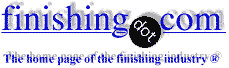
-----
How to reduce Blistering for plating on Zinc Die Cast?
Q. We are brass plating Zinc Diecast #3 & #5. We etch in Sulfuric and have success with most parts, on the other hand some parts seem to have excess skin, which blisters in powder coating at 350 °F. My question is if there is a normal thickness or range for this skin or at what point should it be rejected back to the diecaster as a casting problem.
Thanks,
Max T. Faethplating shop - Los Angeles, California
2001
2001
A. Max,
Even a part that hasn't been buffed shouldn't have a skin like you described. Your diecaster should check his process for even heat distribution in the die as well as his pressure...if it's a pressure casting. As far as plating, I always use a 4 oz/gal Fluoride based acid salt. I also keep the electrocleaner mild and time less than 30 seconds since a smut will form quickly and the copper strike will not adhere.
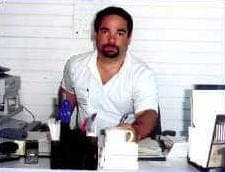
Jim Conner
Mabank, Texas USA
A. Hi. I'm having a little bit of a hard time picturing this "excess skin". I would think that the skin is nothing more than the surface which is contacting the die.
But I have seen plenty of "cold shuts" where there is a crack in the skin due to two flows being squeezed together after the zinc is too cold to fuse together. I suppose if the zinc were colder still, it might be possible for one skin surface to sort of flow over the other, leaving an excess thickness and a laminarity to the skin.
Then again, my actual experience is in plating; and my experience in diecasting is pretty much limited to watching -- so diecasters may be laughing at this idea :-)
Regards,
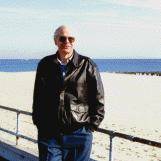
Ted Mooney, P.E.
Striving to live Aloha
finishing.com - Pine Beach, New Jersey
May 18, 2010
2001
by Safranek & Brooman
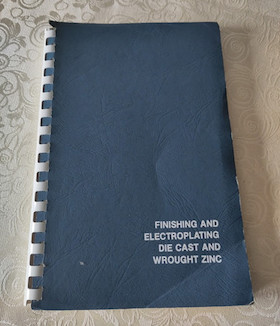
on eBay or Amazon
or AbeBooks
(affil link)
Q. The problem is delayed blistering of zinc die cast parts that are 1st plated with Cu and then Ni. A copper strike solution is utilized 1st and small concentrations of zinc are co-deposited with the copper.
My questions are: what levels of zinc will be harmful (if any) to the copper deposit? How much does a grain refiner like (rochelle salts) ⇦ on eBay or Amazon [affil links] actually help to prevent blistering? No organic additives are presently being used.
Would appreciate any feedback.
[name removed at request]- East Berlin, Pennsylvania
A. Skip the strike copper as I suspect you are getting a powdery deposit here causing the delayed blistering. Ensure proper degreasing, pickling and cyanide copper plating directly.
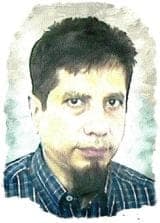
Khozem Vahaanwala
Saify Ind

Bengaluru, Karnataka, India
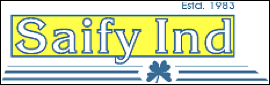
2001
2001
A. Have seen this problem myself and is usually associated with oxide films on the zinc castings that are plated over. Better cleaning and complete removal of the oxide layer from the zinc before a high cyanide low copper strike should solve the problem. If parts have been vibrator finished this is an ongoing problem we have had when the customer allows the surface to become ingrained with material from the vibrating process.
We have never found a complete solution to the problem sorry.
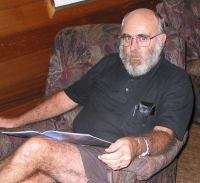
Bob Lynch
plating company - Sydney, Australia
Q. Hi there
our company does jobs for Zinc Die Cast Parts and found Blistering to be one of the prominent problems.
Could anyone please suggest a solution to prevent it?
Thank You.
plating shop employee - Singapore
2007
A. Hello, YC, welcome to the finishing.com community. Blistering on diecastings has been a perennial problem (see threads 4846, 29746, 33784, 47424 for a sampling) and is due to a number of factors including poor surface condition of the diecast "skin", outgassing from porosity, entrapment of solutions due to porosity, and improper pretreatment.
Probably the first thing that needs to be done is the institution of QA measures regarding the quality of the castings. A general rule is that a lot of castings that are suitable for painting or organic coatings are simply not good enough for plating; for example, a part with a cold shut is not useable. A second thing that may be considered is impregnation of the castings to fill the remaining porosity. Third, your chemical process supplier can recommend a proper mechanical and chemical pretreatment cycle, and work with you to implement it.
Conventional wisdom is that you can't "break the skin" because underneath the skin the casting will be porous. However, there are shops that disagree with this idea. New Brunswick Plating [a finishing.com supporting advertiser] has for decades now championed the idea of what they call "chemical milling" of diecastings, and have produced millions of highly reliable parts with it. I do not know whether they would license their process to a company in Singapore, but it's worth an e-mail. Good luck!
