted, we cut the solution back into spec. Am I wrong?
George Brackett IIISr Manufacturing Engineer - Maine, USA
2007
A. It does not matter how you control the ratio. An excess of sulphate means that someone added too much sulphate or has not added enough chromium oxide to maintain the proper chromium level. In 12 years on hard chrome tanks, we never had to cut a solution or to use barium. Proper analysis with proper additions takes care of the problem!
James Watts- Navarre, Florida
A. Dear Friend,
Using barium carbonate or barium chloride is helpful for reducing the sulphate values. Barium carbonate will produce sludge whereas barium chloride will not do so.
Regards,
plating process supplier - Bangalore, India
Q. Thanks James, but the situation is actually this -- we need to add taper to some of our barrels, and we do this by controlling the sulphate. We run several different barrels in each of the plating tanks, so small adjustments are necessary.
George Brackett III- Saco, Maine, USA
A. George,
No knowledge, just gut feeling, is that barium carbonate will promote shelf roughness unless you filter or allow the tank to settle for a period of several hours.
Adding barium chloride will add chloride ions to the tank and they are a better catalyst than sulphate, so I would not use the chloride.
Your co worker's method does not sound like any fun and at best is messy. It also sounds like a lot of trial and test to get it exact.
- Navarre, Florida
A. Sounds like the more analysis, the better, in a case like this. If I was trying to finesse the plating thickness (that is how I interpret "adding taper") via ratio, I'd be analyzing it every day. Possibly, more than once. :)
I hate to differ with people who are actual platers (I am an analytical guy) but adding chloride to a chrome tank in any form is a terrible idea. Chloride is a contaminant in a chrome tank, not an easy one to remove, from what I know. I would stick with barium carbonate.
Mr. Watts: you've worked for more professional outfits than I. Most of the places I've seen have tried to skimp by cutting down on the cleanliness of the rinse preceding the chrome tank. Since this is generally a Watts nickel bath rinse, this practice results in sulphate drag in, and frequent additions of BaCO3 to compensate.
Original poster: the beliefs of your coworker are... interesting. Does he have any vacation time coming up?
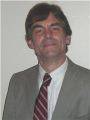
Dave Wichern
Consultant - The Bronx, New York
A. Chromium plating is excellent when it works, but when it goes wrong it is a real pig! The Cr(VI) baths require quite specific ratios of sulphate to Cr(VI) and this should be maintained at all times. How this ratio is maintained is up to you, but I believe in prevention rather than cure. I would therefore strongly recommend that the bath is analysed regularly and accurately; say at least once a day and whenever it has not been used for more than 3 consecutive days. I have to admit I have never had to use a barium treatment for high sulphate, but other platers I know that have done so say it is messy and requires good filtration systems and this is no fun with hexavalent chrome baths! However, it does work when needed!
Of course there are differences between hard chrome and decorative chrome, but the bottom line is that they both come from a sulphate catalysed bath that requires a specific ratio of metal to sulphate. Keep the chemistry right and the process will work!
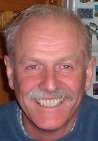
Trevor Crichton
R&D practical scientist
Chesham, Bucks, UK
A. In my past life of chrome plating, I would periodically have to add both sulphate and Barium carbonate. We operated a mixed catalyst bath. To raise sulphate .02 oz/gal I added 200 ml sulfuric / 1000 gal solution. To lower sulphate .02 I added 7 lbs barium carbonate. This is done on off shift, lightly sprinkled over surface of tanks with scrubber system on. The barium carbonate would fizz like Alka-seltzer for a minute. Rinse off bussing, and allow barium to settle to bottom for 1 hour. We continuously filtered our 1500 gal system with 25 micron bags and never had issues with roughness (nor did bags pick up loads of barium when added to system). I have 70 lbs of new barium carbonate that is destined for disposal. Start small with your adds of barium, read chrome suppliers instructions; you can always add more later. Good Day.
Tim DeakinNorth Tonawanda, New York
Q. I would like to know the implications of catalysts (Fluoride)/(Non-Fluoride) in hard chrome plating. What are the types / formulations of these catalysts and what should be the constitution of same in plating electrolyte for Hard Chromium?
Can I use a Hull Cell
⇦ huh?
for concluding the plating rate in such cases by varying catalyst?
Arvinda Kumar
- Ghaziabad,UP, India
2007
A. Hi Ravindar. We appended your inquiry to a thread which addresses the topic and offers a general introduction. I think you must use a "hanging hull cell" (a hull cell with holes in the bottom, and immersed in the chrome plating tank) for chrome plating experiments.
But unless you wish to spend years in research, I think you can use the head start that MSA catalyst will produce higher efficiency than sulfuric acid or fluoride. Good luck.
Regards,
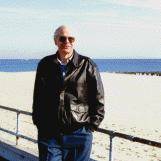
Ted Mooney, P.E.
Striving to live Aloha
(Ted is available for instant or longterm help)
finishing.com - Pine Beach, New Jersey
Q. Sir, Will you please suggest me the ratio of hard chrome solution? What should be ratio of chrome:sulphate:
Arvind Yadav- Bhiwadi, Rajasthan, India.
May 16, 2016
A. Hi Arvind. 100:1. Good luck.
Regards,
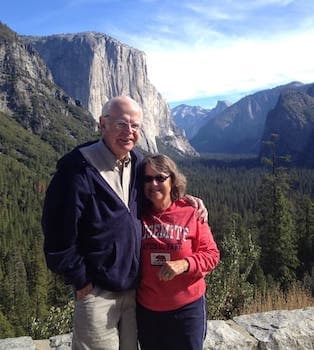
Ted Mooney, P.E. RET
Striving to live Aloha
(Ted is available for instant or longterm help)
finishing.com - Pine Beach, New Jersey

Q, A, or Comment on THIS thread -or- Start a NEW Thread