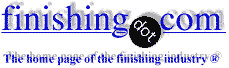
-----
Phosphoric acid anodizing per BAC5555 and ASTM D3933-98
Q. Dear Sirs,
Besides anodize bath conc. , bath temp. and plating current density, is there any other process parameter control on phosphoric acid anodize bath? What is the Al content control for the anodize process?
Thank you for the reply.
- Singapore
2001
Q. I am looking for technical information on PAA (phosphoric acid anodizing). I have searched the web and cannot find much technical info. Do you know where I can get the info? I am trying to set up a small bench top operation. I run a small job shop and I'm just seeking to help a customer out while he does some samples for adhesive bonding tests.
Michael Broussardplating & metal finishing shop - Albuquerque, New Mexico
2001
by J. D. Minford
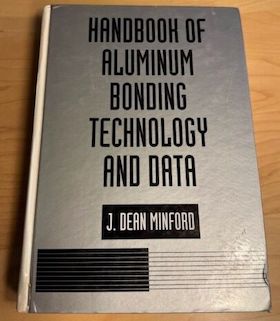
on eBay or Amazon
or AbeBooks
(affil link)
A. Phosphoric acid anodizing is porous and provides a substrate for mechanical locking, so I suppose that is why you need it for the adhesion test. The specification for the adhesion test should have the parameters you need for applying the anodic coating.
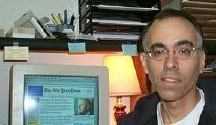

Tom Pullizzi
Falls Township, Pennsylvania
A. It is reference book time. Take a look at this sites "must have" book list. I would take a look at AESF's book (three ring binder) by Grubbs and Montgomery. Very straight forward and the cheapest good reference. There are better, but cost a lot more.
James Watts- Navarre, Florida
----
Ed. note: James' recommendation was from 2001, and even then the "Light Metals Finishing Process Manual" was quite hard to find. If you see an affordable copy anywhere these days, grab it :-)
A. There is very little information on this specialized process. I know of two methods:
The first is used by Boeing for adhesive bonding. It uses 10-12 % by wt phosphoric acid at 70 °F. Anodize at 5-8 ASF for 20-25 minutes.
The second method is 30-50% by volume Phosphoric acid at 80-90 °F. Anodize at 3-10 ASF for 5-20 minutes.
Best of luck to you.
Ira Donovan, M.S.F.Kansas City, Missouri
A. Hi Michael. You may be looking for Boeing's BAC5555 process. You may find something on the web under PAA or BAC5555, or you can do a literature search which will give you some data, or consider contacting Boeing's commercial development office about licensing BAC5555.
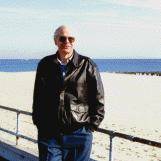
Ted Mooney, P.E.
Striving to live Aloha
finishing.com - Pine Beach, New Jersey
A. The definitive PAA spec is probably BAC5555 from Boeing although if you want a desktop method there are PANTA ["phosphoric acid non-tank anodizing"] or PACS ["phosphoric acid containment system"] systems commercially available.
Ciaron Murphy- South Wales
A. If you can track down ASTM specs, you might try ASTM D3933-98, Preparation of Aluminum Surfaces for Structural Adhesives Bonding (Phosphoric Acid Anodizing).
James Davila- Dayton, Ohio
A. PAA specs would be found in Boeing BAC5555, if you are looking to set up a little bench operation, I set one up using a solution makeup of 15 oz/gal of 85% H3PO4, running at 77 ± 5 °F, 15 amps per square foot for 25 minutes, I used a small piece of metal for my cathode. Good luck
stephen clark- weatherford, Texas
March 4, 2009
Q. I am trying out Phosphoric Acid anodizing for a new customer. I'm using 260 gm/l Phosphoric acid, 4 A/dm sq c.d., time 15 mins, but was unable to get any microns. Can you help me with a process for Phosphoric acid anodizing. My customer requires this process as they need to go for another bonding process.
Thank you,
Johnny Goh- Singapore
2001
Multiple threads merged: please forgive chronology errors and repetition 🙂
RFQs for PAA and related processes . . .
RFQ: Looking for a certified shop to complete F600 (PAA and Bond Primer) with Cessna approval. Please send contact information, I'll forward drawings for an RFQ.
Tim G [last name deleted for privacy by Editor]- Wichita, Kansas, USA
2004
Ed. note: This RFQ is outdated, but technical replies are welcome, and readers are encouraged to post their own RFQs. But no public commercial suggestions please ( huh? why?).
RFQ: Need a source for PAA etch to ASTM D3933-98, mask, BR127 prime and chem-film. Parts are type 7075-T6 aluminum 1/2" x 5" x 23".
