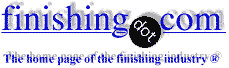
-----
Aluminum de-smut/de-oxidize chemicals & process

Q. I found out a single tank pretreatment chemical, where instead of using three tanks for pretreatment of aluminum before anodizing, one tank can be used to do all the needed pretreatment and gives a much shiny aluminum profile in only 3 minutes compared to the 3-tank pretreatment method.
Do you think it can change a lot in the aluminum industry in terms of cost of production, quality, production efficiency because of less time used in pretreatment among other advantages?
- Kampala Uganda
October 24, 2022
A. Hi David. Thanks to modern technology it has become super easy and free to do a quick preliminary patent search. I think I would suggest that you spend some time seeing if anyone has patented or applied for patents on something similar to what you have discovered. If they have, your discovery will probably not be very marketable. If not, you will start acquiring a feel for what you should do next.
After that you might also post on one of finishing-related groups on Facebook and see if you can arouse any interest. This site doesn't make promote private contact except through clearly labeled advertising ( huh? why?).
Luck & Regards,
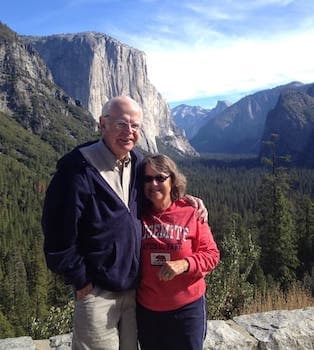
Ted Mooney, P.E. RET
Striving to live Aloha
(Ted can offer longterm or instant help)
finishing.com - Pine Beach, New Jersey
Q. Thank you Mooney ... can you assist me with any link to the Facebook finishing platforms?
Ochola David [returning]- Kampala Uganda
A. Hi again. First you need to sign up on Facebook, then search for "metal finishing" and you will be pointed to some of their groups, and search for "electroplating" to be pointed to others. You may as well spam all of them, everybody else does :-)
Luck & Regards,
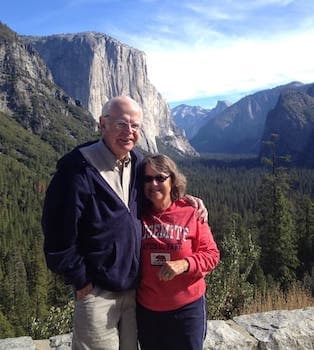
Ted Mooney, P.E. RET
Striving to live Aloha
(Ted can offer longterm or instant help)
finishing.com - Pine Beach, New Jersey
A. Hi David.
Taking a rough guess by the description you gave, it sounds as though you have been introduced to a bright dip type process. there may not be any issue going straight to that tank if parts do not have any type of oils, solvents or other foreign matter on them but if they do then you most certainly would not want to introduce any foreign matter into the tank which you are speaking of. If all of these things line up then I second ted's advice. Start checking things out on line and see how far it can go for you. Good luck to you.
supervisor - Cicero, Illinois
Saporito Finishing Co.

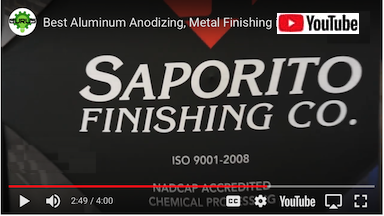
Thank you Philip
Ochola david [returning]- Kampala uganda
October 27, 2022
⇩ Related postings, oldest first ⇩
Q. I am wondering what the pro's and con's of a chromated deoxidizer vs a non chromated deox, is there any benefit to using one over the other?
Steve Adams- cedar city Utah usa
2000
A. Your question is somewhat vague and not easy to answer without any details- what metals or alloys are you deoxidizing? What are you doing to the parts after deoxidizing? Assuming your question concerns aluminum, some people deoxidize prior to welding, others prior to penetrant inspection, others deoxidize prior to anodize (Type I, II, or III) or conversion coating (chromate, chromate-phosphate or non-chrome). The pros and cons of chromates for each application or for each industry utilizing aluminum are different.
