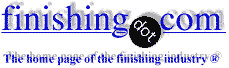
-----
Acceptance criteria after salt spray test
Quickstart:
One of the most common requirements for plating is that it pass a certain number of hours of 'salt spray testing' as proof of its corrosion resistance. What comprises a salt spray test and how it is conducted is described in specs such as ASTM B117 and ISO 9227
Q. Sir
Is there any standard for judgement criteria for salt spray test?
How to define in percentage?
Any pictorial representation is there like we have for grain size , microstructure for metallurgy?
Regards
- faridabad, India
February 19, 2024
A. Hi Sundar,
The specification or process which you are plating in accord with is the document which defines passing or failure. It will depend on what process you are doing on what substrate. For example, pass or fail for chromating aluminum will be much different than pass or fail for sacrificial plating, barrier layer plating, painting, powder coating, passivation of stainless steel, etc.
If you are processing in accord with specifications, please advise what specifications, and we can review their requirements with you. If you are not processing according to accepted specifications, you and your customer will have to argue it out :-(
Luck & Regards,
Ted Mooney, P.E. RET
Striving to live Aloha
(Ted can offer longterm or instant help)
finishing.com - Pine Beach, New Jersey
⇩ Related postings, oldest first ⇩
Q. Does anyone have any ideas on the best way to test EN plating as well as brush nickel plating in terms of corrosion. The parts are made from silicon iron and 1215. Basically the parts are EN plated and then any chips are repaired with brush nickel plating. I want to test the repaired areas. There are many different corrosion chambers on the market, not sure where to begin. Thanks.
Gary PetrilloEngineering - Wallingford, Connecticut, USA
2004
A. The solution to this problems starts with knowing the probable end-use environment, and then finding a lab corrosion test method that replicates most/all of those conditions. When the test method is known, it is much easier to select a lab corrosion testing cabinet that can perform it. Lab corrosion test methods generally fall into three categories: Traditional salt fog & humidity tests like ASTM B117, Basic Cyclic corrosion tests like ASTM G85 Annex 5, and Advanced Cyclic corrosion tests like SAE J2334. Doing a Keyword search on "how to select" and "cyclic corrosion test chamber" could yield articles that will help you focus on specific test methods and the types of cabinets that perform them.
Harold D. Hilton- Chicago, Illinois, USA
Q. What are the acceptance criteria for visual inspection after the salt spray test of Zinc plated & trivalent green passivated parts. There are two types of rust:
i) White &
ii) Red
Is white rust acceptable after 300 hours of salt spray test?
automotive parts manufacturer - BangaloreIndia
2005
A. Dear friend,
You are probably from the receiving inspection department, looking for tightening the supplier. Well.
All zinc coated material will have two types of corrosion, namely Zinc and Iron. The corrosion product of Zinc is Zinc oxides which are white in color. The corrosion product of Iron is ferrous oxide which is red in color. That's how you call the results as White rust and Red rust.
If you are getting a white rust, you can interpret the quality of chromate on zinc coatings. All plated products are chromated to protect zinc corrosion.
With the Red rust you can interpret the quality of zinc plating. The duration to start the red rust after white rust if it is low, then the zinc plating is porous.
In plating getting a white rust after 300 hrs is one of the best quality out of my experience. You need to specify the requirement of salt spray resistance, there are no standards. However remember every process has its own limitation.
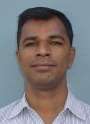
V. G. Rajendran
- Trichy, Tamilnadu, India
A. I believe that there are two types of rust called White rust and Red rust.
White rust is nothing but failure phenomena of coated surface and Red rust is failure phenomena of parent material.
White rust and Red rust can be decided by the nature of coating.Generally salt spray specification for white rust will be 46 hrs and red rust will be 120 hrs, of course depends on nature of coating.
- Chennai
A. While assessing Salt spray test results many interpret black spots or patches as failure of Corrosion test.This is only an intermediate stage and this is not to be taken as failure. Only White corrosion product and later on red rust formation need be considered for interpretation of SS Test results especially in the case of Zinc and Zinc alloy coatings.
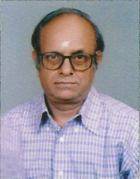
Subramanian Ramajayam
consultant - Bangalore, India
January 16, 2009
Thanks, Subramanian! I can agree 95%, but not 100%. Some specifications define failure, and in that case failure is whatever the spec says it is. And, of course, a buyer can write any spec they wish, which can define failure in any way they wish.
