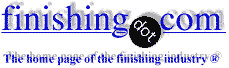
-----
How can we minimize/control galvanize coating thickness
for Engineers, Shops, Specifiers
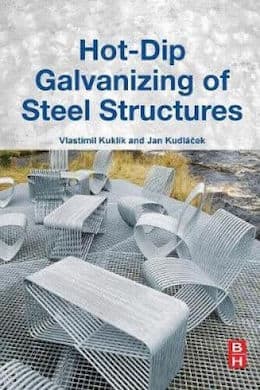
avail from eBay, AbeBooks, or Amazon
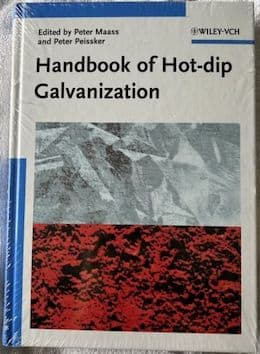
avail from eBay, AbeBooks, or Amazon
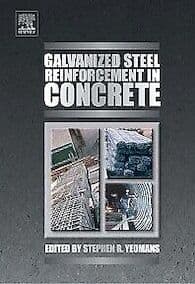
avail from eBay, AbeBooks, or Amazon
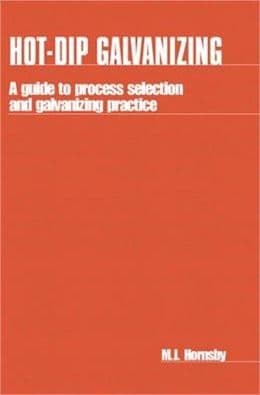
avail from eBay, AbeBooks, or Amazon
avail from Amazon
"User's Guide to Hot Dip Galvanizing for Corrosion Protection in Atmospheric Service" by NACE (1997 only rarely avail.)
avail from AbeBooks, or Amazon
(as an Amazon Associate & eBay Partner, we earn from qualifying purchases)
Q. MY NAME IS SABIR HUSSAIN. I AM WORKING IN A BIG GALVANIZING PLANT IN PAKISTAN. WE ARE GALVANIZING COMMUNICATION TOWERS, TRANSMISSION POLES, GRIDS,CABLE LADDERs, etc. PER MONTH PRODUCTION IS 500 TONS. OUR KETTLE SIZE IS 25 X 5 X 5 FEET. WE ARE USING DEGREASERS, HCl FOR PICKLING, AND FLUX.
WE HAVE PROBLEMS OF EXCESS ZINC COATING 8%, AND HIGH DRAWS (HARD ZINC & ASHES) 40 % OF ZINC CONSUMPTION. WE ARE USING DRYER OVEN AFTER FLUXING AT 40 °C.
PLEASE HELP US TO OVERCOME THESE PROBLEMS. WE WILL BE GRATEFUL FOR THIS KINDNESS
HEAD OF GALVANIZING - LAHORE, PAKISTAN
May 13, 2010
A. When you say 8% what do you mean? How do you define this?
Different people use different measures in this, some including residues (ash, dross) some excluding. Some measure against the black steel weight, some against white steel work. Depending on this, your 8% could be good, could be poor! What is your definition?
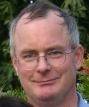
Geoff Crowley
Crithwood Ltd.
Westfield, Scotland, UK
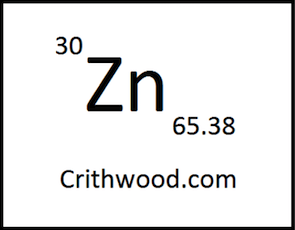
A. You want to reduce the Zinc Coating or pickup. Please try my way:
1. Keep flux Sp. gravity 1.20 and add 2% Glycerine. Add a Nickel base compound made by Soprine, Italy which reduces the alloy layer (follow their instruction).
2. Keep Zinc Bath Temperature 445 to 448 °C.
3. Get your steel to be galvanized tested.
4. In case you are not getting Soprine, then try nickel addition technique marketed by Rada Chemicals, Dubai (follow their instruction).
Hopefully your overall Zinc consumption will come down to 4-5%.
