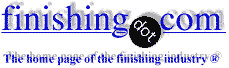
-----
Electroplating of iron onto copper (soldering iron tips, etc.)
Q. I need to plate multiple pieces of Bismuth Shot with Iron or Iron-Zinc coating. much prefer just iron.
What bath, temperature, and pH value do I need?
Could someone help ?
- Irvine California
February 26, 2021
A. Hi Tim. I give the formulation & operating conditions for one iron plating bath on this page; and other readers offer several other proposals on this page and on 3 other long threads on electrodeposition of iron, viz., topics 9456, 24616, and 25982.
But! ... that sounds like the easy part! :-)
... because I'm not finding any info about electroplating onto bismuth, and I don't know what pretreatment sequence is required, nor whether there are reactions with other metals which dictate required plating underlayers.
So plating iron (with the aggressiveness of that solution, its propensity for pitting, its requirement for no air agitation, its high stress, its porosity, etc.) directly onto bismuth sounds quite unlikely. If you have achieved success in plating another metal onto bismuth please tell us about it and we can start from there because that should probably be plated onto the bismuth as an underlayer first :-)
Luck & Regards,
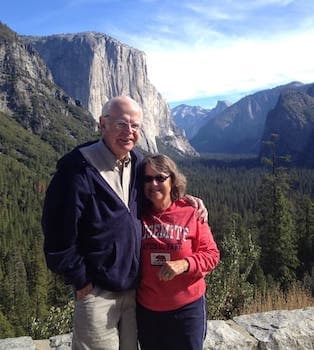
Ted Mooney, P.E. RET
Striving to live Aloha
(Ted can offer longterm or instant help)
finishing.com - Pine Beach, New Jersey
February 2021
February 26, 2021
Q. Thank you Mr. T. Mooney:
I have been able to plate tin and copper directly onto bismuth shot and onto my other products tungsten shot and lead shot. I have been able to plate them thick, like 15 µm to 35 µm.
Thus, I believe we can consider plating iron onto tin or onto copper. Maybe zinc too (I recall a sub contractor plated zinc onto bismuth for another client of his years ago).
Also, what is iron-zinc plating good for?
I studied at Univ. of Hawaii, Manoa. Lived on Big Island for 6 months too, Aloha Spirit is worth spreading...
Mahalo.
Tim
- Irvine California
A. Hi again, Tim. Thanks for the info on plating onto bismuth -- I'm unfamiliar with it and did not see anything readily on google.
I'm not familiar with iron-zinc plating if the order of the metals implies that you are talking bout more iron than zinc. Zinc-iron plating (much more zinc than iron) is an alternative to plain zinc plating and offers improved corrosion resistance plus enhanced ability to do black chromating on it.
Luck & Regards,
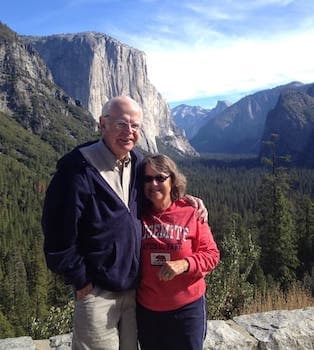
Ted Mooney, P.E. RET
Striving to live Aloha
(Ted can offer longterm or instant help)
finishing.com - Pine Beach, New Jersey
February 2021
July 19, 2021
Q. For those with an interest in the history of iron electroplating, this article on the subject was in the Nov 27, 1869 issue of Scientific American. An interesting note is of the addition of a small quantity of gelatin to "improve the texture". Could this suppress pit-forming bubbles?
November 27, 1869
The Hon. Cassius M. Clay, late U. S. Minister to Russia, has recently returned from St. Petersburg, bringing with him some fine specimens of iron electrotypes, done after the process of Prof. Jacobi and Klein. The process was patented in this country through the Scientific American Patent Agency, Sept. 29, 1868. The following description of the process we copy from the patent specification:
"Our invention consists in the application of a practical galvano-plastic process as to the deposits of iron on molds, or any other form, for reproducing engravings, stereotypes, and for other useful or ornamental purposes.
The galvano-plastic bath we use is composed of sulphate of iron, combined with the sulphates of either ammonia, potash, or soda, which form, with sulphate of iron, analogous, double salts.
The sulphate of iron may also be used, in combination with the chlorides of the said alkalis, but we still prefer the use of sulphates. The bath should be kept as neutral as possible, though a small quantity of a weak organic acid may be added, in order to prevent the precipitation of salts of peroxide of iron.
A small quantity of gelatin will improve the texture of the iron deposit.
As in all galvano-plastic processes, the elevation of the temperature of the bath contributes to the uniformity of the deposit of iron, and accelerates its formation.
For keeping up the concentration of the bath, we use, as anodes. large iron plates, or bundles of wire of the same metal.
Having observed that the spontaneous dissolution of the iron anode is, in some cases, insufficient to restore to the bath all the iron deposited on the cathode, we found it useful to combine the iron anode with a plate of gas-coal, copper, platinum, or any other metal being electro-negative toward iron, and which we place in the bath itself.