The main "con" of chromated deoxidizers is certainly no secret, that is the toxicity of hexavalent chrome. For that reason alone chromated deoxidizers are used only when there is no other deoxidizer which will do the job. For many applications and alloys chromated deoxidizers are overkill, that is not needed because other deoxidizers or desmuts will do the job. For the most part chromated deoxidizers are used only by the aerospace industry and military, where meeting specifications is an absolute must, and where most aluminum that is used is in the form of high strength, easy machining alloys, which contain relatively large amounts of alloying elements which can profoundly affect the ability to meet the specifications.
Phil Johnson
- Madison Heights, Michigan
Nitric Acid to smut or not to smut
Q. We prep aluminum parts for welding. In the process, the part is dipped in a 25% Sodium Hydroxide solution, rinsed, soaked in Nitric Acid and is rinsed. The Nitric is 32 degree baumé mixed 50/50 with water. This all happens at ambient temperatures. Naturally the 2XXX and 7XXX series aluminum turns black in the caustic and then cleans up in the acid. But I have a 6063 (I think) part that turns dark gray in the nitric. 6061 does not do it. Is this normal or has something gone awry? The solutions are both pretty old. I have always thought of nitric acid as a de-smutter, not the opposite.
Thanks for any help!
- West Plains, Missouri, USA
2002
A. Nitric acid is indeed a desmutter, Kelly, but I have seen parts in the 60xx series that refused to clean up except in desmutters that contain dichromate. I'm not chemist enough to know why.
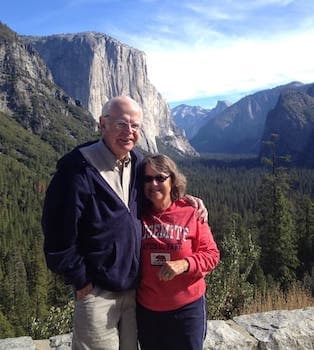
Ted Mooney, P.E. RET
Striving to live Aloha
(Ted can offer longterm or instant help)
finishing.com - Pine Beach, New Jersey
A. You are correct: Nitric Acid is a good deox/desmut for "aluminum", but you listed several alloys that are not "pure" aluminum, having copper, magnesium, zinc and/or manganese in/on the surface.
Mixed Acids, available as proprietary compounds, work much better on the practical aluminum alloys.
Clean nitric acid should probably work well for anodizing since you pull off the alloy smut by reverse current in the anodizing tank; but for chromate conversion you almost always need to use a mixed acid.
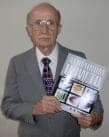
Robert H Probert
Robert H Probert Technical Services

Garner, North Carolina
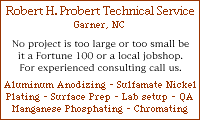
Multiple threads merged: please forgive chronology errors and repetition 🙂
Improving de-smut for chromate conversion coating
Q. I'm researching the chemical conversion coating for aluminum. especially, chromate treatment [MIL-C-5541].
Our factory's process is below:
1.Solvent cleaning (use methyl ethyl ketone )
2.Water clean
3.Alkaline cleaning(use NaOH)
4.Water clean
5.Deoxidation, Desmut (use HNO3, HF, CrO3)
6.Water clean
7.Chromate treatment (use Alodine 1200S)
8.Water clean
9.Dry
Would you mind if I ask you some questions? There are problems in our deoxidation process. Our process is using three acids that are blended in the tank. The materials used are the Al_5052, Al_6061 in the process. I want to improve this process to not use CrO3. Could you recommend for me the replacement material or optimized method in this process? And I want to know the chemical mechanism of the deoxidation process.
Sincerely!
material finishing - Gumi, Gyeongbuk, Korea
2004
A. Although the term "deoxidation" is widely used, I think this step is actually more of a "desmut" process intended to dissolve copper, silicon and other non-aluminum ingredients from the surface. I personally have never seen an anodizing or chromate conversion line that had the two separate steps of de-smut vs. de-oxidize and, although I'm no expert in the chemistry, I think it's just two different names for the same process step, which is done in between etching and anodizing, and whose optimum chemistry depends upon the aluminum alloy you wish to de-oxidize/de-smut.
