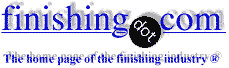
-----
Excessive Sludge Buildup in Zinc Phosphating Bath

Q. How to make a 1000 ltr Phosphating bath? How many ltr of liquid Phosphate and accelerator to add. Sludge making in tank is very fast!
Sagar Patel- Rajkot India
January 15, 2022
A. Hi Sagar. Sludge generation is always fast but TSN Sankara and Tony Wagstaff offer good advice here, and the helpful comments keep on coming :-)
It's probably difficult for people with other native languages to use the same anglicized name on each posting, but please try because it makes it easier for others to help you when we can search the site for your name and see all of your postings to get a better feel for who you are and what your overall situation is :-)
Luck & Regards,
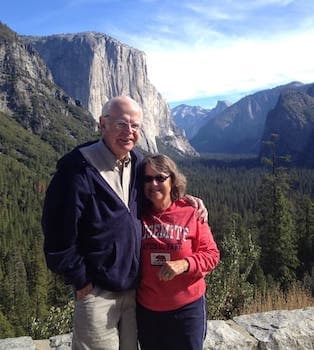
Ted Mooney, P.E. RET
Striving to live Aloha
(Ted can offer longterm or instant help)
finishing.com - Pine Beach, New Jersey
Zinc Phosphate Tank Turnovers
Q. Hello,
I have a 3500 gallon zinc phosphate tank in a system that can theoretically process 5600 sqft of steel each hour, I am trying to determine how many pounds of sludge this will generate. As well as how many tank turnovers I need to make an hour.
Does anyone know how to properly make this calculation? Or could you point me to some literature that might help.
- Niles, Michigan
July 1, 2024
A. Hi Spencer,
We appended your question to this related thread so that you could find some answers immediately while we await readers offering specific attention to your posting --
Martin Ings suggested 4-7 turnovers. While I don't see specific advise on the calculation that you seek, there is a lot of very helpful info on what increases and decreases sludge generation.
Luck & Regards,
Ted Mooney, P.E. RET
Striving to live Aloha
(Ted can offer longterm or instant help)
finishing.com - Pine Beach, New Jersey
⇩ Related postings, oldest first ⇩
Q. Dear Sir
We are facing problem of excessive sludge buildup and the bath does not remain green even after continuous filtration. What can we add in the bath so that the sludge goes down and the color of the bath remains green.
Can some one help me?
Regards,
Paint Shop - Noida, India
2005
A. Dear Amitabh Kohi,
Phosphating is a conversion coating process in which metal dissolution by the attack of free acid (phosphoric acid) is the basis of coating formation. The ferrous ions formed at the metal/solution interface gets oxidized to ferric ions which in turn combines with the phosphate and gets precipitated as ferric phosphate sludge.
If your bath is producing more sludge, then check the free acid value. If the free acid content is higher than the recommended level, then it will cause the formation of excessive sludge.
I am not sure about the green colouration of the bath solution.
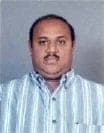
T.S.N. Sankara Narayanan
- Chennai, Tamilnadu, India
(ed.note: The good doctor offers a fascinating blog, "Advancement in Science" )
A. Hi
You have given only basic info, but simply there is nothing you can add to reduce the amount of sludge being produced; however you can look into reducing the amount of sludge produced initially.
1 Is your present filtration/sludge removal system efficient, are pipes becoming blocked, are pumps working correctly.
2 Are you maintaining the correct pointage for total acid and accelerator? High accelerator causes higher sludge levels.
3 Are you getting carryover from the cleaners? Any alkali going into the phosphate tank will cause sludge to be produced.
This is just the start, there is no magic additive.
- Lincoln, UK
Q. Sir
There is no carry over and we are maintaining 2-3 ml of toner in the bath, T.A. 24-26, F.A. - 0.6 still the sludge is more. I want to know what is the usual amount of sludge generated in a Zinc Phosphating bath may be per square meter. We have a problem in our sludge filter pump which picks up chemicals from the tank it is only 1.5 inches in diameter is this creating a problem.
Please help.
Regards,
- Noida, U.P.
A. Without further information I agree with Tony Wagstaff.
In principle the loss of "green colour" is due to the loss of nickel content of the bath. This will be due to mechanical effects or chemical instability resulting from the wrong TA/FA ratios or the wrong Zinc Phosphate replenisher.
