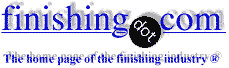
-----
Zinc Plating / Electrogalvanizing Mild Steel Wire

for Shops, Specifiers & Engineers
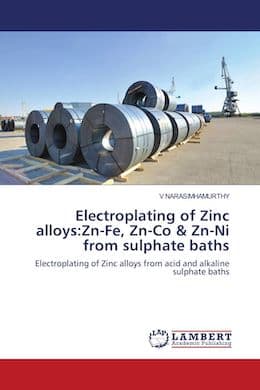
from eBay, AbeBooks, or Amazon
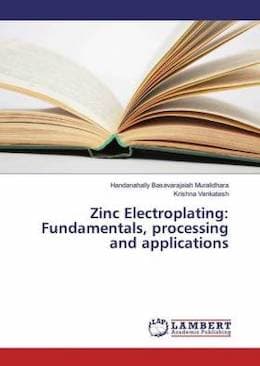
from eBay, AbeBooks, or Amazon
"Alkaline non-cyanide zinc plating with reuse of recovered chemicals" by Jacqueline M. Peden (1994)
from (U.S. EPA)
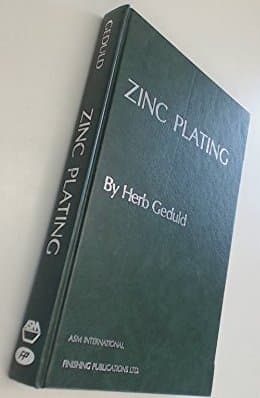
from eBay, AbeBooks, or Amazon
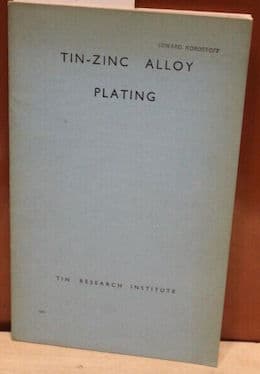
from eBay, or AbeBooks
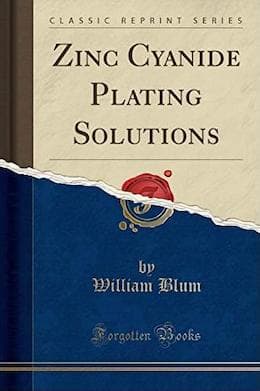
from eBay, AbeBooks, or Amazon
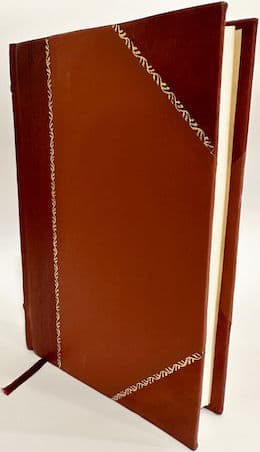
from eBay, AbeBooks, or Amazon
(as an Amazon Associate & eBay Partner, we earn from qualifying purchases)
Q. We are making wires for staple pins --
Which option is better:
1. drawing 1.25mm MS to 0.55 mm , then electroplating.
2. electroplating then draw 1.25 mm to 0.55 mm
and what should be the weight of zinc coating?
Engineer - karachi Pakistan
February 17, 2024
A. Hi Sajjad,
I have seen silver plating on copper wire, and tin plating on copper wire, and in those cases drawing it down after plating was certainly better, economically, logistically, and probably quality-wise as well. I think the general answer is always plate before drawing down if it works :-)
Unfortunately, I have zero expertise in wire drawing, and no experience as to whether zinc plating on steel wire can be reliably drawn down -- we'll have to wait for someone who knows :-(
As for the weight of the zinc plating, that depends on the application, and I'm not quite sure what staple pins are; but specified zinc plating thicknesses in standards such as as ASTM B633 range from 5 microns to 25 microns. If you're talking office staples, even 5 microns may be more that you need.