As a matter of course, this negative plate may also be placed in a separate porous cell, filled with an exciting fluid, as diluted nitric or sulfuric acid, or the nitrates or sulphates of potash and soda.
For producing the current, we usually take no more than one or two cells of Daniels' or Smee's battery, the size of which is proportioned to the surface of the cathode.
It is indispensable that the current should be regulated, and kept always uniform, with the assistance of a galvanometer, having but few coils, and therefore offering only a small resistance.
The intensity of the current ought to be such as to admit only of a feeble evolution of gas-bubbles at the cathode, but it would become prejudicial to the beauty of the deposit if gas-bubbles were allowed to adhere to its surface."
John Erbes
Electroplating Hobbyist - Milwaukee, Wisconsin
A. Hi John. Thanks for the history.
Plating solutions often (probably usually) have at least two addition agents: a brightener and a wetter. The 'brightener' (or combination of brighteners, levelers, etc.) usually serve the general purpose of being attracted to and 'shielding' the high current density areas to improve the leveling and to promote the formation of more adatoms discouraging the growth of large metal crystals (which creates porosity where the crystals meet). The 'wetter' is usually some sort of detergent that reduces the viscosity, surface tension, etc. so that the hydrogen gas bubbles float free sooner. I can't really say the role of the gelatin for sure, but I believe it probably served as a brightener rather than a wetter.
Luck & Regards,
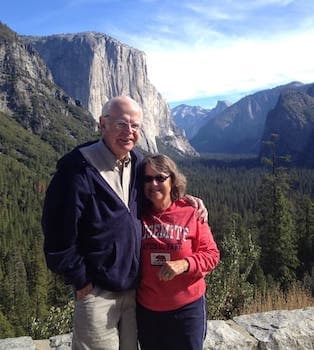
Ted Mooney, P.E. RET
Striving to live Aloha
(Ted can offer longterm or instant help)
finishing.com - Pine Beach, New Jersey
July 2021
⇩ Related postings, oldest first ⇩
Q. How do we do iron coating on copper bits used in soldering irons?
Preet S [surname deleted for privacy by Editor]- New Delhi, India
2002
A. Dear Preet,
Please continue on down this page that you've started, and you'll see good technical answers develop. For a less technical answer, you may be able to obtain a license from a soldering iron manufacturer to use the technology they have developed, or find a supplier of a proprietary iron plating process who will assist you with the application of their process chemistry onto soldering irons.
While waiting for the thread to develop, you might also do a computerized search of the published literature; there have been a few articles on this subject in the journals over the years. Perhaps Metal Finishing Information Service at www.surfacequery.com can assist you with that, or scholar.google.com if you don't have access to such databases.
Or start by telling us what you know and don't know -- that always generates much more enthusiastic responses than a request from a stranger for a unilateral technology transfer. Good luck.
Regards,
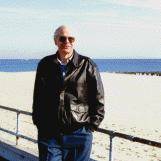
Ted Mooney, P.E.
Striving to live Aloha
(Ted can offer longterm or instant help)
finishing.com - Pine Beach, New Jersey
2002
RFQ: I am looking for a source for iron plating of copper for custom solder tips we make in-house for our soldering department. various shapes and sizes though the largest is about 4" X 8" piece.
We are looking at individual pieces, but could send 5-20 pieces at a time.
Thanks,
Metal Fabrication - Croswell, Michigan
2006
Ed. note: This RFQ is outdated, but technical replies are welcome, and readers are encouraged to post their own RFQs. But no public commercial suggestions please ( huh? why?).
2005
Q. Sir,
We are manufacturers of soldering and de-soldering stations. Since we need long life iron plated soldering bits and de-soldering nozzles we request you to kindly let us know the plating process involved in iron plating on copper.
1. How a plating bath is to be prepared.
2. What is the solution required
3. is there any catalyst required if so what.
4. What is the bath temperature.
5. How to avoid pitting problem.
6. What is the voltage supplied to cathode and anode and the bath.
7. Which kind of iron is to used as cathode and anode.
mfrs of soldering and de soldering station - Hyderabad, Andhra Pradesh, India
A. Hi K.Raghu,
Iron plating is rather uncommon; the plating of soldering equipment being one of very few applications. The other manufacturers of soldering equipment don't seem to be publishing papers about their tricks, so it is difficult to get really good information and feedback.
We appended your inquiry to a thread which presents two possible plating baths. There are other baths available including sulphate and fluoborate; I don't believe that they use catalysts of any type; they do operate at different temperatures though; wetting agents are used to discourage pitting; high purity Armco Iron is used for the anodes.
The best advice may be to get all of the published information you can find, probably starting with the previously referenced "Electroplating" by Lowenheim
⇦[this on
eBay ,
Amazon,
AbeBooks affil links]
, and the Iron Plating chapter in the Metal Finishing Guidebook; but also to investigate the possibility of buying a proprietary iron plating bath which will have already been proven by the supplier for soldering equipment applications.
