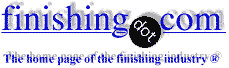
-----
Converting from wet galvanizing to dry galvanizing

< Prev. page (You're on the last page of the thread)
for Engineers, Shops, Specifiers
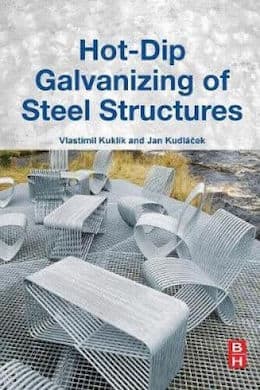
avail from eBay, AbeBooks, or Amazon
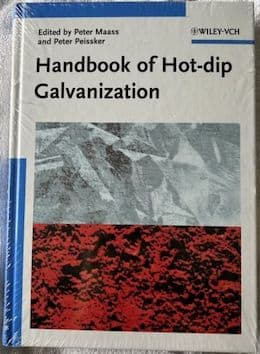
avail from eBay, AbeBooks, or Amazon
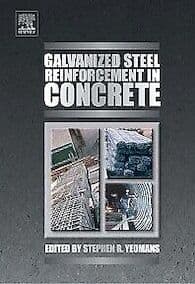
avail from eBay, AbeBooks, or Amazon
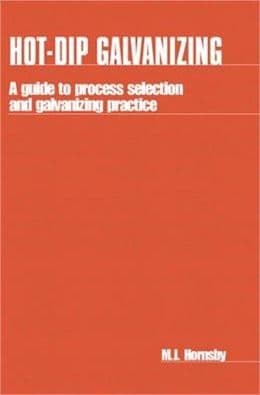
avail from eBay, AbeBooks, or Amazon
avail from Amazon
"User's Guide to Hot Dip Galvanizing for Corrosion Protection in Atmospheric Service" by NACE (1997 only rarely avail.)
avail from AbeBooks, or Amazon
(as an Amazon Associate & eBay Partner, we earn from qualifying purchases)
Q. Dear Dr. Cook,
I have one simple question.
Why consumption of Zn is calculated in MT / hour or MT / year for a dry zinc kettle.
As per me, it should be in Total surface area immersed / dipping and so on...
(In our case 5 MT can have different surface area in each dipping).
Can we calculate on same base?
- Ahmedabad, India
April 2, 2012
A. Mr. Shah:
I have just returned from a two week trip to three galvanizing plants putting old and new technology into these plants. Over inhibited stopped pickling and under inhibited caused very bad fumes in the plant, and short acid lifetimes. Bad inhibitors cause a whole range of problems. There is an easy and effective test for inhibitors and I have published it.
In my previous response in this thread to the question of 20% reject and excessive ash I reported likely bad flux. It is equally possible that something is wrong in the pickling (over inhibited acid causing no pickling or the acid is "spent" in which case testing the free acid content and the iron and zinc in the acid is required, or perhaps the acid is too cold). There are possibly as many as 10 reasons why there are so many rejects and such high ash.
Keep in mind that finishing.com is a website which can be useful, however real on-site WORK is REQUIRED to identify and solve the major problems that are submitted to this site.
Getting back to your question--The large galvanizing plant had a %GZU of 5.5%. Because of the very heavy steel (low surface area of the steel), I am sure that the %GZU is now between 3.0% and 3.5%. If you are a general galvanizer the simple way is to measure %GZU (which is based on steel weight rather than surface area of the steel).
Again %GZU = Total Zinc Consumed/Steel Galvanized times 100%
(No credits for dross or ash).
Regards,
Galvanizing Consultant - Hot Springs, South Dakota, USA
Q. Dear Mr. Cook,
We are using different types of steel which contain different % of Si (0.22% in one and 0.04% in second). Should we care in immersion time of both materials in Zn kettle to avoid extra coating?
Also I have heard that immediate dipping after fluxing & drying in oven is preferable rather than any delay. Is it so? We have 10 to 15 mins delay due to change of fixture after drying. Is that the reason of "Splashing" in kettle? Should we change the sequence?
Regards,
- Ahmedabad, India
A. Sir:
If you get a copy of the Sandlin curve, your question will likely be answered. Phosphorus is even more important than silicon.
I assume that you use HCl and the European fluxing system? If so your baumé is likely high (18 to 25) and your ACN is low (likely 0.6 to 0.9). Also the temperature of the flux solution is likely low (likely around 40 to 50C). Under these conditions even a drying oven is not effective. You likely also lack a good wetting agent.
From the other Finishing.com thread, you will notice that for an HCl plant you have up to one hour after fluxing before galvanizing is required. However if the pH is high and if the product is oven dried (corrosion is faster at a higher temperature) then zinc spatter and black (bare) spots are very likely. Also with the European fluxing system the cook-off time in the kettle is longer giving thicker zinc coatings on the product. I very much like the USA system of fluxing which avoids all these problems. It is a pleasure to answer your questions as best I can on the finishing.com website.
Regards,
Galvanizing Consultant - Hot Springs, South Dakota, USA
Q. Dr. Cook,
We are using fluxing, oven drying and galvanizing in our angles galvanizing plant, doing 2000 tons angles per month. Since our plant has been procured from Europe, I believe we are following the 'European Fluxing' model.