The excessive sludge will be controlled by correct TA/FA ratios, accelerator content and no excessive metal loss, in principle the metal loss should be 50% of the coating weight.
Tank turn-over should be between 4-7 per hour and avoid high temperature above 60 °C.
Good filtration is always important using filter press or paper.
- Bletchley, Milton Keynes, UK
A. Mr. Kohli,
If the green colouration of your bath is due to the nickel salt then I agree with Martin Ings that the loss in green colour is due to the loss in nickel content.
What is the nickel content of your bath?
If you are losing nickel (loss in green colour) then is it also precipitating along with the sludge with ferric phosphate?
Ferric phosphate is white colour. What is the colour of your sludge?
It is surprising to note that your bath is producing heavy sludge for a free acid pointage of just 0.6.
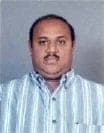
T.S.N. Sankara Narayanan
- Chennai, Tamilnadu, India
(ed.note: The good doctor offers a fascinating blog, "Advancement in Science" )
Q. Dear Sir
You are very right the colour of the sludge is white.
Nickel concentration is about 20% in the pure phosphating chemicals.
Regards,
- Noida, India
A. Phosphating baths are formulated with a zinc salt, phosphoric acid and an accelerator. The amount of zinc salt and phosphoric acid in a bath are chosen in such a way that it contains soluble zinc phosphate with a small excess of free phosphoric acid (Free Acid). The free acid causes dissolution of the metal and enables a raise in interfacial pH (due to the consumption of acid at the metal-solution interface). When the raise in interfacial pH reaches a particular level (called as the point of incipient precipitation), the soluble primary phosphate gets converted to insoluble tertiary phosphate and deposit on the metal substrate.
The equilibrium between soluble primary phosphate and insoluble tertiary phosphate will be altered by a change in pH and temperature of the bath.
If you operate your phosphating bath at a pH or temperature higher than the recommended level, then the conversion of the soluble primary phosphate and insoluble tertiary phosphate will occur throughout the bath and will get precipitated. The tertiary zinc phosphate is also white in colour.
This is the reason why Martin Ings has suggested you to avoid high temperature above 60 °C. Also as suggested by him, check the metal loss and coating weight. The ratio between the metal loss and coating weight (called as conversion ratio) should be around 0.4-0.6.
Check the free acid, total acid, free acid to total acid ratio, pH and temperature of the bath as to meet the recommended level. Also check the conversion ratio. This will give an idea about the amount of metal loss and the quantity of sludge that will be formed.
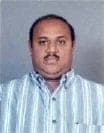
T.S.N. Sankara Narayanan
- Chennai, Tamilnadu, India
(ed.note: The good doctor offers a fascinating blog, "Advancement in Science" )
Q. Sir
I can very well understand the parameters, etc. but when you say ratio between coatings and loss of metal I am not able to understand; can you please let me know the method for the same?
The filtration should be slow and continuous as in this case our outlet pipe from the to the filter is small only 1.5 inch in diameter or it should be big our bath size is 6000 Ltrs., temp is 50 °C.
All the other parameters are within control.
Regards,
- Noida, UP, India
A. Dear Sir,
The green color of the bath is because the ferrous ions of the material coated in it. First, the material dissolves in the bath, it causes a raise of pH and that results in the precipitation of a tri-basic phosphate layer of zinc and nickel (and iron) over the surface.
The sludge is produced (I think) because of the low free acid in the bath, if the sludge is white it is probably zinc phosphate or iron (ferric) phosphate. They precipitate if the pH is higher than 3 or so.
If it is an accelerated (hydroxilamine/chlorate if it is an internal accelerant or nitrite if it is external) phosphate bath, the sludge is almost only ferric phosphate, you can avoid it only changing the product or asking for a new formulation.
I hope that you can find a solution to your problem, the buildup of sludge is unavoidable in phosphate baths, but they can be minimized maintaining the parameters fixed during the process.
Best regards,
- Lanus, Buenos Aires, Argentina
August 13, 2010
Multiple threads merged: please forgive chronology errors and repetition 🙂
Q. What is the best heating method for a zinc phosphate immersion tank? I currently use a plate and frame heat exchanger. The phosphate temperature should be at 115 °F. I am using 150 °F water in the HX.
The HX gets fouled with sludge quickly. The frequency of cleaning of the HX with acid flush is every 3 days or so. Disassembly and hand cleaning is once a month.
We have thought about using a shell and tube HX or using plate coils inside the tank.
