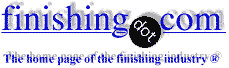
-----
Powder Coating over Zinc Plating Problems
< Prev. page (You're on the last page of the thread)
November 28, 2013
Q. Hi Ted Mooney,
Thank for your suggestions.
We tried two methods and the adhesion is better.
1.Reduce Alkaline Cyanide Zinc Plating time [15 minutes to 7 minutes]
2.Reduce trivalent blue chromating time [15 seconds to 7 seconds]
Both of them get better adhesion and can afford high humidity test more than 48 hours
But we don't know which method is better?
And what is the theory of method 1 ?
Thanks and best Regards,
Steven
- New Taipei City, Taiwan
A. Hi Steven. Here in the USA I don't know of any shop which is doing "home-brewing" of their trivalent chromating. Consequently, most of us (including me) can't offer any real help on suggested chromate immersion time beyond "follow your supplier's recommendations". Apologies.
If you reduce the plating time to 7 minutes, you are seriously impacting the corrosion resistance of your components whether or not it's immediately apparent in your salt spray tests. I wouldn't do it. But if doing it improved adhesion, it makes us suspect that excess brightener in the plating bath is the problem.
Regards,
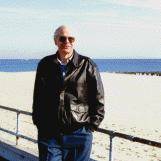
Ted Mooney, P.E.
Striving to live Aloha
(Ted can offer longterm or instant help)
finishing.com - Pine Beach, New Jersey
November 28, 2013
Electrically conductive substrate for powder coat over mild steel?
Q. We're building an electrical enclosure of our client's design that features epoxy powder coat (Axalta ELW505S9) over mild steel. There are two problems that I see with the design:
1) They have specified unpainted threaded holes in the enclosure that will take stainless steel fasteners. This seems like an invitation to galvanic corrosion, which is taboo in the rail industry.
2) In order to maintain electrical conductivity to chassis ground, they are using a conductive foil masking product that is a) expensive, b) more laborious than standard masking materials, and c) apparently prone to adhesive failure. We would like to recommend a suitable coating material to address the corrosion issue and remove the requirement to use the foil masking.
What is a suitable substrate for epoxy powder coating over mild steel that is electrically conductive and corrosion protective? I was leaning towards zinc phosphate, but that is apparently non-conductive, while zinc plating is apparently a poor substrate for powder. Are there other economical coatings that address these issues?
Manufacturing Engineer - Canada
December 16, 2015
A. I would like to address some anomalies in this post:
1st: Zn Electroplate is not a problem to powdercoat if suitable pre-treatment is employed.
2nd: Zn Phosphate is the preferred pre-treatment for both Zn electroplate and HDG substrates.
Zn Phosphate (as the preferred pre-treat) is obviously conductive.
It seems you are working with flawed assumptions.
Hope this helps.
Regards,
Bill
Trainer - Salamander Bay
Thanks Bill. I think we can all largely agree with you but with a couple of cautions.
Considering the frequent powder coating adhesion problems in recent years since the widespread switch to various proprietary trivalent chromating processes, I think I agree that phosphating of zinc plating might be a better approach than chromating it -- but there are probably logistical difficulties in establishing a phosphating on zinc electroplating process because virtually all plating shops use chromating instead of phosphating. In 40 years of travels to thousands of plating shops, I don't recall ever seeing a general purpose zinc electroplating line that didn't include chromate conversion coating or that did include phosphating.
The other issue is that "conductive" is not a go/no-go word. While phosphating is sufficiently conductive for subsequent electrostatic painting, it is obviously not sufficiently conductive for a low voltage contact application -- and I don't know what Murray really needs. You're probably right that phosphating the screw holes is fine
Zinc plating the enclosure is a complication and expense that he probably doesn't need. Thanks again.
Regards,
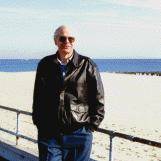
Ted Mooney, P.E.
Striving to live Aloha
(Ted can offer longterm or instant help)
finishing.com - Pine Beach, New Jersey
December 2015
Q. Thanks, Ted and Bill.
Please accept my apologies for my lack of clarity.
We need to maintain electrical conductivity to chassis ground for low-voltage electronic devices, not primarily for electrostatic paint deposition--though, of course, we do require the paint to adhere to this product! In our own product designs, we have almost universally used unpainted hexavalent chromate as the sole finish over aluminum (i.e. in accordance with MIL-DTL-5541
[⇦ this spec on DLA] Type I, Class 3), but this customer design we're building uses powdercoat over unplated mild steel, which is not a finish we're familiar with.
It's my understanding that zinc phosphate, while an excellent substrate for powdercoat, is not sufficiently conductive to provide a path to ground (that would be the "low voltage contact application" that Ted mentions). Please correct me if I'm mistaken.
So, we're looking to recommend to our client a corrosion-resistant, electrically conductive substrate for powdercoat that would protect the screw holes and allow us to delete the expensive and laborious conductive foil mask that they are currently specifying for their grounding points. Instead, we would just use normal masking around the grounding points to provide a conductive path to ground.
Since I first asked this question, I spoke to the finishing shop that will be doing the work, and they recommended *alkaline* zinc plating for this application, which they claim will satisfy our requirements. Having worked with these guys for some time, I'm inclined to defer to their expertise. Do you have any reservations about this approach?
-- - Victoria, BC
January 6, 2016
A. Hi Murray. Alkaline zinc plating plus chromate conversion coating (very similar to the MIL-DTL-5541 which you do on aluminum but done on the zinc plating) is a fine, and conductive, pretreatment. The only reservation being that the plating shop must do proper plating and conversion coating and TEST the adhesion of the powder coating. As I've alluded to, all modern trivalent chromate conversion coatings are proprietary and were developed with the primary goal of matching the old hexavalent chromates in salt spray testing. Other issues like adhesion of subsequent powder coatings were hardly on the radar, with the result that adhesion to some is quite good but adhesion to others might be poor.