It is the first time, while going through your article, that there is a 'USA fluxing' model that is different from the European model.
Request to kindly highlight differences and merits/demerits in both the processes.
With regards,
- Bhiwadi, Rajasthan, India
May 3, 2012
A. Sir:
I have already made these comments on this website several times. I am pleased that you understand the likely advantages of the USA fluxing system. In South Africa we converted a flux from 30 deg. baumé,' ACN 0.4, temp. 25 C to a flux at 13 deg. baumé,' ACN 1.4, temp 71 C and reduced total galvanizing costs by $9,000,000/year (35,000 MT/year). And this was when zinc was cheap (1985). Also production increased 20% with no additional labor. The advantages of USA fluxing are quite clear.
Regards,
Galvanizing Consultant - Hot Springs, South Dakota, USA
![]() |
A. I'm confused by this European vs USA fluxing method (and the references to 1985). ![]() Geoff Crowley Crithwood Ltd. Westfield, Scotland, UK ![]() Q. Dear Dr. Cook, - Bhiwadi, Rajasthan, India |
A. Geoff,
In the USA I think HCl and H2SO4 are about equally used. Also I think the European and North American systems of flux formulation and usage have not materially changed in the last 30 years. Europeans think they are correct and Americans think they are correct. The advantages of the North American methods are compelling. The NA system requires more control.
M.R.
I cannot in good faith describe in detail what North American exact flux may or may not suit you well. The formulation, testing, and maintaining of good flux REQUIRES "in house" testing and means to correct problems as they occur.
Regards, Dr. Thomas H. Cook, Hot Springs, South Dakota, USA
Galvanizing Consultant - Hot Springs, South Dakota, USA
A. Of the galvanizing plants I know that have been operating for say 20-30 years in the UK, I think most have changed their flux management practices twice.
25 years ago very few had prefluxing systems with a tank of water dissolved flux.
30 years ago many had flux blanket systems.
Today flux control is much more precise, as the margins in the business require it to save on zinc consumption.
Most use double or triple salt ratio ammonium chloride / zinc chloride. An increasing number are using potassium chloride.
Its rare to use sulfuric acid in Europe.
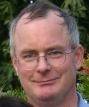
Geoff Crowley
Crithwood Ltd.
Westfield, Scotland, UK
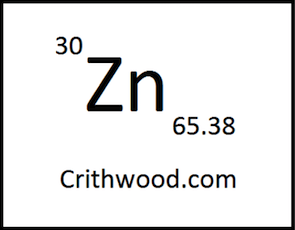
A. Geoff:
As you know the "ACN" = ammonium chloride/zinc chloride. I invented "ACN" about 1985 in South Africa. ACN's for various fluxes are: Double = 0.8; Triple 1.17; and quadraflux = 1.57.
Recently three new plants have been put into the USA using European technology and all are using double salt with high baumé and a drying oven.
Within the last 15 years (here on the ranch) I mixed up a single flux solution with an ACN of exactly 1.00. I sent portions of this flux solution to 13 "certified" testing labs some of which cost me $300 for testing. NONE of these labs came even close to the correct answer. The other ions dissolved like iron, sulphate, etc. were also incorrectly reported. From these data it is clear that testing and control of flux is greatly lacking. I also sent two samples of this flux to two galvanizers that I taught how to test and they got results that were "spot on."
I later published my results in the journal METAL FINISHING which could likely be obtained on the internet or via inter library loan from a large library. The name of this article was something like: TESTING AND CONTROL OF HOT DIP GALVANIZING FLUX.
Shorter kettle "cook out" times in the kettle, much less ash, elimination of icicles on the steel, little or no kettle spatter, and other advantages are characteristic of quadraflux (if properly formulated and maintained). I have been doing this for 40 years. I have tested thousands of fluxes and have found many bad impurities.
Regarding potassium chloride use in a hot dip galvanizing flux: My experience is that it reduces smoke at the kettle, however it increases cook out times giving thicker zinc coatings on the product. It also appears to cause salt and pepper like black (bare) spots in the corners of lightweight product.
Regards,
Galvanizing Consultant - Hot Springs, South Dakota, USA
Q. Can any of you guys post a picture of an ash box or post a link to where I can see one. I am new to the galvanizing industry and am interested in this for my company. And also any automated ash removal systems.
Thanks for the help,
Marcus
- Houston, Texas, USA
August 20, 2012
A. Marcus,
A manual ash box is about 16 inches square on top and about 18 inches square on the bottom (or a rectangle of similar square inches). This semi-pyramid shape keeps the ash from plugging up the ash box. (The sides get bigger as you go down.) Both top and bottom are open. The manual ash box is mounted about 1/3 in the zinc and about 2/3 out of the zinc. The total height of the ash box is about 18 inches.
