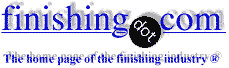
-----
Converting from wet galvanizing to dry galvanizing

for Engineers, Shops, Specifiers
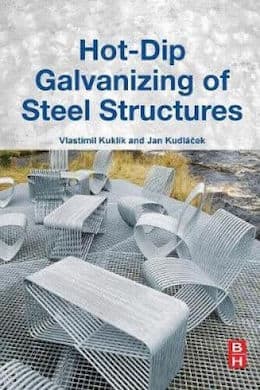
avail from eBay, AbeBooks, or Amazon
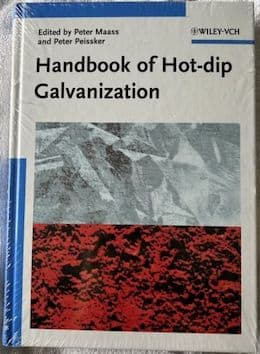
avail from eBay, AbeBooks, or Amazon
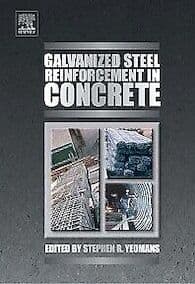
avail from eBay, AbeBooks, or Amazon
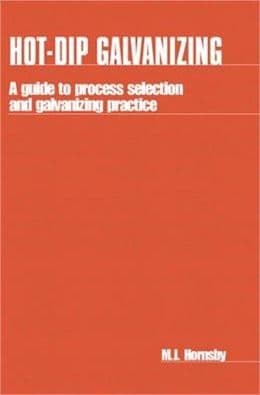
avail from eBay, AbeBooks, or Amazon
avail from Amazon
"User's Guide to Hot Dip Galvanizing for Corrosion Protection in Atmospheric Service" by NACE (1997 only rarely avail.)
avail from AbeBooks, or Amazon
(as an Amazon Associate & eBay Partner, we earn from qualifying purchases)
Q. In Batch dry galvanizing, we are galvanizing Solar Installation components. 1.50 2.0 & 3.0 mm thick. Mostly U Type. Weighing from about 8.50 to 17.9 kgs.
Lately:
MS weight 210841 kgs.
GI " 223901 "
Ash " 2769 "
Hard Zn 734 "
Intend to have an expert opinion if these are correct? If yes why? If not what are the corrective measures?
Employee - Lahore Punjab Pakistan
December 27, 2021
A. Your ash at 1.24% of the galvanized weight processes is very high. You could use a target of between 0.2-0.5%
Your dross (hard zinc some call it) at 0.33% of galvanized weight is good (target 0.5-0.9%)
Another number to summarize these is to state the weight of zinc consumed to galvanize the 223.9 tonnes you state as production. From what you've said, it sounds like it might be about 6%. (A little high).
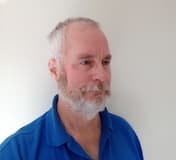
Geoff Crowley, galvanizing consultant
Crithwood Ltd.

Bathgate, Scotland, UK
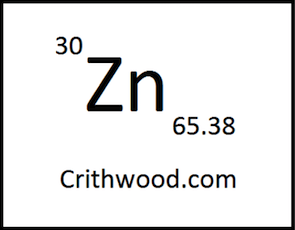
Dear Geoff,
Thanks for reply.
Yes Zn Pick up on MS is around 6.19 %. About net 13060 Kgs on galvanized parts.
But as it is calculated Zn put in the kettle was 18183 kgs. Including Ash, Dross & other wastages.
Q. Could corrective measures kindly be suggested to put the system right?
Thanks again.
General Manager - Lahore, Punjab, Pakistan
A. Good performance in HDG isn't usually a simple question of one or two aspects. It's usually a combination of many things, including: Pickle performance, rinsing, drier, Fe control in flux, dipping rate, withdrawal rate, additions to zinc, types and quantities; steel chemistry, shapes, allowances for drainage of zinc; bath practices, dross performance and maybe more that these. Such a general question of "How can I reduce zinc consumption?" is beyond the scope of a forum such as this, but this forum is good for answering specific questions. There are many questions and perhaps some observations of the factory practices that can help pinpoint the issues to concentrate on in improving performance.
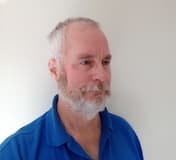
Geoff Crowley, galvanizing consultant
Crithwood Ltd.

