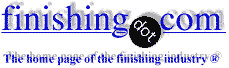
-----
Satin nickel plating problems

Satin nickel tank whitespot. How to remove white spots?
James manualEmployee - Gujarat, India
July 28, 2023
⇩ Related postings, oldest first ⇩
Q. Hello. We plate zinc die cast with cyanide copper then acid copper then satin nickel. But with both zinc die cast parts and mild steel parts after the satin nickel they are getting blackened like black stains. We polish them but it was in vain. Our scrap rate is getting high. Is it possibly excessive satin brightener? or...? So, could you help me?
Emre TunaIstanbul, Turkey
2004
A. Hello,
I think for zinc diecast components you need to give a very good coating of cyanide copper , which is been deposited at lower current and a very smooth deposit, also then a bright nickel coating and at last satin nickel, if the satinizer is not been added at controlled measure it results in black spots , also if the primary additives are not in range also ends up in such problems , carbon treat the bath, dummy , make this a regular practice and work with limited additions of satinizer , ALL THE BEST !
REGARDS
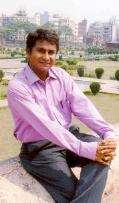
Praveen Kumar
plating process supplier
Mumbai, India
![]() |
A. Raise the Nickel sulphate content above 400 g/l. I know it sounds strange but it is a proven method to solve black spots problem on satin nickel. ![]() ![]() Sara Michaeli Tel-Aviv-Yafo, Israel A. Hi, get long-time stable satinizer. Satinizer breakdown will bring this guest (so called black spots) to your house regularly. Good luck Qutub SaifyAjman, UAE |
Multiple threads merged: please forgive chronology errors and repetition 🙂
Satin nickel burning
Q. Hi, I am doing satin nickel plating on brass hollow tube. nowadays I continuously face a burning problem on above 2 or 3 piece of jigs. what is possible causes of that.
Kunjan VazeMumbai, Maharashtra, India
2005
A. Very probably the burned parts are in the corners with the top corners the most probable. Solution is to use robbers or thieves attached to the rack to lower the high current density in that area. An option is to use a dummy part in that position and a lesser desirable option would be to leave those positions empty.
Shields are an option, but most people find them slowing down racking and de-racking.
Navarre, Florida
A. I have to agree with Mr. Watt's answer, but one more thing I thought of, are you running the carrier in your nickel high enough, this is another possibility of why your getting that burn.
Regards,
Scranton, Pennsylvania
Multiple threads merged: please forgive chronology errors and repetition 🙂
Q. We are in lock manufacturing Business. We have manual satin nickel process on M.S.
We are facing the problem black spots after satin nickel process. We are doing filter on regular basis, at least 1.5 - 2 hours daily before work starts. Now the concentrations of bath are listed below.
1. Nickel Metal = 100-105 gms/litre
2. Chloride as Nickel chloride = 50-60 gms/litre
3. Boric Acid = 40-41 gms/lit.
Please give me a suggestion to solve this problem permanently.
Mumbai, Maharashtra, India
2006
A. Dear Mr. Rajendra,
Please clear the surface with filter paper before starting production, check temperature of bath it should not go above 60 °C.
filtration duration should be at least 4-6 hours with carbon pack, per filter use carbon up to 250- 400 gms.
Enjoy satin plating.
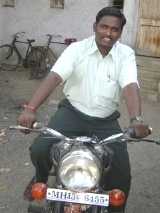
Vishwas Nangare
motorcycle accessories mfgr.
- Aurangabad, Maharashtra, India
A. I know in bright nickel black stains indicate a copper impurity. I do not know if it is the same for your nickel.
Check ppm of copper.
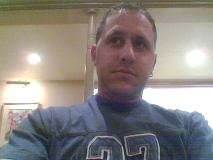
Gary Joseph
Johannesburg,
South Africa
A. Hi there,
One has to take a lot care for filtration in satin nickel , but there are emulsifiers which don't need filtration everyday , organic impurities and excess addition of organics results in black deposition , and maybe there is contamination of metallic impurity , on my opinion you should dummy the solution on regular basis...........and in the end maintain chloride 30 - 40 gms / ltr
Thanks
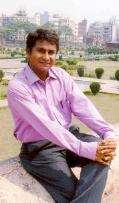
Praveen Kumar
plating process supplier
Mumbai, India
A. Black spots in Satin Nickel do not come from copper/zinc contamination. The cause is insufficient filtration.
Try to filter the solution into a holding tank, clean the plating tank very well and then filter back the plating solution into the plating tank.
