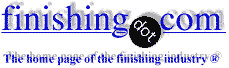

Jump to this related thread:
• Topic #4844 "Salt Spray Test Inconsistency and Scribe Marks"
• Topic #21901 "Salt Spray Condensate Collection and Orientation of Parts"
• Topic #58588 "Salt spray test: Can't get adequate solution flow"
• or continue with -----
ASTM B117 Salt Fog Test Chamber Operational Q&As, Problems: Salt Spray Woes
Q. With what solution can I unclog the nozzle if it has grains of salt stuck?
Alejandro HernandezLab Lead Engineer - Tijuana, Mexico
November 23, 2022
A. Hi Alejandro
I'm not sure if any solution will work better than hot water.
Good luck,
- Winnipeg, CANADA
December 7, 2022
A. You can most likely use a very dilute solution of hydrochloric and DI, I use it all the time to clean films on probes. Hot DI is your best bet for a non-solution based method.
Milyssa Raboin- Avon, Connecticut
February 10, 2023
Q. Hello,
First of all, thank you very much for your help.
I test according to ASTM B117. My salt solution is 5%. density The density of the collected solution is always high. I can't adjust the density in any way. Would you help me with this?
- TURKÏE ANKARA
March 3, 2024
A. Hi &Ounl;zgenur,
While waiting for a specific response, please make sure to read Davey Shaw's comment on collection.
Luck & Regards,
Ted Mooney, P.E. RET
Striving to live Aloha
(Ted can offer longterm or instant help)
finishing.com - Pine Beach, New Jersey
⇩ Related postings, oldest first ⇩
Salt Spray and Water Quality
Q. Hi Everyone,
Can I get some feedback on the quality of water used in a chem film operation and salt spray results.
Since we moved locations and are no longer using city water we have been having trouble with salt spray tests. At least that seems to be the only conclusion I can come up with.
Any thoughts?
Thank-you
Micheline
Finishing Company - Rincon, Georgia, USA
January 31, 2008
A. Are you salt spray testing real parts or test panels, Micheline? If it's test panels, I would suspect damage to them, or non-equivalence of your new source, before I'd suspect water quality.
If it's not the test panels, I may sound like a broken record on this, but some people believe that only deionized water should be used in plating shops anymore. If the water usage rate is not high, a simple 2-bed DI system will solve the problem this time, and forever as well :-)
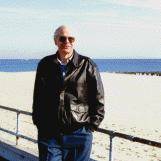
Ted Mooney, P.E.
Striving to live Aloha
(Ted can offer longterm or instant help)
finishing.com - Pine Beach, New Jersey
Thanks Ted,
It is test panels, but we make them ourselves. I've tried various grits from 180 to 1200. Believe it or not there was no rhyme or reason, some past and others did not (no pattern)
After failing a test I decided to run a set through the system and another through buckets using DI water, I bet you can guess that both past with absolutely no pits.
I'm kinda hoping it is the water because we are in the middle of purchasing a Wastewater recycle system which will provide us with DI water.
This has been driving me crazy.
Thanks,
Micheline
- Rincon, Georgia, USA
Concentration of collected solution for salt spray test is too low
Q. Dear friend,
I have a question: during salt spray test, the concentration of collected solution is lower than original solution, e.g., the solution I mixed is 5%, but collected solution concentration only about 2%.
What happened to it?
Thanks a lot.
- Suzhou, China
March 9, 2008
A. I'm not familiar with any ASTM B117 requirement to run a condensate analysis, but would not necessarily expect the condensate to contain the exact concentration of the bulk solution being aspirated into the (95 °F) tank. You may want to compare your 2% result with the concentration of solution taken from the bottom of the tank and from the "moat" that provides the air-tight seal around the lid.
TRH
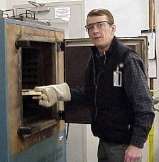
Thomas Hanlon, Materials Engineer
aerospace finishing - East Hartford, Connecticut, USA
A. I politely but strongly disagree with Thomas. The analysis only counts on the collected condensate that does NOT drip off of the parts.
If anything, the salt concentration would be expected to be higher in the condensate since the aspiration of the solution would evaporate it.
How are you checking (measuring) the salt concentration?
- Navarre, Florida
A. Hi
We operate SS chambers per the ASTM and it does indeed require that the collected solution be analyzed for both pH and concentration. You can measure concentration by using specific gravity or by using a salt refractometer. The solution must not have touched any parts and it is not to be taken from the water seal around the lid. There are strict requirements in the ASTM as to how the atomized solution is to be collected.
Thanks,
- Auburn, Washington
A. This question intrigued me, so I contacted one of the world's experts on this subject (at a UK salt spray cabinet manufacturer) and this was their reply.
