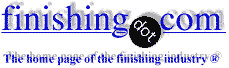
-----
Some problems in alkaline zinc plating

< Prev. page (You're on the last page of the thread)
Q. Dear Sir,
We have alkaline zinc plating tank, and we use the HNO3 for yellow dip approx. in 2-3 ml/ liter , and also we use the H2SO4 for color maintaining. Now it's improved.
We are facing a problem in cleaning now; we are doing pretreatment (cleaning) process in HCl , but component shine is not coming, so please give us the cheap and good suggestion so that we can get shining on component.
Regards,
- Delhi, India
September 18, 2013
A. Hello Sanjeev,
That your parts shine, or your parts brightness, could depend on how you clean your parts or how you plate your parts... If you have a cleaning problem, you should see if you are loading fully degreased parts, that your HCl is in correct concentration, if you use or not a wetting agent (if you don't, you should, I think it is very helpful, and cheap), if you use or not an electrolytic degreaser...
If you answer most of these questions with "yes", then you must tell us more about your process in order to help you. If not, you should see if you can make that happen.
We (at least I) can't say anything else to help you if you don't specify more what is the defect, what are you doing, and in which conditions.
Hope this helps! Best regards,
- Delhi, India
Q. Dear sir,
1. Why the discolouration comes at the olive green zinc plating?
2. Why the white passivation comes at the metal bonded area at green zinc plating?
3. Salt spray requirement for green plating?
4. What is difference between alkaline plating and zinc plating?
for Shops, Specifiers & Engineers
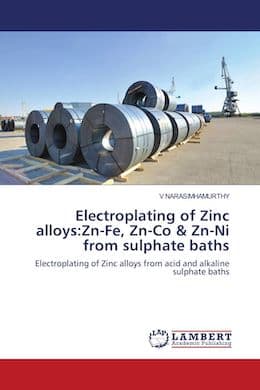
from eBay, AbeBooks, or Amazon
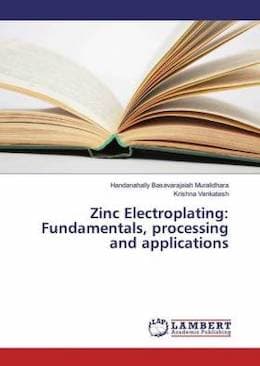
from eBay, AbeBooks, or Amazon
"Alkaline non-cyanide zinc plating with reuse of recovered chemicals" by Jacqueline M. Peden (1994)
from (U.S. EPA)
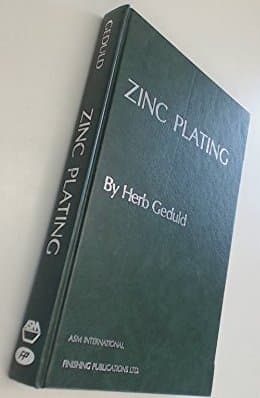
from eBay, AbeBooks, or Amazon
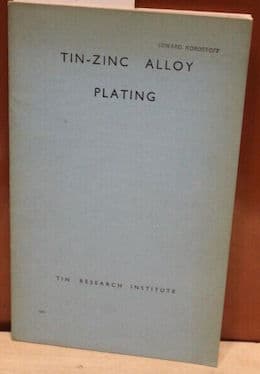
from eBay, or AbeBooks
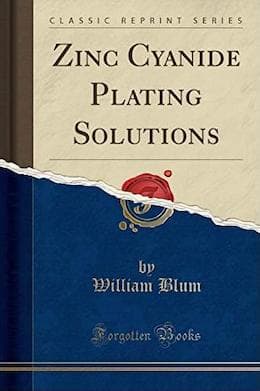
from eBay, AbeBooks, or Amazon
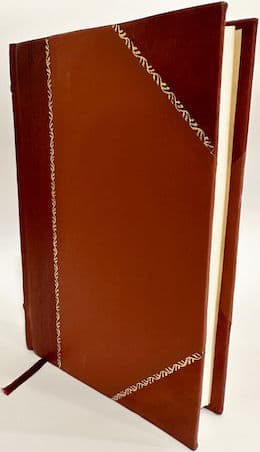
from eBay, AbeBooks, or Amazon
(as an Amazon Associate & eBay Partner, we earn from qualifying purchases)
- Delhi, India
December 29, 2013
A. Hi Kumar.
1). Please give data about what you're doing, from which people may be able to tell you what you are doing wrong (or what you mean by discoloration).
2). I don't think you mean "white passivation" ... maybe you mean "white rust"? White rust is corrosion of the zinc plating.
3). The customer often specifies the required salt spray hours, but 96 to 192 hours to white rust could be pretty customary.
