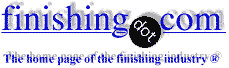
-----
Thick Galvanized Coatings, How to Get, What is Maximum
1999
CLOSE BUT NO CIGAR?
You might instead be interested in:
letter 55032, "How can we minimize galvanize coating thickness?" or
letter 7666, "Hot Dipped Galvanized Coatings: G140 vs. G90 vs. G60" or
letter 45732, "Thickness of hot dip galvanizing vs. salt spray test results"
Q. I am trying to find information on the relationship between the quality of the hot-dipped zinc coating on light gauge non-structural sheet steel and the thickness of the steel.
We fabricate roofing and venting products for the construction industry.
A rather non-specific standard call out is the term "corrosion resistant" galvanized steel and sometimes an actual thickness (i.e., .019" or 26 Ga) will be included. Little else is given in terms of what specifically it it meant by "corrosion resistant" in relation to the use of the metal. Our contention is that the thickness of the steel has less to do with it's ability to withstand galvanic corrosion than the type, quality, and thickness of the zinc coating.
As of present, we have been unable to find any information to assist in better understanding this relationship. Any assistance would be greatly appreciated.
Neil Chapmanmetal products - Long Beach California
for Engineers, Shops, Specifiers
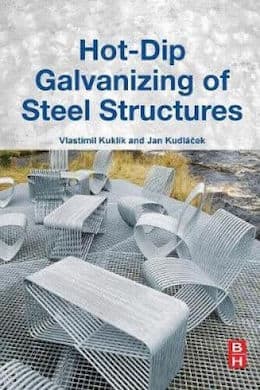
avail from eBay, AbeBooks, or Amazon
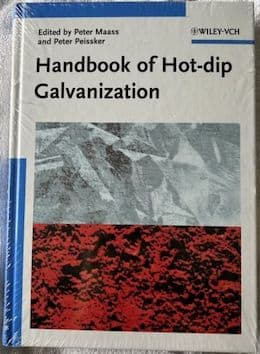
avail from eBay, AbeBooks, or Amazon
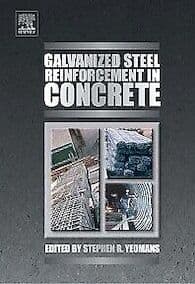
avail from eBay, AbeBooks, or Amazon
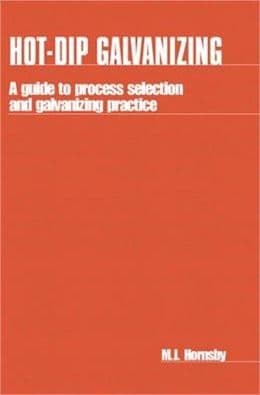
avail from eBay, AbeBooks, or Amazon
avail from Amazon
"User's Guide to Hot Dip Galvanizing for Corrosion Protection in Atmospheric Service" by NACE (1997 only rarely avail.)
avail from AbeBooks, or Amazon
(as an Amazon Associate & eBay Partner, we earn from qualifying purchases)
A. You are correct,
from the Metals Handbook, American Society for Metals. So a specification as to thickness of coating versus service conditions, similar to some electroplating standards against corrosion, is probably available. When I was in the coil coating business, my boss was trying to coil coat galvanized steel so that it would last longer in use for pig shelters. I don't know how far he got.
Look up specification ASTM A123 and ASTM A153 for coating weight requirements:
A123/A123M-97ae1 Standard Specification for Zinc (Hot-Dip Galvanized) Coatings on Iron and Steel Products Copyright 1999 AMERICAN SOCIETY FOR TESTING AND MATERIALS, West Conshohocken, PA. All rights reserved.
1. Scope 1.1 This specification covers the requirements for zinc coating (galvanizing) by the hot-dip process on iron and steel products made from rolled pressed and forged shapes, castings, plates, bars, and strips.
or
A153/A153M-98 Standard Specification for Zinc Coating (Hot-Dip) on Iron and Steel Hardware Copyright 1999 AMERICAN SOCIETY FOR TESTING AND MATERIALS, West Conshohocken, PA. All rights reserved. 1. Scope 1.1 This specification covers zinc coatings applied by the hot-dip process on iron and steel hardware.
