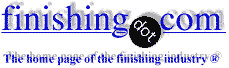
-----
Science fair project - plating a quarter with copper
Q. My situation is that I want to find the best electrolyte for plating a quarter with copper, so that can be my control for the experiment. Then I will think up different acids and test them as the variable. please help me!
Christopher H [last name deleted for privacy by Editor]- Orlando, Florida, USA
2005
A. Did you see our FAQ, "Electroplating -- How It Works", Christopher? You didn't say what grade you are in, or what you need to exhibit. You can exhibit the finished quarters, but if the plating solution is to be demonstrated, you can't use any solution except vinegar ⇦in bulk on eBay or Amazon [affil link] because you can't put toxic materials out on display at most science fairs. Some "real" plating solutions are based on cyanide (a powerful poison, out of the question) and fluoborate (also out of the question). But if you are in high school and can get some supervision from the science teacher, and don't have to put the solutions on display, some workable ones would be copper sulphate ⇦ on eBay or Amazon [affil link] (with a little sulfuric acid), copper chloride (with a little muriatic acid ⇦ on eBay or Amazon [affil link] ) or copper pyrophosphate. Good luck.
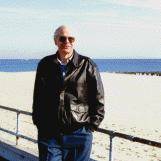
Ted Mooney, P.E.
Striving to live Aloha
(Ted can offer longterm or instant help)
finishing.com - Pine Beach, New Jersey
2005
2005
Q. Sorry Mr. Mooney about the short letter, I was in biology at school and the bell rang. Here's everything you need. I am in 9th grade, and am doing a science fair at Edgewater High School. I am trying to find a solution that works better than the control solution (what electroplating plants use). Can you tell me what industrial electrolyte is? I've heard it is copper sulphate and weak sulfuric acid. I'm using a D-cell battery and letting the solution sit for about an hour.
I was just fooling around, and I used citric acid, water, copper sulphate, table salt, vinegar, table sugar, and lemon lime Gatorade mix (don't ask me why I used it :) ). At first it didn't work so good, but then I suddenly noticed 2 days later I left pennies in it, and it was a blue green color. I tried it again, and it worked awesome! I think it was strangely the Gatorade, but I'm not sure. If I were to use that in one my variable solutions, I don't know what amount of anything I put in there. The only thing I know is I put a whole lot of salt and sugar, a decent amount of copper sulphate (I only have 5 ml from a chem. set) and the same amount of citric acid as copper sulphate. I'm also having a problem with dumping the stuff down a sink(I haven't yet), since it eroded a quarter in like 3 hours. I think its caustic but I'm not sure. If anyone can answer my questions, PLEASE HELP!
They are:
What is the standard solution for copper plating?
Can you suggest 1(one) solution using household chemicals? ( I'm using 5 test solutions and I have 4 already)
Was it the Gatorade mix that made it work so good or was it letting the solution get blue with copper?(the dime I electroplated (that is now shiny and coppery) wasn't like that fresh out of the solution. It had about 3/8 inch of coppery smut on it. I cleaned it with toothpaste and an old electric toothbrush and it looks like a fresh penny's copper on a dime. If I use this solution, then I will have to find out what's in the
Gatorade mix that makes it work (if that's what is making it electroplate). I hope the Gatorade mix isn't what made it electroplate! I think it was because it sat for 2 days with pennies in it.
What should I do with the solution after I'm done with it?
P.S I read one of the letters another 9th grader wrote (www.finishing.com/41/88.shtml) and I tried your solution of: Table sugar, Epsom Salts, vinegar, Copper sulphate, and dishwasher soap and it didn't work at all :(. I think it's because I didn't let it sit for a couple of hours.
Christopher H [returning]- Orlando, Florida, USA
2005
A. The most common industrial electrolytes are probably copper cyanide and copper sulphate. Copper pyrophosphate and copper fluoborate are also used industrially. Formulations are in the Metal Finishing Guidebook, which should be available in some local library. Maybe you cold arrange a visit to the American Electroplaters Society (www.nasf.org) since the national headquarters happens to be in your town [this was true at the time of Christopher's posting, but no longer is].
You can neutralize the solution before disposal with slow and careful additions of baking soda [in bulk on eBay or Amazon [affil link] or milk of magnesia.
The blue-green color is probably copper ions in solution, which is very good, but I'd expect them to have come from the copper sulphate, not the Gatorade. But the Gatorade or something else could be dissolving the copper from the pennies. vinegar does work, lemon juice would probably work as an alternative.
