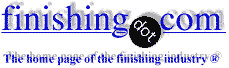
-----
Diphenylcarbohydrazide Trivalent/Hexavalent Chrome Testing/Checking method
Q. Hello all,
We have a customer inquiring about the use of diphenylcarbohydrazide to detect hexchrome in chemfilmed parts. The customer has not specified any particular application or use of this hexchrome verification, they simply inquired about the process.
Does anyone have any experience using diphenylcarbohydrazide to check hexchrome on chemfilmed parts? Any information or insight into this process would be greatly appreciated.
- Denver CO
November 20, 2024
Ed. note: While awaiting responses, we appended your inquiry to a thread which explains it pretty well.
Multiple threads merged: please forgive chronology errors and repetition 🙂
Q. I am having difficulty getting a firm answer regarding the yellow zinc dichromate / hexavalent chromium plating issue. For instance, one of my fasteners specifies a "MFZn5-C" finish. I am fairly sure that this is a hexavalent plating (yellowish in color). Is there a website where I can research various coatings to verify which are "good" from the hexavalent/trivalent standpoint? When do Tier 1's have to stop using / phase out? Where can I find the "law" or documentation stating this?
Thanks,
- Auburn Hills, Michigan
2003
A. Mr Andrew Card
Much has been written about ELV and it is on the net under ELV.
Your specific need :
1) If the chromate is yellow the likelihood of the layer containing Hex Chrome is very strong.
2) The European Union End of Life Vehicle ( ELV) directive is a good place to start your search.
3) Various companies like Ford, Toyota, GM , Delphi have outlined and defined their route to zero Chromate as early as 2004 and 5 for tier one suppliers.The directive allows till 2006-7 for conformity to zero Chromate.Individual companies have defined their own approach to this issue and at a AESF meeting early last year some clarity was achieved.
The article in back issues of Metal Finishing and other similar publications, AESF websites and even this site carry much of the data you need.
The directive states that by 2007 at least 80 percent of the average vehicle weight should be reused or recoverable, and by 2007, 80 percent should be reused or recyclable. The purpose of this edict, enacted in September 2000, was to prevent waste from the recovery, reuse and recycling of vehicles when they hit the scrap yard -- or their end of life. The legislation covers four heavy metals that make recycling difficult: cadmium, lead, mercury, and -- the one impacting the metal finishing industry most -- hexavalent chromium. The original legislation limited the amount of hexavalent chromium to 2.0 grams per vehicle, but only where the Hexavalent chrome was present for purposes of corrosion protection.
What we are talking about here are chromate conversion coatings, in all of their various hexavalent formulations. Chromates have been the mainstay for decades in providing adequate corrosion protection for zinc or zinc alloy-plated fasteners, tubing, brackets and other small parts. These parts number in the thousands.
Of 9 test methods available, no standard test is recognized by ELV Directive to validate 2.0 gms Hex chrome permissible per vehicle. Original compliance dated 2002 was postponed. Implementation delayed to 2007. AND ELV standard reduced to 0.0 (ZERO) gms. Hex chrome per vehicle effectively from 1-1-2007. Auto makers being global (central design, world wide manufacturing), there is no alternative. To do business with Europe, all must follow the ELV directive. Impossible for one specification to be compliant in Europe, another spec for rest of the world. Hence automakers constrained to produce to one universal specification. Plating Suppliers have answered the need with offerings of Hex chrome-free finishes, Trivalent chromates, and chrome-free dip spin coatings. Trivalent chrome appears to be an immediate replacement. Tri-chrome does not offer same corrosion resistance as hex. for all colors nor does it have self-healing capabilities. Yet Tri-chrome is a viable option. Automakers are encouraging total elimination of chrome-containing processes. Some view the switch from Hex to Tri chrome as an unsatisfactory temporary solution.
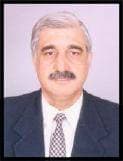
Asif Nurie [deceased] [deceased]
- New Delhi, India
With deep sadness we acknowledge the passing of Asif on Jan 24, 2016
Q. Dear Asif Nurie,
Our customer has requested that we test our parts for lead, mercury, cadmium and chromium hexavalent. Our parts are made up of plastic housing, metals and printed circuit boards. It is appreciated if you could share the various test methods available for the above heavy metals for the different materials. Like you said there are 9 test methods for Cr6+.
Thanks.
Manufacturing - Malaysia
2004
Multiple threads merged: please forgive chronology errors and repetition 🙂
Test to identify hexavalent parts
Q. Hi,
Please let me know how to identify Trivalent & Hexavalent passivation (Zinc plated parts).