But what a buyer probably cannot do (as you say) is fail to define failure, but then claim that black spots or patches constitute failure :-)
Regards,
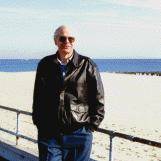
Ted Mooney, P.E.
Striving to live Aloha
(Ted can offer longterm or instant help)
finishing.com - Pine Beach, New Jersey
Q. I want to ask you only one question about salt spray on spanner coated with chrome plating.
We are using 1% NaCl for test and temp. of 35°, nickel thickness on the spanner is 12 micron. But it stands up to 15 hours, why?
- Jalandhar, APunjab, India
May 16, 2012
A. Hi Deepak.
Nickel-chrome plating is a barrier layer type of plating, not a sacrificial plating. Thus, if there is any porosity or any pinhole, the nickel plating will accelerate the rusting of the substrate. You probably need duplex nickel plating or thicker nickel plating to improve the salt spray results. 12 microns only qualifies as suitable for mild exposure, not moderate exposure, let alone severe or very severe, per ASTM B456. What standard, if any, are you trying to plate to, and how many salt spray hours are you looking for. Thanks.
Regards,
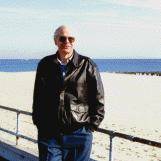
Ted Mooney, P.E.
Striving to live Aloha
(Ted can offer longterm or instant help)
finishing.com - Pine Beach, New Jersey
Q. Normally in India we use acceptance criteria of 144 hours for salt spray.
However, it is not clear at what time/limit white rust should be accepted.
- Mumbai Maharashtra India
December 5, 2012
A. Hi Prashant. What specification are the parts plated to? The plating specification, such as ASTM B633 for zinc plating, usually defines what constitutes failure. If not, Subramanian's answer should be helpful to you. Good luck.
Regards,
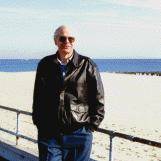
Ted Mooney, P.E.
Striving to live Aloha
(Ted can offer longterm or instant help)
finishing.com - Pine Beach, New Jersey
Q. We are doing salt spray test on zinc plated parts.
As per our internal specification no white rust/red rust should appear after 144 hours.
However, what I understand is, white rust is actual corrosion of plating and not corrosion of base material.
So plating coat is actually preventing base material and sacrificing itself.
So why not accept white rust and only concentrate on red rust?
So what should be acceptance criteria for white rust?
- Mumbai Maharashtra India
December 14, 2012
A. Hi Prashant. White rust is unsightly and it can "gum up" things -- making it difficult or impossible to assemble/disassemble things, operate door latch mechanisms & triggers, fire extinguishers, etc.
White rust is supposed to be forestalled with chromate conversion coatings ... and there is nothing wrong with a spec that demands some given number of salt spray hours before white rust.
Regards,
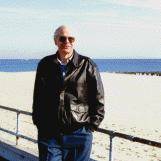
Ted Mooney, P.E.
Striving to live Aloha
(Ted can offer longterm or instant help)
finishing.com - Pine Beach, New Jersey
Q. Dear experts,
We are producing hot rolled steel sheet metal part with zinc plating.
The salt spray test basis is ASTM B117, 96 hours no white rust or red rust.
The test was passed, but customer refused to accept the parts because they found 1 black spot on a sampled part.
Now, he asks for a standard to testify that black spot is allowed after salt spray test is passed, before he can accept this lot.
However, I can't find any ASTM standard denoting the acceptance of black spot.
Would anyone share with me the standard or his experience how to deal with this situation?
Best regards,
Fai.
Engineering - Hong Kong
November 4, 2013
A. Hi Fai. As Subramanian tells us on this page, black spots do not constitute failure. However, I think the main problem here is that you and the customer must agree what specification you are plating to, and I see no mention of that. Specifications help define what comprises passing and failure.
If your customer is not requiring plating to a specification, I don't see how he can reject anything; nor can I see how you can claim to be offering a satisfactory plating service short of polling the whole world for every vague opinion :-)
Good luck, but please use this disagreement as a launching pad for correcting the omission by referencing specifications in purchase orders and certs. Good luck.
Regards,
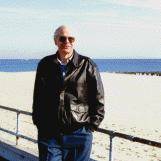
Ted Mooney, P.E.