Best regards, Tom
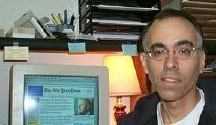

Tom Pullizzi
Falls Township, Pennsylvania
A. I agree with Tom's recommendation. However, there is still the matter of the bonding strength of the zinc coating (no matter how thick) to the substrate. Factors prior to zinc coating such as cleaning, degreasing, and other surface preparation makes it worth this condition.
Q. Speaking of thickness, our technical staff have been thinking whether a zinc electroplated material can attain the same thickness (assuming same bonding strength) of a hot dip galvanized either by plating in much longer time or accelerating the time by adjusting the electrical supply. Is this feasible, technical and economy wise? Your inputs would greatly be appreciated.
Anthony Austria- Philippines
1999
A. No, Anthony, it's probably not feasible. Normal zinc electroplating thicknesses are from about 0.0002" to about 0.0010" thick (5 µm to 25 µm). Beyond that thickness it not only takes too long and consumes too much energy, but the properties start becoming different (too much porosity, stresses too high, lack of brightness, etc.)
When you want thin coatings, zinc electroplating is usually better than galvanizing or any other method of applying the zinc; when you want the thickest coatings, galvanizing (or flame spray for field work) usually wins; in between, mechanical plating, dip-spin-coatings, or sherardizing might be applicable.
Regards,
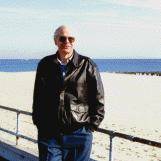
Ted Mooney, P.E.
Striving to live Aloha
(Ted can offer longterm or instant help)
finishing.com - Pine Beach, New Jersey
Multiple threads merged: please forgive chronology errors and repetition 🙂
Q. Hi,
Please I have to know that if Galvanize coating thickness is 85 microns, what should be maximum admissible thickness of Galvanize coating.
Highly appreciate your prompt reply. Thanks
Regards
Employee - UAE
June 16, 2011
A. Most standards state a minimum thickness for galvanizing, and no maximum.
But there is a practical maximum, defined by physical things that happen when coating is thick, or by the cost of obtaining a thick coating.
To get a very thick coating (say >1000µ ), long immersion times are required. For plain mild steel, some hours might be required. But for processes to make money, they normally want immersion times of 5-10 minutes, or less. So there's a cost in getting thick coatings.
But very thick coatings tend to separate along the lines of the various alloys involved in the coating. In simple terms this means some of the coating falls off, and other parts become apparently brittle. (while not technically brittle, they delaminate easily with impact).
So, please expand your question. Why do you want thick coatings?
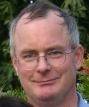
Geoff Crowley
Crithwood Ltd.
Westfield, Scotland, UK
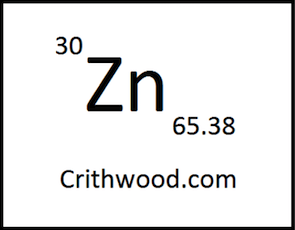
June 17, 2011
A. That is absolutely correct: all specifications of Hot Dip Galvanizing demand minimum Zinc Coatings.
It is also equally important what thickness of work you are Galvanizing. It is very difficult to give 100 µ Zinc coating on 1.5 mm thick sheet; on the other hand it is also again very difficult to give 40 µ zinc coating on a 25 mm thick plate.
Normally in fabricated steel structures, customers define the plating thickness.
- Mumbai, Maharashtra, India
August 1, 2011
Q. I will not add some comments or answers to your queries but I will ask questions that could help also my problem on galvanization. Here it is: What is the standard minimum thickness of galvanization for metal hardware? I have 1 mm thickness hardware that is used for pet gates. Is there any standard galvanization materials that will guarantee best results? Thanks to let us know.