Bathgate, Scotland, UK
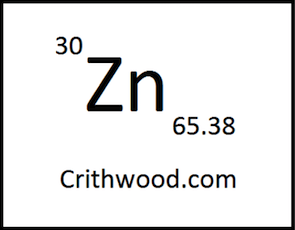
Q. Dear Geoff,
Thanks for guidance,
1.0 To minimize the yield of Ash & Dross is common challenge of the Industry. Many of us are discussing the same at various times.
2.0 Yes the whole process through degreasing to end including steel chemistry, etc., is to be optimized --but it needs investment of time & money. At times many factors may suggest otherwise?
3.0 Therefore, in this perspective it is desired if 1 or 2 most important areas that may decrease Ash & Dross generation could be suggested?
Thanks again.
General Manager - Lahore, Punjab, Pakistan
A. Hi Muktar. In electroplating, which is reasonably analogous to galvanizing, Larry Durney suggests in "Trouble in Your Tank" that the no. 1 starting point, the no. 1 weapon you have, is making sure everything is "letter of the law right". Because not only are things complicated & interrelated as Geoffrey notes but, despite metal finishing being a science, there are numerous things at the molecular level that we don't truly and actually understand. Thus if we let anything be an uncontrolled variable instead of being carefully controlled (and Geoff suggested a long list of such things), cause & effect become essentially indeterminable. So to reduce ash & dross, perhaps step No. 1 isn't to change something, but rather to NOT allow anything to change until you have a reliable and well-documented baseline from which you can very confidently see cause & effect. Just a thought :-)
Luck & Regards,
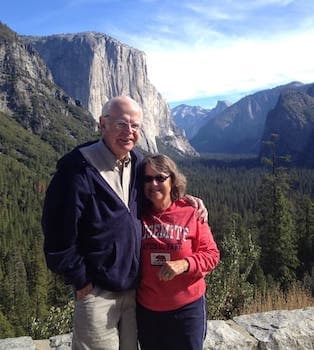
Ted Mooney, P.E. RET
Striving to live Aloha
(Ted can offer longterm or instant help)
finishing.com - Pine Beach, New Jersey
January 2022
Dear Ted Mooney,
Thank you for thoughtful guidance. Correctly said that process has to be right to expect right results.
May I ask another question for expert advice?
Q. For Zn bath appropriation what are purity levels of Al & Pb to be added? Could normal commercial grade Al & Scrap Pb be used?
Thanks in anticipation
General Manager - Lahore, Punjab, Pakistan
A. Mukhtar,
I missed your latest question - I was away helping a customer.
To add Al to a zinc kettle the most common is to use an alloy of about 5% Al. 95% Zn. Al will not melt at the normal temp of a galv kettle, but will slowly dissolve. Using alloy with similar melting point to the kettle helps a lot. It does dissolve slowly and the limits of solution are higher than where problems in general galvanizing becomes a problem. Trying to add "pure" Al usually results in quality problems.
For Pb, the MP of Pb is much lower, and it melts easily, but does not dissolve readily, to just over 1%. The rest melts and due to the much higher density, it sinks where it sits on the bottom of the kettle. The purity isn't so important as what the impurities are? Watch out for Fe, Sn, Cu. As not much Pb is required, usually most scrap Pb will do, or you can buy new shiny ingots of high grade.
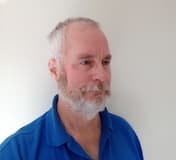
Geoff Crowley, galvanizing consultant
Crithwood Ltd.

Bathgate, Scotland, UK
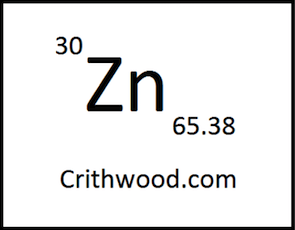
February 20, 2022
Dear Geoff,
Thanks for guidance.
General Manager - Lahore, Punjab, Pakistan
⇩ Related postings, oldest first ⇩
Q. Sir,
We are hot dip galvanizers and currently using wet galvanizing process. Now we need to go for dry galvanizing process, i.e., we will remove blanket of flux over the zinc bath. I would like to know how much zinc I will lose due to increased oxidation either in absolute quantity or as fraction of zinc consumption. Percentage of zinc oxidation may vary from plant to plant so in any case MINIMUM how much zinc I will lose to oxidation. It will be better if someone tells me zinc oxidation will be minimum ____% of gross zinc consumption.
regards,
ERW pipes - Murbad, Maharashtra, India
2006
A. Atul,
For general galvanizers (not automatic pipes) in a wet kettle the ash is usually about 5% to 8% of the zinc used. For general galvanizers in a dry kettle the ash is usually about 10% to 15% of the zinc used. Put a different way, for general galvanizers using a dry kettle based on production, dry ash is about 0.8% (of production) for no ash box,
0.4% for a manual ash box, and 0.2% for a motorized ash box. Pipes galvanizers should produce less dry ash. For automatic pipes a very much better flux solution is required for dry kettle than for a wet kettle. Also the method of pushing the pipes into the zinc is extremely important in a dry kettle (the pipes cannot be allowed to push back up during bending). The best push down method that I know is a "progressive ventilated screw."
