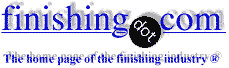
-----
Ruthenium/Iridium coated Titanium anodes
Current question and answers:
Q. Hello,
I am currently working on a project that involves generating repeated short-duration high-voltage pulses (around 6 microseconds and 80 kV) and making current flow though an aqueous solution. For this, I have been using stainless steel 316 in the shape of plates as electrodes, but the amount of iron, chromium and nickel ions released is too high. Unfortunately, this contaminates the treated solution and makes the electrodes last very little.
I was wondering if there was any type of plating that could withstand these high voltages. As far as I know (no experience), titanium works very well and it can be plated with inert metals like ruthenium, rhodium, palladium, iridium, platinum and gold. Do you think any of these are worth trying or if they could even work? Do you recommend other plating materials?
Thank you very much in advance for any advice that you can have.
- Hamburg, Germany
February 22, 2021
A. Hi Matias. We appended your inquiry to a thread about anodes of this sort. It should give you a start on the selection. In addition there is a very interesting posting from Tom Baker on thread 11754 which you might want to review.
Luck & Regards,
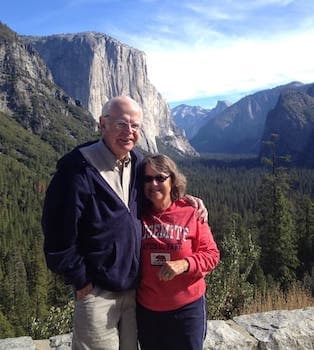
Ted Mooney, P.E. RET
Striving to live Aloha
(Ted can offer longterm or instant help)
finishing.com - Pine Beach, New Jersey
February 2021
February 25, 2021
A. Applying 60kV for 20 microseconds is likely to produce intense plasma close to the electrode which is likely to result in physical processes such as sputtering, chemical etching etc. I wonder if such situations are considered in electroplating, for the plasma may influence the chemical processes.
Titanium can be coated with gold and many other metals, metal nitrides, carbides etc by PVD processes.
Bangalore Plasmatek - Bangalore Karnataka India
Ed. note: Please, please, pretty please,
No abstract questions!
Q. Does anyone have any information or experience with selective passivation of portions an Iridium surface? I know low concentrations of F will accelerate passivity of the entire surface, but is there a way to selectively passivate (permanently) small areas or edges - I do not want to grind off
Ed Skorupski- Stillwater New York, USA
November 26, 2020
November 2020
? Hi Ed. Apologies but I'm getting no mental picture -- why you can't passivate the whole surface, what these edges are, what it is you want to stop grinding off and how passivation will save grinding it, whether you're talking about anodes or some other topic. Unfortunately, 'passivation' is one of the more confusing words in the finishing lexicon because it applies to so many processes in so many ways (passivation of stainless steel, passivation of carbon steel in boilers, passivation of zinc plating with chromates, passivation of phosphatizing with final rinses). Please tell us what you're building and what problems it is presenting. Thanks.
Luck & Regards,
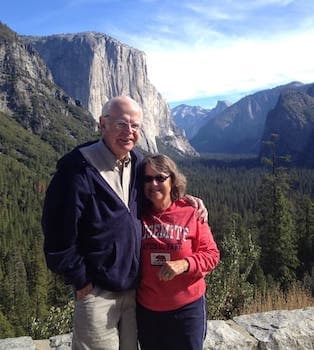
Ted Mooney, P.E. RET
Striving to live Aloha
(Ted can offer longterm or instant help)
finishing.com - Pine Beach, New Jersey
Q. The process involves continuous plating of copper out of acid sulphate bath on to a rotating cathode - the anode is wider than the cathode and as a consequence the hi-current density at the edge is manifesting itself as a "heavy" plated edge - because of the configuration and size of the anode and how the Ir coated anode plates are affixed to the subframe, mechanical methods are not feasible. When I use "passivate". I mean render non-conductive.
Ed Skorupski [returning]- Stillwater, New York, USA
November 28, 2020
A. Hi again. If the anode cannot be shortened, is it not possible to mask the ends either with a polymer or by installing a mylar or similar sheet between the anode and cathode to act as a shield? I admit that I don't fully understand your arrangement, but it seems to me that rendering the ends of the cathode non-conductive would just slightly reduce the width of the plated strip without solving too-thick at the edges plating problem.
