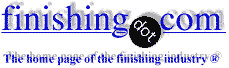
-----
Powder Coating over Zinc Plating Problems
Q. We are failing miserably with powder coating over Fe/Zn13 (.0005 thick) zinc plating with gold chromate. The base metal is cold-rolled steel with stainless steel hardware. The parts receive a nickel strike process prior to zinc processing to prevent the stainless from blistering.
Once we receive the parts back from the platers, we are pre-baking the plating at 275 deg. for 30 min. to accelerate the curing of the chromate and to check for any premature zinc or chromate blistering. We then clean and phosphate coat the parts prior to powder coating. After powder coating, the parts are baked at 400 °For 30 min. After baking, the parts look like we painted over 60 grit sandpaper. Are these zinc explosions? What is causing the paint to outgas so bad? Are our customers asking for a process that should not be done?
- Seal Beach, California
2000
A. My guess is that you do not require the Nickel strike before Zinc plating. Try Zinc + powder coating.
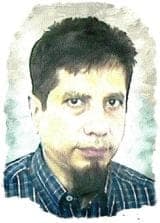
Khozem Vahaanwala
Saify Ind

Bengaluru, Karnataka, India
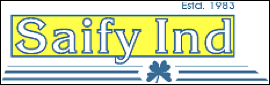
2000
A. Prebaking at 275 will not help to accelerate the chromate curing ... it will destroy it. Why do they want a plated finish before powder coating? Wouldn't a good zinc phosphate be more sensible?
Dougie Lightfoot- Fife, Scotland
2000
2000
A. This sounds like a very similar problem to one we encountered, although without seeing the parts it's difficult to confirm this, our problem was similar.
Components (mild steel) were zinc plated, chromate passivated and powder coated. After curing at 200 °C, the surface of the paint looked, as you said, like sandpaper.
Just stripping off the paint layer showed that the zinc displayed lots of micro blisters that had popped. There was no sign of gross adhesion failure, we could bend the parts through 180 degrees with no de-lamination of the layer.
We investigated substrate, cleaning, etc., but could find no pointers to the cause in the metallurgy or pre-treatment cycle -- consequently we looked at the zinc bath itself: we had recently changed from what I would call a standard alkaline zinc to one of the newer types that the literature & sales people said plated more evenly and faster. Which it did;, however we ran the same parts through the previous zinc solution and the problem disappeared. Our vendor either couldn't or wouldn't offer an explanation. Everybody on the vendor's side stayed pretty tight lipped about possible causes except to say parts were either overcleaned/undercleaned or the base material was poor.
We hazarded a guess that the possible high incorporation of organics/breakdown products were breaking down under the stoving temperature and outgassing and erupting/disrupting the zinc coated layer; there was no pattern to the disruptions, high CD low CD areas showed it did not depend upon the racking of the parts, there was no roughness or occluded particles. One observation we did make is that we could predict what parts and where it would happen by looking at the surface texture, the areas that showed the problem tended to have an almost granular feel.
We never did get to the bottom of it, all the parts ran fine through the previous alkaline zinc so we stuck with that, although I would love to know the answer to it backed up with a bit of hard science. None of this helps you if the parts are plated in acid or cyanide zinc though! I would investigate the type of zinc solution used to see if it's similar to what we encountered, Try plating some parts in a different zinc solution. As neither chemical analysis nor Hull Cell
⇦ huh?
testing revealed the problem with our solution.
Regards
- Lowestoft, U.K.
Q. Dear Mr Richard,
You would be rendering yeoman's service if you could elaborate upon the two 'different' alkaline baths which you have mentioned. The one you were originally with and have reverted to sounds promising and it would be very helpful to a lot of people to know what you have succeeded with . Regards,
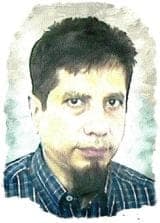
Khozem Vahaanwala
Saify Ind

Bengaluru, Karnataka, India
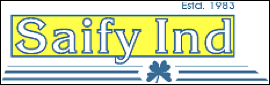
2000
A. Khozem,
I don't know whether it's allowed to what in effect would be bad mouthing to the world somebody's product by name when we're not sure what the problem was. What I can say is the unsuccessful bath had a two part brightener/addition system (as well as a water conditioning addition) one of which was an aldehyde based brightener system for the low CD areas and the bath ran at a fairly high zinc concentration of 12 - 15 gpl, whereas our previous bath ran at a much lower concentration of zinc (in our plant about 6.0 gpl was optimum), and was a one shot addition system in conjunction again with a water conditioning addition added in proportion to caustic soda ⇦liquid caustic soda in bulk on
Amazon [affil link]
additions, all the brighteners in both systems we tried were dosed automatically via amp-hour meters. Sorry I can't be more specific, but I don't think the finishing.com guys want the site to turn into a place where we rubbish particular products; think what it would do for their advertising revenue.
