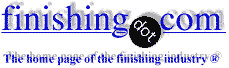
-----
Do It Yourself Nickel Plating onto Steel, p.2
< Prev. page (You're on the last page of the thread)
Q. I recently tried to nickel plate several steel parts and 2 brass rods about 5" long x 1/8" Dia. all in the same bath and at the same time. I left them in for about 30 minutes, 4 volts, 1.2 amp. The steel parts plated fine but the brass didn't take the nickel. Any answers as to why. They were highly polished. Should I have blasted them before plating? Also, how do I know a bath is worn out. The 6" nickel anode I'm using doesn't seem to be deteriorating at all. Thanks for your help. Bob
Bob Benedict [returning]- Humboldt, Tennessee, USA
April 12, 2013
<
Q. Ted
I wanted you to know your site help me greatly a few years ago when I was setting up a Wood's Nickel Bath. Thanks for being patient and not responding negatively to some of the inputs. Some people have no respect. I set up the bath at 59 grams of nickel per liter. It has risen to the low 70's due to anode etching. We keep the % free acidity at approximately 14 %. I was planning to remove some of the nickel back to 59 g/l. I haven't seen any problems with the high nickel content. I would like your comments on this. Thanks again
Dickie
- Laurens, South Carolina, USA
September 4, 2013
by Jack Dini
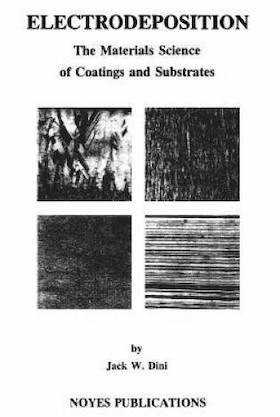
on eBay or Amazon
or AbeBooks
(affil link)
A. Hi Dickie. I'm feeling old today because I remember Donald Wood (dec.), the inventor of Wood's Nickel, very well. I lived near a farm stand / pie stand and would sometimes bring him his favorite, pumpkin pie, when I visited his shop.
Wood's nickel is not intended to be a plating solution, but a strike solution for activating stainless steel and old nickel plating. The reason it is low in nickel content is so the HCl can attack the substrate and get it active and keep it active until it has some new nickel plating on it. So, you judge the effectiveness of Wood's Nickel by the adhesion it offers. If it's doing what you need it to do, it's probably okay. Jack Dini's "Electrodeposition" has a great chapter titled "Adhesion" which deals with Wood's Nickel quite deeply.
Regards,
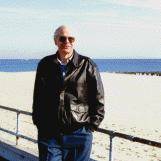
Ted Mooney, P.E.
Striving to live Aloha
(Ted can offer longterm or instant help)
finishing.com - Pine Beach, New Jersey
September 5, 2013
November 23, 2015
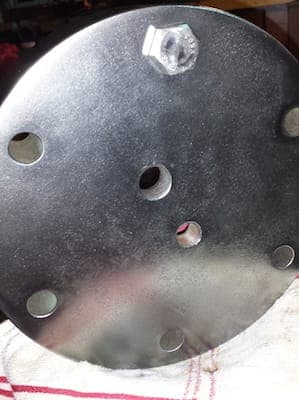
Q. I recently attempted electroplating an old single cylinder engine head. The head is cast iron, and originally came plated, but essentially all that was left of the original plate was where the hex bolt heads had it covered up (engine is about 100 yrs. old).
I used pure nickel in the recipe for nickel acetate, along with vinegar
⇦in bulk on
eBay
or
Amazon [affil link] .
My setup was amateurish, (five gallon plastic bucket, with 5 nickel plates suspended in the solution from copper wire, which I connected to a low volt wall charger + wire.
Negative hookup on the object was a cleaned nickel 55 welding rod bent to fit securely in one of the bolt holes on the head.
After about 2 days, the head seemed to be plated nicely, and polished up quite well. 2-3 days after that, I noticed a very light brownish powder in spots on the finish.
I wonder if the nickel plate is not thick enough, or would the major mistake be using less than a pure nickel rod for the negative hookup? Content of the negative rod is 55% Ni, with the remainder being iron, and several trace minerals, including copper.
I also had earlier plated two pipe fittings for the engine with the same setup, and haven't noticed any "rust" powder appearing on these.
Thanks for any help/advice
Rebuilding vintage engines - Scarbro, West Virginia USA
Q. How do you test the nickel content of your solution?
I have been lucky enough to have been given a few liters of premixed nickel plating solution, brightener and some copper plaiting solution formulated by an industrial chemist :) The stuff works a treat however down here in NZ finding pure nickel to use as an anode is not an easy task.
For the anode I ended up getting my hands on some nickel battery strapping. This is 99.95% pure and seems to be working well so far.
Having done a fair amount of copper electroforming and battling with oversaturated copper solutions I was wondering if the same thing happens with nickel and if so how can you test and balance the solution?
Im not overly keen on having to build a backyard mass spectrometer at the moment but it is on the long list of toys to add to the workshop :)
evil genius - Howick, Auckland, New Zealand
September 16, 2017
A. Hi Boris. It is very unlikely that your nickel anode will dissolve too readily. It is customary to use sulfurized nickel anodes to assist in dissolution because the problem is usually the opposite.
Please study up on Hull Cell ⇦ huh? . I think your next step should be to build a backyard Hull Cell rather than a backyard mass spectrophotometer :-)
Luck & Regards,
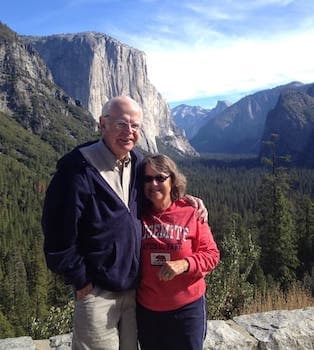
Ted Mooney, P.E. RET
Striving to live Aloha
(Ted can offer longterm or instant help)
finishing.com - Pine Beach, New Jersey
September 2017
Q. Thanks Ted :)
I will see if I can locate some sulfurized nickel locally. I did a few test plates last night with the setup I have that seemed to work quite well; however, the second piece, which was an electroformed copper acorn, started to get a nice layer on it then for some reason the nickel started to get stripped back off mostly around where the cathode was attached. It left a pretty awesome effect but was not ideal.
Not sure if this is a result of a depletion of the nickel in the solution, a power supply issue or some other problem.
- Pakuranga, Auckland, New Zealand
September 16, 2017
Q. Finally I have managed to locate some nickel locally however it came in the form of small blocks and not strips. they are about 25 mm X 25 mm X 15 mm thick so for my home setup these will last a long time...
Currently my bath is a pyrex jar. It was great for strip, however, with these anodes it's going to be a little harder to join them. So I had several thoughts...
Drill a hole in them and string them together along a stainless rod was my first thought but I was not sure if the stainless is going to break down and start to contaminate the nickel. I thought about getting some titanium but that comes at a pretty high cost down here.
If however Stainless does not break down I was thinking about maybe making a stainless bath and just dropping the anodes in to the bottom; then all I need to do is connect the bath to the + of the supply and start plating.
For the time being I may just run a sealant in the outside of the stainless shaft so it does not come in contact with the solution but would like to find a better alternative.
I would appreciate any advice on this...