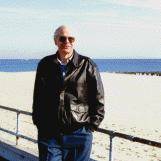
Ted Mooney, P.E.
Striving to live Aloha
(Ted can offer longterm or instant help)
finishing.com - Pine Beach, New Jersey
![]() |
Isn't there a little law that prohibits the defacing of money? Just a thought. Hi Sheldon, actually, I don't think there is a law prohibiting children from plating coins. 2005 December 30, 2011
|
Q. Thanks a lot Mr. Mooney! I have two more questions though. do you know where I can get copper sulphate, and copper cyanide? Can you tell me the dangers and health risks of cyanides?
if anyone can answer these question that would be great.
- Orlando, Florida, USA
2005
2005
A. You could try Fisher Scientific for the copper sulphate. There are also a number of places which sell small quantities of chemicals to high school labs, but I wouldn't be familiar with them; just type 'lab supplies' into a search engine. You can't buy copper cyanide because it's too dangerous--both an extremely powerful poison as a powder and a poison which is very easy to accidentally or deliberately turn into a deadly gas.
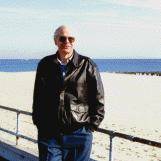
Ted Mooney, P.E.
Striving to live Aloha
(Ted can offer longterm or instant help)
finishing.com - Pine Beach, New Jersey
Q. Mr. Mooney, can you give me a recipe for the amount of copper sulphate and sulfuric acid to put in a basin, so it can be used for electroplating? it would help also if you specified the strength of the sulfuric acid and copper sulphate(in moles) that should be added.
Thank you so much for your time,
- Orlando, Florida, USA
2005
2005
Q. Dear Mr. Mooney,
I am trying to electroplate a quarter and a key for my science project and your website has been very helpful to me.
The first try I used too strong of a battery and got a lot of smut. Then I changed to a 1.5 volt D battery and it seems to be working better as far as the smut. My quarter and key got a little coppery, but not much.
I am using a flat piece of copper as my anode and it has been sitting in the vinegar solution for a week, since my last try. Now the water is very blue green, and from what I read on your site, this is because the copper ions are dissolved in it.
Yesterday I tried again using this blue green solution and it was like magic! In a matter of minutes everything I put in there turned to copper! I was so excited, but there seems to be problem.
The problem is the copper seems to fade as the quarter or key dries. If I leave it in longer, the quarter and the key turn dark brownish grey. My question is, how can I get the copper color to stay? I would like to demonstrate them for my science fair project.
Thanks for your help,
Tyler, 7th grade
- Port Charlotte, Florida, USA
A. It sounds like you've done great, Tyler. If the solution has been sitting there a week, perhaps most or all of the vinegar evaporated. I'd suggest trying an addition of vinegar. Also, keep the quarter far from the anode. Good luck.
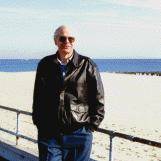
Ted Mooney, P.E.
Striving to live Aloha
(Ted can offer longterm or instant help)
finishing.com - Pine Beach, New Jersey
2005
2006
Electroplating:
A Copper Plated Dime
By: Chris H.
December 28 2005
ELECTROPLATING: A COPPER PLATED DIME
H., Chris W.
Mr. Randall Ius, Edgewater High School Orlando
Electroplating is the process of depositing a metallic coating from one object to another by using electric current. Industries use the electroplating process in everything from manufacturing jewelry to chrome plating car parts. It is used to improve the appearance of metals and to help stop corrosion of metals. The purpose of this project is to find an environmentally safer copper plating solution than currently used in the plating industry. This experiment is being performed because with the advancement of technology, more and more plating is being utilized. The hypothesis of this experiment is a less environmentally harmful copper plating solution can be found to plate copper onto a dime.
The control is a solution of copper sulphate, sulfuric acid and Deionized water, which is the industry standard plating bath. Four variable solutions were used, including two that used nitric and hydrochloric acid, which are less dangerous than sulfuric. The other two solutions consisted of vinegar as the acid, copper sulphate, deionized water and either table salt or Epsom salt. These solutions were tested at both three and seven volts for twenty minutes.
The vinegar with salt solution at seven volts worked the best when compared to the other plating baths. The second best was the nitric acid at three volts. Third and fourth were nitric acid at seven volts, and muratic acid at three volts. It is concluded that a safer and less environmentally harmful solution can be used today in the copper plating industry.