Regards,
Galvanizing Consultant - Hot Springs, South Dakota, USA
Q. Sir,
Currently we have wet galvanizing process and remove inactive blanket flux daily. Quantity of removed flux is about 1% of total zinc consumed and it contains around 25% zinc. What should be idle zinc content of this. Now when I will move to dry galvanizing process so instead of removing flux we shall be skimming and removing dry ash, i.e., oxidised zinc. Please let me know what will be/should be its zinc content, metallic and oxide.
regards,
ERW pipes - Maharashtra, India
A. Atul,
If you need to remove inactive flux blanket daily, then something is wrong. Have you tried to add ammonium chloride (as large lumps) to reactivate your flux blanket? While in India I found some commercial flux containing about 20% sodium chloride and potassium chloride. This is not suitable for most types of galvanizing (including pipes). At another location in India they made their own flux using zinc chloride and fertilizer grade ammonium chloride (which upon testing was quite pure). They got excellent results and a %GZU of 5.3% (no credits for dross or ash)."Wet" "spent" top flux is normally about
50% zinc (and is used to make flux or fertilizer). The METALLIC zinc content of "dry" ash is normally above 90%. In fact, an 80% recovery is common in a retort machine marketed in Europe. I strongly recommend that you have your new, incoming flux fully tested.
Regards,
Galvanizing Consultant - Hot Springs, South Dakota, USA
Q. Sir,
Frankly speaking we remove spent flux daily because it is a practice in our plant rather than necessity. Sometimes when we realise that previous day zinc consumption is more or quantity of material available for galvanizing is not very much, then we skip waste/spent/inactive flux removal. In fact we do not know weather we should remove it daily or not. Sometimes when we do not remove it we get flux sticking on galvanized pipes and extraction unit rolls or pipes getting bend due to thick blanket flux cover. Our method of removing flux is that first we add ammonium chloride in powder form (not in lump form) mix it well then we add saw dust, mix it, and then remove it. Normally process is repeated till flux removing trey is full. When black spots occurs we add pre prepared flux or ammonium chloride at the required area of bath. Frankly speaking we do not know weather we should add flux or ammonium chloride to stop black spots.
Another important point is that area of bath from where pipe is withdrawn is naked and not covered by flux. Dry ash continue to form there which is periodically removed and mixed with flux cover on remaining area of zinc bath. when we remove inactive flux it is the mix of flux and dry ash. We have to do this as we do not have pulveriser to remove zinc particles from dry ash, so we mix it with blanket flux and try to melt zinc particles by adding ammonium chloride then we add saw dust and remove the so called inactive flux. Please comment on this.
ERW pipes - Maharashtra, India
A. Atul
With use, top flux becomes rich in zinc chloride (butter of zinc) and lacking in ammonium chloride. "Spent" top flux is about equal molar in zinc chloride and ammonium chloride (mono salt). Most galvanizers use triple salt (one mole zinc chloride and three moles ammonium chloride) to make up top flux and then add ammonium chloride in small amounts during production to keep the top flux active. In time impurities (e.g. iron from the flux solution) contaminate the top flux and removal is required. Using the top flux for a long time gives more dross. The sawdust makes bubbles and increases the depth of the top flux. Other agents have been used.
A company makes a device that recovers about 70% metallic zinc from dry ash. The recovered zinc has about the same composition as the kettle zinc except it is 10 times more concentrated in iron (e.g.
0.4% as compared to 0.04%). This gives slightly more dross but is not a problem. This day I telephoned US rep. and recommended they become sponsor of finishing.com.
If you are able to convert from "wet" to "dry" kettle your dry ash should about double and your dross should become about one-third of what it is now.
Pipe galvanizing is about 20 times more difficult as compared with general job-shop galvanizing. You do need expert help.