4). Zinc plating can be done from cyanide-based zinc baths, alkaline non-cyanide zinc baths, and acid zinc plating baths. Cyanide has the disadvantage of being highly toxic, and is rapidly falling out of favor around the world. Today's alkaline non-cyanide baths can replace the cyanide processes. Acid zinc baths give a brighter plate, but usually have poorer throwing power so are less capable of achieving relatively even plating thickness.
Please ask as many questions as you like and as many as it takes, but please provide details on each of them rather than presenting the readers with an abstract flash-card quiz; it's considered good netiquette to expend more effort on your own behalf than you ask others to expend, and that can be demonstrated by posting clear descriptions of your situation and exactly what you are doing :-)
Thanks and Regards,
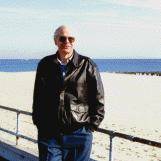
Ted Mooney, P.E.
Striving to live Aloha
(Ted can offer longterm or instant help)
finishing.com - Pine Beach, New Jersey
Iridescent passivation peels off of alkaline zinc plating
Q. I am facing problem of passivation at customer's end.
The process is as below:
Base : Fe
Plating : Non-Cyanide alkaline Zinc
Passivation : Iridescent hex-chrome.
Problem : Passivation Adhesion problem. The plated parts after passivation shows slip out of passivation meaning improper adhesion of passivation.
Could anybody explain the reason for this and remedy for it ?
- Delhi, India
February 23, 2014
Q. I have a component in diameter 8.
Material: Mild Steel
Total length of component is around 800 mm
My customer is asking plating thickness more than 15 Micron
My question is
1. Whether it is possible to give coating thickness 18 micron?
2. What will be effect of cost?
- Delhi, India
September 2, 2015
A. Hi Pramod. Yes, even 25 microns is still a "standards-based" thickness for "very severe" exposure.
Nobody can quote you the cost of someone else's services, of course. But you should have little difficulty finding a plating shop willing to do 15-18 micron plating for twice the cost of 8 micron plating, It will take twice as long, and will half their production rate, but they will see materials savings in the other processes, and probably labor savings, if they half their production rate. Good luck.
Regards,
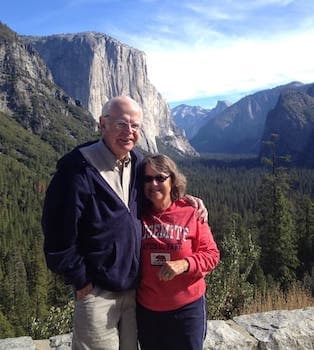
Ted Mooney, P.E. RET
Striving to live Aloha
(Ted can offer longterm or instant help)
finishing.com - Pine Beach, New Jersey
Yellowish zinc deposit after alkaline zinc plating
Q. We use alkaline non-cyanide zinc plating with 800 liters. The bath is working good but lately the plated barrel shows yellowish or golden deposit after plating instead of bright silver color. Please tell me the problem.
Eskedar bekele- Delhi, India
February 10, 2016
A. AFTER ALKALINE ZINC PARTS COMES OUT YELLOW, CHECK THE NITRIC DIP CONCENTRATION OR MAKE UP NEW; AFTER THAT NO MORE YELLOW PARTS COMES OUT.
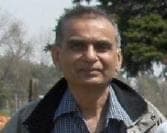
Popatbhai B. Patel
electroplating consultant - Roseville, Michigan
Effect of Temperature
⇦ Tip: Readers want to learn from your situation;
so some readers skip abstract questions.
Q. If the temperature of the alkaline Zinc bath is increased up to 35 °C then what will be the effect on the plating and the reactions going on in the plating tank??
- Delhi, India
December 31, 2016
A. Hi Veerendra. Alkaline zinc plating temperatures can range from room temperature up to about 48 °C. As a very general rule, plating speed increases at higher temperatures, but so does brightener consumption. What temperature does the process supplier suggest? Why do you want to exceed it? Thanks.
Regards,
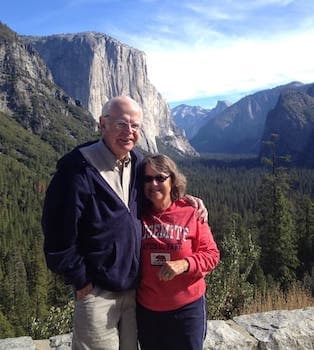
Ted Mooney, P.E. RET
Striving to live Aloha
(Ted can offer longterm or instant help)
finishing.com - Pine Beach, New Jersey
A. Hi Veerendra,
Alkaline zinc temperature range 25 °C to 35 °C , Optimum temp 26 °C. You can run with higher temperature but it burns brightener and other components and increases plating speed.
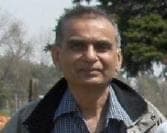
Popatbhai B. Patel
electroplating consultant - Roseville, Michigan
A. When increasing temperature on an Alkaline Non Cyanide Zinc line the formation of carbonates speeds up which are detrimental to the bath once significant build up happens.