Reference List
1. Finishing.com. Ted Mooney.15 may 1995. 24 September 2005. www.finishing.com/375/01.shtml
2. "Electroplating." Wikipedia. Wikipedia+++++. 28 December 2005. Answers.com 28 Dec. 2005. http://www.answers.com/topic/electroplating
3. Artisan Plating. 28 December 2005. Artisan Plating. 28 December
2005.
http://www.artisanplating.com/articles/platinghistory.html
Table of Contents
Introduction:
A. Purpose.........4
B. Problem........4
C. Hypothesis........4
D. Background Information...4-7
Methods:
A. Subjects.............................................................8
B. Materials.......8
C. Procedures8-9
Results:
A. Tables, graphs, diagrams...10-12
B. Statistical Analysis......13
Discussion:
A. Conclusion...14-15
B. Application...15-16
C. Recommendations...16
Acknowledgements.17
Glossary.18-19
Literature....20-21
Appendices..22-25
Introduction
Purpose:
The purpose of Electroplating: A Copper Plated Dime is to find an environmentally safer copper plating solution than currently used in the plating industry. This experiment is being performed because with the advancement of technology, more and more plating is being utilized. This is important because industry will need to use a less damaging plating system that plates just as well as the current system, to protect our world.
In this experiment a plating bath will be used to test four different copper solutions to electroplate copper onto a dime. These tests will give results to find if any of the solutions are successful copper plating mediums.
Problem:
Can a safer copper plating solution than the industry standard Sulfuric Acid (H2SO4) be found?
Hypothesis:
A less environmentally harmful copper plating solution can be found to plate copper onto a dime.
Background Information:
Electroplating is the process of depositing a metallic coating from one object to another by using electric current. Industries use the electroplating process in everything from manufacturing jewelry to chrome plating car parts. It is used to improve the appearance of metals and to help stop corrosion of metals.
Electroplating starts with a plating bath, plating solutions, electrical current, an anode and cathode. To plate copper onto an object, industry uses a plating solution of copper sulphate (CuSO4), Sulfuric acid (H2SO4) and deionized water. A cathode (the object to be plated) is placed in a plating bath as well as an anode (a piece of pure copper). An electrical current is turned on and copper ions migrate from the copper plate, through the solution, onto the object to be plated.
Process
The process used in electroplating is called electrodeposition. The item to be plated is placed into a container containing a solution of one or more metal salts. The item is connected to an electrical circuit, forming the cathode (negative) of the circuit while an electrode typically of the same metal to be plated forms the anode
(positive). When an electrical current is passed through the circuit, metal ions in the solution are attracted to the item. The result is a layer of metal on the item. However, considerable skill and craft-technique is required to assure an evenly-coated finished product.
A more detailed description of the electrodeposition process follows: The anode and cathode in the electroplating cell are connected to an external supply of direct current, a battery, or more commonly a rectifier. The anode is connected to the positive terminal of the supply, and the cathode (article to be "plated") is connected to the negative terminal. An example is in an acid solution Cu is oxidized to Cu++ by losing two electrons. The Cu++ associates with the anion SO4 2- in the solution to form copper sulphate. At the cathode, the Cu++ is reduced to metallic Cu by gaining two electrons. The plating is most commonly a single metallic element, not an alloy. However, some alloys can be electrodeposited, notably brass and solder.
Industrial use
Electroplating is used in many industries for functional or decorative purposes. Some well known examples are chrome-plating of steel parts on automobiles. Steel bumpers become more corrosion-resistant when they have been electroplated with first nickel and then chromium. Steel camshafts resist wear better when they have been electroplated with chromium. Plain steel or aluminum parts in light fixtures become beautiful when they are electroplated with nickel and then decorative chromium or brass.
Steel bolts last much longer because they are sold with a coating of zinc that has been applied by electroplating. Zinc electroplating and passivation provides a double protection system for steel components. Virtually all types of steel can be protected, including castings. Newly developed electrolytes and process methods are able to provide greatly increased corrosion prevention. In addition to the well known yellow full passivation, there are blue, olive and black variants available to meet modern requirements. Modern electrolytes can produce brilliant chrome like finishes. Specially developed processes produce improved metal distribution over complex shapes. Alloy zinc deposits offer extra performance.
Electroplating can be used to silver plate copper or brass electrical connectors, since silver tarnishes much slower and has a higher conductivity than those metals. The benefit of the silver is lower surface electrical resistance resulting in a more efficient electrical connection. Silver plating is also popular for RF connectors because radio frequency current flows primarily on the surface of its conductor; the connector will thus have the strength of brass and the conductivity of silver.