- Pakuranga, Auckland, New Zealand
September 23, 2017
(affil links)
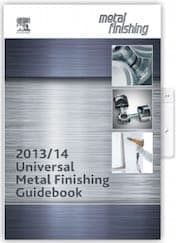
free pdf is currently available from academia.edu
Hi again. You are certainly welcome to design things any way you wish and experiment with them, Boris.
But I think you will make it difficult on yourself if, instead of starting with conventional practice and modifying it as necessary for economy and your situation, you instead re-invent the art starting from nowhere.
Please get hold of a plating book like the Metal Finishing Guidebook.
to see how & why things are normally done, and then you'll be in a better position to make any necessary modifications. A stainless steel tank has no shot at proper plating of any item with any metal; and a submerged stainless steel anode rod in an acidic solution won't work either. Good luck!
Regards,
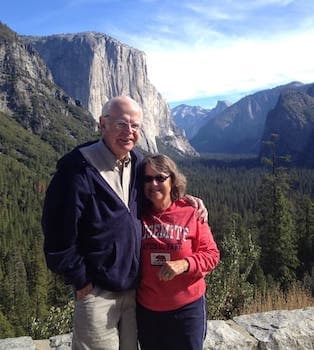
Ted Mooney, P.E. RET
Striving to live Aloha
(Ted can offer longterm or instant help)
finishing.com - Pine Beach, New Jersey
September 25, 2017
Q. Thanks again Ted,
As stated the solution I have is premixed from a supplier of plating solutions, was put together for me by an industrial chemist along with a bottle of brightener.
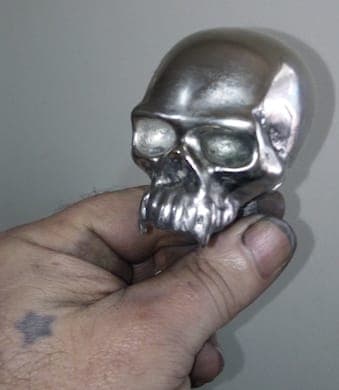
Using a Nickel anode and the the plating power supply I built with regulated voltage and current I get a really nice layer of Nickel on parts, this includes the plastic parts that have been coated in a layer of graphite to bring their surface resistance down to about 300 Ohms.
The voltage is set on the supply to about 3V and the current is reduced dependent on the size of the object. The nickel deposits using this method are coming out consistently at about 35 microns. I have however also managed to do a couple of test parts where the plating was a lot thicker but did find that there seemed to be a lot of internal stress on the plastic part as it seemed to warp slightly. This may or may not have been as a result of the plating and I have not had the chance to reprint the test piece to see if it was.
Ideally I would like to use a titanium mesh to hold the anode in the solution but in New Zealand it's not viable to purchase this in small quantities and a large amount is just not viable.
The tank I used when I did my apprenticeship many many moons ago was a plastic tank with a kind of canvas liner with all of the nickel anodes stacked around the edges. The + was feed in to the tank at one end and all of the nickel "bricks" made contact with each other. This however is only really viable for a larger tank.
We used a stripping tank that was made from Stainless Steel and filed with cyanide. My thoughts were to look at making a small stainless tank and lay all the nickel anodes in the bottom and around the sides at strategic points. this would mean they would all be connected to the + via the stainless tank wall however I was not sure if the stainless would be eroded and contaminate the plating solution.
Boris
- Pakuranga, Auckland, New Zealand
How to calculate amperage/voltage for Watts Nickel?
Q. I am trying to nickel plate steel bicycle parts, I have the Watts bath prepared and the water tank heater ready to go. I bought a variable DC power source but my question is what should I have it set to and how long should I run it. I am doing this in about 1 gallon of solution. The surface area that I want to plate is about 20 sq inches.
Side question is, how many times is the Watts bath solution good for? How many times can I plate something in it before having to dump it and mix a fresh batch?
Thanks so much for your help.
- San Francisco California , USA
November 30, 2017
A. Hi Andrew. Let me take your last question first because it will make some other things that people have said a bit clearer: your plating bath can theoretically be used every day for decades ... and industrial platers often achieve exactly that. In industrial plating, one of the goals of the process control is equilibrium -- the solution operates at the same temperature, same pH, same nickel concentration, and same current density every hour of every day, year in and year out.
Sometimes hobbyists will tell us we're full of beans and "you really don't have to worry about blah blah blah". And they're not exactly wrong -- you can often get a good part without ideal conditions, but the goals in industrial plating is every piece is a good piece, you can't afford to wreck your solution and waste treat hundreds or thousands of gallons. A hobbyist can perhaps use an old chunk of nickel as an anode whereas the industrial plater must use nickel "S rounds" or other highly purified sulfurized nickel or he will have ever increasing problems every day :-)
Regarding current and voltage, the first question is whether the part must come out of the tank bright & shiny or you are willing to buff it. If it must be shiny, you'll need to plate at 30 - 40 amps per square foot of surface area. If you can buff it, you can plate at half that rate or lower, and encounter fewer problems. The voltage is whatever is needed for the current density you want, and depends on the anode to cathode spacing, but will probably be about 3 or 4 volts in a 1-gallon tank. As for plating time, look at the "Electrochemical Equivalents" chart in the appendix of The Metal Finishing Guidebook (download it while it's available) and you will see a chart of plating thickness vs. amp-hours; it will be a good start. Good luck.
Regards,
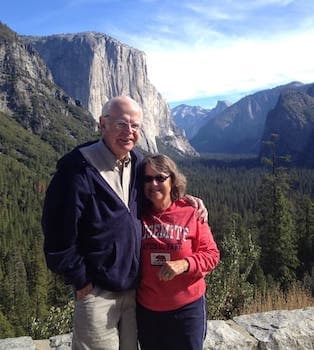
Ted Mooney, P.E. RET
Striving to live Aloha
(Ted can offer longterm or instant help)
finishing.com - Pine Beach, New Jersey
November 2017
How to clean parts before plating them?
Q. I am nickel plating steel bicycle parts, the steel is new and I have sanded and cleaned it to a smooth finish. What else do I need to do to prepare the part for plating? Thanks
Andrew Koltuniak [returning]- San Francisco California , USA
December 2, 2017
A. Hi again Andrew. If you can reach the whole surface of the part, cleaning it abrasively like that is a possibility. Sanding alone, then rinsing, may work. But after sanding, or in lieu of sanding if the part is free of scale, you can use a ⇦ on eBay or Amazon [affil link] with hot water, a little detergent, and powdered pumice ⇦ on eBay or Amazon [affil link] (make sure to wear gloves to avoid finger oils). Rinse, and do the plating immediately after the cleaning.
It's when you can't get to the whole surface, or manual cleaning is too laborious, that chemical cleaning becomes necessary.
Regards,
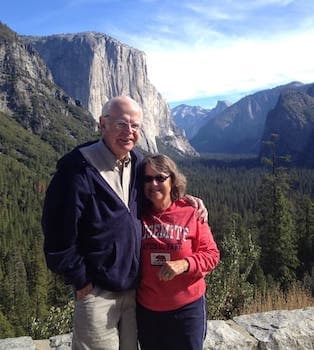
Ted Mooney, P.E. RET
Striving to live Aloha
(Ted can offer longterm or instant help)
finishing.com - Pine Beach, New Jersey
December 2017
Chemical amounts for my solution
Q. Hello again, one more question, I have ordered two pounds of Nickel sulphate, a pound of Boric acid and one pound of Nickel Chloride. I fear that I under calculated the amount. I need 2 gallons of solution and based on what I have seen here and other places I will need about 72 ounces of sulphate, 24 ounces of chloride and 12 ounces of Boric acid to mix with 2 gallons of distilled water. Do these amounts seem correct? If not please tell me how much you would use for a 2 gallon Watts bath.