Any shared experience would be appreciated,
Pretreatment chemicals - Rocky Hill, Connecticut, USA
2006
A. Something is not right with the bath itself. Unless you're using it 24 hours per day you should not generate that much sludge. Sludge in a Zinc phosphate bath comes from three sources - one is the water being used to make up the bath, anything in the water will form sludge when the water evaporates, (hardness ions like Calcium and Magnesium make a hard, whitish scale). Another source is the metallic phosphates that naturally form during the processing of metals, being a conversion coating process there are some by-products that will form sludge. The third can be a byproduct of the accelerator.
OK, there's a fourth... excessive drag-in of dirty rinse water or cleaning materials WILL cause excess chemical usage and sludge.
In short, first get the bath under control, then be sure the water going into it is good, then keep the rinse ahead clean. If drag-in is a problem you'll have to address it.
My money is on process control and water issues. Take care of those two things and the savings will pay for the effort.
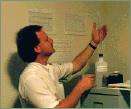
Jeff Watson
- Pearland, Texas
Q. David,
We have the exact same problem, and are on a similar if not more frequent schedule as you are. We currently use city water rather than RO water for water additions/makeup... Is RO water an absolute must to prevent excessive sludge?
- Redmond, Washington, USA
2006
A. If the temperature is more than 15 or 20 degrees differential, you form zinc phosphate flakes inside the heat exchanger. The temperature must be modulated. That's what makes the flakes. Use a step down heat exchanger and an automatic johnson valve to control the temperature. It works. Good luck.
DENNY [last name deleted for privacy by Editor]- Peru, Indiana, USA
January 26, 2011
A. I have seen zinc phosphate baths work with very little sludging. The tanks were heated with steam coils that were electropolished with quick release couplings to switch coils in and out quickly. The electropolish allows the dried sludge to fall off with one hit. One tip is the tank size should allow you to keep parts 6 inches off the bottom so as not to disturb the sludge. Every week let the tank sit overnight and draw off the liquid -- clean the walls and bottom of the tank and put the solution back in your tank. This keeps the tank broken-in, keeps your ratios in line.
If you idle the tank without running work thru it the ratio changes so it is best to have a basket of steel to run to keep the ratio up if you only have the occasional parts.
- Waterbury, Connecticut, USA
June 14, 2018
Q. Sir,
We are planning to install a continuous filtration system for our zinc phosphating bath. How effective is a filter press? Are there any other options like bag filters for this application available. Sludge build up would be around 5 kgs per day.
Thanks in advance.
- Chennai, India
April 7, 2011
A. Hi Jothi
My personal opinion is that when you have a lot of sludge production, and the sludge generation is a continuous process, and it's a relatively filterable sludge rather than a gelatinous mess -- all as in zinc phosphating -- gravity belt filters with continuous disposable paper rolls are a good way to go.
The way these work, briefly, is that a continuous roll of newsprint unrolls onto an open wire conveyor belt, and the sludge is pumped onto it at one end, the liquid flows through the paper and is collected in a pan below the belt and returned to the phosphating tank; and the paper and sludge roll off the other end of the belt into a dumpster of some sort. There is a simple liquid level control which causes the belt and paper to advance no faster than necessary to keep the filter from clogging.
Luck & Regards,
Ted Mooney, P.E. RET
Striving to live Aloha
(Ted can offer longterm or instant help)
finishing.com - Pine Beach, New Jersey
Q. 1. What should be the quantity of sludge content in phosphating bath?
2. Which elements are present in Accelerator and in Neutraliser?
- Gurgaon, Haryana, India
February 6, 2012
Hi, Tahir.
Can you please try to post with more words explaining your own particular situation? It isn't clear yet in what ways the previous responses are & aren't helpful.
Thanks and Regards,
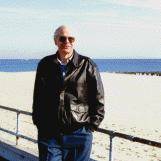
Ted Mooney, P.E.
Striving to live Aloha
(Ted can offer longterm or instant help)
finishing.com - Pine Beach, New Jersey
Q. How many (in grams) sludge will be formed per square meter of steel when treated with zinc phosphate. Thanks! Kindly post the reference if there is any.
Cris Jhon G. Caipang- Manila, Taguig City, Philippines
September 25, 2012
Q. Dear all,
Can anyone help me to find out how much amount of accelerator that we have to add into phosphating bath per Liter volume?