Regards
MP (eastern) Limited - England
----
Ed. note: Thanks Richard, and that's only one of many reasons we compare technologies here but we don't compare brands & sources (why?)
A. The difference I guess is method of zinc dip or zinc plate! Under zinc dip,the utmost temperature of GALVANIZED wire is about 180 degrees.
Davied Wei- Xiamen, Fujian, China
2004
Zinc Plating Gets Cloudy During Powder Coating
Q. I powder coat parts after zinc plating and the zinc that is not coated has a white cloudy film. How or what can I do to get rid of the residue. It will not wipe off, I get the same results just rinsing the parts and heating them at 250 degrees F. need help.
Bob Parks- San Jose California USA
2001
A. It's because the passivate is burning it starts to dehydrate above 60 °C; you need to protect the uncoated area from as much direct heat as possible. I have seen this in another product; it was very expensive but can be done -- also the age and condition of the gold passivate and rinse water quality will contribute to the finish (cloudy).
Hope this helps.
- Australia
2001
Powder coating over zinc plating is rough, and it bubbles & peels
March 22, 2013Q. To avoid rust issue we have done zinc plating over mild steel, and finishing with powder coating.
Before powder coating we have done below process:
1. Due to some mild scratches we use soft sandpaper to make it smooth.
2. We clean the plate with thinner
3. Pre heating process
4. Powder coating process
5. Oven temperature 200 °C and curing time 20 to 30 minutes.
We have peel-off issues, bubbles, and the surface is not smooth.
Please advise how to solve the quality issues.
Thanks
mano
Engineering - Sungai Petani, Kedah, Malaysia
A. Hi Mano. Paint or powder will not adhere properly to bare zinc, and if you are sanding the plating, you are removing the chromate conversion coating which is necessary for proper adhesion. As the first step in solving the problem, I think you ought to stop sanding. Ideally, the chromate conversion coating should be allowed to cure for 24 hours, then the items powder coated with no other prep steps (with exception of mild preheat as required). Obviously, this means they must be kept free of fingerprints and other soils. Good luck.
Regards,
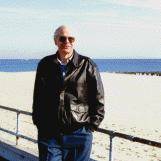
Ted Mooney, P.E.
Striving to live Aloha
(Ted can offer longterm or instant help)
finishing.com - Pine Beach, New Jersey
March 26, 2013
Q. Hi
Q1. What will happen if the mild steel plate was not rusty and wash with de-rust chemical?
Q2. What will happen if more iron phosphates used before powder coating process?
Please advise.
engineering - Sungai Petani, Kedah, Malaysia
March 28, 2013
A. Hi again Manogran. I like your first posting better because it describes what you actually do and the problems you are having. In your second posting you are posting questions that I don't understand, but which can't be answered anyway because they are abstract (What will happen if ...?)
1. These mild steel plates that you are talking about are or aren't zinc plated? Are you asking what would happen if you stopped doing zinc plating and chromate conversion coating and simply powder coated the raw steel after dipping it into some sort of rust-proofing compounds? It wouldn't work: your corrosion resistance would drop terribly and you'd probably have no adhesion at all onto de-rusting chemicals.
2. Are you proposing iron phosphate on top of zinc plating and chromate, or on top of rust-proofing compound, or on bare steel? Iron phosphate on bare steel might work but would be nowhere near as corrosion resistant as the zinc plating plus chromate conversion coating.
Something to be remembered is that no process will work properly if you just try this and that with a scattergun approach but no attention to detail. You had a good process theoretically with the zinc plating and chromate conversion coating followed by powder coating, but you have to do each step properly and tie down all the parameters. Good luck!
Regards,
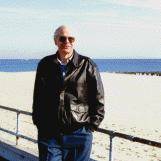
Ted Mooney, P.E.
Striving to live Aloha
(Ted can offer longterm or instant help)
finishing.com - Pine Beach, New Jersey
March 28, 2013
March 29, 2013
Q. Hi Ted Mooney,
1. What will happen if raw steel is dipped into rust proofing compound for 12 hours
2. Next dipping into iron phosphates for 20 minutes
3. Keep dry and go to preheat process
4. Powder coating process with oven temperature 180 °C and curing 20 minutes?
Please advise how do I get good finishing or advise me the proper method.
1.We don't go for powder coating over zinc plating due to expense.
