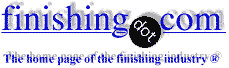
-----
Relationship between thickness of hot dip galvanizing and salt spray test results
2007
dear sir:
We are using high amount of hot dip galvanized pieces such as screw,nut ...,we have some problems to fastening hot dip galvanising screw & nut together regarding those thickness of galvanizing ,is it possible we have some parts with low thickness of galvanizing such as 15-25 microns but resistance to salt spray test same as parts which have 40-45 microns zinc thickness? if it is possible to dispatch to us a table that shows relation between thickness of zinc hot dip galvanizing and salt spray test resistance.
technical manager - Zanjan, Iran
2007
It's my opinion that the salt spray test is inappropriate for hot dip galvanizing.
My reasoning is that the protection galvanizing affords is as a result of the oxide layer on the surface of the zinc coating. If the zinc didn't oxidize, it would soon be all gone, as it's quite reactive.
Salt spray test abrades the oxide layer, so removing the protective layer, exposing the pure zinc, accelerating the corrosion.
Salt spray tests bear no relation to reality in this case. That is they do not mimic real life. And that's what such a test should do - it should show in short time, what happens in real life in the long term. For galvanized surfaces salt spray tests suggest a shortened life not actually experienced in life.
But to your question about thinner coatings...
You could try centrifuge galvanizing. As short an immersion time as possible should also be used.
For threaded components where both the internal and the mating external thread are of galvanized material, its quite common to have only one surface galvanized. To do this, either the bolt thread or the nut thread is cut (or tapped) after galvanizing, removing the coating.
The uncoated surface is protected by the coated mating surface.
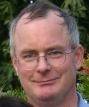
Geoff Crowley
Crithwood Ltd.
Westfield, Scotland, UK
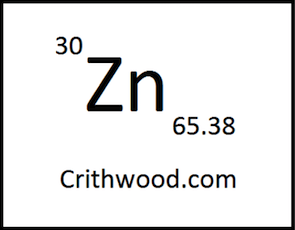
May 1, 2008
CAN YOU SUPPLY ANY COMPARATIVE INFORMATION BETWEEN 60G AND 90G IN GALVANIZED HOT DIPPED PRODUCT? HOW MANY HOURS DIFFERENCE IN BREAKDOWN OF COATING PROTECTION?
THANKS,
Hi, Don.
Real life is directly proportional to thickness for sacrificial coatings. Because a G90 coating is 50% thicker than a G60, it can be expected to last 50% longer. Per the previous Q&A, salt spray testing is not an appropriate test for galvanizing because it doesn't really indicate anything.
Regards,
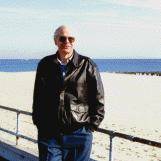
Ted Mooney, P.E.
Striving to live Aloha
(Ted can offer longterm or instant help)
finishing.com - Pine Beach, New Jersey
I have a hot dip galvanizing plant & I want to reduce the thickness of zinc coating ... what method I can use or what material I should mix in order to achieve a thin coating.
KUSHAL GUPTA- Dehradun, Uttranchal, India
June 9, 2009
Hi, Kushal. What thicknesses are you currently getting, and what methods and what mix are you using? Is the centrifuge galvanizing and the short immersion time which Geoff has suggested appropriate or inappropriate for your situation? Let's try to keep the discussion moving forward instead of starting over :-)
Thanks.
Regards,
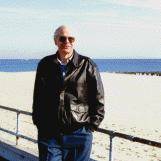
Ted Mooney, P.E.
Striving to live Aloha
(Ted can offer longterm or instant help)
finishing.com - Pine Beach, New Jersey
June 9, 2009
June 14, 2009
If you need to reduce the zinc coating to 15 microns you will have to electro-galvanise. The corrosion protection will depend on the passivation and sealer you use.
Best regards,
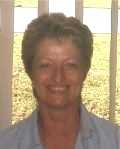
Trudy Kastner
electroplating service - Durban, KZN, South Africa
WE REQUIRE COATING OF 50 - 60 MICRON, BUT OUR COATING STAYS 120-150 MICRON)
SUNIL KUMAR MOKHRA- PANIPAT ,Haryana & INDIA
August 11, 2009
Dear All,
I wanted to know about the relation ship in between thickness of mild steel and the galvanizing film thickness i.e., to be provided for the same, especially in marine atmosphere. For example I am having mild steel angles, 30 x 30 x 3 mm for cable trays and supports installation in ships . What should be the micron thickness of galvanizing film to be provided to avoid corrosion.
- Cochon, Kerala, India
October 2, 2009

Q, A, or Comment on THIS thread -or- Start a NEW Thread