Thanks again.
Bicycle frame builder and finisher - San Francisco California , USA
December 3, 2017
December 2017
Hi again. As noted above, a typical Watts Nickel bath is:
- 225 to 300 g/l NiSO4.6H2O (nickel sulphate hexahydrate)
- 37 to 53 g/l NiCl2.6H2O (nickel chloride hexahydrate)
- 30 to 45 g/l H3BO3 (boric acid)
270 g/l would be 270/28.3g/oz or 9.54 oz/l,
which would be 9.54 x 3.79 l/gal or 36 oz/gal,
which would be 72 oz for two gallons.
Regards,
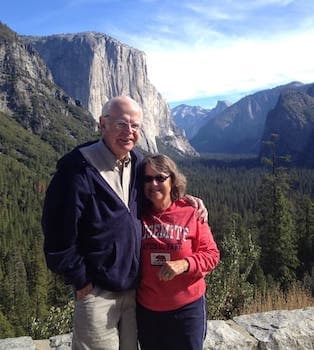
Ted Mooney, P.E. RET
Striving to live Aloha
(Ted can offer longterm or instant help)
finishing.com - Pine Beach, New Jersey
Change salts in Watts nickel bath to acetate
Q. Hi all. I'm a hobbyist and have plated a few parts, but mostly only plate out of curiosity and not functionality. I've been using a Watt's bath, but also have done the Nickel Acetate experiment. My question is... Is it possible to use different salts in a Watt's bath such as directly substituting nickel acetate for nickel sulphate? I believe I read other salts do not have as high of a deposition rate, but that wouldn't be an issue for me. Would maximum plating thickness be affected or anything else? Also, what would happen if I combined my leftover nickel acetate solution with my nickel sulphate solution? I do not want to try for fear of ruining my sulphate solution.
Cortez GonzalasHobbyist - Youngstown, Ohio, USA
April 6, 2018
April 2018
by William Safranek
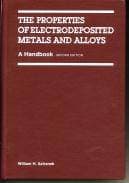
on eBay or Amazon
or AbeBooks
(affil link)
A. Hi Cortez. As a semantics matter it's no longer a Watt's Nickel bath once you add acetate :-)
William Safranek's "The Properties of Electroplated Metals and Alloys" is an interesting work which focuses on what happens to the electrodeposited layer when you change this and that.
His Nickel plating chapter alone is 74 pages. It presents data on acetate baths but there are so many potential variables in plating that discussing mixing an acetate bath with a Watt's bath didn't make the cut.
So, I doubt that you will find anyone who can tell you the specific effects of mixing them, and I doubt that your hobbyist plating is controlled closely enough to really learn anything new by mixing them either. If you intend to continue your nickel plating and improve it and learn from it, I would not mix them.
Regards,
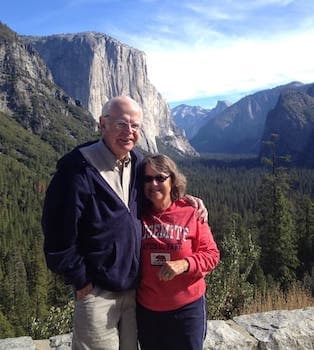
Ted Mooney, P.E. RET
Striving to live Aloha
(Ted can offer longterm or instant help)
finishing.com - Pine Beach, New Jersey
Q. Hi, I have been replating some old (1910s - 1920s) Meccano in Nickel - as it was originally manufactured - using the Watt's bath with pretty consistent success. The set up I have can cope with the smaller items - up to 6 inches, but not the larger pieces. It is a 2 litre glass beaker [beakers on eBay or Amazon [affil link] sitting on a stirrer hotplate - to agitate and get the temperature up to around 50 °C (I am a Chemistry teacher so have access to the normal lab kit which the average DIYer would not).
I have just put together a larger plating bath, but I don't have a big enough glass vessel so have put it in a plastic tub, unfortunately I can't heat this with the hotplate (though I can still agitate as before with a magnetic flea).
My question is therefore, how important is it for the Nickel plating process to have the bath at 50 degrees - if I ran it at ambient temperature (my garage would typically be 10 °C) what effect would that have on the plating - slow it down or make it not work at all? Any thoughts would be gratefully received. By the way I am only after a thin coating, so run the bath for 5 - 10 minutes for each piece at the lower end of the recommended current density range (which approximates to about 4 volts typically).
Kind regards
Andy
- Godalming, Surrey, UK
April 12, 2018
A. Hi Andy. The usual temperature for professional nickel plating is actually 60 °C, not 50 °C. I can quickly think of three reasons that professional platers exercise tight control over the temperature and other operating conditions:
1). For the best deposit properties.
2). To allow continuing operation all day without constant work stoppage for overheating, raising/lowering concentration, raising/lowering pH, carbon treatment, and other interruptions;
3). To prolong solution life; they want their process solutions to last months, years, or decades without need for dumping and waste treatment.
Consider for a second what would happen if a production plater tried room-temperature nickel plating: with all the Kilowatts of plating power they put into the operation, they could only operate for a short while before the bath temperature rose to a very different temperature range; their only options would be to either stop plating to let it cool, install mechanical refrigeration, or simply suffer whatever consequences varying temperatures might cause (variations in solution concentration, degradation of brighteners, different deposit properties, etc.).
So, when hobbyists ask if they can 'get by' without doing this-or-that or without controlling for this-or-that, the answer might be that there are so many variables, from concentration to pH to current density to type of brighteners to temperature to metallic impurities, that professionals simply might not know because they can't afford to let parameters become uncontrolled and they've never tried it :-)
IN general, low temperatures cause significantly slower plating, difficulty keeping enough boric acid dissolved for good buffering, and very high tensile stress in nickel deposits -- but those things may not be a killer for you. Good luck.
Regards,
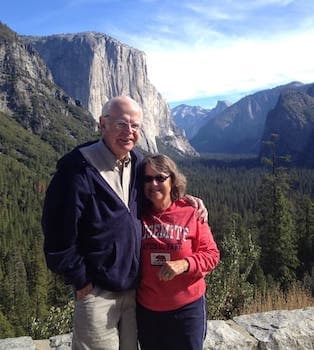
Ted Mooney, P.E. RET
Striving to live Aloha
(Ted can offer longterm or instant help)
finishing.com - Pine Beach, New Jersey
March 31, 2020
This site should really just become a paid membership only access. I hear your arguments, though they're rather weak! The plating industry was conceived first by people who had a thirst for curiosity and experimentation. And I love how the plating pro's here get up on their soapboxes and preach about responsible handling of plating bath chemical waste. Since when did the plating industry give two shits about our environment? Gee mid-70's, sound right? Huh? What do you thunk brought all the severe regulations you have to face in this day and age? So from the turn of the century (late 1800's into 1900's) all the way to mid 1970's you guys (industry) polluted our environment without any regard for the future. So don't bitch about how expensive it is to dispose of your waste in a responsible manner! You (industry) brought that upon yourselves!