Thanks for your help :)
- Bogor, Indonesia
November 25, 2012
Hi Cris, Mutiara, and readers ...
As you are seeing here, when questions are cast in the abstract, people usually don't respond. The first thought of many readers may be "I'm here to participate in solving interesting problems, not to look stuff up in a book so others can avoid doing so" :-(
Please try your best to introduce yourself and to draw interest towards your specific situation; people want to learn from it :-)
Luck & Regards,
Ted Mooney, P.E. RET
Striving to live Aloha
(Ted can offer longterm or instant help)
finishing.com - Pine Beach, New Jersey
Q. Please tell me on what basis addition of sludge modifier is to be done in phosphate bath. Is there any criteria for addition?
Kedar patil- pune , Maharashtra
October 7, 2014
A. Hello dear,
Sludge content in Phosphate bath depends on following some factors as :
1. Activation tank condition. How old is activation bath? Do you have any overflowing/refreshing mechanism of activation tank in regular production?
2. For activation bath should maintain TA<6 & pH<9
3. Keep Phosphate TA, FA & Toner value at lower side of Specification.
4. Keep Phosphate bath temperature at middle of spec. (<55°C)
5. Filtration pump capacity should be such as it will filtrate 1/3rd of phosphate chemical per hour.
6. last but imp. point that Main chemical & toner of phosphate should not be added at one location of phosphate tank to avoid its faster reaction. You can keep main chemical addition at tank entry & Toner addition at tank exit.
Hope this will help you to resolve your problem.
Thank you.
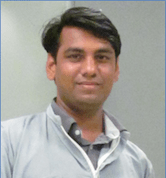
Sachin Gite
- Pune, Maharashtra, India
Q. Dear All:
How may I reduce the sludge formation in a non-accelerated phosphating bath working at 75 °C, TA 50, FA 5-7, Iron 0.1% to 0.5%? Is there a chemical additive to reduce the sludge formation?
Thank you
- bogota, colombia
November 10, 2014
Q. Respected sir ... please tell me function of fa, ta, accelerator in phosphating process.
Rajesh Kumarsswl - Dapper,Punjab, India
July 5, 2016
Hi Rajesh. We appended your inquiry to a thread which generally addresses your questions.
If you are having a specific phosphating problem I am confident that the readers can help you. Please tell us what items you are phosphating, what metal the substrate is, what type of phosphate you are dealing with, and why you are phosphating (as a break-in coating, as a pretreatment for powder coating, etc.)
Are you using a proprietary phosphating process from a supplier, or attempting to do a home-brew? Thanks.
Regards,
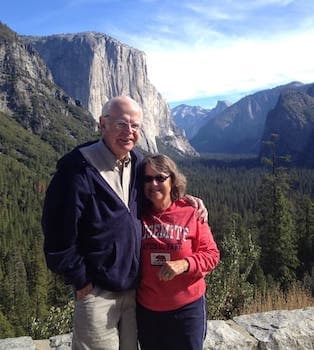
Ted Mooney, P.E. RET
Striving to live Aloha
(Ted can offer longterm or instant help)
finishing.com - Pine Beach, New Jersey
Q. Respected sir, we are using tri-cation phosphate of 40 kl. Parameters are following:
fa 1-2
accelerator 3-4.5
We are phosphating wheels of mostly car & tractors.
Problem is that my components show yellowness after water rinse, and coating is not observed on components.
sswl,dapper,Punjab - hisar,haryana, India
Sludge build-up in Phosphating
Q. Hello,
I am trying to find different ways in which sludge explosion can be avoided in a phosphating bath (zinc phosphating process). I know that this could be avoided via the addition of old sludge or tertiary zinc phosphate crystals. However, I cannot find theoretical resources on the topic.
Any other suggestions of how sludge explosion could be avoided are also highly appreciated.
Razan
- Worth am Rhein, Germany
August 1, 2016
by Biestek & Weber
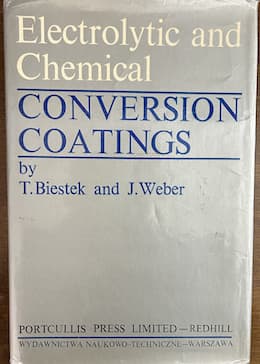
on Amazon
on AbeBooks
(affil link)
A. Hi Razan. This thread offers some good insights. Biestek and Weber's "Conversion Coatings" ⇨
suggests that heavy sludging is due to incorrect coefficient "f", or presence of Ca and Al. If you can explain your own particulars in detail you will usually get more & better responses. Thanks.