What is your percent gross zinc usage (no credits for dross or ash; e.g. %GZU = (zinc consumed/production)times 100%?
Regards,
Galvanizing Consultant - Hot Springs, South Dakota, USA
Q. Zinc used varies according to size, for 15 mm(1/2") it is 7% for
50 mm(2") it is 5% and for 150 mm(6") it is 2.7%. It includes all coating, dust, dross, etc.
When dry ash is mixed with blanket flux and ammonium chloride is added with saw dust as I explained previously, can we recover some zinc. Another thing is that does aqueous ammonia, when added to spent inactive flux, give better results then ammonium chloride. I am under impression that when ammonium chloride is added, ammonia
⇦ on
eBay or
Amazon [affil link] escapes and HCl remains in bath which converts bath zinc to zinc chloride thus causes the loss of zinc. So adding aqueous ammonia is better. Please comment.
ERW pipes - Maharashtra, India
2006
A. Atul,
You are right, in pipes galv. dia. of pipe (actually wall thickness of pipe) is very important because of the variance of surface area. I remember in Southern India that zinc usage (overall) was about 5.3%. This plant was the first one with a withdrawal angle of 14 degrees that I worked with (the previous plants having a withdrawal angle of
11 degrees to be able to use the "walking beam"). This steeper angle gave a better result. Some equipment now have an angle of 25 degrees and then a lay down to 11 degrees for blowing. The results are said to be good.
I have no experience with aqua ammonia adding to dry ash. Indeed adding ammonium chloride on the zinc surface converts some zinc to zinc chloride. However some ash (actually small zinc particles do remelt into the bath. The literature says an 80% recovery is possible with "fresh" dry ash whereas only a 40% recovery can be done with
"cold" and old dry ash.
I have taken coarse zinc blowings and mixed a small amount of ammonium chloride in a 1 inch diameter test tube and heated strongly with a propane burner and recovered 90% of the powder to ingot. I am confident that the dry ash recovery device available in Europe could also handle the coarse zinc blowings. If India has high import duty for zinc, then recovery of zinc from dry ash and coarse zinc blowings is very important economically.
Steam accumulators near the blow head can give much better internal pipes blowings.
Regards,
Galvanizing Consultant - Hot Springs, South Dakota, USA
Q. Dear Dr Cook
While reading your valuable suggestions made to Mr Atul, I take the opportunity to interact with you!
Dr my first submission is that, which flux is most appropriate for steel wire galvanizing, out of- Mono, Di, & Tri ZINC- AMMONIUM-CHLORIDES.The ordinary stoichiometric mixing practiced by some suppliers may not facilitate the controlled formation of Fe-Zn intermetallic layer.I request you to kindly enlighten me on the characteristics of all the three salts.
My second submission to you is that, you suggested UK retort M/C,for distillation. In case the high quality Indian clay retorts availability is in your memory please also advise
REGARDS,
- BHILAI, Chhattisgarh, India
2006
A. Dear Dr. Maitra:
My experience with single strand wire galvanizing is very limited. My article: "Composition, Testing, and Control of Hot Dip Galvanizing Flux," is available from Metal Finishing (the journal published by Elsevier). Online it is metalfinishing.com I think you can pull it off the internet directly. I think it was a "first choice" for the editor that month in 2004. Otherwise you can get it from interlibrary loan for xerox charges. In Pakistan they used straight ammonium chloride for wire flux (likely due to low price and poor quality of commercial fluxes found in much of India).
Your second submission is about the dry ash recovery machine. It is NOT distillation but simply a melting machine. It looks rather like a small cement mixer. In general galvanizing the usual recovery for fresh dry ash is about 70% with this machine.
Regards,
Galvanizing Consultant - Hot Springs, South Dakota, USA
Q. Dear Dr Cook
I feel privileged in getting replies from you, I will try to read the referred documents & may seek your advice again.
Regarding my next point I would like to inform you that we generate bottom sludge in our kettle, and instead of selling it we preferred to destabilize the Fe -Zn intermetallic to recover Zn-4 grade, metal out of it .The recovery in this endeavor was only 50%. To achieve higher recovery we may have to go for Zn distillation & require retort, that's why I requested to you to inform me the sources.
WITH KIND REGARDS
Dr P K Maitra
- BHILAI, Chhattisgarh, India
A. Dear Dr. Maitra,
I think that some zinc producers have distillation equipment to produce very pure zinc. I suggest that you contact them.