Are there any testing methods to identify this?
Regards,
electronics - Bangalore, Karnataka, India
2004
A. Trivalent chromium isn't yellow, so that's the first easy screening. If they're yellow they're not trivalent so they're not acceptable; throw them away.
No, wait! I just heard that people decided it's a good idea to dye trivalent parts yellow so everyone will think they are still their toxic predecessors :-)
Never mind then, one by one chemical testing is the only way; see GMW 3034 for the test procedure. Somebody certainly has a great opportunity to make a fortune if they can invent some sort of remote hexavalent detector akin to an infrared temperature gun or alloy/scrap sorter hand-held x-ray fluorescence gun. And I guess dyeing trivalent coatings spring green isn't gonna happen :-)
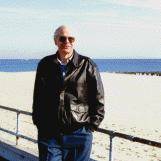
Ted Mooney, P.E.
Striving to live Aloha
(Ted can offer longterm or instant help)
finishing.com - Pine Beach, New Jersey
A. Dear Suman JSS,
A simple check is the difference in the colours,
Trivalent clear, has a Violet-Blue appearance,
Hexavalent clear, Blue-silver appearance,
Trivalent colour, Green-red more green than red,
Hexavalent colour, multi coloured with more yellow.
All the best
- GB
2005
Hi Andrew. Thanks for your posting! But with today's various proprietaries I think it's ever decreasingly accurate anymore.
Regards,
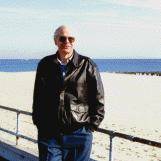
Ted Mooney, P.E.
Striving to live Aloha
(Ted can offer longterm or instant help)
finishing.com - Pine Beach, New Jersey
Q. PLEASE SPECIFY ANY SPOT TEST METHOD TO IDENTIFY THE TRIVALENT CHROME AND TRIVALENT CHROME PLATED PARTS.
VENKATESWARAN SUBRAMANIAMautomotive - Bangalore, Karnataka, INDIA
2004
Q. We are a fastener distributor and, because we are supplying more product with either trivalent chromate or no chromate finishes, we were wondering if there is any simple test we may perform in our incoming inspection to confirm the presence of hexavalent chromate.
Tim Day- Milwaukee, Wisconsin
2004
A. Tim,
You should obtain a copy of the GM standard GMW3034. It describes a laboratory method using chemicals for detecting the presence of hexavalent Cr. Global Engineering Documents sells this standard.
Automotive module supplier - Michigan
![]() |
Q. My company provides 2 identical stamped parts for a customer with the exception of plating - one part is trivalent chrome plated, while the other is hexavalent chrome plated. - Waterbury, Connecticut, US 2005 A. Short answer is no, because chromium PLATING is neither hexavalent or trivalent. Those terms refer to the oxidation state of the chromium in solution in the plating bath. A chromium plating has chromium in oxidation state zero (because it is metal and not in solution), and it does not depend upon which type of chromium bath it was plated from. ![]() James Totter, CEF - Tallahassee, Florida A. If you are referring to chromate coatings and not chrome plating, there are tests used to tell the difference between trivalent chromium coatings and hexavalent chromium coatings. The methods are given in ISO 3613. Timothy McGrady- Lansing, New York |
Multiple threads merged: please forgive chronology errors and repetition 🙂
Q. I am a chemist in a leading automotive electricals in India. Some of the components used to be passivated with Trivalent chromium for better corrosion resistance.
What is the suitable methodology to spot test on plated components of trivalent and hexavalent to differentiate between them?
Automotive electricals - Chennai, India
2006
Q. We're electronic industry, so we have to obey RoHS directives. I need help to test Cr+6 in just outer layer of chromate coating qualitatively or quantitatively. The laboratories here do not measure the outer layer Cr amount. Only in Japan. How and where can we find the test kit to measure the Cr+6 existence or amount?
Thanks ...
engineer - TURKEY
2006
A. "Directive 2002/95/EC of the European Parliament and of the Council of 27 January 2003 on the restriction of the use of certain hazardous substances in electrical and electronic equipment" does not mention chemical testing for the restricted substances.
A 208-page document, "IEC 62321, Ed.1: Procedures for the determination of levels of six regulated substances (Lead, Mercury, Cadmium, Hexavalent Chromium, Polybrominated Biphenyls, Polybrominated Diphenyl Ethers) in electrotechnical products," should be available in October 2006, noticeably after the 1 July 2006 effective ban date!
https://www.iec.ch/
Of practical use, the Metal Finishing Suppliers' Association has a pdf download 'Hexavalent Chromium Testing' by Frank Altmayer at http://www.mfsa.org/ ⇩
A shorter version, with color photographs but fewer test descriptions, is at https://www.pfonline.com/articles/080603.html ⇩
Some of the listed possible sources of hexavalent chromium are mere technicalities, as normal rinsing (dragout rinse, flowing rinses, warm DI water rinse) should remove entrapped hex. Cr to below applicable limits.
