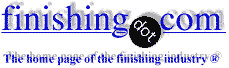
-----
Misc. problems in CED (cathodic electrodeposition) coating
This thread covers many CED problems, but Pinhole problems have been moved to Thread 57561. Please search the site for many more threads about CED.
for Shops, Specifiers, & Engineers
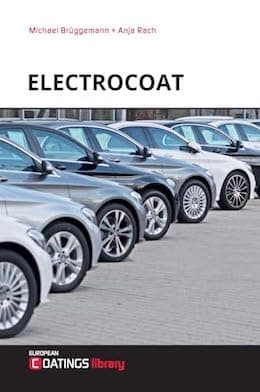
avail from eBay, AbeBooks, or Amazon
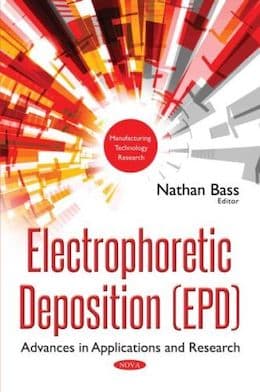
avail from eBay, AbeBooks, or Amazon
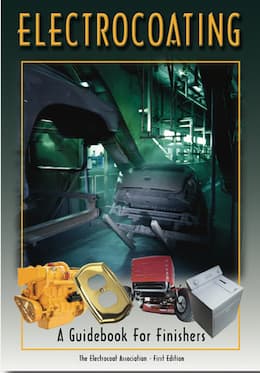
avail from AbeBooks, or Amazon
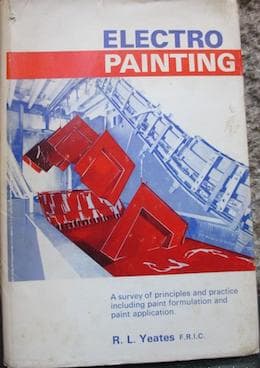
avail from eBay, AbeBooks, or Amazon
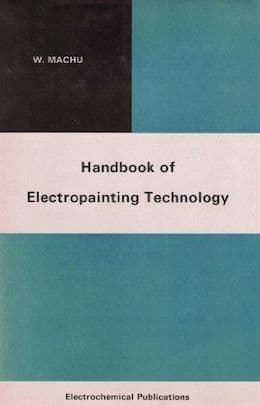
avail from eBay, AbeBooks, or Amazon
(as an Amazon Associate & eBay Partner, we earn from qualifying purchases)
Q. Paint chips off from the CED + Liquid silver coated steel wheels. We suspect high DFT -- are there any other possible causes?
K KANAGARAJPrivate employee - Chennai, India
February 28, 2024
Q. My supplier is having finishing issues with the aluminium parts he coats for us. The results we are seeing is milky-like streak on black cathodic electro dip. What are the potential causes for this?
Sara Milva- Seixal, Portugal
March 1, 2024
Please share photos of these problems.
Avinash Vidhate- Nashik, Maharashtra, India
March 10, 2024
⇦ Tip: Readers want to learn from your situation;
so some readers skip abstract questions.
Q. How to control CED coating dust, orange peel like defects?
Prem Kaswa- Ahmednagar, Maharastra
March 4, 2024
Q. Hello sir, my name is piyush. I work in ced coating as a lab technician but recently I face a dust problem in part. It's GI coated part so please tell me how can I resolve it?
Piyush Gaur
- Faridabad Haryana
July 4, 2024
Multiple threads merged: please forgive chronology errors and repetition 🙂
Q. I am getting the problem of half-coating and half no-coating in CED. Defect rate is low. I have checked the contact points and there seems no problem with that. Defect rate might be around 1 in 100.
Madhukesh Jamadagnipainting shop - Mysore, Karnataka, India
2004
A. Check CED bath parameters. Check for bath and anolyte conductivity.
Manish Dhyani- New Delhi
Q. Please send me the information of the defects of CED COATING, and provide the answers for the questions relating to the topic. I will be grateful to you.
THANKS,
- Faridabad, Haryana, India
2006
A. Hi cousin Manmohan. Others, perhaps suppliers, might have free booklets available of the sort you seem to be seeking, but we don't. However, we've listed six books on the subject if you want to you want to try to get access to one or more of them.
This public forum is more suited to helping people work their way through a specific problem they are encountering; to take best advantage of what we're able to do, please try to detail your situation; feel free to send pictures to mooney@finishing.com for posting here. Thanks.
Luck and Regards,
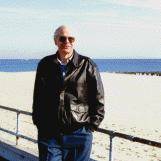
Ted Mooney, P.E.