Luck & Regards,
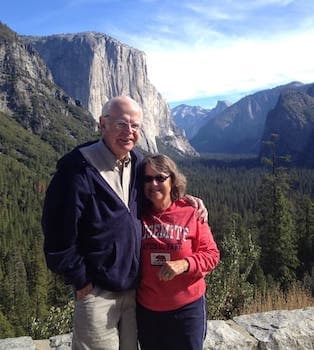
Ted Mooney, P.E. RET
Striving to live Aloha
(Ted can offer longterm or instant help)
finishing.com - Pine Beach, New Jersey
November 2020
⇩ Related postings, oldest first ⇩
Q. I'm looking for an anode resistant to corrosion in aqueous media and at high voltage (25 - 50 volts). For example, When proceeding to electrolysis of water, a relatively inert anode which also has some good electric properties is required. I am looking for that kind of anode.
Vincent CaronUniversity of Sherbrooke - Quebec, Canada
1996
1996
A. Platinum or Graphite. Platinum clad mesh materials go for about US$5.00/square inch. The Metal Finishing Guidebook lists several sources for both materials.
Good Luck,
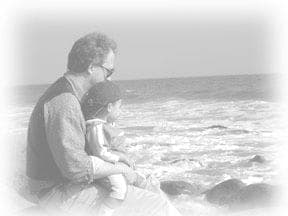
Dave Kinghorn
Chemical Engineer
SUNNYvale, California
A. You can try activated titanium electrodes, this is titanium covered by ruthenium and/or iridium oxide. This is also known as DSA (dimensionally stable anode) material.
Another possibility is Ebonex.
Regards,
Frank Vork- Eindhoven, The Netherlands
1996
Q. I've heard that titanium covered with ruthenium and/or iridium oxide is a very expensive technology. I'm looking for an anode with a surface area of about 200 square cm.
Vincent Caron [returning]University of Sherbrooke - Quebec, Canada
1996
RFQ: Our company is based in Malaysia and we are involved in plating of leadframes. We are presently looking for a vendor to plate iridium oxide on our titanium anodes. We plan to convert all our platinum anodes to Iridium oxide coated Titanium anodes.
Nick Lim- Malaysia
1997
Ed. note: This RFQ is outdated, but technical replies are welcome, and readers are encouraged to post their own RFQs. But no public commercial suggestions please ( huh? why?).
A. Hello Nick,
Typically this process is done via vacuum methods, or by plating of Ir then thermal oxidization. Do you actually want reduced Iridium or the Oxide exposed? I am interested in understanding why you choose the Oxide? Also, are these platinum anodes that you will replace with IrOx/Ti located in your high-speed cells or your low speed flood cells? Using it in your high speed cells may introduce a severe design constraint into your cell tooling designs. I am sure if you contacted Technic, Inc. they will put you in contact with someone that they supply Ir to.
Regards,
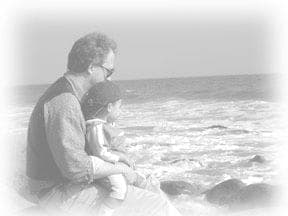
Dave Kinghorn
Chemical Engineer
SUNNYvale, California
1997
Properties of ruthenium oxide and iridium oxide coatings
Q. I am searching for the electrical and corrosion properties of ruthenium oxide and iridium oxide anode coatings intended for the electrodeposition of cationic coatings.
Paul R. Kerr1998
Q. Dear Sir,
We are looking for the RESISTIVITY of IRIDIUM OXIDE ( IrO2 ). Many thanks for an answer on this subject.
Sincerely yours.
Jean-Michel.DESVIGNESLab. CHARLES FABRY de l'INSTITUT d'OPTIQUE - Orsay FRANCE
2000
A. The electrical resistivity of our IrO2 films is about 40 micro-ohm-cm (which compare well with that of single-crystal bulk IrO2). this particularly answers the questions of Jean-Michel.DESVIGNES from Lab. CHARLES FABRY de l'INSTITUT d'OPTIQUE and Paul R. Kerr.
-We have developed a new physical process to coat virtually any surface (Titanium is an excellent substrate with highly conductive and dense IrO2 films with an excellent adherence (Appl. phys. Lett. 69, (1996) 2027) . So this is a direct response to the Nick Lim - Malaysia.
- These iridium oxides have been tested for some specific corrosion studies and they have exhibited excellent corrosion resistant behaviors. Other applications are currently under evaluation.