Low force/low voltage separable connectors used in telecommunications switchgear, computers, and other electronic devices are typically plated with gold or palladium over a barrier layer of nickel. The tail ends of these connectors, which are usually joined to the device by soldering, are plated with a tin/lead alloy, or pure tin.
History
Modern electroplating was invented by Italian chemist Luigi V. Brugnatelli in 1805. Brugnatelli used his colleague Alessandro Volta's invention of five years earlier, the voltaic pile, to help the first electrodeposition. Unfortunately, Brugnatelli's inventions were repressed by the French Academy of Sciences and did not become used in general industry for the following thirty years.
By 1839, scientists in Britain and Russia had independently thought up metal deposition processes similar to Brugnatelli's for the copper electroplating of printing press plates. Soon after, John Wright of Birmingham, England discovered that potassium cyanide was a suitable electrolyte for gold and silver electroplating. Wright's associates, George Elkington and Henry Elkington were awarded the first patents for electroplating in 1840. These two then founded the electroplating industry in Birmingham England from where it spread around the world.
The Laws of Electrolysis
Michael Faraday observed that when you placed 96,485 coulombs of electrical charge through an electrolytic solution that one equivalent of substance is plated out onto an electrode. If you double the current passing through the cell than 2 equivalents would be deposited. He concluded that the quantity of substance deposited on the electrode is directly proportional to the current passing through the cell. This is how the whole electroplating process works.
Methods
Subjects:
This experiment will use four different copper plating solutions and two voltage settings to copper plate a dime. The results will be compared to dimes plated using the industry standard copper plating solution (Control Group).
Materials: See appendix for sources
CuSO4 - Copper sulphate White Distilled vinegar Alligator Clips
H2SO4 - Sulfuric Acid Salt (NaCl)
rubber glovesrubber gloves
⇦ on
eBay or
Amazon [affil link] /
goggles
⇦ on
eBay or
Amazon [affil link]
Deionized Water Epsom Salt (MgSO4) Power Source
HNO3 (Nitric Acid) Copper Wire 12" (5) 6x6x2 Plastic Basin
HCl (Hydrochloric Acid) 1/32" Copper Sheet (20) Dimes
Procedures:
Control Group:
1) Plating solution Wearing safety goggles and gloves, combine in a beaker [beakers on
eBay
or
Amazon [affil link] :
250g CuSO4
10ml H2SO4
Deionized water Fill to 1 liter
Allow this solution to sit 24 hours covered.
2) Pour 355ml solution into basin (plating bath container)
3) Clean dime with toothpaste and toothbrush, rinse well.
4) Attach dime to an alligator clip and 6" wire.
5) Dip a 2" x 2" copper sheet into vinegar to remove protective coating.
6) Attach copper sheet to alligator clip and 6" wire.
7) Attach dime with wire to the negative terminal of the power source. This is the cathode.
8) Attach copper sheet with wire to positive terminal. This is the anode.
9) Place the anode and cathode into the plating bath, a minimum of 1" apart. Do not allow to touch.
10) Turn on power source.
First test 3 volts for 25 seconds.
Second test 7 volts for 25 seconds.
11) Record results.
12) Repeat first and second test.
13) Record results.
Test Groups:
Follow the same procedures as the control group using the following plating solutions and times.
