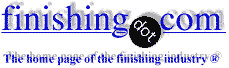
-----
How can we minimize/control galvanize coating thickness
< Prev. page Next page >
for Engineers, Shops, Specifiers
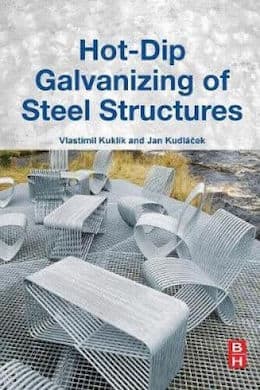
avail from eBay, AbeBooks, or Amazon
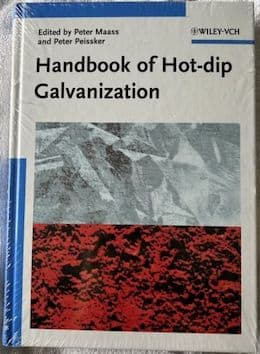
avail from eBay, AbeBooks, or Amazon
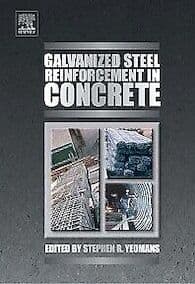
avail from eBay, AbeBooks, or Amazon
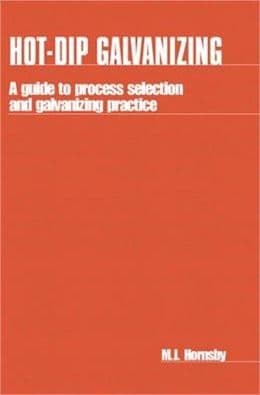
avail from eBay, AbeBooks, or Amazon
avail from Amazon
"User's Guide to Hot Dip Galvanizing for Corrosion Protection in Atmospheric Service" by NACE (1997 only rarely avail.)
avail from AbeBooks, or Amazon
(as an Amazon Associate & eBay Partner, we earn from qualifying purchases)
Q. Most of our galvanized steel has considerably high coating thicknesses according to the standard BS EN ISO 1461:2009. But also some items have a good coating thicknesses (just slightly greater than the standard values). I heard that one reason for high coating thicknesses is silicon content of the steel. My question is, is it a good decision to buy a silicon analyzer to measure Si content prior to galvanize?
Prabath Gunasekara- Colombo, Sapugaskanda, Sri Lanka
October 15, 2012
A. Si is indeed one of the factors that affect galvanizing thickness, but if you knew what it was prior to processing, what would you do differently?
The only time I think this becomes relevant is in a manufacturing plant where in-house galvanizing is done. Then there is control on the purchase of the steel, and a specification for the steel can consider the impact on the galvanizing cost.
In our case the many hundreds of customers (we're very much a jobbing plant) make their own decisions, and I doubt they ever consider the impact of their steel chemistry on galvanizing. They do not buy steel to suit galv.
So, even in jobbing, if you were to measure Si content (and that's not the exclusive impacting element), then you find Si % that suggests it will be a heavy (thick) coating, what to do next?
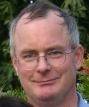
Geoff Crowley
Crithwood Ltd.
Westfield, Scotland, UK
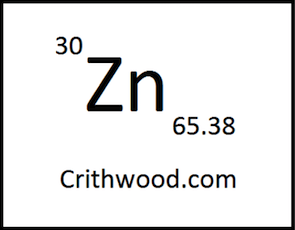
October 18, 2012
Q. After knowing the Silicon content, can't we reduce the bath temperature & dipping time to reduce the coating thickness? By reducing bath temperature, we can reduce the reaction rate. But fluidity of the Zn melt is also reduced with temperature, so that we can reduce the dipping time. Is it not possible?
Prabath Gunasekara [returning]- Colombo, Sapugaskanda, Sri Lanka
October 19, 2012
A. Hi
According to your discussion, I think that an important thing in coating size in galvanization is to factor:
1. flux
2. pick up speed
We in our project with a little change in flux composition and daily control of its several material %, such as Fe, and its gravity, reduce coating size about 20 micron off, but coating size depending on ST of steel and its pick up speed is variable. However, I think don't use Ni in flux, please control its Fe and its temperature about 40-60 °C. In addition you should pick up your staff entirely.
- Nowshahr, Iran
October 25, 2012
----
Ed. note: Sorry, we couldn't figure out the last 5 words of this reply.
October 27, 2012
? Sir:
I have some questions relating to your response:
What do you mean "...a little change in flux composition..."
What change(s) did you make?
What is "...ST of steel..."
I do not know this term.
"...don't use Ni in flux..." I agree, did you try this?
What is: "...Pick up your staff entirely..."