As far as the process of electro-plating goes, it really isn't a complex process and yes you can achieve very good results without the fancy proprietary chemicals! Also the truth is that most municipalities' wastewater treatment plants can handle most common metal salts if a DIY'er should be so careless as to dump his plating solution down the drain. Believe me, if an individual was doing this on a regular basis, the utilities company would eventually show up to your residence along with investigators and regulators and you will be fined heavily. Possibly could face criminal charges. But for small quantities of do-it-yourself plating solutions, it is very easy to neutralize those solutions and render them safe.
In fact, I bet one of those 10 yr olds that you keep speaking of who are learning the fundamentals of plating from your FAQ's could turn their solutions into oh, I don't know, say fertilizers for their house plants. For what they are, nothing more than metal salts. Most minerals that are found underground and in the soil all around are also various metal salts.
Now you're right Ted, I also learned how to copper plate a key with nothing more than a couple D-cells, a penny, some wire and a little pinch of Cu(II)SO4 from my chemistry set. I believe I was 11 or 12 at the time. The result not being useful for anything other than learning some fundamental principles of chemistry and physics. There is absolutely nothing wrong with hobby plating by individuals and with just a little bit more knowledge on the subject and a nice regulated linear DC power supply, an individual can achieve fantastic results even using those old archaic recipes you so sharply mention! I cannot think of another industry shrouded in so much secrecy and effort to keep the chemistry unpublished as the plating industry practices. It's sad really, because that concept of thinking has only stifled your ability to discover newer and better processes in a more timely fashion.
Lastly, maybe the fact that so many individuals having a need or desire for one or two simple items to be plated should tell you (the industry) that you're missing out on a growing untapped customer base! It's absurd the prices I've been quoted for having a part which I machined and about the size of my middle finger to have plated!
Yeah, here is a disclaimer: If you are an individual who desires hobby plating at home, then leave this site now! You eon't get the help you are seeking from this site. Finishing.com is for professionals ONLY who work in, or operate a commercial plating operation.
Thanks!
- Colorado Springs, Colorado U.S.A
Hobby nickel plating is taking days
May 9, 2020Q. Hi,
I've been doing some nickel plating lately. Initially, I did the typical homebrewed version with vinegar and nickel electrolyte with OK results after some trial and error. However, upon getting more serious and hoping for better results, I bought a nickel kit with professional nickel salts and an 86 °F aquarium heater.
Results have not been good.
-There are no hydrogen bubbles forming that can be seen by eye.
-Plating is horribly slow, taking days to build a rust protective layer.
-Parts tend to form small pits (almost with appearance of casting pores).
-There is a horrible roughness on the surfaces. I've gotten a sense this is mostly on the upper part as it sits in the bath.
I have tried reading up on this, but it's hard to figure out the cause.
Could I have too low pH? It seems I still have some white powder in the bath that has failed to dissolve.
The anode is like a net shape, and tends to dissolve in an uncontrolled manner. I have speculated if this is what is causing the roughness on parts, but this is just speculation.
Any help is appreciated. Thank you very much.
- Sweden
A. Hi Johan. This is a place of camaraderie, so full name and town please.
a). My guess is that your power supply is not putting out anywhere near the necessary amperage because, if it did, the power would have to go somewhere -- either nickel deposition or generation of hydrogen bubbles. Please see our FAQ on Faraday's Law.
b). The white powder might be boric acid (a buffer). Its solubility is highly temperature dependent; so if you're operating at 86 °F rather than 140 °F it is very likely to remain largely undissolved.
c). Professional platers use both anode bags and constant filtration to remove particles, so roughness can easily happen if you have neither.
d). When you reduce the plating time to under an hour, rather than days, things may get better. Good luck.
Regards,
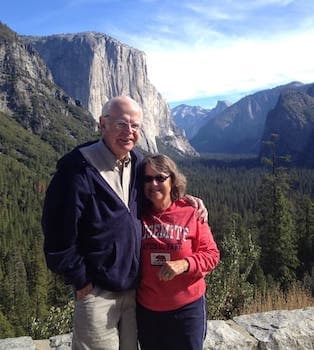
Ted Mooney, P.E. RET
Striving to live Aloha
(Ted can offer longterm or instant help)
finishing.com - Pine Beach, New Jersey
May 2020
July 14, 2020
Q. Hi finishers,
Got a little restless during lockdown here and started revamping an old style heavy duty pasta roller.
I've stripped the powder coat off the steel side plates and am now trying to do a home job of nickel plating them. I figured this should be pretty food safe and can avoid the flakes of blue powdercoat coming off in my pasta.
The surface area of each plate is 800 cm2.
I'm gonna plate in watts nickel plating solution, my recipe for 4L being:
1kg nickel sulphate hexahydrate
0.16kg nickel chloride hexahydrate
0.13kg boric acid
According to the (very excellent) nickel plating handbook I will need a cathode current density of 2 A/dm2 using the Watts solution.
So my cathode will be 800 cm2 = 8 dm2 so therefore I need a power supply capable of delivering 16 A.
Problem is I only have a 0-32V 0-5A adjustable power supply. It is both voltage and amperage adjustable.
SO!
question is, if I go ahead using my 5 A max power supply: will the lower cathode current density merely slow down the deposition of nickel onto my cathode but still give nice results or will I have real problems doing a nice job?
I've already spent quite a bit of money ordering chemicals and nickel anodes and whatnot and don't really want to buy a high amperage power supply in order to do this :(
I even have a sous-vide cooker to setup a bain marie bath at the right temp.
- Melbourne, Australia
A. Hi David. You wouldn't send someone onto Master Chef trying a dish by reading it out of a cookbook ... you probably wouldn't even let them serve it to a large party.
That, rather than the size of the power supply, is the salient point to me. You practice plating on scrap or something of no importance; and after you feel that you've learned enough to apply some personal knowledge to the problem, only then do you try plating your important components. So plate something at 2 A/dm2, then plate another at 5/16 x 2 A/dm2 = 0.625 A/dm2 and decide for yourself whether it will work. My answer is that the current density will be fairly far down the list of potential problems, but yes it will work if you have otherwise learned to do nickel electroplating. You might want to banter with Dave S on thread 26881. Best of luck with it.
Regards,
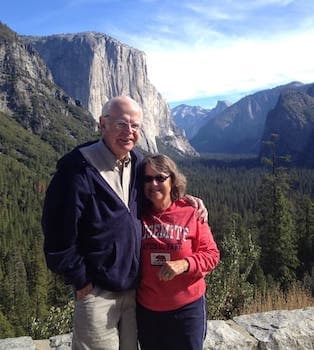
Ted Mooney, P.E. RET
Striving to live Aloha
(Ted can offer longterm or instant help)
finishing.com - Pine Beach, New Jersey
July 2020
Badly nicked plated steel parts
August 5, 2020Q. I posted a few weeks back seeking advice on a home nickel plating setup - it was to plate an antique pasta machine I'm restoring. I ended up returning all the chemicals and other crap for the home plating rig when I found a plating shop willing to do the job for much, much cheaper than I was originally quoted.
It ended up costing $120 to plate 3 items: 2 steel plates (21 x 27cm) and a cast iron wheel.
The cast iron wheel looks OK but has some rust spots in places but the steel plates have lots of bright orange rust all around the edges and lighter blooms can be seen in many places.
I said this to the plater when I paid/collected them this morning and he told me they would just wipe them off with water.
I wiped with water and brake cleaner and of course it did not work.
