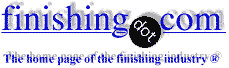

Jump to this related thread:
• Topic #4844 "Salt Spray Test Inconsistency and Scribe Marks"
• Topic #21901 "Salt Spray Condensate Collection and Orientation of Parts"
• Topic #50132 "ASTM B117 Salt Fog Test Chamber Operational Q&As, Problems: Salt Spray Woes"
• or continue with -----
Salt spray test: Can't get adequate solution flow
Q. Hello
I'm a French student and I'm currently working on a salt spray device.
We bought this device from a Chinese company.
According to the European standard NF EN ISO 9227, we need to have a flow of 1.5 (+-0.5) mL/h into the measuring bucket,
BUT we're really under this measure (approximately 0.3 mL/h)
We tried to increase the pressure and we also tried different heights with the dispersal cone but the result is the same.
If someone had the same problem and can help me, I would be grateful to you.
- France
May 30, 2012
![]() |
A. From experience and not from great knowledge, here are my thoughts-- - Navarre, Florida A. Hi Thomas, Aerospace - Yeovil, Somerset, UK |
A. Bonjour Thomas.
Comment allez vous?
I had similar problems with our salt spray cabinet, which is an old Harshaw model built in the 1980's.
What are your tower temps, pressures, cabinet temps? Are you using ASTM D1193 Type IV water? One needs to use a good quality D.I. water source, with low TDS , uS as salts will clog the nozzle orifices (as you well know).
Since this is a closed loop system relying on pressure to feed the water tower and the salt vessels, inspect EVERY fitting to ensure there are no leaks / drips.
I went and gave old Betsy a complete overhaul, and found HAIRLINE cracks in some fittings, which when replaced produced more than adequate ml/h fog. I needed to close the vents somewhat
Also, the salt vessels are equipped with a 5 you poly pro filter, to ensure no particles can gain entry to the atomizers. Bon Chance!
- Toronto, Canada
A. I too had a similar problem with a Singleton cabinet and will present you with another possible solution. After weeks of fiddling, cleaning, and adjusting I determined that the angle of the atomizer to the bevel of the spray apparatus was off.
Scott Merritt- Eastman, Georgia, USA
A. Hi Thomas,
Better you can check the Funnel diameter for the collection, in general collection area should be 80 sq.mm, for this area you need to select the funnel diameter of 100 mm.
And keep one collection unit near nozzle & one is in end of the nozzle in the distance.
- Salem, Tamilnadu, India
A. I had a similar problem on a Harshaw cabinet. A thorough cleaning of the atomizer nozzle did the trick for me.
Phil Brown- Welcome, North Carolina, USA
Q. Hello, I wanted to know what is the flow rate used from the solution tank to the sprayer.
How to determine the flow rate from the solution tank to the spray?
Hope I get a response soon. Thank you.
- Mauritius
September 17, 2012
Q. I also am trying to determine the flow rate for salt spray testing between the reservoir and the atomizer. All I have are pressure readings in ps,. Can anybody help.
James Threadgill- Largo, Florida, USA
September 21, 2013
A. There is no instrumentation for this as it is a function of aspiration of the salt solution. Placement of your recovery grad cylinders can make a major difference.
Also, they can not be where the parts could drip into the funnel that you have on top.
If your numbers are low, clean/replace the cloth filter and blow out the passageways.
- Navarre, Florida
Low collection in Salt Spray chamber
Q. We have been running a Singleton salt spray chamber for four years, two weeks ago the air compressor went out causing the DI feed tank to drain into the humidity tower and therefore internal salt solution reservoir. After getting pressure back to an equilibrium we have had continuous low collection. We've washed all tubing, the internal salt reservoir, the filter below the atomizer, and the atomizer itself. We have adjusted the angle of the atomizer daily looking for any variation in collection, there is none. We have changed the location The salt solution feed tank is expelling salt solution, when we cleaned the internal reservoir it filled quickly with salt solution from feed tank. I turned the pressure up from 15 to 17 psi and have seen a slight increase in collection, however still below the requirements of ASTM B117. Is anyone out there able to provide any other insights that I may be missing? I do not have good customer service experience with Singleton so I'm trying to avoid calling them at every cost. Thank you for any advice that you can offer.
Melissa D.Aerospace laboratory - Tacoma, Washington USA
May 7, 2015
A. Many years ago I had a somewhat similar problem that just "appeared". Checked everything. Changed filters and made new salt solution with no help. The 4th or 5th time that I had it apart, I finally noticed a tiny flap of plastic parallel to the orifice, so no problem. Wrong, when air flowed, it would move the flap and nearly close off the orifice. Cut it off and problem solved.
James Watts- Navarre, Florida
Anyone use the Ascott salt fog chamber?
Q. I have a few questions on our Ascott Salt Fog Chamber and would like it if there were others with that also have one. I am having problems with the atomizer. It is pulsating out the spray and then eventually it stops and just trickles out. I have changed the lines and filers and checked pressures etc. When it does this I do not have anything in my external collection tubes. I am new to this and hope someone can help. Thank you.
LORIE CRONINMETAL LAB EMPLOYEE - FOXBORO, Massachusetts, USA
June 8, 2016
A. Lorie,
Sounds like the atomizer needs to be cleaned. I use a set of weld torch tip cleaners. I bought mine for $5 from one of the major industrial supply companies.
- Horicon, Wisconsin
Thank you for your response. I had changed the atomizer filter and rinsed the top portion and all parts. And I still had issues, so today I changed out the Atomizer and I'll see how it looks after the weekend.
METAL LAB EMPLOYEE - FOXBORO, Massachusetts, USA
Q, A, or Comment on THIS thread -or- Start a NEW Thread