- Bhuj, Gujrat, India
----
Ed. note: please try to keep the public discussion of these nickel addition techniques generic rather than recommending specific suppliers. Thanks.
by International Agency for Research on Cancer
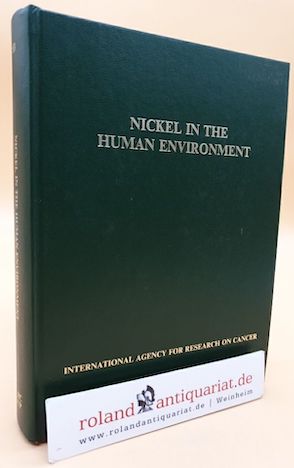
on eBay or Amazon
or AbeBooks
(affil link)
A. Sabir,
I assume you work for PECO. Under UNIDO I worked for your company three times (about a month each time) and we were able to reduce zinc usage about 25% (lowering total product cost by about 9%). The last time I was in Lahore was about 15 years ago during the first Gulf war. Over time you have obviously lost this technology. Now there may be a safety issue for Westerners in Pakistan.
I caution the use of nickel compounds in the flux because of safety issues because nickel compounds are known to cause lung cancer. There is a delay time from nickel exposure to the onset of lung cancer of 5 to 50 years (according to one printing of the CDC handbook).
A flux density of 1.20 g/mL is a baumé of 24.2 which is clearly the European way to galvanize not the North American way. I much prefer the North American way.
You say your zinc consumption is 8% which IS high for your operation. Be aware that a zinc consumption of 4 to 5% may or may not be good depending on the thickness of the steel (e.g. the thicker the steel the lower the surface area to galvanize). I have clients that have nearly 3% GZU.
I assume Mr. Dalela is recommending glycerine at 2% as a wetting agent. There are MUCH more effective wetting agents that are effective at about 0.03%. I am not sure if pyrolized glycerine products would be healthy or not.
Regards,
Galvanizing Consultant - Hot Springs, South Dakota, USA
A. Dear Sir.
To minimize zinc coating on steel there are many aspects to see such as:
1 ) Pre Treatment process of materials.
2 ) zinc bath temperature.
3 ) silicon contents in your raw materials.
First check the silicon content in your materials.
Check specific gravity of your Flux, and Quality of your Acid.
Keep zinc temperature in between 450 °C and 455 °C.
Hope this will help you to get your result.
Gunatit Builders

Manjalpur, Vadodara, Gujarat
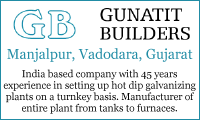
A. Hello,
1. Get the iron content checked for your flux.
2. Add inhibitors to your acid it can be that steel is getting over pickled. Zinc is directly proportional to the surface area.
3. What is the withdrawal rate for your steel
4. Frankly speaking I don't think 40 percent dross and ash in composite is bad.
Pickup is high but you need to mention what tonnage you are doing for material with thickness 3 mm and below.
towers - kolkata, India
by Kuklik & Kudlacek
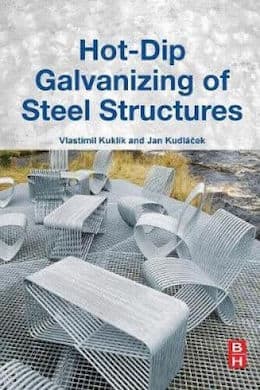
on eBay or Amazon
or AbeBooks
(affil link)
A Guide to process Selection & Galvanizing Practice"
by M. J. Hornsby
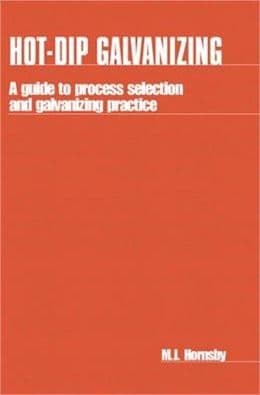
on eBay or Amazon
or AbeBooks
(affil link)
Q. The amount of zinc coating required is only 87 micron (610 gms/ sq.m) but we end up coating 100 microns (on an average) and many time ends up in 120 micron approx. What are the ways to reduce the zinc coating
the furnace temperature maintained is 455 °C - 460 °C. Let me know if you need more details
Thanks in advance. Expecting a quick reply
student - Ahmedabad, Gujarat, India
April 14, 2011
A. You don't really give enough info to be definitive suggestions to help.
But your temperature seems a bit high to me. 450 °C seems better, but that might depend on the things you haven't told about.
What flux? What drying? What steel? Ni or not? Flux type? Steel/material types? Jobbing or manufacturing? Vertical dipping or mixed? Steel thickness? Withdrawal speed?