Test Group 1:
10ml white vinegar
250g salt
250g CuSO4
Fill with deionized water to 1 liter
Test time: 20 minutes at 3 and 7 volts
Run test two times
Test Group 2:
10ml HCl
250g CuSO4
Fill with deionized water to 1 liter
Test time: 20 minutes at 3 and 7 volts
Run test two times
Test Group 3:
10ml HNO3
250g CuSO4
Fill with deionized water to 1 liter
Test time: 20 minutes at 3 and 7 volts
Run test two times
Test Group 4:
10ml white vinegar
250g CuSO4
250g Epsom salt
Fill with deionized water to 1 liter
Test time: 20 minutes at 3 and 7 volts
Run test two times
Results
Test Run #1 Characteristics 3V 7V
Shine 10 10
Control Quality of plate 10 10
Group Color Pink Copper Pink Copper
(H2SO4) Smut None None
Shine 0 8
Test Group 1 Quality of plate 0 8
(Salt/Vinegar) Color Silver Pink Copper
Smut None Small Amt on Edges
Shine 6 7
Test Group 2 Quality of plate 7 2
(Muratic Acid) Color Pink Copper Pink Copper
Smut Small Amt on Edges None
Shine 6 4
Test Group 3 Quality of plate 9 10
(Nitric Acid) Color Pink Copper Pink/Orange Copper
Smut None None
Shine 0 0
Test Group 4 Quality of plate 2 0
(Epsom Salt /Vinegar) Color Blackish Grey/Green Coating
Smut Total Total
Quality of plate is 0 no plate, 10 consistent thick plate
Shine scale 0 no shine, 10 shiniest
Figure 1
Results
Test Run #2 Characteristics 3V 7V
Shine 10 10
Control Quality of plate 10 10
Group Color Pink Copper Pink Copper
(H2SO4) Smut None None
Shine 0 6
Test Group 1 Quality of plate 0 5
(Salt/Vinegar) Color Silver/Small Streaks Pink Copper
Smut None Med. Amt on Edges
Shine 4 4
Test Group 2 Quality of plate 7 5
(Muratic Acid) Color Light brown Copper Light brown Copper
Smut Small Amt on Edges None
Shine 5 4
Test Group 3 Quality of plate 10 10
(Nitric Acid) Color Pink Copper Pink Copper
Smut None None
Shine 0 0
Test Group 4 Quality of plate 3 0
(Epsom Salt /Vinegar) Color Dark brown Grey/Green Coating
Smut Total* Total*
Quality of plate is 0 no plate, 10 consistent thick plate
Shine scale 0 no shine, 10 shiniest
* White residue coated anode copper plate 9 minutes into test run
Figure 2
Results
Shine/Quality Combined Scores
Test Run 1 Test Run 2
Test 3Volt 7Volt 3Volt 7V
Control 20 20 20 20
Group
(H2SO4)
Test Group 1 0 16 0 11
(Salt/Vinegar)
Test Group 2 13 9 11 9
(Muratic Acid)
Test Group 3 15 14 15 14
(Nitric Acid)
Test Group 4 2 0 3 0
(Epsom Salt /Vinegar)
- Shaded results are not included in statistical analysis because they did not result in copper plating.
Figure 3
Statistical Analysis:
Analysis consists of visual observations of shine, quality of plate, color and smut. The control group results were used as the standard for these characteristics. The control group test ran for only 25 seconds because of the strength of sulfuric acid.
Shine - Was measured on a scale of 0 to 10. 0 no shine. 10 very shiny like a new penny.
Quality of plate Was measured on a scale of 0 to 10. 0 no copper plating visible.
10 copper plating evenly deposited over the dime's surface.
Color Was reported as: Pink copper; Pink/Orange Copper; Light Brown Copper;
Brown Copper; Dark Brown Copper; Blackish; Grey/Green Copper. Optimal results would be a pink copper similar to a new penny.
Smut Was reported as none, small, medium or total coverage of smut and where it was located on the dime.
The Shine/Quality Combined Score Chart (Figure 3) shows the combined numerical scores for shine and quality. Tests that resulted in poor color or total smut coverage were not considered in the following analysis as they did not achieve the end goal of copper plating a dime.
Top 5 Plating Results
Rank Test Group Voltage Combined Score
1 1 7V 16
2 3 3V 15
3 3 7V 14
4 2 3V 13
5 2 7V 9
Figure 4
Discussion
Conclusion:
The experiment Electroplating: A Copper Plated Dime, was based upon the hypothesis that a less environmentally harmful plating solution can be used to copper plate.
This experiment has conclusively proven this hypothesis to be true. Results reported in Figure 1 and Figure 2 show that copper plating was achieved in 10 of the 16 variable tests. These results are summarized in the statistical analysis of Figure 3 and Figure
4.
With a visual score of 16, the results show that a plating solution of white vinegar and salt (Test Group1) can be used as a highly successful plating solution at 7 Volts. Both white vinegar and salt are environmentally safer than the sulfuric acid solution commonly used in industry today.
The results of the experiment also show that a Nitric Acid plating solution is highly successful at both 3 Volts (Score of 15) and 7 Volts (Score of 14). Nitric Acid is less dangerous to the environment than Sulfuric Acid.
The test results also show Muratic Acid can be used successfully in a copper plating bath at both 3 Volts (Score of 13) and 7 Volts (Score of 9). Muratic Acid is less dangerous than both Sulfuric and Nitric Acids.
The test group of salt and vinegar (Test Group1) at 3 Volts resulted in no plating. The test group of Epsom salt and vinegar (Test Group
4) resulted in a black or grey/green plate color coated with smut. These tests were not considered as valid plating substitutes because a copper plate could not be achieved. It is interesting that during all of the Epsom salt tests a chalky white substance formed on the anode 9 minutes into the test (Test Group 4, 3V and 7V).