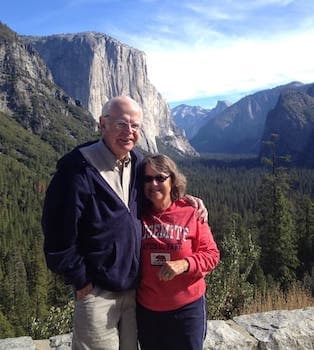
Ted Mooney, P.E. RET
Striving to live Aloha
(Ted can offer longterm or instant help)
finishing.com - Pine Beach, New Jersey
A. For alloys mentioned by you a nitric acid tank with concentration of 300-400 g/l will be enough for desmutting.
Ilya OstrovskyGermany/Israel
Who has a good nonchrome desmut?
RFQ: We have a small sulfuric Acid anodizing line that is mainly occupied with internal work for our manufacturing side. We have recently been informed that our Deoxalume D-90 desmut has been discontinued. We are currently looking for new product to evaluate. We are looking for a non-chromated room temp. desmut. If anyone has any opinions on what is a good desmut and/or could provide a us with a drum or more of D-90 so that we can take our time and evaluate other desmut solutions available we would greatly appreciate your help.
Thanks,
2004
Anodizing - Tualatin, Oregon
Ed. note: This RFQ is outdated, but technical replies are welcome, and readers are encouraged to post their own RFQs. But no public commercial suggestions please ( huh? why?).
Q. We run a chromate conversion line using the following steps Cleaner - Rinse, Desmut - Rinse, Chromate - Rinse. We recently ran into some problems with parts not coating and were asked to implement a Nitric Acid bath or a Sulfuric acid bath. What will these do? and where should we place the baths on the current line (front or end of line) Also can you use Sulfuric for Desmut?
Robert DavisJOBSHOP - Texarkana, Texas
2004
A. Hi Robert. I don't understand about the addition of an acid bath to your cycle -- sorry.
The desmut process removes non-aluminum constituents from the surface of the part. Depending on the alloy, the types and quantities of non-aluminum constituents could vary, so the composition of the desmut could vary. However, the desmut process usually requires an oxidizing agent--and sulfuric acid (except concentrated sulfuric acid) is not one. Nitric acid is a powerful oxidizing agent and could replace your existing desmut or be part of the formulation of a new desmut (if there is substantial silicon in your alloy, straight nitric acid won't desmut it, you need fluoride ion as well).
Insufficient desmutting is usually manifested as a black smut on the parts, hence the name. My suspicion is that your cleaning might be inadequate and that when you make it more aggressive you may see smut left behind, and at that point you may need to change the desmut composition. Good luck.
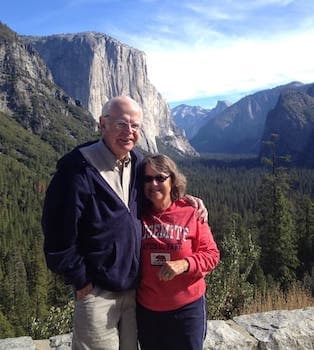
Ted Mooney, P.E. RET
Striving to live Aloha
(Ted can offer longterm or instant help)
finishing.com - Pine Beach, New Jersey
Brown stains on chem film
Q. We are experiencing brown staining on 2024 t3 material with chem film, MIL-C-5541 class 1a. The longer we clean using our alkaline cleaner (Turco) the worse it gets. It does not go away completely using our chromate deoxidizer. We also have tried our nitric deoxidizer to no avail.
David Prescottplating - Seattle, Washington, USA
2006
A. Will the brown film wipe off manually? when your cleaner is cool, can you see a sheen of contaminants floating in it? (oil) It sounds like the copper in the 2XXX series is emerging out of the alloy and not being removed by the deox..
I am assuming you are using a etch/cleaner? or perhaps your cleaner is becoming weak and pre etching the parts exposing the Copper in the alloy...
If the film can be wiped off manually and is not oil, I would increase the desmutting time/check the concentration in the desmut/deox tank and perhaps suspect the organics in the deox are too great.