Regards,
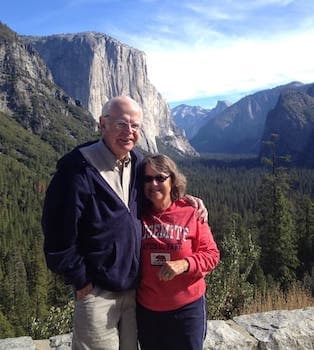
Ted Mooney, P.E. RET
Striving to live Aloha
(Ted can offer longterm or instant help)
finishing.com - Pine Beach, New Jersey
Zinc phosphate sludge formation rate
Q. My coil finishing department has 2 zinc phosphate tanks to provide coating to carbon steel coils (Weight of each coil=1.4 MT). One tank has a dewatering filter attached to it to filter out the phosphate sludge. We want to incorporate the existing filter for both the tanks. How should I go about this problem? is there a way to determine the sludge formation rate based on bath parameters and total coils coated each day?
Zain Ansariproduction engineer - Mumbai, Maharashtra, India
October 24, 2016
A. Hello Zain!
Getting rid of the sludge is a batch process, so if now you are pumping the sludge two times per week, if you use the same filter/tank for both processes, you may be using it four times per week instead of the old two.
We have a phosphating line for 1,4 MT coils with one phosphating bath, and two times per week for a 7000 liter bath is enough to clean it up.
Hope that information can help you decide how you make this work!
Best regards,
Daniel
N FERRARIS S.A. - Cañuelas, Buenos Aires, Argentina
Q. Sir, in our Zinc Phosphating plant we have a PHE and a motor to circulate Phosphating solution. our problem is that a huge amount of sludge is generated every month blocking the PHE. Is there any contactless method to heat Phosphating solution, and any chemical which can dissolve Phosphating sludge?
Ashwin DeshpandePlant Engineering - Pune - India
November 27, 2018
Ed. note: This RFQ is outdated, but technical replies are welcome, and readers are encouraged to post their own RFQs. But no public commercial suggestions please ( huh? why?).
A. Hi cousin Ashwin. We appended your inquiry to one of at least a half-dozen threads about phosphating sludge. Please search the site if you don't see the answers you need on this page.
I don't know of contactless heating methods, nor of a practical way to dissolve the sludge, but I believe there are five possible things to do --
1). Minimize the sludge generation through the process control measures described here.
2). Keep the sludge from adhering, and make it easier to clean, by using electropolished type 316SS wherever possible.
3). Whatever heating method you employ, use 'derated' heaters so they will not be as hot.
4). Try to design hopper-style tanks so there is a desired place for the sludge to accumulate.
5). Remove, filter, and dispose of the sludge in the hopper frequently.
Luck & Regards,
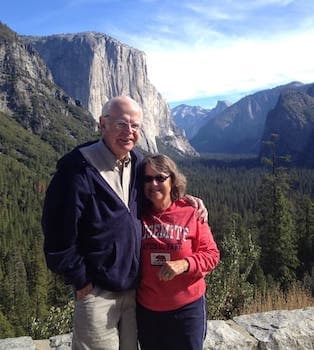
Ted Mooney, P.E. RET
Striving to live Aloha
(Ted can offer longterm or instant help)
finishing.com - Pine Beach, New Jersey
Q. Thanks for the reply sir, Is there any means by which I can avoid sludge formation within our PHE. We need to clean it within 30 days.
Ashwin Deshpande [returning]Kirloskar Saswad - Pune, Maharastra, India
A. Hi Ashwin. There is no way to avoid sludge formation, you can only minimize it, as explained on this page, by proper chemical balance and avoiding high temperatures.
I assume PHE means plate heat exchanger? My personal opinion is that an external heat exchanger is not a good way to heat the phosphatizing solution: heat exchangers rely on high fluid flow rates to generate high U factors so that high temperatures and smaller heat exchange areas can be used. This is the opposite of the 'as low as possible' temperatures and 'as high as possible' surface area desired for heating phosphate solutions.
Oversized (derated) electropolished stainless steel heating coils in the phosphatizing tank are (in my opinion) the best approach.