This experiment included controls such as the use of the same amount of acid and copper sulphate to make each plating solution. The same amount (355ml) of plating solution was used in each test bath. Each test group used a controlled amount of voltage 3V and 7V and ran for the same amount of time (20 minutes).
Variables in this experiment include the control group ran for only
20 seconds due to the strength of the sulfuric acid vs. the 20 minute run time for each test group 1-4. This variable does not affect the results as these tests were based upon visual results achieved, not the length of time it took to plate.
Another variable is the plating bath temperature. Tests were run over several days outdoors. On some days the temperature was in the 70's, some days in the 60's, resulting in different solution temperatures. This variable may have affected the plating quality due to more copper being released in a warmer solution. A 20 minute plate run time for the test was used to help overcome the temperature variable.
In summary, it is felt that he results of this experiment support the use of an environmentally safe solution in the copper plating industry. This is important because the use of plating is increasing with technology, and there must be safer method to safeguard the environment.
Application:
This project relates to the real world because of the frequent use of electroplating using dangerous acids in industry. The results of these experiments show that a less environmentally harmful plating solution can be produced and used successfully. By using environmentally safer solutions, industry would be able to keep our waste water systems cleaner and also reduce the cost of disposing dangerous used plating solutions.
Recommendations:
This experiment has several areas that could use different procedures. It is recommended that there should be testing using the following:
1) Increase the voltage: The results of the tests performed with vinegar/salt solution (test Group 1) improved with the 7 volt test. It would be interesting to see if increasing the voltage would speed up the plating time without smut.
2) Use more vinegar and salt: It would be interesting to see if using more sale and vinegar in the Test 1 solution would increase conductivity reducing plating time.
3) Use a circulating plating bath: A bath that circulates the plating solution may prevent the copper ions from sinking to the bottom of the solution. This may prevent the bottom of the dime from plating faster than the top.
Acknowledgements
Much of the background information used in these experiments was given by Mr. Ted Mooney, P/E/ at Finishing.com, Inc. via e-mail. Mr. Mooney was able to advise how to make an industry standard plating bath solution as well as the cleaning methods used for the anode copper and the cathode dime.
Mr. Randall Ius supplied the Nitric Acid.
Mrs. Cheryl Hatcher supplied local sources for Muratic Acid, Sulfuric Acid and Copper sulphate.
Glossary
Anode- The negatively charged terminal of a primary cell or of a storage battery that is supplying current.
Cathode-The positively charged terminal of a primary cell or a storage battery that is supplying current.
Smut- particles of dirt left on the dime as a result of too much current going through the plating bath during the electroplating process.
Plating Solution- the liquid inside the basin used to electroplate objects
Terminal- a contact on an electrical device (such as a battery) at which electric current enters or leaves
Alligator Clip- a clip with metal rivets that attach to the copper plate and dime.
Deionized Water- is a form of water which lacks ions, such as those from sodium, calcium, iron, and copper. This type of water is created using an ion exchange process. Deionized water is similar to distilled water, in that it is useful for scientific experiments.
Sulfuric Acid- A highly corrosive, dense, oily liquid, H2SO4, colorless to dark brown depending on its purity and used to manufacture a wide variety of chemicals and materials including fertilizers, paints, detergents, and explosives. Also called oil of vitriol, vitriol.
Nitric Acid- A transparent, colorless to yellowish, fuming corrosive liquid, HNO3, a highly reactive oxidizing agent used in the production of fertilizers, explosives, and rocket fuels and in a wide variety of industrial metallurgical processes. Also called aqua fortis.
Muratic Acid- A clear, colorless, fuming, poisonous, highly acidic aqueous solution of hydrogen chloride, HCl, used as a chemical intermediate and in petroleum production, ore reduction, food processing, pickling, and metal cleaning. It is found in the stomach in dilute form.
Plating Bath- the basin used to hold the plating solution
Electrodeposition- To deposit (a dissolved or suspended substance) on an electrode by electrolysis.
Electron- A stable subatomic particle in the lepton family having a rest mass of 9.1066 x 10-28 grams and a unit negative electric charge of approximately 1.602 x 10-19 coulombs.
Alloy- A homogeneous mixture or solid solution of two or more metals, the atoms of one replacing or occupying interstitial positions between the atoms of the other: Brass is an alloy of zinc and copper.
Tarnish- To dull the luster of; discolor, especially by exposure to air or dirt.