This is a quick draw answer with the little information I had to work with; I do hope it helps.
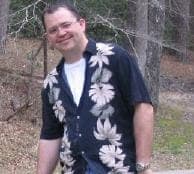
Ryan Cook
Toccoa, Georgia
Q. I am starting a small anodising shop in the UK and urgently need answers to the following questions:-
With extensive research I cannot find the chemical ratios for Aluminium De-smut and whether phosphoric or Nitric Acid is better. Help with this would be gratefully received.
Also the chemical ratios to electropolish aluminium? Again with lots of research I cannot find suitable information.
Owner - Bolton, Lancashire, UK
2007
A. Hi Neil. The short answer, which many newcomers are not aware of, and which may be exactly the answer you are seeking, or may be no help to you, is that the great majority of shops buy proprietary chemicals for this: You don't have to develop your own chemistry; such processes are widely available and come with technical support. Come back if that's the wrong answer for you :-)
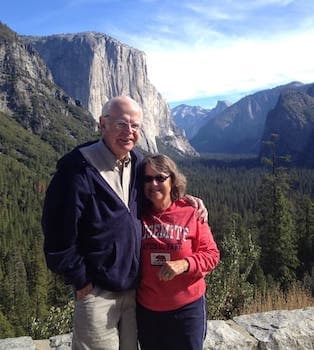
Ted Mooney, P.E. RET
Striving to live Aloha
(Ted can offer longterm or instant help)
finishing.com - Pine Beach, New Jersey
Q. Thanks Ted Mooney for your rapid response. Unfortunately the proprietary chemicals in this country are supplied in volumes that are economically out of my reach and need to purchase small quantities till I get on my feet. My operation will be a small jobbing shop for motorcyclists and some automotive work. Therefore I need the ratios for de-smut and electropolishing as I can buy the base chemicals in much smaller quantities. I hope this explains my situation and hope you can help.
Thank you in advance; it is nice to know that there are people giving there time to help.
Regards,
- Bolton, Lancashire, UK
Treatment &
Finishing of
Aluminium and
Its Alloys"
by Wernick, Pinner
& Sheasby
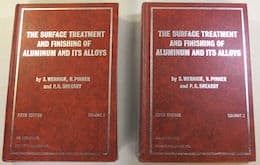
on eBay or Amazon
or AbeBooks
(affil link)
A. Hi again, Neil. Thanks for the kind words.
An important reason that metal finishing distributors are in every large area throughout the world is that they can buy the products in bulk from the manufacturers, and stock them, split orders, etc., in the same way that wholesale vs. retail works in every other field of business. The reason that proprietaries sell at a premium, besides the technical support that is included, is that they are the result of years or decades of research and continuous feedback from trial & error the field. So, yes, we can talk about generic formulas but you will unfortunately be starting over in 1952 :-)
The idea behind desmutting is that when you alkaline etch aluminum, and sometimes when you just alkaline clean it, the hydroxide dissolves the aluminum but leaves behind the copper, silicon, and the other alloying materials as a dark smut. So a desmutter is basically a chemical or combination of chemicals which will dissolve those alloying materials. If the aluminum alloy is cast, and thus contains silicon, hydrofluoric acid or fluoboric acid is a requirement in the mix. If the smut is due to copper, nitric acid is very useful in dissolving that without attacking aluminum. Although chromic acid is decreasingly used due to environmental reasons, it is exceptionally effective on most aluminum smuts. For lab scale work, hopefully these hints will get you started. I do not have formulation experience and don't know if buffers, wetting agents, or other additions are ever used in the proprietary formulations, but Wernick, Pinner & Sheasby will probably cover everything.
Electropolishing will not work except on quite pure aluminum alloys that are designed for electropolishing. ASM Vol. 5 "Surface Engineering" offers good treatment of electropolishing. An alternative also covered in that volume is "bright dipping"; again, proprietaries are available, while for generics you would start with mixtures of phosphoric and nitric acid -- very nasty, fume-y stuff requiring special exhaust ventilation and secondary containment provisions.