Look for labs doing any of the ISO, ASTM & auto mfr. tests mentioned.
A homogeneous coating must be analyzed in its entirety. E.g., with chromated zinc plating, you need to weigh & remove the entire coating and determine its Cr(+6) content. On a steel substrate, first remove any separately applied organic sealer (topcoat) using solvent, weigh the part, entirely dissolve the zinc & chromate in 50 vol% phosphoric acid (85 wt%) solution, reweigh the bare part to get coating weight by difference, then determine [Cr+6] in the solution spectrometrically using diphenylcarbohydrazide ⇦ on
Amazon [affil link]
.
If an organic binder is an integral component of the coating, it must be weighed & dissolved (e.g., using acetone
⇦ on
eBay
or
Amazon
[affil link] Warning! Flammable!
) and analyzed, along with the rest of the coating.
- Goleta, California

Rest in peace, Ken. Thank you for your hard work which the finishing world, and we at finishing.com, continue to benefit from.
Ed. update: The above links are broken. Thankfully, the Internet Archive preserved a copy here
Please consider a donation to The Internet Archive. Don't follow abandoned links, old URLs are sought out by hackers to install malware!
Thanks very much, Ken. That article from pfonline is excellent at pointing out the difficulties. The meaning of "homogeneous coating" is driving the world crazy :-)
As previously noted in "Galvanizing Industry in Denial?", the AGA apparently believes we are to weigh the entire article in question -- steel plus zinc coating and ignore all this stripping stuff (I'm confident they're wrong though!).
The RoHS definition contradicts both common sense and easily acquired experience. How can the regulations be based on "Chromate coatings cannot be physically stripped off the plated substrate"? Pooh. The chromate on zinc plated parts can be mostly, and very easily, rubbed off with a pencil eraser -- sometimes it is! Conversely it's difficult to mechanically remove zinc plating; if adhesion is excellent, it's impossible. Also, the chromate coating is orders of magnitude thinner than the zinc plating, so how can we consider such radically different yet easily separable things as the chromate layer and the zinc plating layer a single "homogeneous" material?
And ehen we zinc plate and chromate zinc diecastings, as is often done for a nice appearance, how shall a stripping method differentiate the zinc plating from the zinc substrate?
Zinc plating plus chromate coating is NOT a "homogeneous coating", so until the methods are completely spelled out as part of the RoHS code we are "Through the Looking Glass" where homogeneous "means just what I choose it to mean -- neither more nor less". My rant only, so stick with the stripping.
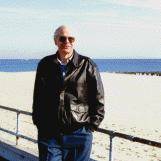
Ted Mooney, P.E.
Striving to live Aloha
(Ted can offer longterm or instant help)
finishing.com - Pine Beach, New Jersey
Ed. note: Please see also letter 16365, "Determining if you have hexavalent or trivalent zinc chromate coating" for more ideas.
Test for Chromate Conversion Coating on Aluminized Steel
We are looking for a suitable method for identifying whether aluminised steel has been treated with a chromate conversion coating. We have discovered that the Chromate interferes with the degreasing / application of high temperature paint ⇦ on eBay or Amazon [affil link] to aluminised steel, causing the coating to fail in service.
Allan NichollsQuality Manager - Auckland,, New Zealand
2006
![]() |
A. Get yourself some diphenylcarbohydrazide ⇦ on
Amazon [affil link]
. If you have an analytical lab that does your waste water monitoring, they will probably give you a couple of grams. Mix 1 gram with about 50 grams reagent grade sodium chloride, well. ![]() Dave Wichern Consultant - The Bronx, New York A. Allan -
Acronyms:
FTIR = Fourier-transform infrared spectroscopy There are several ways to check for that kind of coating. X-ray fluorescence can look for the Cr but you have to have a piece of your aluminized steel that is non-chromated to compare with since your base metal may have Cr in it. Another way is to use FTIR. This will work if the coating is like an Alodine 1200 which will display a CN band. Finally, there are chemical spot tests for these kinds of coatings, but can you tell which particular one you are dealing with? - Auburn, Washington |
Q, A, or Comment on THIS thread -or- Start a NEW Thread