Brightener consumption increases.
The above two will increase running and maintenance costs.
I find there is a point in temperature where the bath performs adequate to the point of "diminishing returns", meaning increasing temperature further doesn't give much benefits in terms of the quality of finish.
- Perth, Western Australia
July 4, 2022
Part is smaller in diameter after plating
Q. Hello sir, I face a problem that diameter of component becomes less after plating. What is the reason? Please help. Material is 16 mncr5
Sidharth kamboj- Delhi, India
January 18, 2017
A. Hi Sidharth. That strikes me as exceptionally unlikely. To begin solving the problem you would need to measure the diameter after each step in the plating process and determine in which tank it happens. If you discover a reduction in diameter after rechecking, please tell us the starting diameter, ending diameter, and which tank it happened in (soak cleaner, electrocleaner, acid activator, alkaline zinc plating tank, chromate conversion coating tank, etc.) Thanks.
Regards,
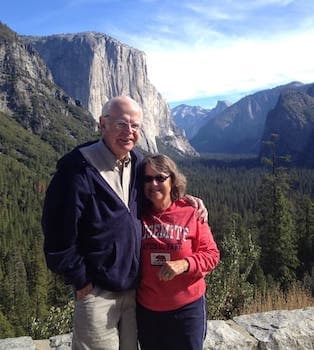
Ted Mooney, P.E. RET
Striving to live Aloha
(Ted can offer longterm or instant help)
finishing.com - Pine Beach, New Jersey
Burning in Alkaline Non Cyanide Zinc plating
Q. We have been seeing problems where the edges of the parts end up with a serious amount of high current density burning. We have added low current formula and brightener to keep these concentrations up. I've sent samples of the plating bath to our chemical manufacturer and they come back in balance. We still see this issue and it's causing issues with powder coat paint applications after the plating process.
Paul King- Delhi, India
March 22, 2017
A. Hi Paul. Obviously there is a current density beyond which burning in the high current density edges is unavoidable, and the only resolution is to plate at lower current density. I'm not sure how to say exactly where that point is except from vendor suggestions, reports of successful and unsuccessful current density, and previous experience.
It might vaguely be possible to increase the current density by shielding those edges, but only if it's a long run of identical parts.
Regards,
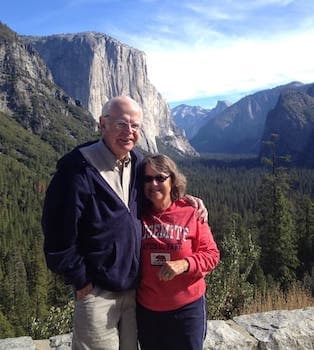
Ted Mooney, P.E. RET
Striving to live Aloha
(Ted can offer longterm or instant help)
finishing.com - Pine Beach, New Jersey
"...sent samples of our plating bath to our chemical manufacturer and they come back in balance" ?!
Did he run a Hull Cell
⇦ huh?
Panel? The solution might titrate "in balance" and be loaded with dragged in HCl which has converted to NaCl and will surely chew up the HCD edges.
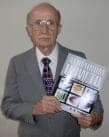
Robert H Probert
Robert H Probert Technical Services

Garner, North Carolina
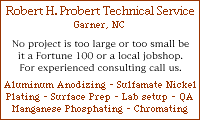
Thank you for the responses. Yes, we did a hull cell. We did that first and it came up with the parts looking good. Of course the hull cell was a flat panel and didn't have any variance in the plating because of this. Thanks for the thought there though.
What we did and will continue to do is add a small daily quantity of a LCD booster. And change the concentration of our brightener feeder pump. Both of these additions have resulted in more uniform finish across the surface of all the parts and specifically in the HCD areas on the bigger parts. When the brightness gets too high, I'll cut both back and see how long it takes to plate out.
Thank you both for you contribution.
- Delhi, India
A. Hi Paul, I would suggest a brightener feeder system based on your rectifier amp hours, especially on tanks larger than 500 gal. Adding a small amount, say every 500 to 1,000 amp hours, based on the Tech Data sheet would maintain an even level. Takes the human error out of it ... well, not completely.
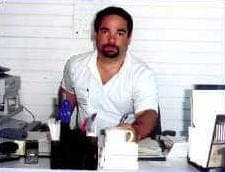
Jim Conner
Mabank, Texas USA
Shiny edges and dull centers on zinc plated parts
Q. Hello
I work in a metal finishing shop and we have been having issues with our zinc plating on some parts. The biggest issue is the finish is not uniform and we are getting shiny edges and dull centers, especially on larger parts. I have heard this referred to as "TV screen effect" but hours of googling have not given me any results.
Our technicians are reasonably certain that the problem lies in our zinc solution and not anywhere else. Our zinc phosphate and even our yellow zinc do not have these issues. We have been in business for over 20 years and never had an issue like this.