Luck & Regards,
Ted Mooney, P.E. RET
Striving to live Aloha
(Ted can offer longterm or instant help)
finishing.com - Pine Beach, New Jersey
Q. In production of Staple wire, if we draw the wire after electroplating problem is - drawing lubricant may adhere to the surface and can impact gluing operation at the time of staple mfg.
Sajjad Soomro [returning]Engineer - Karachi, Pakistan
February 20, 2024
⇩ Related postings, oldest first ⇩
Q. I do electroplating of wire in continuous process. My chemical is prepared with 300 gm/ltr of zinc chloride and 140 gm/ltr of ammonium chloride. Both these chemicals mixed with each other in 2000 ltr tank.
It's gravity is 32 degrees.
Am I doing the right galvanizing?
Give suggestions.
wire manufacturer -Jammu and Kashmir, India
2003
A. Does it work?
Do you get what you want?
If the answer to both is "yes", then you are doing it right. If not, you are doing it wrong.
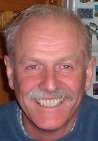
Trevor Crichton
R&D practical scientist
Chesham, Bucks, UK
Trevor is not being a "wise guy", cousin Mohit, but is emphasizing that "performance specifications" are more important than "process specifications". If the work is satisfactory, no need to worry about whether the process is satisfactory ... it is :-)
Regards,
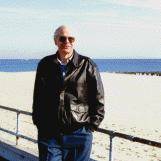
Ted Mooney, P.E.
Striving to live Aloha
(Ted can offer longterm or instant help)
finishing.com - Pine Beach, New Jersey
⇦ Tip: Readers want to learn from your situation;
so some readers skip abstract questions.
Q. 1. Minimum and maximum distance between anode to cathode.
2. Why to maintain this distance?
3. What is the principal to maintain proper distance.
4. How it works.
5. What is the purpose of using boric acid and how it works.
Can anyone suggest regarding this matter?
2006
wire - Dubai, UAE
A. There is no real minimum or maximum anode-to-cathode distance. Whatever suits your condition should work. But in general terms, the larger the distance, the more solution resistance, so the more wasted power and heat. But the cathode must never touch the anode, and for shapes that are more complicated than wire, you may want a bit of distance so that the ratio of distance from the closest point to furthest point is as close as practical to unity.
As electrolysis proceeds, some water will be converted to H2 and 2OH-. The H2^ evolves as a gas and the OH- tends to raise the pH of the solution. Boric acid is a buffer to help stabilize the pH.
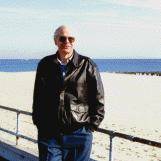
Ted Mooney, P.E.
Striving to live Aloha
(Ted can offer longterm or instant help)
finishing.com - Pine Beach, New Jersey
Q. Thank you Mr. Ted Mooney,
As you replied me when the pH of potassium chloride zinc plating bath increases we should add boric acid as buffer to maintain the pH. But why don't we use the same (boric acid) for ammonium chloride zinc plating bath.
- Dubai, UAE
A. No, buffers are to stabilize the pH rather than to raise or lower it.
Re. ammonium chloride: hopefully a supplier will offer a more authoritative response here, but pending that, ammonium chloride is itself a buffer, eliminating the need for boric acid; I believe that ammonium chloride baths operate at higher pH than potassium chloride baths.
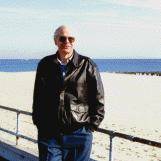
Ted Mooney, P.E.
Striving to live Aloha
(Ted can offer longterm or instant help)
finishing.com - Pine Beach, New Jersey
A. Mohanraj, use muriatic acid (HCl) diluted 50% with water to adjust pH down. pH of this bath should be 5.0-6.0. Boric acid is a buffer. Should be in a range of 3.5-6.0 oz/gal. Boric acid helps prevent burning of the parts.
In an ammonia/potassium bath, the ammonia chloride replaces the boric acid. The mixed ammonia ⇦ on eBay or Amazon [affil link] /potassium bath does allow higher current densities to be applied to the part. There are benefits with both baths. Temperature is also important when zinc chloride plating. Should be kept between 70-100 °F (don't have metric conversion available).