Good luck, and if you get anywhere, please let us know how it's going.
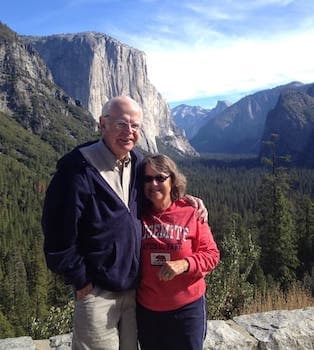
Ted Mooney, P.E. RET
Striving to live Aloha
(Ted can offer longterm or instant help)
finishing.com - Pine Beach, New Jersey
A. Desmut 5% nitric to the litre of water; that's it.
Mr A Hallam- Derbyshire, UK
Multiple threads merged: please forgive chronology errors and repetition 🙂
Chromates, dichromates: what purpose in deox/desmut?
Q. Hi, I'm a new chemical engineer playing catch up in the electroplating industry for aerospace components. I have some experience as a hobby gunsmith but it proves to be of limited utility for the industrial processes on which I'm working now.
I'm the sole chemE on a project to select non-chromated deoxidizers and desmutter solutions for anodizing IC. The current process uses a sulfuric acid and sodium dichromate solution to deoxidize. I cannot find literature that explains the purpose of the dichromate. I understand chromate compounds to be oxidizers so I'm really at a loss as to its purpose.
Help is greatly appreciated and will aid me in understanding the requirements for potential substitutes.
Engineer - Warner Robins, Georgia, USA
March 31, 2009
A. Hi, Joseph. What happens is after you clean the aluminum alloy, you caustic etch it for uniformity, texture, etc. In doing so, you leave copper, silicon and the other alloying ingredients on the surface because they do not dissolve in caustic (nor will they anodize). So the main function of the desmut step you are speaking about is to remove whatever are the alloying materials in the alloy you are using. Chrome based desmutters can be very effective but they are also increasingly disdained due to environmental pressures. I use the term "environmental pressures" rather than "environmental reasons" advisedly. The way we focus on the ounce of chemical instead of the ton of metal we condemn to early replacement is a sustainability travesty :-)
Regards,
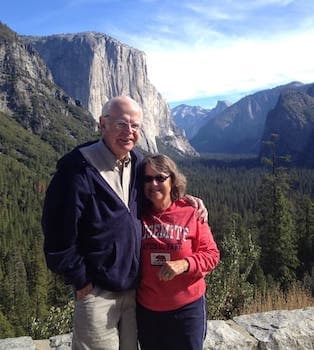
Ted Mooney, P.E. RET
Striving to live Aloha
(Ted can offer longterm or instant help)
finishing.com - Pine Beach, New Jersey
A. Joseph, Hello.
A copy of ASTM B253 is appropriate here. It mentions a Deoxidizing Etch using Sulfuric Acid/Chromic Acid. As chromic acid is present, this is a chromated etch. ASTM B253 also mentions other type of etches and desmutters that are not chromated. It mentions caustic soda ⇦liquid caustic soda in bulk on
Amazon [affil link]
etch. For desmutters, a combination of nitric acid/ammonia bifluoride or sulfuric acid/ hydrogen peroxide or a universal deoxidizer of nitric acid/ sulfuric acid/ ammonia
⇦ on
eBay or
Amazon [affil link] bifluoride.
Most anodizers I know uses caustic soda as an etch followed by nitric acid as a desmutter. There are variations, of course. Good luck.
- Penang, Malaysia
2024 T-3 Should you Deoxidize prior to chem film
Q. Hello All,
This is a general question. When chem filming 2024 T-3 should you deoxidize prior to chem film.
Here is a typical line. Alkaline clean, rinse, deoxidize, rinse, chem film, rinse. Should I skip the deoxidizer when running 2024T-3?
Thanks in advance.
- Rincon, Georgia USA
June 16, 2015
A. Good day Micheline.
I would recommend that you you do indeed deoxidize based on the fact that this alloy has copper, and depending on the age of the panels the copper could/will pose problems as corrosion sites. The deox will also offer a measure of extra cleaning from the alkaline clean as removal of residual alkalinity/organics and provide a water break free surface. This is my opinion only, as I do have very good results after salt spray. Hope this helps.