I believe our problem started because we have recently moved our shop across town. This meant pumping out our zinc solution into totes and and then back into our zinc tank. (3000 gallon tank). This is what leads me to believe there is some contaminant in our solution. (I assume organic contaminants, possibly oil). We never had issues like this at the old shop and the only change we have made is our location. This is the first year that we have not froze out the carbonates but I don't think that is our issue.
As per our chemical supplier, we have added 5 gallons of 7.4% sodium hypochlorite. Plating seems to be improving but we are still seeing the same issues.
One of our technicians thinks it could be a bad batch of carrier or brightener but the boss has ruled that out.
I imagine adding more sodium hypochlorite would help? 5 gallons into a 3000 gallon tank doesn't seem like enough to me. I've also heard EDTA or activated carbon or Rochelle salts
⇦ on
eBay
or
Amazon [affil link]
but I have no experience with those.
Any ideas or suggestions would be very much appreciated! Thanks! I will try to attach some pictures of our problem.
- Delhi, India
April 19, 2017
A. Hi Josh. I am not a zinc plater, so we will will have to wait for someone who is to offer their best guess at the problem. But what I do know is that you don't start by adding sodium hypochlorite or EDTA or Rochelle salts to a 3000 gallon tank ... you add stuff to your 267 ml Hull Cell and see what helps and hurts. Good luck.
Regards,
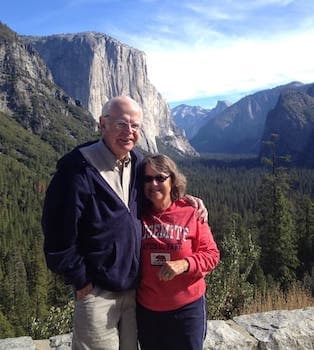
Ted Mooney, P.E. RET
Striving to live Aloha
(Ted can offer longterm or instant help)
finishing.com - Pine Beach, New Jersey
A. What are your numbers? (Zn, NaOH) And, what's your Hull panel look like? Might be additives.
I don't think bleach will help, either.
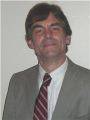
Dave Wichern
Consultant - The Bronx, New York
A. Hi !! Josh,
Add 0.5 gm/ltr potassium permanganate
⇦ on
eBay or
Amazon [affil link] (KMnO4). Mix well. Settle the solution for overnight. Impurities will settle at the bottom of tank. Next morning separate clear solution from sludge. Discard the sludge and use clear solution for plating. I think your problem will get solved with this process.
- Delhi, India
Q. Dear sir: alkaline plating problem.
Alkaline plating in white spot part (okay metal and casting), but white spot problem, so please sir, help.
- Delhi, India
August 18, 2018
A. Hi Saurabh. Unfortunately, I don't think people can even visualize the defect you are experiencing, let alone guess what might cause it. Please send pictures of the defect to mooney@finishing.com for posting here, and tell us what you see in your Hull Cell testing. Thanks!
Regards,
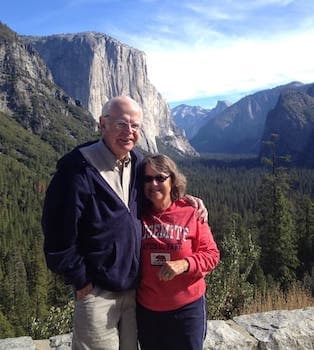
Ted Mooney, P.E. RET
Striving to live Aloha
(Ted can offer longterm or instant help)
finishing.com - Pine Beach, New Jersey
ACRONYMS:
from context, ncz would mean non-cyanide zinc
Q. Hi, sir I am using ncz tank bath. I have problems in a tractor pin like as bolt types pin when we hang with wire. After zinc plating and hexavalent gold chromate it shows wire marks. Please suggest me why this comes. What should be added.
Ram Gopal Verma- Delhi, India
March 28, 2019
A. Hi Ram. Using wire for racking can be a problem, and is usually okay only for certain types of parts. These pins should probably be either barrel plated or use custom racks which do not leave rack marks in unacceptable areas. Good luck.
Regards,
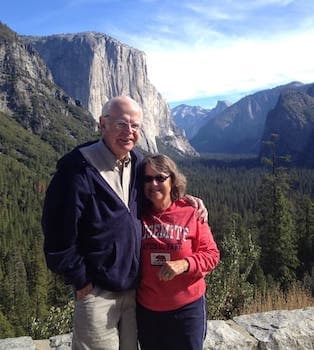
Ted Mooney, P.E. RET
Striving to live Aloha
(Ted can offer longterm or instant help)
finishing.com - Pine Beach, New Jersey
Q. I am having a rack system of alkaline zinc electroplating. Its contents are Caustic 130 g/L and zinc metal 1 2g/liter.