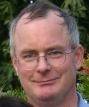
Geoff Crowley
Crithwood Ltd.
Westfield, Scotland, UK
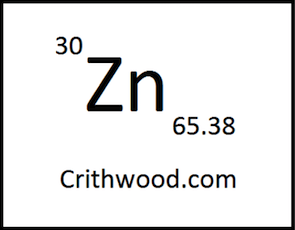
Q. To give you more information (follow up of previous question)
Thickness of plates Time in zinc kettle for 87 micron
3 to 4 mm 1 min 30 sec
5 to 6 mm 2 min
14 to 16 mm 2 min 30 sec
18 to 20 mm 2 min 45 sec
I don't think these were scientifically derived. It is based on time study and trial and error. Are these values correct for corresponding thickness of plate or is there a way to determine the time of retention in zinc kettle.
- Ahmedabad, Gujarat, India
Q. Sorry but here I'm providing some more info.
the process we follow is (though obvious)
1) Degreasing (No rinsing after this stage)
2)Pickling with HCl
(sp. gravity 10 Be to 28 Be, Iron Content < 120 gms/litre)
Acid inhibitor is also used
3) Rinsing (pH 2 to 5)
4) Pre Fluxing (ACN approx. 1.5)
5) Heating in oven at 65-70 °C
6) Quenching
7) Di Chromating
The steel is used for transmission towers (this may give you an idea about the length). Thickness I have mentioned in my previous post. The material is dipped in the Zinc Kettle in batches of 10-20 based on the size of material. It is done through Overhead cranes. The beams are allowed to hang vertically from the crane. once the bottom on the zinc kettle is touched, the beam are lowered to make it horizontal.
We don't follow any rate of removal. You may assume the rate of removal that can be achieved with overhead cranes. Let me know if you need more details. Your response will be highly helpful. thanks in advance.
student - Ahmedabad, Gujarat, India
April 19, 2011
A. Only thing I can add is that your withdrawal speed (by crane) should be about 1 meter per minute vertical speed.
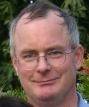
Geoff Crowley
Crithwood Ltd.
Westfield, Scotland, UK
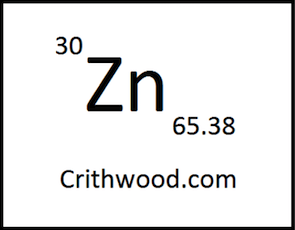
A. Sirs:
ACN is now replaced by a much better term which is ACNV. ACN is ammonium chloride divided by zinc chloride. ACNV is the volatiles (ammonium chloride) divided by the sum of the low volatiles (zinc chloride plus iron (II) chloride plus sulphate, if present). By using ACNV (especially in the presence of high iron (II) or high sulphate a much better result is attained.
While in Lahore I taught a fellow to do a distillation test for ammonium chloride, which frankly is too complex. I now use the "bake and shake" method which is based on heat of solution and density attained by dissolving a dried/weighed sample of flux in a specific volume of distilled water. These methods are easy and give excellent ACNV results directly.
Regards,
Galvanizing Consultant - Hot Springs, South Dakota, USA
Q. I just found that the retention time stated in my previous posts are not strictly followed. We are planning to implement low cost automation for the same with the help of PLC. I would like to get your advise on what should be the retention time to get a thickness of 87 microns (630 gms/ sq.m). We galvanize transmission towers with angles ranging from thickness 4 mm to 20 mm.
We work under the following settings.
1) Degreasing (No rinsing after this stage)
2)Pickling with HCl
(sp. gravity 10 Be to 28 Be, Iron Content < 120 gms/ litre)
Acid inhibitor is also used
3) Rinsing (pH 2 to 5)
4) Pre Fluxing (we mix Ammonium chloride and Zinc chloride in the ratio 60:40 while prepare a new solution. So can I assume the ACN is 1.5. Iron content < 50 gms/litre)
5) Heating in oven at 65-70 °C (but 50% of the production is bypassed this stage. There is time gap of 15 mins between prefluxing and zinc kettle bath immersion when ever bypassed. So there is no dipping of pre flux while dipping the material in zinc kettle)
6) Zinc kettle (455-465 °C)
6) Quenching (60 °C)
7) Di Chromating
We use flux blanket and dross in done once in 2 weeks.