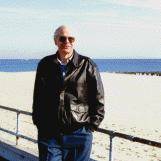
Ted Mooney, P.E.
Striving to live Aloha
finishing.com - Pine Beach, New Jersey
2007
Q. Hey everybody thanks for doing what you do!!
Having some issues w zinc die cast racked parts; we have a process where the piece is milled on the inside for a latch to click in. I already had a cross section done and know that there are pores and cold shuts. Based on that I would think milling the piece would "open a can of worms" in that area.
Is there anything I can do to mask blistering? What should I be looking at specifically? Have pulled parts out of copper cyanide rinse tank before bright nickel and have not seen evidence of blisters. We have a 2 Cu plate tanks before bright Ni. Degrease, Electroclean, Acid Etch pretreatment.
What typically causes blistering in a Cu cyanide of bright Ni tank?
Plating Supervisor - Chicago, Illinois, USA
November 16, 2018
November 21, 2018
A. Blistering on ZINC DIE CAST IS MAINLY DUE to two things, one is porosity & second one is Precleaning.
This blistering mainly occurs in the oven while polymerizing the E-coat. This can be avoided by using low bake lacquers & good precleaning cycle using 1-3% sulfuric Acid as an activator, followed by Alkaline Copper of 10 microns, then followed by your required plating.
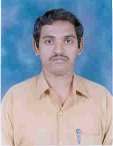
Panjala Mukesh
fashion jewelry mfgr.
Hyderabad, India
Blistering issues plating over porous zinc die cast surfaces
March 20, 2020Q. We've been having some plating issues on many different zinc diecast parts: mostly blistering. It's been occurring off and on for many years, but recently it's become a more consistent issue. FYI, we are plating CN Cu, Acid Cu, duplex Ni, and Hex Chrome over the Zinc diecastings.
The defects are only occurring in very porous areas of the casting where we can see some physical defects even before plating. Possibly improving polish and buff could correct or alleviate these issues (FYI we contract out all of our P&B work), but we have sent parts to another plater and they had no blistering problems, although there were still some visible casting flaws. Our customers aren't so concerned with the casting imperfections, but blistering is 100% unacceptable. So that's the goal.
Defect Explanation (see cross section photos attached):
1. Blistering. Nearly all cross sections that we've done look like the ones I have attached: Cu plating spanning a HUGE void in the casting. The Cu almost always has an area that appears to have been compromised.
2. Black deposit stains - looks like LCD dummy deposit (I believe this is Cu or Zn co-depositing with Ni). Our cross sections show no Ni plate thickness in these black stained areas. Cu still spans most of the void with an area that has been compromised.
FYI, this is my current theory: (but I'm totally fine with being wrong, so please throw out any other ideas)
I know that it's impossible to plate over thin air, so there must have been zinc under this copper bridge at one time. I think the casting porosity in the raw part is much smaller than the voids we see in the cross section, but we're attacking the zinc somehow after CN Cu plating and expanding the void.
My theory is that we're trapping acid in the casting pores and we plate over the pores in our CN Cu's (or at least mostly cover over the pores). The acid continues to eat away the zinc under the Cu, which generates H2 gas. Eventually this Zn attack compromises the Cu layer and allows further plating solutions to enter and continue attack. Possibly the H2 gas pressure is what's causing the blisters to pop or could be escaping through the opening in the Cu deposit, which limits Ni plating in that area.
Recently I've been focusing on our acid rinse to try to flush out any residual acid from the pores:
- Maintain pH close to neutral (it was 2.6 and the ZDC acid pH is 2.15 - this was a huge red flag to me). FYI, it was so acidic because it is a shared rinse with our steel and ZDC acid dips, and the steel acid is MUCH stronger.
- Extending rinse time (from 5 sec to 60 sec)
- High air agitation in the rinse to try to get all of the acid out of the pores.
- Double dip in rinse - just finished modifying our hoist program code to enable this. Won't be able to test until next week.
Engineering Manager - Currently troubleshooting this problem - Grand Rapids, Michigan USA
A. Hey Matthew,
Unfortunately I do not see any pictures. With any die casting a large amount of problems can occur to cause blistering. One common problem I've seen is if your CN Cu layer is too thin, solution from the acid copper can reach the zinc through the porosity of the plating and attack your zinc substrate.
For the rinsing in the cleaning operations;: hotter rinses should be used if you can to help get chemistry out of pores. Clean rinses are also essential as the acid dip can cause blistering if the part is left in there too long, so dirty rinses may be acting like a diluted version of the tank.
Ensure when you go into the CN Cu you enter live. Obviously there could be issues with the process itself, but that would be a very long list.
As for the black stains, do they always show up with blistering or have you seen parts with the black staining and no blistering?
- Sidney, New York USA
April 3, 2020
----
Ed. note: Please e-mail pictures to mooney@finishing.com for posting here.