I face white rust on Mild steel CRCA component where spot welding is done.
After passivation is done and when the component is kept for natural drying the caustic water comes out from the welded area and the golden passivation gets removed. This leads to white patches on the component.
How do I neutralize the caustic between the welded parts before golden zinc passivation?
My post treatment process is
1. Water rinse
2. Nitric rinse
3. Golden passivation
4. Water rinse
5. Hot water rinse
- Delhi, India
September 24, 2019
A. Hello Kartik,
My advice would be to employ any of the following types of agitation in your rinse(s).
1) Work bar agitation in the direction best suited to remove the entrapped solution.
2) Solution agitation
3) Air agitation
4) Work bar vibration.
If you don't use work bars in the rinses and it's manual dipping, you could employ #s 2 & 3. Good Luck!
- Delhi, India
A. OOZING OUT CAUSTIC.
INCREASE WATER RINSE IF POSSIBLE AIR AGITATION IN WATER RINSE.
AVOID HEXAVALENT PASSIVATION, GO FOR TRIVALENT.
BAKE COMPONENT AFTER PASSIVATION, SO TRAPPED CHEMICAL GETS DRIED.
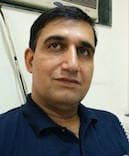
Ajay Raina
Ludhiana, Punjab, India
Chemical flow in welded area
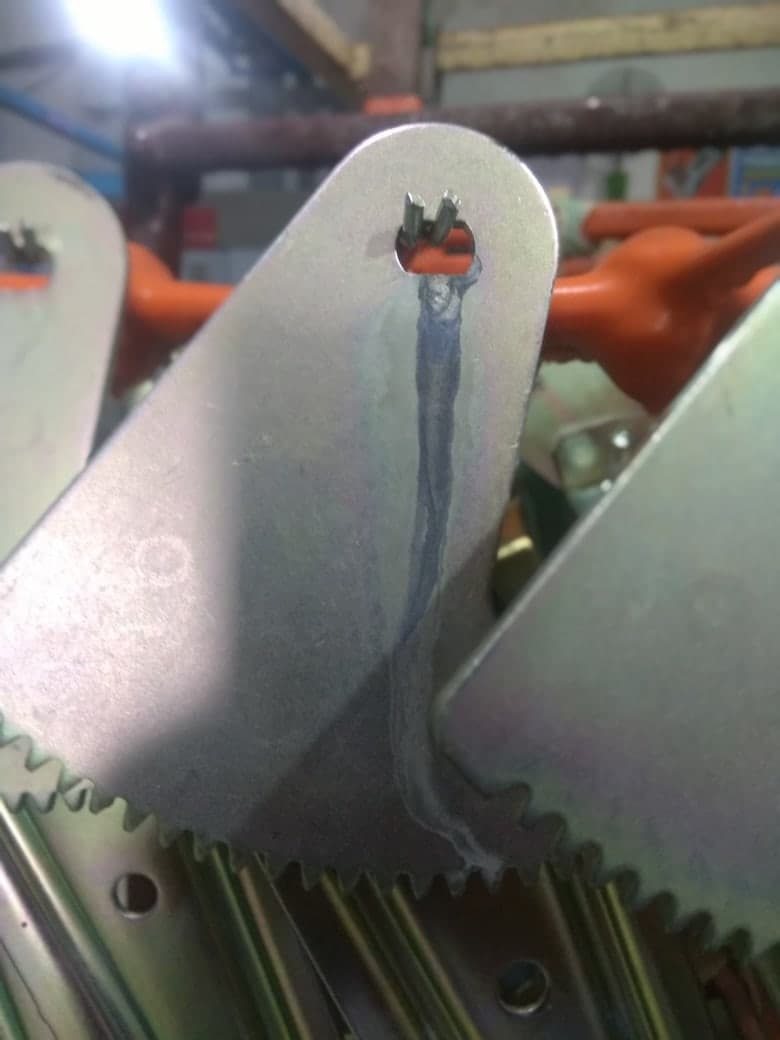
Q. Good evening, My self Arvind Soni from India we are facing problem in sector welding parts when after welding we are plating the same in between cavity sector and arm chemical flow after plating and giving proper curing time of 24 hrs.
This is in Zinc plating process. Kindly suggest -- it's urgent and generating heavy rejection.
- Delhi, India
October 16, 2019
? Hi Arvind. The picture seems to be of a stained part hanging on a plating rack but, sorry, I do not understand the shinier units I see in back of it, nor do I understand your text. Hopefully another reader familiar with this type of part will catch on better. Apologies :-(
This is a public forum and questions may sometimes remain unanswered for weeks or months; please contact a plating consultant for urgent needs. Good luck.