Taking them back tomorrow. They told me over the phone they will try to fix it.
I've spent $90 having these parts blasted and a further $120 on the plating.
What would need to be done to fix this? it's a real mess I think and feel quite ripped of by the experience?
Any advice on what I should say to the plater?
- Melbourne, Australia
September 29, 2020
Q. Hi, Karl in Miami here. Have 1980 Porsche 911 with the original sacrificial plating on many parts having run its course. To preserve this vehicle as long as possible, I'm dedicated to an ongoing preservation that now entails electroplating. Various nickel plating articles have been studied. What I've arrived at is shared below.
QUESTION here is whether I'm 'on the right track' or 'no, you're not'. I'll continue researching in the direction(s) pointed to.
Am dealing first with steel fuel rails that average roughly 1" x 1" x 14" with a few slight protrusions.
Am inclined to nickel plating primarily for corrosion protection. Nickel's silver colored finish is nicely suitable to the arena these parts are in. Whether final plated tone ends up light or dark doesn't matter. A tight surface -- silky-smooth finish --is considered better than rough/matte for the sake of shedding debris. I know nickel is a 'sealer' rather than sacrificial plating so zero pinholes are tolerable for a world-class outcome. This demand concerns me more than anything else. Am shooting for a 0.001" deposit, a measure I have read being regarded as 'excellent' (where nickel applied for corrosion protection is concerned.) Half that measure is 'acceptable' (according to same article.) Respecting there being a formula for calculating thickness, am more inclined to carefully remove the part from the electrolyte and measure the same spot again and again with a stainless steel caliper, proceeding with plating for however long is required to achieve the 0.001" plating. Will include sodium lauryl sulphate in electrolyte to facilitate the cathode's bubble shedding---again, I'm pin-hole terrified.
Rather than buy electrolyte, am thinking to make it with white vinegar, sodium lauryl sulphate powder, and nickel strip anodes. Equipment on hand: rectifier, voltmeter, glass encased heater, glass thermometer, aquarium-type aeration, clear plastic tub, and titanium suspension/connection wiring. For the sake of creating a more consistent plating thickness, I plan to rotate/move the cathode---perhaps the anodes as well---on occasion (to change their relationship to each other.)
Am not dealing with prep here---I know the elimination of surface contaminants is imperative to a productive outcome.
This said, am questioning if I'm on or off track to get a pin-hole-free nickel plating?
- Miami, Florida
A. Hi Karl. Zinc plated fuel rails are a better idea because zinc is a sacrificial coating rather than a barrier layer coating. But if you're going with nickel for the look, 0.001" is a lot and should be enough for "pore-free". Still, I'd suggest that you go to a hobby plating or jewelry plating supplier for a nickel plating solution rather than trying to make your own from vinegar and nickel.
Luck & Regards,
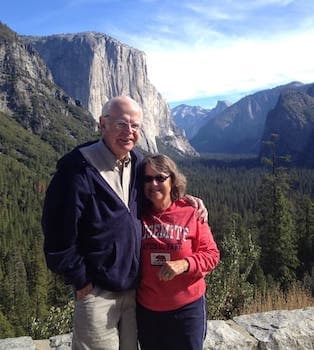
Ted Mooney, P.E. RET
Striving to live Aloha
(Ted can offer longterm or instant help)
finishing.com - Pine Beach, New Jersey
September 2020
Thanks for your advice Ted---will act on that.
- Miami Florida
October 1, 2020
Yellow chromate vs nickel
Q. Hi,
I am learning how to plate zinc and nickel for my stuff but I have a question about corrosion resistance. I am wondering about yellow chromate (after zinc plating) vs plating with nickel after zinc plating. I am using DIY solution found on the web. I am plating automobile stuff to protect against North-east road salt. My current thinking is that zinc plating and then nickel plating on top of that is okay; is this reasonable? I am definitely not an expert here. Perhaps I should paint my stuff after plating to further protect against rust? Thanks for any advice.
Best,
Chris
- Ballston Lake, New York
October 1, 2020
A. Hi. Plating nickel onto zinc plating will probably prove undoable or highly problematic. You'll surely be better off zinc plating, chromating, and painting.
Luck & Regards,
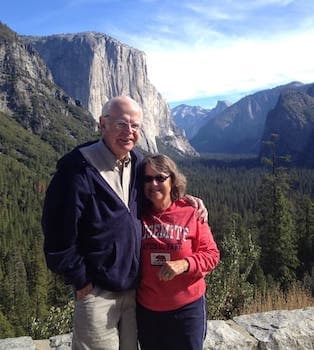
Ted Mooney, P.E. RET
Striving to live Aloha
(Ted can offer longterm or instant help)
finishing.com - Pine Beach, New Jersey
October 2020
February 1, 2021
Q. Hi,
I'm a retired engineer, from England. I'm currently restoring some old guitars, and I want to economically repair a polished nickel-plated item, which has an area of about 1.5 square cm of plating missing. Unfortunately, there are no commercial platers locally, to whom I can take this small job, and anyway, I think I'll enjoy the satisfaction of doing it myself.
If I'm successful, I may progress to experimenting with a bit more plating with Nickel, and possibly also with chromium and gold.
I'd be most grateful if you would please answer a few questions regarding some basics, so that I can make an informed decision on what equipment and technique(s) to try out.
Obviously I don't expect to become an expert overnight - just knowledgeable enough to start in the right direction.
The job in hand is a guitar bridge, made from mild- or carbon- steel, and plated with bright polished nickel. One area has been stripped of nickel by abrasion or perhaps by acidic skin deposits. It looks as though there is a layer of copper plating under the nickel. There is a second component; a small block of brass, also nickel-plated.
I intend to re-plate the bare areas, and possibly follow up if necessary, by adding a layer of plating over the entire surface of the component. I intend to use a commercially available brush-plating kit, or (if you say this is unadvisable), I will buy ready-made materials, and plate in a bath.
If the plating result is perfect and shiny, then I will be (a) delighted and (b) very surprised. I will be quite prepared to build up the plating, then achieve a good finish by polishing & buffing it.
I assume that in "brush plating", the electrolyte simply becomes depleted of nickel and the operator renews the solution on the brush.
So, here are my questions:
1. Regarding activators and nickel striking. Is the purpose of the activator or the strike, purely to prepare existing nickel for further plating? Would I need to use this on the existing nickel, prior to plating?
2. Do I need to first copper-plate either the steel, or the existing nickel, before plating with the nickel ?
3. Regarding 'brighteners'. Do these additives affect the colour / hue of the plating? Or do they affect the surface texture? If they affect colour, can you provide any advice on what additives I should look for, that will produce the colour of bright nickel plating that is commonly found on most musical instruments?
4. Generally, what is the effect on the material qualities of the plating, if the current is too high, or too low? What do I need to look out for, that will tell me to reduce or raise the current?
5. If I use a brush-on technique, then I guess that the plating process varies as the electrolyte is being weakened, and again, when it is replenished on the swab / brush. Is this likely to be a problem, or does it only affect the rate of deposition?
6. My interest is to achieve a smooth shiny decorative finish; even by polishing, if necessary. However, it would also be good to achieve zero porosity, to reduce the possibility of corrosion. Any comments on avoiding porosity, or the effects of embrittlement / stress in the plating etc would be welcome !