Prof. My Ali El KhakaniUniversité du Québec / INRS - Energie et MatÈriaux / Varennes, QuÈbec, Canada
2000
How iridium coating is done
Q. I need information on how to coat Iridium on Titanium anodes. I am trying to coat a spring finger on a rack that is involved for plating.
James J. Sezemsky1999
Q. I am studying about DSA for chlor-alkali industry. I know that they are mostly made from titanium coated with titanium oxide - ruthenium oxide.
My question is this: How is the way of coating this DSAs? and what are the salts used in the coating? I will be thankful if you can guide me.
Yours faithfully,
Mohammad Abedi- Tehran, Iran
2001
A. Platinum group metals are deposited on titanium via thermal decomposition methods. For the most part, any form into which you can fabricate titanium, can be coated.
Depending on application requirements, the coating composition and loading can be altered for better performance.
Iridium oxide or iridium oxide/tantalum oxide mixes are quite common and perform well in a broad variety of applications.
For chlorine generation, mixtures containing ruthenium oxides are typically preferred due to higher yield (i.e. better specificity).
Siemens - Union, New Jersey
2007
Multiple threads merged: please forgive chronology errors and repetition 🙂
Ruthenium or Iridium Oxide coated Ti anodes in electro-coating
Q. I am looking for information on the use of Ruthenium or Iridium Oxide coated Ti anodes in electro-coating. Why are expanded metals used in this type of anodes? One would think it would be difficult to have complete coverage of the expanded metal. I'll appreciate hearing from someone with experience or knowledge in this area.
Thanks,
Paul Lim- Toronto, Canada
2002
2002
A. RuO and IrO are what we refer to as DSA (Dimensionally Stable Anodes). They are used when one or all of the following conditions exist.
1) Very high current densities (greater than 5 amps/SF up to 12 amps/SF)
2) Concern for good UV durability on cationic acrylic tanks. As you experience soluble iron contamination greater than 20 ppm from parts or iron dissolution from stainless steel anodes that leak or overflow from plugged return lines, the UV durability will drop off rapidly.
3) Cationic color control tanks. Cationic tanks whether or not they are acrylic or epoxy can benefit in color control if you minimize the potential for dissolved iron from entering the paint bath from fallen parts or iron dissolution from stainless steel anodes that leak or overflow from plugged return lines. RuO is about twice the price of stainless steel and IrO is even higher yet. The RuO and IrO material are brushed on to a titanium anode. These hold up extremely well, but they can be prone to corrosion if the RuO layer is scratched.
Gurvin SinghMohali, Punjab, India
A. Ruthenium and Iridium Oxide coated mesh type anode is suitable for electrolysis of chlorates and caustic soda ⇦liquid caustic soda in bulk on Amazon [affil link] anodes. It weighs light and surface area is more. You can operate 2KA/m2 suitable. Coating adherence is not a problem for mesh type anodes. Iron will deposit in the anode while power cut and will inactivate your UV system.
R.NagarajanChennai, Tamilnadu, India
2002
A. Expanded metal is a very efficient form of titanium to use in developing an anode. For example, if the mesh pattern has about 50% void area, the surface area is the same as for a solid sheet, even though half the titanium material is used. The cost of expansion is markedly less than the material savings for an expensive material like titanium.
The coatings are applied as salt solutions and the baked in an oven to convert to oxides. Various proprietary methods are used by manufacturers to prepare the surface for the coating and to control the thickness and uniformity of the coating to assure proper quality. Coating uniformity is not perfect, but depending on the manufacturing method, it can be quite good.
Coating loading effects life, but unless the area effected is large, the current discharge would shift to a nearby site that is still active. The titanium would form a passive film that would not breakdown and pass current. In most applications, the majority of the coating would have to fail before titanium substrate failure began.
Barry L. Martin- Concord, Ohio
2003
Seeking IrO2 Coated Anodes
2003RFQ: We are a service looking forward to supplying below product to our good customers. Kindly offer your quotation as below. Titanium Mesh Dimension: W250mm x L640mm x T1 mm, with Iridium Oxide coating as an insoluble plating anode. Life time: in pulse mode of rectifier, Fw120A / Rev240A(current density 120ASF) can last for 6000 hour. General need: 600~1000 pieces per year. If any question please let me know. We are looking forward to receiving your response soon.
Mika Cplating service - Taiwan [last name deleted for privacy by Editor]
Ed. note: This RFQ is outdated, but technical replies are welcome, and readers are encouraged to post their own RFQs. But no public commercial suggestions please ( huh? why?).