Regards,
Luichito
- Ho Chi Minh City, Vietnam
August 9, 2011
A. Dear Luichito,
The standard minimum coating thickness depends on the item's steel thickness. According to International Standard ISO 1461, minimum coating thickness standard for steel thickness 1 mm is 35 micrometer (local) and 45 micrometer (average).
Regards,
- Selangor, Malaysia
August 9, 2011
Is 250 µm galvanizing too thick?
Q. We have a case of galvanising mild steel (E 250, Fe 410, C quality Weldable as per IS 2062) to a thickness of 250 micron.
Would like to get comments on the appropriateness of the coating thickness of 250 micron, from de-lamination point of view.
engineering consultants - Gurgaon, Haryana, India
August 21, 2012
How to get required galvanizing thickness in shorter time?
Q. sir,
We are using 2.74 thick grade 50 steel for galvanizing, and our customer requirement is 150 microns. But to provide that we have to give 40+ minutes dipping time. That is the thing which we want to overcome; please suggest something so that we can get 150 microns in less time period.
engineer - oman
January 21, 2016
A. Shotblast the steel to at least SA2.5 prior to galvanizing and you will reduce this excessively long immersion time.
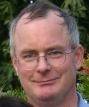
Geoff Crowley
Crithwood Ltd.
Westfield, Scotland, UK
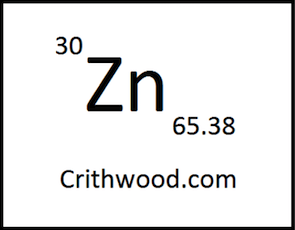
January 22, 2016
A. The thickness of galvanized coatings is influenced by:
1- Surface condition of steel: Grit blasting steel before galvanizing roughens the surface and increases its surface area, producing thicker coatings
2- Composition of the steel: Both silicon and phosphorous contents can have major effects on the properties of galvanized coatings.
3- Material temperature prior to galvanizing: more dried and heated materials delivered to the kettle will lead to a shorter galvanizing time. You could check the dryer prior to galvanizing.
Energya Steel Solution - Jeddah, Saudi Arabia
March 17, 2016
A. Sir:
Turn "Up" the molten zinc temperature. For example, from 835 °F to 850 °F.
Regards,
Galvanizing Consultant - Hot Springs, South Dakota USA
March 17, 2016
A. Turning up the temp in a zinc kettle requires caution.
With increasing temp (up to something like 500? °C) there's increased kettle wall erosion. A 50 mm wall kettle should last 10 years. At 500 °C it is measured in hours.
For anything much over 470 °C, use a ceramic kettle.
Small temp increases (say from 450 °C to 460 °C) don't show any increased galv thickness that is statistically different.
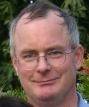
Geoff Crowley
Crithwood Ltd.
Westfield, Scotland, UK
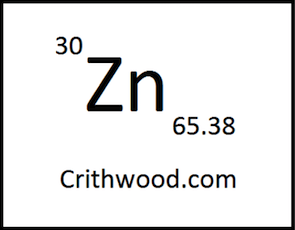
March 19, 2016
Want 200 µm galvanizing -- what thickness steel is needed?
Q. Regarding the zinc thickness in HDG procedure, I have a question: If there is a project which requires a minimum thickness of 200 microns, what thickness of steel should be chosen, considering a normal maintaining time in bath of 5 to 10 minutes. Non-blasted material and blasted material.
Thanks in advance.
- Timișoara, Romania
January 10, 2017
A. Perhaps the biggest influence on galv thickness is the steel chemistry, not immersion time and not steel thickness (though both these also influence coating thickness).
It seems wrong to choose a thickness arbitrarily then decide what thickness of steel to achieve it.
Surely you wish to decide what size steel to use (strength, load, purpose, etc), and then decide how to protect it, by knowing the environment the steel will live in, and the desired longevity.
Then you can arrive at a desired thickness of galvanizing.
But you'll perhaps also know that over-thick coating lead to all sorts of problems, like delamination, cracking, susceptibility to damage, etc.