Fred V [last name deleted for privacy by Editor]- Bohemia, New York
2005
Ed. note: This RFQ is outdated, but technical replies are welcome, and readers are encouraged to post their own RFQs. But no public commercial suggestions please ( huh? why?).
RFQ: Request for quotation. Need a PAA treatment according to ASTM 3933-98 for 72 plates 0.04 X 3 X 6 of type 2024-T3 aluminum
Can anyone help me farther?
- Ramat HaSharon, Israel
2007
Ed. note: This RFQ is outdated, but technical replies are welcome, and readers are encouraged to post their own RFQs. But no public commercial suggestions please ( huh? why?).
Cathode material and other requirements
Q. I have just quoted a large phosphoric anodize job. While very familiar with MIL-A-8625 / MIL-PRF-8625 [⇦ this spec on DLA] Types I, II, and III, I am not very experienced with this process. I have obtained ASTM D3933-98 covering this subject. My main question is what is the recommended cathode material for this chemistry? Thank you in advance for your help.
Best Regards.
Rick Richardson, M.S.F.Dayton, Ohio
A. Phosphoric acid anodizing is done with stainless steel cathodes. If the anodizing tank is stainless steel, the tank itself can be the cathode.
Phosphoric acid anodizing is usually requested by the aerospace industry. It is used as a surface preparation for bonding. There are very stringent requirements for application and inspection of phosphoric acid anodized parts [for aerospace application]. Usually the customer requires a certification before parts can be processed.
If you have further questions, please feel free to follow up.
Ray Handwerker- Bensalem, Pennsylvania
Q. Hi,
I'm an engineer attached to Goddard Space Flight Center's Advanced Manufacturing Branch. People in our composites group are pushing the electroplating facility to install a phosphoric anodizing process to prep aluminum for adhesive bonding.
Can anyone tell me what equipment is needed to phosphoric anodize aluminum? I need info like tank liners, cathode material, voltage and amp requirements, bath temp, etc.
Thank you in advance.
Joel MitchellNASA - Greenbelt, Maryland
2000
A. Hi Joel. We appended your question to a thread which should answer many of your questions without having to wait for replies. Phosphoric acid anodizing (PAA) is used to give aluminum a good tooth for adhesive bonding. See ASTM D3933-98.
There is also a Boeing spec for it, I believe it's BAC 5555. My understanding is that some of Boeing's competition does not use this process for adhesive bonding, but rather a variant of chromic acid anodizing.
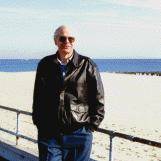
Ted Mooney, P.E.
Striving to live Aloha
finishing.com - Pine Beach, New Jersey
2000
A. I am currently setting up a phosphoric acid anodize (PAA) line. PAA is used to prepare the aluminum surface for acceptance of the primer before bonding. You should note that PAA specifications call for the anodized parts to be stored in a "clean room" environment prior to application of the primer. Parts must be transferred to the clean room within two hours of removal from the PAA line and be primed within 72 hours. After priming, parts can be stored before bonding.
Specifications you might want to obtain for reference include:
- Boeing BAC 5555
- Cessna CSNP 057
- Raytheon BS24554
- Bensalem, Pennsylvania
2000
A. Greetings Mr. Mitchell,
If I may so inquire, why would your company lean towards a phosphoric acid anodize over a chemical film/chromate conversion coating finish. Sure it has hexavalent chromium content in it, but you're still dealing with a product that has less regulation (you are exempt from the chromium standards, because it is a non-electrolytic bath) and the coating is a very inexpensive finish that is geared for adhesive bonding (I have a customer that uses it for 100% this purpose and it works great). Now maybe there are some issues that are addressed inside of NASA that I am not aware of obviously, but I don't see the reasoning behind phosphate coating over chromate. Chromate can withstand 336 and in some cases (mostly material dependent) I have seen in cases it pass 500 hours. I'm not saying phosphoric cannot do this, but why open up a potential can of worms if you can achieve your goal and avoid some headaches.
Matthew Stiltnerplating company - Toledo, Ohio
2000
Treatment &
Finishing of
Aluminium and
Its Alloys"
by Wernick, Pinner
& Sheasby
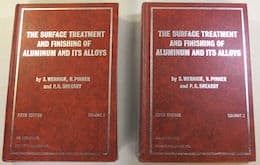
on eBay or Amazon
or AbeBooks
(affil link)
A. Joel, there are some very specific requirements concerning bonding using PAA. There is an engineering document you need to be qualified to for Boeing work. I would suggest starting there with some of the engineering requirements then go to the PAA spec. mentioned above, BAC5555 You will also need BAC5514 for the adhesive primer requirements. Prior to engineering your line you may wish to also think about production flow logistics as Ray mentioned which are critical for best results, as well as meeting most aerospace specs. I cannot talk about certain Boeing processes on an Internet website for obvious reasons but would be glad to speak with you in person if you wish.