Regards,
Galvanizing Consultant - Hot Springs, South Dakota, USA
October 29, 2012
A. Sir:
By "pick up your staff entirely" Do you mean get the workers out of the kettle area during the time the steel is entering the kettle? If "yes" then the usual way to protect the workers (from molten zinc splashes) is to have a vertical moveable "wall" with a safety glass window. The glass usually has wire reinforcement.
Regards,
Galvanizing Consultant - Hot Springs, South Dakota, USA
Galvanizing withdrawal speed
Q. WHAT SPEED IS REQUIRED OF OVERHEAD CRANE FOR WITHDRAWAL FROM ZINC BATH?
SUNIL KUMAR MOKHRA- PANIPAT,HR, India.
March 6, 2014
A. Hi Sunil. Further up the page Geoff has already said 1 meter per minute, so please try to phrase your question as part of the ongoing dialog. Or you may wish to continue the discussion on letter 47904, "Speed of crane for hot dip galvanizing", where Thomas Cook seems to say that it can depend upon what flux is being used (I have no galvanizing experience, so I'm not sure that I am correctly interpreting his posting).
Regards,
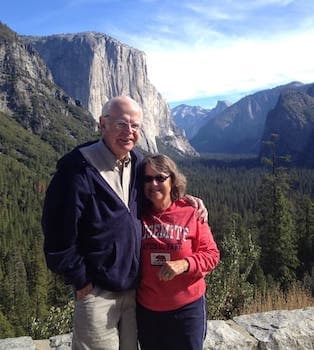
Ted Mooney, P.E. RET
Striving to live Aloha
(Ted is available for instant or longterm help)
finishing.com - Pine Beach, New Jersey
March 2014
A. Hi Sunil. That's true. Mr. Geoff informed earlier for withdrawal speed of materials from zinc bath should be 1 mtr / min ... you can reduce up to 0.8 mtr / min.. Generally for Galvanizing plant we prefer two speed EOT Crane. Dipping should be fast and lifting should be slow.
Ilesh G VyasGunatit Builders

Manjalpur, Vadodara, Gujarat
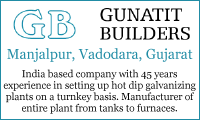
April 15, 2014
Q. Sir,
we galvanize iron and steel of different shapes and sizes. The coating thickness of our galvanized product is high (above recommended coating thickness), what do you think is responsible for this?
- shagamu, nigeria
October 16, 2014
Hi Jinadu. As you see, we've appended your inquiry to a thread where the subject has been discussed at great length. But if there is something you don't understand or need clarification on, please get back to us. Good luck.
Regards,
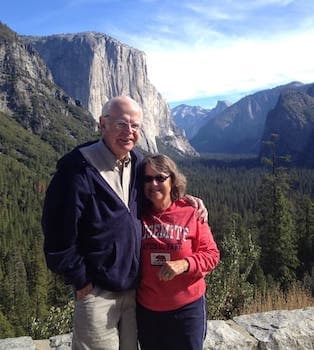
Ted Mooney, P.E. RET
Striving to live Aloha
(Ted is available for instant or longterm help)
finishing.com - Pine Beach, New Jersey
October 2014
Zinc consumption in hot dip galvanizing
Q. I will like to know the quantity of molten zinc that will be consumed for a ton of steel, or how calculate to zinc consumption in hot dip galvanizing
Bola Jinadu- Sagamu, Ogun State, Nigeria
December 17, 2014
A. In order to determine the zinc usage per ton of galvanized work you need two pieces of information: (1) the surface area, and (2) the thickness of the zinc coating. You don't need any more information than this and you cannot determine the usage without both of these pieces of information. The math is pretty simple.
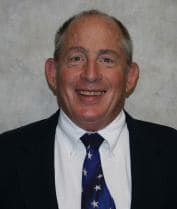
Tom Rochester
CTO - Jackson, Michigan, USA
Plating Systems & Technologies, Inc.

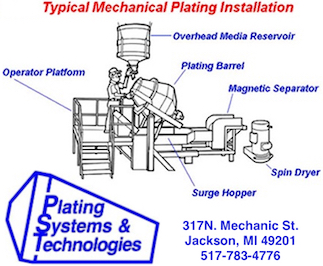
December 18, 2014
A. Sir:
Average zinc usage 40 years ago in North America was about 10% (200 kilograms zinc for every 2,000 kg of galvanized product), Now the average zinc usage is about 5% (100 kg zinc for every 2,000 kg of galvanized product).
Regards,
Galvanizing Consultant - Hot Springs, South Dakota, USA
December 19, 2014
A. While knowing the thickness of the coating and the surface area will allow the calculation of zinc consumed and reporting to the coating, this isn't the whole story. You do need more information.
If you do a zinc mass balance on zinc in a galvanizing plant, it becomes apparent that Zn is reporting, in significant quantities to a variety of other places that the coating.