Striving to live Aloha
(Ted can offer longterm or instant help)
finishing.com - Pine Beach, New Jersey
Do black spots on Electroless Nickel comprise salt spray failure?
Q. I would like to have some clarification on what is considered "corrosion" on electroless nickel. I am testing per AMS2404, using ASTM B117 to make up my solution. Periodically, I see black spots on my test panels. Is that corrosion, or does it have to be "red-rust" to be considered a failure?
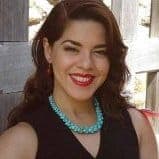
Claudine Meinhardt
Chemist - San Antonio, Texas USA
February 24, 2014
A. Hi Claudine. ASTM B117 is basically only the operating requirements for salt spray testing and doesn't define failure. Often, plating specs define failure, but unfortunately I don't have a copy of AMS2404 handy, so I can't comment on what if anything it says about failure. We appended your inquiry to an earlier topic where Subramanian says that black spots do not comprise failure; so, in the absence of anything to the contrary in AMS2404, you are correct that red rust is the dividing line between passing and failing.
Regards,
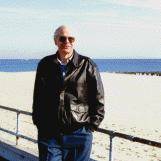
Ted Mooney, P.E.
Striving to live Aloha
(Ted can offer longterm or instant help)
finishing.com - Pine Beach, New Jersey
A. I have a copy of AMS2404, anyone need help please feel free to contact me.
Davey ShawShenzhen, Guangdong, China
Thanks Davey. It's copyrighted, so I can't ask for a copy, but if you would check how it defines failure, that would be a help!
Regards,
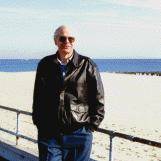
Ted Mooney, P.E.
Striving to live Aloha
(Ted can offer longterm or instant help)
finishing.com - Pine Beach, New Jersey
A. Hi Claudine,
AMS2404 says the base material shall be free from corrosion. So what you really need to know is whether the black spots are corrosion or whether it is something else causing the staining.
Incomplete oxidation of iron caused the formation of a mixture of the ferrous oxide and the ferric oxide (Fe3O4), this tends to be pretty black in color. The classic red corrosion product is the ferric oxide (Fe2O3).
So, can you analyse the black spot? XRF or SEM with EDX would be good tools to use. If the black spots contain iron then you have corrosion product and you should consider that a failure, AMS2404 does not make any distinctions between corrosion product oxidation states.
Aerospace - Yeovil, Somerset, UK
Q. I want to know in salt spray testing of painted material which type of rust comes earlier red or white?
Mohit Angirous- delhi, India
April 8, 2015
A. Hi Mohit. The rust from steel is called red rust, whereas metallic protective coatings on that steel (like zinc plating), if present, corrode to white corrosion products / white rust. In general, you would only get both white rust and red rust if the article is made of steel and has a sacrificial coating of zinc under the paint, and in that case the white rust comes first. But abstract questions are difficult to answer properly because the world if full of possibilities, and we can't cover every "If, and, & but". So if you can give us the details of your own situation, a more complete and reliable answer may be possible. Thanks.
Regards,
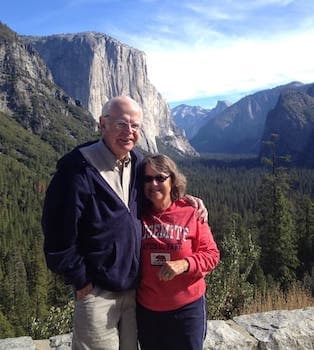
Ted Mooney, P.E. RET
Striving to live Aloha
(Ted can offer longterm or instant help)
finishing.com - Pine Beach, New Jersey
E-coated steel lasts 96 hours salt spray, customer wants 480
ACRONYMS:
CQ = commercial quality
Q. Hi
The customer product is CQ mild steel coated with e-coating and the customer specification is "no corrosion after 480 hours" in salt spray test. Reading the above posts, the spec "should be" between 96 hours to 144 hours. What are your thoughts on this? The substrates failed after 96 hours, with signs of red rust.
Regards
Sheldon
- Pinetown, Kwazulu Natal, South Africa
September 2, 2015
A. Hi Sheldon. I'm sorry but your posting seems to have two errors or wrong assumptions. :-)
First, a customer can require any specification for salt spray endurance he wishes (as long as it was referenced in the purchase order).