Many thanks and kind regards, Keith
- Yeovil Somerset England
January 2021
A. Hi Keith. Before getting to your numbered questions, and for the benefit of other readers, I must remind you that your first efforts should always be on scrap not on important pieces. Plating is part science but part acquired skill, and it's not hard to ruin stuff.
You British tend to call it 'tampon plating' rather than 'brush plating', and that phrase is more descriptive. The metal anode goes into sort of an absorbent pillowcase which is periodically redipped.
1. Proper electroplating can only build onto clean, bare metal, not on to the oxides which quickly develop on most surfaces. So, unless parts are shot blasted, they are almost always dipped in acid to dissolve those oxides. Iron oxides dissolve easily, but nickel oxides are quite acid resistant and a mild acid dip will not remove them; you usually must do a Wood's Nickel Strike.
2. Don't copper plate. Direct nickel plating is easier and better.
3. Brighteners do a lot of things but don't change the hue. You can skip them, or use the generic ones discussed on this page, or buy a solution with them already in it; but be prepared to buff to a shine.
4. Don't exceed 20 amps per square foot and you should be fine.
5. Brush plating is a difficult acquired skill; I'd suggest vat plating if you haven't already bought equipment.
6. In your first attempt at plating you have a tiger by the tail in terms of trying to control everything from cleanliness to activation to current density to solution composition to pH, so the question of how you get a smooth even finish without porosity or stress or embrittlement is difficult. Larry Durney wrote that you can do it is by obeying the letter of the law ... but unfortunately, without analytical equipment you won't be able to do that; the other way is to practice on scrap and be ready to say "well, that didn't work, I guess I should have ..." :-)
That is to say, get some scrap, read the rest of this page about solution concentration, etc., and try it ... then get back to us after you see what you get :-)
Luck & Regards,
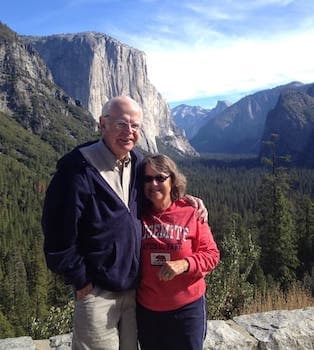
Ted Mooney, P.E. RET
Striving to live Aloha
(Ted can offer longterm or instant help)
finishing.com - Pine Beach, New Jersey
February 2, 2021
Good evening, Ted.
Thank you for such a rapid response, and for your help:-)
I had intended to keep the cost down for such a tiny repair, by sourcing a brush plate kit. Fortunately, I have not yet bought it, so I'll get the materials together for a bath process.
I was really concerned about being able to prep properly, so thanks for the info about using a Wood's Nickel strike.
As you advise, I won't copper-plate first.
Q. Regarding preparation....
If I use some mechanical cleaning, plus chemical degreasing, should I then use the Wood's strike universally on the steel; brass; and existing nickel surfaces?
Should I acid-clean the steel; brass; or copper surfaces, before using the Wood's strike?
Should I remove all the copper from the repair area, or just strike and plate over it?
Obviously, we don't know the original manufacturer's reasons for Cu-plating, but I'd like to know in principle, what possible benefits might be expected from initially plating the steel with copper prior to Nickel?
I guess there are whole books about stress; embrittlement; porosity and other physical issues within the plated layer. Can you just tell me from your experience, would I need to be concerned about any of these properties for this application, and what signs should I look for in the finished plating, that would indicate the presence of any of these "faults"?
I intend to grab that tiger's tail soon-ish, once I've gained a little more understanding. I'll certainly let you know how it all turns out.
Thanks and regards, Keith
- Yeovil Somerset England
A. Hi again. A 30-second dip in 20% or so HCl after cleaning is a good idea for everything, and there's no need to remove the copper. The reason for the Wood's Nickel Strike is that it's the only good way to activate the existing nickel plating. It won't hurt the bare steel, and I don't think it will hurt the exposed copper plating.
The reason I don't want you to copper plate steel is easily dispatched: because acid copper won't stick to steel; only cyanide copper will, and you don't want to mess with cyanide. Why it was originally copper plated is a very long story but is related to the fact that copper can be deposited smooth and bright and in the old days nickel couldn't -- and people stuck with copper plating long after it was no longer really necessary. Decades ago, when I entered the plating business, every car bumper was copper plated; by the time chrome bumpers fell out of fashion, none of them were copper plated before the nickel plating.
If the nickel plating looks good it will be good enough for a guitar bridge, but may not be good enough for a continuous casting mold for a steel plant, or for something that needs to be swaged, or soldered at high temperatures.
Luck & Regards,
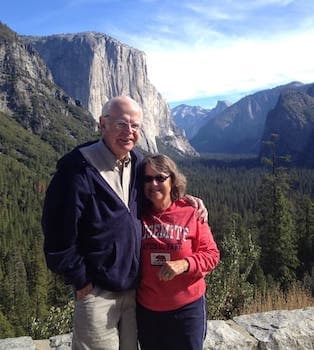
Ted Mooney, P.E. RET
Striving to live Aloha
(Ted can offer longterm or instant help)
finishing.com - Pine Beach, New Jersey
February 2021
Q. Hello again Ted.
I want to check two things with you, before buying my HCl.
It seems to be widely available at 36% w/w concentration. Is it ok to use at this strength, or should I add it to water to reduce it a bit?
Secondly, I can't tell exactly what type of steel or cast iron the item is made from. The component is apparently "molded" .. so I assume cast. It is definitely magnetic, and dense enough to be a ferrous alloy. Will the HCl have the desired effect on any steel alloy? Are there any alloys which may produce an unwanted reaction?
Thanks and regards, Keith
- YEOVIL, ENGLAND
February 3, 2021
February 2021
A. Hi again Keith. People generally use about half that strength for general purpose activation. In general HCl is okay for iron and steel alloys; I've never heard otherwise. But again it is possible to "over pickle" so try 15-30 seconds and watch for any pitting. Commercial plating shops sometimes use plain HCl but often they use proprietary acids with inhibitors which limit dissolution of raw metal, focusing the expenditure of the acid upon dissolving rust and oxides, giving a little bit of insurance against pitting.
![]() |
I greatly appreciate your visits here and don't want to discourage them nor to be rude, but to your " ... want to check two things with you before buying ...", don't be waiting on my account! :-) The reason being: this is a public forum of which I'm the curator, and when I reply too many times in a row, readers start viewing the site instead as a free consulting service -- which discourages the public input which is actually the entire point of the site :-) So I often won't continue long dialogs to their end, but stop with open questions remaining, which hopefully encourages readers to chime in :-) |
Luck & Regards,
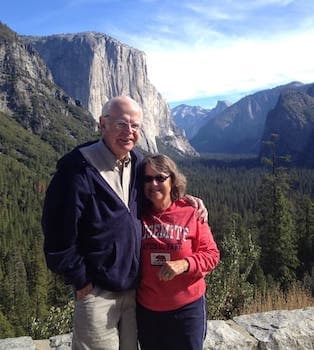
Ted Mooney, P.E. RET
Striving to live Aloha
(Ted can offer longterm or instant help)
finishing.com - Pine Beach, New Jersey
March 24, 2021
Q. I'd like to share my experiences, and my progress so far. It's a bit of a 'full' report, but I did promise that I'd let you know how I got on, after your kind help.
I do also have a question at the end of this, regarding the preparation of a suitable copper electrolyte.