2.We found a lot of scratches and spikes and other quality issues; and also were not getting good powder coating finish coating over zinc plating.
engineering - Sungai Petani, Kedah, Malaysia
A. Hi Mano & Ted,
This is a very confusing dialogue.
Is it possible that what is referred to as Zinc Plating is in fact Galvanising?
That could resolve part of the dilemma.
Perhaps if Mano could describe the articles to be treated, e.g., thickness, complexity of shape, end use, service environment and life expectancy this Community could be more helpful?
Regards,
Bill
Trainer - Salamander Bay, Australia
A. Hi Bill. I'm pretty sure that Manogran is talking about zinc electroplating, and that only Davied Wei introduced the issue of hot dip galvanizing. But you're certainly right that it's quite confusing :-)
Hi Mano. Bill has raised a good point for us to think about, i.e., tell us about the parts and service conditions.
It is possible to get marginally acceptable corrosion resistance from simply iron phosphating and then powder coating, but it won't have nearly the corrosion resistance of zinc plating & chromating followed by powder coating. I would personally not consider iron phosphating followed by powder coating adequate for outdoor use. But Dougie Lightfoot's idea of zinc phosphating in the traditional 7-tank process might be good enough. It hinges upon the details because some components and shapes can be effectively powder coated whereas others may have Faraday cages, lapped joints, or other features which make full coverage impractical, such that plating or e-coating is necessary.
I understand that the reduced cost of iron phosphating compared to zinc plating can be a powerful driver, but then you go on to say "also we're not getting good powder coating finish coating over zinc plating". Surely, many shops successfully powder coat on top of zinc plating; so simply abandoning the approach as your corrective action seems to indicate falling into the trap of the "scattergun approach" mentioned in a prior answer. If possible please try to get your hands on a copy of Larry Durney's priceless "Trouble in Your Tank?", the guide to straightforward troubleshooting of plating problems. Abandoning a process because it's too expensive is one thing, but dismissing accepted processes one after another because they don't work well might indicate a lack of methodical approach. Best of luck!
Regards,
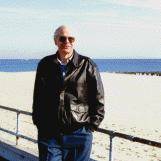
Ted Mooney, P.E.
Striving to live Aloha
(Ted can offer longterm or instant help)
finishing.com - Pine Beach, New Jersey
November 2013
Powder coating peels off of zinc plating near threaded holes
November 19, 2013Q. We use Cold-Rolled Steel as raw material and pretreatment by Alkaline Cyanide Zinc Plating, then dry for powder coating. There are some adhesion problems. The coating peels off near threaded holes!
The Cyanide Zinc Plating Process
Acid Cleaner (HCl) [15 minutes]
Rinse
Electro cleaner (NaOH) [3 minutes]
Rinse
Alkaline Cyanide Zinc [4A, 4.6V, 15 minutes]
Rinse
Chromating [trivalent blue chromium 15 seconds]
Dry [90 °C, <10 minutes]
Powder coating
If we don't use powder primer and zinc phosphate to improve adhesion, do you have other suggestions?
- Taiwan
A. Hi Steven. If the zinc plating is properly adhering to the substrate, as it seems, then you needn't worry further about the steps that precede zinc plating.
It's always difficult to ascertain whether the problem is in the zinc plating & chromating half of the cycle or the powder coating portion, but my first guess is a problem with the trivalent chromating -- only because I've heard of it several times before when shops converted from hexavalent to trivalent chromating. Many different approaches to trivalent chromating were brought to market with 99% of the focus being on salt spray results, and some of them offer poor adhesion for subsequent powder coating. Trivalent chromating on cyanide zinc is a somewhat uncommon approach anymore, and I think it's highly possible that the chromate is not adhering to the plating properly.
Regards,
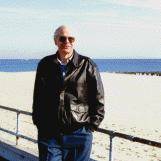
Ted Mooney, P.E.
Striving to live Aloha
(Ted can offer longterm or instant help)
finishing.com - Pine Beach, New Jersey
November 2013
A. I'm surprised you don't get more adhesion problems when you have nothing in between the zinc plating and the powdercoating. Surely a zinc phosphate, a chromate or a dry in place system between the two is required?
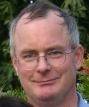
Geoff Crowley
Crithwood Ltd.
Westfield, Scotland, UK
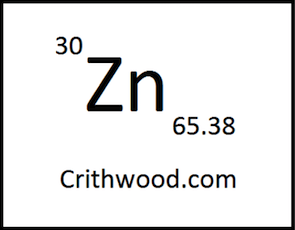
November 24, 2013
(you are on the 1st page of the thread) Next page >
Q, A, or Comment on THIS thread -or- Start a NEW Thread