Second, these "96 hour" and "144 hour" specifications on this page are referring to zinc plated surfaces, not e-coated surfaces. E-coated surfaces do not fail in the same way as zinc coated surfaces, where the sacrificial zinc coating is gradually consumed.
I don't know your particular parts and your particular e-coating, but 96 hours sounds low for any high quality organic coating; are you doing good quality phosphating before the e-coating? 480 hours does not sound impossible, and may not even be unreasonable. Good luck with the issue.
Regards,
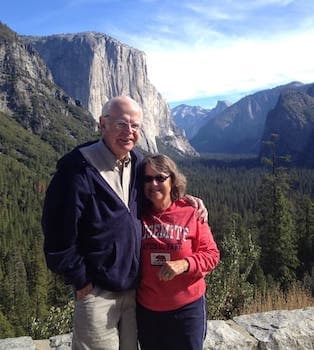
Ted Mooney, P.E. RET
Striving to live Aloha
(Ted can offer longterm or instant help)
finishing.com - Pine Beach, New Jersey
Q. Is it possible to have agreement with our customer on the white rust, something like % of white rust observed over the total surface?
Also, I want to get some clarifications over the topic of Black spots.
I feel that either white rust or black spot acceptance depends on situation or product structure. Areas which are not cosmetically visible and not obstructing function can be allowed to have some % of white rust / black spots. In this case we should have an agreement with our customer.
Automation - Hyderabad, India
June 23, 2016
A. Hi Pankaj. You are right that a buyer & seller are free to negotiate the performance requirements of the contract but there is an exception: some published specifications forbid you from 'diluting' them. The spec may contain wording that a purchase order can add restrictions or performance requirements but cannot reduce the requirements or selectively quote the spec. For example, if spec XXXX123 requires 96 hours of salt spray performance, the spec organization has declared in advance that a purchase order saying "plate per spec XXXX123 but only 48 hours salt spray resistance is required for 'B' surfaces" is employing the spec invalidly. In the event of a contract dispute you would therefore have a mess on your hands.
Plus, a salt spray test is an accelerated 'advance warning' test which is used to help determine if a process is under control; it usually does not mimic real-life performance, so to spend a lot of time defining allowable percentages of white rust on "A" surfaces vs. "B" surfaces, for example, may not be well applied effort -- real-world corrosion patterns are likely to be entirely different anyway.
Regards,
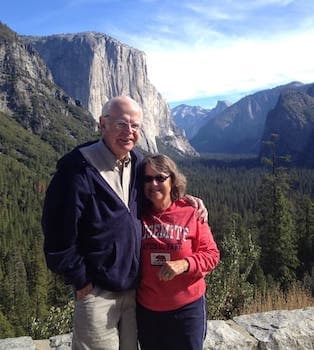
Ted Mooney, P.E. RET
Striving to live Aloha
(Ted can offer longterm or instant help)
finishing.com - Pine Beach, New Jersey
Can e-coating on cast iron withstand 480 hours of salt spray?
Q. Hi Everyone,
I also have similar problem with Sheldon, but the difference is in material; I use cast iron for the Salt Spray Test. And the requirement said it must reach 480 (FPO-5) with no rust at any surface. The part uses Electro Deposition Painting (EDP). Do you think is it still possible? Does anyone have the same problem?
Regards,
Agung
- Bekasi, West Java, Indonesia
August 24, 2016
Q. I would like to know how to differentiate between white rust and salt residue of salt spray test. Can someone help?
KY Tay- Bukit Mertajam, Penang, Malaysia
October 24, 2016
A. Hi Kay. I think it's as simple as the fact that NaCl is soluble and the stain will wash right off (I am not implying that simple rinsing will remove all salt and its corrosive effects ... just that salt will readily dissolve and the stains disappear).
Regards,
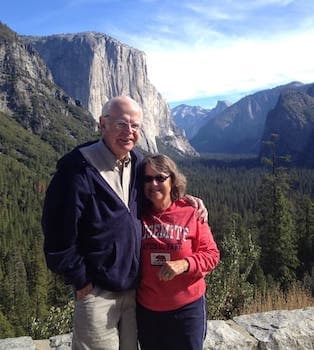
Ted Mooney, P.E. RET
Striving to live Aloha
(Ted can offer longterm or instant help)
finishing.com - Pine Beach, New Jersey
Q. SIR,
REQUEST YOU TO PROVIDE SOME NUMERICAL VALUE (REQUIREMENT FOR SALT SPRAY TEST).