Unfortunately, I could not source a ready-mixed Wood's strike at all, and the only way to source the other electrolytes in a professionally ready-mixed form, in economic quantities, was to buy a small hobby kit, designed primarily for brush plating.
Also of great concern, I was not able to find at the time, any suitable HCl, (again, not in small quantities; only in bulk, and usually only available to businesses.) There were some cleaning products available which appeared to contain HCl, but only at very low concentrations.
I did manage to source a small proprietary hobby kit, which (according to the vendor) would overcome these problems. I therefore decided to buy this kit for my initial experiments, and to consider tank plating at a later date, if I felt that my little project warranted it.
The kit included proprietary 'bright nickel' and 'bright copper' plating electrolytes, and an 'acid activator' . The vendor was unable to supply a nickel strike, but they advised me that the acid activator would adequately de-oxidise and activate the substrate and existing nickel, for copper and nickel plating. This later proved unsuccessful, and the vendor subsequently supplied me with a 'copper flash' solution, which did seem to do the job of activating the old nickel adequately.
The plating pen (anode) in the kit has a spike on the tip, upon which a pad is placed, to hold the electrolyte. (Obviously a new clean pad for each different solution). The pen also has a small bulb fitted, which will glow to indicate current flow. Power is 5v dc.
I decided to use the more badly eroded of my two bridge plates to experiment on, leaving the other plate (with just a tiny area of eroded nickel), for the final job. If I could repair both items, then that would be a bonus!
To clean the workpiece prior to every plating exercise, I used the following sequence: mechanical removal of contamination and/or polishing (if necessary); scrubbing with hot water and detergent; wiping with isopropanol; application of acid activator (with dc power) to any areas which were still bare nickel.
Initial attempts (without the copper flash) to plate both copper and nickel onto the test piece, led to poor results with both copper and/or nickel giving : blackened and burnt deposits; no deposits; and heavy copper powdery deposits which easily rubbed off. I altered my technique, to avoid the burning and loose deposits etc, but still had issues with some areas of the old nickel not accepting the copper or nickel deposits.
I also had issues, in that the current seemed to stop flowing sometimes (despite replenishing the electrolyte on the pad frequently, and re-cleaning).
After these initial setbacks, I obtained the copper flash plating solution, which led to much greater success, although I still had patches on some areas of the old nickel plating, where the copper flash would not adhere, and I still experienced episodes when there appeared to be no current flowing. I could sometimes see a little bubbling at the surface of the work, and a glow in the bulb; sometimes not at all.
I also found that in some areas, when I tried to deposit the flash, it would actually remove some of the earlier deposit!
I wondered if the metal body of the ' en' was contaminating the electrolyte, and affecting the process, so I modified the tools, by attaching the swabs to the pen by copper wire; nickel strips; or titanium wire, for the copper flash & copper plate; the bright nickel; and the activator respectively.
Although I was frequently replenishing the electrolyte on the anodic pad, I hoped that the copper and nickel anodes might also benefit the process, by replenishing ions in the electrolyte during plating.
This led to much greater success, although I still had a few areas of old nickel which would not accept the copper flash. However, these areas DO accept a nickel deposit, after cleaning and using the acid activator.
I would be interested to understand why I had problems with the flash on some areas of nickel. They were easily accessible to clean, although quite a rough 'sand-casting' type of texture. I do wonder if the acid activator is not as effective as pickling in HCl. However, in practical terms, this is not an issue, as all of the areas which require new nickel deposits for a fully serviceable repair, were ok.
After experimenting on the first workpiece, I then successfully deposited copper flash on the damaged area of the second workpiece. I followed this with some bright copper deposits, which, although well- deposited and sound, were extremely thin.
My intention is to build up a good thick deposit of copper, then buff it back, to provide a suitable substrate for the final nickel deposit. I am going to need to tank-plate this copper, as I don't believe I will achieve a thick enough deposit with the pen.
Likewise, I am happy with my experiments with the nickel plating, but again, I will need to use the tank plating method. I'm not worried about the finish too much, as it is easy enough to buff to a good finish.
So, I have now managed to buy a small quantity of the bright nickel solution, enough for a small tank set-up, in readiness for the final job. I'll need to experiment a little first, but with the proprietary solution, I'm optimistic of a satisfactory result.
I have also found a cleaning product (at last, after much searching and a large number of emails) that is simply 36% Hydrochloric acid. I'll add this to some de-ionised water to reduce its concentration, and use it to pickle the existing nickel plating, as advised.
The Copper flash seems to be an adequate substitute for the Woods bath. It seems to adhere to the nickel, following the activator, but I'll be happier now, knowing that I can use HCl as advised. The final job will reveal if the copper flash is a good enough substitute for the Wood's!
My remaining issue is with the Bright copper solution. I was unable to source a proprietary solution in an economical quantity, and I didn't want to make my own electrolyte as per the you-tube 'kitchen-experiment-using-vinegar-and-bits-of-plumbing' videos. I did find and buy some ready-made Copper Sulphate Pentahydrate crystals, which I intended to magically turn into a good quality electrolyte by using (amongst other things) sulfuric acid, as per some rather more professional-sounding instructions which I researched.
ALAS !!! I discovered that it is impossible to buy sulfuric acid in the UK, unless you have a special licencse. Apparently, it is tightly controlled, as it is used in manufacturing explosives.
I've searched numerous sources for information on alternative methods of mixing a good copper plating electrolyte, starting with the copper sulphate crystals, with absolutely no joy!
So, here's my question can anyone please advise me, what is the best way to make a copper plating electrolyte from the copper sulphate crystals ?? I assume some acid is involved, but I cannot use sulfuric. I'm not interested in a bright finish, just a good solid deposit.
Many thanks and kind regards, Keith
- Yeovil England
A. Hi. Is battery acid ⇦ on eBay or Amazon [affil link] unavailable in the UK? If it's not, you'll have to use acetic acid (vinegar) or HCl. You're unlikely to find recipes using those acids in plating books since professionals do not choose to use recipes that are proven to be less satisfactory.
I still feel that this layer of copper is not necessary or beneficial, and nickel plating should be used instead.
Luck & Regards,
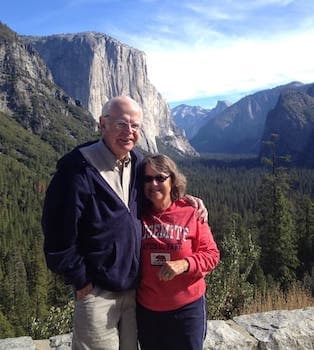
Ted Mooney, P.E. RET
Striving to live Aloha
(Ted can offer longterm or instant help)
finishing.com - Pine Beach, New Jersey
March 2021
A. Try so called Weils copper plating solution -- that is old 19th century formula and can be used instead of cyanide-based solution.
Weils copper plating solution: copper sulphate 30 gms, sodium potassium tartrate
⇦ on
eBay
or
Amazon [affil link]
150 gms, NaOH 80 gms, water 1 lit)...
Second option is pyrophosphate copper.
You can download (free, 0$) probably the best 19th century plating handbook
- Langbein Brants (https://archive.org/details/electrodepositio00languoft).
Hope it helps and good luck!