Striving to live Aloha
(Ted is available for instant or longterm help)
finishing.com - Pine Beach, New Jersey
Dirt in Coating
Q. We are facing dirt/impurities problem on parts after CED coating.
Kalidas Suryawanshi- Pune, India
2007
A. Dirt can come due to improper cleaning in the pre treatment line. It can be due to dirt in the E-coat tank. It could be due to dirt in the rinse tanks after E-coat. It could be due to dirt being blown around in the oven with the forced circulation. It could be because of one or more than one of the reasons above. And the reasons above could also be due to improper housekeeping or ingress of dirt & dust in your E-coat shop.
Test each and eliminate. I assure you this does not require NASA technology.
Mohali, Punjab, India
A. Check for sludge material in phosphate bath ... if it is high, then desludge it immediately. This will solve your problem.
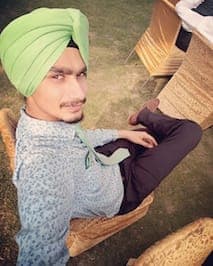
Baljeet Singh
- Ludhiana, Punjab, India
A. Dear kalidas
Reason of dust ...
1- not proper manual cleaning
2- kod/degreasing FAL pointage down
3- contaminated rinse
4- sludge increase in phosphate tank
5- contaminated DI water..
Process incharge - Fharidabad Haryana
August 31, 2021
A. 1. Kindly install filter housing just before CED tank.
2. Use 10 micron filter in CED bath for 10 days and plan to use 10 micron bag filter once in three month.
3. Check CED bath circulation :- it should be properly work, causes of poor circulation paint settling started in bath then generate dust when settling burst.
4. Check incoming material quality first :- it should be dirt free , need & clean material required for ced.
5. Add Solvent as per spec. Less solvent also create dirt or improper finish.
Senior Executive - Looking Paint Process - Haryana, India
A. Otherwise you can check oven and chamber filter cleaning and air quality.
Amit sharma- jamshedpur, India
July 11, 2022
Ra value of CED coating
Q. I would like to know, which is the world wide standard method for checking Ra value-
I want to check Ra value of CED (Cathodic electrodeposition) primered surface, for which I require following information
a) In automobile industry, world wide, which is the common equipment is used to measure Ra value ?
b) What is travel length ( what is world wide standard length?)
c) What is the speed ?
d) What is acceptance level of CED coated / finish painted panel for Ra value in reputed automobile industries ?
Thanks & regards,
Pune, India
2006
Q. PLEASE TELL ME HOW TO CHECK THE Ra VALUE OF CED COATING.
WHAT IS THE RANGE FOR OEM VEHICLES?
WHAT ARE/IS THE INSTRUMENT USED FOR CHECKING RA VALUE?
ENGINEER - INDIA
May 20, 2009
A. Ra is checked by roughness gauge.
Better you ask your paint supplier for Ra Parameters.
Thanks
SURYA
- DELHI, INDIA
A. Hi,
Normally Ra value can be checked with use of Perthometer. try it.
Anand.
- Chennai, India
[editor appended this entry to this thread which already addresses it in lieu of spawning a duplicative thread]
Q. We have an Aluminium Die Casted part having Diameter 660 mm and Thickness 15 mm, and we are doing the Heat Treatment & Machining ... and than last we do the CED Coating. Now according to our experience the Machining surface achieved an Ra value between 0.79 to 1.62 µm. However after CED Coating the Ra value found between 2.741 to 10.95 µm. Hence we would like to know about--
• Ra value is increased after the CED Coating?
• Can we control the Ra up to 3.62 µm after CED Coating?
Please suggest
- Vadodara, Gujarat
March 28, 2024
A. Hi Jayesh.
Presumably you phosphatize the components after machining and before CED coating? Phosphatizing significantly increases the Ra. So a question might be what is the Ra after phosphatizing? Armed with that information you would be better equipped to figure out where the bulk of the roughness is coming from and whether to focus on the phosphatizing or the CED step itself.
Luck & Regards,
Ted Mooney, P.E. RET
Striving to live Aloha
(Ted is available for instant or longterm help)
finishing.com - Pine Beach, New Jersey
! Dear Sir,
For CED coating of aluminium, phosphating is not done; instead chromatising is the process.
Please let us know the process what exactly he is doing.
- Nashik, Maharashtra, India
April 3, 2024
![]() |
🙏 It's your humbleness 🙏 Avinash Vidhate [returning]- Nashik, Maharashtra, India April 6, 2024
|
Dissolution of CED Coating
Q. Hello, could anybody help me understanding the reason for dissolution after CED coating on wheels? It mainly happens with small wheels.