You must use filter aid along with the carbon!
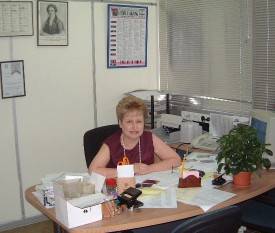

Sara Michaeli
Tel-Aviv-Yafo, Israel
A. Dear Sir,
Tell me your tank size. If your satiniser addition is excess then also this may happened.
The satiniser additive is mix & stir vigorously with 20 times DM water then add to the tank and mix properly, dummy the solution, your problem will definitely be solved.
Aurangabad, Maharashtra, India
Shade variation after bright & satin nickel plating on MS components
Q. We are doing satin nickel finish after copper plating and bright nickel plating. We are getting some shade variation on the components, i.e., within the same components and the matching parts. Due to this our dispatch is getting affected. How to resolve this issue? Is there any rework methods to de-plate the satin and do re satin nickel on those components?
Shanmugam PiramanayagamGoa, India
December 28, 2016
A. Hi Shanmugan,
In the past I have noticed that inadequate final rinsing and drying can be a culprit in situations as described. Do you use post-process IPA?
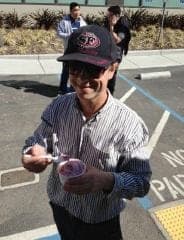
Blake Kneedler
Feather Hollow Eng. - Stockton, California
February 6, 2017
Thanks for all your suggestions.
After proper removal of aged satinizer and increase of Density of the satin bath, now we are getting proper satin finish.
Regards
Goa, India
March 2, 2017
Rusty Satin Nickel Plating
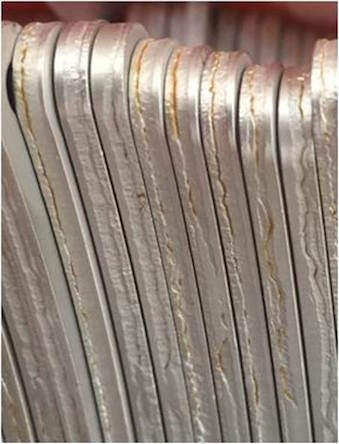
Q. I am an engineer for Electroplating in manufacturing company in Batam, Indonesia.
I have rusty issue in the plating surface, the plating type is Nickel Satin.
Could you help me why this thing happens? Solutions?
Thank you
Batam, Kepri, Indonesia
March 17, 2017
A. Hi Arya. There is a lot involved to achieve successful plating; things could be wrong in 50 different places from an unplateable substrate due to pitting, to poor alkaline cleaning, to inadequate acid dip step, to poor rinsing, to inadequate plating thickness, to poor packaging or storage conditions. I think we can help you, but we would need a pretty cleared detailed question.
I don't know what this component is, and the picture may be deceiving, but it looks to me like you are trying to plate a part that has had no mechanical preparation done, and has very deep welding or casting gouges. What is the substrate please? And could you put a measuring tape or something in the pic to give us a sense of scale? Thanks.
Regards,
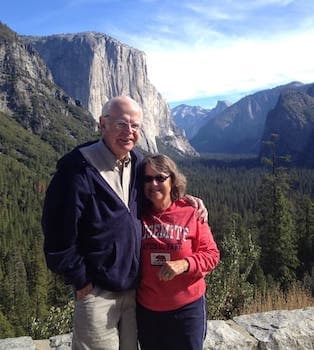
Ted Mooney, P.E. RET
Striving to live Aloha
(Ted can offer longterm or instant help)
finishing.com - Pine Beach, New Jersey
How to reduce the lack of deposit between layers in satin nickel finishing?
Q. We have had a lot of lack of deposit between layers. We rinse the parts after semibright nickel in angel acid rinse, then plate the satin nickel, rinse again and plate microporous nickel. After microporous we use two more acid rinses then we activate the part into a Chrome activator and finally put the Chrome layer. The defects are very tiny lacks of deposit between the semibright and the satin layer. I would like to know what are your suggestions about this item.
Roberto CamargoPuebla, México
February 24, 2018
Q. I am doing regular carbon treatment to satin nickel tank. Before starting production my satin Hull Cell
⇦ huh?
was found to be bright. After addition of satinizer I mix solution properly but still I am facing problem of one or two light spots of sparkling and white patch.
Nickel metal : 86 to 90. Chloride : 27. Boric acid : 40 g/l respectively.