Mr. Stiltner, the answers to your questions are partially in the two volume set by Wernick, Pinner and Sheasby, The Surface Treatment of Aluminum and its Alloys, and a number of books on pretreatments of aluminum for bonding purposes. If you are interested, one I might suggest is Surface Prep. Techniques for Adhesives by R. Wegman published by Noyes publications. Another would be Handbook of Adhesives edited by Skeist.
Basically there are some particular surface phenomenon characteristics with PAA which are not acquired elsewhere other than possibly FPL etches, and that could be arguable. Ted is right that some adhesive bonding is performed using CAA as an alternative to PAA, but my understanding is the lap shear test comparisons do not show the same results over time.
Ward Barcafer, CEFaerospace - Wichita, Kansas
2000
A. For background, you might want to check out MIL-HDBK-83377 which replaces MIL-A-83377 (ADHESIVE BONDING (STRUCTURAL) FOR AEROSPACE AND OTHER SYSTEMS, REQUIREMENTS FOR. When we wrote it some years ago, it contained just about everything we wanted for aerospace structural adhesive bonding.
Surely, since the original document was written, there have been advances in structural adhesive bonding. However, many of the basic tests and ideas for quality control, etc., MAY still make sense. If Boeing's BAC-5555 spec is still active, then it would be prudent to consider it's use. The Mil spec was written to get people to use stressed, environmental testing for adhesive bonding quality control instead of relying only on plain lap shear tests and to use good overall practices. At that time, Phosphoric Anodizing was best for most structural adhesive bonding. Chromic acid and other anodizing methods, while good for corrosion protection, seldom proved in environmental stress tests, e.g., salt spray wedge tests, to be best for adhesive bonding. In addition, clad aluminum bonded parts corroded in the clad layer, thus releasing the bond.
If you want a quick and dirty demonstration, make standard peel test specimens from candidate surface preps. Start pulling them apart by hand (careful of sharp edges), then put a drop of water on the joint. You MAY be surprised by the result.
Weldon Scardino, P.E. (ret)- Dayton, Ohio
2004
Q. It is not clear to me if Phosphoric Acid Anodizing is still patented or not. ASTM D3933-98 process is, in practice, equivalent to BAC5555 process but no reference to BOEING process is present. So, is everybody allowed to use D3933 without the necessity to ask the license to BOEING Company?
TAMIRO, Salvatore- TURIN, ITALY
2002
A. Hi Salvatore. I don't know if the patents have run out on BAC5555 or not -- you'd have to do a patent search. Sorry for the non-definitive answer. But I do know from other cases that just because something is a MIL, ISO, ASTM, or other standard does not guarantee that it's not a patented process or that you can use it without royalty. Good luck.
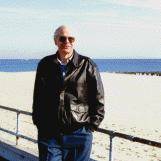
Ted Mooney, P.E.
Striving to live Aloha
finishing.com - Pine Beach, New Jersey
2002
Fatique Issues
Q. Currently we build Aluminum Structure for the Aerospace industry and use Chromic Acid Anodizing (CAA). We would like to switch to Phosphoric Acid Anodizing (PAA) for the corrosion protection of our parts. I need to know what the fatigue behaviors of PAA are in comparison to the fatigue behaviors of CAA or sulfuric acid anodizing (SAA)?
Krag RodewaldAerospace OEM - Dallas, Texas
2004
Q. What are the surface phenomenon characteristics of PAA that make it so desirable for adhesion? Also, are there any alternative platings that can produce the same results?
Jeff Navarro- San Diego, California, USA
2007
A. Hi, Krag and Jeff.
I am not an aircraft engineer and cannot give you an authoritative answer; but maybe this help you until someone more knowledgable steps forward. PAA and Chromic acid anodizing are thin coatings which I wouldn't expect to have nearly the bad effect on fatigue strength that much thicker coatings like sulfuric anodizing have, yet they are somewhat porous and adhere to the substrate well, while being corrosion resistant.
We have a good thread on the site, "Anodizing's Impact on Fatigue Strength", Letter 15354, and also an FAQ: "Introduction to Anodizing" which you may find helpful for this subject.
Regards,
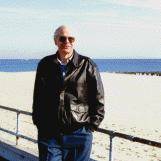
Ted Mooney, P.E.
Striving to live Aloha
finishing.com - Pine Beach, New Jersey
March 16, 2011
(you are on the 1st page of the thread) Next page >
Q, A, or Comment on THIS thread -or- Start a NEW Thread