The salt solution is mixed with air that has passed through the air saturator, this adds some moisture. The take up of moisture by the air is increased if the air saturator is set to a high temperature. Add to this the fact that the chamber is heated through a base covered in water (to maintain humidity levels) there will be some changes in the concentration of the salt solution.
I would be very surprised if the above would cause the level drop from 5% to 2%.
I would suggest measuring the salt concentration remaining in the salt tank at the end of the test to be sure that the salt dissolved is evenly distributed and that additional water hasn't been added to the tank.
Other than the above, I would suspect a fault with the chamber. Perhaps an overfilling air saturator (causes water to be squirted through the atomizer).
Has the chamber been serviced recently? Are you confident that it is working as it should be?
Kind regards,
Martin
This seems to be a very good explanation as it points to several causes that could contribute to the problem and that are worthy of investigation.
Terry
Birmingham, United Kingdom
Correct operation of salt spray tests during weekends
Q. We are a job shop plater and send regularly parts to be tested by two of our vendors in their salt Spray cabinets under ASTM B117 as part of their service for the chemicals we purchase.
We recently discovered that they start the test on a Monday and by Friday they stop the test, and start up again the next Monday.
Is this the normal procedure?
Will the test be valid? At the end, they count the cycles that the cabinet was working, but I don't think the test will be valid? Since parts remain inside the cabinet.
How are plants doing this in the USA? o they use their cabinet on Sundays as well?
I know that someone might tell us that since we are not paying for the service this is what we receive, but it is a part of their service and they are giving us a Certificate that they performed the SS test under ASTM B117
Any inputs?
Thanks
Sergio Hernandez
Plating shop employee - Guadalajara, Mexico
April 1, 2008
![]() |
A. As I read the spec, it is not authorized and there are several chemical reasons why it should not. - Navarre, Florida A. We operate our chambers continuously for the 5% neutral salt fog testing per ASTM B117. When test parts require a one week or two week test period we leave them in with the chamber operating over the weekends all the time. We do not shut down. And I don't know why you would need to shut down. - Auburn, Washington A. Hi Sergio, ![]() Trent Kaufman electroplater - Galva, Illinois |
Our chamber rusts the test parts in too few hours
Q. We are just starting up salt fog testing to ASTM B117 and have found some issues regarding pH and premature rust. We think it's related.
Since we are using mixed bed de-ionizers to make type 4 water, we know that it produces a low pH of about 5.5. Once it has been in the tank with Salt for a while, and once it is atomized in the chamber, we get about 6.2.
Not sure what concentration and acceptable grade of NaOH, and HCl to use for adjusting, so we have just kept the chamber running at 6.2. The problem is our chamber is rusting the specimens prematurely. This is of course in comparison with our platers, and other testing facilities. Does anyone think running the chamber on the lower end of the pH range of 6.2 would affect the test this way?
Also, does anyone know what concentration and grades of the HCl and NaOH we should use? And how much to add?
Buyer, Final Inspector - Northvale, New Jersey
September 29, 2008
A. A pH of 6.2 is not that acid.
I'd suggest using a freshly calibrated pH probe, and 0.01 N NaOH to adjust the pH to 7.0, if you think that will help. (I don't think it will make much difference, but it won't hurt.)
Insofar as documentation: buy the 0.01 N NaOH from Fisher Scientific, and write the lot number down in a book ... it's hard for me to see how even the toughest auditor could object.
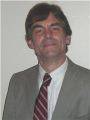
Dave Wichern
Consultant - The Bronx, New York
A. Steve,
This sounds very similar to a problem I had a few years back. I used analytical grade 0.1N NaOH
⇦ on
eBay or
Amazon [affil link]
and HCl for adjustment. Rather than trying to add a fixed amount and see what happened I would take a 100 ml sample and adjust in the Lab and then multiply up to the reservoir size for the addition. In my particular case it was normally found to require about 50-100 ml of 0.1N NaOH in 120 liters of solution. Once adjusted I would retest the pH of the reservoir and ensure it was between the 6.0-7.0 ^ 6.5-7.2 required by the specification.
By the way, this was related to premature failure of chromate conversion coated samples of 2024 Aluminum.
Aerospace - Yeovil, Somerset, UK
A. Steve,
Isn't the pH on fallout required to be 6.5 to 7.2?
And yes, I would think that a low pH will affect your results.
We use 0.1N reagent grade NaOH or acid to adjust. Make small additions
- Auburn, Washington
A. You must maintain your collection pH between 6.5 - 7.2 if you wish to perform testing per ASTM B117 (and also avoid false failures and audit findings). Is the sample exposed to open air for any period of time prior to measuring the pH? If so, it may be possible that the solution is absorbing carbon dioxide from air and the pH is decreasing accordingly.