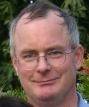
Geoff Crowley
Crithwood Ltd.
Westfield, Scotland, UK
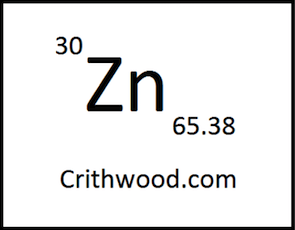
January 13, 2017
![]() |
A. Considering steel what you are Galvanizing normally, If you will take a 10 mm thick plate, shot Blast it both side, Galvanize it 445 °C; I'd hope to get desired 200 microns Zinc coating. Umesh DalelaGalvanizers & Consultants - Delhi, India January 18, 2017 First, many thanks for your answer. - Timișoara, Romania January 16, 2017 |
Q. Dear sir,
We have requirement for 140 micron coating thickness (Hot dip galvanizing)
Material used: Mild steel ASTM A572 GR. 50
Thickness of Steel: 5 mm
Item: Round Tapered Street lighting Pole .
Requested Coating is possible? Could you explain the procedure to achieve the thickness?
ALMEER INDUSTRIES - Ahmadi, KUWAIT
April 1, 2017
A. This steel should achieve about 100µ, but if your customer really wants 140µ (and many don't really know why they want it), then shotblasting the steel first will get about 140µ
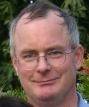
Geoff Crowley
Crithwood Ltd.
Westfield, Scotland, UK
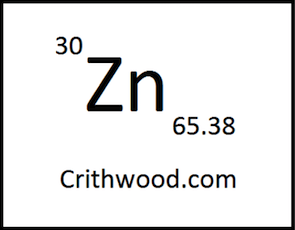
April 3, 2017
We love authoritative and confident replies, Geoff!
Regards,
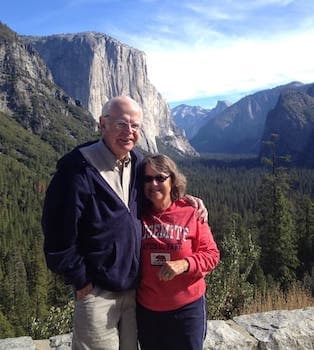
Ted Mooney, P.E. RET
Striving to live Aloha
(Ted can offer longterm or instant help)
finishing.com - Pine Beach, New Jersey
April 2017
A. Actually speaking the thickness of Zinc coating is well defined in respective specification. Even then sometimes a client asks for a higher Zinc coating, then: Shot Blast the entire job properly then Galvanize. Might be you get desired result.
Carry my regards.
- Delhi, India
April 6, 2017
Q. Hi, I'm new to this forum and seeking advice on achieving customer requirement.
We have a 2.5 mm thick steel plate but want to be able to achieve 150-170µm of galvanised coating to withstand category 5 environment weather condition. Our supplier is saying that can't achieve this but from what I'm reading, this might be achieved if they grit blast steel first and immerse the article longer than normal time (5-10 minutes).
What is your recommendations on achieving this thickness?
- Melbourne, Australia
March 19, 2019
A. Hi Peter. I'm not a galvanizer and don't have the answer. But to minimize lost motion when a knowledgable galvanizer gets here, I think they are going to say that it depends on the type of steel, so you might want to get back to us with the grade or composition of your steel.
Regards,
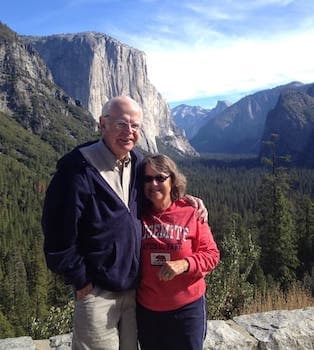
Ted Mooney, P.E. RET
Striving to live Aloha
(Ted can offer longterm or instant help)
finishing.com - Pine Beach, New Jersey
March 2019
A. Peter, your galvanizer (of whom you asked the question), is probably right. Getting that thickness of galv on 2.5mm thick steel is very difficult. While immersion time is a variable influencing thickness of coating, it's a pretty impractical one, and one that few galvanizers will even consider.