Resistance- The opposition of a body or substance to current passing through it, resulting in a change of electrical energy into heat or another form of energy.
Corrosion- atmospheric oxidation of metals. By far the most important form of corrosion is the rusting of iron. Rusting is essentially a process of oxidation in which iron combines with water and oxygen to form rust, the reddish-brown crust that forms on the surface of the iron.
RF- Radio Frequency
Rectifier- A device, such as a diode, that converts alternating current to direct current.
Electrolysis- Chemical change, especially decomposition, produced in an electrolyte by an electric current.
Electrolyte Solution- The plating solution
Electrolyte- A chemical compound that ionizes when dissolved or molten to produce an electrically conductive medium.
Coulombs- The meter-kilogram-second unit of electrical charge equal to the quantity of charge transferred in one second by a steady current of one ampere.
Volts- The International System unit of electric potential and electromotive force, equal to the difference of electric potential between two points on a conducting wire carrying a constant current of one ampere when the power dissipated between the points is one watt.
Copper sulphate- A poisonous blue crystalline copper salt, CuSO4 5H2O, used in agriculture, textile dyeing, leather treatment, electroplating, and the manufacture of germicides.
Bibliography
Internet
1. Finishing.com. Ted Mooney.15 may 1995. 24 September 2005. www.finishing.com/375/01.shtml
2. Finishing.com. Ted Mooney.15 may 1995. 24 September 2005.
www.finishing.com/faqs/plating.shtml
3. Efunda. 1995. 22 September 2005.
http://www.efunda.com/processes/surface/electroplatings.cfm
4. Wise Geek. 2003. 27 September 2005.
http://www.wisegeek.com/what-is- electroplating.htm?referrer=adwords%20ad=03181&%20search%20kw=electropl ating
5. About.com. Mary Bellis. 2005. Techni Inc. 18 September 2005. http://inventors.about.com/library/inventors/blelectroplating.htm
6. Electroplating. Hal Bender. 1998. Clackamas Community College. 4 Oct 2005. http://dl.clackamas.cc.or.us/ch105-09/electrop.htm#top
7. "Electroplating." Wikipedia. Wikipedia+++++. 28 December 2005. Answers.com 28 Dec. 2005. http://www.answers.com/topic/electroplating
8. Artisan Plating. 28 December 2005. Artisan Plating. 28 December
2005.
http://www.artisanplating.com/articles/platinghistory.html
9. PSIgate. 06 May 1997. Resource discovery Network. 28 December
2005.
http://www.psigate.ac.uk/newsite/reference/plambeck/chem2/p02081.htm
10. Electrochemistry Encyclopedia. September++. University of Windsor. 28 December 2005. http://electrochem.cwru.edu/ed/encycl/art-e01-electroplat.htm
11. "The History of Industrial Electroplating". 28 December 2005. Industrial Electroplating. 28 December 2005. http://www.electroplate.biz/history.html
12. "Michael Faraday". RI (Royal Institution of Great Brittan). 28 December 2005. RI (Royal Institution of Great Britain). 28 December
2005. http://www.rigb.org/rimain/heritage/faradaypage.jsp
Books
1. World Book Encyclopedia. Chicago. World Book Inc---. 6. 470.
2. Morgan, Nina. Chemistry in Action. Chicago: Oxford University Inc,
2003. 1. Orange County Public Library Systems Main Library.
3. Nostrand, Van. Scientific Encyclopedia. New York.: John Wiley & Sons Inc. 2002. 1. Orange County Public Library Systems Main Library.
4. Neal, Charles D. Safe and Simple Projects With Electricity. Chicago: Children Press, 1965. 1. Orange County Public Library Systems Main Library
5. The Thomas Edison Book of Easy And Incredible Experiments. New York: John Wiley & Sons Inc. 1988. Orange County Public Library Systems Main Library
6. Faraday, M. Faraday's Chemical History of a Candle: Twenty-Two Experiments and Six Classic Lectures. Chicago, IL: Chicago Review Press, 1988.
7. Williams, L. P. Michael Faraday, A Biography. New York: Basic Books, 1965.
Appendix
Muratic Acid- Found at pool supply stores
Copper sulphate- found at Palmer Feed and Seed
Sulfuric acid- found at auto parts store as car battery acid
⇦ on
eBay
or
Amazon [affil link]
Nitric acid- Mr. Ius supplied me with it
Power source- Radio Shack digital camera power adapter @ 3, 5, 6,
6.5, 6, 7.5 volts regulated output
Alligator clips, wire, copper plate- Sky Craft surplus on Fairbanks Avenue.