Regards,
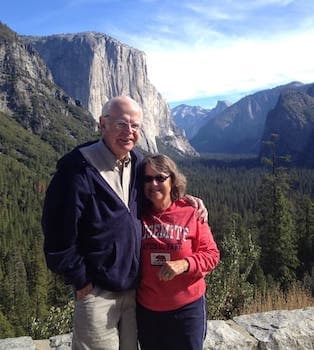
Ted Mooney, P.E. RET
Striving to live Aloha
(Ted can offer longterm or instant help)
finishing.com - Pine Beach, New Jersey
A. Dear Arvind,
Please improve the welding between the two plates.
Avoid the Gap. Your problem is not from plating but from a badly made assembly.
The uneven gap between the two plates entraps the solution and causes bleed out of plating solution later.
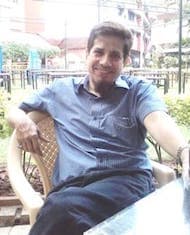
Khozem Vahaanwala
Saify Ind

Bengaluru, India
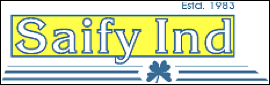
White Tarnish, White Corrosion
Q. Hello everyone,
My name is Bartek and I come from Poland. We run a small galvanic line (racks and barrels on the same line) with the alkaline zinc process. Most of our production is the black finish passivation (based on Cr III) with sealer. The part coating is made on the racks.
We are facing a problem with a white tarnish (white corrosion?) which always turns up after a few days. This problem concerns mostly parts which we have to correct (re-coating process). Parts are made of material and 11SMnPb30.
The process flow chart:
chemical degreasing -> electrochemical degreasing -> 3-step rinsing -> acid pickling -> 2-step rinsing -> alkaline activation -> zinc plating (alkaline) -> 2-step rinsing -> acid activation (HNO3) -> black passivation -> 2-step rinsing -> sealing -> drying
Do you have any ideas what we can do to avoid this problem?
Thank you in advance.
- Delhi, India
November 18, 2019
A. Hi Bartek. Looking at the graphics it looks like the parts are pitted. Perhaps the replated parts are more prone to white rust because they are pitted from their two trips through the acid pickling? But if you search the site for "11SMnPb30" you will find some suggestions regarding the pickling and plating of this leaded steel. Good luck.
Regards,
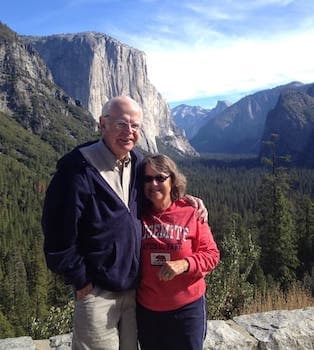
Ted Mooney, P.E. RET
Striving to live Aloha
(Ted can offer longterm or instant help)
finishing.com - Pine Beach, New Jersey
A. Extending on Ted. Lead on the surface forms and insoluble salt in most "pickling solutions" like HCl, and sulfuric acid. Make up a bucket of 30%/vol fluoboric acid which does not form an insoluble salt, try it, come back, let us know.
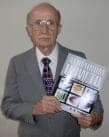
Robert H Probert
Robert H Probert Technical Services

Garner, North Carolina
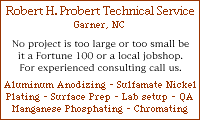
A. While my problem was similar to yours, it was with black spots at similar intervals to yours - I thought I'd comment in case there is some similarity between our problem.
This ended up occurring more frequently when parts sat for too long in the acid rinse which was directly before an NaOH based electrocleaner tank
This acid rinse tank often would have dissolved salts I believe as a contaminant, and if parts sat for too long they appeared to be picking up some sort of staining or containment from the rinse that would remain and leach out later as black spots.
Frequent refreshing of that rinse tank helped stop this issue and watching the time spent sitting in the tank to ensure it's not too long.
- Perth, Western Australia
April 24, 2025
⇦ Tip: Readers want to learn from your situation;
so some readers skip abstract questions.
Q. The technical or other reason for water marks in alkaline zinc plating in automation (rack line) in tubular parts.
Vandana Rawat- Delhi, India
December 24, 2020
Q. Hi,
I would like to ask if electricity can "melt" portions of the items being plated.
There is one item in which "melt/dent" is found after process. The melted part is found in the area in which the item is suspended during process. I have conducted some trials already and I found out that in one rack, there are items with melted area and there are some which do not have such.
We are processing the items in alkaline zinc with blue chromate conversion coating. The ampere that we are using for the items is around 1500 A
- Manila, Philippines
May 7, 2021
![]() |
A. Hi Kevin - Winnipeg, Canada A. "the item is suspended" ... If the "suspension" is loose and wobbly, then when some break contact the current surges on the other parts and dissolves" ("burns" or "melts"). You must have firm, tight, consistent electrical contact on ALL parts in the circuit. ![]() Robert H Probert Robert H Probert Technical Services ![]() Garner, North Carolina ![]() |
A. Hi Kevin. Can you send a photo of the "melted" rack & parts to mooney@finishing.com for posting here so we can have a better understanding of the situation?