Regards,
Lab Tech.- Whitby, On., Canada
Q. Thank-you for your response. The problem I have is the manufacturer of the chem film I use is stating that according to MIL-DTL-5541 you should not use a deoxidizer on 2024 T-3.
I don't see this? I only see a reference to test specimens.
I've tried reading up on this but cannot get a clear idea.
I know that sometimes we cannot get clear answers, but I would really like some data I can make a decision on.
Thanks again,
- Rincon, Georgia. USA
June 22, 2015
![]() |
A. You need to change suppliers of chromate compound to one that is on the Qualified Products List of the MIL spec that covers the compound. All listed will confirm the advice given above. ![]() Robert H Probert Robert H Probert Technical Services ![]() Garner, North Carolina ![]() Good day Micheline. Lab Tech. - Whitby, On, Canada |
A. Hello
If you read 3.2 point in the DTL-5541, it says nothing to prohibit the deoxidize.
I recommend a cleanup as follows:
alkaline degreasing, rinsing, nitric acid, rinse, deoxy, rinse, and rinse chem film.
- Guadalajara, Jalisco, Mexico
Q. Thanks All,
I do use a qualified supplier and I agree that I should be using a deoxidizer. I thought I was missing something about the 2024 T-3.
One more thing I did not mention, which may be a factor. This is for Class 3.
- Rincon, Georgia USA
June 23, 2015
A. Just something to add here … when chem filming 2024 material, especially for the RoHS compliant chem film, avoid etching and avoid iron based deoxidize. Both materials have an adverse affect on corrosion resistance. I speak from experience. You are better off with a nitric acid deox/de-smut for 2024.
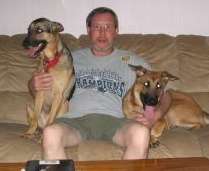
Tim Hamlett, CEF
- West Palm Beach, Florida, USA
A. The Ferric sulphate based (air agitated to re-oxidize 'ous' back to 'ic') is essential for 2024 whether hex or tri, and is especially far better than plain nitric acid on 2000's for RoHS. The above correspondent has "missed" something, probably that his ferric sulphate had sat idle and become ferrous sulfate ⇦ on eBay or Amazon [affil link] . You must air agitate and if not then bring it back with 0.1 %/vol of 30% Hydrogen Peroxide. One vendor actually sells hydrogen peroxide as a proprietary (and he has caused two fire truck involved fires in Atlanta).
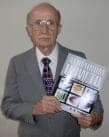
Robert H Probert
Robert H Probert Technical Services

Garner, North Carolina
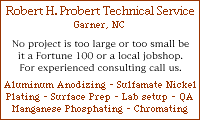
Mr. Probert,
Although I admire your contributions to the industry and have great respect for your knowledge, I haven't missed anything. The information about avoiding the etch and iron based deox/desmut for 2024 alloy before trivalent chromate comes directly from the manufacturer of the trivalent chromate.
Since I began limiting any etch and desmut we perform for 2024, my test panels have yet to fail salt fog testing.
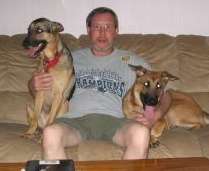
Tim Hamlett, CEF
- West Palm Beach, Florida, USA
Q. Hello,
Thanks for continuing this conversation.
My deoxidizer is sulfuric acid with sodium dichromate(VI) at ambient temperature. I have been using this for years with great success. I am very reluctant to change, but due to customer requirements I may have to.
My reason for not wanting to change this product, is it is user friendly and able to handle 2024 T-3. I appreciate all help but I am still not sure with certainty that 2024 T-3 should be deoxidized?
Thank-you
Micheline Forth
- Rincon, Georgia USA
August 5, 2015
A. Good day Micheline.
I am not quite understanding your dilemma. What I do know, is that the 2024 alloy is predominant with 4-5% copper.