A. I have yet to persuade anyone else to try this, but as a coop part time student in the 1950's, I would cyanide zinc plate the zinc die casting first and then copper-nickel-chrome. The plan would probably work with modern alkaline zinc but not acid chloride zinc.
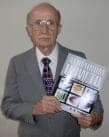
Robert H Probert
Robert H Probert Technical Services

Garner, North Carolina
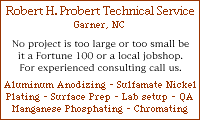
April 4, 2020
April 6, 2020
Q. Thank you for the responses. Pictures are attached:
1. William - I've suspected CN Cu being too thin as well. We've tried significantly increasing this thickness without any success (15um+, 6 mins CN Cu Strike, 30 mins high speed CN Cu Plate).
In the CN Strike we are live as soon as the bar hits the V-block (so there is about 3 seconds dead time for the bottom rows of parts that enter the solution first). We've had blistering issues in the past due to delays with the rectifier turning on, so now the rectifier is live all the time to avoid this.
As for the black staining, this defect has NOT occurred in tandem with blistering. On some parts we don't get blistering, but instead we get these black stains. The one common thread is that both of these defects occur ONLY over areas with visible casting defects (mostly cold shut - visible even before plating). We've been able to significantly reduce blistering by working with our polish and buff vendor, but that is unfortunately causing other rejects (deforming a critical surface, buffing compound trapped in grooved/textured features, etc.).
The odd thing is that we've sent some parts to one of our competitors to be plated. The parts still have high porosity and cold shut visible after plating, but there is no blistering after plating. So it does seem like there is something off with our process that is causing this blistering.
2. Robert - That's a very interesting thought. Unfortunately we don't do any zinc plating here, but I can look into sending some parts to a nearby zinc plater. The only issue I can think of is that they would need special zinc diecast cleaners, right? Most zinc platers are plating over steel, so their cleaners would destroy our zinc diecastings. Maybe I'm better off trying to make up an alkaline zinc bath in our lab to try it out.
- Grand Rapids, Michigan, USA
April 6, 2020
Try the alkaline zinc in your lab.
(1) start with grocery store powdered detergent (Tide) in a 4 L stainless steel beaker, hit it with low anodic current for about 10 seconds.
(2) 5% sulfuric acid
(3) Caustic pre-dip (which you should do anyway)
(4) set it in the alkaline zinc, wait 30 seconds for the alkaline plating zinc to act as an immersion "zincate" to coat any of the exposed aluminum in the alloy, then turn on the current at zero and spend 5 minutes raising the voltage until the target current is seen. Let us all know.
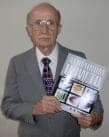
Robert H Probert
Robert H Probert Technical Services

Garner, North Carolina
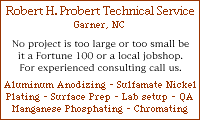
April 14, 2020
A. Hey Matthew,
Those photos, to me show that the substrate is continued being attacked after plating. Plating would not span that surface in that manner. I would take a look heavily at your cleaning process to ensure all chemistries are being removed from the surface.
As I am unaware of your process I'll make some general comments.
If you are using a solvent degreaser ensure it is clean and performing. If not, some of the stubborn buffing compounds will stay and ruin the process.
Lower the temperature of the electroclean as the chemistry will attack the substrate continuously as you remove it from the tank and during transfer times.
After electrocleaning rinse in clean rinse tanks as you do not want a diluted chemistry attacking the substrate. Ideally this will be a two step rinse, the last being clean and warm-hot to ensure the water can rinse out pores.
The acid dip should be mild chemically, ambient temperature, and time in the tank should be kept low (under 1 min more than say 15 seconds) If your using a proprietary mixture follow the low end of the chemical manufacturers recommendations
Between the acid dip and the cyanide plate there should be another very clean rinse, ideally hot, to flush out the pores of any acid before entering the cyanide bath.
Amphenol Aerospace - Sidney, New York USA
A. Porous zinc is not good to electroplate. You need to make sure that all polishing and buffing compound is removed from the pores and then give the casting a good coating of cyanide copper - use this as it has very good throwing power and will hopefully penetrate the pores. You must also ensure that any solutions used to prepare the casting for plating are also removed, as these too will cause blistering. Once the pores are filled, you should be able to get a satisfactory electroplate, but remember to make sure all processing solutions are removed. I have heard of platers who prepare their castings in the correct manner and incorporate very good rinsing in clean water. When it comes to the electroplating stage, the castings are put into the electrolyte and agitated for a minute or so to ensure that any remaining rinse water is removed from the pores and replaced with electrolyte. As an alternative solution, try improving your castings and minimise the porosity.
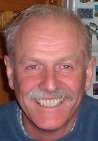
Trevor Crichton
R&D practical scientist
Chesham, Bucks, UK
May 8, 2020

Q, A, or Comment on THIS thread -or- Start a NEW Thread