Copper plate after electroplating
Control Solution
Nitric acid test dime after 5 minutes in the air
Muriatic test dime in baggie
Nitric test dime fresh out of solution
Epsom salt solution
- Orlando, Florida, USA
Hey Mr. Mooney I just wanted you to know that I won the science fair for my school (my name was in the newspaper)and got 3rd place in the regionals for Orange County. Thank you for all your help because you made this possible.
Thanks again,
- Orlando, Florida, United States of America
2006
Wow! Congratulations Chris. As any reader can see, you did an ambitious and excellent science project! It was very nice of you to credit me. Thank you. But I did next to nothing as the readers can see. Congratulations on the recognition you earned!
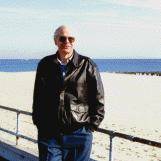
Ted Mooney, P.E.
Striving to live Aloha
(Ted can offer longterm or instant help)
finishing.com - Pine Beach, New Jersey
2006
Q. Sir can you please tell me what to add to CuSO4 to make it more reactive while electroplating . I am a 8th grade student and I need to know it very fast !!
Sonal J- India
February 15, 2012
A. Hi Sonal. The solution should be acidic for best electroplating. Older students would probably add some dilute sulfuric acid, but at your age you might want to try vinegar. Good luck.
Regards,
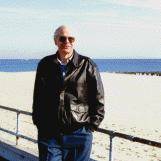
Ted Mooney, P.E.
Striving to live Aloha
(Ted can offer longterm or instant help)
finishing.com - Pine Beach, New Jersey
February 16, 2012
Q. I am a student who is researching on electroplating. I was thinking about an example of electroplating using copper which was to coat aluminium where the electrolyte is copper sulphate. Why is it that you need to use copper sulphate? could the process still be done if you had cyanide which dissolved a copper anode?
Best regards,
Ahmed
- Stockholm, Sweden
February 28, 2012
A. Hi Ahmed.
Cyanide can theoretically be used as a copper plating solution, but it is a powerful, deadly poison, not to be used for student projects or by people untrained in its safe handling. Good luck.
Regards,
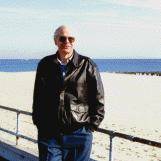
Ted Mooney, P.E.
Striving to live Aloha
(Ted can offer longterm or instant help)
finishing.com - Pine Beach, New Jersey
September 2012
Q. So I'm working on a science fair project -trying to make something non-conductive become somewhat conductive. I plan on coating a non-conductive object (I think I'm going to use a shell) with graphite and electroplating it with copper. I've tried to collect information on just exactly what tools I'll need. I understand I'll need an electroplating bath -containing copper sulphate- a power source putting out around 3 volts?, and an object. Do I need a chunk of copper as well? I've been getting really mixed reports in my research. I hope you can help me... I'm afraid I'm rather in the dark.
Clarissa K [last name deleted for privacy by Editor]- Salt Lake City, Utah, USA
September 27, 2012
A. Hi Clarissa.
Yes, copper sulphate ⇦ on eBay or Amazon [affil link] is fine, 3 volts is fine (two 1-1/2 volt batteries), and a chunk of copper (from wire, a copper pipe fitting, or pennies from 1982 or earlier).
Regards,
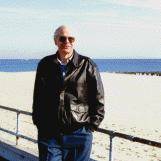
Ted Mooney, P.E.
Striving to live Aloha
(Ted can offer longterm or instant help)
finishing.com - Pine Beach, New Jersey
September 28, 2012
A. I made an instructable on how to copper plate a U.S Quarter without electricity. Here is the link:
http://www.instructables.com/id/Copper-Plating-a-Quarter-Without-Electricity/
and Video:
- Managua, Nicaragua
March 29, 2017
Thanks Marvin!
Note to readers: Although finishing.com is free of pop-ups, instructables.com is loaded with them -- don't blame us :-)
Regards,
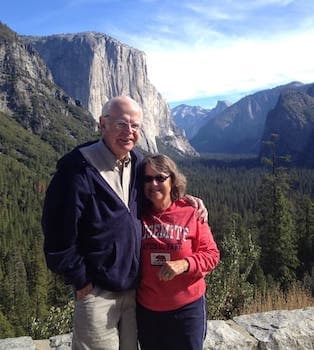
Ted Mooney, P.E. RET
Striving to live Aloha
(Ted can offer longterm or instant help)
finishing.com - Pine Beach, New Jersey
March 2017
Q, A, or Comment on THIS thread -or- Start a NEW Thread