Bill Hemptech svc. w/ chemical supplier - Grand Rapids, Michigan
A. NEVER add boric to adjust you pH! Keep boric within 22-25 gms / Lit for wire plating, otherwise higher boric will encrust upon your anodes which may be at the bottom of your tank!
Muriatic acid is called Hydrochloric acid in this part of the world. Please use it judiciously and do not lower the pH below 4.8 to 5.0 as you have to remember that you are doing wire plating and a pH lower than this will cause immense build up of iron!
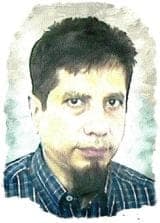
Khozem Vahaanwala
Saify Ind

Bengaluru, Karnataka, India
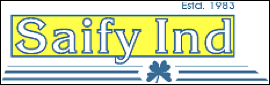
Q. Dear All ,
I'm trying to produce zinc electroplated wire for the staple product . I am using SAE 1018 steel . Wire drawing part is finished . In the coating process I am expecting the coating thickness of 3/4 microns . Adhesion of the coating on wire is very poor and coating peel off .
I'm using the zinc sulphate electrolyte solution .
If anyone know the electroplating of the wire for the staple product , please help me ,
Regards ,
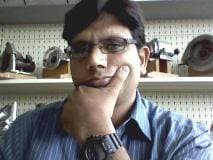
Satish Khule
August 31, 2010
production manager - Pune, Maharashtra, India
A. Hi,
During the drawing process what kind of fluid or soap is been used, is it getting cleaned well before you go for zinc plating? I guess you check on the cleaning, activation part, and at last what kind of zinc sulphate additives you are using?
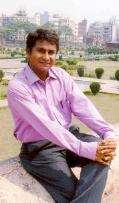
Praveen Kumar
plating process supplier
Mumbai, India
Q. Ours is a small electrogalvanizing unit for mild steel wires. And we are having a continuous line wire galvanising plant for 4.0 mm to 2.0 mm dia wires. Sometimes we are ordered to finish with mirror bright zinc colour. The branded 'Zinc brightener' does not suit our requirements and hence we require to make our own composition. We need help for the names of chemicals and its composition.
Ranjit Singh- Calcutta, West Bengal, India
January 16, 2011
9th Edition, Vol. 5
"Surface Cleaning, Finishing & Coating"
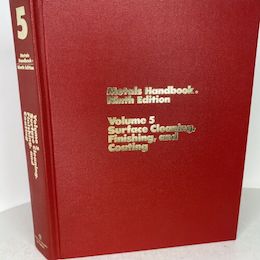
on eBay or Amazon
or AbeBooks
(affil link)
A. Hi, Ranjit. There are a dozen or more brands of bright zinc plating solution, so if you are dissatisfied with what you are using, there are numerous alternatives. Please tell us the general composition of your bath your bath (cyanide, sulphate, chloride, etc.) because many wire platers use zinc sulphate but zinc chloride solutions would usually be used when brightness is wanted.
The composition of chloride zinc brighteners has been largely trade secret for many decades (ASM Metals Handbook, Vol. 5 says ALL are proprietary) so I don't think you'll find much published literature on the subject.
Sometimes these brighteners aren't mixtures anyway, but organic compounds synthesized from precursors, which it is not possible to mix from generic materials, but good luck and hopefully someone will point us to literature. I personally think your time may be better spent searching for another supplier than in trying to make your own, but good luck either way!
Regards,
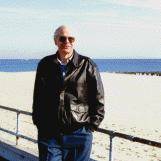
Ted Mooney, P.E.
Striving to live Aloha
(Ted can offer longterm or instant help)
finishing.com - Pine Beach, New Jersey
Q. We are doing zinc electroplating using zinc chloride, potassium chloride and boric acid. Capacity of our bath/cell is 8920 Litter. Kindly suggest me the correct formula of preparing electrolyte solution using these chemicals. i.e what proportion of these chemicals will be used?