Regards,
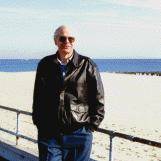
Ted Mooney, P.E.
Striving to live Aloha
(Ted can offer longterm or instant help)
finishing.com - Pine Beach, New Jersey
January 2016
Q. Thanks very much for your advice, Ted. The client requires an adhesion test (plus gloss and thickness) for each paint batch, so that should help us maintain quality control.
Last question, I hope: Is chromate conversion standard on all zinc plating, or does it have to be specified? On our own products, we use fasteners specified to ASTM B633 Type II, which has a yellow chromate conversion applied (not sure if hex or tri), but is it routine on other zinc finishes, or should I make sure it's called out on the drawing?
- Victoria, BC
January 7, 2016
A. Hi again. The finish, including thickness of zinc plating and class of chromate conversion coating should be spec'ed, but it is universally done; I don't think I've ever seen zinc plating done where subsequent chromate conversion coating was not done.
Regards,
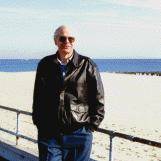
Ted Mooney, P.E.
Striving to live Aloha
(Ted can offer longterm or instant help)
finishing.com - Pine Beach, New Jersey
January 2016
Outdoor furniture- electroplating - to powder coating adhesion issues
September 16, 2019Q. We have a powder coating line that we use on aluminum constantly, we produce outdoor furniture out of indonesia, and I don't get much complaint on the powder adhesion to aluminum (some when they place it in the pool for long times, but I'm working on just using better powder for that instance).
But today I have another issue I'm trying to sort out.
I have more and more steel orders that I have to powder coat after a rustproof process, such as HDG hot dip galvanize or Electroplating.
For HDG to powder process, I checked on your site and others, and so I lightly sand it and clean it before I powder coat with not the best results aesthetically but can pass for garden tables. Still a bit bumpy in some areas. But no adhesion issues thus far.
But for the electro plating and powder coating I'm having serious adhesion issues on the sides and the top round bars of a bistro chair, regular round 19 mm mild steel tubes that I bend and weld, before sending out for EP.
The EP here in Indonesia is different from what I'm used to in China where it comes out almost yellow or bronze with almost acid bath etched look, this just looks like a flat matte grey. I'm guessing they are doing another process in china or this is just a simple zinc plated EP. (I'm no pro I listen to my production department but they are at a loss for answers for me)
The sides of the chair and the top of the chair, both tubes are losing the adhesion, the flat support bars of the chair, where we attach the wood slats to, (its a regular teak wood slat chair, low price point, you can see them in cafes and restaurants patios around the world) is not having that type of loss of powder.
Im assuming its because when they stack the chair they break the powder coating down on the sides, and then it just deteriorates slowly, but I have other products where even if the powder is broken it doesn't just flake off the edges like this. Plus that wouldn't explain the top bar. My production manager said they were using dirty gloves to handle the products but I'm not sure if that is the case entirely.
Im trying to find out what would be the best procedure for degreasing, cleaning, curing etc., before I powder coat on Electroplated steel.
I have one theory that right after powdercoating the powder is on the frame and it makes a quick round in our workshop before it enters the oven, I can see plenty of aluminum dust and steel dust in the air from our welding and grinding workshop just next door, do you think the dust inn the air is doing this? Wouldn't it do it to the whole chair?
We never used to grind steel so close to the line, and I've always asked them to keep that area less dusty but its almost impossible in the space that we have to not have aluminum and steel dust in the air. or could it be the temperature?
I have read plenty of similar situations on your forums trying to find my answers but either I'm not finding them or the questions are not specific enough to my usage.
Buyer - indonesia
A. The only reason is your pretreatment is insufficient! Your can try Zn-Ni plating (NO sealing) instead of it. By the way, your weld point so rough.
ANKA QIUAnka - GZ CHINA
September 19, 2019
XIE XIE !!
I also asked the production manager and he told me the following:
electroplate---- sand with grit 400----wash with WICO ANC manually with cotton or polyester rags----air dry with an air gun------ powder coat at 250 °C for 12 minutes.
This is his process, could it be that the flat bars and the round bars are not the same temp in the oven? could they be not cleaning it properly? Or have to change the rags more often?
I will tell them what you said! Thanks for your response, anything will help at this moment. As for the welds ... this is Indonesia not china hehe, and we cover it with teak seat slats so it doesn't matter to the customer, my thoughts are always I'd rather a chunky weld that doesn't break than a grinder weld that was overground.
THANKS AGAIN!
Outdoor Furniture - Surabaya, Indonesia
September 19, 2019
A. Hi, Oven temp decided by the thickness not the shape of workpiece. usually when T<1.5mm 210>15min (workpiece temp not air temp) is enough. In my point of view, when cross-cutting failed, reasons as below:
1.pretreatment not sufficient
a. Degreasing power not sufficient
b. Wrong Electroplating process
c. Wrong process of pretreatment(Maybe you should cancel sand&wash step, if it necessary, finished it before plating)
2. Powder coating
a. Low temp and short time when workpiece passed oven.
Anka - GZ CHINA
Zinc Chromate Delamination
Q. I am having an issue with chromate delamination on parts plated with zinc per ASTM B633. The issue appears sporadically after parts are masked, painted, baked for 30 minutes at 380 °F. When unmasked, the chromate "peels" off with the tape.
Supplier Quality Engineer - San Jose, California
August 15, 2019
Q, A, or Comment on THIS thread -or- Start a NEW Thread