Maharashtra, India
March 19, 2018
Q. We are doing Satin Nickel plating on Motorcycle handlebars in a PLC controlled plating plant. We are getting Shade variation(glossy and matte finish in a single batch) in around 25% of the parts. Customer is not ready to accept such parts.
Whether this is process limitation or process variation? Please give your suggestion to sustain this shade in all the parts equally.
Ludhiana, Punjab, India
April 3, 2018
A. Hi Unhale, hi Paramjit. I might have misunderstood, but it seems that Blake Kneedler and Shanmugam Piramanayagam have already discussed and resolved the same issue in this discussion. Can you phrase your situation in terms of what they have had to say on the matter? Thanks!
Regards,
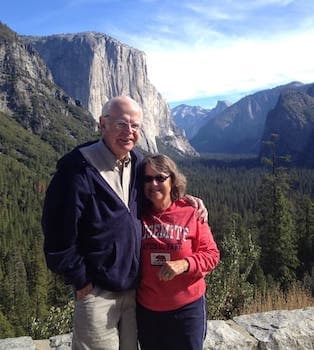
Ted Mooney, P.E. RET
Striving to live Aloha
(Ted can offer longterm or instant help)
finishing.com - Pine Beach, New Jersey
Satin Nickel Layer peels off
Q. Dear Folks,
Can anyone suggest to me that how can I re-chrome Satin Nickel - Zinc Diecast Parts, which are a bit bright. When I am putting it again by doing cathodic and anodic activation into Satin it goes well, but upon doing Chrome it peels off.
Finish is a bit on brighter side, so need it a bit more towards Satin.
Please help.
Uttarpradesh, India
May 18, 2018
Satin nickel peel off from zinc diecasting
Q. Is peel off test required for satin nickel plated zinc diecast components?
Vikrant ShirkeMaharashtra, India
October 28, 2018
A. Hi Vikrant. As a hobbyist you don't need to test anything unless you want to. But if you are supplying someone else, you ought to be supplying quality components, and their purchase order ought to reference standards which include or don't include peel-off testing.
If you do decide to do peel-off testing, and the specs don't detail a required method, thread 23303 is a very good discussion of the subject, covering filing, crushing, tape, and other methods. Best of luck.
Regards,
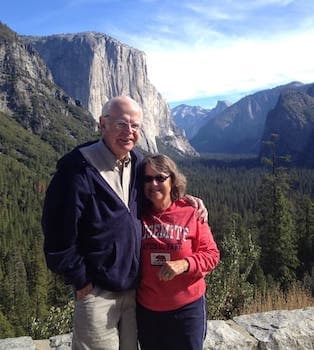
Ted Mooney, P.E. RET
Striving to live Aloha
(Ted can offer longterm or instant help)
finishing.com - Pine Beach, New Jersey
Q. Hi everyone; I am facing peel off problem after copper acid dip at LCD areas in satin nickel process. When I do bright nickel for 2-3 min after copper then follow with satin nickel then no peel off. Tell me the reasons.
Sanjeev SharmaBaddi himachal India
January 12, 2019
? Hi Sanjeev. Have you asked your satin nickel process supplier whether the formulation is suitable for application directly to copper?
Regards,
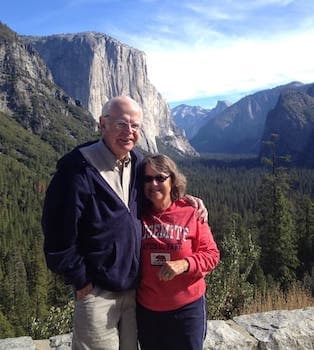
Ted Mooney, P.E. RET
Striving to live Aloha
(Ted can offer longterm or instant help)
finishing.com - Pine Beach, New Jersey
Q. How to reduce the lack of deposit between layers in satin nickel finishing?
We have had a lot of lack of deposit between layers. We rinse the parts after semi-bright nickel in angel acid rinse, then plate the satin nickel, rinse again and plate microporous nickel. After microporous we use two more acid rinses, then we activate the part into a Chrome activator and finally put the Chrome layer. The defects are very tiny lacks of deposit between the semi-bright and the satin layer. I would like to know what are your suggestions about this item.
- Ahmedabad Gujarat
November 5, 2022
----
Ed. note: Related threads --
03013. Satin nickel plating process
43239. Is pearl bright nickel the same as satin nickel?
26692. Filtration system questions for satin nickel plating
Q, A, or Comment on THIS thread -or- Start a NEW Thread