Regards,
wheels - Bologna, italy
April 11, 2014
A. Hi Ale. Sorry, but I don't quite understand what you mean by dissolution after CED coating. Can you offer a synonym or expand upon your situation, please. Thanks.
Regards,
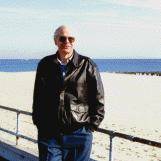
Ted Mooney, P.E.
Striving to live Aloha
(Ted is available for instant or longterm help)
finishing.com - Pine Beach, New Jersey
Q. Hello, I'm sorry, pictures were missing. We produce steel rims and it happens that a few rims (1 to 10% depending on the reference) leave the CED coating bath only half coated; more precisely only the first half on the rim is coated.
I've attached an explicative picture. Which parameters could cause it in your opinion?
Kind regards,
- Bologna, italy
April 15, 2014
A. Sir,
It might be helpful to
- increase bath & anolyte conductivity,
- change the loading position.
Thanks
Surya
- Faridabad, India
Not getting e-coating despite proper voltage
Q. WE ARE GETTING NO COATING ON THE COMPONENT (LOAD BAR). WE GETTING THE PROPER VOLTAGE BETWEEN BOTH POLES AS PER SETTING BUT THE CURRENT IS GOING ONLY 15-20 A DC. OTHER HAND IF WE WILL PROCESS ONLY 2 OR 3 PARTS, WE ARE GETTING COATING AT THE COMPONENT. LET ME KNOW THE ACTUAL PROBLEM AND ALSO IF IT CAN BE THE PROBLEM OF RECTIFIER.
OMPRAKASH YADAV- NOIDA,UTTER PRADESH, INDIA
September 25, 2014
A. Hi,
I'm assuming that that you are using a cataphoretic resin. If it is anophoretic then the advice still stands but swap the words "anode" and "cathode",
Your problem may be caused by the anodes restricting the current flow. So, when you put large areas of work in the bath the cathode current density is too low to initiate deposition of resin. Suggest:
1) Increase the number of anodes
2) If you are using anode boxes make sure that that they are filled with electrolyte of the recommended conductivity.
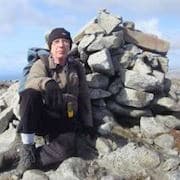
Harry Parkes
- Birmingham, UK
A. Increase anode area
Increase voltage
Increase solid in bath
Increase bath temperature
That is it.
Regards,
- istanbul Turkey
A. Reasons for poor CED coating:
1. Poor electrical contact to the job to be coated.
2. Low cathode-anode ratio. This will be considered in plant design itself. But this may vary if the anode gets corroded; in case of CED, check the anode condition.
3. If ramp up voltage is too high, some parts may get poor coating.
Since amps is showing very low, it means the rectifier to be checked.
- Chennai, Tamilnadu, India
Finish coat cracked due to inferior E-coat under it?
Q. Working with a shop on a repair that used an aftermarket bumper cover (non steel) and when the finish coat was applied it cracked all over as it started to cure.
Shop says it's inferior E-coat used by the aftermarket supplier. Your thoughts?
Phil W [last name deleted for privacy by Editor]insurance claims - Houston, Texas, USA
January 21, 2015
A. Hi Phil. Body shops aren't coatings science laboratories, able to analyze why an aftermarket bumper cover was unpaintable -- but I do trust them to be able to reliably paint proper substrates.
opinion! If these are aftermarket parts specified by an insurance company, someone failed their job of sending the parts to a coatings science laboratory to prove they're okay.
But this problem is the tip of the iceberg; the consumer gets stuck with the long term problems that don't immediately manifest like this one did. Consumer Reports has written about the problem of insurance companies and body shops using inferior replacement parts, such as non galvannealed panels, and the problems which only surface after time has passed. We offer Aloha here, but can't side with offering less than what is required. Low quality sucks. Good luck.
Regards,
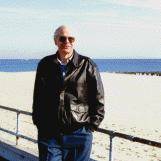
Ted Mooney, P.E.
Striving to live Aloha
(Ted is available for instant or longterm help)
finishing.com - Pine Beach, New Jersey
Q. We are getting water spots and water or paint flow marks on the components after curing. We could identify the marks if we blow air after UF and before curing. How to eliminate these marks?
RAJAGOPALAN SESHADRICED COATING UNIT - Hosur, Tamilnadu, India
February 17, 2015
A. Extend your bus bar to achieve live entry in place of dead entry in CED bath. Or You have to keep it completely wet or completely dry before entering CED bath at water rinse stage before entering into CED tank: Because partially wet or partially dry body can cause such kind of problems.