The current level of zinc consumption (in terms of total production)are 4.12% (ZINC CONS. AFTER EQU.) and 4.43% (TOTAL ZINC CONS. IN %). The split up of the above
Dross 0.38 %
Ash .48% (No ash box. What is ash box ?)
Pick up 3.56% (we calculate pick up by subtract dross and ash from total consumption. Is that right?)
Our target is to bring done zinc consumption to 4% (after equ.)
In brief
1) Kindly suggest ways to bring down overall zinc consumption.
2) what should be the ideal retention time and ways to measure it (from which pt to which pt)
3) How to maintain a constant rate of retrieval with overhead cranes.
Let me know if you need more information.
Thanks in advance. Expecting a fast reply.
Regards
- Ahmedabad, Gujarat, India
May 6, 2011
Q. A small clarification on my previous post.
I have mentioned that the iron content in flux is less than 50 gms/lit. the correction is it is 5 gms/lit, after conversion it is less than 0.45%.
The iron content in pickling tanks are maintained less than 5%
- Ahmedabad, Gujarat, India
When you find the way to improve your zinc pickup, please publish it here.
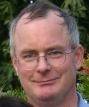
Geoff Crowley
Crithwood Ltd.
Westfield, Scotland, UK
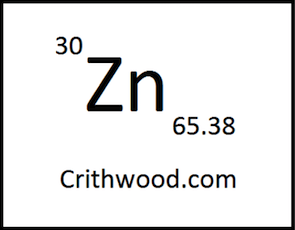
Q. I thought you could help me on that but I'll surely post it here if we find a breakthrough. As of now, we are trying to play with retention time (the time the material is immersed in the zinc kettle)to reduce the coating thickness.
I posted a big question with all details to find out whether we are doing some basic mistake is the process.
I would also like to know whether achieving Zinc consumption of around 3.5% (as a % of galvanized steel) is really possible. Have you come across any plants which work in such range.
As you people seem to have a vast experience, your comments will be highly valuable.
- Ahmedabad, Gujarat, India
May 10, 2011
A. Zinc pickup is so dependent on material type (as well as all the process parameters) that comparison is difficult.
I think 3.5% might be possible in a plant coating the same material all the time, and heavy sections.
We do jobbing work where no two days material is the same, so our consumption varies greatly.
I know of plants doing 10% and others doing 4%.
But each plant will have its own target based on experience with that material type they can sell.
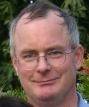
Geoff Crowley
Crithwood Ltd.
Westfield, Scotland, UK
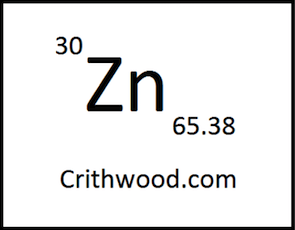
A. Dear Raghul,
Zinc pick up rate (%) is very dependent on your steel thickness. Let just say you have 2 items, same size & design, only difference is that A is 1 mm thick and B is 2 mm thick. Their surface area is the same, but weight of A is only half of B. Therefore, even though they have the same zinc coating thickness, zinc pick up rate (%) for A is double of B's.
If your plant is only galvanizing items of above 8mm thickness, you can easily get a zinc pick up rate of below 3%. The thicker the item, the lower the zinc pick up rate.
Also, iron in pickling bath can help speed up your pickling process. You can refer to Kleingarn graph.
Regards,
- Selangor, Malaysia
Thank you all. The Information provided was very useful
student - Ahmedabad, India
A. The zinc consumption (pick up) is dependent on the thickness of the item galvanized. for a 6 mm thick angle and a coating of 610 gm , the pick up is 2.6%, and for an 8 mm item it is 1.9%. In actual practice to have a minimum average coating of 610 gm , the actual coating will be 630-650 gm i.e., 2.8% for 6 mm thick item. we galvanize items from 2 mm to 20 mm thick and every month, the theoretical pick up based on the surface area galvanized depending on the thickness is calculated and the actual pick up is compared. The ash being 16% of gross Zinc and dross as 5%. it is possible to achieve a gross zinc consumption of 4% with a pick up of 2.75% and balance 1.25% as Dross and ash. dipping time and temperature of the bath is to be controlled.
Hemant Khaitangalvanizer - Kolkata, India
July 5, 2011
(You're on the 1st page of this topic) Next page >

Q, A, or Comment on THIS thread -or- Start a NEW Thread