These include: jigs, acid, dross, ash, rinse water, fume particulates. The quantity reporting to all these undesired places is what can differentiate a profitable plant from another, and can amount to 20-40% of the weight of Zn in the coating. It's highly variable and influenced by many factors.
The numbers Dr Cook has quoted are the total consumption including these sidestreams.
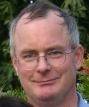
Geoff Crowley
Crithwood Ltd.
Westfield, Scotland, UK
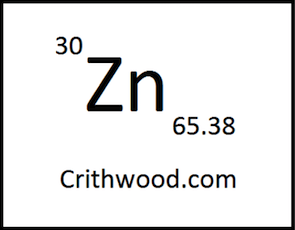
December 20, 2014
A. Galvanising is a quite complex topic, as the zinc forms a complex intermetallic structure with the base steel. the amount of zinc on a steel product also varies with the time it is in the galvanising tank, but as a rule of thumb, hot dipped galvanised steel has a zinc thickness of between 40 and 100 microns (1.5-4 mils). This compares with general electroplated zinc coatings of approximately 0 to 25 microns (0 to 1 mils).
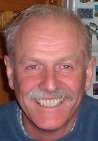
Trevor Crichton
R&D practical scientist
Chesham, Bucks, UK
February 16, 2015
Q. Good morning sir.
I'm a student and I will do research about galvanizing ...
My question: how does the galvanizer calculate zinc consumption?
Thanks
Faisal
- Jakarta. Indonesia
November 30, 2015
Hi Faisal. We try our best to offer help to students when they need it, without doing their homework for them. Your question is the topic of most of the 30+ postings on this page, so please slowly carefully review the page and
1. Offer detailed followup questions about the parameters you didn't understand, or (even better)
2. Offer a hypothesis about calculating zinc consumption, based on what you read here, and ask for the readers' comments and suggestions on your hypothesis. That would really be taking advantage of the opportunity offered to you. Thanks and good luck!
Regards,
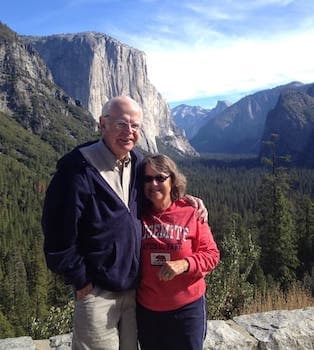
Ted Mooney, P.E. RET
Striving to live Aloha
(Ted is available for instant or longterm help)
finishing.com - Pine Beach, New Jersey
December 2015
----
Ed. note Mar. 2018: It's okay, folks. Although 9 out of 10 students blow off our suggestions when we don't immediately supply the answers to their homework questions, 1 out of 10 does appreciate them, and that's a pretty heartening thing :-)
Q. Sir,
I have started my Galvanization plant, its been 6 months. The constant problem that I am facing is black patches on the material immediately after taking it out of the zinc bath.
Also, a high thickness of zinc coating on MS channels, angles, flats, plates etc. (materials thickness of 5 to 25 mm)
Kindly suggest some measures to be taken to eradicate the issues.
Thanking You,
- Guwahati, Assam, India
June 7, 2016
A. Some photos of the black patches would help diagnose this. It could be one of several issues and pictures might help.
Are the "black" patches bare steel (ungalvanized)? If so this might be under pickling. Are the patches on top of the zinc? Might be excessive aluminium.
When you say "too much" zinc, what thickness are you getting, and what dipping speed, angle, zinc temp? flux type, temp of flux? strength of flux, chemistry of flux? additions in the zinc. All of these have an influence, and without these parameters only wild guesses can be made.
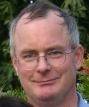
Geoff Crowley
Crithwood Ltd.
Westfield, Scotland, UK
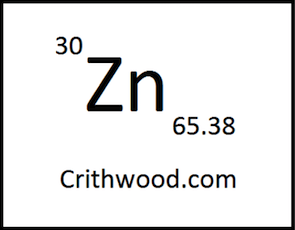
June 18, 2016
Q. Hi All, I will jump into my question directly.
We galvanize Cable Trays (3-Mtr length) in my Galvanizing plant.
Out Plant depth is 3.5 Mtr, so we dip the material in a vertical position to increase production.
The problem we are facing is that the thickness between the top and bottom is always different by around a value of 20 Microns. How to avoid this difference or reduce it to the max?
I know horizontal dipping will solve this issue but that will reduce our production capacity.
Is there any solution to this? Your help will be much appreciated.