- Cerovski vrh, Croatia
March 25, 2021
March 25, 2021
Dear Goran,
Thank you for the reference, I'll download it and have a read! Good luck and thank you for your reply. Stay safe, kind regards, Keith
Q. Dear Ted,
Yes, unfortunately sulfuric (battery) acid is not available here, and is tightly controlled. It is a major nuisance as it seems to be an essential (or preferential) ingredient of so many processes!
Naturally, if I could have sourced HCl and a Wood's solution at the outset, I would have followed the recommended (and best) path straight away. Unfortunately, my problem has been in sourcing the right materials, in suitable quantities.
I chose to experiment with copper plating for 2 reasons: (1) because I was unable to source or make a Wood's strike, and the vendor of the kit suggested that the copper flash would be a good alternative. (2) Because several references advise the suitability of copper deposits as a filler for repair of the areas of erosion, prior to final plating.
Now that I have a supply of 36% HCl, which I believe to be of reliable quality, I can make my own Wood's strike (if I can now also source some Nickel Chloride!)
So, I've been researching recipes for a Wood's bath... there are many, and two examples from this forum are:
Quote:"ASM Metals Handbook: 240g/l NiCl2.6H2O - 250ml/l HCl"; "ASTM B 656 STD: 240g/l NiCl2.6H2O - 320ml/l HCl, anodic 30-60sec and then cathodic 2-6min."
I understand that there are many variations in the quantities of the ingredients, but none of the recipes seem to identify the actual strength(%) of the HCl ingredient part !
What % HCl is being referred to? I imagine that there is an industry understanding on this.
To be absolutely safe,I also need to understand clearly how these percentage figures are used. If I have a bottle labelled "36% HCl" then how does this relate to the actual strength of the acid solution, and to further dilution? Can I assume (for example) that by simply adding a volume of 36% HCl to an equal volume of water, that I will have a 18% HCl solution? Or is there any other conversion factor required?
Lastly, regarding filling the defects to repair the surface. Do you mean that I should try to fill the defects with nickel deposits and not copper? I've read that this would be very difficult, and also slow, but if you think it would be better then I could try this by tank plating. I have been thinking of how to mask off the areas which do not require filling. Perhaps petroleum jelly, or grease? Or would that contaminate the electrolyte?
Anyway, thank you for the tip on vinegar or HCL, for a copper electrolyte. It's precisely because of a lack of recipes in books etc (ie avoiding sulfuric) that I asked for your advice! I'll have a look at the reference that Goran kindly sent, but I'd expect that your own knowledge may be a lot more advanced than 19th century chemists :-) Can you recommend any actual recipes using either of these acids please? Thanks and kind regards.
Keith
- Yeovil, England
A. Hi Keith. The need for 'filling' is more common in old diecastings than in steel items, and it can be quite an art. But yes, steel items are sometimes soldered, sometimes brazed, sometimes plated with copper and then 'mush buffed' as an attempt to fill pits. My issue with copper plating is just that, in general, acid copper will not adequately adhere to steel. If you are getting adequate adhesion to the steel & nickel for your purposes, carry on! I would not mask to try to fill pits, but just plate the whole thing.
As for formulas, unless otherwise noted, percentages usually refer to percentage by weight, obviating the need to define the starting concentration. But when people use liquid measure like 1 quart per gallon they are usually referring to starting with the most commonly available concentration. I don't think Donald Wood ever patented or marketed his nickel strike so there's probably no 'official' concentration. But Jack Dini says 240 g/l (2 lbs./gal) NiCl2 and 120 ml/l HCl (presumably of 35-38% commercial strength), and I'd go with his numbers because he actually quantifies the measured adhesion strength.
Luck & Regards,
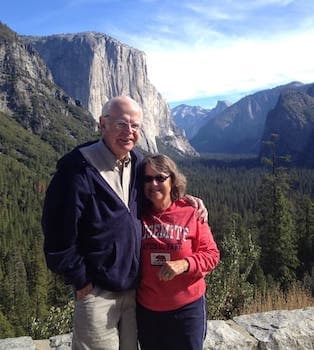
Ted Mooney, P.E. RET
Striving to live Aloha
(Ted can offer longterm or instant help)
finishing.com - Pine Beach, New Jersey
March 2021
June 14, 2021
Q. I am getting these patterns on the brass test part.
Part is about 1 cm square total area.
This pic was at about 150 mA (less than a minute).
I am using a new professional solution and a brightener.
Part was polished to a mirror finish before plating and well cleaned.
- Alpharetta, Georgia
A. Hi Mansour. I think your first attempt to plate was at way beyond reasonable plating rates.
If 1 cm2 is the actual surface area, that's 0.01 dm2, so 150 mA on the part equals 15 ASD (140 ASF). Even assuming that you were speaking of one side, the total surface area would be 0.02 dm2, and 70 ASF is still way too high.
At 40 ma, you are at a reasonable plating rate if the surface area is 0.02 dm2, but if the area is only 0.01 dm2, you are trying to late at 37 ASF, which is certainly doable in production but requires careful control of all of the variables.
Please confirm that 1 cm2 is the entire surface area (including both sides), and that you operating at 140 °F. Meanwhile, cut the power in half again. You definitely have nodules; the picture isn't clear enough to be sure whether you also have gas pits (tiny, shiny hemispherical indentations). Some brasses require copper plating before nickel plating.
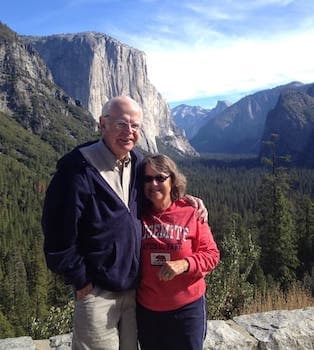
Ted Mooney, P.E. RET
Striving to live Aloha
(Ted can offer longterm or instant help)
finishing.com - Pine Beach, New Jersey
June 2021
⇦ Tip: Readers want to learn from your situation;
so some readers skip abstract questions.
Q. Hi there,
I am Essam.
I am asking about necessary steps to electroplate steel with nickel.
What are the cleaning and pretreatment chemicals and what should I use before nickel plating.
Best regards.
Essam
- Giza Egypt
November 7, 2021
A. Hi Essam. It's very hard to answer questions which are posed in the abstract rather than with your own situation. Some aerospace suppliers would probably sandblast the part and go direct to the nickel plating tank. Manufacturers making tens of thousands of widgets might go to an alkaline soak clean, then a rinse, then an alkaline electroclean, then a couple of rinses, then an acid activation tank, then a couple of rinses, and then to the nickel plating tank. A hobbyist who is plating just a few parts might scrub them with a pumice solution, then rinse them, dip them in 20% HCl, rinse them, and on to the nickel plating tank.
Please advise what you do, what kind of parts and what kind of steel, their general shape (are they blastable, scrubable, or only chemically cleanable?), and how many you're speaking of. Thanks.
Luck & Regards,
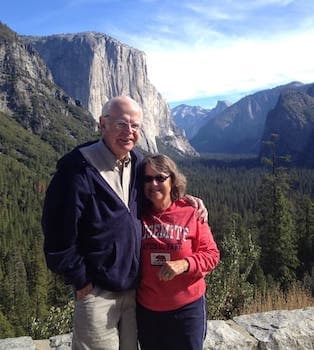
Ted Mooney, P.E. RET
Striving to live Aloha
(Ted can offer longterm or instant help)
finishing.com - Pine Beach, New Jersey
November 2021
Q, A, or Comment on THIS thread -or- Start a NEW Thread