Sulfuric acid will not remove the copper, I believe it will only deal with the oxidation of the copper. The nitric @ 10% (I am using 3%) in the deox will remove any surface traces of copper, offering you the best corrosion protection as can can be proven as salt spray results.
We do a thin film anodize on 2024 (4% H2SO4 B/W), coating weight 400 mgs/ft2, 0.0001" approx.... = Zero pits @ 336 hours salt spray.
I do not process the 2024 with an alkaline etch, as it does expose the copper more readily on the surface, giving a greater chance of occurrence of corrosion sites/pits in salt spray. Copper cannot be anodized.
Hope this helps.
Regards,
- Whitby, On., Canada.
Copper builds up in de-smut/de-oxidizer
Q. Hi, anyone know why copper content in Turco desmut/deoxidizer 6/16 builds up very high? I'm trying to add DE-17 toner, but the copper content still remains the same. We are processing 7050 aluminium. Our film also shows brown stain after desmut.
izham yusop- Penang, Malaysia
August 28, 2018
Q. Good Morning Finishing.com Contributors
In continuation of the DEOX discussion (e.g., topics 41654 and 44432), I am asking for a method of tempering a fresh bath of Nitric Acid and proprietary C-IC 6MU deoxidizer to achieve the proper etch rate.
When the bath is made up fresh the etch rate is measuring 0.6 Mils/Surface/Hour. The recommended range is 0.4 - 0.1 Mils/Surface/Hour.
In the months of testing once my etch rate falls into range my salt spray testing will pass on 2024-T3. When the Etch rate is high it fails with >15 pits.
What is the preferred method of tempering this bath?
Thank You
- Lexington Massachusetts USA
April 17, 2019
Desmut versus Deoxidize on Aluminum
Q. I keep reading in various articles the following maxim in regards to aluminum pretreatment prior to anodizing, chromate conversion coating, zincating, EN plating, etc:
"A DEOXIDIZER WILL DESMUT BUT A DESMUT WILL NOT DEOXIDIZE"
I always thought it was the other way around. I thought an acid or a caustic will ALWAYS remove the oxide off the aluminum surface, but you may get a smut remaining, i.e, the intermetallic compounds of copper, silicon, etc.
A typical desmut to get rid of the copper or silicon intermetallics would be nitric acid + ammonium bifluoride.
In my opinion, it should be the other way around:
"A DESMUT WILL ALWAYS DEOXIDIZE, BUT A DEOXIDIZER WILL NOT ALWAYS DESMUT"
If a desmut solution can get rid of intermetallic compounds of copper, silicon, etc, why on earth does the first maxim say a desmut solution cannot deoxidize, i.e., get rid of an aluminum oxide?
NAVAIR Standards Engineer - Lakehurst, New Jersey USA
April 25, 2019
A. Hi Rade. I've personally never heard that, nor have I ever heard of a processing line having both steps anyway. Although I know that the best chemistry will depend on the alloy, I always believed that whether people called the step de-ox or desmut was just semantics. Maybe I'm learning to the contrary here :-)
Regards,
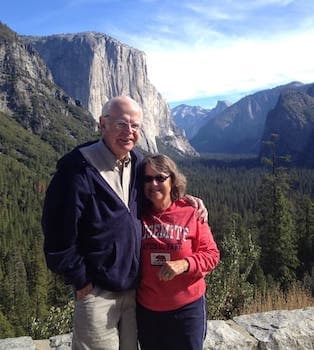
Ted Mooney, P.E. RET
Striving to live Aloha
(Ted can offer longterm or instant help)
finishing.com - Pine Beach, New Jersey
HF/HNO3 Desmut for Aluminum - Control Measures?
Q. I am currently designing an anodizing Type 2 system using sulfuric Acid. As for the desmut phase before anodizing, when do we know to change the desmut solution? Is there a control measure for this? The desmut solution I'm using is HF + HNO3 base. Thank you.
Rekshavan Mani MaranEngineer - Kuala Lumpur, Malaysia
August 19, 2019
Q, A, or Comment on THIS thread -or- Start a NEW Thread