Without an ash box expect ash to be about 0.8% of production. With a manual ash box expect about 0.4% ash to production. With a motor driven ash box expect about 0.2% of production. Use a thin steel sheet cover to reduce smoke. If you still use lead in the zinc (Prime Western), then the guy working the ash box may be at risk for lead in his blood or urine. If you use nickel in the zinc there may be a nickel exposure to the guy working the ash box. If ash is more than 0.8% to 0.2% of production for the above conditions then there is something wrong with the flux or how you use it. For example, a contaminated, high baumé flux, with low ACNV and high temperature will give very excessive ash. Using this type of flux results in two layers of flux on the product: (1)The outer layer of flux dried to a shell, and (2)The inner layer of wet mushy flux which causes violent explosions upon entry to the molten zinc. This flux and its use is a very bad "hybrid" of North American and European fluxing systems.
I have seen an excellent motor driven ash box at a galvanizer. Also there was a guy making commercial automatic ash boxes, but this site is not for advertising*. I think this guy is now concentrating on immersion heaters.
Regards,
Galvanizing Consultant - Hot Springs, South Dakota, USA
* A small clarification: although these dialogs shouldn't steer readers to vendors, the site is for advertising in the same way as professional journals: advertising should be both paid for and marked as such, and we certainly encourage vendors of automatic ash boxes or any other products to advertise here -- the Editor
Q. Hi.
My name is Meysam from Iran. I heard that when you have been burning the zinc soil, ammonium chloride strewn on the surface of kettle reduces percent of zinc soil. Does this sound true? If this is true, how much ammonium chloride should we strew on the surface of kettle?
Thank you.
- Mashhad, Khorasan, Iran
A. It is true.
A light sprinkling (a cupful or less) sprinkled finely helps to get some of the metallic zinc to get wet and re-enter the molten zinc in the tank.
It creates a lot of fume though.
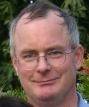
Geoff Crowley
Crithwood Ltd.
Westfield, Scotland, UK
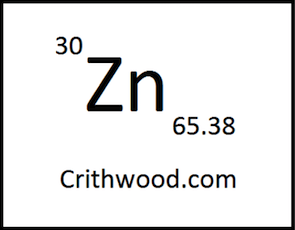
Q. Sir what is the Difference between zinc dust
⇦ on
eBay or
Amazon [affil link]
. Finely divided zinc particles - perhaps size of table salt or sugar, but metallic zinc.
Zinc Ash. Oxides of zinc with perhaps some metallic zinc included.
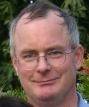
Geoff Crowley
Crithwood Ltd.
Westfield, Scotland, UK
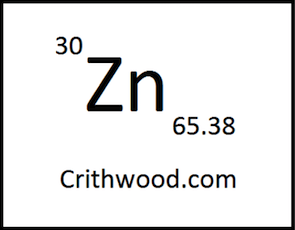
Q. What will I do to have a good pressure of zinc control in galvanizing line?
Andrew adandom mbaolak roofing nigeria limited - nigeria oyo
October 30, 2018
A. Hi Andrew. "Pressure"? Maybe that was an auto-correct and you meant "measure"? More words please -- no fewer words in your question than you want in the answer. Thanks!
Regards,
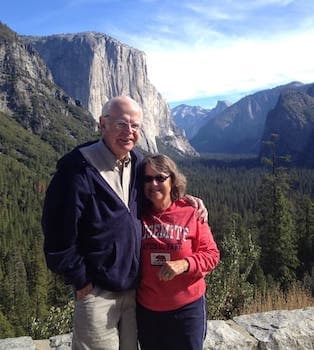
Ted Mooney, P.E. RET
Striving to live Aloha
(Ted can offer longterm or instant help)
finishing.com - Pine Beach, New Jersey
October 2018
Q. Dear sir, please suggest the best possible way to reduce the ash generation in molten zinc bath. In our zinc bath ash generation is about 1.2% of total production.
Amol Balsarafshop employee - Wardha, India
December 9, 2019
A. Regarding galvanizing ash-- I have one client who has 0.1% of production ash. He uses an MZR machine to recover zinc at 85% from unworked ash. His production is 500,000 pounds/day.
I expect you are using very concentrated (high baumé), and likely contaminated flux. Contamination could come from your flux or ammonium chloride supplier or from "hard water." Perhaps your flux formulation is wrong.
Regards,
Galvanizing Consultant - Hot Springs, South Dakota
A. I've found that in general round Europe, and UK, that between 0.1 and 0.3% (or production tonnes) is the typical weight of ash produced.
But MZR can confuse the statistics. Is ash measured before the metallic zinc is extracted or after? We measure both in order to know what's happening at each point of the process. What's happening at the kettle, and what's happening in the MZR plant. Both are important to know.
But post MZR ash must surely be much lower than pre MZR, so comparing an MZR plant with a non MZR plant who reports post MZR ash figures would lead to misunderstanding.
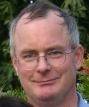
Geoff Crowley
Crithwood Ltd.
Westfield, Scotland, UK
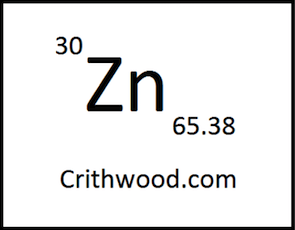
Q, A, or Comment on THIS thread -or- Start a NEW Thread