Silicon and phosphorous content of the steel are by far the biggest factors to be considered, and a lower influencing factor is surface profile (blasting). Most fairly plain carbon steels of 2.5 mm thickness will get about 45-55µ thickness. Blast that steel to SA2.5 (standard) and you might get 80µ. I don't think there's a practical way to get 150-170µ.
Where this often comes from is specifiers that don't know what they're talking about! They read something that says for example that 80µ will last 40 years. They also read that the life expectancy is proportional to thickness, so they use these two factors to reason that 160µ will last 80 years. Then they just specify that, without knowing that it might be impossible to achieve it. We know this from specifications for all sorts of weird numbers - 125µ, 135µ, 115µ, 155µ etc.
So your galvanizer that said "no, can't be done" is probably right. If design life for the steel fabrication exceeds the life deliverable by galvanizing, then there are other ways to get there, such as an organic coating (paint) over HDG. Or there are means such as metal spraying to get thicker coatings. But start at the spec. Likely it starts with someone making wrong assumptions that could be sorted out on paper before you go spending the money in failing something.
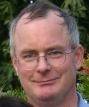
Geoff Crowley
Crithwood Ltd.
Westfield, Scotland, UK
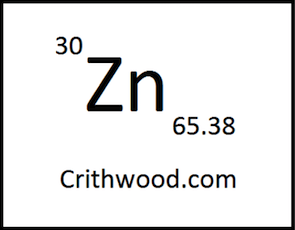
March 19, 2019
Q. Sir I want to do hot dip galvanization with spangles on 8-liter containers made of 0.5 mm thick sheet of MS. Coating should be maximum, up to 100 micron. Please advise in this matter.
Sanjay KumarSheet Metal - Ambala Cantt, Haryana, India
July 24, 2019
A. Sanjay,
You didn't state what might be more important, a MINIMUM zinc thickness, nor why you want spangles?
Without any minimum thickness stated, you probably could achieve this on your product by taking it to any galvanizer.
Spangle is an aesthetic issue, not a functional one. Generally the desire to have it is misguided, thinking that galvanizing is a beauty coating. It isn't. It might be best described as the ugliest coating available, but the one that delivers the most cost effective corrosion protection. So if you want to prevent rust - Galvanize. If you want great looks and beauty, do something else!
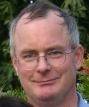
Geoff Crowley
Crithwood Ltd.
Westfield, Scotland, UK
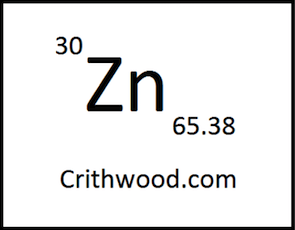
July 30, 2019
Q. Thanks Mr. Geoff for guiding me in this matter. Actually the product (container) to be galvanized has a top diameter of 9 inches, base dia. of 9 inches and height of 9 inches of MS sheet with total weight 1000 grams. We tried to galvanize this product in-house but the zinc coating is very thick with approximate deposit of 225 grams. Temp. during treatment was maintained at around 460 °C and if we increase the temp, the product gets dented. How can we get very thin zinc coating up to 80 to 100 micron or zinc deposit maximum up to 100 grams on our product? Thanks.
Sanjay Kumar [returning]Sheet Metal - Ambala Cantt, India
July 31, 2019
Q. Hello My Name is Arif Rahman. We have client requirement that galvanized thickness shall be minimum 87.5 micron for all steel part (except threaded part and some hardware as in state in ASTM A153 ). In ASTM A123 we have galvanized thickness minimum depends per steel base thickness. but, what maximum thickness can be obtained? lets say for less than 3 mm plate.
Arif HakimRekayasa Industri - Balikpapan, East Kalimantan, Indonesia
November 11, 2019

Q, A, or Comment on THIS thread -or- Start a NEW Thread