Regards,
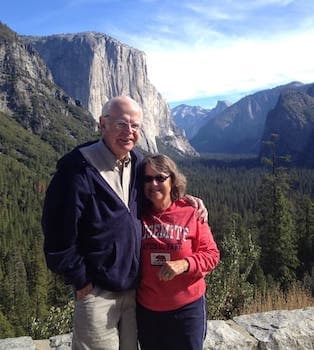
Ted Mooney, P.E. RET
Striving to live Aloha
(Ted can offer longterm or instant help)
finishing.com - Pine Beach, New Jersey
A. I used to be an on site service technician for a treatment company many years ago at an automotive manufacturing facility. The zinc phosphate system at that time generated a lot of sludge. My current employer a coil coater, in the last few years has been using zinc phosphate on HDG as a preferred system where previously it was only used occasionally. Apparently some break-though was made by my former employer which greatly reduced the sludge production.
The system here uses a heat a exchanger that uses thermal fluid. This probably also helps.
The sludge can be cleaned out with HCl but the tanks and piping must be rinsed well after to prevent what they call white nubbing.
Coil Coating - Brampton, Ontario, Canada
December 3, 2018
Tube heat exchanger issues with iron phosphate tank
Q. We just installed a tube and shell heat exchanger to heat our stage one cleaner/coater powdercoat pretreatment bath. The boiler side of the heat exchanger runs at max temp 180 °F. The bath temp is 120 °F. We pump 100 gallons of bath water through the heat exchanger per minute. The tubes in the heat exchanger will buildup with a yellow/white sludge after a couple of days of running the line. Once the tubes are coated with the sludge the exchanger is no longer able to keep the stage 1 bath at 120 °F. How can we minimize the sludge buildup in the heat exchanger tubes so we can extend the time between descaling the heat exchanger?
Josh Gallemployee - Burlington, Iowa
November 29, 2018
A. Hi Josh. Although your process is iron phosphate rather than zinc phosphate, your question is so similar to Ashwin's that we put them on the same page. I personally believe that heating coils within the tank are a better idea than external heat exchangers for phosphating solutions.
Regards,
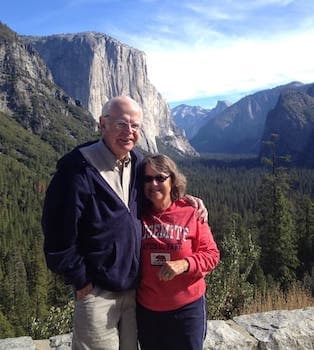
Ted Mooney, P.E. RET
Striving to live Aloha
(Ted can offer longterm or instant help)
finishing.com - Pine Beach, New Jersey
Comment: Late to the thread but I frequently check in on topics. Lots of good info on this site. In this thread, there is a lot of missing detail. Sludge formation is determined by many factors, FA being a small portion. My suggestion would be to include more bath particulars such as water quality, fluoride content, type of washer (spray?, immersion?), normal targets, substrate mix, type of Accelerator, and more...
It is challenging to figure this out without some of this info. While the original issue is quite old I am not sure if the numbers presented are correct with .6/24.0 FA/Ta? Seems off? Just seems strange, is this dilute FA or KCl?
Anyway, I know the post is old so I apologize if I am wasting time.
Best Regards
Technical Sales Management - Des Moines, Iowa USA
October 9, 2019
A. Thanks very much Aaron! I once read a 'Hints from Heloise' newspaper column where a woman wrote that she spilled red wine on her blouse, and Heloise's answer began: "If you can catch it before it starts to dry ...". Seriously? The writer had composed a letter, mailed it, awaited its selection and syndicated publication in a newspaper. The stain had certainly started to dry :-)
The point being that, while we try to answer people's inquiries in timely fashion if we can, there are (just like with Heloise) far more silent readers than posters. 37 people read this page in the last month, spending an average of 7 min 22 secs on it -- so your posting continues to be seen and appreciated. There are no "dead" threads on this site -- only threads with recent input and threads without. Thanks again!
Regards,
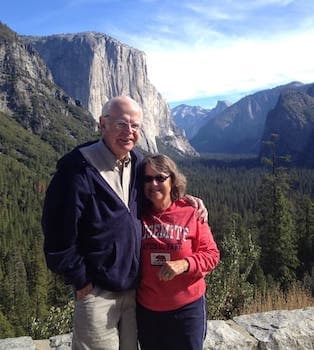
Ted Mooney, P.E. RET
Striving to live Aloha
(Ted can offer longterm or instant help)
finishing.com - Pine Beach, New Jersey
Q, A, or Comment on THIS thread -or- Start a NEW Thread