Leon and Robert probably each have more practical experience in this than I, and plating can definitely "burn"; nevertheless, I am reminded of the several 'parlor trick' examples of how difficult, if not impossible it is, to even burn paper or cloth when it's wet. The idea that you could actually melt a steel part or a stainless steel or copper rack through solution-borne plating current while it is immersed in a vat of watery alkaline zinc plating solution just does not compute for me :-)
Underwater welding can be done but it's not trivial, and it's not the watery solution conducting the current through an ionic path, it's metal to metal. I'd suspect the parts actually hitting the anodes, if anything.
Luck & Regards,
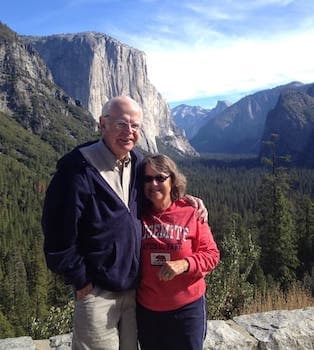
Ted Mooney, P.E. RET
Striving to live Aloha
(Ted can offer longterm or instant help)
finishing.com - Pine Beach, New Jersey
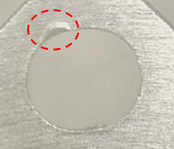
Gentlemen,
Thank you for sharing with me your ideas. I will be checking those items you pointed out.
- Manila, Philippines.
Q.
Hello!
We are glad that we found you in the website forum finishing.com.
Our small company is doing non-cyanide alkaline zinc rack electroplating. We use mostly Coventya chemicals. We started to experience some kind of pixel like coating from one of our baths. The electrolyte is new. Around 1 month of use and it's not used that much. We don't have this kind of problem on our other bath, with older electrolyte > a year.
I'm attaching some photos to help you visualize the problem better.
Do you have any idea what could cause this issue? We had also powder-like material stuck to our coating in one of our other baths. Some of which could be washed off and some not.
Thanks in advance, wish you all the best!
Boyan DabovicBulgaria
June 23, 2021
![]() |
A. Hi Boyan, ![]() Popatbhai B. Patel electroplating consultant - Roseville, Michigan A. Unless it is leaded steel, it is blatantly a cleaning problem. If it is leaded steel you need to use fluoboric acid instead of HCl or sulfuric. ![]() Robert H Probert Robert H Probert Technical Services ![]() Garner, North Carolina ![]() |
Q. Hi sir Hello
Alkaline zinc rack plating: after yellow passivation white patches observed on top of job (jig position area & part holes area) after plating and bright dipping nothing known, but after yellow passivation only that pbm observed. Tell me a way to solve this problem ...
Conc -6.3%; Fe-21.08 ppm; zinc-6.2 gm; pH-2.2
Thank you sir...
Production chemist - India, tamil nadu, India
July 19, 2021
A. Hi S. Logu,
The info you provided is very helpful, but it may not be enough. A photo would help, plus, what does a Hull Cell panel show? Does the same whiteness show up on the LCD or HCD end of the Hull Cell panel? Thanks.
Luck & Regards,
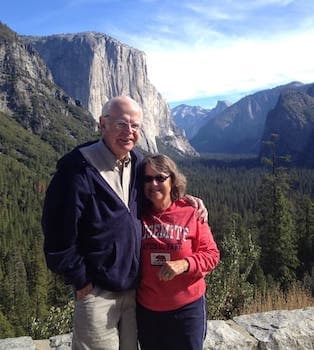
Ted Mooney, P.E. RET
Striving to live Aloha
(Ted can offer longterm or instant help)
finishing.com - Pine Beach, New Jersey
Q. Hi!
I have a process of cyanide-free alkaline zinc process and I have a problem with this piece.
This piece is with white passivate and organic seal, and after some days, the piece has a formation of dust in a high-density area, which is easily removed with a cloth, I don't know what the problem is due to and this is generating rejections with my client.
- Mexico/ Guanajuato
March 18, 2022
A. Hi Albert. As you see we added your inquiry to one of several treads about similar problems in alkaline zinc plating. Pictures sent to mooney@finishing.com for posting here would help, but even still here can be several causes for any given plating problem. My first guess would be that you are drying at too high a temperature. The high current density areas (corners, edges) are also the area that will overheat first in a hot dryer. If the parts are not overheated during drying, my next guess would be 'burning' which just wasn't noticed earlier.