Multiple threads merged: please forgive chronology errors and repetition 🙂
Mixed Metal Oxide Coating (MMO) on Titanium Dimensionally Stable Anodes (DSA)
Q. The electrolytic chlorine generation industry and the "grounding" industry associated with galvanic corrosion both reference a Mixed Metal Oxide or MMO coated Titanium electrode. The metals referenced are NIOBIUM, PLATINUM, RUTHENIUM, IRIDIUM, etc. Does anyone have any details on this MMO coating and the process involved in producing this MMO coating? In addition, there seems to be new technology out there emerging which allows the polarity of the anode and cathode to change without damage to the coating. All info would be appreciated.
Thanks,
- Batesburg, South Carolina
2005
![]() |
Q. I need the detailed information about how the mixed metal oxide coating on Titanium mesh. SK.Gajalakshmi- Theni, Tamilnadu, India 2006 Q. I need the detailed information about how the mixed metal oxide coating on Titanium mesh/plate. John Wong- Shanghai, China 2006 RFQ: We are interested in buy some anodes plated with the IrO2 coating, 50 square meters. TONNY [last name deleted for privacy by Editor]plating shop - Longgang, Shenzhen, China 2006 Ed. note: This RFQ is outdated, but technical replies are welcome, and readers are encouraged to post their own RFQs. But no public commercial suggestions please ( huh? why?). Q. How to coat the Iridium & ruthenium oxide with titanium metal. aparna sivalingamproduction manager - Coimbatore.Tamil Nadu, India April 6, 2009 Q. DSA. We need to coat the mixed metal oxide like Ir, Ru Oxide coating technologies. student - coimbatore.tamil nadu, India April 6, 2009 |
Issues with anodes for chloride zinc plating bath. How long do anodes last?
Q. We are using iridium coated anodes in our chloride zinc plating bath. After 3 weeks the resistance started going up and the current flow started down. I checked them with x-ray florescence and found the iridium is still there but I am now showing chrome also. I had a problem with chrome contamination around the same time. Could chrome immersion plate on the surface of the iridium and would it stop the current flow?
Chuck Beckerditecaptive plating shop - Versailles, Missouri, USA
July 29, 2008
A. Hi Chuck. Chrome should not immersion plate on your anodes because iridium is a noble metal. Although such anodes can be used as auxiliary anodes to reach low current density areas, I'm not familiar with doing zinc plating with only such anodes. Where does the zinc come from if not from zinc anodes?
But chrome can really mess up a plating process. I'd suggest doing some Hull Cell ⇦ huh? testing to see if the plating solution has been successfully decontaminated and will plate properly. Good luck.
Regards,
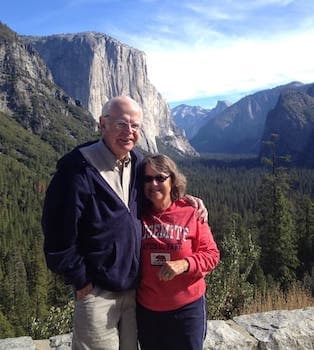
Ted Mooney, P.E. RET
Striving to live Aloha
(Ted can offer longterm or instant help)
finishing.com - Pine Beach, New Jersey
Hydrogen production vs. surface area
Q. Formula needed: I want to have Titanium Plates coated in Iridium for Hydrogen production in distilled water using a non caustic Electrolyte. What is the Electrochemical formula for the amount of hydrogen produced, by the amount of square inches of plate or mesh size, by the amps used?
Is there one?
Plate size example:
2.75" x 8" plates , 8 solid plates, or 8 mesh plates?
- Eldersburg, Maryland
May 29, 2009
June 4, 2009
A. Hi, Howard. I don't think there is a formula for amount of hydrogen per square inch -- I think that's an empirical number based on the construction details. But I think that the amount of hydrogen per amp-sec should be predictable by Faraday's Law of Electrolysis, which says that 96,485 amp-seconds will release 1 gram equivalent weight.
Regards,
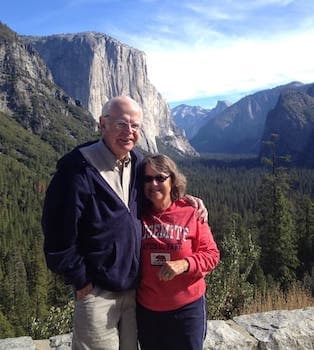
Ted Mooney, P.E. RET
Striving to live Aloha
(Ted can offer longterm or instant help)
finishing.com - Pine Beach, New Jersey
Need mmo coating of titanium sheet
RFQ: I need titanium coated with a mmo that is compatible with KOH as an electrolyte and able to be used as an anode in electrolysis. I am looking for a price to coat both sides of titanium sheet .8 mm thick 4' x 8', 4' x 10', 8" x 8", 6" x 6", 4" x 4".