You are in the soldering equipment business, yet have no knowledge of this technology? The obvious question on readers' minds then is whether that is because you are having the parts plated by an outside shop, or whether it's because you currently are doing a plating other than iron on the tips? If you are currently doing a different type of plating please tell us about it!
If you are already in fact doing iron plating, please relate your situation and difficulties; your willingness to share may inspire others to do so. Thanks!
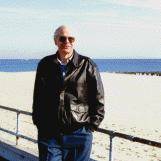
Ted Mooney, P.E.
Striving to live Aloha
(Ted can offer longterm or instant help)
finishing.com - Pine Beach, New Jersey
2005
A. Having performed this very application a couple of years ago, it's indeed very tricky! We used a ferric chloride ⇦ on eBay or Amazon [affil link] bath, very hot. It's very inefficient, so gas liberation is big problem leading to, as you guessed, pits. We were only able to get rid of pits by putting a cam on the work bar to raise it up 3 or 4 inches and then drop it on the sides of the tank literally knocking off the pit forming bubbles. The actual bath formulation came from one of the above references. Good luck

Milt Stevenson, Jr.
Plating shop technical manager - Syracuse, New York
2005
That's a good point, Milt: iron baths are very subject to oxidation, so air agitation is a problem. Perhaps eductors are workable; but I haven't seen them or tried them in this application.
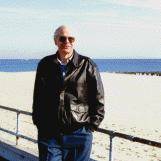
Ted Mooney, P.E.
Striving to live Aloha
(Ted can offer longterm or instant help)
finishing.com - Pine Beach, New Jersey
2005
![]() |
I have coated various metals metallic substrates with plasma technology. It should be possible to coat copper with iron. H.R. Prabhakara - ConsultantBangalore Plasmatek - Bangalore Karnataka India 2006 |
Q. I'm looking for some information regarding the coating of a soldering head. I'm looking to put a new soldering machine into production, but the soldering surface has to be a custom shape, so I'm unable to use an off-the-shelf tip. As I understand it, iron is the preferred material, but I'm finding it hard to locate a company in England that performs iron coatings.
Is there an alternative metal/material/process that can be used to protect the copper in the tip from corrosion by the flux? From my research, it seems that ferrous sulfate
⇦ on
eBay or
Amazon [affil link] is the most common electrolyte for plating. Is anyone able to tell me about the practicalities of performing this process in-house, bearing in mind that we are not an electroplating company. I don't think a particularly smooth finish is required, but a reasonable level of join stability is needed, as it is subject to thermal expansion and contraction cycles.
Nickel is often used to prevent the solder from running up the tip, as the solder cannot 'wet' to the nickel surface. Does anyone know if chromium can be used instead of iron for the tip coating, and how does this perform in contact with the solder?
- Southampton, Hampshire, England
2003
A. Hi Rupert. You are doing a pretty good job of figuring out what is involved in plating the tips of soldering irons. But if I were in your position I would continue looking for someone to do the plating. Bringing plating into house is not impossible but often subjects companies to an entire new set of responsibilities and harassments they are not prepared for including wastewater treatment, hazardous waste disposal, ventilation systems, employee exposure monitoring, etc.
Something that most potential users who have not been exposed to electroplating since school days may not realize is that in general you don't formulate plating processes from basic chemicals like in school; rather, there is a whole industry of suppliers who have perfected the plating solutions, and offer them as proprietary products. They can provide workable process solutions, and be of great assistance to you in planning for an in-house installation.
Good luck.
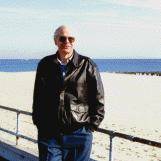
Ted Mooney, P.E.
Striving to live Aloha
(Ted can offer longterm or instant help)
finishing.com - Pine Beach, New Jersey
2003
A. If you are talking about a small number of tips that would be of a medium size tip for electronics and are having grief finding a plating firm in the UK, you might want to take a look at brush plating. Tampon plating in your corner of the world. Talk to vendors in your country (at least 2).
Instead of doing it all with the brush method, do the iron step in a tiny tank. This would not involve more than 50 to 100 ml. This could be used a few times and then stored in a used solution container. If your laws are similar to the USA ones, you can keep the small amount generated for a very very long time and then ship it off for proper treatment. Their smallest rig that is above the plating pen size would do you nicely. Probably would only take 5 amps. Plan on sending a competent person to their school that is typically 2-5 days.
James Watts- Navarre, Florida
2003
A. Iron plating of solder iron tips is still the best finish. Electroless nickel is used for de-soldering. Iron is also plated from an HCl, ferrous chloride solution at 90 °C plating. Not a nice solution to have in a shop. There is also ferrous sulfamate that plates at pH 4, but it is little used mostly because people don't know very much about it.
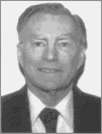
Don Baudrand
Consultant - Poulsbo, Washington
(Don is co-author of "Plating on Plastics" [on Amazon or AbeBooks affil links]
and "Plating ABS Plastics" [on Amazon or eBay or AbeBooks affil links])
2003
Q, A, or Comment on THIS thread -or- Start a NEW Thread