- Chennai,Tamil Nadu, India
October 10, 2018
Q. How to reduce galvanized coating thickness on 2 mm metal sheet.
Regards,
- HYDERABAD TELANGANA India
October 12, 2018
A. Hi Venkata. We appreciate that you have identified your product as 2 mm metal sheet; nonetheless, the question remains vague :-(
Is this a coil reel-to-reel line where some sort of wipers might be applicable, or is this post-galvanizing of discrete components? How thick are the present coatings, and how thick would you like them to be? Is there any chance that electrolytic zinc plating could get you the thickness you desire?
Regards,
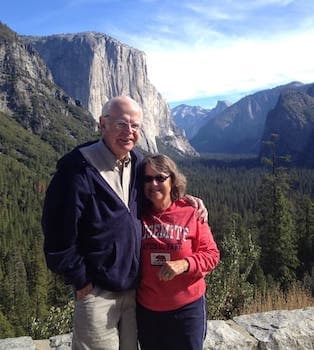
Ted Mooney, P.E. RET
Striving to live Aloha
(Ted is available for instant or longterm help)
finishing.com - Pine Beach, New Jersey
October 2018
Galvanizing thickness is varying
December 15, 2018Q. Dear Sir,
Greetings. We have a Hot Dip Galvanizing Plant in the State of Qatar set up in the year 2015.
Details of the Plant as followa:
1) Kettle Size: Depth 1.8 Meter x Width- 1.2 Meter x Length- 7.0 Meter
2) Zinc Grade- 99.995 SHG, Lead, Aluminium Alloy
3) HCl 31-33% Conc.
4) Degreaser
5) Rinsing
6) Flux Tank-Double Flux (pH- 4.5%)
5) Heating Oven- 60-90 °C
(Technology from Ani Metals-Turkey).
The Problem is High Zinc Coating varying from 100 Microns to 250 Microns.
Thickness of Materials are 1.0 mm, 1.2 mm, 1.5 mm and 2.0 mm. We are buying Steels from the Top Mills around the Globe like- Jindal Steel, Boa Steel, Benxi Steel, Arcelormittal, TAT Metals, etc., where the quality is not compromised, definitely Silicon content is controlled to 0.01% to 0.03%.
Our last report on the Kettle composition are as follows--
1) Zinc- 98.99%
2) Lead- 0.2%
3) Iron and Aluminium -0.05%
Please advise the reason for high coating on our steels. Best regards,
Sunil Sharma- Qatar
A. Sir: Looks like you are a sheet galvanizer. Are you sheet to sheet or continuous coil to coil? Does the sheet go cross-wise through the kettle or length-wise? Is your zinc kettle iron or ceramic? What is the temperature of the zinc? What is the time the steel is in the zinc? Most modern sheet galvanizers use gaseous flux 5% H2 and 95% N2. Have you heard about "Galfan?" I wonder if it may work better for you. From what country to you buy flux? I have only moderate information on sheet galvanzing.
Regards,
Galvanizing Consultant - Hot Springs, South Dakota, USA
January 6, 2019
Dear Mr. Sunil.
As mentioned by you, it seems that you are having sheet metal galvanizing job.
Please let us know if it's continuous process or batch-wise process. If it's continuous then coating seems too high; however, if you have batch-wise process, your coating should be around 75 to 90 microns.
Tell us your immersion of materials speed as well lifting speed and also tell us your working temp.
We will help you to solve the problem.
Gunatit Builders

Manjalpur, Vadodara, Gujarat
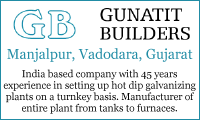
Q. I want to calculate or want to know how the quantity of zinc varies per Ton of production based on micron thickness. For example I know that it takes 5 kg of Zinc for 100 kg of Galvanized structure but this is at what micron coating thickness? How to know the variation of amount of zinc consumed per Ton based on Galvanizing micron thickness?
Vishal PatilManufacturing - Mumbai, India
February 25, 2019
A. You need to know the surface area per unit weight. With that, it is simple arithmetic. Without that it is just guesswork.
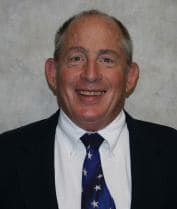
Tom Rochester
CTO - Jackson, Michigan, USA
Plating Systems & Technologies, Inc.

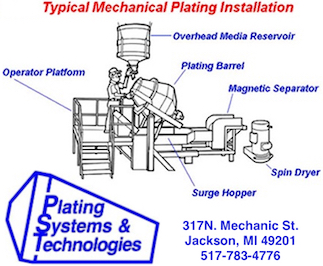
February 26, 2019
----
Ed. note: Tom is the author of "Surface Area Formulas and Tables -- A Resource for Surface Finishers"
Ok thank so much TOM. I will calculate surface area per unit weight of Plates, C Channels, Angles, H and I Beams, Tubes, Bars, of some sample dimensions and then take a average of it.
Manufacturing - Mumbai, India
February 27, 2019

Q, A, or Comment on THIS thread -or- Start a NEW Thread