Jason Bambenekelectrolysis - St Cloud, Minnesota, USA
September 9, 2010
Ed. note: This RFQ is outdated, but technical replies are welcome, and readers are encouraged to post their own RFQs. But no public commercial suggestions please ( huh? why?).
Need MMO plating of titanium
RFQ: Need 3 square meters / month
David Leeelectronics mfgr - , Florida, USA
January 20, 2011
April 11, 2012
Q. I am looking to bring Iridium coating in house. It is currently out sourced to a company that I believe is brushing it on. The material we are coating is Titanium and it is an anode structure.
I am not having much luck finding techniques or information on the topic. I think the people doing it now are roughing the surface then painting a coating on it, which is bluish (I believe IrO). Then I believe it is being baked in an oven.
Any help would be appreciated.
- Dayton, Ohio, USA
A. The substrate is sand blasted and pickled for the removal of scales. A paint of isopropyl alcohol with the metal chlorides along with titanium tetra chloride is painted by brush with no metal parts. It is baked in oven at 400 to 600 degrees. Painting and baking done many times to achieve the desired thickness. If wear resistance is needed iridium chloride is added, if catalytic action is needed ruthenium chloride is added, for water electrolysis, more platinum chloride is added. If high current density is required niobium is added. As far as I know.
Ganesanbala Chandran- Chennai, India
May 18, 2012
Paints or pastes for coating Ti electrodes with Ru and Ir Oxides
Q. We use Ti electrodes in electrolysis of salt solution. We need to coat the Ti with ruthenium and iridium oxide. Any suggestions about how to do it will be greatly appreciated.
Vinod SikkaProduct Designer - Oak Ridge, Tennessee, USA
July 6, 2015
September 3, 2015
My understanding is that one applies the Ru or Ir to the CLEAN Ti surface as the appropriate nitrate. By CLEAN I mean totally free of oxides. One does this by treating the Ti with a nitric/HF or nitric/NH4HF2 pickle. Right after rinsing, you paint the precious metal nitrate on. Then, bake, to something like 400 °C.
After baking, you may with to add more nitrate solution, you might wish to do this a few times. On the final baking cycle, cool the coated metal electodes rapidly. One wants a certain amorphous nature in the coating; that helps the catalytic activity.
There's lots of literature out there about this technology. Such electrodes are commercially known as DSA - dimensionally stable anodes.
My knowledge of this is rusty. This is some stuff I did 20 years ago. I tried, not having any Ru or Ir, to coat my anodes with a mixed oxide of Ni and Co. I got a nice adherent coating, but the catalytic activity was disappointing.
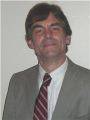
Dave Wichern
Consultant - The Bronx, New York
⇦ Tip: Readers want to learn from your situation;
so some readers skip abstract questions.
I wanted a detail parameters for iridium coating on titanium plates. Also wanted to know whether these parameters remain same for MMO coating as well?
Eshan Gupta- Delhi, India
February 20, 2020
A. Hi Eshan. If you introduce yourself and your situation and a rather specific problem that you are encountering, this forum will generally help you address the specific problem. But if you are looking for a technical paper addressing the subject, scholar.google.com or surfacequery.com is probably a better idea.
Dave gave the general idea of how th process is done 23 years ago, and others have offered miscellaneous hints in the intervening years, but it seems that despite many people asking a similar question before you, nobody has yet offered to write a paper on this subject for us :-(
Regards,
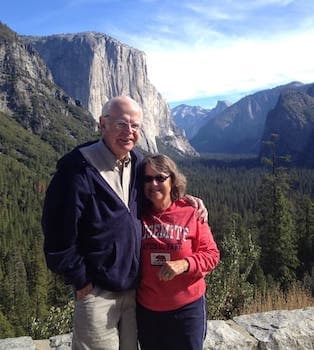
Ted Mooney, P.E. RET
Striving to live Aloha
(Ted can offer longterm or instant help)
finishing.com - Pine Beach, New Jersey
February 2020
Q, A, or Comment on THIS thread -or- Start a NEW Thread