WE ARE DOING SALT SPRAY TEST AS PER ASTM B117 FOR REINFORCING BARS WITH EPOXY COATING FOR 96 hr AS WELL AS 204 hr.
CORROSION RATE INDEX (cri) CALCULATED.
AT PRESENT WE ARE GIVING ONLY MASS LOSS (g/m2) AGAINST UNCOATED SAMPLES -- BOTH WILL BE SUBJECTED TO TEST.
CIVILAID TECHNOCLINIC PVT. LTD - Bangalore, KARNATAKA, India
November 21, 2016
Q. Hello all.
The salt spray test results report shows at 96 hours 5 g and the customer said I wish 10 g on e-coat process; the raw material is cast iron. The question is, for this process is it possible to meet with zero corrosion during 96 hrs ASTM B117 test.
Industrial Finishing - Brownsville Texas
April 11, 2017
A. Hi Santiago. I'm not understanding your usage of grams of corrosion, and the customer wanting more corrosion than you are getting -- something seems to be worded funny. But, yes, you can certainly get 96 hours of salt spray performance from proper pretreatment and e-coating.
Regards,
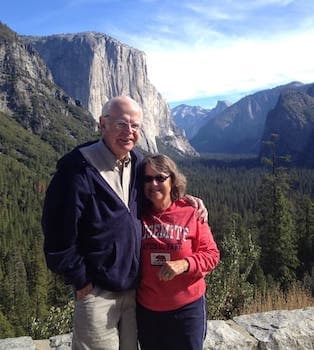
Ted Mooney, P.E. RET
Striving to live Aloha
(Ted can offer longterm or instant help)
finishing.com - Pine Beach, New Jersey
Q. Hello to all.
Please clarify the black spot observed in SS test what is this effect during testing time?
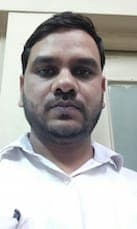
VIJAY Singh
lohia corp limited kanpur - kanpur uttar pradesh India
June 2, 2017
A. Hi Vijay. Subramanian says it does not represent failure. I agreed except that if the customer specs says it's failure, then it's failure. Brian Terry tells us that some specs like AMS2404 define the appearance of any corrosion as failure, and that the spots might be corrosion and can be tested. Then too, one person's black spots may not look the same or be the same as another person's black spots.
Please explain your situation so it's less abstract, and send some pics if possible. Thanks.
Regards,
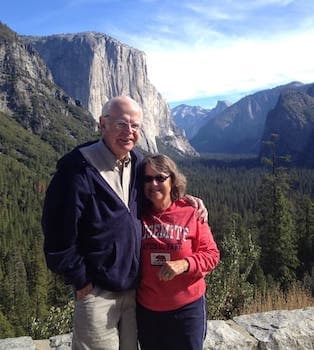
Ted Mooney, P.E. RET
Striving to live Aloha
(Ted can offer longterm or instant help)
finishing.com - Pine Beach, New Jersey
Q. Hi sir,
Define salt spray test and how many hours test for door handle (Mild steel) and what is the conditions. Which standard we need to refer for corrosion resistance test on ferrous materials?
- trichy, tamilnadu, India
November 30, 2017
? Hi cousin balaji. Please start with who you are, what you do, what type of plating or coating you are talking about, and what kind of door handle you are referring to (automotive interior, automotive exterior, home interior, home exterior lockset, etc.)
Regards,
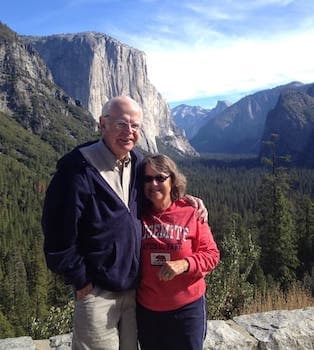
Ted Mooney, P.E. RET
Striving to live Aloha
(Ted can offer longterm or instant help)
finishing.com - Pine Beach, New Jersey
Q. Sir,
I want to know that in SS test what is method to check black corrosion on zinc plating. According to our product standard, conditions is 0.05% corrosion area of total test surface of base metal would be the passing criteria, so please help me can I consider black corrosion or spot as base metal corrosion or, if not, then what is the process to know base metal corrosion?