Thank You
- Lahore, Pakistan
June 30, 2015
? Please provide more data:
- By the products you mention, you use a potassium-boric acid zinc bath. So, you have a vendor for brighteners for this bath, have you asked them? Or you make your own bath?
- Provide conditions: Time? Current? Conditions of the wire when you plate (straightened, in rolls...)? pH? Concentrations?
- Do you use chromate conversion coatings? Lacquers?
If you give us more information, we can assess you better. Hope you can solve your issue!
Regards,
- Cañuelas, Buenos Aires, Argentina
Q. Thanks Mr.Daniel Montañés
Volume of solution (Zinc chloride + Boric acid + Potassium chloride) is about 6000 Litters. Conditions of process are:
Specific gravity = 20,
pH = 6
Temperature = around 30 °C
Cell dimensions are Length = 45 ft, Width = 4 ft, Depth = 1.75 ft
No. of amperes used per hour is round about = 5000A (it depends upon the load, i.e., no of steel wires passing through whole cell).
Straight wires are passing through cell and finally passed through dilute Nitric acid bath for finishing.
We are still not doing chromate passivation.
When wires at the end are passed through the nitric acid solution, they are bright; but with the passage of time, e.g., after one day, they begin turning black. I want to enhance two things: one is shine and the other is storage period. Kindly assist me.
Thank you
- Lahore, Punjab, Pakistan
? Dear sir
Please tell us the process you're running, and after that the problem you are facing.
Thanks.
chemicals - Moradabad , Utter Pradesh , India
Hi Mukesh. Umer has told us that his problem is that the wire he is plating is not shiny enough after one day, and it turns black in a few days.
I think he needs to change his dilute nitric acid to a chromate treatment. What do you think?
Regards,
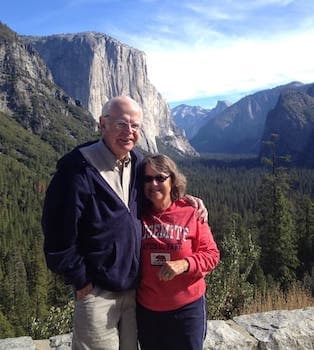
Ted Mooney, P.E. RET
Striving to live Aloha
(Ted can offer longterm or instant help)
finishing.com - Pine Beach, New Jersey
Q. Dear friends
We do acid zinc plating on ms wire. I am able to achieve 1 micron now. How can I increase the plating thickness to 5 microns? The running time of the wire in the tank is 15 seconds, the tank length is 12 feet, the zinc metal is 130 g, ammonium chloride is 230 g and boric is 20 g ,current is 450 amps please suggest.
- kerla , India
August 9, 2016
A. Hi, A.M.
Faraday's Law says that the deposit thickness is directly proportional to the ampere-seconds applied. There might be some small variation based on the cathode efficiency of the solution, but essentially the only way to get 5X more thickness is to apply 5X more ampere-seconds. Unfortunately, you'll probably find that you can't increase the current much without causing burning, and the answer is going to be that you need to run the wire at 1/5 the current speed and produce only 1/5 as much wire.
Regards,
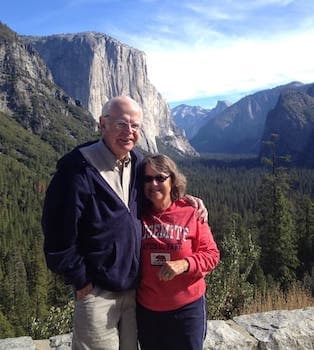
Ted Mooney, P.E. RET
Striving to live Aloha
(Ted can offer longterm or instant help)
finishing.com - Pine Beach, New Jersey
Q. Sir
We do electrogalvanizing of wire for staple making. During rainy season the wire turns yellow from white. This is not acceptable in our product. How to avoid this problem?