Luck & Regards,
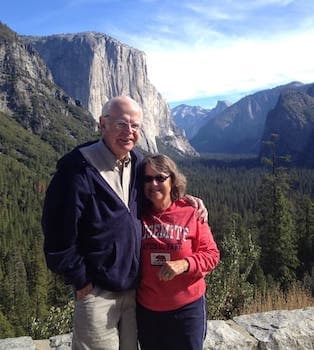
Ted Mooney, P.E. RET
Striving to live Aloha
(Ted can offer longterm or instant help)
finishing.com - Pine Beach, New Jersey
- Mexico/ Guanajuato
A. Hi again. The pics are too small and from too far away to see any detail in high current density areas. But the unsatisfactory plating seems to be in random areas, which is hard to explain other than poor cleaning or poor plating bath composition/operation.
As always, Hull Cell panels can reveal whether the problem is on the plating tank. Good luck.
Regards,
Ted Mooney, P.E. RET
Striving to live Aloha
(Ted can offer longterm or instant help)
finishing.com - Pine Beach, New Jersey
Q. Hello,
I am Anand, I am working in fasteners unit. We operate a non-cyanide alkaline zinc bath. We have facing problem of non coating in shank bolts only.
We maintain:
Caustic - 130 gms/ ltr
Zn - 9 gms / ltr
Pickling - 20%
- Chennai, India
October 11, 2022
A. Hi Anand.
In addition to the problem of lack of plating on the shank, the plating on the head is chipped off badly, and we can see from the cracks and lack of adhesion that it will soon be even worse. My first suspicion is that the problem isn't your plating bath but the fact that the bolts are not prepared suitably for plating -- possibly not truly clean, possibly still with scale on them.
Can you blast a few and tell/show us what result you get when you plate them?
Luck & Regards,
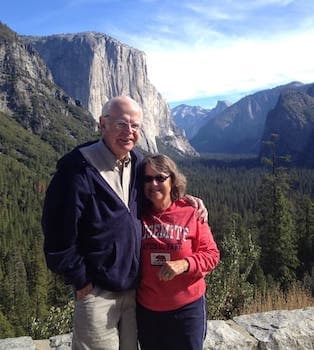
Ted Mooney, P.E. RET
Striving to live Aloha
(Ted can offer longterm or instant help)
finishing.com - Pine Beach, New Jersey
A. Dear sir,
Please increase the concentration of HCl pickling from 20 % to 40 %. This cause occurs due to cleaning of parts not properly done. The bonding of metal and zinc not in proper way -- that was this defect occurring. I think these parts look like tempered, and high carbon scaling on parts. That's why I recommend to increase the HCl concentration in tank.
- ludhiana punjab
Plating slows at higher temperatures
Q. Hi Ted and Popat ,
I work in a research company on metal finishing. I recently studied the effect of temperature on the plating of alkaline zinc. You mentioned in your post that the plating speed is higher at higher temperature. While in my study, I tested barrel plating at 5 ASF at three different temperatures (21, 32, and 43 °C). Surprisingly I found that at higher temperatures (32 and 43 °C) the initiation period is much longer than that at room temperature (21 °C), which makes the total plating time at higher temperatures (32 and 43 °C) is around 20 minutes slower than at room temperature (21 °C). Do you know the reason behind this? I'm confused and thank you very much.
chemist - Charlotte, NC
May 9, 2022
A. Hi Jenny. Most chemical reactions occur faster at higher temperatures due to the greater mobility of the ions, but for this case the experimental results are what they are. Hopefully someone else can explain them.
Luck & Regards,
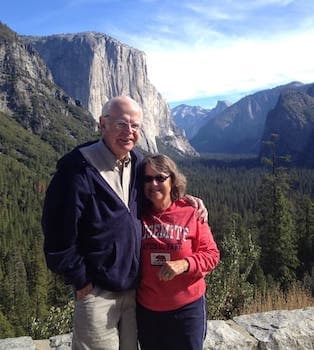
Ted Mooney, P.E. RET
Striving to live Aloha
(Ted can offer longterm or instant help)
finishing.com - Pine Beach, New Jersey
Thank you very much for your quick response, Ted!
chemist - Charlotte, NC
A. At the higher temp, particularly at 43 °C, you were making carbonate faster and carbonate slows down the plating rate.
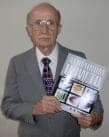
Robert H Probert
Robert H Probert Technical Services

Garner, North Carolina
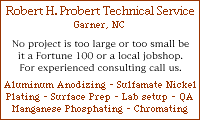
Hi Robert,
Thank you very much for shedding light on this topic.
chemist - Charlotte, NC
May 11, 2022
A. Keep in mind that the operating characteristics of the brightener additives changes significantly once above 35 °C, e.g.,coverage issues arise in LCD areas first. Perhaps this may be playing a part of the decrease in efficiency.
Boris Siljanoski- Western Australia
January 26, 2023

Q, A, or Comment on THIS thread -or- Start a NEW Thread