Another question: does your pH meter automatically compensate for temperature differences? If the meter is assuming 77 °F, but your sample is 95 °F, there will be enough error to make you believe you are out of tolerance.
As mentioned before, increase your salt solution with 0.1N NaOH prior to introduction into your chamber. You want to target the higher end of the tolerance since pH of the collected fog will almost always be lower than your salt solution. Also measure with a fresh calibration and a suitable pH electrode/meter. We prefer to calibrate prior to each use.
- Dayton, Ohio, USA
The fallout is indeed required to be 6.5-7.2. I think I may be getting my ASTM mixed up with ISO 9227 for the make up. One of the problems of trying to run a salt spray to multiple specifications!
If there is a continued problem with low pH as collected, the ASTM does allow you to boil the sample for a period to remove the dissolved carbon dioxide. I have tried this before and it does work, but has always felt as if I was fudging the results. Preferable to adjust your reservoir to obtain the correct collected pH.
Aerospace - Yeovil, Somerset, UK
Specific gravity readings are rising during ASTM B117 salt spray testing
Q. I am having trouble keeping the specific gravity in range, it always seems to be a little high. I use a premixed 5% salt solution, testing the solution before use I get a S.G. of about 1.035 straight out of the drum. After I test the collections I am getting S.G. of 1.045 to 1.050. Could anyone give me an idea of what might be causing the S.G. to raise during the testing?
Shaun DickensonQuality Tech. - Frankfort, Indiana, USA
December 22, 2010
A. That is because of the atomization of the solution: some of the moisture and only a bit of the salt goes out the vent.
I always made up my salt solution on the low side so that the condensed salt solution was on spec.
Carbon dioxide caused me a bit of pain in controlling the pH of the collected solution. It required adjustment a couple times a week.
- Navarre, Florida
Effect of unbalanced pH Level on Salt Spray Test
Q. I'm looking for an answer on the effect of unbalanced pH Level during salt spray testing.
As you know ASTM B117 requires the collected Salt solution be within pH Level of 6.5 to 7.2, but what if we don't monitor the pH Level of our Salt Spray Testing ... is there a significant effect on our specimen?
We just follow the 5% NaCl mixture solution.
Also, what are different types of Failure or Effect of Salt Spray testing considering all types of specimen? Is there such thing as reference on how to identify the type of Failure or Effect of Salt Spray. I'm still new with Salt Spray Testing and I'm not familiar with other kinds of Failure ... All I know is Red Corrosion or Rust.
I'm even confused between white corrosion and Calcium deposits.
Please advise.
Thanks!
Quality engineer - NSW Australia
March 1, 2011
A. Hi Jem. We appended your inquiry to an earlier thread which should offer you some insights. See the subheading "Our chamber rusts the test parts in too few hours" above. Good luck.
Regards,
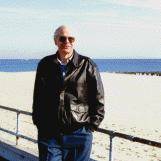
Ted Mooney, P.E.
Striving to live Aloha
(Ted can offer longterm or instant help)
finishing.com - Pine Beach, New Jersey
A. Hi Jem,
You really need to tell us what you are testing, both base materials and coatings. At the moment it sounds like you are testing on steel, possibly zinc or zinc alloy plated steel?
Anyway the failure to monitor the pH means that you cannot claim to be testing in accordance with ASTM B117. The specification requires that you keep a daily log of the pH from the collectors. So regardless of the effects of pH you need to monitor it anyway.
Aerospace - Yeovil, Somerset, UK
A. Hi Jem.
1. The corrosion behavior of different platings on different substrates in acidic or alkaline environment are different. Therefore, it is imperative that you maintain pH at 6.5 ~ 7.2 (ASTM B117) to consistently achieve and interpret salt spray results.
2. Interpretation of pass/failure of SST will depend on the standard that the plated part has to adhere to. There is no one reference or standard that covers all. As an example, the mention of white rust and red rust suggests zinc plating on steel substrate. If you are plating to ASTM B633 ( Standard specification for electrodeposited coatings of zinc on Iron or steel ), it states:
The appearance of corrosion products visible to the unaided eye at normal reading distance shall be cause for rejection except that white corrosion products at the edges of specimens shall not constitute failure.
Corrosion Resistance Requirement Types Test Period, hours
II 96
III 12
- Penang, Malaysia
Thank you for the advice. I am now maintaining the pH Level of the collected solutions and already identified the best pH reading for the Salt Solution in order to have a reading of pH 6.5-7.2 for the collected solution.
- NSW Australia
(you are on the 1st page of the thread) Next page >
Q, A, or Comment on THIS thread -or- Start a NEW Thread