Regards,
Galvanizing Consultant - Hot Springs, South Dakota, USA
by Kuklik & Kudlacek
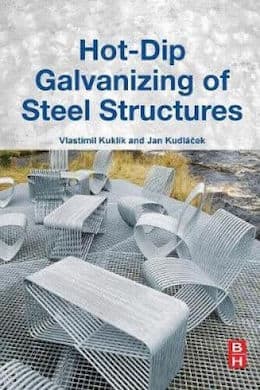
on eBay or Amazon
or AbeBooks
(affil link)
Q. Hello Dr. Cook & others
I just have some doubts with what you have posted before
in this thread and other threads about norms on zinc ash and dross consumption.
We are (wet) galvanizing steel transmission towers and our zinc consumption (after equ) is 4.12% (our target 4%) [Kindly comment on our current consumption and whether target is realistic]. The zinc consumption (before equ) is 4.43 % (104.3 MT). The split up (as a percentage of total production) is
Dross 0.38% (8.75 MT)
Ash 0.48% (11.58 MT) (your suggestion was 0.8%)
Pick up 3.56% (84.30 MT) (we calculated it by subtracting dross & ash from total zinc consumed. Is it a correct way?)
The above figures are well within the limits you have suggested as norms. We don't use ash box.
But while calculating the same as a percentage of zinc consumption, the figures are well above the norms you have stated. Why it is so?
Dross 8.36%
Ash 11.07% (your suggestion was 5% to 8%)
Thanks in advance
- Ahmedabad, Gujarat, India
May 5, 2011
Q. Sir,
We have a general galvanizing unit producing tower /communication steel items with the zinc bath 7.5 x1.0 x1.2 size of zinc kettle.
We maintain flux with double salt Zinc ammonium chloride and maintain 18 -22 Be. the Iron content does not go more than 0.22 % and have continuous filtration unit.
The flux heating is not enough and we are looking into that.Our ash formation is quite high and almost 22%.
Can you suggest any methods to reduce the same.
Hoping to hear from you,
regards
work here as senior Manager - Puducherry, India
January 19, 2012
A. The Ash formation basically depends on
1. Type of Galvanizing Process - Dry or Wet. Normally in Structural Galvanizing we use Dry process with pre fluxing. And Ash formation is slightly higher. SKIM BATH ONLY THE AREA TO BE USED; NOT FULL BATH. REST AREA KEEP IT COVER WITH ASH.
2. In wet bath process add Zinc Chloride approx. 60% in flux; you will get less Ash.
3. Keep the Zinc Bath temperature as low as possible even during production- you will get less Ash.
4. Use of Aluminium also helps in low Ash formation.
- Mumbai, Maharashtra, India
A. Sir:
For this size kettle to be profitable, about 10,000,000 pounds of steel should be galvanized each year. Thus calculating at 7%GZU this would mean a consumption of 700,000 pounds of zinc. For a manual ash box the usual ash is 0.4% of production which would be: 10,000,000*0.004=40,000 pounds of dry ash/year.
You are calculating dry ash based on zinc consumption which means: 700,000*0.20 = 140,000 pounds of ash/year. Clearly this extra 100,000 pounds of ash each year is a major problem. You are producing 3.5 times more dry ash than is normal.
Regards,
Galvanizing Consultant - Hot Springs, South Dakota, USA
⇦ Tip: Readers want to learn from your situation;
so some readers skip abstract questions.
Q. Why do we only use a combination of ammonium chloride and zinc chloride in flux.
krunal patil- nagpur, India
March 22, 2012
A. Dear Raghavan Sir & Dr. Thomas H Cook,
While Raghavan Sir has given data of Ash formation, he has forget to mention the thickness of sheet used to make tube which is galvanized. He has also forget to write if the tube is heavily rusted. The rejection after galvanizing is above 20 % (fabrication error, material defect, improper pickling due to heavy rust as well as galvanizing defect).
Q. My question to Cook Sir is: do the above factors lead to ash formation as told by Raghavan sir or the furnace heating is also to be blamed?
- Vadodara, Gujarat, India
March 26, 2012
A. Mr. Singh:
A rejection rate of 20% and high dry ash formation is quite characteristic of very BAD FLUX. Likely the flux has very high iron (Fe+2) and or high sodium chloride, potassium chloride, calcium chloride, and magnesium chloride. Also the concentration of the flux (baumé) is likely very high.
Regards,
Galvanizing Consultant - Hot Springs, South Dakota, USA
(you are on the 1st page of the thread) Next page >
Q, A, or Comment on THIS thread -or- Start a NEW Thread