- India
July 4, 2017
by Larry Durney
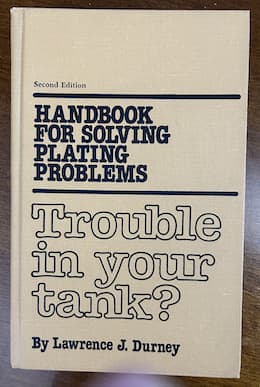
on eBay or Amazon
or AbeBooks
(affil link)
A. Hi Manish, "turns yellow from white" is a bit vague. Are you talking about the incoming wire? Is it possible that the wire is slightly rusty? Are you talking about immediately after chromating, that the chromate color goes yellow in higher humidity? Are you saying that over the course of a month or so it turns yellow in storage.
Please see if you can locate a copy of Durney's "Trouble in Your Tank?". It's basic premise is that it can take us all from flailing to an orderly way of troubleshooting. Good luck.
Regards,
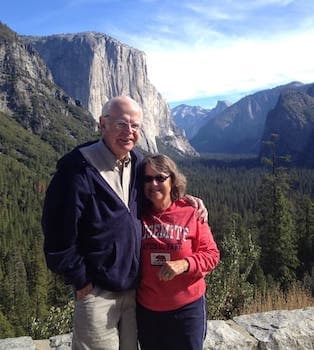
Ted Mooney, P.E. RET
Striving to live Aloha
(Ted can offer longterm or instant help)
finishing.com - Pine Beach, New Jersey
Q. 1. How much coating can we get from cold dip process on wire without making the deposit brittle?
2. Please suggest best book to refer electrogalvanising process?
I deal with wire.
Thank you.
- Mumbai, Maharashtra, India
April 27, 2018
A. Hi Mandar. I am not terribly familiar with acid zinc plating of wire; but for zinc plating of discrete objects, up to 25 microns is a standard spec and 12 microns is very common for automotive requirements. And bending parts around a mandrel for adhesion testing is common, so this would probably not be considered a "brittle" plating.
But the diameter of the test mandrel would be proportional to the diameter of the wire, so it's easy to picture a wire so thin that 12 microns of plating would be problematical. Please try your best to present your actual needs.
The only book which I am familiar with about zinc plating is the previously illustrated "Zinc Plating" [on Amazon, AbeBooks affil links] by Geduld; it has a 13-page chapter on continuous plating of strip and wire, and was published in 1988.
Regards,
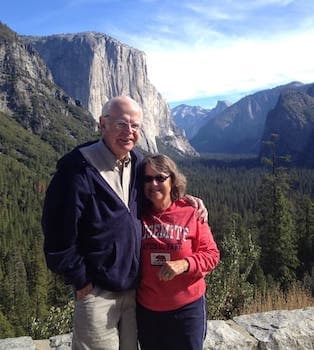
Ted Mooney, P.E. RET
Striving to live Aloha
(Ted can offer longterm or instant help)
finishing.com - Pine Beach, New Jersey
Q. My situation:
We are running a Continuous M. S. Wire Electroplating Plant using Zinc Chloride Bath along with Boric Acid as pH Maintaining agent. I am facing a lot of problems in the same and want to upgrade my processes to ensure quality. Kindly let me know what all information you would like me to provide to help you understand my process better.
Business Owner - Kanpur, Uttar Pradesh, India
July 2018
A. Hi Rishabh! Are you describing an entire old processing line that your plan to scrap and replace, or do you wish to just put more efficient process chemistry in the existing tanks? If you want better chemistry for existing tanks can you please briefly give us your process/tank sequence (like: soak clean, electroclean, rinse, rinse, acid dip, rinse, plating, rinse, nitric acid dip, chromate, rinse, rinse, warm rinse).
P.S.: You asked a particular reader to contact you personally, but this forum doesn't work that way: it would cut adrift the interested readers who have been trying to follow along; it would rewards vendors for not supporting the site by letting them reap free commercial benefit from it anyway; and it would make me spend my time and our advertisers' money in match up potential customers with non-advertisers. Sorry, anything that is shared must be shared publicly.