SANJEE KUMAR- ALLAHABAD, India
July 16, 2022
CED Painting Defect: 'Partial Coagulation'
Q. Please tell me about the CED painting defect of "partial coagulation" on child bicycle parts like swing arm, center stand and prop stand.
Prince Kumar- gurgaon, haryana, India
August 1, 2015
Ed. note: Please send photos to mooney@finishing.com for posting here, as well as some data.
Anodic to cathodic cell ratio in CED electrocoating
Q. Hi sir I want to know how much ratio in anodic and cathodic cell in CED bath
Sandeep kalidas rautCED coating - Mumbai, Maharashtra, India
December 16, 2015
A. Dear sir
Greetings
Anode and cathode ratio-1:14
Thanks
Process incharge - Faridabad [India]
Q. How to calculate the anode cell ratio in CED? Please, I am preparing for an interview and I need a clear answer.
BALA maniprivate automobile company - Chennai, tamil nadu, India
March 16, 2016
CED Bath: Why/How has Sodium Increased with no other changes?
Q. Hello sir,
There is increase in the sodium content in the CED bath while all parameters of the bath are as per specification. Please suggest.
- Pune, Maharashtra India
March 31, 2016
![]() |
A. Na content increases due to carryover of alkaline cleaners from P.T. line. Rinse parts thoroughly. - Nasik, Maharashtra, India A. An increase in the sodium level can be due to drag out from your alkaline cleaner. Are you using a sodium hydroxide based cleaner? Dan Mack- Horicon, Wisconsin USA |
Q. Hi
What is maximum oven temperature for CED jobs?
Can we put CED & Power Coated jobs into one batch for Curing the coatings?
Please give details.
Thanks & Regards
powder coating & CED coatings - Pune, Maharastra, India
June 27, 2016
A. Generally CED Paint cures at 150 °C / 20 minutes or 160 °C / 10 minutes Effective Metal Temperature. Oven Air temperature can be set depending on the Material thickness (Component) and time available for Oven curing.
If it is thin material may be 170 °C, 30-40 minutes more than sufficient to cure. In case of thick material like Forging or Casting we may go ahead up to 200 - 220 °C.
Logically we can bake both Powder and E.Coat in the same oven and there will be not any issue in the baking as long as if we meet the baking window criteria.
However E.Coating is a 'wet' process and it is cured in an oven to promote cross-linking. Solvent and Moisture evaporation takes place. Whereas in Powder, Curing causes the particles to melt and also serves as the catalyst for a chemical reaction that produces the desired finish. Both are different process.
During the Hot air circulation sometime loose powder particles deposits on the E.Coat surface before curing causes finish problem. Hence I would not advise Technically. Let us wait for some expert comment please.
- Chennai, Tamilnadu, India
Hi. That sounded like "expert comment" to me. Thanks!
Regards,
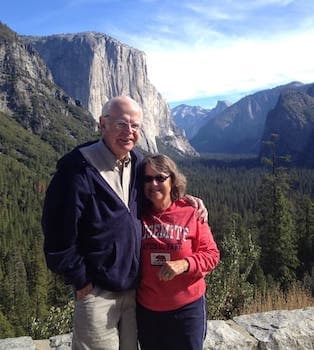
Ted Mooney, P.E. RET
Striving to live Aloha
(Ted is available for instant or longterm help)
finishing.com - Pine Beach, New Jersey
Q. How can we control roughness after CED coating? It is varying a lot. I want to maintain it to its standard.
monu mittal- gurgaon, haryana, India
March 24, 2017
A. CHECK EARTHING.
PRASHANT KUMARCEPL - PUNE, Maharashtra, India
Anode Cell Area Calculation
Q. Can anyone please help me how to calculate the Anode cell area/ no. of Anode cells required in ED Coating process according to Area of Component or Tank size?
Also how to select the range of Rectifier?
Designer - India
October 7, 2017
Q. Can anyone please help me how to calculate the Anode cell area/ no. of Anode cells required in ED Coating process according to Area of Component or Tank size? How do we know what is the capacity of anode in relation to surface area? How much surface area is covered by one anode?
We manufacture wheel rims; when we hang these on a basket after CED coating some area is unpainted where they are touching each other. What is the real cause of this
Rohit Kumar- Faridabad haryana , India
November 27, 2017
Masking for CED Coating
Q. Hi
We'd like to mask the wheel rim knurling during CED process.
Please suggest any masking.
- Chennai, India
January 22, 2018
(you are on the 1st page of the thread) Next page >
Q, A, or Comment on THIS thread -or- Start a NEW Thread