- Udaipur,raj. India
January 20, 2018
Q. Hello. I just want to ask you some help. Can you offer me any documents which I can get help while interpreting ss test results?
Thank you so much.
- istanbul TURKEY
January 29, 2018
A. Hi Yunus. The most important document is the specification which the parts were processed according to. Very often this will tell you how to interpret the results. Interpreting the results for salt spray testing of aluminum conversion coating, various electroplated coatings, powder coating, etc., may be quite different. Please tell us what specification number the parts you are referring to were processed to. Thanks.
Regards,
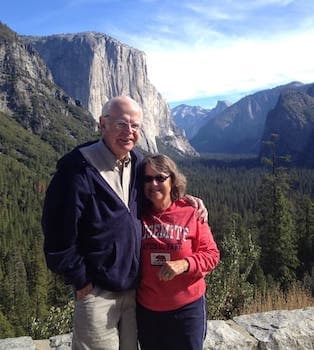
Ted Mooney, P.E. RET
Striving to live Aloha
(Ted can offer longterm or instant help)
finishing.com - Pine Beach, New Jersey
Q. Hi TED;
thanks for answering.
We're processing fe-zn, fe-ni, fe-cr, cuzn-ni, zn-cr, zn-ni.
So I need something about these processes.
Thank you so much.
Regards.
- istanbul TURKEY
January 29, 2018
A. Hi again, Yunus. You probably should find/choose a spec for each of those 6 processes (although I'm not sure what platings you are describing: Zn on Fe, Ni on Fe, Cr on Fe, Ni on Brass, Cr on Zn, Ni on Zn?).
In the USA we have MIL specs, ASTM specs, SAE-AMS specs and probably a few others. There are German DIN specs, Japanese JS specs, British BS specs, and ISO international specs. As previously mentioned, some of these specs will include interpretive guidelines for what constitutes failure in salt spray testing, but there is no single spec which defines what constitutes failure except with regard to itself.
Regards,
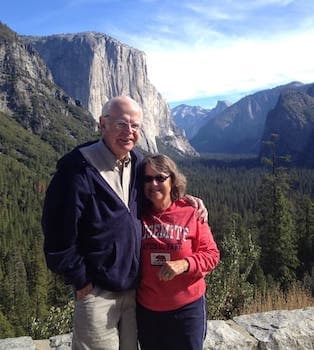
Ted Mooney, P.E. RET
Striving to live Aloha
(Ted can offer longterm or instant help)
finishing.com - Pine Beach, New Jersey
Q. Dear all,
We are a manufacturer of metal parts and we have received complaints from customer about failure of salt spray test. They are claiming of 72 hrs SST and therefore we have forwarded the complaints to supplier. They have replied that the storage time is one of the factors that affect the test result since the product customer used has been stored for 6 months and the test is best performed within the period of 24 hrs after electroplating. We are not sure if there is any direct relationship for the result and time period.
May I ask if there is any time limit or requirements for salt spray test after the metal is freshly electroplated? Can supplier of electroplating guarantee period of time that the products can pass the test? I have heard of half year from the supplier but I'm not sure. Currently the supplier is claiming that the test should be best performed within 24 hours after electroplating. Thanks for all your support.
Wang Tak Metal Products - Hong Kong
February 4, 2018
A. Hi Vincent. I'd be happy to hear to the contrary from any readers, and a buyer can write any spec they wish and demand compliance with it ... but I side with your supplier. If the parts endured shipment by sea, or storage in a corrosive, damp, or smoggy industrial environment for 6 months they could very well be exhibiting corrosion signs which will fail an examination after salt spray even before they go into the salt spray chamber :-)
Regards,
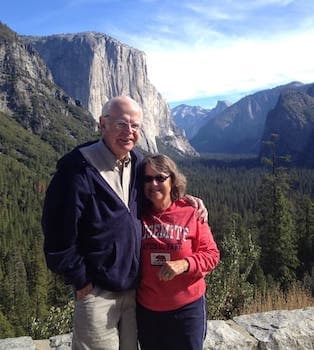
Ted Mooney, P.E. RET
Striving to live Aloha
(Ted can offer longterm or instant help)
finishing.com - Pine Beach, New Jersey
(you are on the 1st page) Next page >

Q, A, or Comment on THIS thread -or- Start a NEW Thread