Regards,
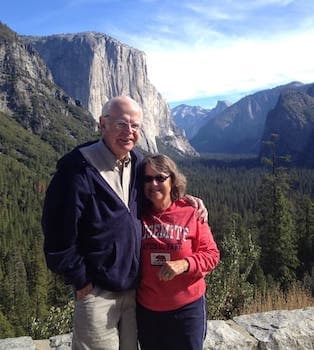
Ted Mooney, P.E. RET
Striving to live Aloha
(Ted can offer longterm or instant help)
finishing.com - Pine Beach, New Jersey
Q. We are trying first time to operate zinc acidic galvanizing line with zinc chloride and ammonium chloride and carrier and brightener; we have no technical support. We are trying to operate the line of 10 parallel wires to be plated in four plating baths of 330 lt capacity each. We could not reach the required brightness. We work at pH 4.6, brightener 4 ml per lit, carrier 40 ml per lt. During our start up we face black foam at end of first bath; sometimes the final product surface has black coloured area then disappearing. Would like advice regarding the brightness and the optimum specification.
Mohamed ben zyada- tripoli, libya
December 27, 2021
A. Hi. Regarding the black foam, please see "Black Tar on surface of Acid Zinc Chloride bath" on thread 40095.
Can you run a Hull Cell ⇦ huh? panel to get an idea what is going on?
Luck & Regards,
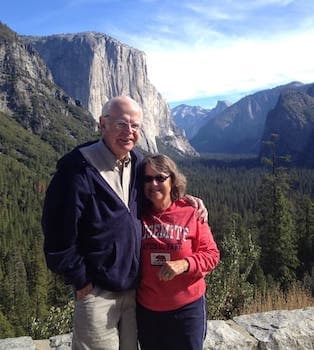
Ted Mooney, P.E. RET
Striving to live Aloha
(Ted can offer longterm or instant help)
finishing.com - Pine Beach, New Jersey
-- this entry appended to this thread by editor in lieu of spawning a duplicative thread
Q. I am building electric galvanizing line for wires. I built a basin with a length of 12 meters, a width of 0.75cm and a height of 0.35cm and I bought two transformers, each 1500 amps. I have reached the chemical stage and I have no experience in these things. I have got this formula and I do not know if it is correct or not.
And what materials should I add this composition to? Is it distilled water?
Zinc chloride 40-80 g/L
Potassium chloride 180-220 g/L
Ammonium Chloride 22-37 g/L
Boric acid 20-30 g/L
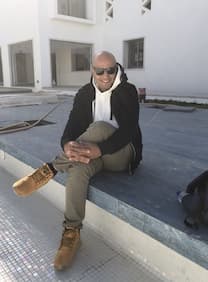
Yahya saleh
- Iraq erbil
December 11, 2022
A. Hi Yahya. Wire plating can be done from cyanide baths, straight sulphate baths, sulphate acetate, ammonium sulphate, and potassium chloride and/or ammonium chloride baths as you have described, and several more. Your bath sounds okay, and yes, distilled or demineralized water is always a safer bet than city water with unknown quantities of minerals in it.
It is a tall order to design plating line chemistry with "no experience in these things". If a consultant or plating process supplier is available, you should try to get their help. If not, a trustable book such as Herb Geduld's "Zinc Plating" [on
Amazon,
AbeBooks affil links] is probably second best ⇨
Luck & Regards,
Ted Mooney, P.E. RET
Striving to live Aloha
(Ted can offer longterm or instant help)
finishing.com - Pine Beach, New Jersey
Thank you very much Mr. Ted_Mooney
Your answer was more than enough for me.
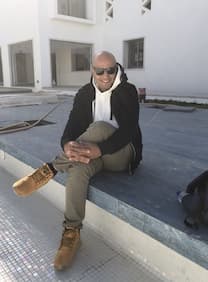
- Iraq erbil
December 12, 2022
Q, A, or Comment on THIS thread -or- Start a NEW Thread